Die Industrie ist auf dem Weg zur Smart Factory
Die „Smart Factory“ – die „intelligente Fabrik“ – steht im Mittelpunkt von Industrie 4.0 und bezeichnet die Produktionsumgebung, die sich selbst organisiert. Viele Unternehmen sind mitten im Transformationsprozess, andere auf dem Weg dahin. In einem Gastbeitrag beschreibt Markus Diesner von MPDV, wie die Transformation mithilfe von MES-Systemen vollzogen werden kann.
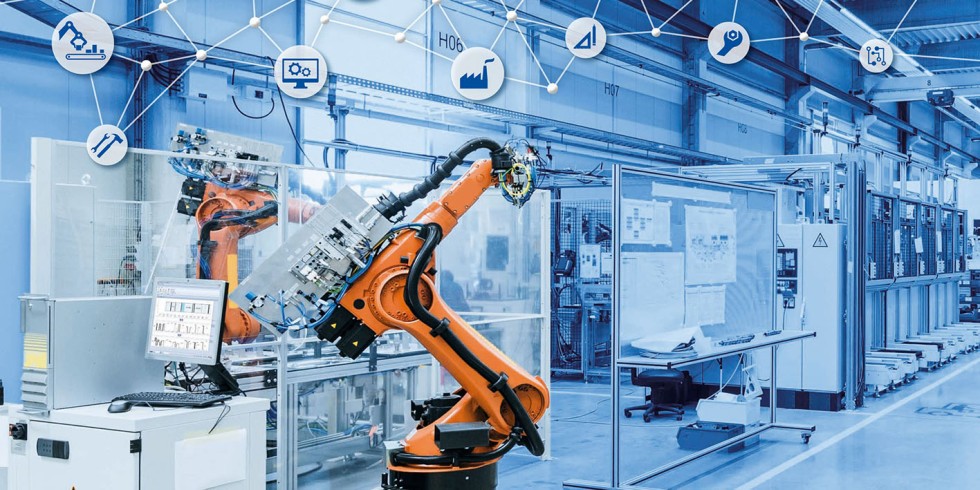
„Blick über den Tellerrand“: Nach dem letzten Schritt, der funktionalen Vernetzung in der Smart Factory, lassen sich beispielsweise Produkte und deren Bestandteile über die komplette Wertschöpfungskette rückverfolgen. Bild: MPDV, Westend61/stock.adobe.com
In vielen Fachbeiträgen wird die Smart Factory mit Begriffen wie cyber-physische Systeme (CPS) oder Internet of Things (IoT) in Verbindung gesetzt. Das mag für theoretische und Zukunfts-gerichtete Betrachtungen sinnvoll sein. Ein Großteil der produzierenden Betriebe und insbesondere der kleineren und mittelständischen Unternehmen (KMU) lebt heute allerdings noch in einer ganz anderen Welt. Hier ist nicht selten die Rede von klassischen BDE-Systemen (Betriebsdatenerfassung) oder einfachen MDE-Lösungen (Maschinendatenerfassung). Die Softwarekategorie der Manufacturing Execution Systeme (MES) ist zwar in vielen Unternehmen bekannt, aber lange nicht in allen. Auch die Zahl derer, die ein MES im Einsatz haben ist für die heutige Zeit noch viel zu gering. Daher soll in diesem Beitrag ein etwas „bodenständigeres Wording“ zum Einsatz kommen – wohlwissend, dass insbesondere größere Konzerne auch mit den zuvor genannten Begriffen wie CPS oder IoT bereits vertrauter sind. Die Fähigkeiten und Nutzen eines MES-Systems eignen sich sehr gut dafür, eine Brücke zu schlagen zwischen der bekannten und der neuen Welt. Dass die Smart Factory ein wesentliches Ziel des Zukunftsprojekts Industrie 4.0 ist, darüber sind sich beiden Lager sicher einig.
Was leistet ein MES-System auf dem Weg zur Smart Factory?
Als MES wird eine prozessnah operierende Ebene eines mehrschichtigen Fertigungsmanagementsystems bezeichnet. Oft wird dafür auch der deutsche Begriff „Produktionsleitsystem“ als Synonym verwendet. Es gestattet die Führung, Lenkung, Steuerung oder Kontrolle der Produktion in Echtzeit. Dazu werden alle relevanten Daten übernommen: Betriebs-, Maschinen- und Prozessdatendaten, Personal- und Qualitätsdaten. Mit diesen Informationen entsteht im MES ein digitales Abbild der Fertigung; Planungsfehler und Optimierungschancen lassen sich schnell aufdecken.
