Digital Twins im gesamten Produktlebenszyklus nutzen
Sie sind das virtuelle Abbild der materiellen Welt und geben dadurch völlig neue Einblicke: digitale Zwillinge. Insbesondere Mittelständlern erschließen sich so neue Chancen. Doch in der praktischen Umsetzung hapert es häufig noch.
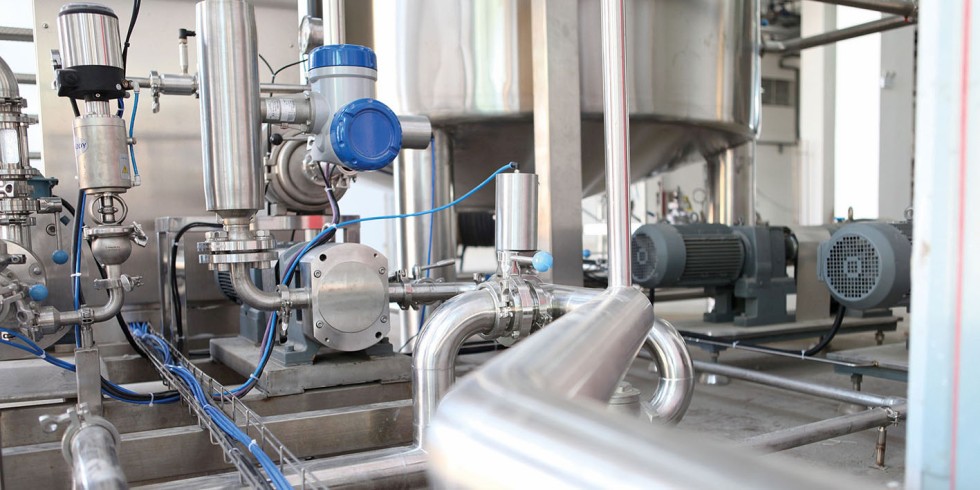
Wie Digital Twins in der praktischen Anwendung funktionieren, zeigt zum Beispiel ein deutscher Chemieproduzent. Das Unternehmen hat eine Mess- und Regelanlage entwickelt, in die das gesammelte Know-how einfloss: Diese überwacht nun erfolgreich den Einsatz von Chemikalien.
Foto: tresmo
Mittlerweile gehören Digital Twins in zahlreichen Unternehmen fest zur digitalen Transformation dazu. Und das hat vor allem einen Grund: Unternehmen können diese ab dem Beginn der Entwicklung über die Produktion bis hin zum Anwendungszeitraums des jeweiligen Produkts nutzen. Jedes Unternehmen kann dabei die Herangehensweise wählen, die zum jeweiligen Geschäftsmodell und zur eigenen Vision am besten passt. Doch wie schaffen es Mittelständler, die sich bietenden Chancen für sich zu erschließen?
Die Idee dahinter
Das Konzept des Digital Twin beschreibt die virtuelle Abbildung von physischen Objekten. Beschaffenheit und Form des realen Produkts werden ebenso wie Verhaltensweisen und Zusammenhänge digital gespiegelt. Dazu nutzt ein digitaler Zwilling in der Regel Sensoren, um den Zustand des realweltlichen Gegenstücks zu erfassen. Darüber hinaus braucht der Zwilling eine definierte Datenstruktur zur Abbildung des echten Objekts. Zu guter Letzt sorgt ein „User Interface“ dafür, dass Anwender sich die Informationen in Form von aufbereiteten 3D-Modellen ansehen können. Mit diesem Modell können Teams dann nicht nur den Zustand eines Produkts beobachten, sondern auch sein Verhalten und seine Funktionsweise modellieren. Mit dieser Erweiterung eignen sich Digital Twins nicht nur für Anlagen oder Maschinen, sondern auch zur Abbildung von Prozessen.
