Digitale Geschäftsprozesse zum Greifen nahe
„Data-driven Enterprise“ ist bei einem oberpfälzischen Präzisionsteilefertiger nicht nur eine Vision, sondern fester Bestandteil des Tagesgeschäfts. Moderne Softwaretools bieten hierfür zukunftssichere Lösungen. So lassen sich die ehrgeizigen Ziele des Unternehmens in der Digitalisierung so schnell wie möglich erreichen.
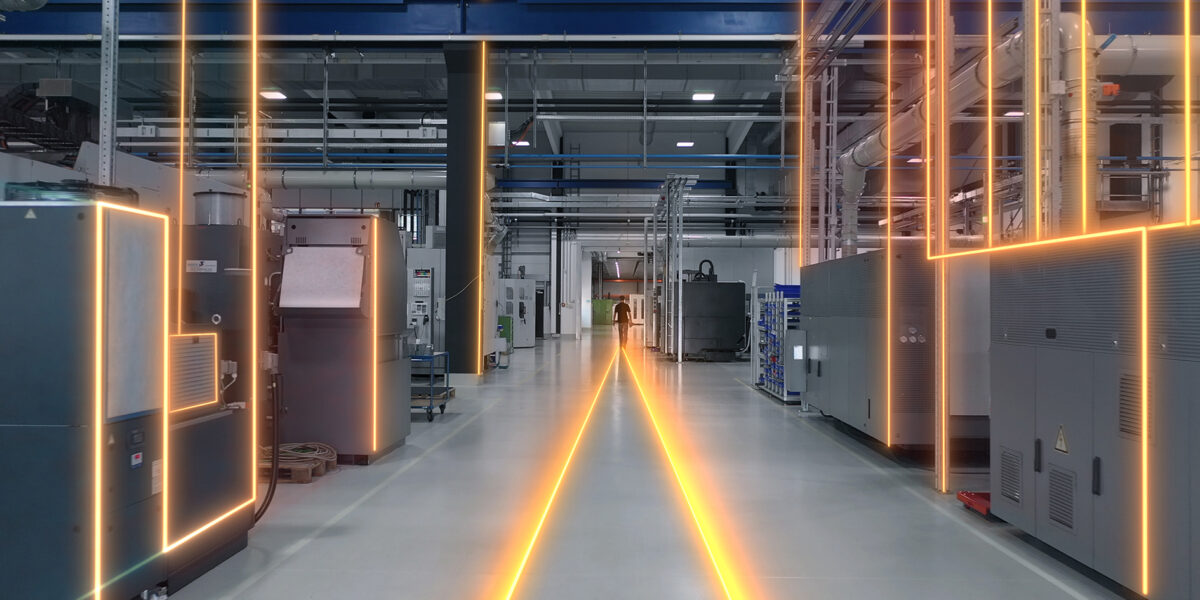
Eine zukunftsfähige, skalierbare Vernetzungslösung für den Shopfloor hat SK Technology an seinen zwei deutschen Produktionsstandorten ausgerollt. Hier entstehen kundenspezifische Präzisionsbauteile an der Grenze des Machbaren mit State-of-the-Art-Technologien. Grafik: Coscom
And the winner is… SK Technology. Der 2024 gewonnene Bayerische Mittelstandspreis reiht sich ein in den Reigen von Auszeichnungen, wie das im Jahr zuvor erhaltenen Zertifikat „Great Place to Work“. Die Ehrungen würdigen die Kreativität sowie die Dynamik in der Betriebsführung von Vater Stefan Kulzer und Sohn Benedikt Kulzer. Der neue Firmenname (seit 2022) trägt dem gewachsenen Leistungsumfang Rechnung, der von der jahrzehntelangen Erfahrung in den Fertigungstechnologien Drehen, Fräsen, Erodieren, Schleifen, Honen sowie Läppen herrührt. Selbst komplexeste Geometrien werden auch bei kleinen Stückzahlen gefertigt. Praktisch alle im DAX vertretenen Industriefirmen werden beliefert – und wenn es sein muss, in kürzester Zeit.
