PPS-Systeme auf den neuesten Stand gebracht
Eine hohe Termintreue ist für deutsche Industrieunternehmen unerlässlich, um am Hochlohnstandort „überleben“ zu können. Doch sind unsere im Kern über 60 Jahre alten PPS-Systeme dafür noch geeignet? Mit welchem Lösungsansatz kann man sie weiterhin nutzen?
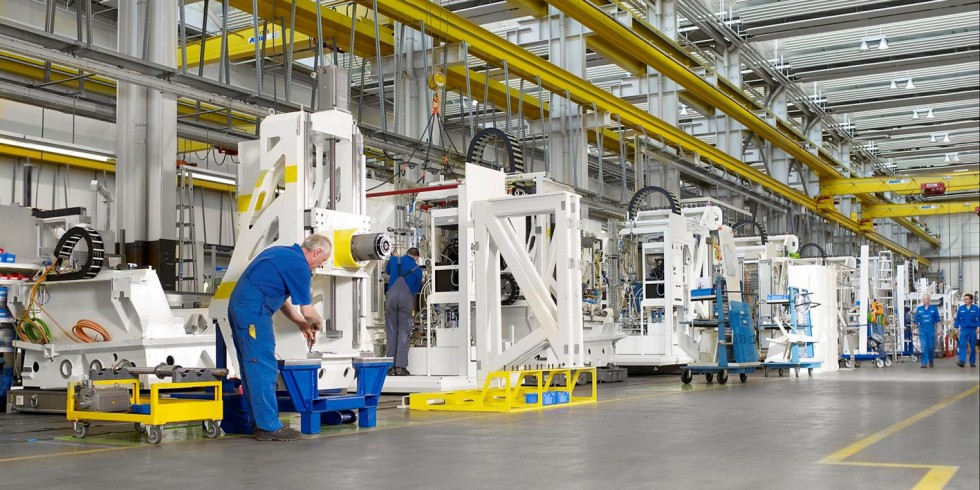
Maschinenmontage bei einem deutschen Werkzeugmaschinenbauer: Software-Systeme zur Produktionsplanung und -Steuerung (PPS) werden immer noch in vielen deutschen Unternehmen genutzt, bilden die heutige Fertigungsrealität aber nur unzureichend ab.
Foto:Heller
Ein Großteil der in Deutschland produzierenden Unternehmen greift zur Produktionsplanung- und Steuerung (PPS) auf IT (Informationstechnik)-Systeme zurück. Diese sollen die Betriebe unter anderem dabei unterstützen, eine möglichst gute Termintreue zu erreichen – einer der wichtigsten Faktoren, um weiterhin die Wettbewerbsfähigkeit der deutschen Industrie an einem Hochlohnstandort sicher zu stellen [1; 2].
PPS-Systeme bilden seit den 1980er Jahren die Basis
Zur Beherrschung der hierfür notwendigen Zeit- und Materialwirtschaft bildet seit rund 40 Jahren die PPS als zentrales Konzept das „Gehirn“ produzierender Unternehmen – und damit rücken die entsprechenden Software-Systeme in den Fokus. Jedoch ist trotz des beinahe flächendeckenden Einsatzes der PPS-Systeme das Ergebnis meist nicht zufriedenstellend [3; 4]. Termintreue wird in der Realität oftmals nur durch einen hohen manuellen Steuerungsaufwand erreicht.
In diesem Beitrag wird daher die These vertreten, dass die im Kern über 60 Jahre alten Ideen, die die Basis der meisten PPS-Systeme bilden, nicht mehr für die Probleme heutiger Produktionssysteme geeignet sind und eine Anpassung der viele Jahrzehnte alten Denk- und Vorgehensweisen der PPS notwendig ist. Im Weiteren werden zunächst die Kritikpunkte an aktuellen PPS-Systemen herausgearbeitet und ein hybrider Steuerungsansatz aus einer zentralen Grobplanung und einer dezentralen Feinplanung als Lösungsvorschlag skizziert.
Was leisten aktuelle PPS-Systeme?
