Aktive Schwingungsdämpfung als Retrofit-Lösung für Werkzeugmaschinen
Das Zeitspanvolumen von Werkzeugmaschinen wird häufig nicht durch die installierte Antriebsleistung begrenzt, sondern durch das Auftreten von hohen Schwingungsamplituden (Ratterschwingungen), welche in den kritischen Eigenfrequenzen auftreten. Eine aktive Schwingungsdämpfung ist eine kostengünstige Retrofit-Lösung, um auftretende Schwingungen zu unterdrücken und so die ratterfreien Zeitspanvolumina weiter zu erhöhen.
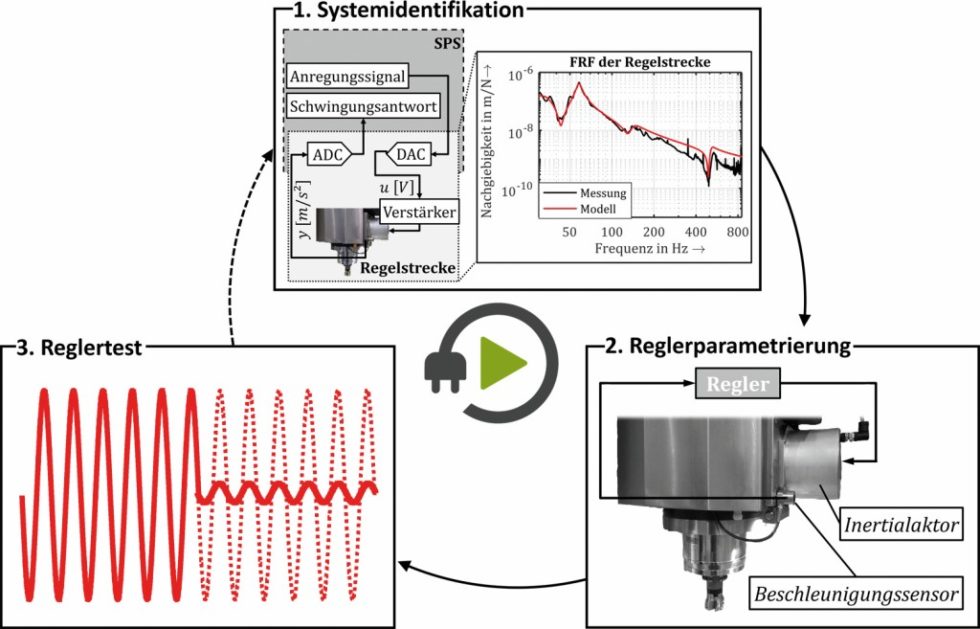
Systemaufbau und Ablauf der automatischen Konfiguration. Bild: iwb, TU München
Vorgestellt wird die Implementierung einer aktiven Schwingungsdämpfung an zwei unterschiedlichen Werkzeugmaschinen, wovon sich eine bereits im Serienproduktionseinsatz befindet. Die im Normalfall sehr aufwendige Parametrierung des Systems findet dabei automatisiert statt.
Die Produktivität von spanenden Werkzeugmaschinen wird häufig durch das Auftreten von Instabilitäten während des Zerspanprozesses begrenzt.
Einleitung und Zielsetzung
Wird bei festgelegten Prozessparametern die axiale Schnitttiefe zur Steigerung des Zeitspanvolumens über die Stabilitätsgrenze hinaus erhöht, so treten deutliche Ratterschwingungen am Werkzeug auf, welche die Maschine beschädigen können, den Verschleiß des Werkzeugs erhöhen und die Oberflächengüte des Werkstücks verschlechtern [1]. Durch eine aktive Schwingungsdämpfung kann die Stabilitätsgrenze und damit die Produktivität der Werkzeugmaschine erhöht werden [2]. Der Vorteil aktiver Systeme gegenüber herkömmlichen Strategien besteht darin, sich variablen Systemeigenschaften und Schwingungscharakteristiken anzupassen [1].
