Unterstützung bei der Einführung von KI in der Produktion
Künstliche Intelligenz (KI) bietet erhebliche Chancen zur Optimierung von Prozessen und Geschäftsmodellen entlang der Wertschöpfungskette von produzierenden Unternehmen. Dennoch zögern viele Betriebe bei der Umsetzung von KI-Projekten. Jetzt gibt es Hilfestellung durch ein Netzwerk.
![Exemplarisches Prozessergebnis aus dem ProKI-Netz: Lasergeschweißte Hairpin-Verbindungen haben einen entscheidenden Einfluss auf die finale Qualität des gefertigten Stators. Links: korrekte Verbindung; rechts: fehlerhafte Kontaktstelle nach [22]. Foto: FAPS/Fau](https://www.ingenieur.de/wp-content/uploads/2024/10/Bild-0-Exemplarisches-Prozessergebnis-Laserschweissen-1200x600.jpg)
Exemplarisches Prozessergebnis aus dem ProKI-Netz: Lasergeschweißte Hairpin-Verbindungen haben einen entscheidenden Einfluss auf die finale Qualität des gefertigten Stators. Links: korrekte Verbindung; rechts: fehlerhafte Kontaktstelle nach [22].
Foto: FAPS/Fau
Um das bisher verhaltene Tempo bei der KI-Einführung zu adressieren, wird gezeigt, wie Unternehmen bei der Realisierung von KI-Projekten durch das universitäre ProKI-Netz erfolgreich unterstützt werden. Zudem werden drei KI-Use-Cases aus dem Bereich der Fügetechnik vorgestellt, die am ProKI-Zentrum in Nürnberg erarbeitet wurden.
Ausgangssituation: vor allem KMU nutzen KI-Technologien selten
Die Methoden der Künstlichen Intelligenz (KI) halten zunehmend Einzug in die industrielle Produktion [1]. Die Potenziale zur Optimierung von Prozessen und Geschäftsmodellen entlang der gesamten Wertschöpfungskette, von der Logistik bis hin zu einzelnen Fertigungs- und Montageprozessen, sind bereits in verschiedenen Studien beleuchtet worden [1–5]. Dennoch zeigen viele Unternehmen, insbesondere kleinere und mittlere Unternehmen (KMU), Zurückhaltung bei der Umsetzung von KI-Projekten. Dies liegt hauptsächlich an fehlenden Kompetenzen und Ressourcen. Viele KMU scheuen den vermeintlich hohen Aufwand und das Investitionsrisiko, da sie oft nicht über das notwendige Fachpersonal verfügen [1]. Während 25 Prozent der Großunternehmen bereits KI-Technologien einsetzen, liegt dieser Anteil bei KMU nur bei 15 Prozent [5]. Angesichts der hohen Lohnkosten und der alternden Bevölkerung ist Deutschland – als ein hoch entwickeltes Industrieland – in besonderer Weise auf den Transfer von Erfahrungswissen und die Automatisierung mittels KI angewiesen, um seine Wachstumsziele zu erreichen [4]. Besonders das produzierende Gewerbe stellt einen wichtigen Bereich für künftige KI-Anwendungen dar [5].