Der Begriff MES wird in Deutschland durch die VDI-Richtlinie 5600 und das NAMUR-Arbeitsblatt NA 94 transparent gehalten. Das VDMA-Einheitsblatt 66412 definiert zudem die Kennzahlen, mit denen die Zielvorgaben zu den Produktionsprozessen im Fertigungsmanagement überwacht werden. Das Vier-Stufen-Modell des Softwarespezialisten MPDV beschreibt einen Weg zur Smart Factory, der auch für kleine und mittelständische Unternehmen (KMU) gut gangbar sein soll. Das Mittel der Wahl ist hierbei das integrierte MES-System „Hydra“.
Ein Software-Ansatz in vier Stufen
Grundlage für den vorgeschlagenen Weg zur Umsetzung der Smart Factory ist ein schrittweises Herangehen, welches sich an den Bedürfnissen und Anforderungen des jeweiligen Unternehmens orientiert. Zusammengefasst bedeutet das: Zunächst muss die Fabrik transparent werden, um darauf basierend reaktionsfähiger sein zu können. Beides macht Selbstregelung möglich und führt zusammen mit der funktionalen Vernetzung letztendlich zur Smart Factory. Im Folgenden werden die einzelnen Stufen des Modells und die entscheidenden Schritte des Wegs anhand von Beispielen erklärt, Bild 1.

Bild 1. Das Vier-Stufen-Modell der „Smart Factory“ aus Sicht des MES (Manufacturing Execution System)-Anbieters. Bild: MPDV
Stufe 1: transparente Fabrik
Jedes System benötigt eine verlässliche Datenbasis – so auch die Smart Factory. Neben den vielfältigen Daten aus Sensoren profitiert die intelligente Fabrik allerdings auch von der Berechnung geeigneter Kennzahlen und von der Korrelation technischer mit betriebswirtschaftlichen Daten. Deshalb ist ein IT-System unabdingbar, das beide „Welten“ kennt und somit einen 360°-Blick auf die Fertigung zulässt – ein Manufacturing Execution System. Ein MES wie Hydra kann alle nötigen Daten erfassen und diese nutzergerecht zur Verfügung stellen, Bild 2. Beim Aufzeichnen der Daten unterstützen sowohl automatisierte Datenschnittstellen wie „OPC UA“ als auch ergonomische Erfassungsdialoge auf industrietauglichen Touchscreen-Terminals oder Tablet-PCs. Zur Auswertung und Visualisierung haben sich Diagramme und filterbare Tabellen als zielführend erwiesen. Damit kann Transparenz sowohl in Form von vergangenheitsbezogenen Analysen als auch in Form eines echtzeitfähigen Online-Monitorings realisiert werden.

Bild 2. Der Shopfloor-Client erfasst und visualisiert Echtzeitdaten direkt an der Maschine. Bild: MPDV
Stufe 2: reaktionsfähige Fabrik
Die Verfügbarkeit geeigneter Daten gestattet im zweiten Schritt sowohl eine realitätsnahe Planung und Steuerung der Produktion als auch ein schnelles Reagieren auf Störfaktoren und andere äußere Einflüsse. Bei der Planung kann und sollte ein MES alle an der Produktion beteiligten Ressourcen berücksichtigen. Dazu gehören neben den Maschinen und den Aufträgen auch benötigte Werkzeuge und weitere Hilfsmittel, das zu verarbeitende Material, die Mitarbeiter und möglicherweise auch Energie.
Im Gegensatz zu vielen ERP-Systemen (ERP steht für Enterprise-Resource-Planning) und zu reinen Planungstools kann ein MES auch Echtzeitdaten aus der Fertigung berücksichtigen und so eine Planung gegen reale Kapazitäten umsetzen, Bild 3. Dies wiederum wirkt sich positiv auf die Reaktionsfähigkeit des Gesamtsystems aus. Beispielsweise können Engpässe frühzeitig erkannt und somit umgangen werden. Auch die Integration von Wartungen und Instandhaltungstätigkeiten in die Fertigungsplanung steigert die Qualität der Planung. Im Fall einer Störung kann auf Basis der vorliegenden Daten schnell reagiert und falls nötig umgeplant werden. Dabei sind die sich daraus ergebenden Folgeerscheinungen sofort im MES sichtbar.

