3D-Komplettlösungen für die flexible Laserbearbeitung
Für dreidimensionale Schweiß- oder Bearbeitungsanwendungen in Industrie und Forschung eignen sich Laseranlagen ideal. Doch bei der passenden Auslegung für die jeweilige Fertigungsaufgabe ist Engineering-Kompetenz gefragt. Ein Gespräch mit einem Hersteller und einem Anwender zeigt, worauf es ankommt.
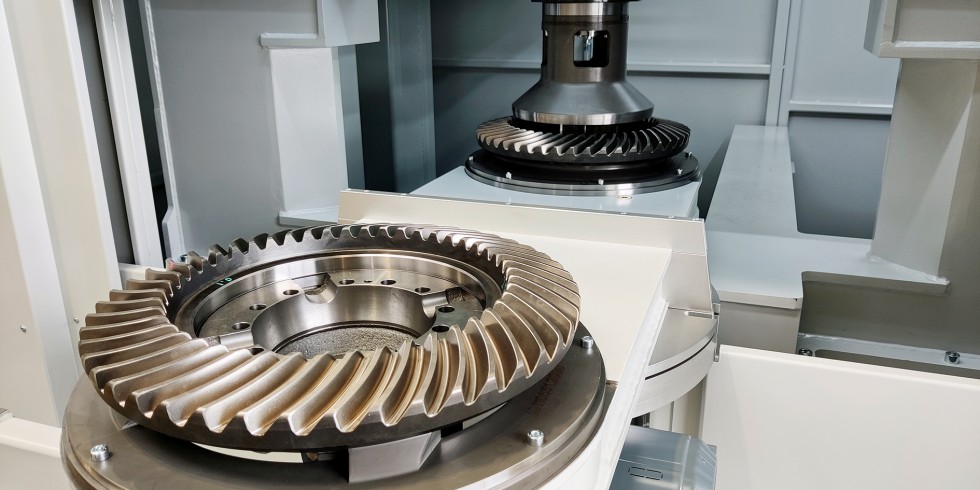
Großbauteil: Das Schweißsystem eignet sich für das automatische Fügen einer Baugruppe für das Differential eines Busgetriebes. Das Gesamtgewicht liegt bei circa 100 Kilogramm.
Foto: Arnold
Bei der Auslegung von Lasersystemen für anspruchsvolle Bearbeitungsaufgaben geht zum Beispiel um folgende Fragen: Passt die Strahlquelle optimal zu den Werkstoffen und zur gewünschten Bearbeitungsaufgabe? Wie können die Werkstücke optimal zugeführt, gespannt, bearbeitet und geprüft werden? Welche Taktzeiten sind erreichbar? Wie ist die Umrüstflexibilität bei wechselnden Aufgabenstellungen und wie sieht es mit Schulung, Beratung, Wartung und Service aus?
Langjährige Erfahrung zahlt sich aus
„Unser Unternehmen hat sich aus einer Spezialschweißerei entwickelt, die bereits vor dem Einstieg in die Lasertechnologie über ein breites Know-how in den Bereichen Schweißen und Spanntechnik verfügte“, erläutert Dipl.-Ing. (DH) Hansjörg Klotz, Vertriebsleiter bei der Karl H. Arnold Maschinenfabrik. Da dort schon immer alle möglichen Teile mit „vertrackten“ Geometrien im Gewichtsbereich vom Kleinteil bis zu tonnenschweren Eisenbahnkomponenten zu verarbeiten waren, wurden seit jeher auch Vorrichtungen und Sondermaschinen hergestellt und zunehmend auch verkauft. Schon 1985 entstand erstmals eine Schweißanlage mit einer Laserquelle für das Schweißen von Antriebskomponenten bei der ZF Friedrichshafen. Dies war der Startschuss für eine schnelle Weiterentwicklung zum Hersteller komplexer, voll automatisierter Lasersysteme für anspruchsvolle Fertigungsaufgaben mit dreidimensionaler Strahlführung.
