Additive Fertigung in der Automobilindustrie
Seit einiger Zeit ist es technisch möglich, mithilfe des 3D-Drucks Konstruktionen umzusetzen, die klassisch nicht gefertigt werden können. Voraussetzung dafür sind in erster Linie neue Denkansätze. Als Engineeringpartner der Automobilindustrie beschäftigt sich csi bereits seit Anfang 2013 mit diesem Thema und setzt unter anderem bei dem Projekt „3i-Print“ metallischen 3D-Druck intensiv ein.
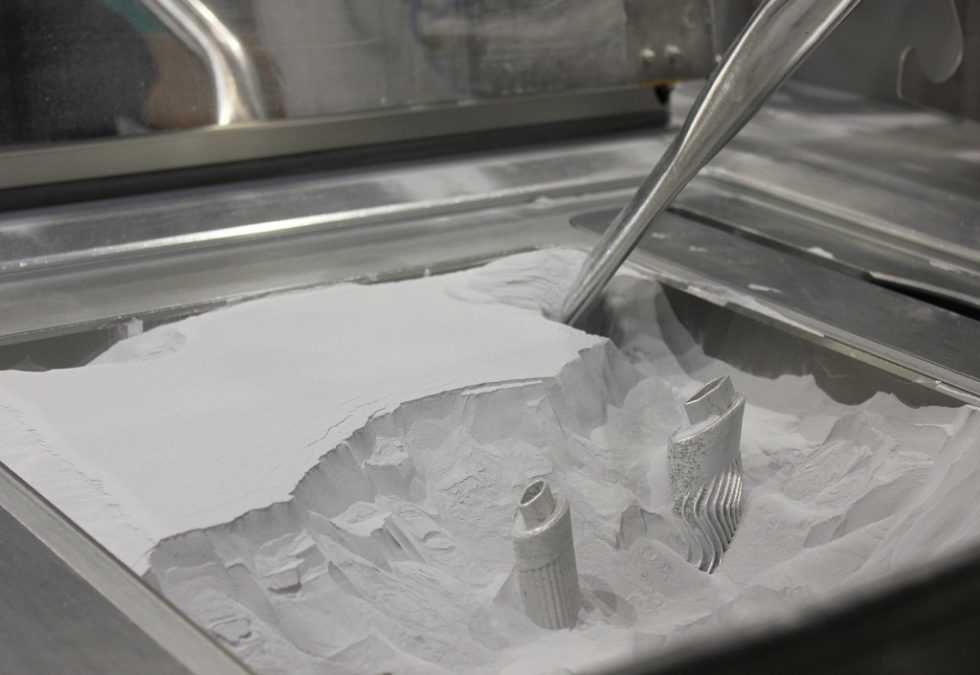
Bild 1. Für den Einsatz in der Automobilindustrie sieht csi das pulverbettbasierte ‧Laserschmelzen als besonders zukunftsträchtiges additives Fertigungsverfahren. Bild: csi
Der Leichtbauexperte Stefan Herrmann weiß um die vielfältigen Vorteile dieser neuen Technologie – er ist aber auch davon überzeugt, dass sie mittelfristig übliche Fertigungsverfahren ergänzen und nicht ersetzen wird.
Additive Fertigung hat zahlreiche Vorteile. So kann der Anwender beispielsweise seinen Werkstoff frei wählen. Ob Stahl, Aluminium, Titan oder andere Metalle – das Prinzip für die Herstellung und die einzusetzende Anlage bleiben weitgehend gleich. Zudem werden keine Werkzeuge benötigt, was Kosten für den ansonsten teuren Werkzeugbau entfallen lässt. In Konsequenz daraus kann die Fertigung sehr flexibel arbeiten. Stückzahl „1“ ist kein Problem.
Neue Freiheiten nutzen
Als ebenso wichtig bezeichnet Herrmann, Experte bei csi, die neuen ästhetischen Freiheiten: „Wir können Bauteile ganz anders gestalten und neue Funktionen integrieren. So lassen sich etwa durch ,intelligente‘ Konstruktionen thermische Wärmeleiteffekte nutzen, Luft- oder Flüssigkeitsleitungen integrieren oder eine Lastpfad- und Crash-optimierte Topologie anwenden.“ Da beim 3D-Druck keine Werkzeugtrennungen und Entformschrägen notwendig sind, erweitert sich die gestalterische Freiheit der Konstruktion zusätzlich.