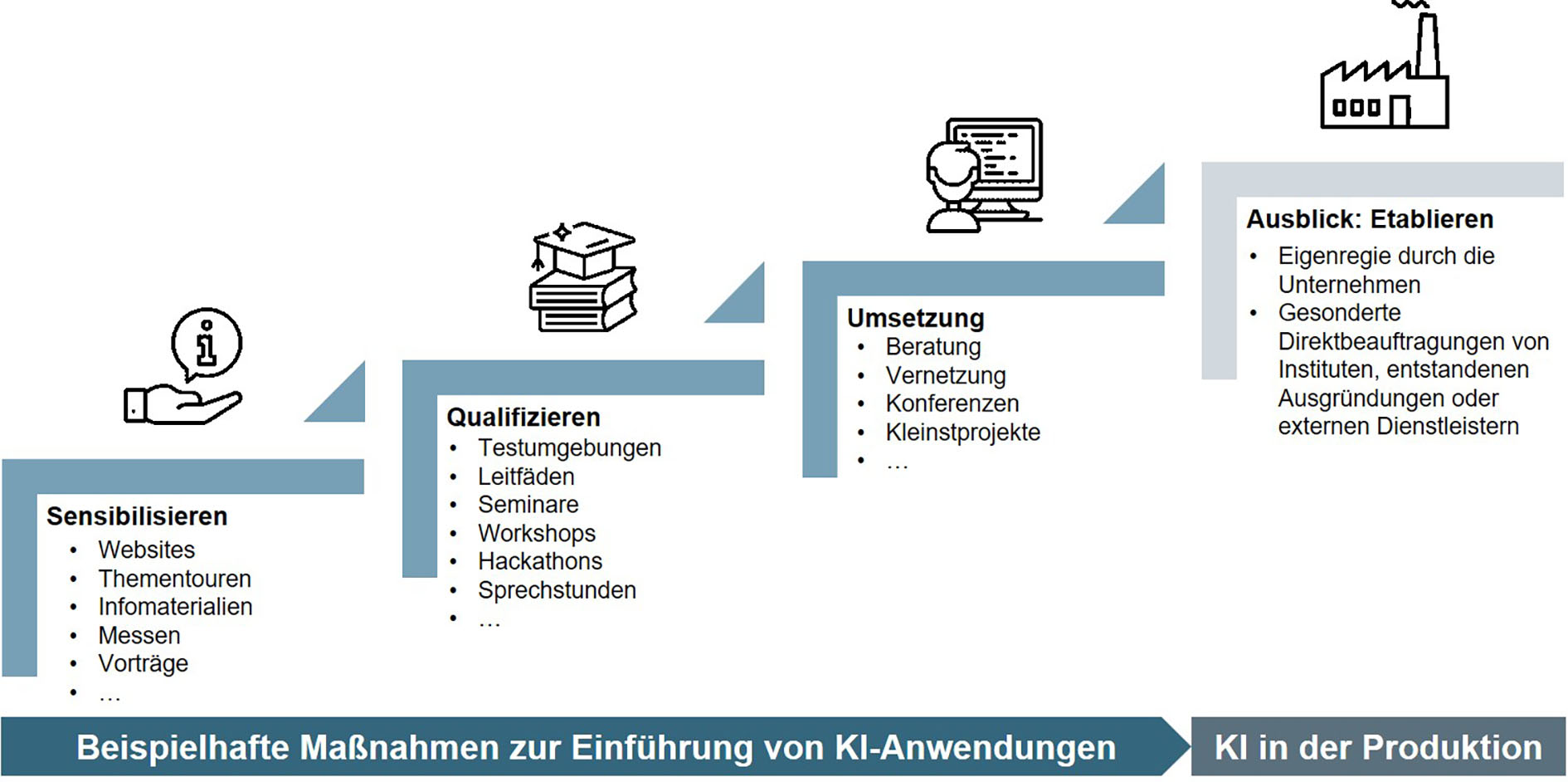
Die Vorgehensweise im ProKI-Netz zur Unterstützung von produzierenden Unternehmen bei der Einführung von Künstlicher Intelligenz. Grafik: FAPS/Fau
Potenziale und Herausforderungen der KI im produzierenden Gewerbe
Die Verwendung von KI im industriellen Umfeld bietet eine weite Spanne von Potenzialen. Im Bereich der prädiktiven Instandhaltung können Wartungsintervalle von Maschinen und Anlagen durch die Einbindung von KI-Verfahren optimiert werden, sodass Stillstände vermieden und Ressourcen optimal eingesetzt werden können. Auch bei der Qualitätskontrolle können KI-Verfahren Anwendung finden, beispielsweise zur Fehlererkennung basierend auf Bilddaten. Durch kontextspezifische Arbeitsanweisungen können KI-basierte Assistenzsysteme die Mitarbeiter bei manuellen Tätigkeiten unterstützen und Einlernzeiten reduzieren. Die im Zuge der Automatisierung zunehmend eingesetzten kollaborativen, sensorgestützten Leichtbauroboter entfalten ihr volles Potenzial erst durch die Kombination mit KI-Verfahren, etwa zur Realisierung komplexer Handhabungs- und Fügeoperationen – basierend auf bestärkendem Lernen. Weitere Anwendungsfelder der KI können Studien wie [1–6] entnommen werden. [1, 3]
Für den Einsatz von KI ergeben sich jedoch, je nach Use Case, auch verschiedene Herausforderungen, welche eine Umsetzung erschweren. Grundlegend für die erfolgreiche Anwendung von KI-Verfahren ist die Nutzung einer geeigneten Datenbasis. Ein prozessorientiertes Vorgehen, das vom zu optimierenden Produktionsprozess ausgeht, erlaubt die Definition der Bedarfe für einen dafür geeigneten KI-Einsatz und stellt sicher, dass relevante Daten gezielt für diesen spezifischen Zweck erhoben werden [3]. Die Relevanz dieser Daten kann durch domänenspezifisches Wissen evaluiert werden, sodass insgesamt eine höhere Datenqualität erreicht wird, die sich positiv auf die Effizienz der KI-Modelle auswirkt [3]. Für die Erhebung der Daten muss entsprechende Sensorik mit ausreichender Genauigkeit und Auflösung integriert sein. Eine Systematik zum Aufbau einer geeigneten Datenbasis für KI-Anwendungen im produzierenden Gewerbe ist in [7] beschrieben. Zudem sind für die Datenspeicherung und die Ausführung der KI-Modelle die notwendigen Speicher- und Rechenressourcen bereitzustellen. Lösungen hierfür können beispielsweise Cloud- und Edge-Technologien bieten. Im Zuge dessen spielt die Datenhoheit eine entscheidende Rolle [5].
