Technologievorsprung macht Randschichthärten attraktiver
Das Härten von industriell genutzten Maschinenelementen ist für deren Funktionsfähigkeit bei vielen Anwendungen unabdingbar. Die häufig eingesetzte, ofenbasierte Härtung hat jedoch Nachteile. Vorgestellt werden ausgefeilte Verfahrenstechniken zum Randschichthärten.
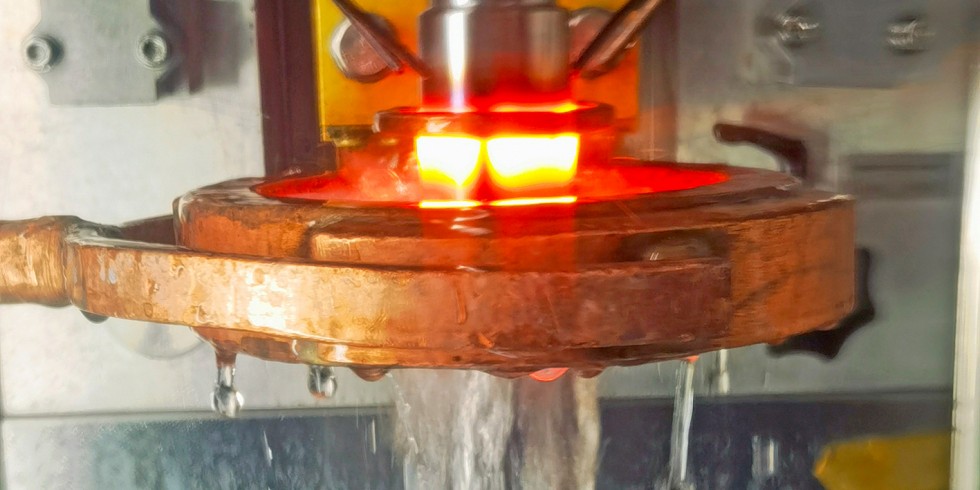
Automatisches induktives Randschichthärten des Bundes einer Welle im Durchlauf. Oben erzeugt der Induktor Rotglut, die rasche Abkühlung durch die nachfolgende Brause sorgt für die gewünschte harte Oberflächenschicht.
Foto: Klaus Vollrath
Bei zahlreichen in der Industrie verwendeten Bauteilen wird eine Kombination aus zähem Kern und harter Randschicht benötigt, damit sie den Beanspruchungen im Einsatz besser standhalten können. Das Härten geschieht durch schnelles Aufheizen der Oberfläche mit anschließender schneller Abkühlung. Hierfür stehen unterschiedliche Verfahren zur Verfügung. Je nach Bauteil und Aufgabenstellung zeichnen sich diese jedoch durch spezifische Vor- bzw. Nachteile aus. Das personell wie auch anlagentechnisch gut ausgestattete Kompetenzzentrum der Härterei Gerster AG berät Interessenten bei der Wahl und Auslegung von optimal auf die Aufgabenstellung angepassten Lösungsstrategien.
Worauf kommt es beim Härteprozess an?
„Beim Randschichthärten wird die oberflächennahe Randschicht von Bauteilen aus Stahl in einem definierten Bereich bis zu einer bestimmten Tiefe austenitisiert und anschließend schnell abgekühlt“, erläutert Beat Reinhard, Leiter Verfahrenstechnik und Entwicklung der Härterei Gerster AG in Egerkingen (Schweiz). Im Unterschied zu Ofenverfahren wie dem Einsatzhärten müsse beim Randschichthärten nicht das gesamte Volumen aufgeheizt werden. Das spare in erheblichem Umfang Energie. Jedoch sollte die Behandlung individuell auf die Gegebenheiten des Teils abgestimmt werden, wofür von Fall zu Fall nicht nur der Härteprozess an sich, sondern zusätzlich auch die vor- und nachgeschaltete Wertschöpfungskette zu berücksichtigen sei.