Während eingebettete Lösungen zur aktiven Schwingungsdämpfung bereits existieren [3;4], kommen Retrofit-Lösungen bisher aufgrund des hohen Konfigurationsaufwands und des unbekannten Ausfallverhaltens nicht zum Einsatz. Am Institut für Werkzeugmaschinen und Betriebswissenschaften (iwb) der Technischen Universität München wurde in Kooperation mit Schaeffler Technologies und der Spinner Werkzeugmaschinenfabrik eine automatische Konfiguration für aktive Schwingungsdämpfungssysteme entwickelt und die Robustheit sowie die Leistungsfähigkeit im industriellen Einsatz untersucht.
System-Hardware
Die Retrofit-Lösung wurde an zwei verschiedenen Werkzeugmaschinen installiert. Zum einen stand das Fräsbearbeitungszentrum „Spinner U5–620“ in der lehrstuhleigenen Versuchshalle für Versuche zur Verfügung, zum anderen wurde eine Vertikaldrehmaschine des Typs „Pittler PV 630“, die sich in der Lagerfertigung bei Schaeffler im Einsatz befindet, mit einem aktiven Schwingungsdämpfungssystem ausgestattet. Das Ziel besteht darin, die während des Zerspanungsprozesses auftretenden Schwingungen durch eine um 180° phasenverschobene Gegenschwingung auszulöschen. Hierzu werden die Schwingungen der Maschine mithilfe eines Beschleunigungssensors gemessen. Dieses Messsignal wird für die Berechnung des passenden Reglerstellsignals verwendet.
Das Reglerstellsignal wiederum wird dem Inertial-Aktor als Eingangsgröße zugeführt. Dieser bringt daraufhin eine Kraft auf die Maschinenstruktur auf, die die störenden Schwingungen dämpft. Bei beiden Installationen wurde sowohl für die Schwingungsmessung als auch für die Berechnung des Reglerstellsignals auf eine speicherprogrammierbare Steuerung von B&R („X20CP1586“) zurückgegriffen. Tabelle 1 gibt einen Überblick über die verwendeten Beschleunigungssensoren und -Aktoren an den beiden Werkzeugmaschinen.
Tabelle 1. Verwendete Hardware-Konfigurationen an den Werkzeugmaschinen. | |
Fräsbearbeitungszentrum SPINNER U5–620 | |
Beschleunigungssensor | KS813b SN 11023, Hersteller MMF |
Inertialaktor | SA10-V30, Hersteller CSA ENGINEERING |
Vertikaldrehmaschine PITTLER PV 630 | |
Beschleunigungssensor | 0ACS100A.90–1, Hersteller B&R |
Inertialaktor | MICA 300CM, Hersteller CEDRAT |
Inbetriebnahme eines aktiven Schwingungsdämpfungssystems
Für die Bewertung, ob der Einbau eines aktiven Schwingungsdämpfungssystems prozessstabilisierend wirkt, muss zunächst das Schwingungssignal während eines instabilen Bearbeitungsprozesses mittels einer Betriebsschwingungsmessung analysiert werden. Ein aktives Schwingungsdämpfungssystem, basierend auf einem externen Inertial-Aktor, eignet sich nur für die Dämpfung von Maschinenschwingungen. Liegen hingegen Spindelwellen-, Werkzeug- oder Werkstückschwingungen vor, wird das System zu keiner Verbesserung führen.
Ein Indiz für eine hohe Anfälligkeit für Maschinenschwingungen sind lang auskragende Strukturen. Neben der Betriebsschwingungsmessung muss zudem das dynamische Nachgiebigkeitsverhalten der Maschinenstruktur analysiert werden. Zudem gilt es, die dominante Schwingungsrichtung für das Auftreten von Ratterschwingungen zu bestimmen. Können die produktivitätsbegrenzenden Ratterschwingungen einer Maschineneigenmode zugeordnet werden, lohnt sich die Installation eines aktiven Schwingungsdämpfungssystems.