Digitalisierung hebt Fertigung auf neues Level
Als strategischer Partner unterstützt der Lohnfertiger die ambitionierten Zukunftsprojekte seiner Kunden – von der Entwicklung bis hin zur Fertigung von Einzelteilen, Prototypen und Serien. Die beiden Standorte Roding und Waldmünchen in der bayerischen Oberpfalz zeichnen sich durch eine hohe Fertigungstiefe aus. In der Zerspanung gehören CNC-Drehen, -Fräsen, Senk- und Drahterodieren, Rund-, Flach- und Profilschleifen zu den Hauptdisziplinen. Moderne Messmaschinen stellen eine Maßhaltigkeit bis zu 30 nm sicher. 330 Mitarbeitende garantieren mit insgesamt 125 Maschinen und 300.000 Fertigungsstunden eine hohe Liefertreue. Das Team ist erfrischend jung, denn das Durchschnittsalter der Mitarbeitenden liegt bei 34 Jahren, an dem die 42 Auszubildenden natürlich ihren Anteil haben.
Vor gut vier Jahren rückte das Thema Sauberkeit in der Fertigung in den Vordergrund (Stichwort „High-Purity Fertigung“). Seitdem stehen nicht nur die geometrischen Bauteil-Toleranzen im Fokus der Qualitätssicherung, sondern auch die Sauberkeitstoleranzen. Flecken auf Bauteilen sollen im Fertigungsprozess nicht abgereinigt werden, diese dürfen grundsätzlich nicht entstehen. Reinraumcharakter und damit verbunden höchste Ansprüche, werden auch an die Digitalisierung gestellt – gefordert wird Spitzenklasse: „Wir sind auf allen Ebenen durchdigitalisiert. Digitale Zwillinge sind bei uns überall anzutreffen: Beim Gebäudemanagement, bei den Maschinen, bei den Werkstücken und bei den Zerspanungs-Werkzeugen. Wir versuchen, auch die komplexesten Prozesse zu automatisieren. Daher ist das ECO-System von Coscom unsere essenzielle Basis. Der Anbieter ist einer der wichtigsten Partner in unserem Netzwerk“, sagt Benedikt Kulzer, Geschäftsführer der SK Technology.