Das Potential des 3D-Metalldrucks ist demnach sehr groß. Doch welche Verfahren werden „das Rennen machen“, in welchem Umfang wird die additive Fertigung zum Einsatz kommen, und wie lassen sich deren Vorteile am besten nutzen? csi stellt sich diese Fragen schon seit Jahren und hat inzwischen einige Antworten parat.
Derzeit entwickelt sich laut dem Engineering-Unternehmen das pulverbettbasierte Laserschmelz-Verfahren, Bild 1, besonders positiv. In Forschung und Entwicklung sind hier jedes Jahr große Entwicklungssprünge zu erkennen. Zwar werden der Baugeschwindigkeit dieser Maschinen immer physikalische Grenzen gesetzt bleiben, die Möglichkeiten der Individualisierung sind dafür jedoch enorm. Jedes Bauteil kann komplett anders aussehen, denn aus dem Pulverbett lassen sich völlig flexible Geometrien herstellen. Doch auch alternative Verfahren wie das „Binder Jetting“ stehen bereits „in den Startlöchern“ und finden weitere Verbreitung. Diese müssen sich allerdings noch weiter in der Praxis beweisen.
Bauteilgestaltung ist entscheidend
Entscheidend ist primär die intelligente Bauteilgestaltung und Konstruktion. Es gilt beispielsweise, Stützstrukturen weitgehend zu vermeiden und an Stellen, wo das nicht möglich ist, die Strukturen so zu konstruieren, dass sie einen technischen Zweck erfüllen. Denn Stützstrukturen können generell vielfältige Funktionen übernehmen – sowohl für die Wärmeabfuhr im Bauprozess, als auch für das tatsächliche Stützen über Kopf hängender Bauteilstrukturen. „Hier sind top-geschulte und erfahrene Konstrukteure gefragt, die wissen, worauf es bei diesem Fertigungsverfahren ankommt“, berichtet Herrmann und ergänzt: „Sie sollten zum Beispiel in den Bahnen denken, die der Laser abfährt. Außerdem müssen sie berücksichtigen, wie sich der Werkstoff bei entsprechend hoher Wärmezufuhr verhält, damit sich die Bauteile dadurch möglichst wenig verziehen.“
Sehr interessant sind auch hybride Verfahren, zum Beispiel „Laser Metal Deposition“. Hierbei werden konventionell hergestellte Halbzeuge „umdruckt“, Bild 2.
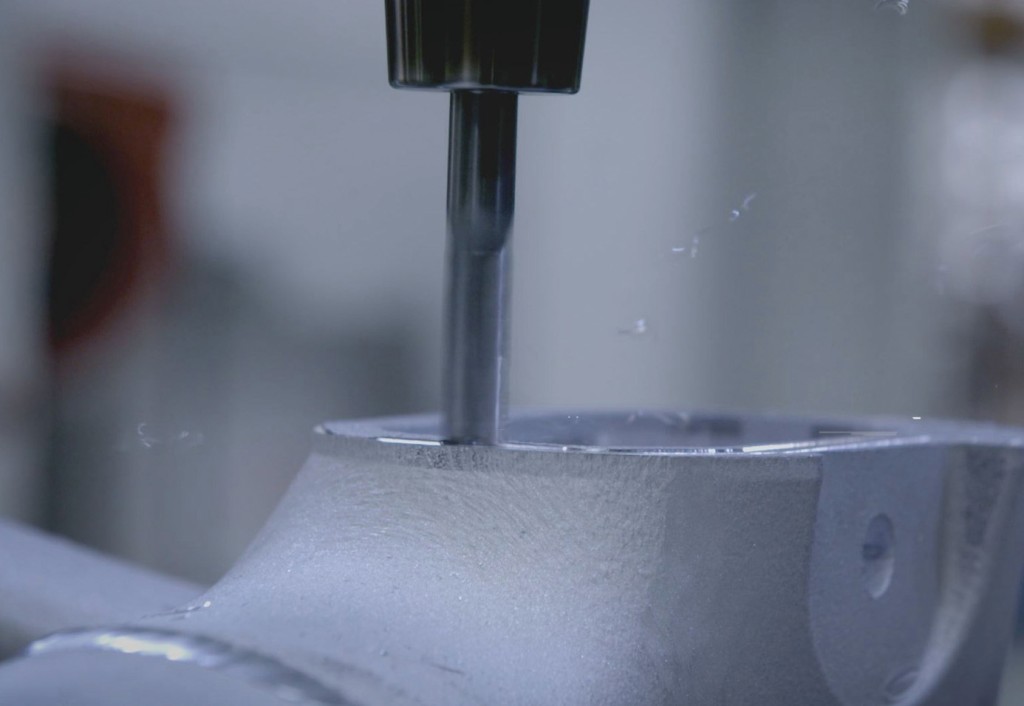
Bild 2. Die additive Fertigung wird mittelfristig in den meisten Fällen klassische Fertigungsverfahren ergänzen und nicht ersetzen. Konventionell hergestellte Halbzeuge werden beispielsweise „umdruckt“.