Die Positionierung sollte nach Möglichkeit an einer Stelle mit großer Schwingungsamplitude (Schwingungsbauch) geschehen [1]. In den meisten Fällen ergibt sich hieraus eine Position möglichst nah an der Prozesszone. Dabei darf es allerdings nicht zu Einschränkungen des Arbeitsraums kommen. Die erforderliche Bandbreite des Inertial-Aktors ergibt sich aus der niedrigsten und höchsten zu dämpfenden Eigenfrequenz. Für eine exakte Auslegung der benötigten Aktorkraft muss eine Struktur-Prozess-Simulation durchgeführt werden [5]. Ansonsten besteht die Gefahr, dass ein zu schwacher Aktor das maximale Zeitspanvolumen, das sich aus der installierten Spindelleistung ergibt, nicht stabilisieren kann, wohingegen ein zu starker Aktor die Kosten des Systems unnötig erhöht.
Um die Hürden für die Installation eines aktiven Schwingungsdämpfungssystems möglichst gering zu halten, wurde eine automatische Konfiguration der Regelungsparameter entwickelt. Diese gliedert sich in drei Schritte: Systemidentifikation, Reglerparametrierung und Reglertest. Mithilfe eines automatisierten Verfahrens zur Systemidentifikation wird das dynamische Nachgiebigkeitsverhalten der Werkzeugmaschine ermittelt. Die Maschinenstruktur wird mit dem installierten Inertial-Aktor angeregt. Über den Beschleunigungssensor kann die resultierende Schwingungsantwort gemessen und schlussendlich der Nachgiebigkeitsfrequenzgang ermittelt werden.
Aus dem gemessenen Nachgiebigkeitsfrequenzgang lassen sich die kritischen Eigenfrequenzen der Werkzeugmaschine bestimmen. Dann folgt die automatische Parametrierung des Reglers. Hierbei wird eine möglichst starke Dämpfung der stabilitätsbegrenzenden Eigenfrequenzen unter Berücksichtigung der maximalen Aktorkraft sowie der Stabilität des geschlossenen Regelkreises angestrebt. Abschließend folgt bei den Reglertests erneut eine Anregung der Maschinenstruktur mit dem Inertial-Aktor. Der nun aktivierte Regler registriert die resultierende Schwingungsantwort und erzeugt ein Stellsignal, das zur Minimierung der Schwingung führt. Das Ergebnis dieser Untersuchung ist das dynamische Nachgiebigkeitsverhalten der aktiv gedämpften Maschinenstruktur. [2]
Bewertung der Produktivitätssteigerung
Mithilfe der automatischen Systemidentifikation ließen sich eine kritische Eigenfrequenz von 58 Hz am Fräsbearbeitungszentrum identifizieren sowie eine Eigenmode bei 46 Hz an der Vertikaldrehmaschine [2]. Zur Beurteilung der Leistungsfähigkeit des aktiven Schwingungsdämpfungssystems wurden das Stirnfräsen an dem Fräsbearbeitungszentrum sowie das Längsdrehen an der Vertikaldrehmaschine betrachtet. Tabelle 2 gibt einen Überblick über die Prozessparameter bei den Zerspanungsversuchen.
Tabelle 2. Prozessparameter bei den Zerspanungsversuchen. | ||
Verfahrensart | Stirnfräsen | Längsdrehen |
Werkzeug | 50 mm Eckmesserkopf | Längsdrehmeißel |
Anzahl Schneiden | 4 | 1 |
Spindeldrehzahl | 557 min-1 | 188 min-1 |
Vorschub | 400 mm/min | 0,45 mm/U |
Werkstückmaterial | Stahl C45 | 100Cr6 |
Die Schnitttiefe wurde stufenförmig in Schritten von 0,2 mm je Stufe entlang der Vorschubrichtung erhöht. Mithilfe dieser Versuche kann untersucht werden, bis zu welcher Schnitttiefe ein beispielhafter Fräsprozess stabil bleibt. Bild 1 zeigt die aufgenommenen Beschleunigungssignale während des Zerspanungsprozesses.
