Virtuelle Inbetriebnahme „Digitaler Zwillinge“
Modelle von Werkzeugmaschinen sind nicht neu. Oft „kranken“ sie jedoch bisher noch daran, dass sie mehr schlecht als recht oder nur unvollständig die Realität abbilden. Ein Konzept, das an den entscheidenden Stellen mit Original-Hardware arbeitet, erzeugt Digitale Zwillinge, die diesen Namen auch verdienen. Folgendes Beispiel zeigt deutlich, dass die Digitalisierung im Maschinenbau voranschreitet und wesentliche reale Vorteile bietet.
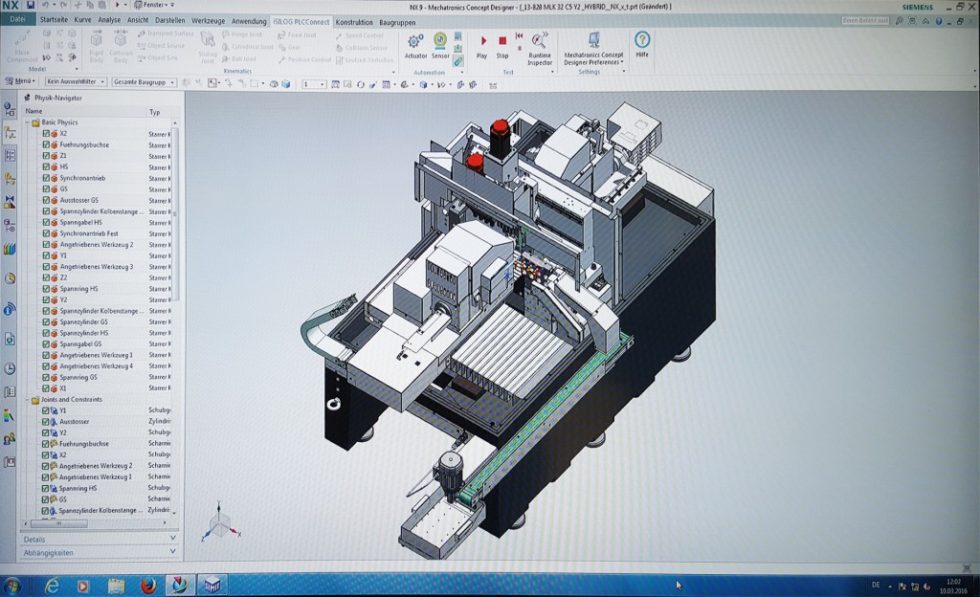
Bild 1. Bevor die reale Maschine ‧entsteht, wird sie als „Digitaler Zwilling“ ‧beziehungsweise kinematisiertes Modell mechatronisch komplett fertig konstruiert. Bild: Siemens / Ramona Riesterer
Einem Interessenten die gefragte Werkzeugmaschine (WZM) innerhalb von Minuten mit „ein paar Mausklicks“ zusammenstellen: virtuell präsentiert sowie vollständig funktionstüchtig. Der Kunde kann sogar sein Werkstück programmieren und probeweise durchlaufen lassen – und das alles auf Sondermaschinen / Unikaten. Dies ist keine Zukunftsvision, sondern sehr real in Vorbereitung bei der Maier Werkzeugmaschinen GmbH & Co. KG, Wehingen, in Zusammenarbeit mit Siemens.
Alle Voraussetzungen sind beim Werkzeugmaschinenbauer vorhanden
Bereits umgesetzt ist dafür die Voraussetzung: Mit dem Konzept des Digitalen Zwillings, der sich virtuell in Betrieb nehmen lässt. Die WZM werden hier – bevor die realen Maschinen entstehen – als kinematisierte Modelle mechatronisch komplett fertig konstruiert und mit Original-Steuerungstechnik in Betrieb genommen, Bild 1. Viele Entwicklungsschritte, die zuvor zeitlich nacheinander erfolgen mussten, können dabei parallel ablaufen. Dieses Vorgehen beschleunigt und erleichtert die Werkzeugmaschinenentwicklung und -inbetriebnahme also ganz grundsätzlich.