Für bestimmte Anwendungen kann dies hinsichtlich Geschwindigkeit und Kosten erhebliche Vorteile bringen. Denn klassische Fertigungsverfahren haben nach wie vor viele Vorzüge, die genutzt werden sollten. csi-Ingenieur Herrmann dazu: „Es darf nicht der Eindruck entstehen, dass wir mittelfristig jedes Fahrzeug drucken. Da gibt es klare physikalische Grenzen, und auch wirtschaftlich macht das keinen Sinn. Die Verfahrensentwicklung schreitet aber tatsächlich sehr schnell voran und wir wissen noch nicht mal annähernd wohin die Entwicklung führt.“
Insbesondere die Herstellung von sehr großen Bauteilen als kompletter 3D-Metalldruck aus dem Pulverbett heraus wäre viel zu teuer. Dafür wären riesige Fundamente nötig – und den Abmaßen der Produkte entsprechend müsste der Bauraum komplett mit Pulvermaterial gefüllt sein. Das bindet enorm viel Kapital – insbesondere beim Einsatz teurer Materialien wie Titan. Nicht zu vergessen: Um das wertvolle Pulver wiederverwenden zu können, muss es aufwendig recycelt werden. Auch die Oberflächengüte ist oft nicht ausreichend, Bild 3.
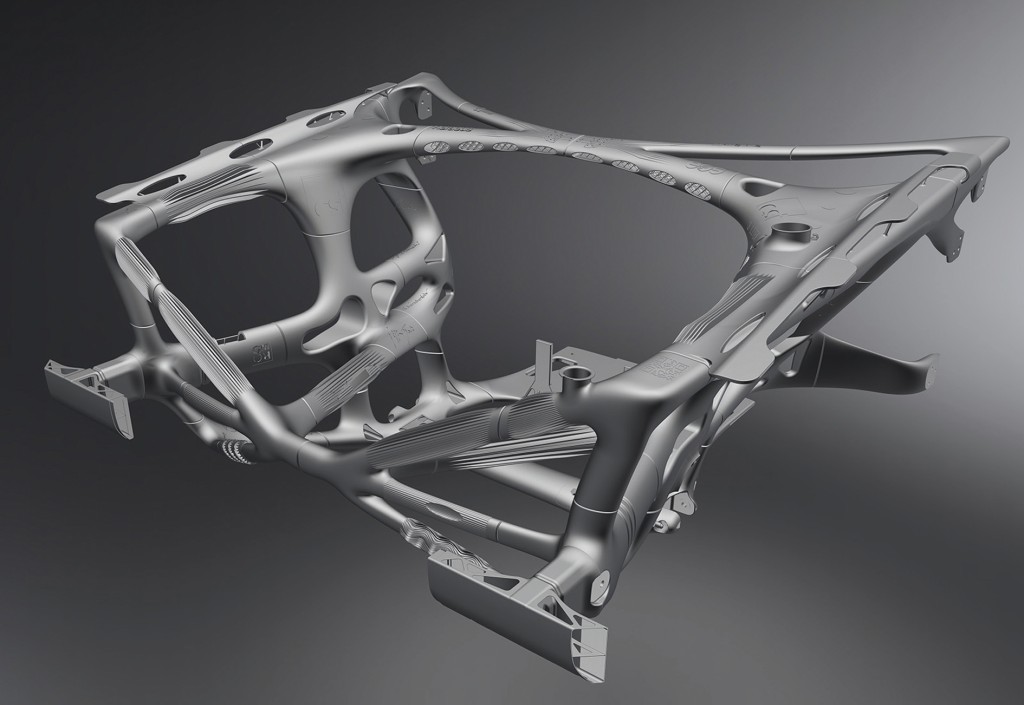
Bild 3. Die Oberflächengüte von 3D-Druck-Bauteilen ist vergleichbar mit der von Druckgussbauteilen: Die optische Oberflächenqualität reicht für Einsätze bei Außenhautanwendungen noch nicht aus. Bild: csi
Konzeptstudie bringt praktische Erfahrung
Wie kann also additive Fertigung sinnvoll genutzt werden? Für die richtige Antwort braucht der Konstrukteur praktische Erfahrung. Nicht zuletzt deshalb hat csi im Oktober 2016 mit dem „3i-Print-Projekt“ eine Konzeptstudie gestartet, die die Entwicklung des Karosseriebaus der Zukunft betrachtet. In diesem Projekt hat csi gemeinsam mit namhaften Partnern (siehe gelber Kasten) den kompletten Vorderwagen eines VW Golf 1 Caddy für den 3D-Druck konstruiert, produziert und montiert. Der Vorderwagen wurde deshalb ausgewählt, weil er besonders viel Lernpotential bietet – schließlich zählt er zu den komplexesten Umfängen des Rohbaus, Bild 4.