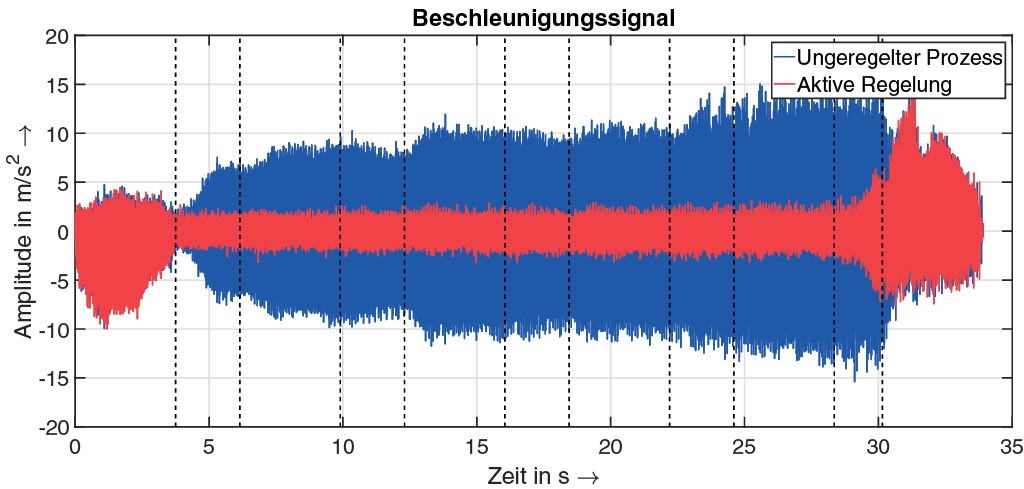
Bild 1. Vergleich der Beschleunigungssignale beim Zerspanprozess (ap = 1,2 … 2,0 mm). Bild: iwb, TU München
Es ist zu erkennen, dass die Beschleunigungssignale des ungeregelten Zerspanungsprozesses höher sind als diejenigen mit aktiver Schwingungsdämpfung.
Bild 2 zeigt die Analyse der Beschleunigungssignale im Frequenzbereich (2-fach integriert).
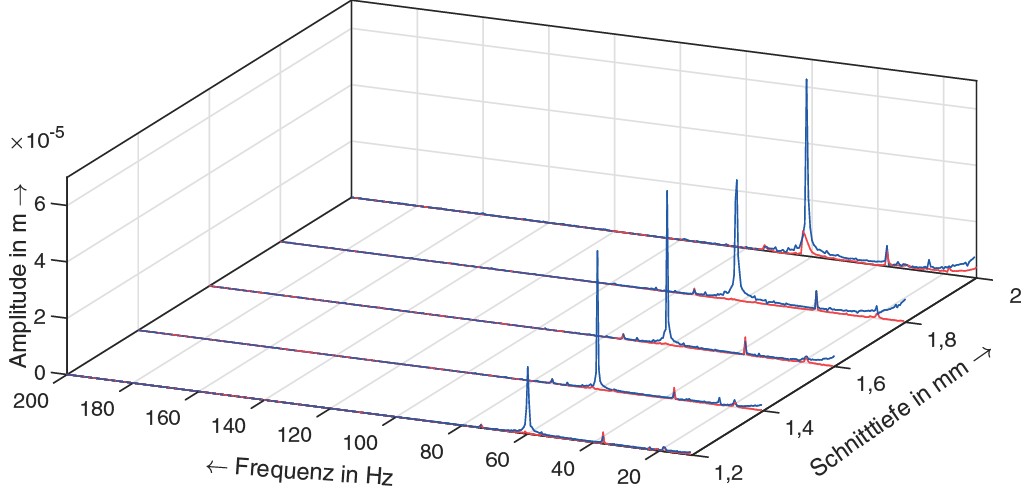
Bild 2. Vergleich des Wasserfalldiagramms (ap = 1,2 … 2,0 mm): ungeregelter Zerspanungsprozess (blau), aktive Schwingungsdämpfung (rot). Bild: iwb, TU München
Daraus ist ersichtlich, dass mithilfe der aktiven Schwingungsdämpfung die kritische Eigenfrequenz bei 58 Hz deutlich gedämpft wird.