In diesem besonderen Fall wurde bei dem Spezialisten für Langdrehmaschinen gleichzeitig auch noch der Umstieg auf Steuerungstechnik von Siemens vollzogen und vereinfacht. Gleich beim ersten umgesetzten Digitalen Zwilling handelte es sich um eine komplexe, hochproduktive „Sinumerik“-gesteuerte Maschine des Typs „ML 32 G2“ mit drei Spindeln und zwölf Achsen. Auf die Frage, wie sich die virtuelle Konstruktion und Inbetriebnahme in der Praxis dargestellt haben, antwortet Michael Maier, Geschäftsführer des Wehinger Sondermaschinenbauers, mit zwei kurzen Worten: „Absolut reibungslos.“
Entwicklung beschleunigen und Inbetriebnahme optimieren
Während bei Neukonstruktionen oder Maschinenerweiterungen zuvor die Bereiche Mechanik, Elektrik etc. organisatorisch sowie personell für sich gearbeitet haben, liegt dem Digitalen Zwilling ein mechatronischer Ansatz zugrunde, der ein gemeinsames Vorgehen verlangt. Mit Blick auf das Gesamtsystem lassen sich Entwicklungsschritte parallelisieren und optimieren. Da mit echter Hardware gesteuert wird, entsteht am Schreibtisch ein zwar virtuelles, aber doch voll parametriertes und kinematisiertes Maschinenmodell, das sich in Betrieb nehmen lässt. Abläufe und Bewegungen entsprechen dem, was hinterher real auf dem Hallenboden stehen und passieren wird. Probleme lassen sich auf diese Weise noch vor dem Bau der realen Maschinen erkennen – egal, ob es um die Mechanik, die Software oder um Hindernisse geht, die sich normalerweise erst bei der realen Inbetriebnahme feststellen und klären lassen. „Je länger bei einer Inbetriebnahme an der realen Maschine gearbeitet werden muss, desto länger steht das Geld gebunden in der Halle“, weiß Michael Maier. „Deshalb ist jede einzelne Tätigkeit, die wegfällt, weil wir sie vorab am Digitalen Zwilling erledigen können, ein Gewinn.“ Während das bisherige Vorgehen in der Konstruktion die Zahl der ausgelieferten Maschinen auf etwa eine pro Woche begrenzte, will Maier mit dem neuen Konzept künftig die Produktivität um 50 % steigern und 1,5 Maschinen pro Woche ausliefern.
Vollständige reale Simulation
Der große Unterschied zu bisherigen Maschinenmodellen ist, dass es sich beim Digitalen Zwilling um ein vollständig kinematisiertes Modell handelt, bei dem alle Komponenteneigenschaften und -funktionen bekannt sind. Die wesentlichen Bestandteile, die das möglich machen, sind die Software „Mechatronics Concept Designer“ von Siemens PLM Software, das Simulationsprogramm „Simit“ (inklusive Simulation-Unit, dem Nachfolgegerät der „Simba-Box“), als Original-Hardware lediglich die NCU (Numerical Control Unit) sowie die Bedienoberfläche (Operator Panel und Maschinensteuertafel). Durch Letzteres hat der Programmierer das Gefühl „wie an der echten Maschine“.
Der Mechatronics Concept Designer basiert auf dem CAD-System „NX“. Via „PLC Connect“ wird das CAD-Maschinenmodell an die Original-PLC (Programmable Logic Controller) angebunden und so die Lücke zwischen mechanischer Konstruktion und Steuerungstechnik geschlossen. Die Simulationsumgebung Simit enthält sämtliche Hardware-Informationen, während die Simulations-Unit als Hardware-Schnittstelle das komplette Verhalten von bis zu 250 Feldgeräten rückwirkungsfrei in Echtzeit simuliert (Steuerung, Antriebe und so weiter). Dabei ist ein Mischbetrieb von realen und simulierten Geräten möglich. Bei Maier ist unter anderem die Original-NCU der Sinumerik 840D sl eingebettet. Es entsteht damit eine „Hardware-in-the-Loop-Lösung“, die eine realistische virtuelle Inbetriebnahme zulässt, Bild 2.