Von der virtuellen Idee zu besserem Design und effizienterer Produktion
Schon in der Entwicklungsphase ist der Einsatz digitaler Zwillinge ein spannender Aspekt. Denn die Gestaltung eines virtuellen Abbilds des geplanten Produkts erlaubt es Entwicklungsteams, bereits Verhaltensweisen vorherzusehen und Design-Ideen auszuprobieren, bevor es überhaupt einen Prototypen gibt. Außerdem erleichtert ein digitaler Zwilling die Zusammenarbeit über mehrere Standorte hinweg – ein Faktor, der gerade in internationalen Unternehmen oder bei Gemeinschaftsprojekten eine wichtige Rolle spielt.
Kosten und Zeitaufwand für die frühe Erstellung eines physischen Prototypen fallen weg und jede:r Beteiligte hat von überall jederzeit Zugriff auf den Digital Twin, um im jeweiligen Spezialgebiet Ideen auszuprobieren und Prognosen zu erstellen. Und noch einen Vorteil bieten realistische virtuelle Modelle: sie bringen Design und Fertigung dichter zueinander. Die gesammelten Informationen aus früheren Produktionen sind ein optimales Fundament für die Verbesserung der Folgegenerationen.
Besonders während des eigentlichen Produktionsprozesses profitiert der industrielle Mittelstand von digitalen Zwillingen und der Transparenz, die sie schaffen. Das virtuelle Abbild zeigt stets präzise an, wo in der Wertschöpfungskette sich die Produktion gerade befindet, was schon erledigt ist und welche Schritte noch anstehen. Der so generierte Gesamtüberblick über sämtliche Laufzeiten sowie Produktionsparameter kann den verantwortlichen Teams dabei helfen, bessere Voraussagen zu Lieferzeiten zu treffen, Engpässe frühzeitig zu erkennen und den Prozess kontinuierlich zu verbessern. Auch die Frage, wann der nächste Instandhaltungstermin fällig ist, kann auf Basis eines Digital Twins zuverlässiger beantwortet und so das Ausfallrisiko messbar gesenkt werden. Kommt es doch einmal zu einer Unregelmäßigkeit, beginnt die Fehleranalyse bereits im digitalen Zwilling, sodass das Problem oft identifiziert werden kann, ohne dass ein:e Servicetechniker:in vor Ort sein muss.
Digitale Zwillinge lassen Produzenten über den Tellerrand blicken
Über die Nutzung ihrer Produkte nach dem Verkauf wissen Hersteller häufig wenig bis gar nichts. Auch hier kann ein Digital Twin unterstützen, indem er völlig neue Einblicke gewährt. Davon können Anbieter lernen und ggf. nachsteuern, bevor der Kunde mit möglichen Fragen oder Beschwerden auf das Serviceteam zugeht. Dank der übertragenen Informationen aus zentralen Steuerelementen und Sensoren erkennt der Hersteller in seinem Digital Twin, ob sein Produkt den Anforderungen des Nutzers gewachsen ist und wo es möglicherweise noch Optimierungspotenzial gibt. Zusätzlich eröffnet die neu gewonnene Transparenz die Möglichkeit, proaktiven Service anzubieten und Kunden so ein besseres Erlebnis zu bieten und sie gleichzeitig noch stärker an die eigene Marke zu binden. Darüber hinaus können Unternehmen die Nutzungsdaten für spätere Produktweiterentwicklungen optimal nutzen.

Digital Twins bieten Vorteile in jeder Phase des Produktlebenszyklus. Beschaffenheit und Form des realen Produkts werden ebenso wie Verhaltensweisen und Zusammenhänge digital gespiegelt. Grafik: tresmo
Genug Theorie, wie steht’s um die Praxis?
Wer jetzt überzeugt ist, dass Digital Twins im eigenen Unternehmen einen wertvollen Beitrag stiften können, sucht nach dem sinnvollen ersten Schritt in einem relativ komplexen Themenfeld. Insbesondere kleine und mittelständische Betriebe brauchen kostengünstige Lösungen, um erste Erfahrungen zu sammeln. Dazu gibt es auf dem Markt IoT (Internet of Things)-Plattformen, die eine einfach nutzbare Modellierungssprache bereitstellen, um reale Dinge oder Geschäftsprozesse digital nachzubilden. Daran können Unternehmen mit geringem Aufwand IoT-Geräte und bereits bestehende Softwaresysteme anbinden und erste Modelle nutzen.