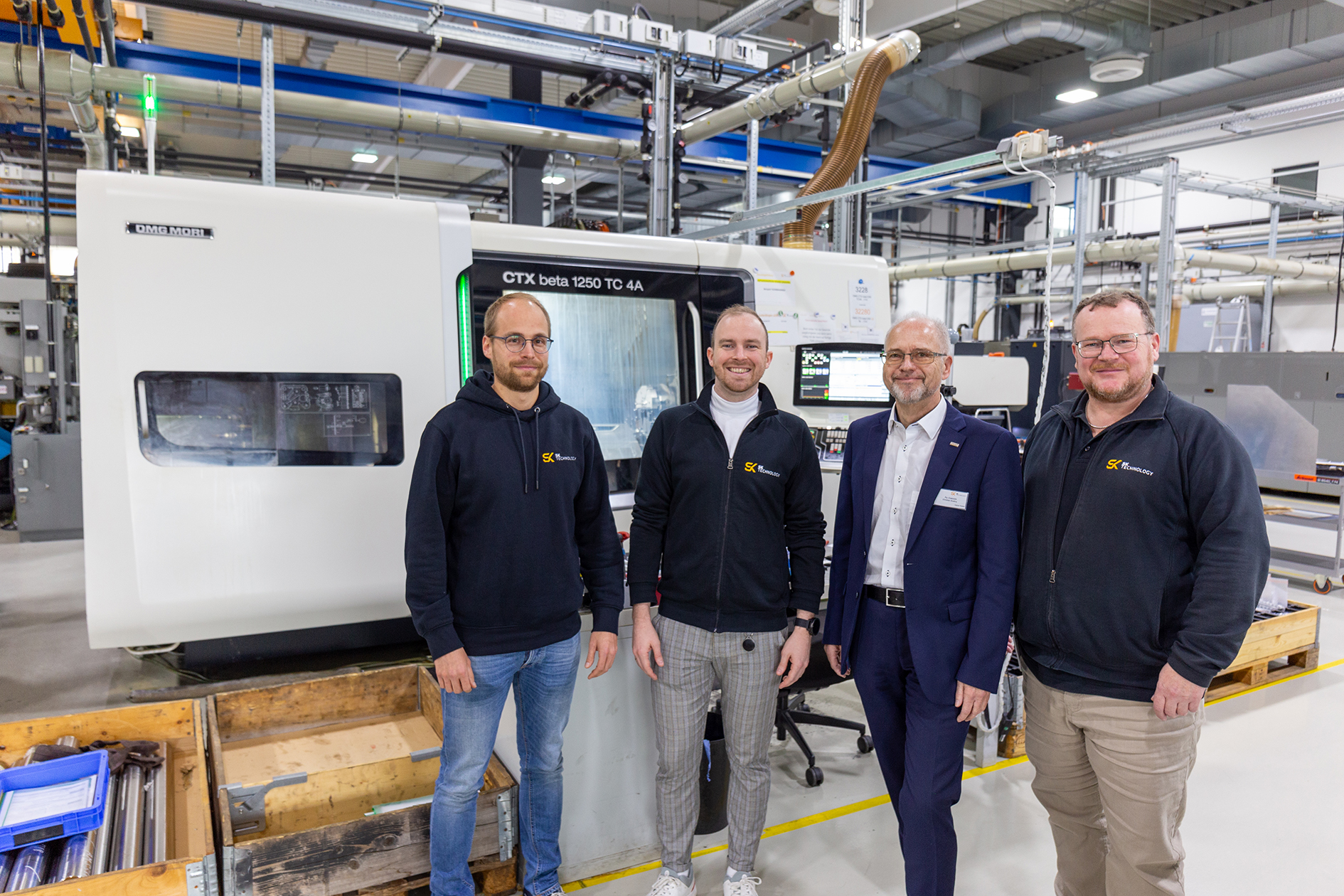
Ziehen am gleichen Strang im Sinne der durchgängigen Digitalisierung vom ERP bis an die Maschinen: Andreas Gruber (Coscom-Key-User), Benedikt Kulzer (Geschäftsführer), Christian Snetivy (Coscom Area-Manager) und Robert Heitzer (Leiter CAD/CAM-Programmierung, von rechts nach links).
Foto: Coscom
Von der Expertise der Coscom Computer GmbH aus Ebersberg bei München ist der Geschäftsführer vollständig überzeugt. Soll beispielsweise nach drei Jahren ein Wiederholteil auf einen Mikrometer genau in Serie gefertigt werden, so sind auf Knopfdruck die erforderlichen Informationen immer online-aktuell verfügbar.
Fünfzehn Jahre am gleichen Strang ziehen
Bereits 2009 wurde am Standort Roding mit großer Akribie eine Werkzeugdatenbank von Coscom eingeführt. Im zweiten Schritt folgte die Installation einer text- und regelbasierte Vernetzungslösung eines Dritt-Anbieters zwischen der Technischen Arbeitsvorbereitung (TAV) und dem Shopfloor. Diese heterogene Lösung, die zwischenzeitlich in die Jahre gekommen war, wurde durch das homogene „ECO“-System abgelöst. Eine umfangreiche Systempartner-Evaluierung führte zur Entscheidung für das System von Coscom als offene, integrative Systemplattform. Neben dem großen Funktionsumfang überzeugten unter anderem auch die Zukunftssicherheit, der modulare Aufbau sowie die Ausbaufähigkeit. Zum „Proof of Concept“ wurde ein Testlauf durchgeführt – die damit verbundenen Projektziele wurden alle erreicht und sogar noch übertroffen.
