Welcher Kommunikationsstandard für künftige Industrie 4.0-Fabriken?
Industrie 4.0 birgt umfassendes Potential für Unternehmen und Kunden. Beim Einrichten von „Industrie 4.0-Fabriken“ tritt jedoch an zahlreichen Stellen das Problem auf, dass es noch keine hinreichenden Standards gibt. Daher geht ein großer Hausgerätehersteller die Standardisierung konsequent an und legt die erforderlichen Konzernrichtlinien fest.
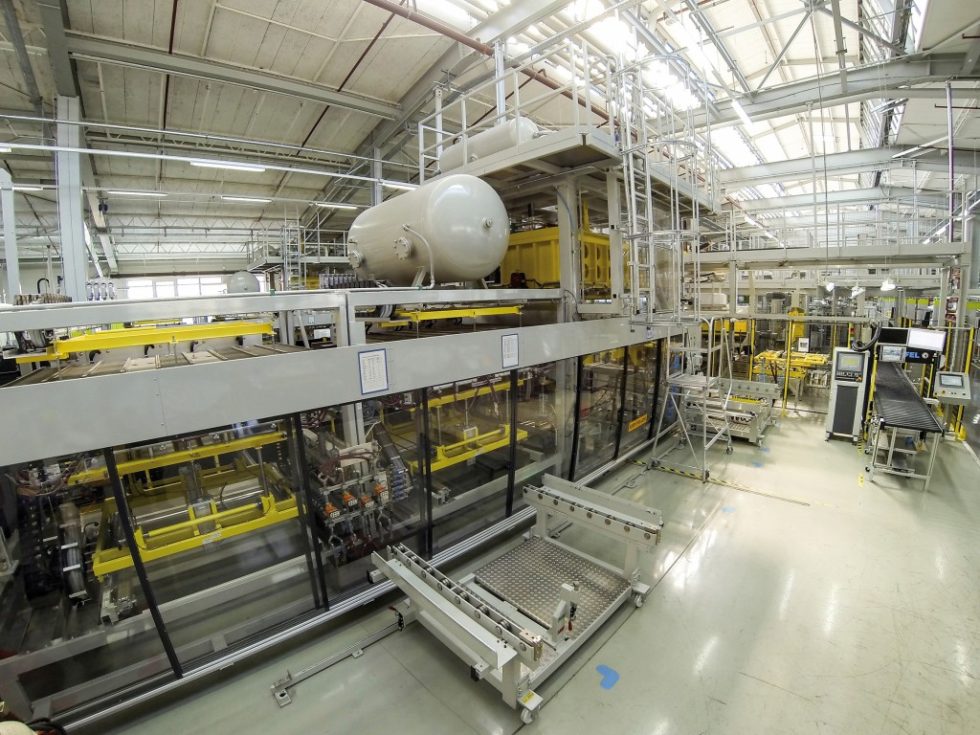
Bild 1. Fertigungsumgebung beim ‧Hausgerätespezialisten, der mit wissenschaftlicher Unterstützung den am besten geeigneten Maschine-zu-Maschine-Kommunikationsstandard suchte. Bild: BSH
In Zusammenarbeit mit der Hochschule Rhein-Waal wurden verschiedene Protokolle für die Kommunikation zwischen Maschinen und im speziellen zwischen Maschinen und dem Fertigungsmanagementsystem verglichen und auf ihre Eignung als Standard für alle Werke untersucht, Bild 1. Dabei stellte sich ein klarer Favorit heraus.
Anforderungen an die Maschine-zu-Maschine-Kommunikation
Welche Anforderungen muss ein Protokoll für die Datenübertragung von Maschine zu Maschine erfüllen? Die folgenden acht Kriterien wurden hoch priorisiert, Tabelle:
- „Interoperabilität / Kompatibilität“ beschreibt die Fähigkeit der Kommunikation zwischen verschiedenen Systemen (zum Beispiel unterschiedliche Betriebssysteme).
- „Skalierbarkeit“ ist die Anpassungsfähigkeit bezüglich des Umfangs der Komponentendaten – beispielsweise ein einzelner RFID (Radio Frequency Identification)-Tag versus Transferstraße – und der Anzahl der Komponenten selbst.
