Dreidimensionale Faserverstärkung in additiv gefertigten Kunststoffbauteilen
Additive Fertigungsverfahren erfreuen sich einer großen Beliebtheit, insbesondere zur Herstellung von Einzelteilen und Kleinserien. Sie werden jedoch zunehmend auch dann eingesetzt, wenn das Ziel der Auslegung die Massereduktion bei gleichzeitiger Wahrung der mechanischen Bauteileigenschaften ist. Beispiele hierfür sind topologieoptimierte, metallische Tragstrukturen.
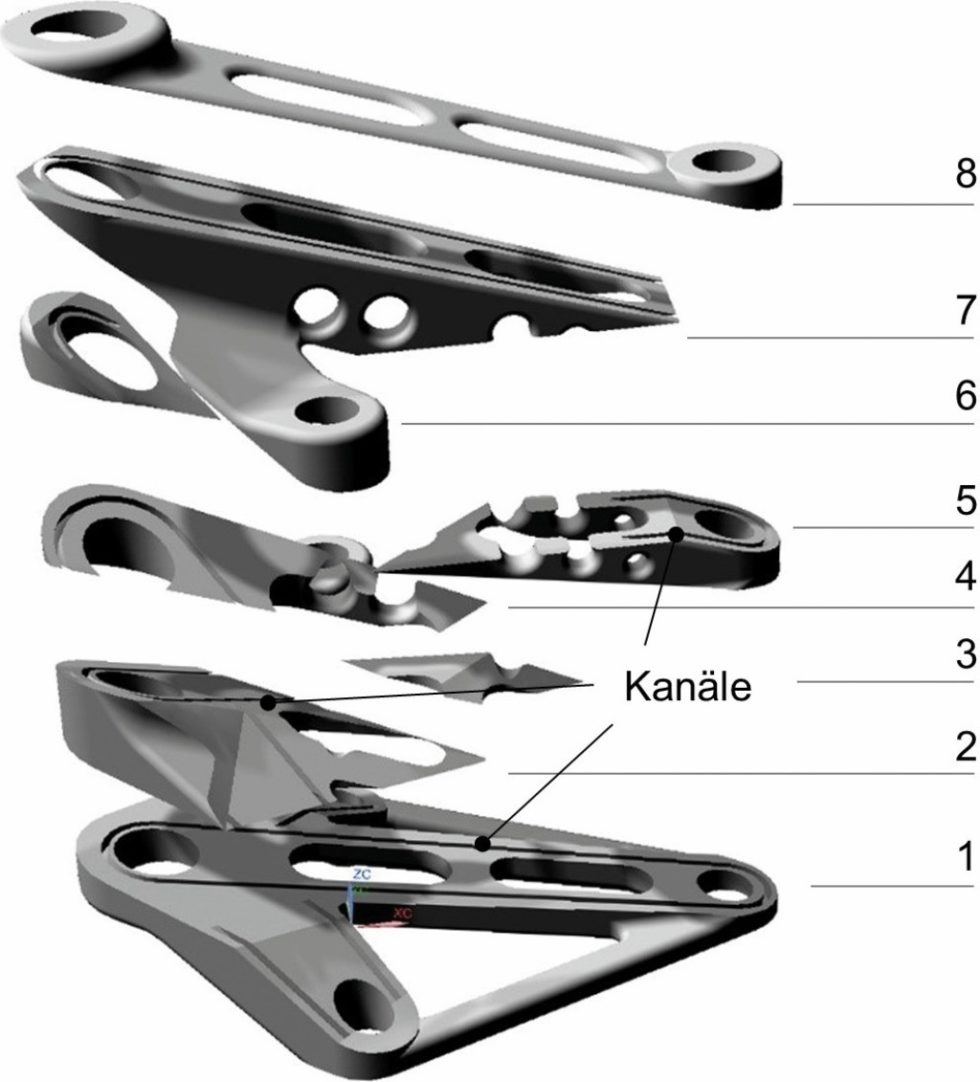
Aufteilung des Labormusters für das erweiterte Fused Deposition Modelling (FDM) mit UD-Faserverstärkungen. Bild: CFK Nord
Diese nutzen den mechanisch isotropen Ausgangswerkstoff nur in belastungsrelevanten Bereichen nutzen [1]. Eine weitere Massereduktion ist dann möglich, wenn Werkstoffe mit exzellenten gewichtsspezifischen Steifigkeiten und Festigkeiten eingesetzt werden. Da diese Werkstoffe zumeist anisotrope Materialeigenschaften haben, ist deren optimale Ausnutzung nur durch eine exakte Ausrichtung entlang der Lastpfade möglich. Im Bereich der Faserkunststoffverbunde bieten Fertigungstechnologien wie das „Automated-Fiber-Placement“ prinzipell Lösungen für die lastpfadorientierte Materialablage. Diese ist allerdings bisher nur in annähernd ebenen Strukturen umsetzbar. Die Herausforderung besteht zukünftig darin, die Ablage von Verstärkungsfasern im dreidimensionalen Raum möglich zu machen und somit die Voraussetzung zur Herstellung topologieoptimierter Tragstrukturen unter Ausnutzung der gewichtspezifischen Vorteile anisotroper Werkstoffe zu schaffen.
Ausgangssituation
Faserverbundwerkstoffe setzen sich zunehmend als Konstruktionswerkstoff für hochbeanspruchte Leichtbauanwendungen durch. Dies gilt insbesondere für endlos-kohlenstofffaserverstärkte Kunststoffe. Das Leichtbaupotential dieser Werkstoffe kann vor allem dann ausgeschöpft werden, wenn Beanspruchungen im Bauteil in einer Raumrichtung besonders dominant ausfallen. Für eine optimale Ausnutzung der Eigenschaften von Faserkunststoffverbunden (FVK) ist daher eine kraftflussgerechte Orientierung der Verstärkungsfasern notwendig [2].