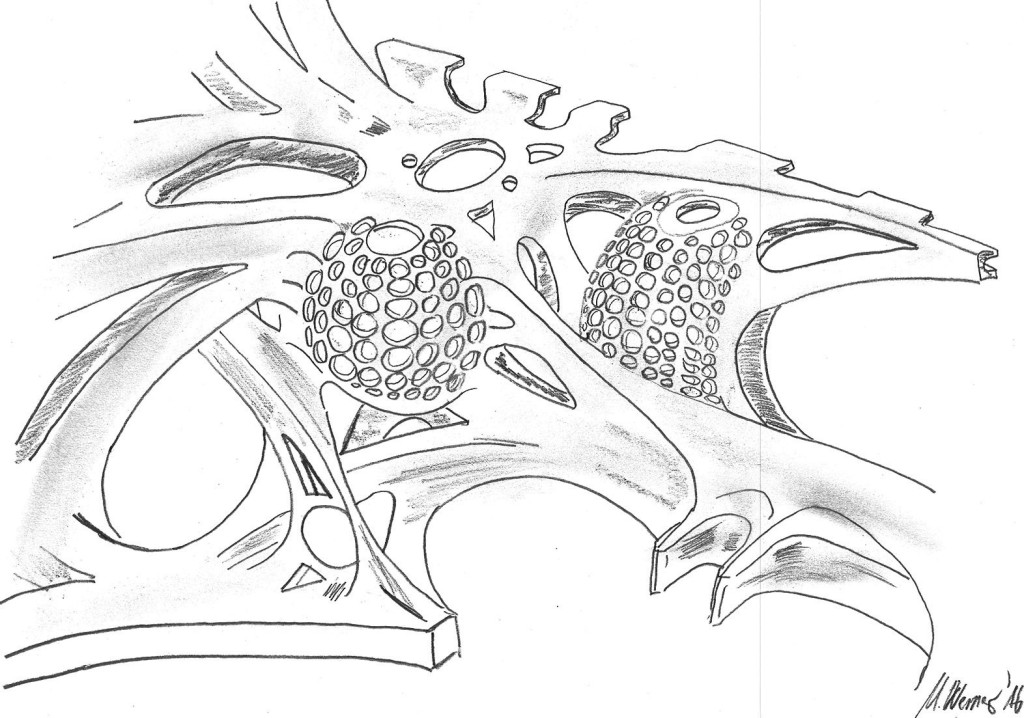
Bild 4. Auf Basis von Handskizzen wurden zunächst erste Entwürfe der Struktur erarbeitet, diese virtuell ausgelegt und die Ergebnisse der Optimierungsläufe in einem eigens für Additive Manufacturing etablierten Prozess zum Vorderwagenkonzept auskonstruiert. Bild: csi
Hierbei gilt es zahlreiche funktionale und geometrische Rahmenbedingungen aus dem Gesamtfahrzeug-Bereich zu beachten – beispielsweise Fußgängerschutz, Crash, Steifigkeit, Produzierbarkeit.
