Diamantschichten nach Maß für hochleistungsfähige Zerspanwerkzeuge
Mit fundiertem Know-how in der Beschichtungstechnologie entwickelt ein renommierter Werkzeughersteller auch extrem harte und verschleißbeständige Diamantschichten. Diese werden zur Zerspanung von Materialien wie CFK, Keramik, Grafit oder Aluminiumlegierungen eingesetzt. Beschrieben wird, auf welche Parameter es beim jeweiligen Einsatzfall ankommt.
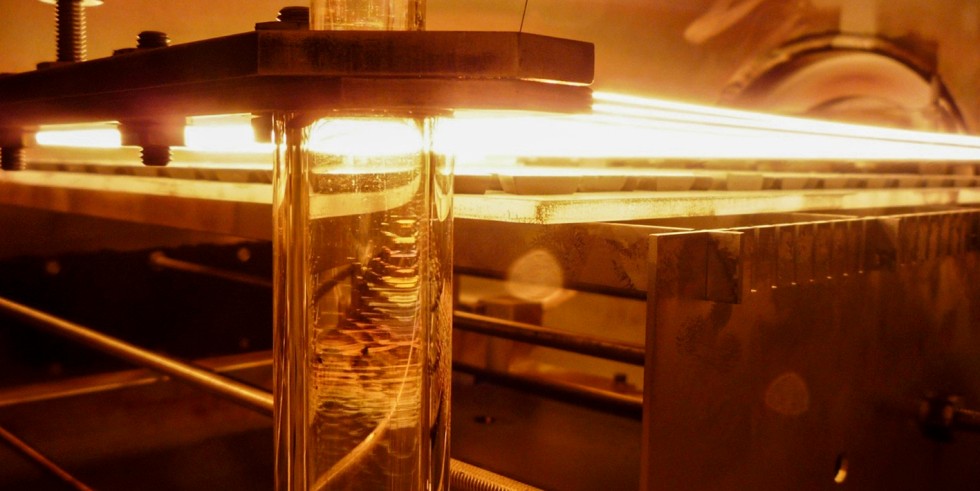
Moderner Beschichtungsprozess: Innenansicht eines Reaktors während des „Hot‐Filament‐CVD“-Verfahrens zur Synthese von Diamantschichten.
Foto: Mapal
Vor allem für Anwendungen in der Automobil- und der Luftfahrtindustrie, im Werkzeug- und Formenbau sowie in der Medizintechnik erreichen die Zerspanungslösungen des Aalener Spezialisten dank der aktuellen Optimierungen höhere Standzeiten und mehr Prozesssicherheit. Der Werkzeugexperte verfügt an seinem Stammsitz im Osten Baden-Württembergs sowie in seinen Kompetenzzentren über bestens geeignete, moderne Beschichtungsanlagen, um Wendeschneidplatten (WSP)- und Vollhartmetall (VHM)-Werkzeuge zu beschichten. Genutzt werden sowohl PVD (Physical Vapour Deposition – physikalische Gasphasenabscheidung) als auch CVD (Chemical Vapour Deposition)-Verfahren.
Was ist bei der Auswahl des Verfahrens zu berücksichtigen?
Die Wahl des passenden Beschichtungsverfahrens richtet sich nach den jeweiligen Anwendungsparametern. Für die Trockenbearbeitung und hohe Schnittgeschwindigkeiten wird in der Regel CVD gewählt, bei instabilen Bearbeitungssituationen oder schwierigen Zerspanungsbedingungen kommen die zäheren PVD-Schichten zum Einsatz.
Kommt es beim Bearbeiten von Werkstoffen vermehrt zu adhäsiven Verschleißvorgängen, ist der Einsatz von diamantähnlichen Kohlenstoffschichten (DLC) sinnvoll. DLC-Schichten werden ebenfalls mit PVD- oder einem plasmaunterstützten CVD-Verfahren abgeschieden. Diese Schichten werden von einer Mischung aus sp2-hybridisierten Kohlenstoffatombindungen (Grafit) und solchen mit sp3-Hybridisierung (Diamant) gebildet. Das Mischungsverhältnis bestimmt dabei die physikalisch-mechanischen Eigenschaften der Schichten. Je mehr sp3-Atombindungen enthalten sind, desto härter ist die Schicht.