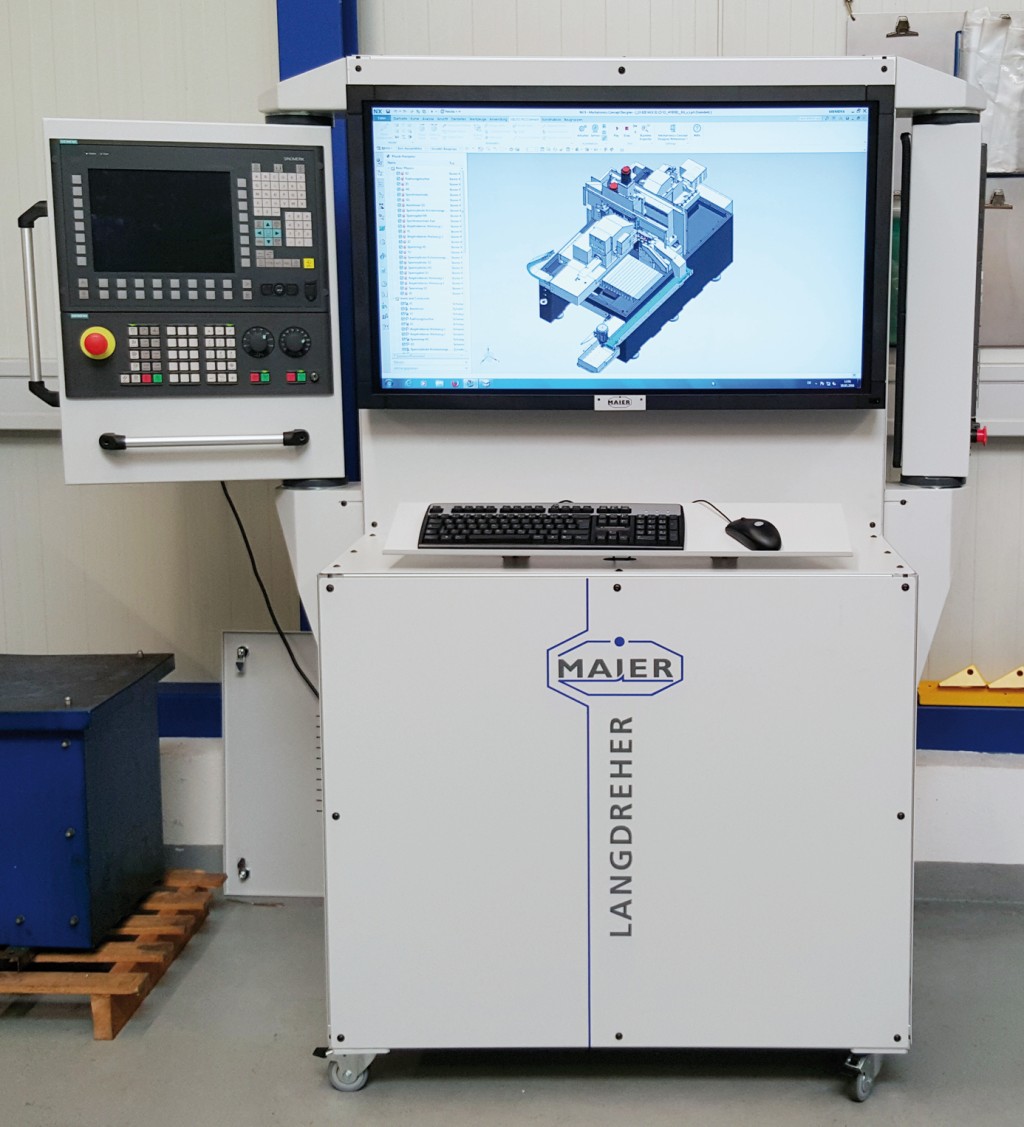
Bild 2. Bei Maier Werkzeugmaschinen ist unter anderem die Original-CNC „Sinumerik 840D sl“ eingebettet, sodass eine „Hardware-in-the-Loop-Lösung“ entsteht, die eine realistische virtuelle Inbetriebnahme zulässt. Bild: Siemens / Ramona Riesterer
Reibungsloser Umstieg auf die neue Technologie
Sich auf einen Digitalen Zwilling zu verlassen, wenn vertraute Komponenten zum Einsatz kommen, ist das eine. Etwas ganz anderes ist es, mit bisher gänzlich unbekannter Technik zu arbeiten. Doch genau das haben Michael Maier und sein Team getan: Schon lange hatte er damit geliebäugelt, seine Maschinen auch mit Siemens-Steuerungstechnik anzubieten. Als wieder einmal einer seiner Stammkunden darauf drängte, entschloss er sich – das Konzept des Digitalen Zwillings vor Augen – diesen Schritt zu wagen. Spätestens jetzt wird die Dimension klar, die hinter der Aussage „absolut reibungslos“ steckt. Der Geschäftsführer begründet seine Aussage: „Der erste Digitale Zwilling war gleichzeitig die erste Maschine, die bei uns jemals Siemens ‚gesehen‘ hat. Mittels dem Mechatronics Concept Designer konnten wir sämtliche Software-Funktionen und Zyklen virtuell testen, sodass die erste echte Inbetriebnahme nur unwesentlich länger dauerte als mit den bisher üblichen Komponenten.“ Zwischenzeitlich ist der Aufwand für das Erstellen eines Digitalen Zwillings bereits deutlich gesunken. „Maximal zwei Tage – dann können wir virtuell in Betrieb nehmen“, so Maier.