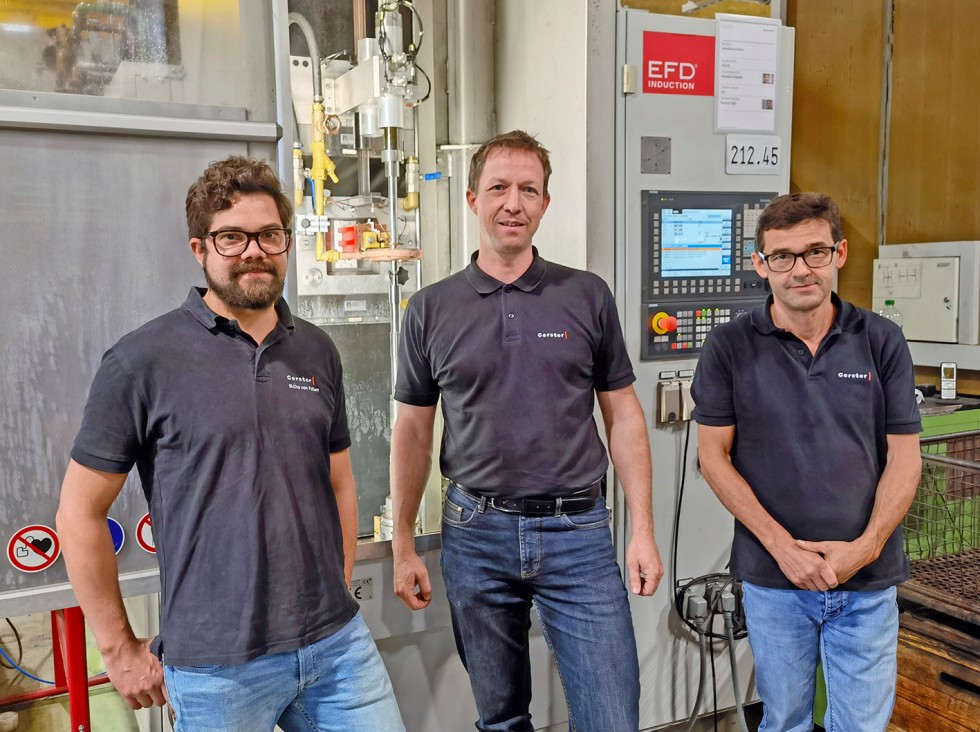
Das Kompetenz-Team beim Oberflächentechnik-Spezialisten: Projektingenieur Micha von Felten, Beat Reinhard (Leiter Verfahrenstechnik und Entwicklung) sowie Abteilungsleiter Peter Fluri (v.l.n.r.).
Foto: Privat
Der 1950 gegründete mittelständische Familienbetrieb Gerster mit rund 110 Mitarbeitern – und seit Kurzem auch einem deutschem Firmenstandort in Sprockhövel – verfügt auf diesem Gebiet dank langjähriger Erfahrung über umfassendes Know-how. Das Unternehmen ist nach eigenen Angaben Marktführer im Bereich Wärmebehandlungen in der Schweiz und bedient die Kunden höchst erfolgreich im Härten von nichtrostenden Stählen. Diese können auf kostensparende Lösungen zurückgreifen (www.hard-inox.de).