Verbreitete Fertigungstechnologien im Faserverbundleichtbau, die einen überwiegend schichtweisen Aufbau von textilen Einzellagen vorsehen, erlauben allerdings nur eine eingeschränkte Ausrichtung der Verstärkungsfasern entlang der Kraftflüsse. Ein Beispiel hierfür sind Automated-Fiber-Placement (AFP)-Prozesse [3–6]. Verfahrensbedingt ist bei ihnen der Gestaltungsraum von endlosfaserverstärkten Bauteilen eingeschränkt. Demzufolge kann der ressourcen- und gewichtseffiziente Einsatz von Verstärkungsfasern in kraftflussgerecht ausgestalteten Faserverbundstrukturen bisher nicht gewährleistet werden.
Die im Folgenden behandelte Studie befasst sich mit einem Verfahren, in dem eine Kopplung von AFP-Technologien und deren Materialien mit der Methode des Schmelzschichtens (Fused Deposition Modeling – FDM) prototypisch umgesetzt wurde. Damit sollen die Verstärkungsfasern frei und beanspruchungsgerecht in ein dreidimensionales Bauteil eingebracht werden. Anhand eines Labormusters wird in einer numerischen und experimentellen Analyse das endlosfaserverstärkte Strukturkonzept den konventionell kurzfaser- und unverstärkten Kunststoffstrukturen auf Polyamidbasis gegenübergestellt.
Charakterisierung der Halbzeuge
Zunächst wurden vorbereitend auf die Simulations- und Fertigungsstudie die einzusetzenden faserverstärkten Polyamid-Halbzeuge lichtmikroskopisch und mechanisch charakterisiert.
Faserverteilung, Fehlstellen
Bild 1 (a) zeigt den Querschliff des kurzfaserverstärkten PA6.6-Filaments. Die Kurzfasern sind mit einem Faservolumenanteil von circa 20 % gleichmäßig verteilt und aufgrund des Herstellungsprozesses überwiegend in Längsrichtung des Filaments ausgerichtet. Es sind keine Lufteinschlüsse zu erkennen.
