Kombinierte Prozesskette aus additiven und subtraktiven Fertigungsverfahren
Das „Hybrid Manufacturing“, bei dem subtraktive und additive Fertigungsverfahren miteinander kombiniert werden, wird erst seit wenigen Jahren entwickelt und kaum industriell praktiziert. Diese kombinierte Prozesskette bietet aufgrund der Verbindung der konstruktiven Vorzüge der additiven Fertigung mit den realisierbaren Toleranzen der spanabhebenden Verfahren viel Potential für Anwendungen in der Automobil- und Luftfahrtindustrie sowie der Chemie- und Medizintechnik. Derzeit beschränkt sich die Anwendung des Verfahrens jedoch auf die Entwicklung von entweder Metall- oder Kunststoffbauteilen.
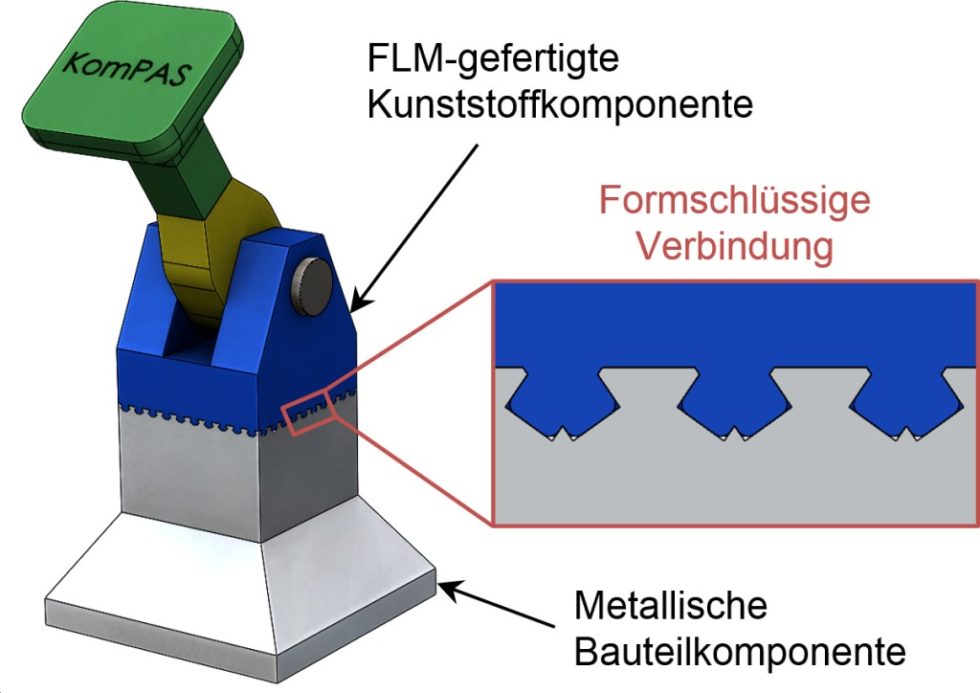
Demonstratorbauteil für die kombinierte Prozesskette. Bild: TU Dortmund
Die Verbindungstechnik zwischen Bauteilkomponenten aus unterschiedlichen Werkstoffen ist beim Hybrid Manufacturing eine zentrale Herausforderung und noch weitgehend unerforscht, wenngleich die Hybridisierung von Bauteilen eine gängige Praxis bei der Produktentwicklung ist.
Eigenschaften und Verbindungstechnik von Multimaterialbauteilen
Multimaterialbauteile zeichnen sich durch die Integration unterschiedlicher werkstoffspezifischer Eigenschaften aus. Aufgrund des hohen Individualisierungsgrads von Systemen – zum Beispiel von Beinprothesen – kommen zur Herstellung von Kunststoffkomponenten immer häufiger flexible additive Fertigungsverfahren wie das Fused Layer Modeling (FLM) zum Einsatz. Zur Bearbeitung hochbelastbarer metallischer Komponenten und zum Beispiel zur Vorbereitung von Schnittstellen sind dahingegen subtraktive Fertigungsverfahren wie das Fräsen zu bevorzugen.
