Bei der Spindelanalyse ist Eigeninitiative gefragt
Ein Spindelausfall tritt auf, die Werkzeugmaschine „steht“ und es gibt keine Ersatzteile? Gezeigt wird, wie Fertigungsbetriebe durch eigenes Überprüfen Ausfälle verhindern können.
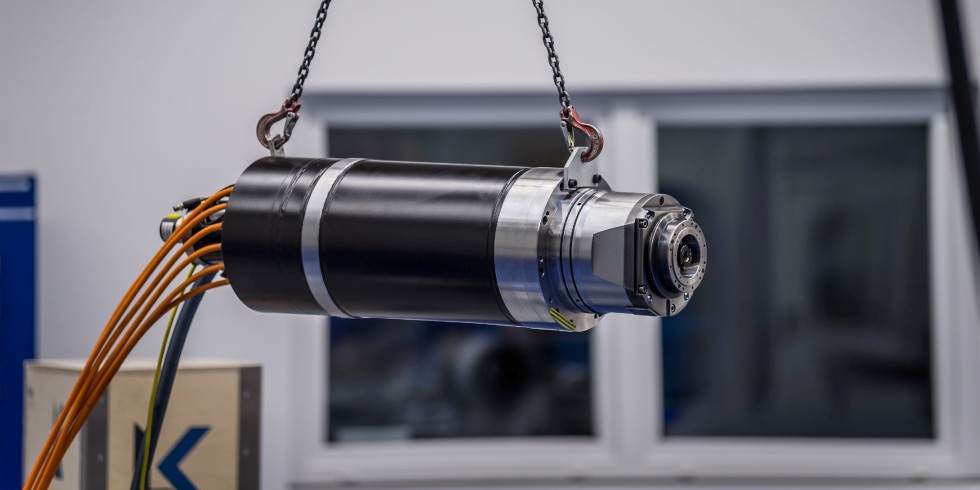
Die Spindel wurde für Reparaturzwecke ausgebaut, die Maschine "steht": der Super-Gau für produktive Fertigungsbetriebe. Vorausschauende Maßnahmen können dies vermeiden.
Foto: Kern GmbH
Die Spindel ist das Herzstück einer Maschine. Sie dient dazu, das Werkzeug aufzunehmen, und sorgt zumeist auch für den Antrieb (direkt angetriebene Motorspindel). Ihre Aufgabe ist es also, zu gewährleisten, dass Werkzeugmaschinen „laufen“. Ist eine Spindel beschädigt, führt das demnach zum Ausfall der gesamten Maschine oder sogar Anlage – und in der Folge oft auch zu langen Zwangspausen im Betrieb. Das zieht mitunter große finanzielle Einbußen mit sich.
Kritische Situation für viele Fertigungsstätten
Die aktuell herrschenden Lieferengpässe stellen viele Unternehmen vor Probleme, da sie keine Tauschspindel erhalten können, sollte ihre eigene ausfallen. Aus diesem Grund ist es wichtig, dass man einem Spindelausfall vorbeugt. Doch wie genau kann das einem Unternehmer gelingen?
Auch wenn es sich um eine sehr komplexe Angelegenheit handelt, können Betriebe selbst einen großen Teil dazu beitragen, die Spindel so lange wie möglich zu nutzen. Es gibt dabei eine Vielzahl an Faktoren, die sich überprüfen lassen, um den Stand des Verschleißes der Spindel zu erkennen oder eventuelle Probleme bereits im Voraus auszumerzen. In diesem Artikel verrät Markus Kern, Geschäftsführer der Kern GmbH in Burladingen in Baden-Württemberg, wie genau Unternehmer ihre Maschinen überprüfen können, um Fehlfunktionen zu vermeiden.
Die Spindel genauestens anschauen und auf störende Geräusche achten
Zur präventiven Instandhaltung, um also dem Ausfall der Spindel vorzubeugen, sollte man sie genau betrachten und abtasten, um zu spüren, ob sie ruhig läuft. Zudem sollte sie regelmäßig angehalten werden, um auch ihren Klang zu überprüfen – ungewöhnliche Geräusche können auf ein Problem hinweisen.