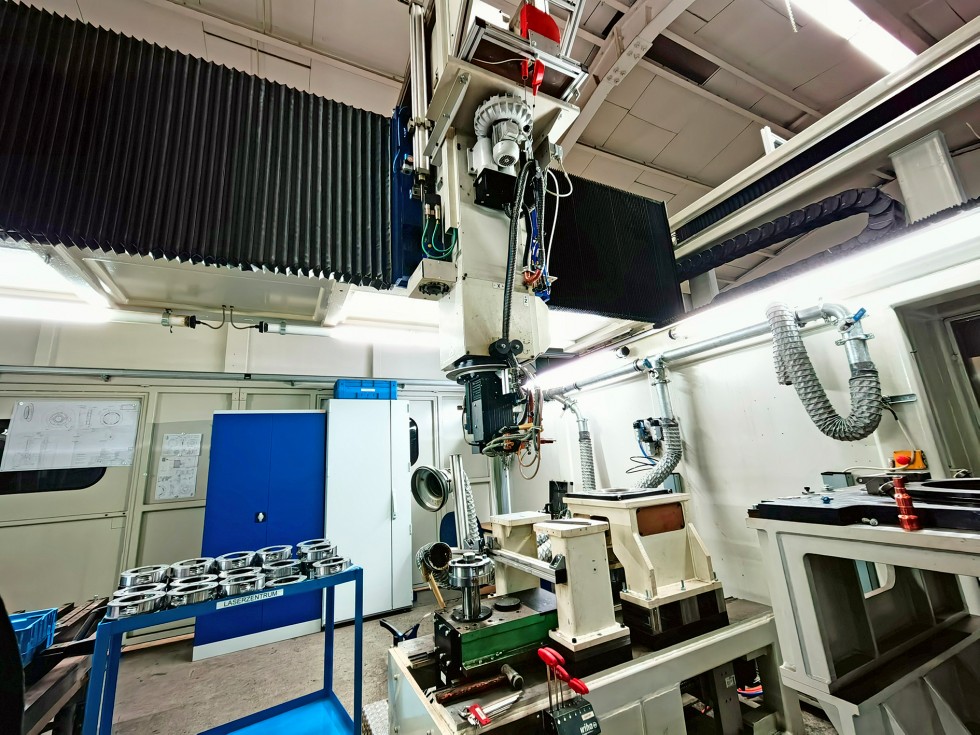
Zur Ausstattung des Job-Shop-Laserzentrums gehört auch diese großformatige Portal-Laserschweißanlage, in der gerade Planetenträger für Omnibusgetriebe im Kundenauftrag verschweißt werden.
Foto: Klaus Vollrath
Zu den schlüsselfertigen Lösungen gehören auch alle erforderlichen Vorrichtungen und Begleitprozesse wie Press-, Erwärm- oder Reinigungsstationen sowie die Qualitätsprüfung z.B. mittels Ultraschalltechnik. Die Kundschaft kommt aus den Bereichen Fahrzeugbau, Maschinenbau oder Anlagenbau, inzwischen auch verstärkt aus Hightech-Branchen wie der Medizintechnik, der Luft- und Raumfahrt oder der Elektrotechnik. Auch mehr als ein Dutzend Forschungseinrichtungen wie Fraunhofer-Gesellschaften oder Hochschulinstitute im Bereich Material- und Verfahrenstechnik schätzen Arnold-Anlagen wegen ihrer Umrüstflexibilität für unterschiedlichste Aufgabenstellungen.
Breites Know-how bezüglich Laserverfahren und Automatisierungen
„Unsere Aufgabenstellungen sind fast schon unendlich vielfältig“, ergänzt H. Klotz. Deshalb gebe es so gut wie keine Systeme von der Stange: Fast jede Anlage sei eine exakt auf die individuellen Aufgabenstellungen des Kunden hin optimierte Sonderanfertigung. Das zwinge zu hoher Flexibilität und Innovationsbereitschaft. Bezüglich der Strahlquellen werden die jeweils am besten geeigneten Aggregate von führenden Herstellern bezogen. Es gibt auch Anlagen, in die gleich mehrere unterschiedliche Strahlquellen integriert werden.