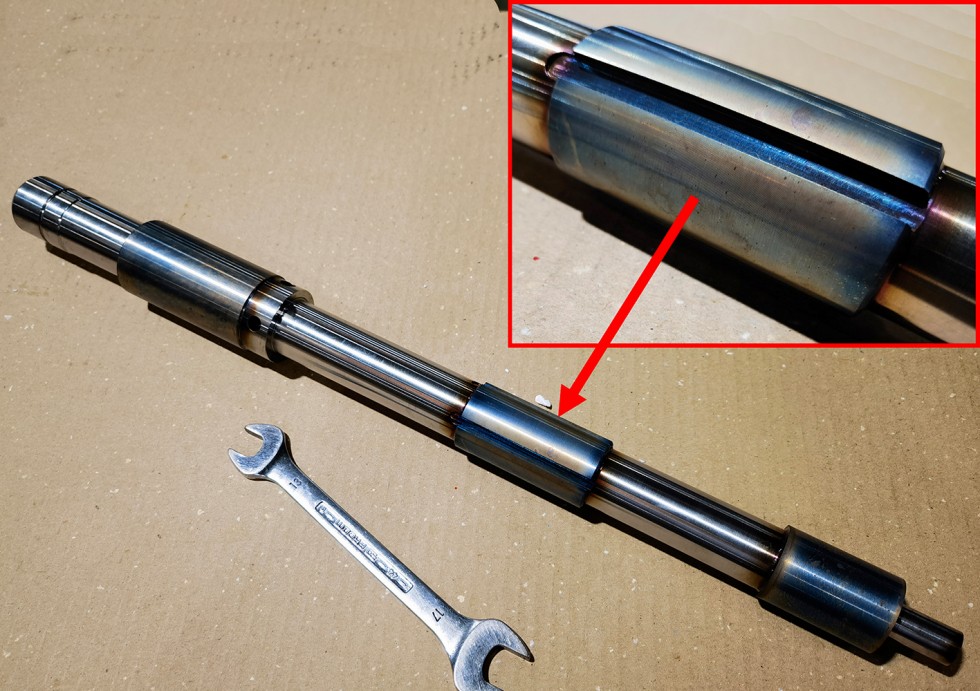
Die graue Oberfläche der Bundbereiche dieser Welle aus rostfreiem Stahl macht die erfolgreiche Härtung mithilfe des Induktionsverfahrens deutlich.
Foto: Klaus Vollrath
Zudem wird seit Jahrzehnten kontinuierlich in die Technologien investiert. Hinzu kommen zahlreiche Vorrichtungen sowie teils selbst entwickelte Automatisierungssysteme. Auch personell ist der Betrieb breit aufgestellt und dementsprechend leistungsfähig und reaktionsschnell. Unterstützt werden verschiedenste Branchen wie beispielsweise Maschinenbau, Hydraulik, Antriebstechnik, Automobilindustrie, Medizintechnik, Luftfahrt, Nuklearindustrie oder Lebensmittelindustrie.
Anwendungsbeispiel: Kurvenscheibe für einen Maschinenbaubetrieb
„Welche Vorteile sich durch eine Optimierung des Härteverfahrens ergeben können, zeigt das Beispiel einer Doppelkurvenscheibe für einen Maschinenhersteller“, ergänzt Micha von Felten, Projektingenieur bei der Firma Gerster. Hierbei handelt es sich um ein Verschleißteil für Textilmaschinen, das ständig am Lager gehalten werden muss. Früher wurde es in einem aufwendigen Verfahren zunächst geschmiedet und mechanisch vorbearbeitet. Anschließend wurde die Scheibe komplett gehärtet und kostenintensiv geschliffen. Die Vorratshaltung dieser teuren Teile band viel Kapital im Lager.
