Dauerlauf statt Spindelstillstand im CNC-Maschinenpark
Die CNC-Technologie ist an Flexibilität, vor allem in der Fertigung von Prototypen und Kleinserien, kaum zu überbieten. Doch oftmals liegen im Maschinenpark eines Fertigungsbetriebs noch einige Reserven verborgen, die es zu heben gilt.
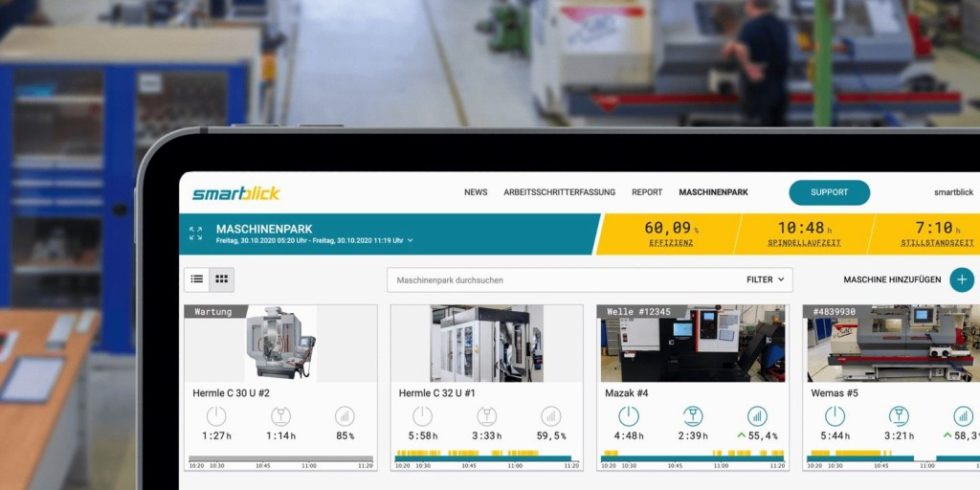
Den Maschinenpark im Blick behalten: Die aktuelle Auslastung jeder einzelnen Anlage wird visualisiert. Es lässt sich sofort erkennen, ob ungeplante Stillstände kurzfristig für zusätzliche Jobs genutzt werden könnten.
Foto: smartblick
Dank der Technologie der rechnergesteuerten Werkzeugmaschine (CNC – Computerized Numerical Control) lassen sich auf ein und derselben „Hardware“ die unterschiedlichsten Materialien verarbeiten und nahezu beliebige Produkte mit hoher Präzision automatisch herstellen. Jedoch sind zunächst einmal erhebliche Investitionen in die technische Grundausstattung zu tätigen. Daher ist es für Fertigungsbetriebe wichtig, die CNC-Maschinen möglichst rund um die Uhr laufen zu lassen. Niedrige Auslastungen führen über höhere Maschinenstundensätze schnell zu einer eingeschränkten Wettbewerbsfähigkeit des Unternehmens.
Eine neue Lösung kann diese ungenutzten Chancen jetzt heben: Mit „smartblick“ eröffnet sich die Möglichkeit, freie Kapazitäten im Maschinenpark sofort zu erkennen und unerwünschte Spindelstillstände in produktive Leistung zu verwandeln – unabhängig davon, ob es um die Verarbeitung von Metall, Holz oder Kunststoff geht.