Für ein umfassenderes Verständnis der nachfolgenden Kritikpunkte wird zunächst das Aufgabenspektrum eines PPS-Systems definiert. Ein PPS-System unterstützt die Gestaltung und Durchführung des Produktionsprogramms. Im Rahmen der Produktionsplanung und -steuerung ist insbesondere festzulegen:
- welche Produkte in welcher Stückzahl innerhalb eines definierten Zeitraums hergestellt werden müssen (Primärbedarfsplanung),
- welche Mengen an fremdbezogenen und eigengefertigten Einsatzgütern benötigt werden (Sekundärbedarfsplanung),
- in welchen Losen die jeweiligen End-, Zwischen- und Vorprodukte produziert oder beschafft werden (Losgrößenplanung),
- wann die Herstellung der einzelnen zu Fertigungsaufträgen zusammengefassten End- und Zwischenprodukte unter Berücksichtigung der verfügbaren Ressourcen produziert werden (Termin- und Kapazitätsplanung),
- wann welche Fertigungsaufträge in der Produktion physisch durchgeführt werden (Auftragsfreigabe) und
- in welcher Reihenfolge die Fertigungsaufträge am jeweiligen Arbeitsplatz bearbeitet werden sollen (Ablaufplanung).[5]
Kritikpunkt 1: Die Systemgestaltung ist heute nicht Aufgabe der PPS
Wie der vorstehenden Definition der PPS entnommen werden kann, wird heute die Systemgestaltung nicht als Teil der PPS gesehen. In der aktuell üblichen Vorgehensweise wird – basierend auf Faktoren wie der Art des Teileflusses, der Material- und Produktkomplexität und der Schwankungen des Kundenbedarfs – das passende PPS-Konzept ausgewählt [6]. Das Problem dabei ist, dass die aktuellen Ausprägungen des zu steuernden Produktionssystems als gegeben hingenommen und nicht hinterfragt werden. Die Komplexität wird nicht durch entsprechende Gestaltung der Strukturen reduziert. Es wird lediglich versucht, die IST-Situation möglichst detailgetreu abzubilden.
Dies führt zu den extrem komplexen PPS-Systemen in der Praxis, die kaum einen strukturierten Überblick erlauben und deren Planungsergebnisse für die Mitarbeiter nicht mehr nachvollziehbar sind, wie in Bild 1 dargestellt ist.
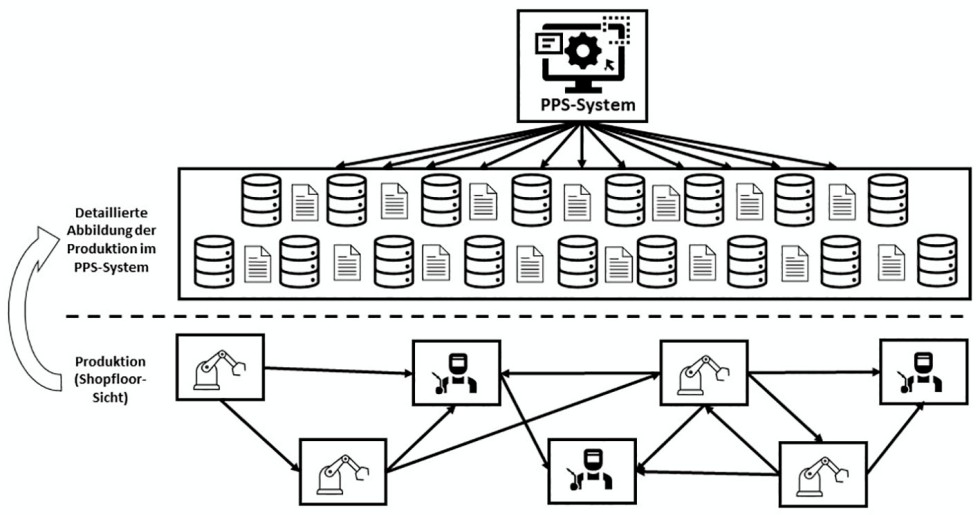
Bild 1. Die Produktion wird möglichst detailliert im PPS-System abgebildet. Die bestehenden Strukturen werden jedoch nicht hinterfragt. Grafik: TZ PULS
Da die Komplexität des Steuerungssystems maßgeblich von der Komplexität des zu steuernden Systems abhängt, führt der Weg zum Aufbau eines einfachen Steuerungssystems nur über eine Vereinfachung des Produktionssystems. Das heutige PPS-Verständnis muss erweitert werden. Die Möglichkeiten einer ganzheitlichen und interdisziplinären Systemgestaltung können nur durch die Zusammenarbeit von Prozessplanern und IT-Experten realisiert werden.
Kritikpunkt 2: Mangelnde Qualität der Eingangsdaten und Fehlerfortpflanzung
Es ist problematisch, dass die Ergebnisqualität der PPS-Systeme erheblich von der Qualität der Eingangsdaten abhängt [7], diese aber meist mangelhaft sind. Eine wichtige Planungsbasis für PPS-Systeme bilden die Stücklisten. Sind diese nur mangelhaft gepflegt oder veraltet, stimmen alle in Folge ermittelten Berechnungen nicht. Es kommt zur Fehlerfortpflanzung. Nicht umsonst wird die Stückliste als „Mutter aller Informationen“ in einem Unternehmen bezeichnet.