Nachfolgend dient die Betrachtung der Schwingungsamplituden nahe der kritischen Eigenfrequenz bei 58 Hz als Basis für die Bewertung des aktiven Schwingungsdämpfungssystems, Bild 3.
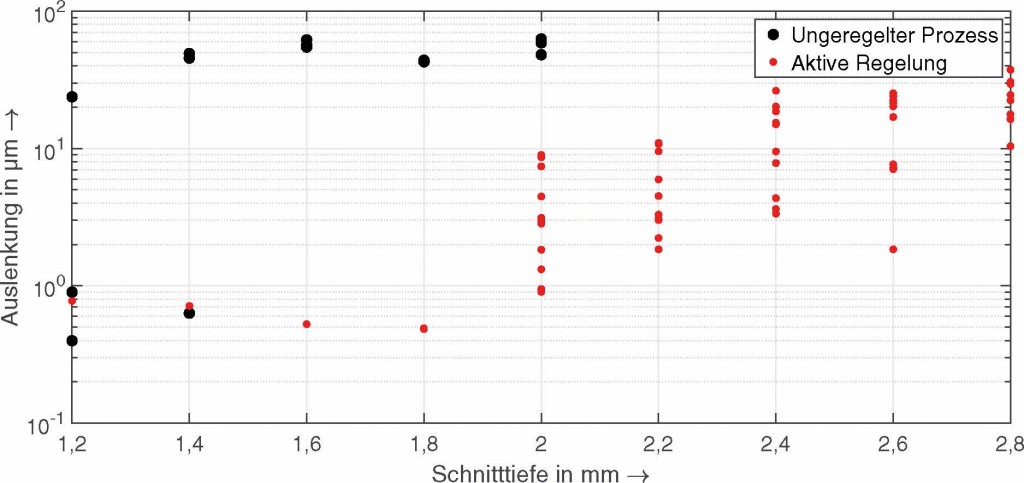
Bild 3. Vergleich der maximalen Schwingungsamplituden nahe der Eigenmode bei 58 Hz. Bild: iwb, TU München
Ohne aktive Schwingungsdämpfung treten bereits ab einer Schnitttiefe von 1,2 mm leichte Ratterschwingungen auf, wohingegen mit aktiver Schwingungsdämpfung eine Erhöhung der ratterfreien Schnitttiefe auf bis zu 2,8 mm möglich ist. Dies entspricht einer Produktivitätssteigerung von über 130 %.
Für die Vertikaldrehmaschine zeigt die Systemidentifikation eine kritische Eigenmode bei 46 Hz. Analog zu den Untersuchungen beim Fräsbearbeitungszentrum wurden auch hier die Schwingungsamplituden nahe der kritischen Eigenfrequenz analysiert, Bild 4.