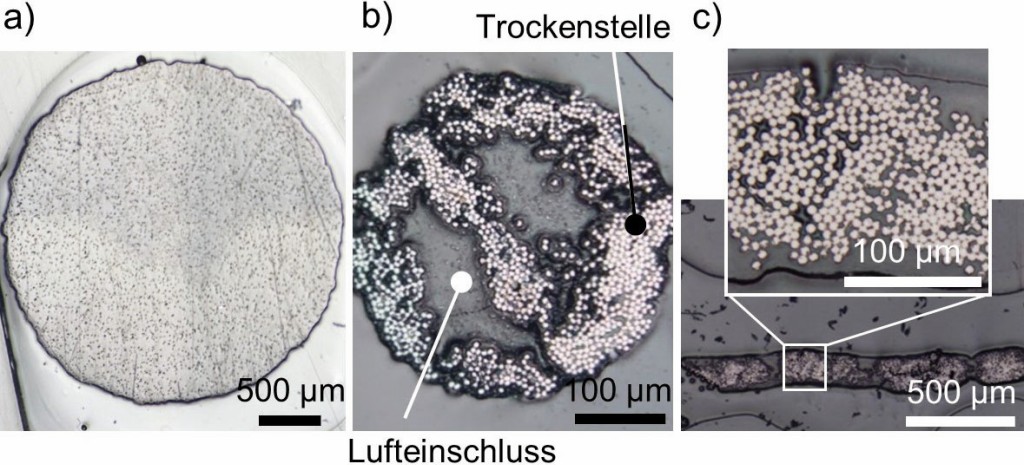
Bild 1. FDM-Filament in kurzfaserverstärktem PA6.6 (a); im unidirektional faserverstärktem PA6.6 sind Lufteinschlüsse und Trockenstellen im Filament zu sehen (b); sowie industrielles „Prepreg-Tow“ mit PA6-Matrix (c). Bild: CFK Nord
Bild 1b zeigt den Querschliff eines unidirektional (UD) faserverstärkten PA6.6-Filaments. Dieses ist, wie auch das kurzfaserverstärkte Halbzeug, speziell für FDM entwickelt worden. Neben der deutlich erkennbaren Trockenstelle enthält das Filament Lufteinschlüsse. Eine mögliche Begründung hierfür könnte der Herstellprozess des Halbzeugs sein. Aufgrund der Faserverteilung im Querschnitt wird angenommen, dass diese aus einem flachen Ausgangsmaterial ähnlich einem Prepreg-Tow (Bild 1c) resultiert, das durch Umformung in eine runde Querschnittsgeometrie überführt wurde.
Die erreichbaren mechanischen Eigenschaften der im FDM hergestellten Kunststoffbauteile hängen erheblich von der Anbindung zwischen den Einzelschichten sowie von der Druckrichtung ab. Bei faserverstärkten Filamenten wirkt sich zusätzlich die Haftung zwischen Thermoplast und Verstärkungsfaser auf das Verhalten unter Belastung aus. Zur Bewertung der verschiedenen Materialien und Materialkombinationen wurden UD-kohlenstofffaserverstärkte (UD-CF) sowie un- und kurzfaserverstärkte PA6.6-Couponproben – angelehnt an die DIN EN ISO 527 – mechanisch charakterisiert.
Steifigkeit und Festigkeit
Die Ergebnisse von Steifigkeit und Festigkeit sind in Bild 2 gegenübergestellt.