Die Durchlaufterminierung findet auf Basis der Arbeitspläne statt. Diese enthalten meist relativ genau ermittelte Bearbeitungszeiten, da diese zur Kalkulation der Fertigungskosten genutzt werden. Bis zu 95 Prozent der Durchlaufzeiten machen aber die Übergangszeiten für Qualitätssicherung und Logistik aus. Diese werden meist nur grob geschätzt und mit erheblichen Sicherheitspuffern einmalig in das PPS-System eingetragen. Diese Zeiten werden weder exakt gemessen noch systematisch reduziert. Damit bleiben durch den heute üblichen PPS Einsatz erhebliche Potenziale zur Durchlaufzeitreduzierung ungenutzt. Die gesamte Detailplanung fokussiert sich somit lediglich auf circa 5 Prozent der gesamten Durchlaufzeit [8; 9].
Plant ein PPS-System gegen „unendliche Kapazitäten“, so ist das Ergebnis kein Plan, sondern ein Wunsch. Wird gegen verfügbare Kapazitäten geplant, so ist diese im Normalfall nicht exakt bekannt. Es wird ein einmal ermittelter, statischer Wert und eine angenommene Verfügbarkeit von beispielsweise 85 Prozent in das System eingetragen. Dies führt zu ständiger Überplanung, wodurch ein manueller Kapazitätsausgleich notwendig ist, der enorme personelle Aufwände erfordert und die Termintreue gefährdet [10; 11]. Die heute meistens verwendeten deterministischen Modelle gehen davon aus, dass die Eingangsdaten mit Sicherheiten belegt sind [12]. Dies ist jedoch im heutigen PPS-Umfeld kaum anzunehmen, wie obige Beispiele zeigen. Das heute übliche hierarchisch-sequentielle Planungsvorgehen [13] verschleiert die mangelnde Datenqualität auf jeder Planungsstufe. Am Ende des Planungsprozesses werden die Qualität der Eingangsdaten und das vermeintlich exakte Planungsergebnis nicht mehr hinterfragt.
Es müssen Wege gefunden werden, wie sich mit weniger Planungsdaten ausreichend gute Planungsergebnisse erzielen lassen. Nur für eine stark reduzierte Datenbasis kann der Pflegeaufwand bewältigt werden. Auch muss die Planung ohne die Anforderungen an höchste Datengenauigkeit auskommen. Auf jeden Fall sollten die Führungskräfte die Unzulänglichkeiten der Planungsdaten einkalkulieren und die Ergebnisse mit entsprechender Vorsicht nutzen.
Kritikpunkt 3: Eine Ergebniskontrolle und ein Lernen finden nicht statt
Obwohl sich viele Unternehmen der schlechten Datenqualität in ihren EDV-Systemen durchaus bewusst zu sein scheinen, ist es um so erstaunlicher, dass es meist keine Lernstrategie zur kontinuierlichen Verbesserung der Planungsdatenbasis in Unternehmen gibt. Die Planergebnisse der PPS-Systeme werden nicht systematisch mit den tatsächlich im laufenden Betrieb am Ende des Tages erreichten Durchlaufzeiten und der Termintreue der Aufträge verglichen. Es findet meist kein Plan-/Ist-Vergleich statt. Die PPS-Systeme liefern zwar ein stimmig und exakt wirkendes Ergebnis – aber ob dieses jemals in der Realität umsetzbar ist und/oder auch tatsächlich jemals so erreicht wird, wird nicht kontrolliert.
Entscheidende Planungsparameter, wie die Durchlaufzeit und die aktuelle Verfügbarkeit von Anlagen, werden meist aufgrund des erheblichen Erfassungsaufwands nur einmal manuell erfasst und als statischer Wert in das System eingetragen. Die Daten werden nicht durch einen systematischen Prozess kontinuierlich überwacht und verbessert.
In unseren auf Effizienz getrimmten Unternehmen wird sehr vieles kontrolliert und kontinuierlich verbessert. Gerade wegen des erheblichen finanziellen und personellen Aufwands und der Wichtigkeit für die Unternehmen muss die Effizienz und Effektivität der PPS-Systeme gemessen und entsprechend verbessert werden.
Kritikpunkt 4: Mängel der zumeist angewendeten MRP II-Logik
Ein Großteil der in der Industrie eingesetzten PPS-Systeme greift auf die „MRP II“-Logik zurück. Auch daran gibt es einige Kritikpunkte: Der heute meist etablierte „PUSH“-Ansatz sieht vor, jeden Arbeitsplatz einzeln zu planen und anzusteuern. Diese detaillierte Planung verbessert jedoch keineswegs die Planungsqualität. Sie erzeugt aber erhebliche Planungskomplexität. Hier die Lösung in der immer weiteren Detaillierung der Planung zu suchen, ist genau der falsche Weg. Außerdem erfordert dieser Planungsansatz sehr große Datenmengen. Diese werden auf Basis eines hierachisch-sequentiellen Modells im Rahmen eines MRP-Laufs zur Ermittlung des Materialbedarfs weiterverarbeitet. Aufgrund des meist enormen Umfangs kann dieser nur einmal über Nacht durchgeführt werden.