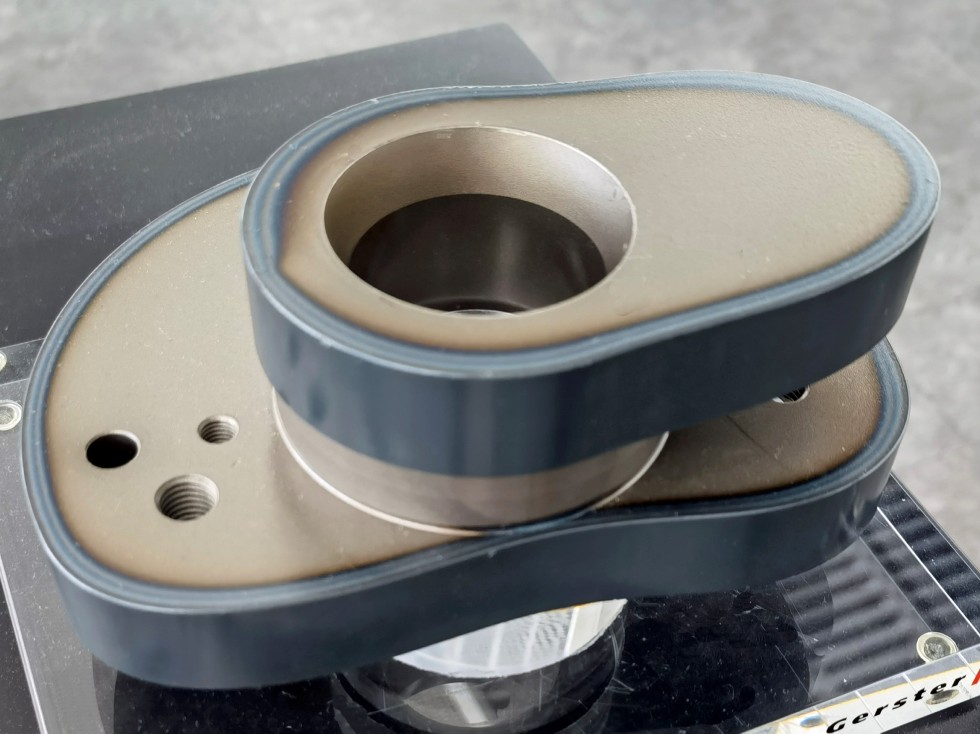
Die gesamte Prozesskette zur Herstellung dieser Doppel-Kurvenscheibe für eine Textilmaschine wurde erfolgreich auf Laserhärtung umgestellt.
Foto: Klaus Vollrath
In Zusammenarbeit mit dem Kunden wurde ein alternativer Prozesspfad entwickelt. Zum Aufgabenbereich der Härterei Gerster gehörte dabei die Unterstützung bei der Überprüfung und anschließenden Optimierung des gesamten Herstellprozesses sowie die Auswahl des optimalen Härteverfahrens aus dreizehn Grundverfahren. Anschließend wurde der Härteprozess gewählt und auf die Anwendung – u. a. die gewünschte Lage der Härte- und Schlupfzonen – abgestimmt.
Im Ergebnis verringerte sich der Kostenaufwand für die Herstellung mit dem neuen Prozess um rund 50 Prozent. Nach dem Schmieden und der Bearbeitung auf Fertigmaß wird die Kurvenscheibe jetzt nur noch im Bereich der Laufflächen mit dem Laserverfahren gehärtet und anschließend mittels Gleitschleifen gefinisht. Den entscheidenden Anteil an der Kostenminderung hatte das Weglassen des teuren CNC-Schleifens. Hinzu kamen noch weitere wesentliche Vorteile: Die Wiederbeschaffungszeit verringerte sich von 80 auf 20 Tage, die Losgröße konnte von 100 auf 50 Stück gesenkt werden und die Kapitalbindung im Lager ging um 75 Prozent zurück.
Vor- und Nachteile der drei wichtigsten Verfahren
„Die drei bei uns hauptsächlich eingesetzten Verfahren zur Randschichthärtung sind das Flammhärten, das Induktionshärten sowie das Härten mithilfe des Lasers“, erklärt Beat Reinhard. Das Flammhärten mit Gasbrennern ist das älteste Verfahren und hat immer noch rund 10 Prozent Anteil an den bei Gerster durchgeführten Randschichthärte-Behandlungen. Da die Wärme der Gasbrenner von der Oberfläche her ins Innere der Bauteile eindringen muss, sind die Prozesszeiten bei größeren Einhärtungstiefen entsprechend lang. Die Leistung ist jedoch durch Einsatz von mehr Brennern gut skalierbar. Das Verfahren eignet sich besonders gut für Bauteile mit größeren Abmessungen und bei größeren Einhärtungstiefen – in speziellen Fällen können das auch mal 40 Millimeter sein. Zur Abschreckung kommen je nach Einsatzfall Wasser, Polymergemische, Öl, Schutzgas oder Druckluft zum Einsatz.

Eine bei der Härterei Gerster selbst entwickelte und realisierte Anlage mit zahlreichen Brennern, Pyrometern und Regelzonen für das Flammhärten von runden Bauteilen. Diese können Durchmesser bis 1,4 m und Höhen bis 650 mm haben.