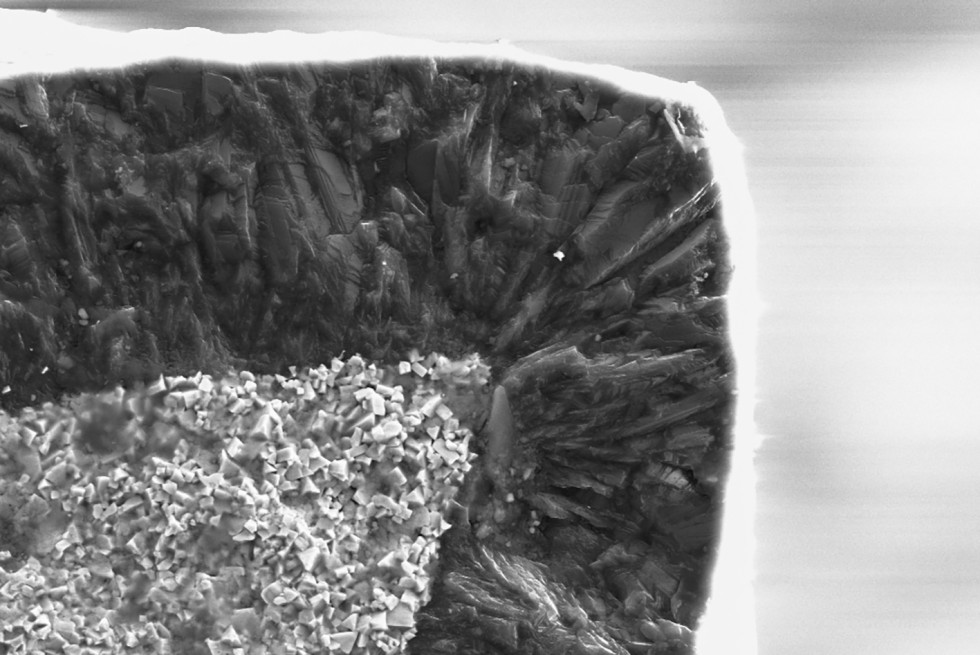
REM (Rasterelektronenmikroskopische)-Aufnahme der Bruchkante eines diamantbeschichteten Vollhartmetallwerkzeugs, Vergrößerung: 3.000-fach.
Foto: Mapal
Neue Beschichtungsvarianten dank CVD-Diamant-Reaktoren
Zum Fräsen oder Bohren stark abrasiver Materialien sind reine Diamantschichten erforderlich. Das in der Mapal-Gruppe eingesetzte Verfahren zur Synthese von Diamantschichten ist eine Abwandlung des rein thermischen CVD und nennt sich „Hot‐Filament‐CVD“ (kurz HF-CVD). Für die Beschichtung von Schaftwerkzeugen sind herkömmliche CVD-Schichten ungeeignet, weil es aufgrund der Werkzeuglängen und der hohen Beschichtungstemperaturen meistens zu einem Längenverzug kommt. Bei HF-CVD erhitzen Drähte aus Refraktärmetallen ein Gemisch aus Wasserstoff und Methan auf Temperaturen bis zu 2.500 Grad Celsius. Dabei bilden sich sehr reaktive Methylradikale, die sich nach und nach auf der bekeimten Hartmetalloberfläche als Diamantschicht abscheiden. Beim Werkzeughersteller stehen dafür eigene CVD-Diamant-Reaktoren zur Verfügung.
„In den vergangenen Jahren haben wir uns intensiv mit der Verbesserung des Diamantbeschichtungsprozesses beschäftigt und uns bei der Herstellung neue Möglichkeiten eröffnet“, berichtet Dr. Martin Kommer, Teamleiter R&D Cutting Material / Coating. Der Werkzeugspezialist habe damit nun die komplette Prozesskette der Auslegung – von der passenden Geometrie über die Auswahl eines geeigneten Hartmetalls bis hin zur Beschichtung – in der eigenen Hand, betont Kommer. Damit können Tools noch gezielter auf die Anforderungen der Kunden hin generiert werden. Die Entwicklungsabteilung in Aalen verfügt darüber hinaus über ein eigenes Zerspanungszentrum mit moderner Maschinentechnik, das neue Werkzeuge unter anderem auf ihre Standzeit und hinsichtlich des Verschleißverhaltens untersucht.