Hybride Bauteilkomponenten müssen anforderungsgerecht verbunden werden. Im Sinne des Leichtbaus und aufgrund anwendungstypischer Lastbedingungen stehen auch in der hier vorgestellten Forschungsarbeit formschlüssige Verbindungen im Fokus. Hierzu ist zunächst zu untersuchen, unter welchen Bedingungen eine formschlüssige Verbindung in einem FLM-Prozess möglichst optimal hergestellt werden kann. Die Belastbarkeit und Zuverlässigkeit einer formschlüssigen Verbindung ist neben einer anforderungsgerechten Auslegung und Konstruktion von einem stabilen Fertigungsprozess und einem ausreichenden Ausfüllen der Verbindungselemente abhängig. Wie eine möglichst gleichmäßige und vollständige Formfüllung erreicht werden kann, ist Gegenstand dieser Forschungsarbeit.
Stand der Technik
Die Prozesshybridisierung von additiven und subtraktiven Fertigungsverfahren wird erst seit einigen Jahren wissenschaftlich untersucht [1;2]. Seither wurde der Stand der Technik zum Beispiel um einen Algorithmus zur Prozessplanung hybrider Wertschöpfungsketten erweitert [3]. Inzwischen bieten verschiedene Hersteller additive Fertigungssysteme zur Verarbeitung pulvermetallurgischer Werkstoffe im industriellen Maßstab an [4]. Eine Lösung zur Kombination von Funktionselementen aus verschiedenen Werkstoffen existiert jedoch bislang nicht.
Hybride Bauteilkomponenten lassen sich in der Regel nicht chemisch verbinden, was aus dem FLM-Bereich durch die Verwendung von Beschichtungen, Dauerfolien oder Klebstoffen zwischen dem metallischen Druckbett und dem Kunststoffbauteil bekannt ist [5;6]. Aus diesem Grund sind mechanische Verbindungselemente von Interesse, für die prozessunabhängige, allgemeine Gestaltungsrichtlinien zur Hemmung verschiedener Freiheitsgrade und zur Kraftübertragung existieren [7]. Der Einfluss der Prozessführung generativer Prozesse auf die Verbundfestigkeit ist dabei nicht zu vernachlässigen [8].
Experimentelle Untersuchungen zum Fused Layer Modeling
Bei der Versuchsanlage handelt es sich um eine Eigenentwicklung in üblicher XY-Portalbauweise mit Z-Hubtisch und leistungsgesteigerter Extrusionseinheit. Der Versuchsaufbau ist so gestaltet, dass die Analyse der variablen Prozessgrößen des FLM-Verfahrens bezüglich ihres Einflusses auf die Füllung einer Nut möglich wird. Neben der erreichten Fülltiefe zf stellt auch das Verhältnis von gefülltem Volumen zu extrudiertem Materialvolumen eine Zielgröße dar, da zu erwarten ist, dass nicht das gesamte Material in die Nut gelangt.
Es wurde eine bN = 1 mm breite und zf max = 15 mm tiefe Nut gefüllt, welche in ein zweigeteiltes Aluminiumbauteil gefräst ist, Bild 1 (A, B).