Kommt es während der Durchführung des MRP-Laufs zu kurzfristigen Änderungen oder unvorhersehbaren Störungen, ist der aktuelle Plan obsolet. Das Ergebnis ist eine Bedarfsermittlung, die mit der Realität nicht übereinstimmt. Für die Produktion, insbesondere die dort tätigen Meister, entsteht ein sogenannter „untertägiger Blindflug“. Daher werden PPS-Systeme benötigt, die mit häufigeren Planläufen auch kurzzyklisch auf Veränderungen reagieren können.
Um das komplexe System des (in viele einzelne Arbeitsfolgen zerlegten) Produktionsprozesses überhaupt noch steuern zu können, wird zwischen den Arbeitsplätzen ein hoher Bestand an Material und Zwischenprodukten eingeplant. Probleme bei der Termintreue und Fehlteile werden regelmäßig mit noch höherem Bestand kompensiert, der zu einer noch höheren Durchlaufzeit führt. Dieser „Teufelskreis“ wird als Durchlaufzeitsyndrom bezeichnet. Durch die aktuellen PPS-Systeme wird dieses in der Praxis häufig festzustellende Problem nicht gelöst, sondern teilweise sogar noch verschlimmert.
Weiterhin treten in vielen Produktionssystemen „Bullwhip“-Effekte auf. Auslöser von Bullwhip-Effekten sind zum einen mehrstufige Produktionssysteme und zum anderen sogenannte „Time Lags“. Häufig sind für ein PPS-System notwendige Informationen erst mit erheblichen Verzögerungen verfügbar, beispielsweise durch manuelle Rückmeldeprozesse oder Datenverarbeitungen im Nachtlauf.
Wechselwirkungen besser berücksichtigen
Ein weiteres Problem der MRP II-Logik ist, dass die Systemdynamik, die Wechselwirkungen innerhalb des Systems, bei den Berechnungen und Auswertungen aktuell nicht berücksichtigt werden. Die gängigen Systeme verwenden nur statische Werte. Beispielsweise werden die Durchlaufzeit und die Verfügbarkeit manuell in das System eingetragen und sind nicht Teil des Planungsprozesses, sondern ein fixes Eingangsdatum (!). Dadurch treten in einer Produktion Warteschlangen auf.
In der Literatur wird die Entstehung von Warteschlangen vor allem auf den sogenannten Dehnungseffekt der Auslastung in der Produktion zurückgeführt. Dieser beschreibt, dass es einen Zusammenhang zwischen der Auslastung eines Systems und der Warteschlangenzeit (beispielsweise der Durchlaufzeit) gibt. Bei einer Auslastung über circa 85 Prozent nimmt die Durchlaufzeit durch Variation der Prozess- und Ankunftszeiten exponentiell zu.
Den Autoren ist heute kein PPS-System bekannt, das diese während der 60 Nutzungsjahre Jahre ermittelten Erkenntnisse berücksichtigt. Dies ist jedoch von nicht zu unterschätzender Wichtigkeit zur Erklärung der mangelhaften Leistung unserer PPS-Systeme. Mit dem Ziel der meisten Planungssysteme, eine Auslastung der Ressourcen zu 100 Prozent zu erzielen, wird dem Dehnungseffekt ein maximaler Vorschub geleistet.
Die Reaktion der Disponenten auf all diese Probleme ist, als „Terminjäger“ zu agieren, damit wichtige Aufträge doch noch innerhalb des zugesagten Zeitfensters fertiggestellt werden können. Dies geschieht jedoch auf Kosten der restlichen Aufträge im Umlaufbestand (WIP), deren Wartezeit und somit Durchlaufzeit weiter steigt – auch hier ein Teufelskreis. Das Ergebnis einer Umsortierung der Auftragsreihenfolge führt zu schwankenden und unvorhersehbaren Durchlaufzeiten. Aufträge sind nicht mehr planbar und eine akzeptable Termintreue ist nur bedingt und mit einem sehr hohen manuellen Steuerungsaufwand erreichbar.