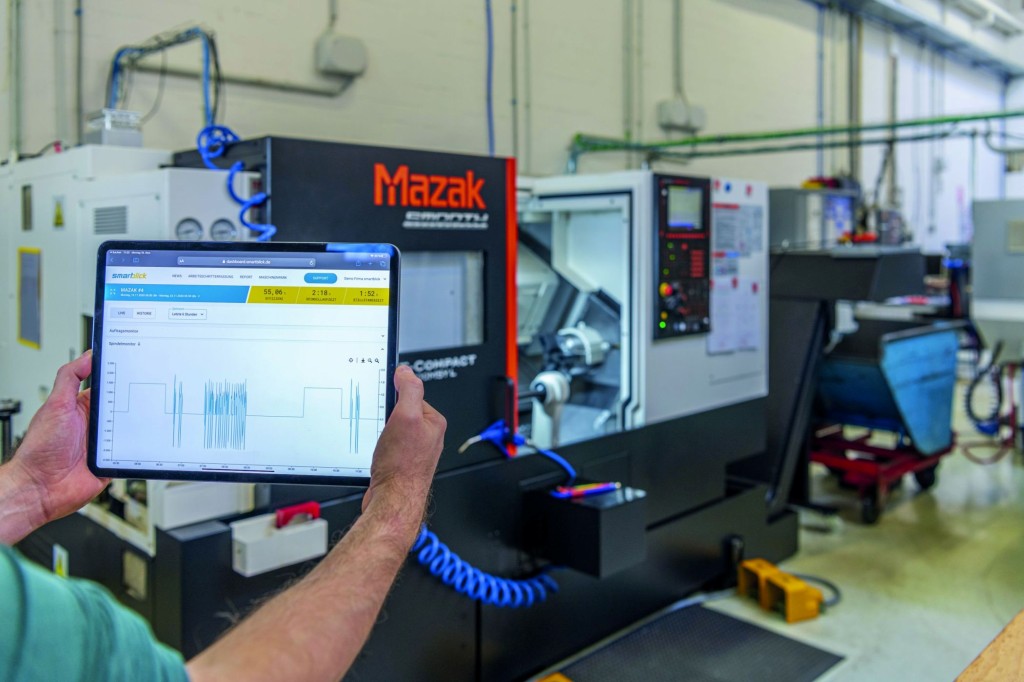
Minimaler Installationsaufwand, maximale Effizienz: Die Auslastung im CNC-Maschinenpark lässt sich per Web-Interface auf beliebigen Endgeräten (Smartphone, Tablet, PC) übertragen und in Echtzeit verfolgen.
Foto: smartblick
Fokus auf alle Werkstoffe und Bearbeitungstechnologien
Wie viele Dreh-, Fräs- und Universalmaschinen oder CNC-Bearbeitungszentren in Deutschland aktuell im Einsatz sind, lässt sich kaum beziffern. Für Zerspaner ist die Bearbeitung des Werkstoffs „Metall“ heute zwar das wichtigste Betätigungsfeld. Jedoch liegt der CNC-Technologie das Funktionsprinzip der Drehbank zugrunde, das ursprünglich auf die Verarbeitung von Holz abzielte. Zum Beispiel werden auch viele Möbelteile sowie Fenster- oder Türrahmen mit CNC-Maschinen angefertigt, und sogar in der Produktion von Musikinstrumenten erfreut sich das Verfahren zunehmender Beliebtheit.
Das dritte wichtige Aufgabengebiet der CNC-Bearbeitung ist inzwischen der Kunststoffsektor. Einzelteile für den Bau komplexer Architekturmodelle, filigrane Zahnräder für die Prototypenherstellung kleiner Getriebe oder CNC-gedrehte Teile für medizinische Geräte werden regelmäßig aus Materialien wie Polyethylen (PE), Polyamid (PA), Polyvinylchlorid (PVC) oder Polypropylen (PP) angefertigt und bilden gerade in der Lohnfertigung die Existenzgrundlage vieler kleiner und mittelständischer Betriebe.
Freie Kapazitäten rasch erkennen – und sofort nutzen
Welche Art von Material auf einer CNC-Maschine konkret bearbeitet wird, spielt für die Nutzung der smartblick-Technologie keine Rolle. Das Softwaretool richtet sich ausschließlich am Betriebszustand der jeweiligen Maschine aus.