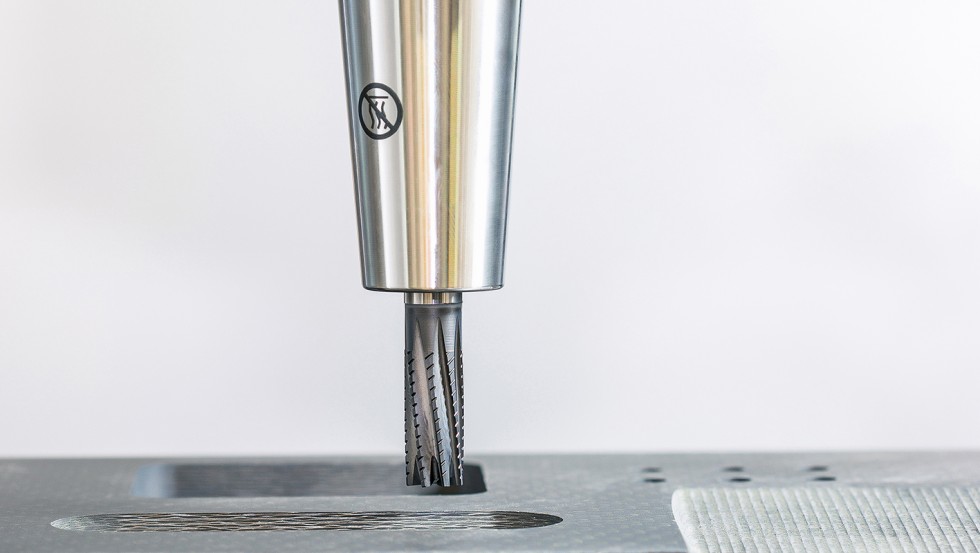
Die homogene CVD-Diamantbeschichtung aus Aalen sorgt für lange Standzeiten und hohe Prozesssicherheit, zum Beispiel beim OptiMill-Composite-Speed-Plus“-Vollhartmetallfräser für CFK-Werkstoffe.
Foto: Mapal
Steuerung des Beschichtungsprozesses
Da der Beschichtungsablauf über eine chemische Reaktion in Kombination mit einer mechanischen Verklemmung „funktioniert“, ist auch eine geeignete Vorbehandlung wichtig. Genutzt wird dazu das definierte Ätzen der Hartmetalloberfläche und eine „Bekeimung“. Weil für diese Behandlung nicht jedes Hartmetall infrage kommt, evaluiert der Werkzeughersteller geeignete Substrate.
Ob bei der Beschichtung feinkörnige mikrokristalline oder nanokristalline Schichten entstehen, wird über die Temperatur, den Druck und den Fluss der jeweiligen Reaktivgase während des Prozesses gesteuert. Theoretisch können per HF-CVD Schichten bis zu einer Dicke von 50 Mikrometern erzeugt werden. Für die Beschichtung seiner Werkzeuge beschränkt sich Mapal derzeit auf den Bereich zwischen 3 und 15 Mikrometern, abhängig der jeweiligen Anwendung.
Der optimierte HF-CVD-Prozess erzeugt Schichten mit nahezu homogener Dicke, was der Werkzeughersteller bei der Entwicklung seines „OptiMill‐Composite‐Speed‐Plus“ genutzt hat. In der jeweiligen Zerspanungsanwendung kann damit die gesamte Schneidenlänge, unabhängig von der Schnitttiefe, prozesssicher genutzt werden. Neben der selbst entwickelten Diamantbeschichtung erlaubt die Erhöhung des Kerndurchmessers bei diesem Tool eine Steigerung der Bruchfestigkeit um 50 Prozent. Das optimierte Nutprofil sorgt für eine schnelle und sichere Abfuhr von Stäuben und Prozesswärme, auch bei großem Zerspanungsvolumen. Der Schneidkeil wurde eigens auf die Anforderungen spröder Werkstoffe optimiert. Die spezielle Verzahnung der Schneiden bewirkt eine Doppelkompression, wodurch Faserüberstände an den Werkstückkanten der Ober- und Unterseite prozesssicher abgetrennt werden. Substrat, Geometrie und Beschichtung wirken ideal zusammen und sorgen für bestmögliche Zerspanungsresultate.
Das könnte Sie auch interessieren:
Wie ein kleiner Fertigungsbetrieb die digitalisierte Produktion „lebt“
Einstellbar-gedämpfte Bohrstange schont Werkstück und Werkzeug