- „Sicherheit“ beschreibt den Schutz vor unerlaubten und unbemerkten Zugriffen von außen oder auch innerhalb des Systems.
- „Transportfähigkeit“ meint die Leistungsfähigkeit des Datentransports (Übertragungsraten und Datenformate).
- „Modellierung“ beschreibt die Fähigkeit, eine große Menge von Daten zu verknüpfen und mittels einer Navigationsfunktion auszuwerten sowie zu strukturieren.
- „Plug-and-Produce-Tauglichkeit“ steht für eine schnelle und einfache Integration von weiteren Komponenten in ein vorhandenes System (wie Plug and Play).
- „Konformität“ stellt alle vorher genannten Eigenschaften sicher. Werden Produkte vor dem Vertrieb geprüft? Gibt es eine Zertifizierung – und, wenn ja, welche?
- „Bekanntheitsgrad“ beschreibt den Verbreitungsgrad des Protokolls in der Industrie und die Verfügbarkeit von Komponenten.
Vier Protokolle in der engeren Auswahl
Es gibt eine Menge von Datenprotokollen, die unterschiedliche Aufgaben in der Maschinenkommunikation übernehmen, Tabelle.
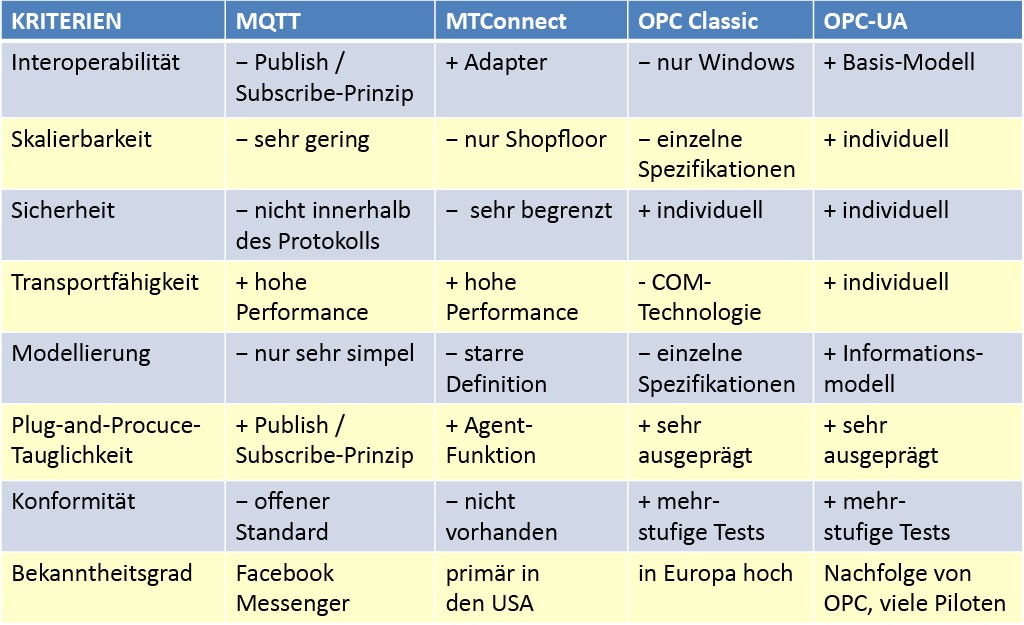
Tabelle. Auflistung und Gegenüberstellung der acht wesentlichen Kriterien zur Analyse der verschiedenen Kommunikationsstandards. Bild: Hochschule Rhein-Waal
„OPC“ (Open Platform Communication) und der Nachfolger „OPC-UA“ (Unified Architecture) sind insbesondere in Deutschland weit verbreitet [1]. Viele Unternehmen arbeiten schon mit dem „OPC Classic Standard“. Daher soll auch das Potential der OPC-UA ermittelt werden. „MQTT“ (Message Queue Telemetry Transport) ist ein Datenprotokoll, das in vielen Anwendungen (zum Beispiel „Facebook Messenger“) die Kommunikation zwischen zahlreichen kleinen Geräten steuert. In den USA ist das Datenprotokoll „MTConnect“ sehr verbreitet, insbesondere bei vielen CNC-Maschinenherstellern.