Ebenso interessant: Durch eine geschickte Konstruktion lassen sich Probleme hinsichtlich „Package“ und Wärmeabfuhr lösen. Die Idee: ein „mitkühlender“ Rahmen. Dadurch ließe sich der eigentliche Kühler des Fahrzeugs verkleinern. Solche Ansätze zu nutzen, dürfte für Nischenfahrzeuge im Hochpreissegment schon bald interessant sein. Denn 3D-Metallteile haben laut Herrmann schon heute eine hohe und zuverlässig produzierbare Qualität: „Additiv gefertigte Bauteile haben verschiedenste Freigaben im Bereich der Luftfahrt – aus Kunststoff und aus Metall. Das beweist, dass der Prozess stabil ist.“
Namhafte Partner
Am Anfang des Prozesses standen die Produkte von Altair: Deren Tools werden bei csi bereits seit einiger Zeit für die methodische Auslegung und Optimierung von Leichtbaustrukturen eingesetzt und tragen dazu bei, im Hinblick auf die additive Fertigung zielgerichteter konstruieren. Beim verwendeten Pulver handelt es sich um ein hochlegiertes „Scalmalloy“-Aluminium-Pulver von Heraeus, dem Weltmarktführer im Bereich der Pulverherstellung.
Für die Fertigung der Einzelteile des Rahmens stellte EOS, Kraillig, eine „M400“ zur Verfügung. Dieses ultraschnelle Laser-System eignete sich mit seinem Bauvolumen von 400 mm x 400 mm x 400 mm und einer 1000 W-Laserleistung ideal für die hohen Anforderungen. Erfahrene Mitarbeiter gaben wichtige Hinweise im Hinblick auf die Parameterwahl. Inzwischen wurden zahlreiche csi-Konstrukteure über das EOS-Tochterunternehmen Additive Minds auch diesbezüglich geschult.
Den Druck des Rahmens hat mit APworks eine Tochter der Airbus-Group übernommen. Durch diese Zusammenarbeit kam darüber hinaus der Zugriff auf den hochfesten Aluminiumwerkstoff Scalmalloy zustande. Gemeinsam mit APworks hat csi an der Qualifizierung des Materials gearbeitet sowie Materialkarten erstellt. Das ist insofern sehr wichtig, weil heute kein Werkstoff mehr für Fahrzeuge verwendet werden darf, der nicht komplett in der Simulation virtuell abgebildet werden kann.
Beim Zusammensetzten der einzelnen Teile bekam csi Unterstützung von der Firma Gerg. Die erfahrenen Prototypenbauer haben den Rahmen aus den einzelnen Elementen geschweißt und sozusagen „die Gedanken materialisiert“. Hierzu ist sehr viel Erfahrung notwendig, da ein solcher Rahmen als Baugruppe extrem geringe Fertigungstoleranzen hat. Es wird noch anspruchsvoller, weil etwaige Schweißverzüge schnell das komplette Ergebnis „ruinieren“ können. Die Prozesskette ist an dieser Stelle besonders fragil – für den kompletten Rahmen gab es nur einen einzigen Versuch.
Fazit
Herrmann will die neuen Möglichkeiten auch weiter für die Automobilindustrie nutzen. „Dennoch bin ich absolut überzeugt, dass die generative Fertigung in absehbarer Zeit ein zusätzlicher Baustein in der Auswahl verfügbarer Fertigungsverfahren sein wird. Und die Gewichtung wird sich zunehmend in Richtung 3D-Druck verschieben.“ Wie schnell das geht, hängt jedoch nicht zuletzt von der Entwicklung der Wirtschaftlichkeit der Verfahren und der verwendeten Materialien ab.
csi entwicklungstechnik
Das Unternehmen ist Entwicklungspartner der Automobilindustrie, beschäftigt rund 600 Mitarbeiter und hat ihren Hauptsitz in Neckarsulm. Weitere Niederlassungen befinden sich in Ingolstadt, Sindelfingen, München, Wolfsburg, Zwickau, Weissach und Winterberg (Alu-Car). Bedeutende Automobilhersteller und zahlreiche Systemlieferanten vertrauen auf das Know-how bei der Entwicklung kompletter Module für Oberflächen (Strak), die Karosserie und das Interieur. Spezialisiert auf den Produktentstehungsprozess der Automobilbranche, unterstützen die csi-Teams ihre Kunden auch durch Beratungsdienstleistungen, ein Aus- und Weiterbildungsangebot an der „csi akademie“ sowie im Projektmanagement über alle Bauphasen hinweg.
csi verwaltungs GmbH, Robert-Mayer-Str. 10, 74172 Neckarsulm, Tel. 07132 / 9326-0, E-Mail: info@csi-online.de, Internet: www.csi-online.de
Peter Klingauf betreibt die Agentur k+k-PR in Augsburg.