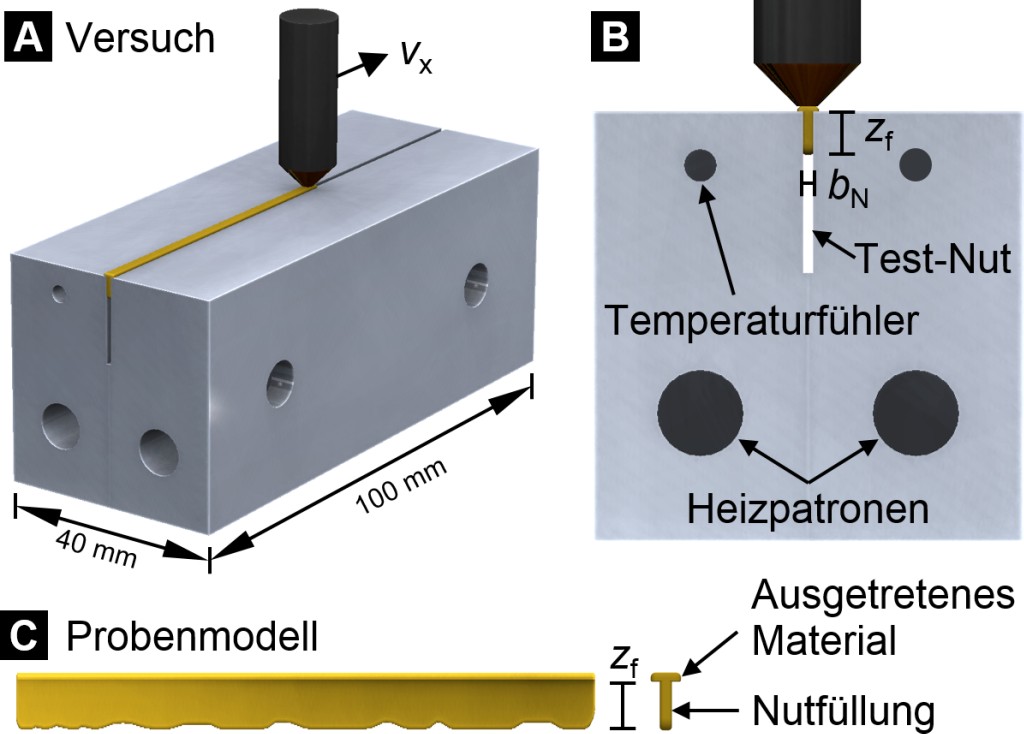
Bild 1. Schematischer Aufbau der Versuchsanlage, die eine Analyse der variablen Prozessgrößen erlaubt. Bild: TU Dortmund
Anschließend wurde eine Probe herausgelöst und in Bezug auf ihre Geometrieeigenschaften analysiert, Bild 1 (C). In Screening-Versuchen wurde dann zunächst der Einfluss der Prozessparameter – wie des Achsvorschubs vx, der Temperatur der Heißkanaldüse TD sowie der Sollfülltiefe zs und der Temperatur des Aluminiumbauteils TWS – untersucht. Des Weiteren wurden der Düsendurchmesser DD sowie die Temperatur des Bauteils mit der zu füllenden Nut TWS variiert.
Die vorab durchgeführten Screening-Versuche wiesen darauf hin, dass die Düsentemperatur TD keinen signifikanten Einfluss auf die Nutfülltiefe hat. Daher wurde für die weiteren Untersuchungen im Hinblick auf die Materialeigenschaften des verwendeten Werkstoffs ABS (Acrylnitril-Butadien-Styrol) eine Düsentemperatur von TD = 240 °C gewählt. Bei der verwendeten Düse handelte es sich um eine handelsübliche FLM-Extruderdüse („E3D-Volcano“) mit den Durchmessern 0,6 mm, 0,8 mm und 1,0 mm. Da sich die besten Füllergebnisse in den Screening-Versuchen mit DD = 0,6 mm erzielen ließen, fanden die weiteren Untersuchungen mit diesem Durchmesser statt.
Die Erfassung der Eindringtiefe wurde mithilfe eines Auflichtmikroskops (Modell „Olympus DSX500“) an mehreren Messpunkten in definierten Abständen durchgeführt. In Bild 2 sind zwei Proben, wie sie aus der Nut entnommen und vermessen worden sind, dargestellt.