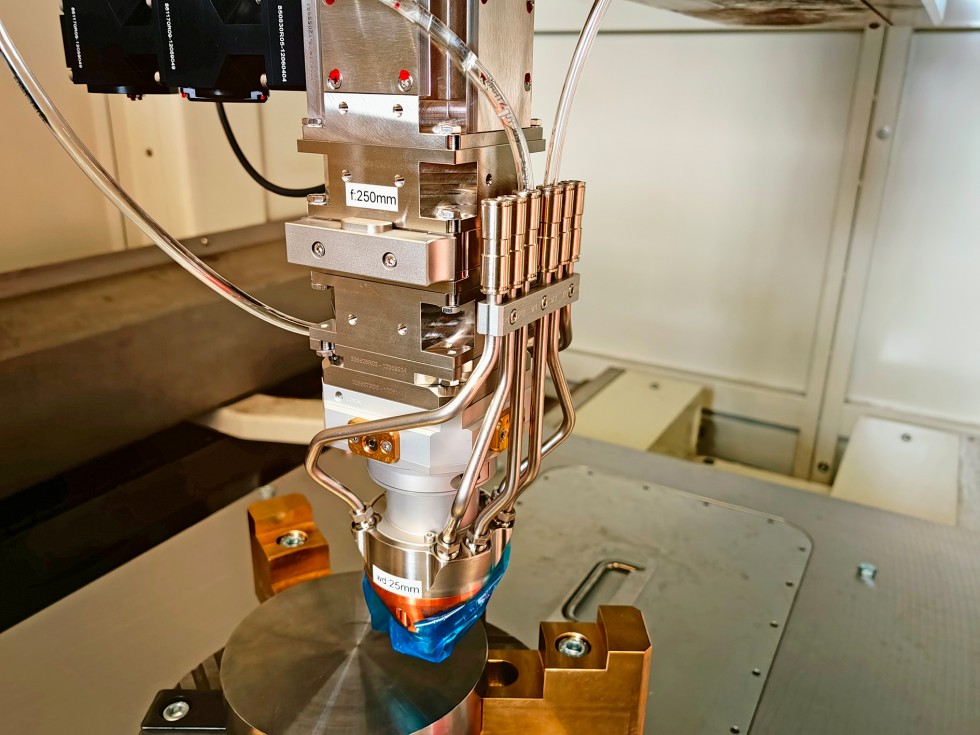
Laserkopf für das Pulverschweißen: Die sechs Zuführrohre für das Pulver führen von der Klemmleiste in der Bildmitte rechts herunter zum Strahlbereich.
Foto: Klaus Vollrath
Das gleiche gilt für die enorme Bandbreite an Prozess- und Automationstechnologien. Eine große Auswahl langjährig bewährter Zulieferpartner optimiert die Technologie. Mit diesen – ebenso wie mit zahlreichen Forschungseinrichtungen – wird auch gemeinsam Forschung und Entwicklung betrieben. Dabei geht es darum, die Machbarkeit und Optimierung von Aufgabenstellungen der Kunden abzuklären und abzusichern. An diesen Projektentwicklungen sind dann oftmals auch direkt die entsprechenden Abteilungen der Kunden beteiligt. Dank dieser Kooperationen verfüge das Arnold-Team über ein besonders breites Know-how.
Vielfältige Anwendungsbereiche
„Unsere Aufgabenstellungen gehen mittlerweile weit über die ursprünglichen Standardschweißungen an Stählen und Aluminium hinaus“ erläutert H. Klotz. Heute lassen sich selbst exotische Werkstoffe wie pulvermetallurgisch erzeugte Molybdän-Kupfer-Verbunde fügen. Auch Schweißverbindungen von Aluminium-Druckguss mit Walzaluminium oder druckdichte Schweißverbindungen an großflächigen Edelstahlblechen für Wärmetauscher werden mithilfe der Anlagentechnik erzeugt.
Praktiziert werden unter anderem Tiefschweißen, Pulverauftragsschweißen, Löten oder Härten. Eine Sonderanlage erledigt sogar das Entgraten von Schnittkanten durch kurzes Anschmelzen. Andere löten exotische Werkstoffe in einer Vakuumkammer, härten genau definierte Oberflächenbereiche oder polieren Glasbauteile mittels Laser. Es gibt zudem extrem anspruchsvolle Sonderlösungen für die Behandlung von korn-orientierten Elektroblechen für die Trafoherstellung oder für die Erzeugung feinster Lochbilder in Maschinenkomponenten für die Papierherstellung. In einem anderen Fall ging es um die Entwicklung einer hochgenauen Strahlführung für das kontinuierliche Verschweißen von Plattierungsblechen mit Rohren innerhalb des engen Spalts zwischen Rohr und Blech während des Aufwickelns. Für Versuche sowie für Auftragsspitzen oder besonders ausgefallene Aufgabenstellungen verfügt Arnold der Spezialmaschinenbauer über einen eigenen Job-Shop mit gut adaptierbaren Anlagen.