Bild 3. Das MES-System „Hydra“ gestattet eine ressourcenübergreifende Planung. Bild: MPDV, industrieblick/stock.adobe.com
Stufe 3: selbstregelnde Fabrik
Die Verfügbarkeit von Daten in Kombination mit einer reaktionsfähigen Planung gestattet gleichzeitig auch die Einrichtung von selbstregelnden Prozessen – dem nächsten Schritt auf dem Weg zur Smart Factory. In der einfachsten Form besteht Selbstregelung aus der Überwachung eines bestimmten Messwerts und der Einleitung von Gegenmaßnahmen, sobald sich dieser außerhalb seines Sollbereichs bewegt. Ein MES kann darüber hinaus auch komplexere Szenarien überwachen und somit auch umfangreichere Regelwerke umsetzen.
Die Anwendungsfälle für selbstregelnde Prozesse reichen von der zustandsorientierten Instandhaltung über die fertigungsbegleitende Qualitätssicherung bis hin zu integrierten Intralogistikprozessen. Der Mensch nimmt in der selbstregelnden Fabrik die Rolle eines „Augmented Operator“ ein, der auf Basis von umfangreichen Informationen dort eingreifen kann, wo das System selbst nicht zu einer zielführenden Lösung kommt. Dabei unterstützt das MES den Menschen dabei, die Komplexität der Produktionsprozesse besser zu überblicken, Bild 4.
Stufe 4: funktional vernetzte Fabrik
Der vierte und letzte Schritt auf dem Weg zur Smart Factory bedeutet den „Blick über den bisherigen Tellerrand hinaus“. Vorhandene Systeme sollten so miteinander vernetzet sein, dass Daten korreliert werden können, die zu neuen Erkenntnissen im Sinne der Optimierung führen. Ein Beispiel dafür ist die Vernetzung von Produktion und Intralogistik, um schneller auf Anforderungen aus den Prozessen heraus zu reagieren. Sinnvoll wäre auch beispielsweise eine automatische Transportanforderung an das „Warehouse Management System“ (WMS), sobald eine bestimmte Anzahl von Produkten gefertigt ist. Auch Systeme wie das Gebäudemanagement oder andere an der Supply Chain beteiligten Anwendungen benötigen Daten aus dem MES oder stellen Daten zur Verfügung.
Manche branchenspezifischen Anforderungen können auf diese Weise einfacher oder überhaupt erst realisiert werden – beispielsweise die Rückverfolgbarkeit von Produkten und deren Bestandteilen über die komplette Wertschöpfungskette hinweg. Andererseits ist auch die Vernetzung von Anwendungen entlang des Wertstroms sinnvoll. Ein Beispiel dafür ist die automatisierte Übernahme von Prüfmerkmalen für die Qualitätssicherung aus den CAD-Modellen der Konstruktion. Hiermit werden sowohl Aufwände reduziert als auch Fehlerquellen ausgeschlossen.
Selbstkontrolle: Wurden die gesteckten Ziele erreicht?
Es bleibt die Frage, ob jedes Unternehmen, das bei Stufe 4 angekommen ist, automatisch eine Smart Factory hat. Oder ob eventuell sogar bereits auf einer früheren Stufe das Ziel erreicht wurde. Da die Anforderungen jeder Branche unterschiedlich sind und jedes Unternehmen den Forderungen auf ganz individuelle Art und Weise begegnet, ist ein generelles Urteil weder möglich noch zielführend. Das Vier-Stufen-Modell zeigt lediglich die Möglichkeiten und gibt Orientierung auf dem Weg zur Smart Factory.
Einen finalen Zustand wird es darüber hinaus kaum geben, da weder der Markt noch das Angebot innovativer Technologien stillstehen werden. Und somit ist der Weg zur Smart Factory auch gleichzeitig das Ziel der Bemühungen um mehr Effizienz in der Fertigung und einer langfristigen Wettbewerbsfähigkeit einzelner Unternehmen sowie ganzer Industriestandorte. Eines ist jedoch sicher: Ein Manufacturing Execution System wie Hydra ist auf dem Weg zur Smart Factory für KMU ein geeigneter und nutzbringender Begleiter. Technologien wie Künstliche Intelligenz (KI) oder das Industrial Internet of Things (IIoT) sind weitere nützliche Werkzeuge, die das MES dabei unterstützen, die vorhandenen Daten zielführend zu verarbeiten und so die Effizienz zu sichern.
Weitere Details und Anwendungsbeispiele zum Vier-Stufen-Modell finden sich im Whitepaper, das kostenlos angefordert werden kann: http://mpdv.info/favdizsf
Markus Diesner ist Marketing Specialist Products bei MPDV Mikrolab in Mosbach.