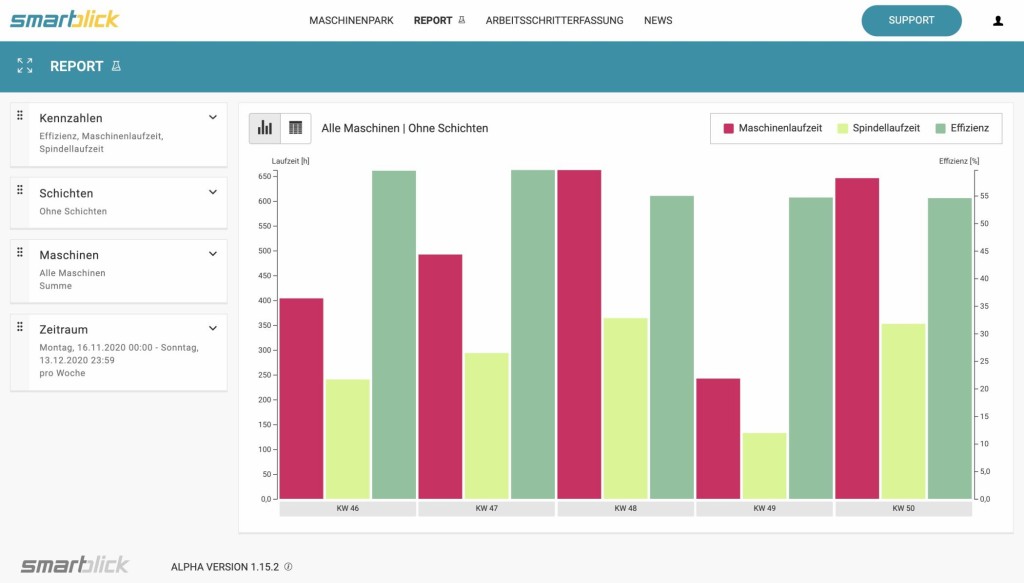
Per Dashboard kann die Effizienz einzelner Schichten im Nachhinein exakt nachvollzogen und für die Zukunft optimiert werden. Grafik: smartblick
Der Zustand aller Maschinen einer Fertigungsstätte lässt sich in Echtzeit abbilden und ist auch mit CNC-Systemen älterer Bauart kompatibel. Statt die Auslastung nur anhand von Erfahrungswerten und Maschinenspezifikationen zu planen, erlaubt smartblick den dynamischen Einsatz aller verfügbaren Ressourcen. Freie „Slots“ auf den Maschinen sind sofort erkennbar und können für weitere Aufträge genutzt werden, die sonst womöglich abgelehnt oder an Dritte vergeben worden wären. In der Retrospektive kann die Effizienz einzelner Schichten exakt nachvollzogen und für die Zukunft optimiert werden, etwa durch gezielte Zuordnung des jeweils am besten geeigneten Bedienpersonals an die einzelnen Maschinen.
„smartblick“ ist eine Marke der F&M Werkzeug- und Maschinenbau GmbH aus Berlin. Die Zerspaner von F&M verfügen über große Erfahrungen im Bereich der CNC-Technik und entwickelten damit ein bahnbrechend einfaches System zur Effizienzsteigerung des CNC-Maschinenparks. Die entstandene Technologie soll jeder Werkzeugmaschine zur Industrie 4.0-Fähigkeit verhelfen. Die Sensorik sorgt dabei für den bestmöglichen Überblick über alle Fertigungsprozesse.
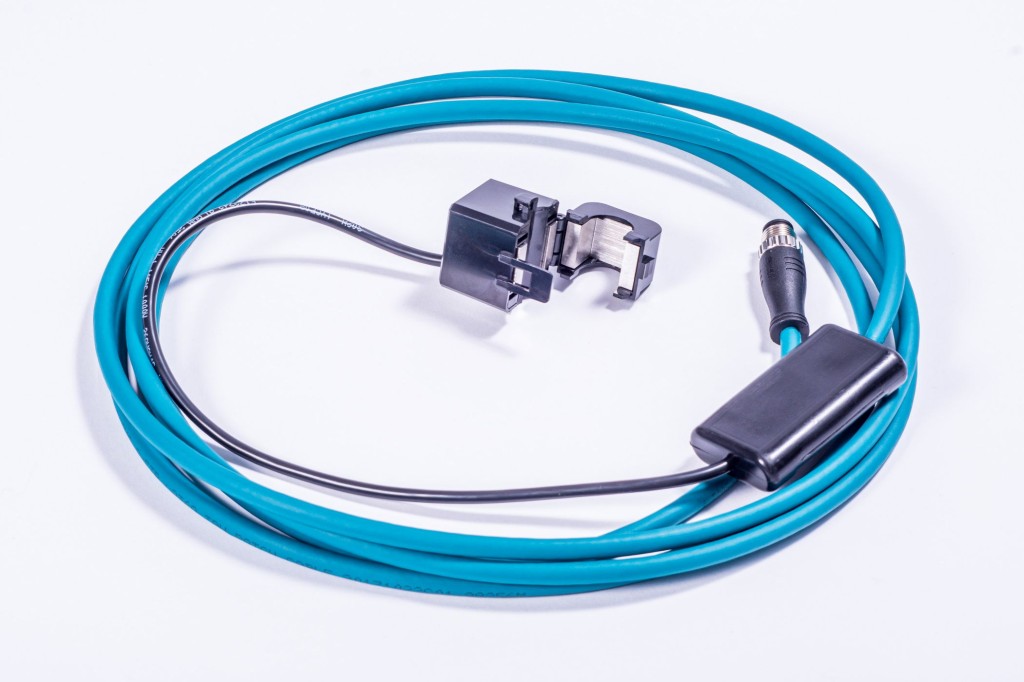
Kontaktlos an der Stromzufuhr der Hauptspindel angebracht, nutzt der Sensor den Hall-Effekt als Messprinzip. Das Magnetfeld des fließenden Stroms liefert alle nötigen Informationen, um den Maschinenzustand kontinuierlich und umfassend abzubilden.