Die MRP II-Logik in Verbindung mit unserem auf REFA basierenden Produktionsverständnis schafft sich paradoxerweise selbst die denkbar schlechtesten Voraussetzungen für eine hohe Termintreue. Wird die Termintreue als wichtigstes Planungsergebnis akzeptiert, muss die althergebrachte Vorgehenslogik in Frage gestellt und neu gedacht werden. Es muss ein Weg gefunden werden, wie die Planungsläufe kurzzyklisch untertägig durchgeführt werden können. Dabei sollten seit Jahrzehnten bekannte Effekte wie das Durchlaufzeitsyndrom, der Bullwhip- und Dehnungseffekt weitgehend vermieden und die Systemdynamik angemessen berücksichtigt werden, um realistische Planungsergebnisse zu erhalten.
Lösungsansatz: Aufbau eines hybriden PPS-Systems
Auf Basis der Erfahrungen aus dem Forschungsprojekt „Layout based Order Steering – LOS1“ [14] wird vorgeschlagen, dass ganz bewusst die Gestaltung des zu steuernden Systems als Teil der PPS gesehen wird. Die Ziele müssen sein, die Komplexität zu reduzieren und die Steuerbarkeit des Systems zu verbessern.
Die Steuerbarkeit des Systems kann durch folgende Ansatzpunkte in geeigneter Weise beeinflusst werden:
- Als erster Schritt wird vorgeschlagen möglichst viele Baugruppen aufzulösen. Im Lean-Umfeld wird dies mit dem Prinzip „flache Stückliste“ umschrieben. Der Effekt ist, dass sehr viele bisher einzeln zu planende und zu steuernde Zwischenzustände mit eigenen Teilenummern entfallen. Das System wird dadurch entschlackt und stark vereinfacht [9]. Durch die Reduzierung der Planungsstufen wird zudem der Bullwhip-Effekt reduziert.
- Ein zweiter Schritt ist die zielgerichtete Gestaltung der Fertigungs- und Materialflüsse. Es können beispielsweise mehrere Arbeitsplätze zu einer U-Zelle oder Produktionsinsel zusammengefasst werden [15; 16]. Dies reduziert die Anzahl der zu steuernden einzelnen Arbeitsplätze nochmals erheblich. In der Lern- und Musterfabrik des Technologiezentrum Produktions- und Logistiksysteme (TZ PULS) wird im Planspiel „Von der Werkstatt zur Fließfertigung“ aus vormals sieben einzeln zu steuernden Arbeitsplätzen eine verkette U-Zelle mit einem Einsteuerungspunkt gestaltet. Auch im PPS-System reduziert sich der Pflegeaufwand von sieben Teilprozessen auf einen höher aggregierten Prozess.
Systemgestaltung mit Prozessprofilen
Die bisher beschriebenen Schritte leisten einen enormen Beitrag, das ansonsten häufig auftretende Durchlaufzeitsyndrom zu verringern. Für die verbliebenen zu planenden Prozesse wird vorgeschlagen, anstatt der Arbeitspläne Prozessprofile zu nutzen. Dieser neue Begriff soll verdeutlichen, dass die Durchlaufzeit des gesamten Prozesses die ausschlaggebende Größe ist. Für die Bearbeitungszeiten sind heute meist viel zu detaillierte Informationen vorhanden, für die Übergangszeiten viel zu grobe Schätzungen. Es muss auch diskutiert werden, dass Arbeitspläne heute in der Praxis allerlei „unternehmenspolitischen Ballast“ beinhalten (wie Leistungsgrade, Pausenvereinbarungen usw.), der die Tauglichkeit vieler Arbeitspläne als Grundlage für die PPS fragwürdig erscheinen lassen.
Ein neuralgischer Punkt zur Steuerung von Prozessen ist der „Engpass“. Als Engpass wird meist die Ressource mit der geringsten Kapazität bezeichnet. Es kann aber auch ein „restriktiver Engpass“ in der Systemgestaltung festgelegt werden [17]. Für die Aufgabe der Planung und Steuerung legt ein Engpass eindeutig den Fokus fest und trägt zur Lösung vieler in der PPS auftretenden Zielkonflikte bei.
Ein weiterer neuralgischer Punkt ist der Kundenentkopplungspunkt. Ab diesem Punkt wird das Produkt kundenspezifisch. Ein Produktionssystem muss vor und nach diesem Punkt jeweils anders gesteuert werden. Außerdem wird durch die Lage dieses Punktes im Wertschöpfungsprozess die Lieferzeit zum Kunden maßgeblich beeinflusst (Make to Stock vs. Make to Order). Viele PPS-Systeme, die nur von IT-Experten eingerichtet werden, steuern mangels Produktionssystemwissen alle Systemteile gleich. Der Kundenentkopplungspunkt wird durch die Produktkonstruktion festgelegt. Soll dieser bewusst zur Gestaltung eines Produktionssystems festgelegt werden, ist eine enge Zusammenarbeit mit der Technischen Entwicklung unabdingbar. Gleiches gilt für die Varianzbildungspunkte, die den Aufwand vor allem für die Logistik in einem Produktionssystem beeinflussen.