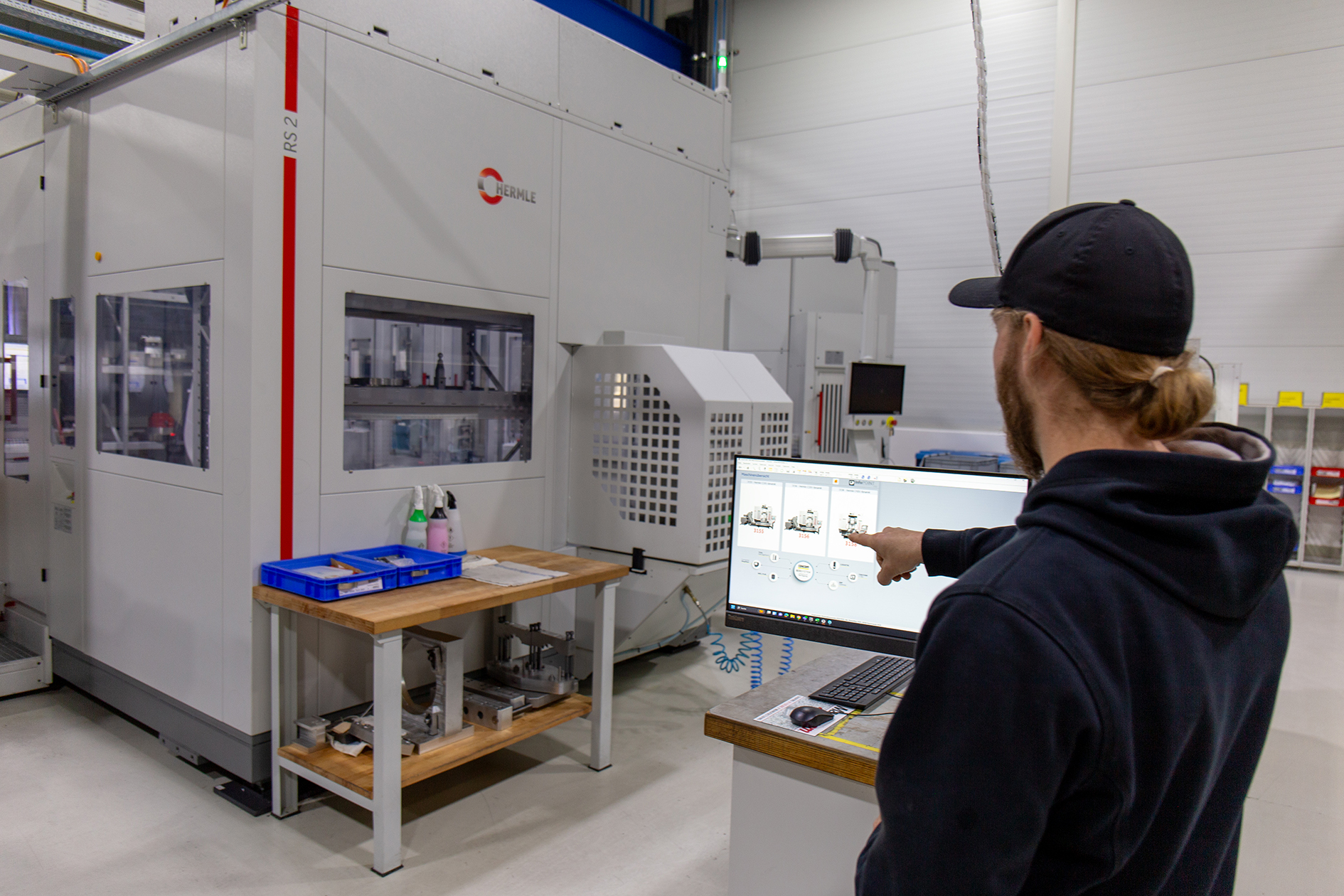
Etwa 25 NC-Programme werden am Tag für die Werkzeugausgabe freigeschaltet. Alle zugehörenden Fertigungsinformationen lassen sich an den InfoPoint-Terminals in unmittelbarer Nähe der Bearbeitungszentren aufrufen.
Foto: Coscom
Die Aufgabenstellung für das ECO-System bei SK Technology lautete:
- Datenversorgung und Vernetzung von drei unterschiedlichen CAM-Systemen, dem Werkzeugvoreinstellgerät und den NC-Maschinen,
- Datenmigration aus dem Alt-System samt Datenbereinigung,
- flexible Prozessgestaltung von Losgröße-1-Fertigung bis hin zu Serienteilen,
- online-aktuelle Visualisierung der Fertigungs-Informationen direkt an den NC-Maschinen,
- · digitale Abbildung des gesamten Werkzeugkreislaufs,
- nachhaltige digitale Unterstützung bei der Anwendung im Fertigungsprozess.