Die wirklichkeitsgetreue Simulation bringt auch Erleichterungen im Servicefall und beim Aftersales: „Fragte ein Maschinenbetreiber bisher nach einer Erweiterung, konnte es schon einmal vorkommen, dass wir ein Papp-Modell gebaut haben, um zu überprüfen, ob die betreffende Maschine für die Produktion eines bestimmten Werkstücks in Frage kommt“, berichtet Maier schmunzelnd. Lässt sich an einer bestimmten Stelle noch eine Einheit aufbauen? Reicht es vom Platz her aus? Mit dem Digitalen Zwilling sind diese Fragen einfach zu beantworten. Darüber hinaus lassen sich gleich noch die Zyklen auf der CNC für die fragliche Anwendung überprüfen: „Und das alles ganz entspannt – denn ein Crash in der Simulation ist leicht zu verschmerzen.“
Nächster Schritt: der Konfigurator
Ein dynamischer Konfigurator, der einzelne voll kinematisierte Maschinenmodule hinterlegt hat – mit sämtlichen Metadaten für das ERP (Enterprise Resource Planning)-System, die Beschaffung und so weiter –, erleichtert auch die Verkaufsgespräche. Sobald dies verwirklicht ist, verkürzt sich die Zeit für die Erstellung eines Digitalen Zwillings von den zwei Tagen auf die eingangs erwähnten wenigen Mausklicks. Der Interessent muss dann nicht länger versuchen, an einer statischen Zeichnung nachzuvollziehen, ob die angebotene WZM die geforderten Leistungen auch tatsächlich erfüllen kann.
Digitalisierung bietet zahlreiche Vorteile
Lieferzeiten verkürzen und Simulationen wirklichkeitsgetreu durchführen – für Michael Maier ist dies bereits Realität. Insbesondere bei seinen Sondermaschinen, die modular zusammengestellt und auf den einzelnen Kunden abgestimmt sind, freut er sich schon auf die Verkaufsgespräche, bei denen der Konfigurator zum Einsatz kommen wird, Bild 3: „In der Theorie lässt sich viel beschreiben und erzählen“, so Maier.