Foto: Klaus Vollrath
Das Induktionshärten erfolgt mit Induktoren (Spulen) zur Übertragung von Energie mit Frequenzen zwischen 10–1200 Kilo-Hertz. Die Wechselfelder bringen mithilfe der formangepassten Induktoren Energie direkt ins Innere des Werkstoffs ein. Dadurch läuft das Aufheizen schneller als beim Flammhärten ab. Die Einhärtungstiefe kann bis zu 5 Millimetern betragen. Der Prozess lässt sich elektronisch äußerst präzise und wiederholgenau steuern und ist dadurch sehr gut beherrschbar. Abgeschreckt wird mit den gleichen Medien wie beim Flammhärten.
Domäne des Laserhärtens ist das Erzeugen von örtlich sehr genau definierten, vergleichsweise dünnen (typischerweise etwa ein Millimeter tief) gehärteten Oberflächen. Der energiereiche Laserstrahl bewirkt eine extrem schnelle Erwärmung der Oberflächenschicht, die vom kalten Materialinneren dann äußerst rasch wieder abgekühlt wird. So entsteht eine Härteschicht mit sehr feinkörnigem Martensit. Eine Anlassbehandlung ist üblicherweise nicht erforderlich und die Teile erleiden nur minimalen Verzug. Das Verfahren ist hoch produktiv und damit kostengünstig. Der Laserstrahl wird durch einen Roboter hochpräzise geführt, sodass die Härtung nur in genau definierten Bereichen abläuft. Bei Einsatz von Schutzgas bleiben die Oberflächen zudem blank.
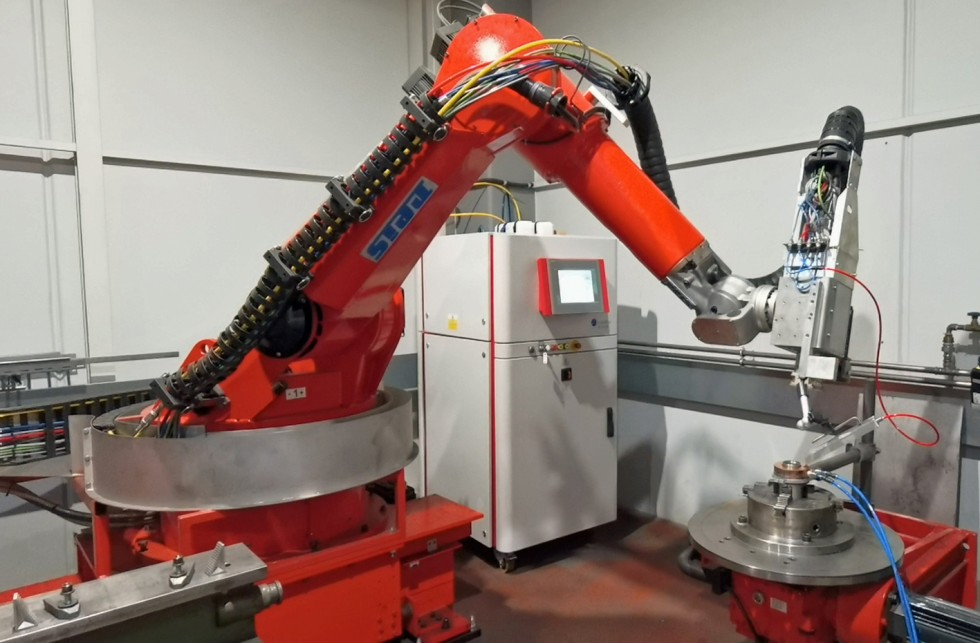
Der Roboter für das Führen des Lasers. Dank seiner Laufschiene kann er auch Langteile bis 9.000 mm bearbeiten.