Eine Bewertung aller Protokolle in Bezug auf die vorne genannten Kriterien soll die Eignung als Konzernstandardprotokoll für Industrie 4.0-Fabriken zeigen, Bild 2.

Bild 2. Durch einen allgemeinen Kommunikationsstandard soll das starre Verständnis der Automatisierungspyramide aufgebrochen werden. Bild: Hochschule Rhein-Waal
Unter Berücksichtigung der Systemvoraussetzungen im Konzern wurden diese vier Datenprotokolle für eine intensivere Analyse ausgewählt.
MTConnect – nur für den Shopfloor relevant
MTConnect ist ein offener und erweiterbarer Standard, der von der amerikanischen Association for Manufacturing Technology (AMT) ab 2006 entwickelt wurde. Ziel der Entwicklung des Datenprotokolls war es, den Datenaustausch auf der Shopfloor-Ebene zu vereinfachen. In den USA ist dieses Datenprotokoll sehr verbreitet. MTConnect definiert fünf Komponenten, die eine Maschinenkommunikation im Netzwerk modular erlauben. Komponenten kommunizieren über das Netzwerk mithilfe eines Agenten und eines optionalen Adapters mit dem Client, zum Beispiel einer Anwendung im Bereich Monitoring. Aufgrund kurzer Produktlebenszyklen ist es wichtig, neue Komponenten verschiedener Hersteller integrieren zu können und somit die Produktion anzupassen. MTConnect löst diese als Plug-and-Produce-Tauglichkeit definierte Anforderung mithilfe des Adapters. Dieser kann individuell gestaltet werden und definiert eine standardisierte Schnittstelle zum Agenten. Somit bleibt er kompatibel zum bestehenden Netzwerk.
Die nötigen Mechanismen zum Versenden von Daten über die Grenzen der einzelnen Fabrik hinaus sind bei MTConnect nicht vorhanden, da es hauptsächlich für die Verwendung innerhalb einer Fabrik – insbesondere zwischen Maschinen und dem Fertigungsmanagementsystem – entwickelt wurde. Ein weiteres Detail, das gegen MTConnect als potentiellen Standard einer „smarten“ Fabrik-Kommunikation spricht, ist die strikte Definition von Methoden und die besonders standardisierte Beschreibung von Dateninhalten in der Spezifikation. Das vereinfacht zwar die Kommunikation, jedoch lassen sich Anpassungen oder individuelle Anforderungen nur mit einer Änderung der kompletten Spezifikation umsetzen. Eine fehlende Zertifizierung der entwickelten Produkte mit der MTConnect-Schnittstelle gibt zudem nicht die gewünschte Sicherheit, dass die Interoperabilität zwischen MTConnect-fähigen Produkten auch wirklich zuverlässig gewährleistet ist [2].
MQTT – für Anwendungen mit Ressourcenknappheit
MQTT ist ein Protokoll, das auf dem Weg zur Standarisierung durch die „Organization for the advancement of structured information standards“ (Oasis) ist. Das Protokoll wurde 1999 von Dr. Andy Stanford-Clark von IBM und Arlen Nipper von Acrom entwickelt, um Pipeline-Systeme überwachen zu können. Das entspricht der „Big Data“-Idee von Industrie 4.0 – viele verschiedene Informationen sollen zu einer großen Datensammlung zusammengeführt werden, aus der dann mithilfe von Methoden der Datenanalyse wertvolles Wissen generiert wird. Das wiederum soll dazu genutzt werden, Prozesse und somit die Produktion zu optimieren [3]. Aufgrund der schwachen Infrastruktur im Bezug auf Brandbreite und Übertragungsmöglichkeiten zur Zeit der Entwicklung von MQTT war es das Ziel, mit weniger Ressourcen viele Daten zu übertragen. Die Übermittlung von kleinen Datenpaketen ist mit großer Zuverlässigkeit und Geschwindigkeit möglich. Das Transportieren von größeren Datenmengen war nicht vorgesehen und ist somit eine Schwäche von MQTT. Aufgrund der Optimierung hin zur Maximierung der Datenübertragungsgeschwindigkeit wurden auch notwendige Sicherheitsmechanismen vernachlässigt.