Doch für digitale Zwillinge gilt, was für alle neuen Technologien gilt: Wichtig ist eine klare Zielsetzung und eine genaue Idee der erwarteten Mehrwerte für das eigene Business und vor allem für die Kunden. Doch gleich mit Kanonen auf Spatzen zu schießen ist insbesondere im Mittelstand keine gute Idee. Vielmehr gilt es für Verantwortliche zuerst einfache Digital-Twin-Ansätze im Hinblick auf die verfügbaren Ressourcen des Unternehmens zu etablieren und erste Erfahrungen zu sammeln.
Unterstützung bei der Umsetzung kommt z.B. von tresmo, einem führenden IoT-Dienstleister in der DACH-Region. Die Augsburger Digitalagentur bietet Innovation und Entwicklung von digitalen Lösungen und Produkten rund um IoT, Cloud und App. Seit 2012 werden Kunden unterschiedlichster Branchen und Unternehmensgrößen in engen Partnerschaften auf dem Weg zu eigenen digitalen Produkten und Services begleitet. Dies reicht von der Innovations- und Lösungsberatung über die Systemintegration bis hin zur Umsetzung komplexer digitaler Lösungen.
Best-Practice-Beispiel aus der Chemieproduktion
Ein schönes Beispiel, wie Digital Twins in der praktischen Anwendung funktionieren, liefert ein deutscher Chemieproduzent: Das Unternehmen eignete sich über die Herstellung seiner Produkte ein breites und zugleich tiefes Know-how über deren Verwendung in unterschiedlichen Kontexten an. Um dieses Fachwissen am Markt zu platzieren, entwickelte der Betrieb eine Mess- und Regelanlage, die den Einsatz von Chemikalien überwacht.
Mit einem genauen Blick auf die Kunden betreibt der Produzent eine bedarfsgerechte Digitalisierung seiner Regelungstechnik. Jede Regelanlage hat einen digitalen Zwilling, der die Daten aus der Steuerung sowie aus zahlreichen Sensoren an den Hersteller zurück spielt. So gewinnt der Chemieproduzent wertvolle Informationen über die Anlage, die sich beim Kunden im operativen Einsatz befindet. Dank des Digital Twins kann das Unternehmen Rückschlüsse auf die Nutzung der Produkte, den Verbrauch der Chemikalien, den Einsatz unterschiedlicher Produktarten und mögliche auftretende Probleme ziehen. Das erweitert nicht nur das Know-how des Produzenten und eröffnet die Möglichkeit zur Entwicklung neuer Geschäftsideen sowie zielgerichteter Marketing- und Vertriebsstrategien. In erster Linie kann das Unternehmen seinen Kunden einen proaktiven Service und Support anbieten, der drohende Störungen verhindert und einen ressourcen- und damit kostenschonenden Einsatz der Chemikalien zulässt. Darüber hinaus profitiert die Planung der Produktionskapazitäten vom digitalen Zwilling: Die Informationen zum kumulierten Verbrauch der Chemieprodukte durch die Regelungstechnik ermöglichen belastbare Prognosen zum künftigen Bedarf.
Das könnte Sie auch interessieren:
Warum Digitalisierung (endlich) die Fabriktore verlassen muss
Ist die Industrie auf dem Weg zur digitalen Exzellenz?
Immer die beste Lösung: Equipment as a Service

Dr. Sebastian Heger ist Solution Specialist bei tresmo in Augsburg. Zuvor sammelte er als Projekt- und Teamleiter bei der Projektgruppe Wirtschaftsinformatik des Fraunhofer-Instituts für Angewandte Informationstechnik FIT Erfahrungen an der Schnittstelle von Forschung und Praxis. Er hat Wirtschaftsinformatik an der Universität Augsburg studiert und zur Gestaltung soziotechnischer Informationssysteme promoviert. Foto: tresmo