Foto: Klaus Vollrath
Erfolgsfaktoren: Beratungskompetenz und Verfahrensbandbreite
„Das Randschichthärten erfordert stets eine teilespezifische Anpassung des Prozesses“, weiß Maik von Felten. Deshalb gebe es so gut wie nie „Patentlösungen von der Stange“. Dazu sei die Bandbreite der Geometrien, der Werkstoffe und der geforderten Eigenschaften einfach zu groß. Hinzu kämen kaufmännische Gesichtspunkte wie Stückzahlen, Logistikanforderungen sowie die Herstellung teilespezifischer Vorrichtungen oder sogar kompletter Anlagen z.B. für das Flammhärten von Rundteilen mit großen Abmessungen.
Voraussetzung für die Findung einer technisch wie kostenmäßig optimalen Lösung sei daher vor allem viel Erfahrung. Häufig gehöre dazu auch die Realisierung spezieller Vorrichtungen oder individueller Handling- bzw. Automatisierungslösungen.
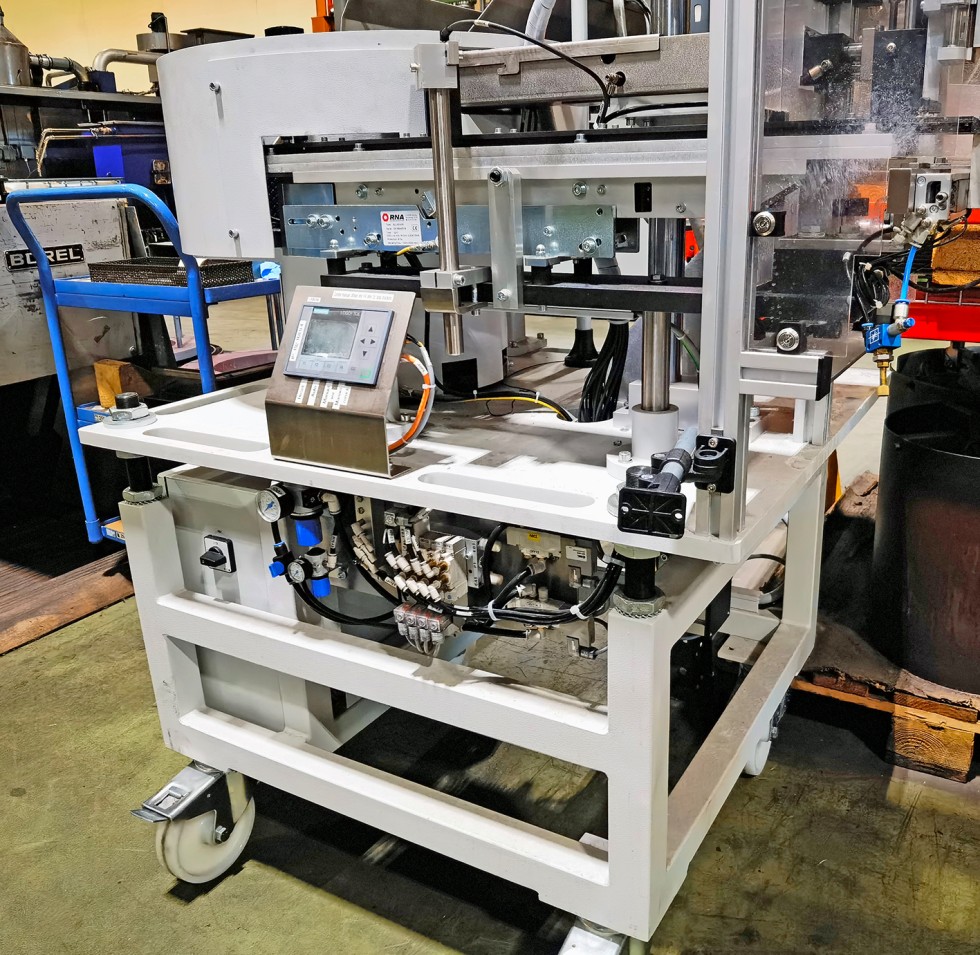
Rollwagen mit Handlingsystem für die automatische Zuführung von Massenteilen. Bei größeren Serien kann der Wagen mit wenigen Handgriffen an eine sonst manuell bediente Anlage für das Induktionshärten von Kleinteilen angedockt werden.