Aufbau des ProKI-Netzes als bundesweites Demonstrations- und Transfernetzwerk
Ausgehend von den Herausforderungen, die sich mit der Anwendung von KI-Verfahren in der Praxis ergeben, lässt sich insbesondere ein Unterstützungsbedarf bei KMU ableiten. Daher wurde seitens des Bundesministeriums für Bildung und Forschung (BMBF) das sogenannte ProKI-Netz [8] ins Leben gerufen, welches aus insgesamt acht universitären Demonstrations- und Transferzentren besteht, die sich über ganz Deutschland verteilen. Es hat sich zum Ziel gesetzt, Erkenntnisse aus der universitären KI-Forschung in die industrielle Praxis zu übertragen. Interessierte Unternehmen werden sowohl bei der Identifizierung als auch Umsetzung von KI-Use-Cases begleitet, um nachhaltige KI-Lösungen im Unternehmen zu etablieren. Neben der Friedrich-Alexander-Universität in Erlangen-Nürnberg sind Universitäten aus Hannover, Berlin, Aachen, Dresden, Ilmenau, Darmstadt und Karlsruhe am ProKI-Netz beteiligt. Jeder dieser Standorte fokussiert sich auf einen gewissen Schwerpunkt, etwa KI-Anwendungen in der Füge-, Umform- oder Trenntechnik.
Zunächst wird das generelle Vorgehen des ProKI-Netzes zur Unterstützung von Unternehmen bei der Einführung von KI-Anwendungen dargestellt. Im Anschluss werden drei KI-Use-Cases vorgestellt, welche von ProKI-Nürnberg in Form von Demonstratoren implementiert wurden. Sie können als Orientierungshilfe für Unternehmen mit gleichen oder ähnlichen Problemstellungen dienen.
Vorgehensweise zur Unterstützung von produzierenden Unternehmen bei der Einführung von KI
Zur Unterstützung von Unternehmen bei der Identifikation und Realisierung von KI-Anwendungen wurde innerhalb des ProKI-Netzes ein vierstufiges Vorgehen definiert. Die erste Phase umfasst die Sensibilisierung von Mitarbeitern hinsichtlich der Chancen und Herausforderungen von KI. Die zweite Phase setzt sich aus verschiedenen Qualifizierungsmaßnahmen zusammen, um Unternehmen dazu zu befähigen, vielversprechende KI-Use-Cases selbstständig zu identifizieren, zu bewerten und zu implementieren. In der darauffolgenden Umsetzungsphase werden interessierte Unternehmen bei der Implementierung ausgewählter KI-Use-Cases durch die Experten des ProKI-Netzes unterstützt. Die letzte Phase gibt einen Ausblick auf die langfristige Etablierung, Weiterentwicklung und Wartung der umgesetzten KI-Use-Cases, die maßgeblich durch die Unternehmen selbst oder zwischenzeitlich einbezogene IT-Dienstleister erfolgt. Das Einstiegsbild zeigt dieses Vorgehen mitsamt beispielhaften Maßnahmen für jede der vier Phasen.
1. Sensibilisierung
In der ersten Stufe geht es darum, Unternehmen und ihre Mitarbeiter für das Thema KI zu sensibilisieren. Ziel ist es, das Bewusstsein für die Chancen und Herausforderungen von KI zu schärfen und ein grundlegendes Verständnis zu schaffen. Diese Phase ist entscheidend, um Berührungsängste abzubauen und die Bereitschaft für die Integration von KI-Technologien zu fördern. Durch gezielte Informationskampagnen und praxisnahe Demonstrationen soll das Interesse geweckt und die Vorteile von KI-Anwendungen verdeutlicht werden.
Beispielhafte Maßnahmen zur Sensibilisierung umfassen die Bereitstellung von adressatengerechtem Informationsmaterial über verschiedene Kanäle wie die ProKI-Website [8], YouTube oder Messestände. Vorführungen und Videos zu KI-Demonstratoren zeigen interessierten Unternehmen die Anwendungsmöglichkeiten und den Nutzen von KI auf.
2. Qualifikation
Die zweite Stufe umfasst die Qualifikation der Mitarbeiter durch gezielte Weiterbildung und Schulung. Hierbei sollen die notwendigen Kenntnisse und Fähigkeiten vermittelt werden, um KI-Technologien im eigenen Unternehmen anwenden zu können. Diese Phase ist entscheidend, um die theoretische Basis zu schaffen und praktische Fähigkeiten zu entwickeln, die für die erfolgreiche Implementierung von KI notwendig sind.
Beispielhafte Maßnahmen zur Qualifikation sind die Bereitstellung von umfassenden Leitfäden und Handlungsempfehlungen, die konkrete Anleitungen zur Implementierung von KI bieten. Weiterhin können Seminare und Workshops des ProKI-Netzes besucht werden, die sowohl theoretische als auch praktische Einblicke in spezifische KI-Anwendungen geben. Die Teilnahme an Hackathons ermöglicht eine praxisnahe Anwendung und Vertiefung des erlernten Wissens, indem Mitarbeiter in interdisziplinären Teams konkrete KI-Projekte bearbeiten. Zudem können die Demonstratoren an den einzelnen ProKI-Zentren als vorwettbewerbliche Testumgebung für interessierte Unternehmen dienen, um eigene KI-Ansätze zu erproben.