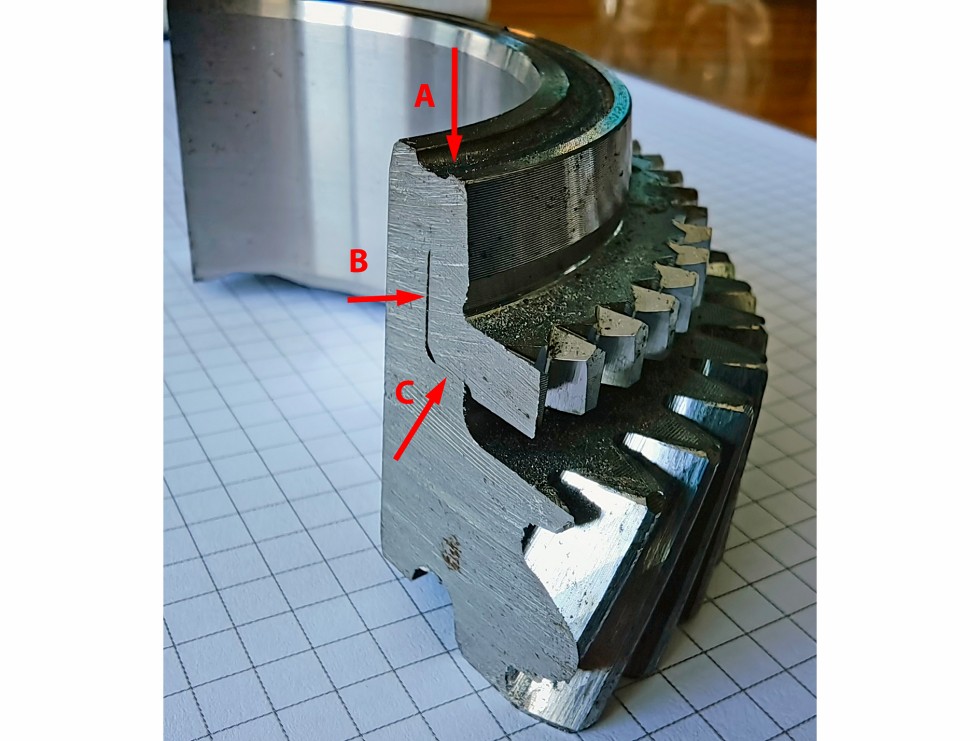
Schweißbaugruppe aus Getrieberad und Synchronring. Der separat hergestellte Synchronring wird über eine Presspassung (im Bereich oberhalb des „B“) bis zum Anschlag „C“ auf das Getrieberad gepresst. Die Tiefschweißnaht „A“ reicht mehrere mm weit ins Material.
Foto: Klaus Vollrath
Modulares, flexibel adaptierbares Zellendesign
„Angesichts der Vielfalt der an uns herangetragenen Kundenwünsche legen wir unsere Systeme so modular und so vielseitig anpassbar wie möglich aus“, verrät H. Klotz. Die dadurch mögliche Kostensenkung bei der Grundstruktur verschaffe den Entwicklern Freiräume, um sich verstärkt auf die Optimierung der kundenspezifischen Sonderausstattungen zu konzentrieren. Beispiel für einen solchen Anlagentyp ist das „Flexline“-3D-Lasersystem, das große Fahrwege auf relativ kleiner Grundfläche bietet. Das tragende Grundgestell, auf dem alle Komponenten aufgebaut sind, erlaubt nach der Abnahme den schnellen Transport zum Kunden. Die jeweils gewünschte 5-Achs-Kinematik kann durch verschiedene Kombinationen von Fahrwegen, Optik und Werkstück realisiert werden. Die verschiedenen Köpfe lassen sich schnell austauschen.