Ein Digital Native im B2B-Umfeld
Vor der endgültigen Systemauswahl hatte SK Technology die internen Shopfloor-Prozesse durchleuchtet. Der Fertigungsbetrieb versteht sich als eine Art „Digital Native im B2B-Umfeld“ und will digitale Prozesse auf die gesamte Firma ausweiten. „Bereits beim ersten Anlauf soll ein Bauteil perfekt gefertigt werden können. Das verlangt, dass das Fachwissen der Mitarbeiter digital abgebildet und mit einem intelligenten Tabellenbuch verschmolzen wird“, sagt der Geschäftsführer und bringt hierzu künstliche Intelligenz als Enabler-Technologie ins Spiel. Aber der Weg ist lang: „Problematisch ist, dass jeder unserer Partner, seien es nun die Steuerungs- oder Maschinenhersteller, ihre eigene digitale Lösung aufbauen will. Dies macht es uns schwer, allgemeine Anwendungsfälle als kleinsten gemeinsamen Nenner zu finden“, gibt Benedikt Kulzer zu bedenken. Er fügt hinzu: „Es kann nur dann ganzheitlich digitalisiert werden, wenn alle Bausteine zusammenpassen.“
Christian Snetivy, Area-Manager beim Shopfloor-Vernetzer, erläutert: „Wir loten stets die Grenzen des Machbaren im Sinne des Kundennutzens aus, um prozessfähige und zukunftssichere Integrationslösungen zu realisieren. Bei allem Ehrgeiz, die optimale Digitalisierungslösung für eine spezielle Kundenanforderung zu entwickeln, ist Coscom stets darauf bedacht, die Update-Fähigkeit der Lösung zu garantieren. Neu entwickelte Lösungen werden in den eigenen ,Standard‘ integriert.“ Snetivy nennt als Beispiel die Istdaten-Übertragung zu den Maschinen: „Für den Anwender ist es immer der gleiche Ablauf: Die montierten Komplettwerkzeuge werden auf dem Zoller-Werkzeugvoreinstellgerät vermessen. Die Lösung generiert aus den Messdaten das jeweilige Steuerungsformat und dieses wird an die Maschinen weitergegeben. Für die Übertragung werden verschiedene Technologien genutzt. Das reicht von einem üblichen File-Copy über OPC-UA bis hin zu spezifischen Hersteller-Technologien, wie z.B. Heidenhain, wo direkt auf die ToolTable zugegriffen wird. Das heißt: ein Prozess, drei unterschiedliche Kommunikations-Technologien.“
Zentrale Versorgung von drei CAM-Systemen mit den gleichen Werkzeugdaten