3. Umsetzung
In der dritten Stufe steht die konkrete Umsetzung von KI-Projekten im Fokus. Unternehmen sollten dabei unterstützt werden, vielversprechende KI-Use-Cases zu identifizieren, Machbarkeitsstudien durchzuführen und entsprechende Projekte zu starten. Die Umsetzungsphase ist entscheidend, um die theoretischen Kenntnisse und praktischen Fähigkeiten in realen Projekten anzuwenden und die ersten Erfolge zu erzielen. Beispielhafte Maßnahmen zur Umsetzung beinhalten individuelle Beratungsangebote, die Unternehmen bei der Bewertung des KI-Reifegrads, der Machbarkeit von KI-Use-Cases und der Make-or-Buy-Entscheidung unterstützen. Unternehmen können zudem Beratung bei der Zusammenstellung interdisziplinärer KI-Projektteams, bei der Projektplanung und -durchführung und der Auswahl geeigneter externer Partner anfordern.
Den mittlerweile wichtigsten Teilbereich der KI stellt das Maschinelle Lernen (ML) dar. Durch ML wird es Computersystemen ermöglicht, automatisch Muster in Daten zu erkennen und die erkannten Muster zu verwenden, um Vorhersagen für zukünftige Daten zu treffen [9].
![Bild 1. Cross Industry Standard Process for Data Mining (CRISP-DM) zur Umsetzung von ML-Projekten. Grafik in Anlehnung an [10]. Grafik: FAPS/Fau](https://www.ingenieur.de/wp-content/uploads/2024/10/Bild-1-Cross-Industry-Standard-Process-for-Data-Mining.jpg)
Bild 1. Cross Industry Standard Process for Data Mining (CRISP-DM) zur Umsetzung von ML-Projekten. Grafik in Anlehnung an [10]. Grafik: FAPS/Fau
Zur Umsetzung von ML-Projekten eignet sich in den meisten Fällen der bewährte „Cross Industry Standard Process for Data Mining“ (CRISP-DM) [10], siehe Bild 1. Der CRISP-DM unterteilt sich in sechs Phasen, welche zyklisch durchlaufen werden, um die anvisierte ML-Lösung zu entwickeln, zu evaluieren und iterativ zu optimieren. Aufgrund des agilen Charakters von ML-Projekte sind Rücksprünge auf vorhergehende Phasen möglich, um bei entdeckten Unzulänglichkeiten direkt Anpassungen in den entsprechenden vorhergehenden Phasen, etwa der Datenvorbereitung, vornehmen zu können.
Phasen des CRISP-DM sind:
- Geschäftsverständnis: Diese Anfangsphase konzentriert sich darauf, die Projektziele und -anforderungen aus geschäftlicher Sicht zu verstehen und in eine Definition des ML-Problems sowie einen Projektplan zur Erreichung der Ziele zu überführen [10].
- Datenverständnis: Die Phase des Datenverständnisses beginnt mit einer ersten Datensammlung und umfasst Aktivitäten, um sich mit den Daten vertraut zu machen, Datenqualitätsprobleme zu identifizieren, erste Einblicke in die Daten zu gewinnen und Hypothesen für versteckte Informationen zu bilden. Die Phasen „Geschäftsverständnis“ und „Datenverständnis“ können mithilfe von Werkzeugen wie dem „Industrial AI Canvas“ [11] unterstützt werden. Dieses ist am „Business Modell Canvas“ [12] orientiert und umfasst verschiedene Fragestellungen unterteilt in neun Blöcken, welche unter anderem dazu dienen, die Problemstellung, Datenverfügbarkeit und -qualität, den Use Case und den Nutzen der anvisierten ML-Anwendung zu spezifizieren [10].
- Datenvorbereitung: Die Phase der Datenvorbereitung umfasst alle Aktivitäten, um aus den Rohdaten den endgültigen Datensatz zu erstellen, welcher in der nachfolgenden Modellierung verwendet wird. Die phasenspezifischen Aufgaben beinhalten die Auswahl von repräsentativen Datenpunkten, Attributen und Annotationen sowie die Transformation und Bereinigung der Daten [10].
- Modellierung: In dieser Phase werden verschiedene Modellarchitekturen und Lernalgorithmen ausgewählt, implementiert sowie deren Parameter optimiert. Da es meist eine Vielzahl von möglichen ML-Ansätzen für eine gegebene Problemstellung, die mit spezifischen Anforderungen an die Datenvorbereitung einhergehen, sind oftmals Rücksprünge zur vorhergehenden Phase nötig [10].
- Auswertung: Bevor ein erstelltes ML-Modell endgültig eingesetzt werden kann, ist es wichtig, es gründlich zu bewerten und sämtliche Schritte der Modellerstellung zu überprüfen, um sicherzustellen, dass es die Geschäftsziele erreicht. Am Ende dieser Phase sollte eine Entscheidung über die Nutzung des Modells getroffen werden.
- Bereitstellung: Falls das ML-Modell alle gesetzten Anforderungen erfüllt, wird es in der letzten CRISP-DM-Phase in die Produktionsumgebung integriert. Das gewonnene Wissen muss für den Kunden nutzbar gemacht werden. Dies kann den Einsatz von Modellen in Entscheidungsprozessen umfassen. Oft führt der Kunde diese Schritte selbst durch, muss aber von Anfang an wissen, welche Maßnahmen nötig sind, um die Modelle effektiv zu nutzen.