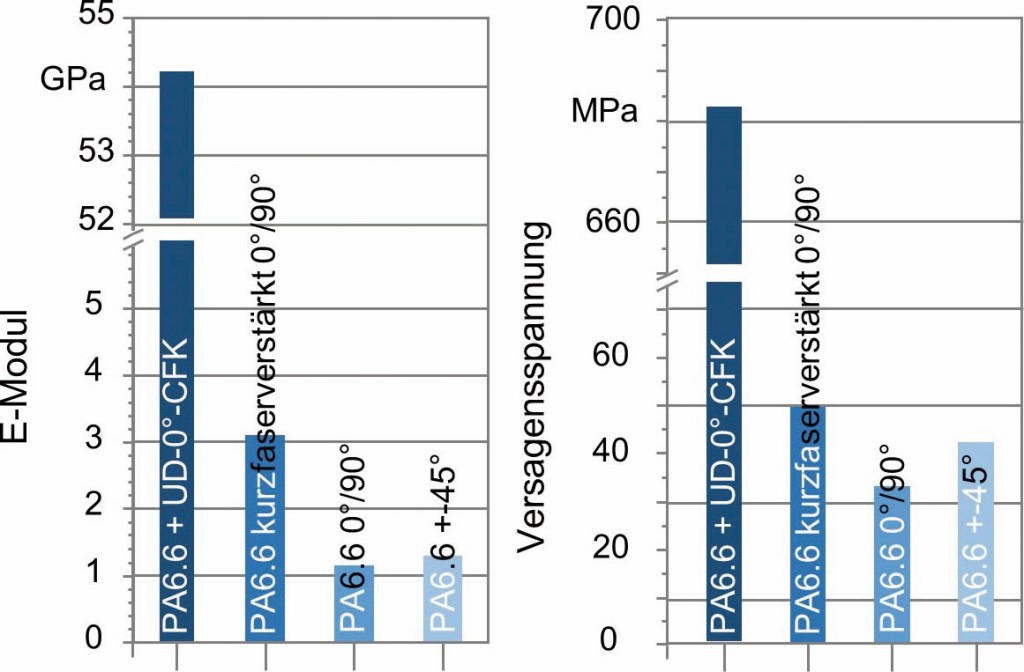
Bild 2. E-Modul und Versagensspannung von Nylon (PA6.6) für verschiedene Faserverstärkungstypen und Druckrichtungen (0°/±45°/90°). Bild: CFK Nord
Die Werte des UD-CF-PA6.6 zeigen, dass durch den Einsatz einer geeigneten Verstärkungsfaser eine deutliche Erhöhung sowohl der Steifigkeit als auch der Festigkeit in Faserrichtung erreicht werden kann. Während die Kurzfaserverstärkung mit einem Faservolumenanteil von circa 20 % bereits mit 3,1 GPa doppelt so steif ist wie die unverstärkte Probe, liegt die Steifigkeit der Probe mit circa 35 % Anteil an UD-Fasern mit 54 GPa erwartungsgemäß deutlich darüber.
Die gezeigten Verstärkungseffekte können in diesem Maße allerdings nur erreicht werden, wenn die Endlosfasern ausreichend an den Matrixwerkstoff angebundenen sind. Es ist zudem zu erkennen, dass bereits die im Prozess gewählte Druckrichtung einen Einfluss auf die mechanischen Kennwerte hat. Die in ± 45° orientierten Druckbahnen führen zur Verbesserung von E-Modul und Versagensspannung um 14 % beziehungsweise 28 % im Vergleich zur 0/90°-Orientierung.
Fertigung eines Labormusters im erweiterten FDM-Verfahren
Im nächsten Schritt wurde zur Analyse der verstärkenden Eigenschaften der Kohlenstofffasern in Bauteilen mit dreidimensionalem Beanspruchungszustand das in Bild 3 gezeigte Labormuster eines Beschlags entworfen und gefertigt.
Dessen Geometrie sieht eine Lasteinleitung, die parallel zur Befestigungsebene verschoben ist, sowie eine feste Anbindung an die Befestigungsebene über drei Punkte vor. Die Proben wurden in drei unterschiedlichen Materialkonfigurationen gefertigt: unverstärktes PA6.6, kurzfaserverstärktes PA6.6 und unverstärktes PA6.6 mit zusätzlichen, in Richtung der Beanspruchung orientierten UD-CF-Schlaufen.
Die ersten beiden Bauteilvarianten konnten im konventionellen FDM hergestellt werden. Um die Proben mit UD-Faserverstärkung herzustellen, wurden in der Geometrie Kanäle für die Schlaufen vorgesehen und die Geometrie in acht Teilgeometrien aufgeteilt.