Durch das Verwenden eines Publish / Subscribe-Prinzips wird die Idee von „Plug-and-Produce“ in diesem Protokoll möglich, jedoch leidet die Interoperabilität unter dieser Methode. Eine bekannte Anwendung des MQTT-Protokolls ist der „Facebook Messenger“, bei dem die Stärken des Protokolls wie Leistungsfähigkeit und niedrige Ressourcennutzung zum Tragen kommen. Für die gesamte Kommunikation in Netzwerken von smarten Fabriken ist MQTT jedoch aufgrund der genannten Gründe nicht geeignet.
OPC – eine bekannte Lösung mit Grenzen
OPC ist ein Kommunikationsstandard, der den Austausch von Daten zwischen zwei industriellen Automatisierungsmaschinen definiert. Er wurde 1995 von einem Konsortium aus der Automatisierungsindustrie entwickelt. Durch die OPC Foundation hat dieser Standard primär in Europa einen hohen Bekanntheitsgrad. Die Motivation für die Entwicklung war es, das Plug-and-Play-Prinzip – bekannt von Homeoffice-Druckern – in einem Kommunikationsstandard zu definieren, um die Anbindung von Produktionsmitteln in Fabrik- und Unternehmensnetzwerken zu erleichtern. Über eine standarisierte Schnittstelle kann ein OPC-fähiges Produkt verhältnismäßig schnell eingebunden werden und bietet den Herstellern genug Freiraum, um anwendungsspezifische Elemente zu gestalten.
OPC Classic basiert auf der COM- und der DCOM-Technologie (Component Object Technology und Distributed Component Object Technology). Diese Technologien beschränken die Verwendung von OPC auf Microsoft-Anwendungen, sodass die Interoperabilität deutlich eingeschränkt ist. Das Konzept von OPC ist, dass ein Client im Netzwerk auf die Information zugreift, die auf einem Server gespeichert ist. Mit zunehmender Verbreitung von OPC als Standard wurde der Anwendungsbereich enorm vergrößert. Die OPC Foundation reagiert darauf mit anwendungsbezogen Substandards wie OPC-AE (Alarms and Events), OPC-HDA (Historical Data Access) oder OPC-DA (Data Access). Die Kommunikation zwischen den Standards gestaltete sich jedoch zunehmend schwierig, was dazu geführt hat, dass ein neuer Standard entwickelt wurde, der die bekannten Probleme lösen soll. Dieser Standard heißt OPC Unified Architecture, kurz OPC-UA.
Nutzen von OPC-UA
2006 veröffentlichte die OPC Foundation ihre erste Spezifikation zu OPC-UA. Dieser Standard ist die neuere Version und abwärtskompatibel zu OPC Classic und vereint die positiven Eigenschaften dieses Standards sowie seiner anwendungsspezifischen Spezifikationen ohne die Nachteile der erschwerten Interoperabilität. Die modulare Architektur gestattet eine plattformübergreifende Kommunikation. Diese lässt sich für jede Anwendung spezifisch zusammenstellen, ohne dabei die Interoperabilität zu gefährden.
Zwei Grundbestandteile von OPC-UA sind der Transport-Mechanismus und das Datenmodell. Der Anwender kann zwischen verschiedenen Transportmöglichkeiten wählen und sowohl das „Transmission Control Protocol“ (TCP) als auch Web-Services einsetzen – je nachdem, ob eine hohe Datenrate oder eine Kommunikation über Firmennetzwerkgrenzen hinweg benötigt wird [4].
Das Datenmodell wird durch eine festgeschriebene OPC-UA-Basis und das darauf aufgebaute anpassungsfähige Informationsmodell flexibel. Die Basis definiert die allgemeine Kommunikation zwischen Server und Client, wie es aus OPC Classic bekannt ist. Die Informationsmodelle lassen sich anwendungsspezifisch kreieren, ohne die Interoperabilität negativ zu beeinflussen. Aufgrund der Anpassungsmöglichkeiten dieses Standards können Sicherheitsmechanismen im gewünschten Umfang integriert oder weggelassen werden.
Ein entscheidender Vorteil dieses Kommunikationsstandards gegenüber anderen Datenprotokollen ist, dass durch die Zertifizierung aller OPC-UA-fähigen Geräte die Interoperabilität offiziell gewährleistet wird. Bei dieser Zertifizierung wird in einem mehrstufigen Prüfprozess die Kommunikation zwischen Geräten oder Anwendungen via OPC-UA von der OPC Foundation getestet.