4. Etablierung
Die begleitete Bereitstellung des ML-Modells bildet den Übergang zur letzten Stufe des ProKI-seitigen Vorgehens. Die Stufe der Etablierung zielt darauf ab, die umgesetzten KI-Anwendungen nachhaltig im Unternehmen zu etablieren. Die eingeführten KI-Lösungen sollen langfristig im Unternehmensalltag verankert und kontinuierlich weiterentwickelt werden. Diese Phase ist entscheidend, um die erzielten Erfolge zu festigen und die KI-Technologien dauerhaft in die Unternehmensprozesse zu integrieren.
Wie dem Einstiegsbild zu entnehmen ist, ist die letzte Phase kein zentraler Bestandteil der Unterstützungsmöglichkeiten seitens des ProKI-Netzes. Auf Basis der angebotenen Qualifizierungs- und Beratungsleistungen sollen Unternehmen die Etablierung entweder möglichst eigenständig durchführen oder externe Partner (zum Beispiel gesonderte Beauftragung von IT-Dienstleistern oder Instituten) einbeziehen. Durch regelmäßige Weiterbildungen ist seitens der Unternehmen sicherzustellen, dass die Mitarbeiter hinsichtlich der neuesten KI-Entwicklungen auf dem Laufenden bleiben und ihre Kompetenzen kontinuierlich erweitern. Darüber hinaus trägt die Partizipation und Pflege einer starken, unternehmensübergreifenden ProKI-Community dazu bei, von einem steten Wissensaustausch zwischen Unternehmen und Fachleuten zu profitieren.
Vorstellung ausgewählter KI-Demonstratoren des ProKI-Standorts in Nürnberg
Um Unternehmen das Potential von KI anhand von konkreten Anwendungsfällen zu demonstrieren, wurde an den Standorten des ProKI-Netzes eine Vielzahl an KI-Demonstratoren implementiert. Die erarbeiteten Demonstratoren sollen die Bestandteile und Funktionsweise von KI-Systemen im Produktionsumfeld illustrieren und als Anregung zur Identifizierung von KI-Use-Cases im eigenen Unternehmen dienen. Der ProKI-Standort in Nürnberg [13] fokussiert sich insbesondere auf KI-Anwendungen im Bereich der Fügetechnik. Die DIN 8580 [14] definiert das Fügen als ein „auf Dauer angelegtes Verbinden oder sonstiges Zusammenbringen von zwei oder mehreren Werkstücken geometrisch bestimmter fester Form oder von eben solchen Werkstücken mit formlosem Stoff; dabei wird der Zusammenhalt örtlich geschaffen und im Ganzen vermehrt.“ Gemäß DIN 8593 [15] lässt sich das Fügen in neun Verfahrensgruppen unterteilen, zu denen unter anderem das „Fügen durch Löten“ sowie das „Fügen durch Schweißen“ gehören. Um ebendiese beiden Verfahrensgruppen soll es auch in den nachfolgend vorgestellten KI-Demonstratoren von ProKI-Nürnberg gehen, die vielversprechende Use Cases aus dem Bereich der Elektronik- und Elektromotorenproduktion aufgreifen und sich in dieser oder ähnlicher Form auch in Unternehmen umsetzen lassen.
Automatische Optische Inspektion von Lötstellen
Bei klassischen Systemen zur Automatischen Optischen Inspektion (AOI) von Lötstellen stellt das häufige Auftreten von Pseudofehlern ein weit verbreitetes Problem dar. Solche Pseudofehler können vermeintliche Defekte wie unzureichende Lötqualität, Versatz, fehlende oder falsch orientierte Bauteile betreffen. Um diese Pseudofehler zu identifizieren und ein voreiliges Ausschleusen teilweise kostspieliger Bauteile zu vermeiden, wird in der Regel eine manuelle Nachinspektion durchgeführt. Diese manuelle Nachprüfung ist jedoch mit einem hohen Arbeitsaufwand verbunden.
![Bild 2. Inspektionsbilder von korrekt ausgerichteten SMT-Bauteilen mit einem Pseudofehler, einer vermeintlichen Verpolung (a), sowie einer richtigen Erkennung der passenden Polarität (b). Foto in Anlehnung an [16]. Grafik: FAPS/Fau](https://www.ingenieur.de/wp-content/uploads/2024/10/Bild-2-Inspektionsbilder.jpg)
Bild 2. Inspektionsbilder von korrekt ausgerichteten SMT-Bauteilen mit einem Pseudofehler, einer vermeintlichen Verpolung (a), sowie einer richtigen Erkennung der passenden Polarität (b). Foto in Anlehnung an [16]. Grafik: FAPS/Fau
Beispielhaft ist in Bild 2 ein Pseudofehler für die Polarität einer LED (a) sowie eine korrekt platzierte LED (b) dargestellt. Bei der konventionellen Testroutine wird dabei in dem relevanten markierten Bereich eine Kantenerkennung durchgeführt. Ist die Differenz der Grauwerte dabei unter einem fest definierten Grenzwert, wird das Bauelement als Defekt identifiziert, was in diesem Fall zu einem Pseudofehler führt. Auch wenn der Polaritätsmarker für einen Menschen ohne Probleme zu identifizieren ist, können kleinere Abweichungen bei der Belichtung oder durch Abschattung zu so einem Pseudofehler führen. Bei einem tatsächlichen Fehler wäre die LED um 180° gedreht.