Zwischen den einzelnen Teilgeometrien wird der Prozess kurzzeitig unterbrochen; die thermoplastischen Prepreg-Tows werden manuell in die dafür vorgesehenen Kanäle mehrlagig schlaufenförmig eingelegt und anschließend die einzelnen Lagen durch lokales Aufschmelzen stoffschlüssig mit dem gedruckten PA6.6-Grundkörper verbunden, Bild 4.
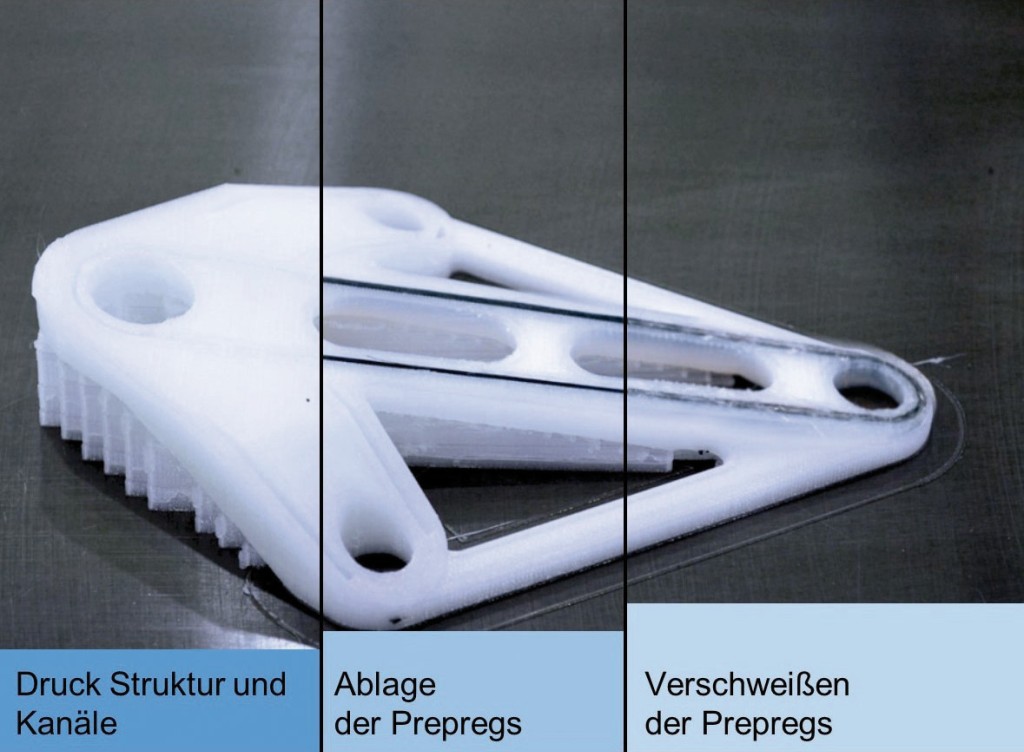
Bild 4. Phasen der Herstellung eines Kunststoffbauteils mit dreidimensional verlaufenden UD-Kohlenstofffaserverstärkungen. Bild: CFK Nord
Daraufhin wird der Druck fortgesetzt.
Da der Prozessschritt des Schweißens bisher weder automatisiert noch hinsichtlich seiner Qualität überprüft werden kann, wird für die weiteren Betrachtungen davon ausgegangen, dass es zu keiner vollkommen fehlerfreien Verbindung zwischen den Schweißpartnern kommt. Insgesamt wurden auf diese Weise vier Schlaufen in das Bauteil integriert.
Im Beispiel wird somit – bei einem Faservolumenanteil des Halbzeugs im Bauteil von 60 % – ein Fasergesamtanteil von 2,9 % erreicht. Der Gewichtsvergleich zeigt, dass die unverstärkte und die UD-faserverstärkte Varianten mit 106 g identisch schwer sind, wohingegen die kurzfaserverstärkte Version durch den höheren Gesamtfaseranteil 113 g wiegt und damit circa 7 % schwerer ist.