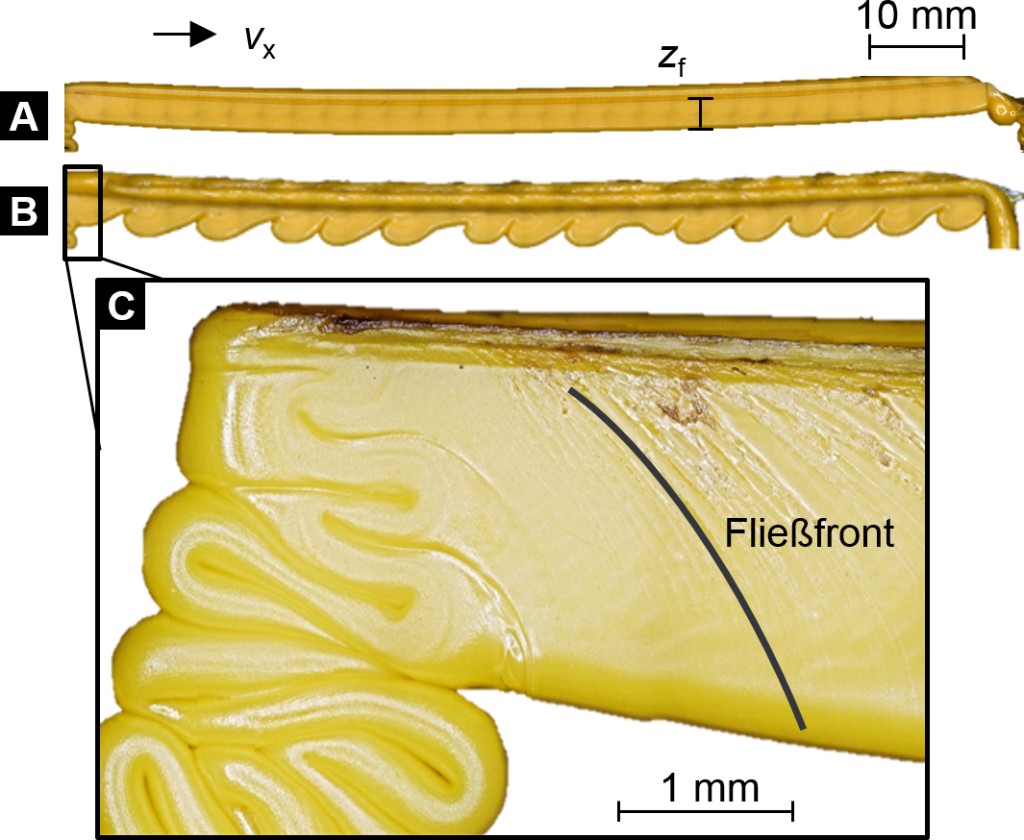
Bild 2. Beispiele vermessener Proben, die aus der mit Material befüllten Nut entnommen wurden. Bild: TU Dortmund
Deutlich ist zu erkennen, dass die Prozessparameter einen signifikanten Einfluss auf die Homogenität der Füllung haben, sodass verschiedene Prozesskonfigurationen (zum Beispiel Bild 2 B) nach dem Screening nicht weiter untersucht wurden. Bild 2 (C) zeigt den Einlaufbereich sowie die Fortpflanzung der Füllung detaillierter. Die Füllung beginnt links, wo der Kunststoff zunächst auf einer Länge von etwa 3 mm eine inhomogene Einlaufstruktur zeigt und sich erst anschließend eine gleichmäßige Fließfront aufbaut. Letztere bildet sich aufgrund der anfänglichen Inhomogenität sichtbar bogenförmig aus.
Aufbauend auf den Erkenntnissen aus den Screening-Versuchen fand eine weitere Versuchsreihe auf der Basis eines CCD (Central Composite Design)-Versuchsplans mit den Einflussfaktoren Achsvorschub vx, Soll-Fülltiefe zs und Nut-Temperatur TWS statt. Die Grenzen des Faktorraums sind in Bild 3 dargestellt.
Versuchsergebnisse zum Fused Layer Modeling
Für die Auswertung der Versuchsergebnisse wurde der Einfluss der Modellvariablen, deren Potenzen zweiter Ordnung und deren Wechselwirkungen untersucht. Die relevanten Größen aus dieser Faktormenge sind in Bild 4 mit ihrem relativen Einfluss auf das Systemverhalten aufgeführt.