Um den Aufwand für die manuelle Nachinspektion zu reduzieren, wurde im Zuge des vorliegenden KI-Use-Cases das auf klassischer Bildverarbeitung basierende AOI-System einer Surface Mount Technology (SMT)-Linie um eine zusätzliche KI-Komponente erweitert. Zur Ausführung der KI-Komponente wurde ein leistungsfähiges Edge-Gerät in das Inspektionssystem integriert und die Benutzeroberfläche erweitert. Anhand historischer Daten wurde ein KI-Modell trainiert, welches im Falle eines vermeintlichen Defekts eine zusätzliche Bewertung des Inspektionsbildes durchführt. Um sicherzustellen, dass kein Fehlerschlupf auftritt, wurde ein kritischer Konfidenzwert definiert, den das Modell bei einer Prognose erreichen muss, um einen Fehler als Pseudofehler zu deklarieren, Bild 3.
![Bild 3. Funktionsweise des ML-basierten Systems zur Reduzierung von Pseudofehlern unter Zuhilfenahme eines kritischen Konfidenzwertes des Modells. Grafik in Anlehnung an [16]. Grafik: FAPS/Fau](https://www.ingenieur.de/wp-content/uploads/2024/10/Bild-3-Funktionsweise-des-ML-basierten-Systems.jpg)
Bild 3. Funktionsweise des ML-basierten Systems zur Reduzierung von Pseudofehlern unter Zuhilfenahme eines kritischen Konfidenzwertes des Modells. Grafik in Anlehnung an [16]. Grafik: FAPS/Fau
Wird dieser Wert erreicht, wird die Lötstelle als in Ordnung (i. O.) betrachtet und erfordert keine weitere Inspektion, wodurch der manuelle Aufwand direkt reduziert wird. Wird der kritische Konfidenzwert nicht erreicht, ist weiterhin eine manuelle Inspektion erforderlich. In diesem Fall wird der Konfidenzwert des KI-Modells dem Bediener über die erweiterte Benutzeroberfläche angezeigt, um als Hilfestellung für die manuelle Bewertung zu dienen. Lötstellen, welche bei der finalen manuellen Fehlerverifikation als i. O. bewertet werden, haben die Kontrolle bestanden. Findet eine n. i. O.-Bewertung statt, stellt die Lötstelle einen Defekt dar, sodass Nacharbeit stattfinden muss, oder die Baugruppe entsorgt werden muss. Das Ergebnis der manuellen Nachinspektion kann zudem dem ursprünglichen Inspektionsbild zugeordnet werden, sodass zusätzliche gelabelte Daten für ein weiteres Training des Modells entstehen [16].
Da die KI-basierte Nachinspektion zunächst im Hintergrund als „Schattenmodell“ mitlaufen kann, sind die Einstiegshürden für diesen KI-Use-Case vergleichsweise gering.
Vorhersage der Lötqualität beim THT-Wellenlöten und Optimierung der Lötparameter
Die Erzeugung von IPC-konformen Lötungen in „Through Hole Technology“ (THT) hängt stark vom Leiterplattendesign und dem jeweiligen Bauteil ab. Ein entscheidendes Kriterium für eine ausreichende Lötqualität stellt der vertikale Lotdurchstieg dar, welcher laut IPC-A-610 [17] für Produkte mit hohen Zuverlässigkeitsansprüchen einen Wert von 75 Prozent erreichen. Die Bestimmung des Lotdurchstiegs kann durch eine optische Inspektion der Lötstelle, eine Röntgeninspektion oder eine Querschnittsanalyse erfolgen, wobei letztere Methode die präziseste Bestimmung zulässt, aber auch eine zerstörende Prüfung darstellt. Um diese Vorgaben zu erreichen, müssen die Prozessparameter auf das vorhandene Leiterplattendesign abgestimmt werden. Dafür werden bei der Einführung neuer Leiterplattenlayouts aktuell meist aufwendige Versuchsreihen, basierend auf subjektivem Expertenwissen und dem Trial-and-Error-Prinzip, durchgeführt, bevor es in die Serienfertigung geht. Ziel des vorliegenden KI-Use-Cases ist es, den Versuchsaufwand zur Findung optimaler Prozessparameter durch ein KI-basierte Vorhersage der voraussichtlichen Lötqualität zu reduzieren, Bild 4.