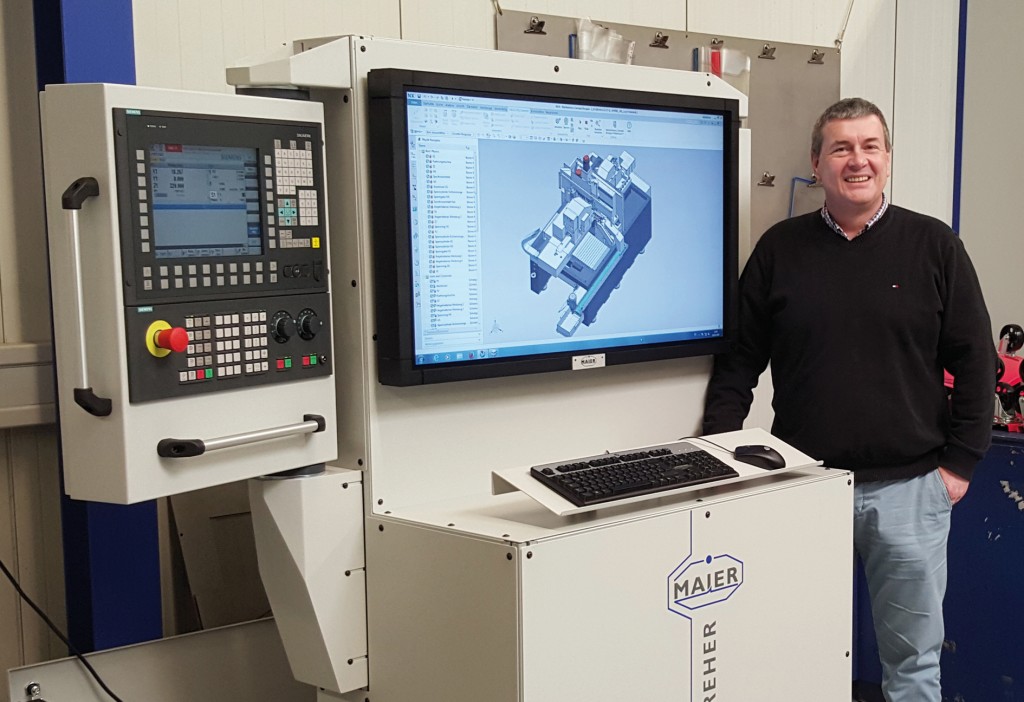
Bild 3. Geschäftsführer Michael Maier freut sich schon auf die Verkaufsgespräche, die er am Konfigurator führen wird. Geplant ist, künftig schneller von der Entwicklung zur fertigen Sondermaschine zu kommen. Bild: Siemens / Ramona Riestere
„Aber es zeigen zu können, sodass der Kunde sieht, wir reden über das Gleiche, ist eine ganz andere Ebene.“
www.maier-machines.de
Vollständige Simulation bietet vielfachen Nutzen
Mithilfe einer vollständigen Simulation wird aufgrund der wirklichkeitsgetreuen Darstellung ein potentieller Kunde schneller zum realen Käufer. Der Bestellvorgang sorgt dafür, dass der Digitale Zwilling der Maschine zügig Realität wird, weil bei den Baugruppen Stücklisten hinterlegt sind. Hiermit ist nicht nur eine Grundlage für eine solide Vorkalkulation geboten. Es ist auch automatisch sichergestellt, dass die Komponenten zueinander passen. Darüber hinaus ist auf Knopfdruck dafür gesorgt, dass alle Teile da sind, wenn sie in der Montage gebraucht werden. Währenddessen kann der Abnehmer der Maschine schon seine Mitarbeiter schulen, Programme erstellen und simulieren – an der echten Steuerung der virtuellen Maschine, die sich 1:1 verhält wie die reale.
www.siemens.de/sinumerik
Klaus Langanke ist Senior Vertriebsbeauftragter bei Siemens in Stuttgart, Digital Factory Division, Machine Tool Systems.