Es zeigt sich, dass insbesondere der Achsvorschub vx und die Soll-Fülltiefe zs für die erreichte Fülltiefe bedeutsam sind. Die Bauteiltemperatur TWS spielt hingegen eine untergeordnete Rolle.
In Bild 5 zeigen dreidimensionale Wirkungsflächen, wie sich die Faktoren kombiniert auf die Fülltiefe zf auswirken. Durch den ausgeprägten quadratischen Einfluss des Achsvorschubs ergibt sich für jede Kombination der übrigen Faktoren ein lokales Maximum. Die Soll-Fülltiefe, Bild 5 (A), und Bauteiltemperatur, Bild 5 (B), zeigen hingegen einen proportionalen Einfluss, sodass sie soweit wie möglich maximiert werden sollten, um eine hohe Fülltiefe zu erreichen.
Mit steigender Soll-Fülltiefe verringert sich das Verhältnis von gefülltem Volumen zu extrudiertem Materialvolumen. Materialreste außerhalb der Nut beeinträchtigen nachgelagerte Prozessschritte, sodass Nachbearbeitungsschritte notwendig werden. Folglich ist zwischen maximal erreichbarer Fülltiefe und Prozesseffizienz abzuwägen. Weiterhin zeigen exemplarische Voruntersuchungen, dass eine modifizierte Düsengeometrie den Nutfüllprozess positiv beeinflussen kann.
Die getestete Geometriemodifikation zeichnet sich durch einen abgeflachten Düsenkopf aus, Bild 6 (B), während handelsübliche FLM-Extruderdüsen eine konische Form haben, Bild 6 (A).
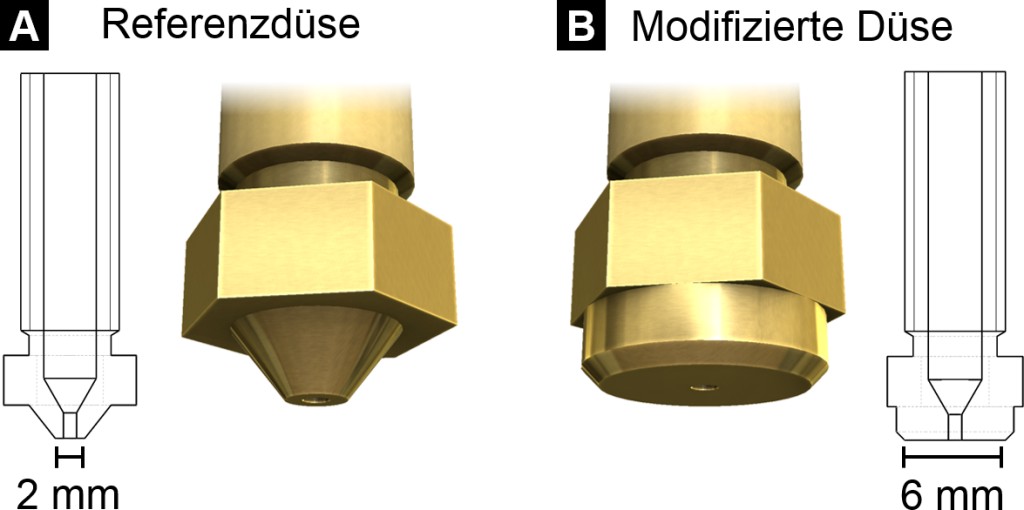
Bild 6. Eingesetzte Düsengeometrien: Eine abgeflachte Bauform (rechts) bringt Vorteile. Bild: TU Dortmund
Mit der modifizierten Düsengeometrie kann die Nutfüllung um bis zu 35 % gesteigert werden, sodass auch dieser Einfluss in zukünftigen Versuchsreihen näher untersucht werden wird. In dieser (auf die Prozessparameter fokussierten) Untersuchung wurden jedoch zunächst nur handelsübliche Düsen eingesetzt.