Ergebnisse der mechanischen Prüfung im Vergleich zur Simulation
Bild 5 (a) zeigt den Versuchsaufbau in der Zugprüfmaschine und exemplarisch die Dehnungsverteilung sowie das Versagen der UD-faserverstärkten Probe in (b) und (c).

Bild 5. Mechanische Prüfung des Labormusters (a), 3D-Dehnungszustand unter Belastung (b) sowie versagte Probe mit UD-Faserverstärkung (c). Bild: CFK Nord
Die Probenkörper wurden gemäß ihrer Auslegung parallel zur Befestigungsebene zunehmend auf Zug belastet. Das Standbild der oberflächigen Dehnungsanalyse zeigt die Hauptbelastung im oberen Teil der mittleren Verstärkungsstrebe. Dennoch versagt die Probe im unteren Teil, was auf ein Versagen der im Inneren liegenden Verstärkungsfasern hindeutet. Dies zeigt auch, dass eine Oberflächenanalyse bei dieser Verstärkungsform nicht mehr ausreichend ist, um den Ort des Versagens vorherzusagen.
Zugprüfung
Bild 6 zeigt die im Zugversuch ermittelten Kraft-Wegverläufe für die drei Materialkonfigurationen.

Bild 6. Vergleich experimentell und simulativ ermittelter Kraft-Weg-Diagramme der belasteten Labormuster. Bild: CFK Nord
Wie schon bei den Couponproben zu erkennen, bewirkt die Faserverstärkung auch im 3D-Labormuster die erwartete Verbesserung. Die unverstärkten Proben versagen im Bereich der Krafteinleitung, wohingegen das Endversagen der faserverstärkten Proben im Verbindungsstück zwischen Krafteinleitungspunkt und dem mittleren Befestigungspunkt stattfindet (Bild 5c). Hierbei ist festzuhalten, dass es zu keinem Versagen von Grenzschichten der im FDM-Prozess gefertigten Bereiche kommt.
Die Kurzfaserverstärkung erreicht Steifigkeiten mit einem ähnlichen Niveau wie die Endlosfaserverstärkung, verhält sich allerdings bereits für geringe Lasten nichtlinear.
Finite-Elemente-Analyse
Parallel zum Experiment wurden die drei Materialkonfigurationen in einer Finite-Elemente-Simulation untersucht. Die Simulation wurde linear in „Abaqus“ unter Annahme idealer Materialanbindungen durchgeführt. Durch die Verwendung der zuvor ermittelten Materialdaten wird der linear-elastische Bereich der un- und kurzfaserverstärkten Proben hinreichend genau durch das numerische Modell abgebildet.
Das plastische Verhalten kann durch das verwendete lineare Modell nicht abgebildet werden. Für die endlosfaserverstärkte Probe sagt das Modell eine um circa 33 % größere Steifigkeit voraus, die im Experiment so nicht beobachtet werden konnte. Diese Diskrepanz zwischen Simulation und Experiment kann neben Modellvereinfachungen insbesondere durch Fertigungsfehler beim händischen Prozess erklärt werden. Da die Proben alle außerhalb der Druckebenen versagen, sind systematische Fehler beim halbautomatischen Druckprozesses hingegen unwahrscheinlich. Somit ist zu vermuten, dass die Hauptabweichung in den nicht im Modell berücksichtigen Grenzflächeneffekten der unterschiedlichen Verstärkungsbereiche zu suchen ist.
Fazit und Ausblick
Sowohl in der Untersuchung der Couponproben als auch am Labormuster konnte gezeigt werden, dass eine in Richtung der Belastung unidirektional faserverstärkte Struktur gegenüber einer gleichmäßig kurzfaserverstärkten deutliche Vorteile bezüglich ihrer mechanischen Kennwerte hat. Es ist zudem davon auszugehen, dass dieses Ergebnis durch Erhöhung des Faservolumenanteils von derzeit lediglich 2,9 % weiter zu verbessern ist.