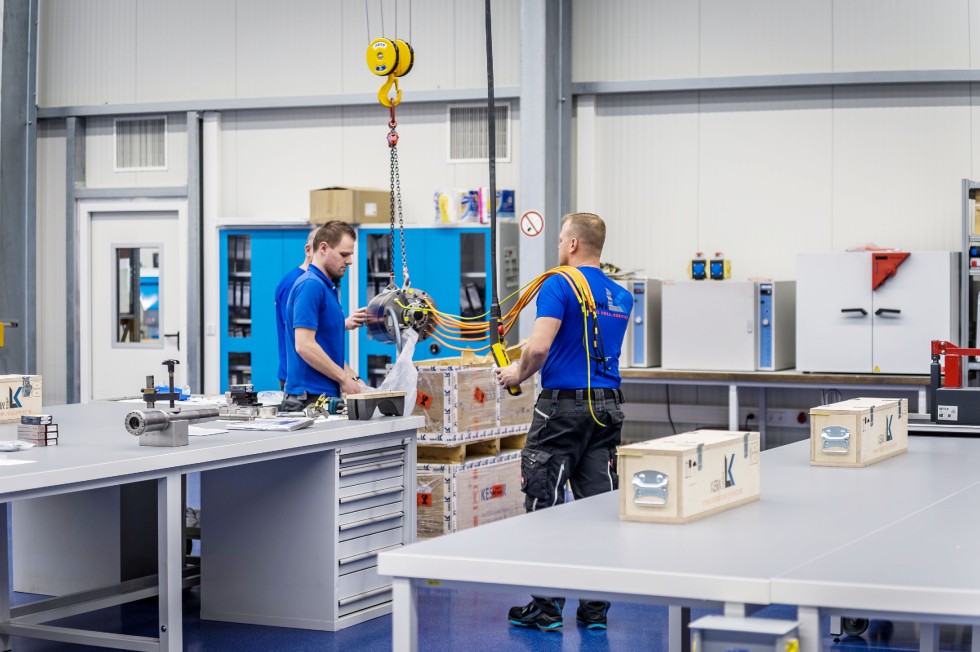
Mit präventiver Instandhaltung lässt sich die Lebensdauer der Spindel deutlich verlängern – ein Ausfall und die teure Reparatur können in aller Regel vermieden werden.
Foto: Kern GmbH
Außerdem ist es möglich, die Lagerwerte vor Ort überprüfen zu lassen, um unter anderem herauszufinden, wie gut die Spindel noch gewuchtet ist. Um sie ruhiger laufen zu lassen, kann sie gegebenenfalls nachgewuchtet werden – so lässt sich die Lebensdauer der Spindel verlängern. Zur präventiven Instandhaltung gehört es zusätzlich, den Hohlschaftkegel (HSK) oder Steilkegel (SK) zu überprüfen. Dabei sollte das Augenmerk darauf liegen, wie stark der Kegel verschlissen ist und wie der Spannsatz aussieht.
Spindel ausgefallen – was nun?
Sollte eine Spindel ausfallen, kann im ersten Schritt die Steuerung überprüft werden. Häufig reicht bereits das Austauschen der Reglerkarte aus, um die Maschine wieder zum Laufen zu bringen – zudem ist der Austausch der Reglerkarte weniger kostenintensiv als der Austausch der Spindel selbst. Sollte die Problematik auf die Steuerung zurückzuführen sein, spart man sich außerdem zukünftige Ausfälle und teure Reparaturen in fünfstelliger Summe. Auch das Kühlmedium sollte überprüft werden, da der Stator aufgrund von Verunreinigung beschädigt werden kann. Bei ölgeschmierten Spindeln ist ein häufiger Ausfallgrund ein zu niedriger Druck – daher ist auch dieser zu überprüfen.
Falls eine Spindel nicht richtig funktioniert, können auch „Lappalien“ die Schuld tragen. Beispiele hierfür sind ein nicht korrekt justierter Drehgeber oder ein Sensor, der nicht richtig auf die Maschine abgestimmt wurde. Es gibt viele verschiedene Gründe, warum es zu einem Ausfall kommen kann, die nichts mit der Spindel selbst zu tun haben. Das kann beispielsweise eine nicht funktionierende Hydraulik sein oder auch eine nicht perfekt im Boden verankerte Maschine.
Auslastung der Spindel – was ist zu beachten?