Fazit und Ausblick
Auf Basis der Versuchsergebnisse konnte eine Charakterisierung des physikalischen Systemverhaltens anhand der signifikanten Einflussgrößen abgeleitet werden. Diese Erkenntnisse werden in nachfolgenden Untersuchungen genutzt, um formschlüssige Verbindungen zwischen Metall- und Kunststoffkomponenten zu untersuchen. Zu diesem Zweck werden Nuten mit Hinterschnitt spanend in die metallische Komponente eingebracht und anschließend als Verbindungselement für eine im FLM-Verfahren direkt aufgetragene Kunststoffkomponente verwendet.
Die mit unterschiedlichen Prozessparametern hergestellten formschlüssigen Verbindungen werden anschließend zum Beispiel hinsichtlich ihrer mechanischen Eigenschaften untersucht. Auch die Entwicklung einer optimierten Düsengeometrie soll ein Gegenstand der geplanten Untersuchungen sein.
Neben den benannten Autoren waren die wissenschaftlichen Mitarbeiter Jonas Baumann (ISF), Philipp Bengfort (FG ME), Daniel Hesse (LKT) und Thomas Rupflin (FG ME) an der Ausarbeitung des Fachbeitrags beteiligt. Die Autoren danken dem Mercator Research Center Ruhr (MERCUR) der Stiftung Mercator für die Förderung des Forschungsprojektes mit dem Titel „Analyse des Produktentstehungsprozesses bei der Kombination additiver und subtraktiver Fertigungsverfahren für die Herstellung von Multimaterialprodukten“.
Literatur:
[1] Kerbrat, O.; Mognol, P.; Hascoët, J.-Y.: A new DFM approach to combine machining and additive manufacturing. Computers in Industry, 2011, S. 684–692.[2] Du, W.; Bai, Q.; Zhang, B.: A Novel Method for Additive/Subtractive Hybrid Manufacturing of Metallic Parts. Procedia Manufacturing 5 (2016), S. 1018–1030.[3] Zhu, Z. et al.: Application of a Hybrid Process for High Precision Manufacture of Difficult to Machine Prismatic Parts. International Journal of Advanced Manufacturing Technology 74 (2014), S. 1115–1132.[4] Levy, G.: Additive Manufacturing – Multi Process, Multi Materials, Multi Applications: Interdisciplinary ECO System. CIRP Conference on Intelligent Computation in Manufacturing Engineering (ICME), Gulf of Naples, 2018.[5] Anderson, T.: Choosing the Best 3D Printing Bed Surface. MatterHackers Inc. Internet: https://www.matterhackers.com/news/choosing-the-right-3d-print-bed-surface. Zugriff am 7.10. 2016.[6] Croccolo, D. et al.: Experimental characterization and analytical modelling of the mechanical behavior of fused deposition processed parts made of ABS-M30. Materials Science 79 (2013), S. 506–518.[7] Ehrenstein, G. W.: Handbuch Kunststoff-Verbindungstechnik. München: Carl Hanser Verlag, 2004.[8] Kuhmann, K.: Prozeß- und Materialeinflüsse beim Mehrkomponentenspritzgießen. Dissertation, Erlangen, 1998.
Prof. Dr.-Ing. habil. Bernd Künne, Jahrgang 1956, ist seit 1993 als Professor an der Technischen Universität (TU) Dortmund tätig und leitet dort das Fachgebiet Maschinenelemente (FG ME). // Prof. Dr.-Ing. Markus Stommel, Jahrgang 1968, hat seit 2014 die Leitung des Lehrstuhls für Kunststofftechnologie (LKT) an der TU Dortmund inne. // Priv.-Doz. Dr.-Ing. Dipl.-Inform. Andreas Zabel, Jahrgang 1969, ist Oberingenieur am Institut für Spanende Fertigung (ISF) der TU Dortmund. // Prof. Dr.-Ing. Bernd Kuhlenkötter, Jahrgang 1971, leitet seit 2015 den Lehrstuhl für Produktionssysteme (LPS) der Ruhr-Universität Bochum. // Prof. Dr.-Ing. Gerd Witt, Jahrgang 1956, leitet seit 1998 den Lehrstuhl für Fertigungsverfahren und Werkzeugmaschinen (RTC) der Gerhard-Mercator-Universität Duisburg.