Foto: Klaus Vollrath
Bei größeren Auftragsvolumina oder auch aufgrund von speziellen Anforderungen macht es manchmal Sinn, den Härteprozess direkt in die Produktionslinie eines Kunden zu integrieren. Der hoch qualifizierte Dienstleister steht diesen Anliegen offen gegenüber und unterstützt solche Verlagerungen im Rahmen der „Gerster Support Services“. So kann der Kunde bei Bedarf sogar eine Rückabsicherung vereinbaren, falls es in seiner eigenen Anlage zu Problemen oder Engpässen kommen sollte.
Ergänzend zu seinen flexiblen und leistungsfähigen internen Abteilungen für Konstruktion, Beratung, Prozessentwicklung und Fertigung kann sich Gerster bei solchen Dienstleitungen auch auf ein breitgespanntes und bewährtes Netzwerk von Zulieferern und Engineering-Dienstleistern stützen. Dies umfasst zum Beispiel den 3D-Druck von Induktoren, Brennern oder Brausen, die Simulation von Wärmebehandlungsprozessen oder den Anlagenbau.
Elementar: Reaktionsgeschwindigkeit und Flexibilität
„Unsere Kunden stehen in der Regel unter starkem Zeitdruck. Deshalb legen wir Wert darauf, auf Anfragen oder Aufträge möglichst schnell zu reagieren“, verrät Beat Reinhard. Das fange schon damit an, dass das Unternehmen keine Betriebsferien mache und die Urlaube der Mitarbeiter so synchronisiere, dass für jeden Kompetenzbereich immer eine ausreichende Zahl von Fachleuten mit der erforderlichen Qualifikation verfügbar sei. Je nach Anwendungsfall umfasse der Service auch eine Konstruktionsberatung, beispielsweise wenn es um die Beurteilung von Risiken bezüglich Spannungen, Verzug oder Rissbildung gehe.
„Das Randschichthärten erfordert stets eine teilespezifische Anpassung des Prozesses. Deshalb gibt es so gut wie nie Patentlösungen von der Stange.“
Flexibel ist auch die Reaktion auf Anfragen, bei denen die Dimensionen oder das Gewicht der zu behandelnden Werkstücke die Möglichkeiten der eigenen betrieblichen Infrastruktur übersteigen. Dann werden auch mobile Behandlungen vor Ort oder Möglichkeiten innerhalb des bereits erwähnten Zulieferer-Netzwerks geprüft und bei Eignung vorgeschlagen.
Qualitätssicherung auf hohem Niveau gehört dazu
Zu den Arbeiten gehört selbstverständlich auch eine leistungsfähige Qualitätssicherung. Den Mitarbeitern stehe eine große Bandbreite an modernen Verfahren vom Lichtmikroskop über die verschiedensten Härteprüfverfahren bis zur Spektralanalyse zur Verfügung. Selbstverständlich verfügt das Unternehmen auch über Zertifizierungen für wichtige allgemeine Qualitätsmanagementsysteme wie ISO 9001 und ISO 14001 sowie über branchenspezifische QS-Systeme für die Automobilindustrie, die Medizintechnik und die Luft- und Raumfahrt.
Für das Randschichthärten sind am Standort Egerkingen in der Schweiz rund 50 verschiedene Anlagen im Einsatz. Das insgesamt angebotene Portfolio an Wärmebehandlungsdienstleistungen ist jedoch erheblich breiter und umfasst im Prinzip die gesamte Bandbreite der klassischen Härtereidienstleistungen. Um die immer zahlreicheren deutschen Kunden besser betreuen zu können, wurde 2022 in Sprockhövel die Gerster Deutschland GmbH gegründet.
Das könnte Sie auch interessieren:
Lötprozesse nachhaltig und taktzeitoptimiert gestalten
Klaus Vollrath arbeitet für das Redaktionsbüro Vollrath in Aarwangen/Schweiz.