Robert Heitzer leitet die CAM-Programmierung und sein Kollege Andreas Gruber ist Key-User des ECO-Systems beim Lohnfertiger. Neben FactoryDirector VM, ToolDirector VM und InfoPoint VM sorgen die drei CAM-Systeme hyperMill, Mastercam und TopSolid sowie ein Zoller-Werkzeugvoreinstellgerät für Effizienz und Fertigungsqualität im Shopfloor. „Unsere drei CAM-Systeme und die NC-Simulationssoftware Vericut verlangen jeweils spezielle Formate der Werkzeugdaten. Diese Aufgabe erledigt der ToolDirector VM. Der Anwender legt die Stammdaten nur einmal in der höchst möglichen Qualität an“, sagt Robert Heitzer zufrieden.
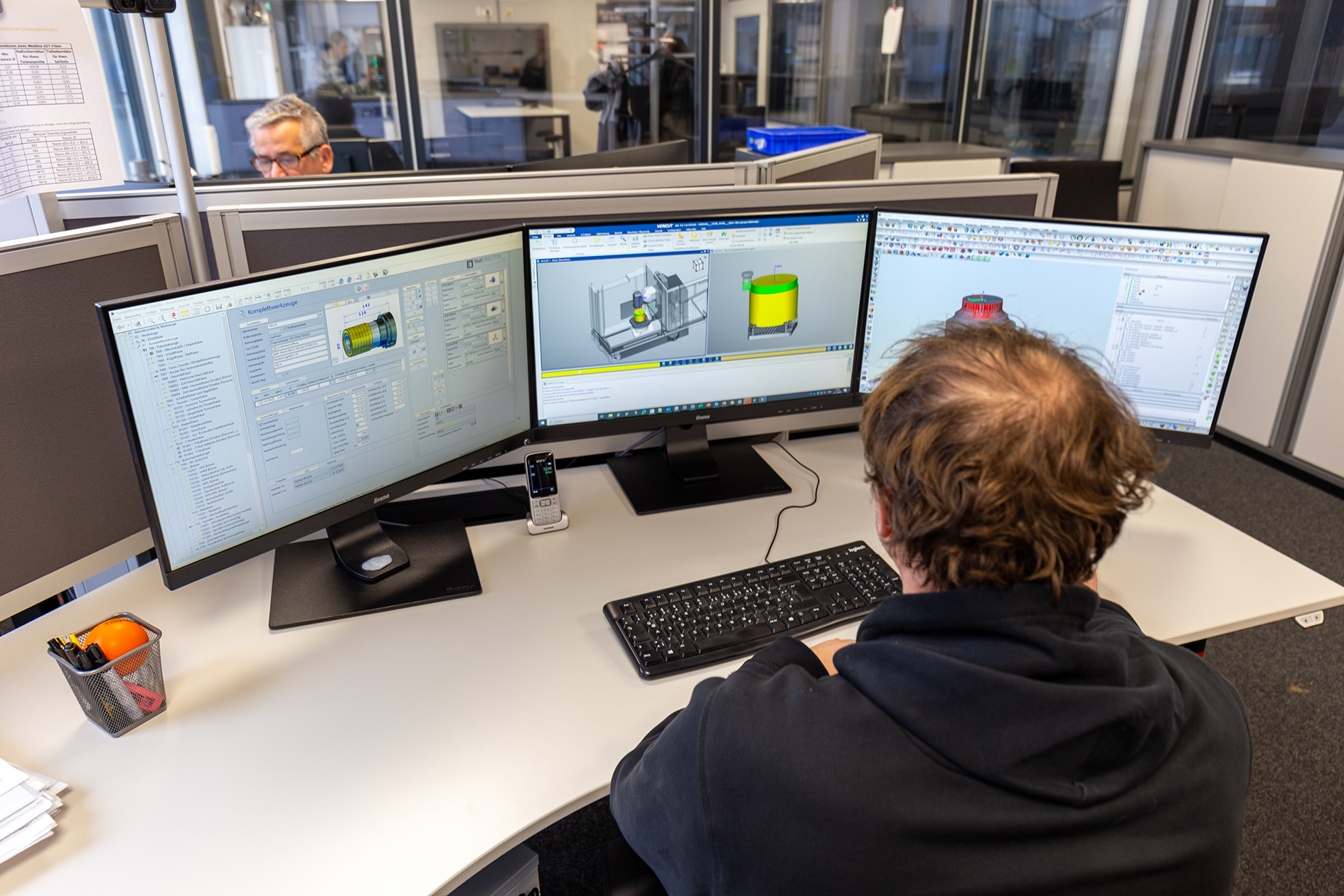
Die technische Arbeitsvorbereitung programmiert mit den drei CAM-Systemen hyperMill, Mastercam und TopSolid. Die individuellen Werkzeugdaten erhalten sie mittels TCI-Technologie über ToolDirector VM.
Foto: Coscom
Das Tool Data Cooperation Interface (TCI) erzeugt die spezifischen Informationen für den Einsatz im jeweiligen Zielsystem, z.B. für die unterschiedlichen CAD/CAM-Systeme. Diese Werkzeugdaten nutzt, neben der Programmier-Abteilung, auch die Technische Auftragsvorbereitung als Montagevorschrift der physischen Komplettwerkzeuge. Jedes komplette Werkzeug ist über eine separate ID-Nummer eindeutig gekennzeichnet. Aufgrund dieser ID können die digitalen Komplettwerkzeuge im gesamten Fertigungsbereich eindeutig identifiziert werden. An den InfoPoints lassen sich diese Werkzeugdaten bei Bedarf im Shopfloor abrufen.
Nach der Bearbeitung findet in der Technischen Arbeitsvorbereitung nicht nur die physische, sondern auch die virtuelle Demontage der Komplettwerkzeuge statt. „Dadurch ist auch digital der Werkzeugkreislauf geschlossen“, erklärt Andreas Gruber. Die Fertigungsdokumentation, einschließlich der generierten NC-Programme, steht online-aktuell zur Verfügung.
Beachtliches Wachstum an geprüftem Datenbestand
Im Durchschnitt werden pro Tag circa 25 Fräs-Programme für die Werkzeugausgabe freigeschaltet. Für Drehprozesse sind es etwas weniger, dort werden mehr Serienteile gefertigt (sechs bis acht Programme pro Tag). Rechnet man die Dummy-Programme ein, werden täglich zwischen 45 bis 50 Programme über das ECO-System organisiert. Pro Jahr werden an die 3.000 Artikel in der zentralen Datenbank angelegt. Dabei kann ein Bauteil aus mehreren NC-Programmen bestehen, wenn zum Beispiel bei der Bearbeitung verschiedene Aufspannungen erforderlich sind. Insgesamt entstehen aufs Jahr hochgerechnet 1.000 Programme für Drehen und 3.500 für das Fräsen. Zusätzlich kommen noch Erodierprogramme und künftig auch Qualitätssicherungsprogramme sowie Schleifprogramme hinzu.