Ebenfalls für die Verwendung dieses Protokolls spricht, dass es aufgrund der bereits langjährigen Einführung von OPC Classic zunehmend Verbreitung findet und an Bekanntheit gewinnt. Forschungsorganisationen wie das Fraunhofer-Institut für Optronik, Systemtechnik und Bildauswertung IOSB in Deutschland forschen mit diesem Standard. Darüber hinaus nutzt ihn die Technologie-Initiative „SmartFactory e.V.“ als zentrales Kommunikationsprotokoll in der ersten modularen Industrie 4.0-Produktionslinie. Des Weiteren empfiehlt die „Plattform Industrie 4.0“ (ein Gemeinschaftsprojekt von Bitkom – Bundesverband Informationswirtschaft, Telekommunikation und neue Medien, VDMA – Verband Deutscher Maschinen- und Anlagenbau und ZVEI – Zentralverband Elektrotechnik- und Elektronikindustrie) in ihren Handlungsempfehlungen, OPC-UA als eine wichtige Schlüsseltechnologie zu betrachten.
Das leistungsfähigste Protokoll
Der systematische Vergleich der Protokolle im Hinblick auf die acht wesentlichen Kriterien hat ergeben, dass das Protokoll OPC-UA als Kommunikationsstandard für die Errichtung von vernetzten Fabriken am besten geeignet ist. Aufgrund der vielfältigen Anpassungsmöglichkeiten in Kombination mit hoher Interoperabilität im gesamten Netzwerk hebt sich OPC-UA von den anderen betrachteten Protokollen ab.
Für eine OPC-UA-Schnittstelle spielt der eigentliche Inhalt der Datenübertragung keine Rolle. Während MTConnect hauptsächlich die Kommunikation zwischen Fertigungsmanagementsystem und Maschine unterstützt, gestattet OPC-UA den Datenaustausch von der Feldbus- bis zur Kennzahlenebene der Unternehmensleitung. Kunden- und Zuliefereranbindungen sind denkbar. Die Verbreitung und Akzeptanz dieses Standards erhöht sich kontinuierlich. Die OPC Foundation arbeitet nicht nur fortlaufend an der Weiterentwicklung des Standards, sondern auch an dessen Verbreitung.
Literatur:
[1] N. N.: Umsetzungsstrategie Industrie 4.0. Bitkom e.V., Berlin; VDMA e.V., Frankfurt am Main; ZVEI e.V., Frankfurt am Main.. Internet: www.bmwi.de/BMWi/Redaktion/PDF/I/industrie-40-verbaendeplattform-bericht,property=pdf,bereich=bmwi2012,sprache=de,rwb=true.pdf. Stand: 2015.[2] Jasperneite, P. D.; Neumann, A.; Pethig, F.: OPC UA versus MTConnect. ComputerAutomation (2015), Nr. Juni, S. 16–21.[3] Okuniewicz, R.; Seibold, J.: MQTT – Message Queue Telemetry Transport Protocol. Hochschule Aalen, Juni 2015.[4] Mahnke, W.; Damm, M.; Leitner, S.-H.: OPC Unified Architecture. Berlin: Springer-Verlag, 2009.
Prof. Dr.-Ing. Alexander Klein MBA, Jahrgang 1977, ist Professor für Integriertes Produktionsmanagement an der Hochschule Rhein-Waal in Kleve. Er lehrt und berät im Bereich Industrie 4.0 sowie beim Produktionsmanagement. // Felix Wolters, B. Sc., Jahrgang 1993, absolvierte seine Bachelorarbeit zum hier beschriebenen Thema und studiert nun im Masterstudiengang Production Engineering and Management an der KTH Stockholm/S. // Prof. Dr.-Ing. Stefanie Dederichs MBA, Jahrgang 1978, hat die Professur für Messtechnik und Signalverarbeitung an der Hochschule Rhein-Waal inne. // Dr.-Ing. Florian Karl, Jahrgang 1982, promovierte am Institut für Werkzeugmaschinen und Betriebswissenschaften iwb der Technischen Universität München. Seit 2015 ist er bei der BSH Hausgeräte GmbH in der Abteilung Zentrale Technik – Produktion in München tätig.