Fokus Weltall: Universalanlage für die Forschung
„Für ein Projekt, bei dem es um den langzeitig vakuumdichten Verschluss eines Elektronikgehäuses für den Satelliteneinsatz geht, arbeiten wir bereits seit Jahren mit der Firma Karl H. Arnold eng zusammen“, sagt Dr.-Ing. Norbert Müller. Er ist am Ferdinand-Braun-Institut, Leibniz-Institut für Höchstfrequenztechnik in Berlin tätig. Im Rahmen des Projekts kommt eine modulare, äußerst flexibel verwendbare Anlage des Typs Flexline zum Einsatz, die mit zwei unterschiedlichen Laserquellen ausgestattet werden kann. Eine Schnellkuppel-Schnittstelle ermöglicht den Einsatz von bis zu drei Laseroptiken.
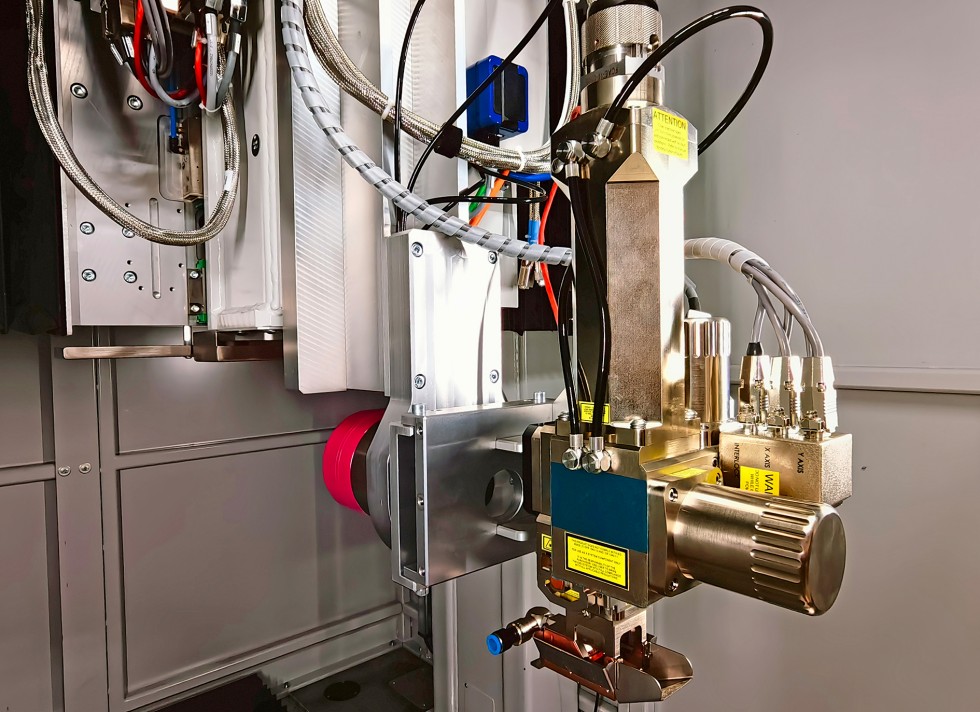
Blick in den Innenraum der Flexline mit einem Monomode-Strahlkopf in Arbeitsposition. Der Wechsel ist schnell erledigt. Es müssen nur wenige Schrauben und Steckverbindungen gelöst werden.
Foto: Klaus Vollrath
Die Anlage ist mit allen Festkörper-Laserquellen kompatibel und kann sowohl für Forschungszwecke als auch für die Entwicklung von Prozessen oder zur Bearbeitung von kleineren Serien verwendet werden. Im vorliegenden Fall ist sie mit einem 200-W-Multimode-Laser für Lötanwendungen sowie einem 2-kW-Singlemodelaser für Schweißaufgaben ausgestattet. Primäre Aufgabe ist derzeit die Entwicklung eines Lötverfahrens für ein Elektronikgehäuse, welches ein ausgeklügeltes Gasgemisch im Vakuum des Weltalls für mindestens 15 Jahre sicher einschließen soll. Dieser Lötprozess muss in einer eigens hierfür entwickelten Vakuumkammer ablaufen. Wegen Platzproblemen am Institut erfolgten gemeinsame Entwicklungsarbeiten bisher in den Werkshallen von Arnold in Ravensburg.