Alle diese „Digital Assets“ dienen als Grundlage für die Definition der digitalen Geschäftsprozesse. Andreas Gruber setzt die genannten Zahlen in Relation: „Wir hatten mehr als 65.000 Datensätze in den Altsystemen, in der neuen Datenplattform sind es derzeit 12.600. Während der Datenmigration haben wir uns von Datensätzen getrennt, weil diese nicht mehr benötigt wurden. Wir haben bisher 13.200 Zusammenbauvarianten (Komplettwerkzeuge) von den rund 9.000 Werkzeugeinzelkomponenten angelegt.“
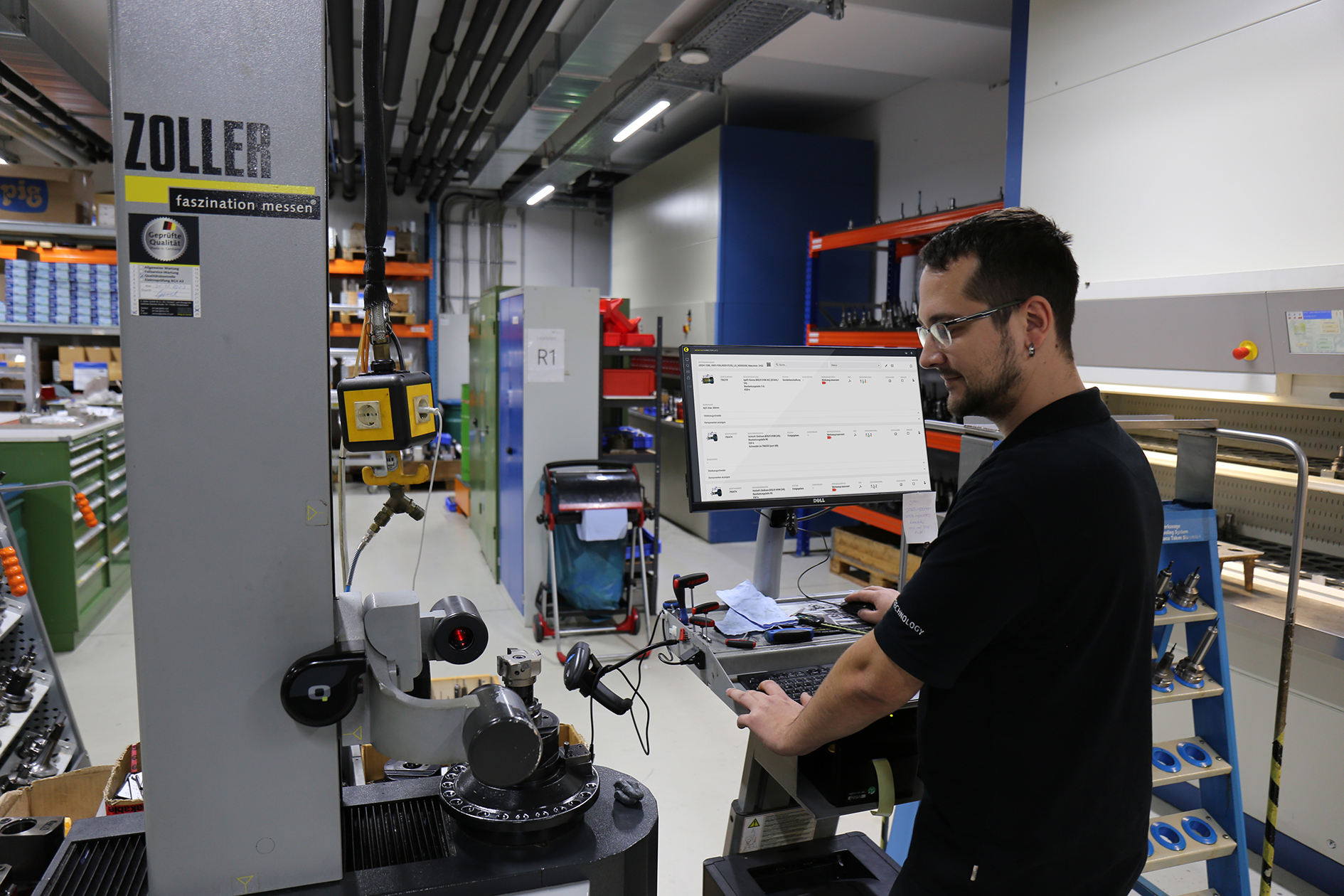
Das Zoller-Werkzeugvoreinstellgerät ist zum Ist-Datenabgleich mit den NC-Maschinen prozesssicher in das ECO-System integriert. 13.200 Zusammenbauvarianten (Komplettwerkzeuge) von 9.000 Werkzeugeinzelkomponenten hat der Betrieb über den ToolDirector bereits im Zugriff.