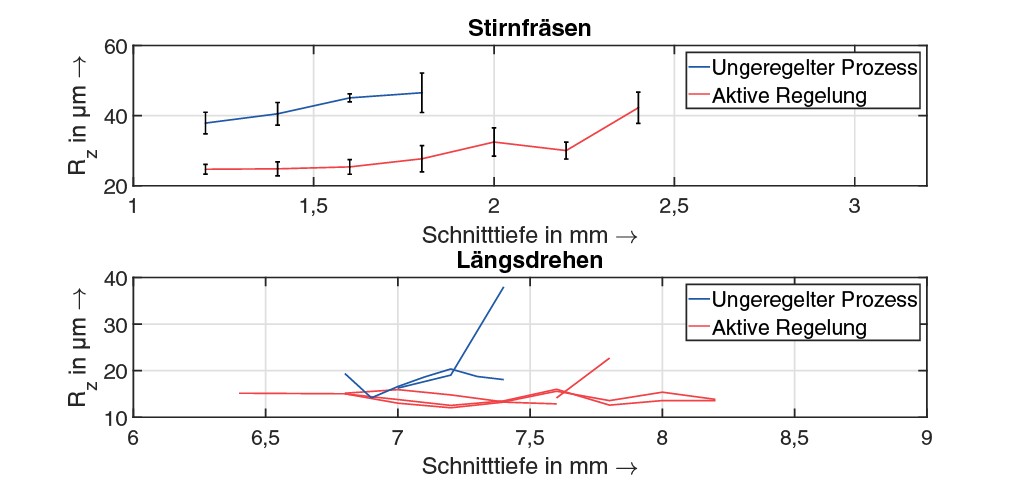
Bild 4. Vergleich der maximalen Schwingungsamplituden für das Längsdrehen nahe der Eigenmode bei 46 Hz. Bild: iwb, TU München
Ohne aktive Schwingungsdämpfung treten bereits ab 6,8 mm Schnitttiefe vereinzelt hohe Schwingungsamplituden auf. Spätestens ab 7,6 mm war der Prozess stets instabil und musste aufgrund der hohen Schwingungsamplituden abgebrochen werden. Mit aktiver Schwingungsdämpfung liegt das Schwingungsniveau durchgehend um den Faktor 10 niedriger als ohne aktive Schwingungsdämpfung. Zudem konnten Schnitttiefen bis zu 8,2 mm realisiert werden. Dies entspricht einer Produktivitätssteigerung von bis zu 20 %.
Bewertung der Oberflächenrauheit
Zur Untersuchung des Einflusses der aktiven Schwingungsdämpfung auf die Oberflächenqualität wurde das Tastschnittverfahren nach DIN EN ISO 3274 angewandt. Die Auswertung der Oberflächenprofile über der Schnitttiefe ist in Bild 5 dargestellt.
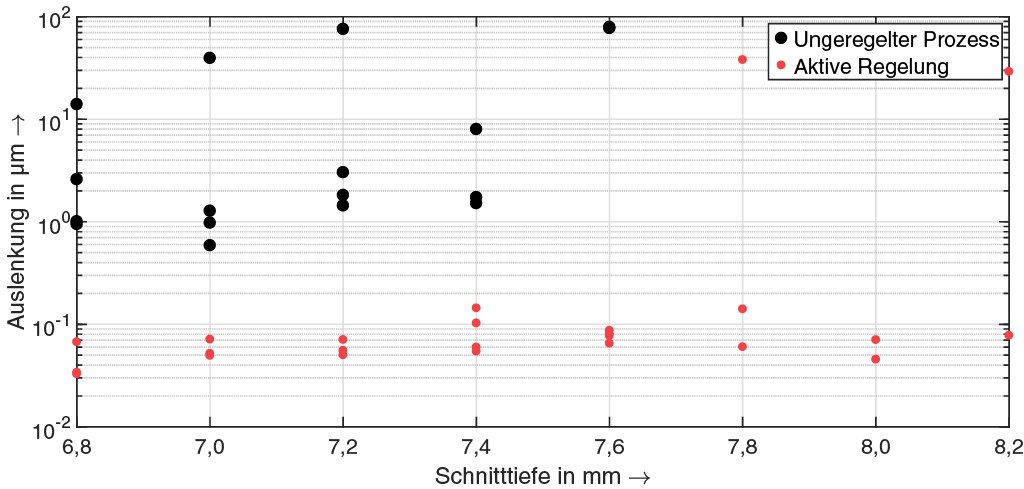
Bild 5. Vergleich der Oberflächenkenngrößen für das Stirnfräsen (oben) und für das Längsdrehen (unten). Ungeregelter Zerspanungsprozess (blau) und mit aktiver Regelung (rot). Bild: iwb, TU München
Sowohl für die Fräsversuche als auch für die Drehversuche ist eine signifikante Verbesserung der Oberflächenrauheit der Werkstücke erkennbar.