Mit dem Entwicklungspartner „sehr zufrieden“
„Die Entscheidung für die Firma Arnold fiel schon, bevor mir die Verantwortung für das Projekt übertragen wurde“, erinnert sich Dr. Müller. Schon seine Vorgänger hätten bei der Beschaffung auf die Qualität und Professionalität aus Ravensburg gesetzt, und er könne diese Einschätzung aufgrund der im Laufe der letzten zwei Jahre gemachten Erfahrungen vollauf bestätigen. Bei allen aufkommenden Fragen und Problemen waren die Fachleute von Arnold stets kompetent und reaktionsschnell. Seine Mitarbeiter konnten ihre Versuche an der in Ravensburg betriebsfertig installierten Anlage durchführen.
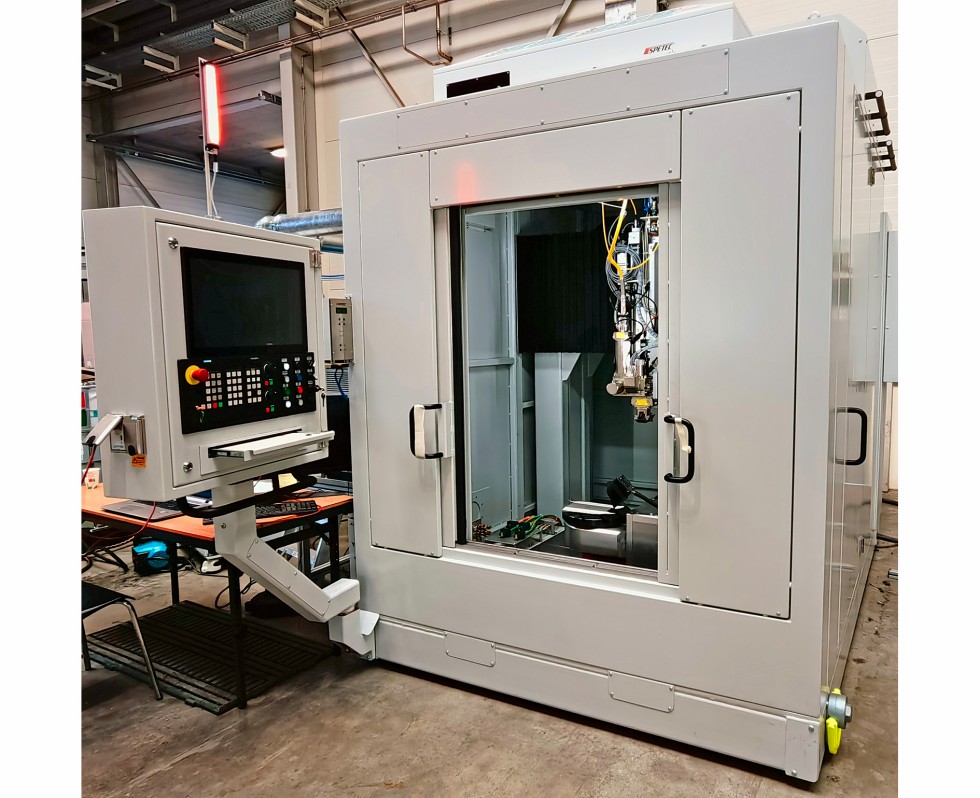
Diese modulare, flexibel verwendbare Anlage des Typs „Flexline“ steht den Forschern vom Ferdinand-Braun-Institut bereits jetzt für Projektarbeiten zur Verfügung.
Foto: Klaus Vollrath
Als Entwickler, die sich in ein kompliziertes Neuland vorzutasten hatten, kamen viele Fragen auf, die bis ins Detail zu beantworten waren. Die besonderen Bedürfnisse des Instituts seien mit Verständnis und Hilfsbereitschaft erfüllt worden. Die hohe Bereitschaft, sich an einer dynamischen, vorher nicht genau per Lastenheft definierbaren Entwicklung zu beteiligen, ist für ihn als Forscher eine große Hilfe. Das habe sich auch gezeigt, als sich herausstellte, dass die für die Anlage vorgesehene neue Halle eine zu geringe Deckenhöhe hatte. Die Konstrukteure bei Arnold entwickelten hierfür extra eine geteilte Deckelkonstruktion, die das Aufstellen am neuen Standort möglich macht.
Das könnte Sie auch interessieren:
Machine Learning unterstützt Überwachung von Schleifprozessen
Die gesamte Prozesskette des Additive Manufacturing im Blick
Klaus Vollrath ist freier Fachjournalist in Aarwangen/CH.