Ebenso wichtig in der präventiven Instandhaltung ist, wie man die Spindel auslastet, denn jede Spindel hat eine individuelle Drehzahl. Gerade mit großen Bearbeitungsspindeln wie Werkzeugspindeln wird teilweise viel Aluminium gefräst – das belastet dieses Bauteil sehr intensiv. Kann diese beispielsweise 16.000 Umdrehungen leisten, heißt das nicht, dass sie diese Zahl durchgehend laufen sollte. „Das lässt sich gut mit einem Auto vergleichen“, so Kern. „Der Motor eines Wagens, der 300 Kilometer in der Stunde fahren kann und auch konstant in dieser Geschwindigkeit gefahren wird, wird das auf Dauer nicht mitmachen. So funktioniert das auch mit Spindeln.“
Wenn also eine Anwendung vorliegt, bei der die Spindel sehr stark belastet wird, ist es umso wichtiger, dass diese perfekt optimiert wurde. Die Drehzahl sollte jedoch immer im Blick gehalten und in keinem Fall überschritten werden. Oft ist auch die Drehdurchführung der Grund für einen Ausfall: Wenn über eine undichte Stelle ein Kühlmedium eintritt und der Stator geflutet wurde, gibt es einen Kurzschluss und die Lager werden zerstört – so entsteht ein sehr großer Folgeschaden.
Bauteil ausbauen – Geld und Zeit sparen
„Wenn die Spindel ausfällt, hängt dies selten mit ihr selbst zusammen – denn diese ist nur der Erreger, nicht die Ursache. Dies vor allem, weil die maschinenbezogenen Anwendungen oder Probleme meistens direkt in der Maschinenumgebung liegen“, erklärt Markus Kern. Eine präventive Instandhaltung ist demnach „Gold wert“, um die Lebensdauer zu verlängern. Wichtig ist dabei Folgendes: Erkennt man anhand der getesteten Werte, dass eine Spindel eine maximale Laufdauer von vier Monaten hat, sollte man diese Zeit nicht vollständig ausreizen.
Denn im Schadensfall handelt es sich dann in der Regel um einen Totalschaden, der viele weitere Probleme mit sich zieht: Das Spannsystem und die Drehdurchführung sind in einem solchen Fall meist defekt und der Stator muss neu gewickelt werden. Auch die Lagerung ist häufig beschädigt und muss erneuert werden, ebenso wie die Aufnahme, die aufgearbeitet werden muss. Dadurch entsteht eine umfangreiche und sehr teure Reparatur.

Geschäftsführer und Firmengründer Markus Kern setzt auf eine ganzheitliche Instandsetzung, Optimierung und Modifikation von Spindeln.
Foto: Kern GmbH
Manche Firmen können die Produktion jedoch nicht stoppen und lassen die Spindel aus diesem Grund weiter laufen – mittelfristig ist das allerdings die falsche Strategie. Die umfangreiche Reparatur und die hohen Kosten können zu etwa 50 Prozent gespart werden, wenn die Spindel früher ausgebaut und repariert wird. Das Fazit von Kern lautet: Die Reparatur geht schneller, die Präzision ist höher und es werden weniger Ersatzteile benötigt.
Erfahrener Spezialist in Wartungsfragen
Als Geschäftsführer und Firmengründer der Kern GmbH hat Markus Kern über 30 Jahre praktische handwerkliche Erfahrung mit der Spindel und ein umfangreiches Wissen über Spindeltechnik. Bei seinem Unternehmen geht es um eine ganzheitliche Instandsetzung, Optimierung und Modifikation von Spindeln, sodass Kunden gerne von einer „Tuning-Werkstatt““ sprechen. Dabei arbeiten die Burladinger zu 100 Prozent herstellerunabhängig und können bereits auf mehr als 14.000 reparierte Spindeleinheiten zurückblicken – von jedem bekannten Hersteller auf dem Markt. Die Laufzeitoptimierung und dazu erforderliche tiefgehende Ausfallanalysen, die zu einer enormen Kostenersparnis bei den Kunden führen, sieht das Unternehmen als seinen Schwerpunkt an.
Das könnte Sie auch interessieren:
Spanntechnik optimiert Zerspanungsleistung beim 5-Achs-Fräsen
Für den Notfall an der Werkzeugmaschine bestens gerüstet