Der Ablauf des Schädigungsfortschritts während der mechanischen Prüfung hat gezeigt, dass die Orientierung und Ausgestaltung der Faserverstärkung noch nicht optimal auf den Belastungsfall ausgelegt werden konnte. Um hierfür bessere Ergebnisse erzielen zu können, ist eine simulativ unterstützte Optimierung beanspruchungsgerechter Faserpfade im Bauteil sinnvoll. Dabei ist insbesondere die Beeinflussung geometrischer Restriktionen der Fertigungstechnologie zu berücksichtigen.
Die Studie hat gezeigt, dass die Kopplung von AFP-Technologien mit Methoden des FDM grundsätzlich das Potential bietet, komplexe Strukturbauteile mit beanspruchungsgerecht verlaufenden Faserverstärkungen hervorzubringen. Eine der zentralen Herausforderungen besteht in der Technologieentwicklung und einer darauf abgestimmten Methode zur Auslegung der Leichtbaustrukturen.
Literatur:
[1] Eschenauer, H. A.; Olhoff, N.: Topology optimization of continuum structures – a review. Applied Mechanics Review 54 (2001), Nr. 4, S. 331–390.[2] Klussmann, N.; Malik, A.: Lexikon der Luftfahrt. 2. Aufl. Berlin: Springer-Verlag, 2007.[3] Brecher, C.; Werner, D.; Kermer-Meyer, A.; Emonts, M.: Lastoptimale Herstellung. Lightweight Design 5 (2012), Nr. 4, S. 20–25.[4] Crosky, A.; Grant, C.; Kelly, D.; Legrand, X. et al: Fibre placement processes for composites manufacture. In: Philippe Boisse (Hrsg.): Advances in Composites Manufacturing and Process Design. INSA de Lyon/F: Woodhead Publishing, 2015, S. 79–92.[5] Dubratz, M.: Laserunterstütztes Tape Placement Verfahren für die Herstellung dreidimensionaler Strukturkomponenten aus endlosfaserverstärkten thermoplastischen Prepregs. Dissertation, RWTH Aachen, 2014.[6] Denkena, B.; Schmidt, C.; Weber, P.: Automated Fiber Placement Head for Manufacturing of Innovative Aerospace Stiffening Structures. Procedia Manufacturing 6 (2016), S. 96–104.
Dr.-Ing. Carsten Schmidt, Jahrgang 1975, leitet den kooperativen Forschungsstandort der Universitäten Hannover, Braunschweig und Clausthal am CFK Nord in Stade. // Dipl.-Ing. Matthias Behr, Jahrgang 1984, ist wissenschaftlicher Mitarbeiter des Instituts für Fertigungstechnik und Werkzeugmaschinen der Leibniz Universität Hannover am CFK Nord in Stade. // Dipl.-Ing. Jonathan Serna Gonzalez, Jahrgang 1984, ist wissenschaftlicher Mitarbeiter des Instituts für Polymerwerkstoffe und Kunststofftechnik der technischen Universität Clausthal am CFK Nord in Stade. Alexander Herwig, M. Sc., Jahrgang 1987, ist wissenschaftlicher Mitarbeiter des Instituts für Flugzeugbau und Leichtbau der Technischen Universität Braunschweig am CFK-Nord in Stade. // Prof. Dr.-Ing. Berend Denkena, Jahrgang 1959, ist Leiter des Instituts für Fertigungstechnik und Werkzeugmaschinen der Leibniz Universität Hannover. // Prof. Dr.-Ing. Peter Horst, Jahrgang 1954, ist Leiter des Instituts für Flugzeugbau und Leichtbau der Technischen Universität Braunschweig. // Prof. Dr.-Ing. Dieter Meiners, Jahrgang 1956, ist Leiter des Instituts für Polymerwerkstoffe und Kunststofftechnik der Technischen Universität Clausthal.