Durch das zielgerichtete Zusammenspiel aller zuvor genannten Gestaltungsmaßnahmen kann die Komplexität des zu steuernden Systems durch die Reduzierung der Planungselemente und der Anzahl notwendiger Schnittstellen erheblich reduziert werden. Wie in Bild 2 erkennbar ist, wird erst das stark vereinfachte Produktionssystem im PPS-System abgebildet. Der Pflege-, Planungs- und Steuerungsaufwand wird entsprechend geringer.

Bild 2. Durch entsprechende Gestaltungsmaßnahmen werden die Steuerbarkeit des Produktionssystems erhöht und die Komplexität des PPS-Systems deutlich reduziert. Grafik: TZ PULS
Dieser Schritt, die Systemgestaltung als Aufgabe der PPS zu sehen, bringt die nachhaltigsten Ergebnisse, da direkt an der Ursache des Problems gearbeitet wird. Viele andere Maßnahmen sind nur eine Symptombehandlung.
Verbesserung der Datenqualität
Natürlich wäre es viel zu einfach, bei mangelnder Datenqualität lapidar vorzuschlagen, die Daten doch einfach besser zu pflegen. Es sind so viele Daten für ein PPS-System nötig, dass die Ressourcen dazu meist nicht vorhanden sind. Es ist auch nicht erkennbar, an welcher Stelle man mit der Pflege beginnen sollte und welche Daten am wichtigsten sind.
Die Reduzierung der Komplexität des Systems durch gezielte Systemgestaltung bildet die Grundlage für die Verbesserung der Datenqualität. Die Planung und Steuerung sollte sich bei der Pflege der Prozessprofile und der Planung auf die kritische Kette konzentrieren. Dies ist der längste (manchmal auch der fehleranfälligste) Teilprozess. Wenn dieser Prozess richtig geplant und im Zeitrahmen ist, sollten es alle anderen Teilprozesse, die schneller sind, auch schaffen. Der Aufwand für die Datenpflege der anderen Prozesse kann geringer priorisiert werden.
Innerhalb der kritischen Kette sollte der Fokus auf den Engpass gerichtet werden. Gerade die verfügbaren Kapazitäten zu ermitteln, ist sehr aufwendig. Da der Engpass per Definition die Ressource mit der geringsten Kapazität darstellt, sollten auch hier bei entsprechender Planung und Steuerung des Engpasses alle anderen Teilprozesse in der Lage sein, dem Produktionsprogramm zu folgen. Es wird daher vorgeschlagen, nur noch den Engpass im Detail zu planen und die Auswirkungen auf die anderen Teilprozesse lediglich grob zu simulieren. Dies reduziert den Ermittlungs- und Pflegeaufwand, im speziellen für die verfügbare Kapazität, enorm. Auf diese Weise sollte es gelingen, eine für eine gute Planung ausreichende Datenqualität zu erreichen.
Mit Industrie 4.0 Transparenz in Echtzeit schaffen
Einen weiteren Beitrag zur Verbesserung der Datenqualität können Industrie 4.0 Technologien leisten. Die realen Produktionsgegebenheiten sollen mithilfe von Sensorik wesentlich schneller und exakter erfasst werden, als dies in heutigen PPS-Systemen möglich ist. Das Ziel ist, möglichst echtzeitnah den aktuellen Zustand der Produktion und Logistik zu erfassen.
Die beiden wichtigsten Daten für ein PPS-System sind die Durchlaufzeiten der Prozesse und die aktuellen Kapazitätsauslastungen der zu planenden Ressourcen. Beides sind Daten, die in aktuellen PPS-Systemen im Vorfeld auf Basis von Schätzungen fixierte Eingangsdaten der Planung sind. Durch eine geschickte Systemgestaltung, der gezielten Auswahl geeigneter Datenmesspunkte mit entsprechenden Technologien und der Kombination der Daten aus verschiedenen Quellsystemen lassen sich Daten echtzeitnah erfassen und verarbeiten. Diese drastische Verkürzung vieler heute noch vorhandener Time Lags trägt zur Reduzierung der Bullwhip-Effekte in einem Produktionssystem bei.
Aufbau einer Lernstrategie
Die Effizienz und Effektivität der PPS-Systeme muss gemessen und entsprechend verbessert werden. Es gilt, eine Lernstrategie für PPS-Systeme zu entwickeln, die einerseits die Eingangsdaten kontinuierlich verbessert und andererseits einen Plan-/Ist-Vergleich der Planungsergebnisse aus dem PPS-System mit dem Erfüllungsgrad in der Realität vornimmt. Die entsprechenden Methoden und Mechanismen sind in vielen Unternehmen mit dem täglichen Shopfloormanagement und KVP-Prozessen bereits vorhanden, müssen aber adaptiert werden.