![Bild 4. Methoden zur Bestimmung des Lotdurchstiegs bei THT-Lötstellen. Foto in Anlehnung an [18]. Grafik: FAPS/Fau](https://www.ingenieur.de/wp-content/uploads/2024/10/Bild-4-Methoden-zur-Bestimmung-des-Lotdurchstiegs.jpg)
Bild 4. Methoden zur Bestimmung des Lotdurchstiegs bei THT-Lötstellen. Foto in Anlehnung an [18]. Grafik: FAPS/Fau
In diesem Demonstrator wurde ein KI-Modell trainiert und validiert, mit dessen Hilfe der Lotdurchstieg – basierend auf gegebenen Prozessparametern (wie Löttemperatur, Vorheiztemperatur und Kontaktzeit) – sowie den Eigenschaften der Lötstelle (beispielsweise Lochdurchmesser und Lagenaufbau) und des elektrischen Bauteils (zum Beispiel Durchmesser und Material des Pins) nachweislich vorhergesagt werden kann [19]. Basierend auf diesem Vorhersagemodell wurde zudem eine Optimierung der Prozessparameter umgesetzt. Dafür werden die Parameterwerte der Lötstelle und des elektrischen Bauteils als konstant definiert. Mithilfe eines geeigneten Suchalgorithmus werden anschließend passende Lötparameterwerte identifiziert, sodass das Modell einen möglichst hohen Lotdurchstieg vorhersagt, welcher die Vorgaben in IPC-A-610 [17] erfüllt.
Qualitätsüberwachung beim Laserschweißen von Hairpin-Statoren
In der Automobilindustrie wird bei der Herstellung von elektrischen Traktionsmotoren zunehmend die sogenannte „Hairpin-Technologie“ eingesetzt. Hairpins bestehen aus lackisoliertem Kupferdraht mit rechteckigem Querschnitt und verfügen über eine charakteristische, dreidimensionale U-Form. Zur Herstellung einer Hairpin-Wicklung werden zahlreiche Hairpins in die Nuten des Statorblechpakets eingeführt und an ihren abisolierten Enden stoffschlüssig miteinander verbunden. Diese Verbindung erfolgt überwiegend durch Laserschweißen, das aufgrund der Vielzahl an Kontaktstellen einen entscheidenden Einfluss auf die finale Qualität des gefertigten Hairpin-Stators hat. Schon kleinere Positionsabweichungen der Hairpin-Enden können zu unzureichenden Schweißverbindungen führen. Weitere Einflussgrößen, die sich zumeist negativ auf die Qualität auswirken, umfassen Rückstände der Lackisolation sowie Variationen in der Schnittkontur. Eine verlässliche Inline-Überwachung einer jeden Hairpin-Laserschweißung ist demnach essenziell, um eine gleichbleibend hohe Produktqualität sicherzustellen [20–22].
Um den Laserschweißprozess möglichst ganzheitlich überwachen zu können, wurde die für Demonstrationszwecke herangezogene Laserzelle mit umfangreicher Sensorik ausgestattet. Neben mehreren Kameras wurden auch ein Prozesslichtsensor sowie ein „OCT“-System (Optische Kohärenztomografie) integriert. Zum Trainieren und Ausführen von ML-Modellen wurde eine modulare, serviceorientierte MLOps-Architektur implementiert, die vollständig auf Open-Source-Technologie setzt. Die Auswertung der Sensordaten erfolgt durch tiefe neuronale Netze, die qualitätsrelevante Merkmale aus den verschiedenen Modalitäten extrahieren und Rückschlüsse auf die resultierende Verbindungsqualität zulassen. Durch den Einsatz von „XAI“-Verfahren (eXplainable Artificial Intelligence) wird eine hinreichende Erklärbarkeit des Klassifikationsergebnisses sichergestellt. Dank der modularen Gesamtarchitektur lässt sich der ML-basierte Überwachungsansatz einfach skalieren und auf Hairpin-Schweißprozesse in Unternehmen übertragen.
Zusammenfassung
Viele Unternehmen, insbesondere KMU, sind derzeit weiterhin zurückhaltend bei der Anwendung von KI-Verfahren. Als Gründe dafür werden hauptsächlich mangelnde KI-Kompetenzen und Ressourcen angegeben. Um diese Hürden zu überwinden, wird in diesem Artikel erläutert, wie das universitäre ProKI-Netz Unternehmen durch Sensibilisierungs- und Schulungsmaßnahmen sowie durch die Begleitung von konkreten Umsetzungsprojekten unterstützen kann, angefangen bei der Use-Case-Identifikation bis hin zur Implementierung der KI-Modelle. Die an den ProKI-Zentren erstellten KI-Demonstratoren zeigen Unternehmen anhand praktischer Anwendungsfälle den Nutzen von KI, etwa zur Überwachung und Optimierung von Löt- und Schweißprozessen. Dank des bundesweiten ProKI-Netzes erhalten Unternehmen gezielte Unterstützung bei der Einführung von KI, wodurch Risiken für Fehlschläge minimiert und die Chancen auf eine erfolgreiche Etablierung wirtschaftlich sinnvoller KI-Use-Cases erhöht werden.
Die in diesem Beitrag vorgestellten Ergebnisse wurden im Rahmen des vom Bundesministerium für Bildung und Forschung (BMBF) geförderten Forschungsprojekts „Demonstrations- und Transferzentrum ProKI-Nürnberg“ (Homepage: https://proki-netz.de/), mit Schwerpunkt auf KI in Fügeprozessen, erzielt.
Literatur
- Pokorni, B.; Braun, M.; Knecht, C.: Menschzentrierte KI-Anwendungen in der Produktion, 2021.
- VDMA: Quick Guide. Machine Learning im Maschinen- und Anlagenbau. 2018.