Zusammenfassung
Aktive Schwingungsdämpfungssysteme eignen sich als Retrofit-Lösung, mit denen die Produktivität und Qualität von Werkzeugmaschinen weiter erhöht werden kann. Um die Hürden für die Installation eines solchen Systems abzubauen, wurde eine automatische Konfiguration der Regelungsparameter entwickelt. Dies erlaubt es dem Endanwender auch ohne Expertenwissen, ein aktives Schwingungsdämpfungssystem in Betrieb zu nehmen. Die System-Hardware, bestehend aus einem Beschleunigungssensor, einem Inertial-Aktor und einer speicherprogrammierbaren Steuerung, kann ohne großen Aufwand in eine Werkzeugmaschine integriert werden.
In den Arbeiten zur Veröffentlichung wurden das Fräsbearbeitungszentrum Spinner U5–620 und die Vertikaldrehmaschine Pittler PV 630 erfolgreich mit einem aktiven Schwingungsdämpfungssystem ausgestattet. Neben einer signifikanten Verbesserung der erzielbaren Oberflächenrauheit konnte das maximale ratterfreie Zeitspanungsvolumen um bis zu 130 % (U5–620) beziehungsweise 20 % (PV630) gesteigert werden.
Für die Förderung des Forschungsprojektes „E²D“ im Verbundprojekt „Green Factory Bavaria“ bedanken sich die Autoren beim bayerischen Staatsministerium für Bildung und Kultus, Wissenschaft und Kunst (StMWFK).
Literatur:
[1] Baur, M.: Aktives Dämpfungssystem zur Ratterunterdrückung an spanenden Werkzeugmaschinen – Entwurf und experimentelle Validierung. iwb, Technische Universität München, 2014.[2] Zäh, M. F.; Kleinwort, R.; Fagerer, P.; Altintas, Y.: Automatic tuning of active vibration control systems using inertial actuators. CIRP Annals 66 (2017), Nr. 1, S. 365–368.[3] Beudaert, X.; Mancisidor, I.; Ruiz, L. M.; Barrios, A.; Erkorkmaz, K.; & Munoa, J.: Analysis of the feed drives control parameters on structural chatter vibrations. XIIIth International Conference on High Speed Machining (HSM 2016), Metz/Fr, 4./5. Oktober, 2016.[4] Mancisidor, I.; Beudaert, X.; Aguirre, G.; Barcena, R.; Munoa, J.: Development of an active damping system for structural chatter suppression in machining centers, Int. J. of Automation Technology, 12 (2018), Nr. 5, S. 642–649.[5] Kleinwort, R.; Weishaupt, P.; Zäh, M. F.: Simulation-Based Dimensioning of the Required Actuator Force for Active Vibration Control. Wie [4], S. 658–668.
Robin Kleinwort, M. Sc., Jahrgang 1988, studierte Maschinenwesen an der Technischen Universität (TU) München. Seit 2014 ist er wissenschaftlicher Mitarbeiter am Institut für Werkzeugmaschinen und Betriebswissenschaften (iwb) der TU München in Garching. Philipp Kapfinger, B. Sc., Jahrgang 1993, befindet sich im Masterstudiengang Maschinenwesen an der TU München. Seit 2018 ist er wissenschaftliche Hilfskraft am iwb in Garching. // Prof. Dr.-Ing. Michael F. Zäh, Jahrgang 1963, ist seit 2002 Inhaber des Lehrstuhls für Werkzeugmaschinen und Fertigungstechnik der TU München. // Christian Weiss, M. Eng., Jahrgang 1979, studierte Maschinenbau an der Hamburger Fernhochschule. Seit 2010 ist er Spezialist für Fertigungsentwicklung in der zentralen Abteilung „Entwicklung Bearbeitungsverfahren Drehen, Bohren, Fräsen“ der Firma Schaeffler Technologies AG & Co. KG in Herzogenaurach. // Dr.-Ing. Martin P. Buschka, Jahrgang 1968, studierte Maschinenbau an der Ruhr-Universität Bochum und promovierte am Institut für Spanende Fertigung der Universität Dortmund. Er ist Leiter der zentralen Abteilung Entwicklung Bearbeitungsverfahren Drehen, Bohren, Fräsen bei Schaeffler Technologies.