Es können täglich Maßnahmen zur Stabilisierung der Durchlaufzeit und gezielten Verkürzung der Planzeiten diskutiert und umgesetzt werden. Einen ähnlichen Vorschlag unterbreiten Stanula et al [18]. Die Einbindung der PPS-System-Verantwortlichen in das tägliche operative Produktionsmanagement ist noch im Detail zu entwickeln und in der Praxis zu testen. Es erscheint äußerst vielversprechend, die heute oft zu beobachtende Lücke zwischen der operativen Steuerung auf dem Shopfloor und der IT-basierten Planung mit der vorgeschlagenen Vorgehensweise zu überbrücken und ein gegenseitiges Lernen zu ermöglichen.
High-Level-MRP und hybrider Steuerungsansatz mit Obeya
Die Programmplanung sollte zentral – nur auf einem sehr hohen Aggregationsgrad – durchgeführt werden. Suri bezeichnet dies als „High Level MRP“ [15]. Die Autoren schlagen zusätzlich noch die Fokussierung auf die kritische Kette und den Engpass vor. Somit wird es möglich, die notwendige Datenqualität sicherzustellen. Die mit Industrie 4.0-Technologien zusätzlich echtzeitnah vorhandenen Daten aus der Produktion – in Kombination mit den häufigen Planungsläufen (durch das High Level MRP) – ermöglichen auch untertägig eine kurzfristige Neu- und Umplanung in der Steuerung. Der bisherige untertägige Blindflug der Meister nach den ersten Änderungen oder Störungen kann somit verhindert werden.
Die Reduktion auf eine zentrale Grobplanung setzt voraus, dass die Detailplanung dann anderweitig durchgeführt werden muss. Um eben diese dezentrale Feinplanung möglich zu machen, wurde am TZ PULS das Konzept des Obeya (siehe Bild 3) aus dem Produktentstehungsprozess von Toyota auf das PPS-System übertragen [19].

Bild 3. Der „Obeya“ (die Kommunikationszentrale) umfasst analoge Mittel aus dem Lean-Baukasten (wie Shopfloormanagement und KATA). Aber auch digitale Hilfsmittel wie Ortungssysteme und ein digitales KVP-Tool sind inbegriffen – hier eine Ansicht aus der Lernfabrik in Dingolfing.
Foto: TZ PULS
Diese Kommunikationszentrale beinhaltet analoge Mittel aus dem Lean-Baukasten – wie Shopfloormanagement und KATA – aber auch digitale Hilfsmittel, wie Ortungssysteme und ein digitales KVP (Kontinuierlicher Verbesserungsprozess)-Tool. Die Kombination aus einer zentralen Grobplanung (High Level MRP) mit dem auf dem Obeya-Konzept basierten Vorschlag zur dezentralen Feinplanung wird als der „Hybrider PPS-Ansatz“ bezeichnet, der vollständig in Bild 4 dargestellt wird.

Bild 4. Ergänzung des PPS-Systems um den Obeya, der die Reduzierung auf eine zentrale High-Level-Planung und die Einbindung einer Lernstrategie für das PPS möglich macht. Grafik: TZ PULS
Alle bisherigen Vorschläge setzen außerhalb des Kerns aktueller PPS-Systeme an. Somit können die bisherigen Verbesserungsvorschläge auch mit den meisten am Markt befindlichen PPS-Systemen vermutlich weitgehend umgesetzt werden. Lediglich für die Berücksichtigung der Systemdynamik und einer weiteren Performanceverbesserung muss das hierarchisch-sequentielle Optimierungsmodell der MRP II-Logik in Frage gestellt werden. In weiteren Forschungsarbeiten soll hierfür ein neuer Kern, beispielsweise auf der Basis von künstlicher Intelligenz, entwickelt werden.
Fazit: Lernstrategie für PPS führt zum Ziel
Die positive Nachricht ist, dass die Unternehmen das bestehende PPS-System weiterhin nutzen können. Die Lösung liegt nicht in der Anschaffung einer neuen Software, sondern in der Reduzierung auf eine zentrale Grobplanung (High Level MRP). Alles übrige kann dezentral über ein Shopfloormanagement und das Obeya-Konzept gesteuert werden, wie es der hybride Steuerungsansatz vorschlägt. Das Ziel ist ein einfaches Steuerungssystem mit untertägigen Planungsläufen. Dieses setzt ein „einfach zu steuerndes System“ voraus. Die beschriebene gezielte Gestaltung des Produktionssystems setzt an der Problemursache an und schafft nachhaltige Problemlösungen. Industrie 4.0-Technologie wird eingesetzt, um ein möglichst reales Abbild der Produktion echtzeitnah zu erhalten. Um die Effizienz und Effektivität der Planung und Steuerung zu erhöhen, sollte eine Lernstrategie für PPS eingeführt werden, um die Datenqualität und die Planungsergebnisse zu messen und kontinuierlich zu verbessern.