- Krüger, J.; Fleischer, J.; Franke, J. et al.: WGP-Standpunkt. KI in der Produktion. Künstliche Intelligenz erschließen für Unternehmen, 2019.
- McKinsey: Smartening up with artificial intelligence. What’s in it for Germany and its Industrial Sector? Studie, 2017.
- Seifert, I.; Bürger, M.; Wangler, L. et al.: Potenziale der Künstlichen Intelligenz im produzierenden Gewerbe in Deutschland, 2018.
- Mayr, A.; Kißkalt, D.; Meiners, M. et al.: Machine Learning in Production – Potentials, Challenges and Exemplary Applications. Procedia CIRP 86 (2019), S. 49–54.
- Meier, S.; Klarmann, S.; Thielen, N. et al.: A process model for systematically setting up the data basis for data-driven projects in manufacturing. Journal of Manufacturing Systems 71 (2023), S. 1–19.
- ProKI: Profitieren Sie von Prozessoptimierung mit KI. Datengestützte Lösungen für Produktionsprozesse. Effizient. Kostensensibel. Energieschonend. Internet: https://proki-netz.de/. Zugriff am 16.05.2024.
- Murphy, K. P.: Machine learning. A probabilistic perspective. Cambridge, Mass.: MIT Press, 2012.
- Chapman, P.: CRISP-DM 1.0: Step-by-step Data Mining Guide. SPSS, 2000.
- renumics: Industrial AI Canvas. Internet: https://renumics.com/assets/files/renumics-industrial-ai-canvas-eca82bf2b91578d89fb9908cd3271456.pdf. Zugriff am 17.05.2024.
- Osterwalder, A.; Pigneur, Y.: Business model generation. A handbook for visionaries, game changers, and challengers. Hoboken, NJ: Wiley 2010.
- ProKI Nürnberg: ProKI ist Ihr Experte für KI in der Fügetechnik. Internet: https://www.proki-nuernberg.de/. Zugriff am 19.05.2024.
- DIN Deutsches Institut für Normung e. V: DIN 8580:2003–09. Fertigungsverfahren – Begriffe, Einteilung. Berlin: Beuth Verlag GmbH.
- ] DIN Deutsches Institut für Normung e. V: DIN 8593–0:2003–09. Fertigungsverfahren Fügen – Teil 0: Allgemeines; Einordnung, Unterteilung, Begriffe. Berlin: Beuth Verlag GmbH.
- Thielen, N.; Werner, D.; Schmidt, K. et al.: A Machine Learning Based Approach to Detect False Calls in SMT Manufacturing. 2020 43rd International Spring Seminar on Electronics Technology (ISSE), Demanovska Valley, Slovakia, 2020, S. 1–6.
- IPC: IPC-A-610 – Revision H. Acceptability of Electronic Assemblies. 2020.
- Seidel, R.; Ahrens, T.; Friedrich, J. et al.: Experimental identification and prioritization of design and process parameters on hole fill in mini wave soldering. Microelectronics Reliability 131 (2022), S. 114497.
- Seidel, R.; Leibold, F.; Thielen, N. et al.: Prediction of the Solder Rise in Selective Wave Soldering Comparing Decision Tree and Logistic Regression. 2020 43rd International Spring Seminar on Electronics Technology (ISSE), Demanovska Valley, Slovakia, 2020, S. 1–7.
- Mayr, A.; Hauck, L.; Meiners, M. et al.: Prediction of the Joint Cross-Section of Laser-Welded Hairpin Windings Based on 2D Image Data Using Convolutional Neural Networks. 2020 10th International Electric Drives Production Conference (EDPC), Ludwigsburg, Germany, 2020, S. 1–7.
- Mayr, A.; Bauer, J.; Franke, J.: A multi-view deep learning approach for quality assessment in laser welding of hairpin windings based on 2D image captures. Procedia CIRP 115 (2022), S. 196–201.
- Raffin, T.; Mayr, A.; Baader, M. et al.: Potentials of few-shot learning for quality monitoring in laser welding of hairpin windings. Procedia CIRP 118 (2023), S. 901–906.
Das könnte Sie auch interessieren:
Intelligente Technologiekette optimiert das Nachbearbeiten additiv gefertigter Bauteile
Karosseriebearbeitung: Fehlstellen erkennen und zuverlässig beseitigen
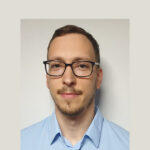
Ben Rachinger, M. Sc., ist wissenschaftlicher Mitarbeiter im Forschungsbereich Elektronikproduktion der Friedrich-Alexander-Universität Erlangen-Nürnberg (Fau), Lehrstuhl für Fertigungsautomatisierung und Produktionssystematik (FAPS). Foto: FAPS
Nils Thielen, M. Sc., ist Forschungsbereichsleiter Elektronikproduktion am FAPS.
Andreas Mayr, M. Sc., ist dort Technologiefeldkoordinator „Künstliche Intelligenz und Maschinelles Lernen“.
Sven Meier, M. Sc., ist wissenschaftlicher Mitarbeiter im Forschungsbereich Elektronikproduktion.
Prof. Dr.-Ing. Jörg Franke ist Lehrstuhlinhaber des Lehrstuhls FAPS.