Foto: smartblick
Stillstände entstehen im Betriebsalltag trotz ausgefeilter Planung
Die Investition in eine CNC-Maschine rentiert sich nach einer Faustregel erst dann, wenn die Stillstände – bezogen auf einen Zeitraum von 24 Stunden – einen Anteil von 15 Prozent nicht übersteigen. Davon sind selbst technisch perfekt ausgestattete Betriebe oft immer noch weit entfernt. Selbst mit einer ausgeklügelten Produktions- und Auslastungsplanung lässt sich nicht verhindern, dass Materialflüsse unerwartet ins Stocken geraten. Häufig kommt es auch vor, dass ein Kunde die beauftragten Werkstücke plötzlich viel schneller benötigt als vorgesehen. Mit dem Wissen um den aktuellen Auslastungsstand aller im Maschinenpark verfügbaren Anlagen könnten personal- und kostenintensive Sonderschichten leicht vermieden werden.
Maschinenstillstände in produktive Zeit umzuwandeln, stellt für jeden in der CNC-Bearbeitung tätigen Betrieb folglich eine zentrale Aufgabe dar. Tagsüber werden ungeplante Leerlaufzeiten üblicherweise relativ schnell erkannt, sodass die freien Kapazitäten umgehend anderweitig genutzt werden können. Während der in der CNC-Branche durchaus üblichen Spät- und Nachtschichten hingegen ist normalerweise deutlich weniger Personal im Einsatz; der Überblick und die kurzfristige Nutzung freier Slots gestalten sich dann deutlich schwieriger.
Statt Erfahrungswerten: Entscheidungen wissensbasiert treffen
Insbesondere in der Serienfertigung müssen Maschinen rund um die Uhr laufen. Produktionsleiter orientieren sich bei den Vorgaben – z.B. zur Fertigstellung bestimmter Stückzahlen pro Schicht oder Zeiteinheit – meist an Erfahrungswerten. In der Praxis ist im Detail aber kaum nachzuvollziehen, ob und wo einzelne Spindeln wie lange und warum stillstehen. Aufgrund dessen bleibt die Produktionsplanung vielerorts faktisch hinter den Möglichkeiten zurück.
Dabei stellt das Wissen um Leerlaufzeiten im CNC-Maschinenpark „einen Schatz dar“, den jeder Betrieb ohne größeren Aufwand heben kann. Wann immer sich an einer Maschine freie Kapazitäten ergeben, kann die Gelegenheit, beispielsweise zur Vorproduktion im Rahmen längerfristiger Aufträge, genutzt werden. Liefertermine lassen sich mithilfe vorgefertigter Teile viel längerfristiger absichern als zuvor. Vor allem in der Kleinserienfertigung kann dies zu merklichen Effizienzsteigerungen führen. Je größer der CNC-Maschinenpark ist, desto mehr summieren sich ungenutzte Zeiten zu einem wirtschaftlich relevanten Faktor. Stillstände der Spindeln sollten die Ausnahme sein und allenfalls zu Wartungszwecken auftreten.