Foto: Coscom
In regelmäßigen Zeitabständen wird kritisch hinterfragt, ob die „Werkzeug-Favoriten“ tatsächlich noch als solche definiert werden können: „Unser Kundenstamm ändert sich, damit auch die Fertigungsbauteile und das verwendete Material (etwa Aluminium statt nickelbasierte Superlegierungen).“ Die Werkzeugkosten werden kontinuierlich in einer Nachkalkulation analysiert. Auch hier unterstützt das ECO-System. Die darin gesammelten Historieninformationen dienen als Entscheidungskriterium für zukünftige Investitionsentscheidungen im Bereich der Zerspanungswerkzeuge.
Schnelle Reaktionszeit, hohe Kundenzufriedenheit
CAD/CAM-Leiter Robert Heitzer sagt zufrieden: „Coscom befasst sich intensiv mit den Anforderungen und Aufgabenstellungen seiner Kunden. Und auch mit Fragestellungen, die in die Zukunft gerichtet sind. Zum Beispiel, inwieweit eine webbasierte Benutzeroberfläche Vorteile bringen kann. Ich erinnere mich an das positive Feedback auf eine Mitarbeiterbefragung zum Einsatz der Web-Apps auf Tablett PCs. Aktuell werden bei uns an einigen Arbeitsplätzen diese Apps für mobile Endgeräte eingesetzt. Sie werden von Coscom stets weiterentwickelt.“ Im vierzehntäglichen Turnus fanden Projekt-Abstimmungsgespräche statt. Beispielsweise ist das „Kunststück“ gelungen, eine perfekt arbeitende, bidirektionale Schnittstelle zum Zoller-Voreinstellgerät zu realisieren. Auch geänderte Messstrategien am Voreinstellgerät in der Werkzeugausgabe lassen sich an die Bearbeitungszentren verlässlich übermitteln. „Wir haben das Werkzeug-Voreinstellgerät prozessfähig ins ECO-System eingebunden. In der Benutzeroberfläche des Geräts ist ein Button zu finden, der ,Coscom‘ lautet. Damit lassen sich alle Messungen und Einstellungen mit einem Knopfdruck in das ECO-System übertragen und an die Datenempfänger verteilen“, erklärt Area-Manager Christian Snetivy.
Fazit: Auch der zweite Standort profitiert von der Digitalisierung
Die Erfolgsstory geht weiter: Auch am zweiten Standort der SK Technology, in Waldmünchen, wird inzwischen das ECO-System „ausgerollt“. Dieser Standort ist bereits mit dem Firmensitz in Roding vernetzt, sodass prozesssicher auf das zentrale System zugegriffen werden kann. „Unser Systemintegrator hat das Ziel, die Wertschöpfung im Zerspanungs-Prozess seiner Kunden zu optimieren, um damit die Konkurrenzfähigkeit sicherzustellen. Dies hat nicht zuletzt zur Folge, dass die Arbeitsplätze dadurch im DACH-Raum erhalten bleiben“, resümiert Christian Snetivy.
Das könnte Sie auch interessieren:
Wer darf an die Maschine? – Zugangsberechtigung mittels KI-Gesichtsunterscheidung
KI-basierte Symbol- und Texterkennung zur Automatisierung der Arbeitsplanung
Process Mining: Mit datengestützten Einblicken zu mehr Transparenz