Literatur
- Jünemann, R., Beyer, A.: Steuerung von Materialfluss- und Logistiksystemen: Informations- und Steuerungssysteme, Automatisierungstechnik. Springer Verlag, 1998.
- Friedli, T.; Schuh G.: Wettbewerbsfähigkeit der Produktion an Hochlohnstandorten. Springer Verlag, 2012.
- Fuchs, R.-M.: Ein Planungsverfahren zur Erkennung und Bewältigung von Material- und Kapazitätsengpässen bei mehrstufiger Linienfertigung. Springer Verlag, 2013.
- Zsifkovits, H. E.; Altendorfer, S.: Logistics Systems Engineering. Rainer Hampp Verlag, 2013.
- Schulte, C.: Logistik. Wege zur Optimierung der Supply Chain. Franz Vahlen Verlag, 2017.
- Lödding, H.: Verfahren der Fertigungssteuerung – Grundlagen, Beschreibung, Konfiguration. Springer Vieweg, 2016.
- Teich, T.: Optimierende Verfahren in der Produktion, 2015. Internet: http://www.prozesse-mittel-stand.digital/images/PDF/Leitfaden_Optimierende_Verfahren_in_der_Produktion.pdf.
- Wiendahl, H.-P.: Fertigungsregelung. Logistische Beherrschung von Fertigungs-abläufen auf Basis des Trichtermodells. Hanser Verlag, 1997.
- Schneider, M.: Lean Factory Design – Gestaltungsprinzipien für die perfekte Produktion und Logistik. Hanser Verlag, 2016.
- Suri, R.: Quick response manufacturing – A companywide approach to reducing lead times. Productivity Press, 1998.
- Wienecke, K.: Jenseits von MRP II ist die Luft noch dünn, 2003. Internet: https://www.computerwoche.de/a/jenseits-von-mrp-ii-ist-die-luft-noch-duenn,1056435. Zugriff am 09.11.2020
- Habicht, C.: Einsatz und Auslegung zeitfensterbasierter Planungssysteme in überbetrieblichen Wertschöpfungsketten. Institut für Werkzeugmaschinen und Betriebswissenschaften, 2008.
- Zelweski, S.; Hohmann, S.; Hügens, T.: Produktionsplanungs- und -steuerungssysteme: Konzepte und exemplarische Implementierungen mithilfe von SAP R/3. Oldenbourg Verlag, 2010.
- Schneider, M.: Prozessmanagement und Ressourceneffizienz – Der Weg zu nachhaltigen Wertschöpfung. Lean Media Verlag, 2012.
- Suri, R.: The practitioner‘s guide to POLCA. The production control system for high-mix, low-volume and custom products. CRC Press, 2018.
- Suri, R.: Erfolgsfaktor Zeit – Quick Response Manufacturing. BoD – Books on Demand, 2017.
- Erlach, K.: Wertstromdesign – Der Weg zur schlanken Fabrik. Springer Verlag, 2010.
- Stanula, P.; Metternich, J.; Glockeisen, T.: Selbstlernendes, dezentrales Produktionssystem in der Kleinserienfertigung. ZWF (2019), Nr. 6.
- Jeffrey, K. L.: Der Toyota-Weg: 14 Managementprinzipien des weltweit erfolgreichsten Automobilkonzerns. FinanzBuch Verlag, 2006.
Das könnte Sie auch interessieren:
Automatisierte Auftragsfertigung ersetzt manuelle Methoden
Wie PLM hilft, die Produktivität zu erhöhen und Wachstumsziele zu erreichen
Smarte Algorithmen automatisieren die Produktionsfeinplanung
Markus Schneider, Prof. Dr.-Ing., hat seit 2008 eine Professor für Logistik, Material- und Fertigungswirtschaft an der Hochschule Landshut inne. Er leitet mit drei weiteren Professoren das Technologiezentrum Produktions- und Logistiksystem (TZ PULS). Außerdem ist er geschäftsführender Gesellschafter der PuLL Beratung GmbH.
Patrick Rannertshauser, M. Eng., ist wissenschaftlicher Mitarbeiter am Technologiezentrum Produktions- und Logistiksystem (TZ PULS) in Dingolfing.