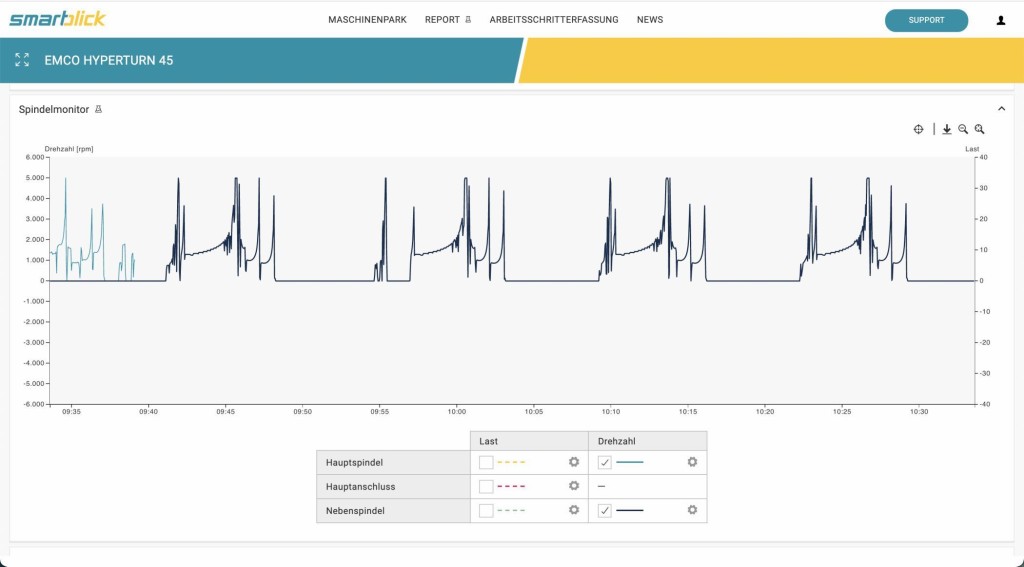
Die Anzahl fertig bearbeiteter Teile, Abweichungen vom Soll oder die aktuelle Werkzeugbelastung: Der Leistungsumfang der smartblick-Software wird kontinuierlich um neue Features ergänzt. Grafik: smartblick
Wie lässt sich der Spindellauf in Echtzeit verfolgen?
Als Datenquelle benötigt smartblick nur die Stromzufuhr der Hauptspindel – anschließend liefert die Lösung auf einfache Weise alle erforderlichen Informationen. Denn dort erfassen die zugehörigen Sensoren kontaktlos – ohne Eingriff in die Maschinensteuerung – die jeweilige Aktivität. Diese kann von der Software auf unterschiedlichste Weise ausgewertet und aufbereitet werden. Ob und wann die Hauptspindel der Maschine steht, mit welcher Drehzahl gerade gearbeitet wird und welche Leistung die Spindel gerade abruft: Stets steht zeitnah das Wissen um den aktuellen Zustand einer CNC-Maschine bereit. Zustandsdaten können nicht nur über längere Zeiträume nachvollzogen, sondern auch in Echtzeit präzise verfolgt werden.
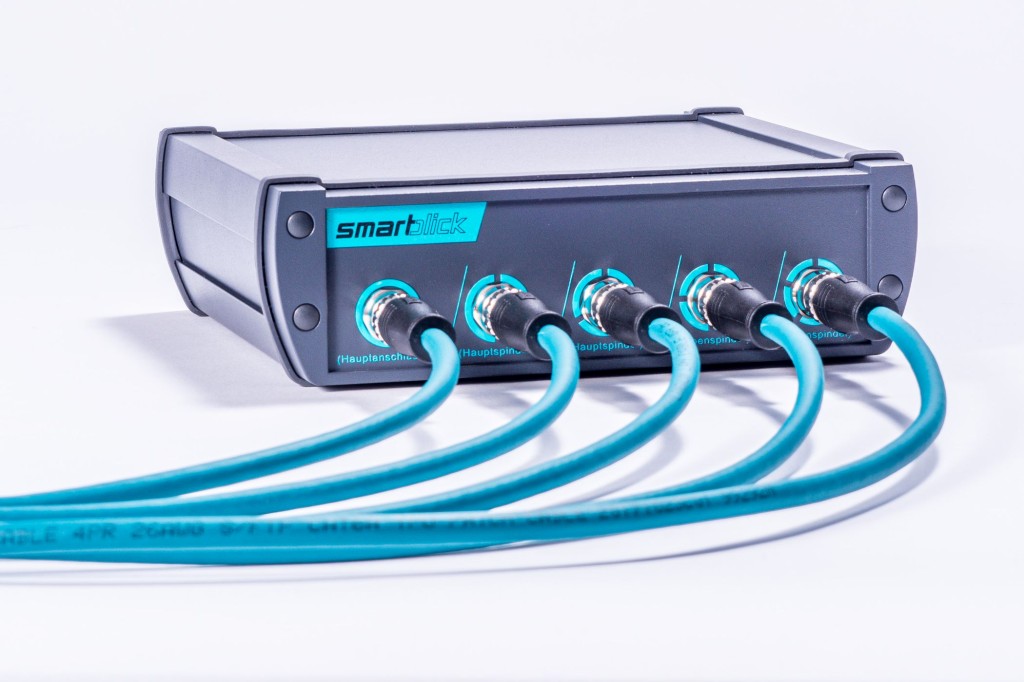
Über die „smartbox“ als Schnittstelle werden Maschinendaten zum Web-Interface übertragen. In wenigen Minuten kann jede CNC-Maschine damit in eine digitale Datenquelle verwandelt werden, unabhängig vom Baujahr oder Hersteller der Anlage.
Foto: smartblick
Per Web-Interface übertragen, lassen sich alle Informationen über beliebige Endgeräte (Smartphone, Tablet, PC) abrufen. Insbesondere bei automatisierten Produktionsabläufen eröffnen sich dadurch neue Möglichkeiten: Wo beispielsweise am Wochenende zur Überwachung der Fertigung bislang noch permanent Maschinenbediener präsent sein müssen, erlaubt smartblick nun flexible Bereitschaftsdienste und das Monitoring aus der Ferne. Von den Vorgaben abweichende Prozessparameter werden sensorgestützt rechtzeitig erkannt und signalisiert. Die permanente Präsenz im Betrieb ist nicht mehr nötig, sodass die Personalkosten reduziert werden können.
Schnelle Installation – ständige Funktionserweiterung
Die Integration der Lösung in einen beliebigen CNC-Maschinenpark dauert pro Anlage durchschnittlich nur 20 Minuten. Das für die Umrüstung nötige Hardware-Paket enthält alle notwendigen Komponenten. Das Installieren ist nach Herstellerangaben rasch mithilfe der beigefügten Anleitung oder mit dem Online-Support möglich. Der Leistungsumfang der Software ist nicht statisch, sondern wird kontinuierlich und den Kundenwünschen entsprechend angepasst und erweitert.
Ein Beispiel für die praktische Anwendung der Maschinendaten ist die Möglichkeit zur Anlage einer auftragsbezogenen Dokumentation. So können einzelne Arbeitsschritte im laufenden Betrieb mit individuellen Kommentaren versehen werden. Nach Abschluss eines Auftrags oder bei der Auswertung bestimmter Zeiträume (etwa bezogen auf die Maschinenleistung im Tages- oder Wochenverlauf) ist dann auf Anhieb nachvollziehbar, ob ein vorübergehender Stillstand wegen eines Werkzeugwechsels notwendig war oder ob die Ursache im Prozessablauf begründet ist. Das könnte zum Beispiel Verzögerungen in der Materialbereitstellung als Ursache haben.
Die Effekte sind spürbar und messbar
Je nach Art und Größe eines CNC-Maschinenparks bewirkt der Einsatz der Softwarelösung, dass sich die Wirtschaftlichkeit um bis zu 20 Prozent verbessern lässt. Ein großer Vorteil für den Anwender ist: Die Kosten für die Nutzung basieren auf einem ausgeklügelten Preismodell. Bei einer monatlichen Abrechnung wird die Bereitstellung der nötigen Sensorik, der Schnittstelle zur Datenübertragung und die Analysesoftware für jeweils eine Maschine mit eingezogen. Damit entfallen für den Nutzer Investitionskosten in Hard- und Software. Berechnet wird nur der tatsächliche „Verbrauch“; die Nutzung verursacht keinerlei Kapitalbindung. Nach Aussage des Anbieters führt dies dazu, dass in den meisten Anwendungsfällen schon in kurzer Zeit ein messbarer wirtschaftlicher Vorteil erzielt wird, der den damit verbundenen Aufwand bei weitem übersteigt.
Das könnte Sie auch interessieren;
Lernfähige Bohrmaschine bietet intelligente Prozessüberwachung
Sensorik und KI optimieren Fertigung von Trägerraketen
Ist die Industrie auf dem Weg zur digitalen Exzellenz?