Erfolgsfaktor Recycling: rasche Wiederverwertung von Ausschussteilen
Mitte Juni öffnet in Düsseldorf die GIFA ihre Pforten. Ein Fokusthema der Messe ist, wie die Gießereiindustrie eine höhere Ressourceneffizienz erzielen kann. An Schmelzöfen gelingt dies dank Inline-Rückführung zerkleinerter Gussmaterialien in den Produktionsprozess.
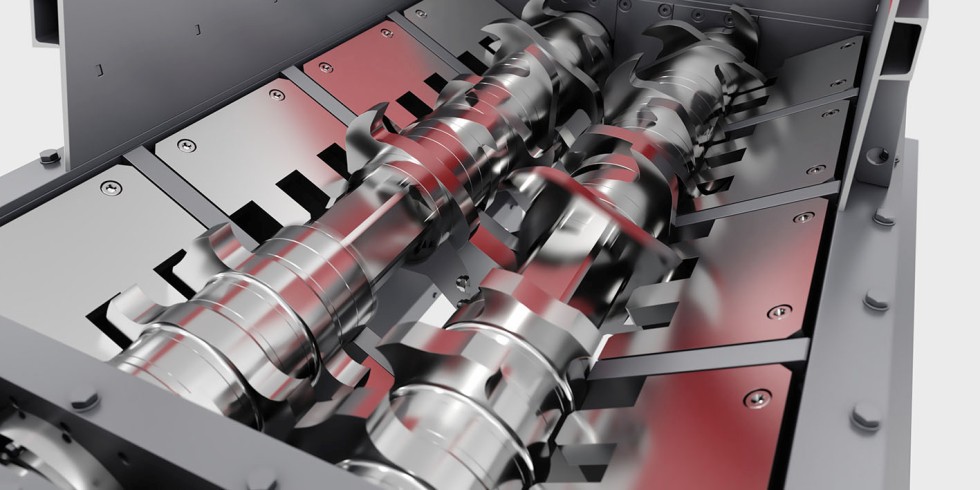
Energieeffizienter Prozess: Mithilfe der einzeln gesteckten Messer aus robustem Spezialstahl lassen sich unterschiedliche Steckfolgen umsetzen, sodass das jeweils anfallende Gussteil- und Spänegemisch optimal zerkleinert wird.
Foto: Erdwich
Europäische Gießereien stehen vor noch nie dagewesenen Herausforderungen: Steigende Rohstoff- und Energiekosten sowie eine erhöhte Nachfrage am Markt bei zugleich verschärften gesetzlichen Auflagen in puncto Nachhaltigkeit sind nur ein Teil der Problematik. Dass trotz hoher Automatisierung und niedriger Fehlertoleranzen im täglichen Betrieb Ausschussprodukte anfallen, lässt sich auch in modernen Produktionen nicht vollständig vermeiden. Umso mehr gewinnt die rohstoffschonende Rückführung der wertvollen Restmaterialien in den Produktionsprozess an Bedeutung.
Fachmessequartett hat Energieeffizienz im Fokus
Vom 12. bis zum 16. Juni 2023 wird Düsseldorf zum Treffpunkt der Gießerei- und Metallurgie-Industrie – und widmet sich auch dem Thema Rohstoff-Rückgewinnung und Ressourceneffizienz: Die Weltleitmessen GIFA, Metec, Thermprocess und Newcast, die alle vier Jahre stattfinden und zusammen das gesamte Spektrum von Gießereitechnik, Gussprodukten, Metallurgie und Thermoprozesstechnik abdecken, sind gerade jetzt bei den energieintensiven Branchen besonders gefragt. Die derzeitigen Herausforderungen befeuern die Digitalisierung in der Metalltechnik und ihre Suche nach nachhaltigen und zukunftsweisenden Lösungen.
Über 2000 Aussteller aus über 50 Ländern greifen globale Trends auf und zeigen in zwölf Messehallen die gesamte Bandbreite an aktuellen Technologien und Produkten. Die Hot Topics der „Bright World of Metals“ lauten folgerichtig: Dekarbonisierung der metallurgischen Industrie, „ecoMetals“, Kreislaufwirtschaft, Digitalisierung, additive Fertigungsverfahren sowie E-Mobilität und automobiler Leichtbau.
Was geschieht mit Ausschussteilen?
Da die Gussteile und anfallende Späne aus der Oberflächenbearbeitung von Strukturbauteilen oftmals sperrig und unhandlich sind, müssen sie zunächst zerkleinert werden. Bisher wurden sie unbehandelt in großen Containern gesammelt, was den Intralogistikprozess negativ beeinflusst. Für Abhilfe sorgt nun beispielsweise der vollautomatisierte Zweiwellen-Reißer „RM1350/2“, der auf der GIFA in Düsseldorf vorgestellt wird. Er lässt sich direkt in Druckgießzellen integrieren und schließt dort anfallende Druckguss-Bauteile aus Aluminium oder Magnesium zuverlässig auf. Die vorzerkleinerten Gussteile lassen sich in einem energieeffizienten Schmelzvorgang wiederverwerten.
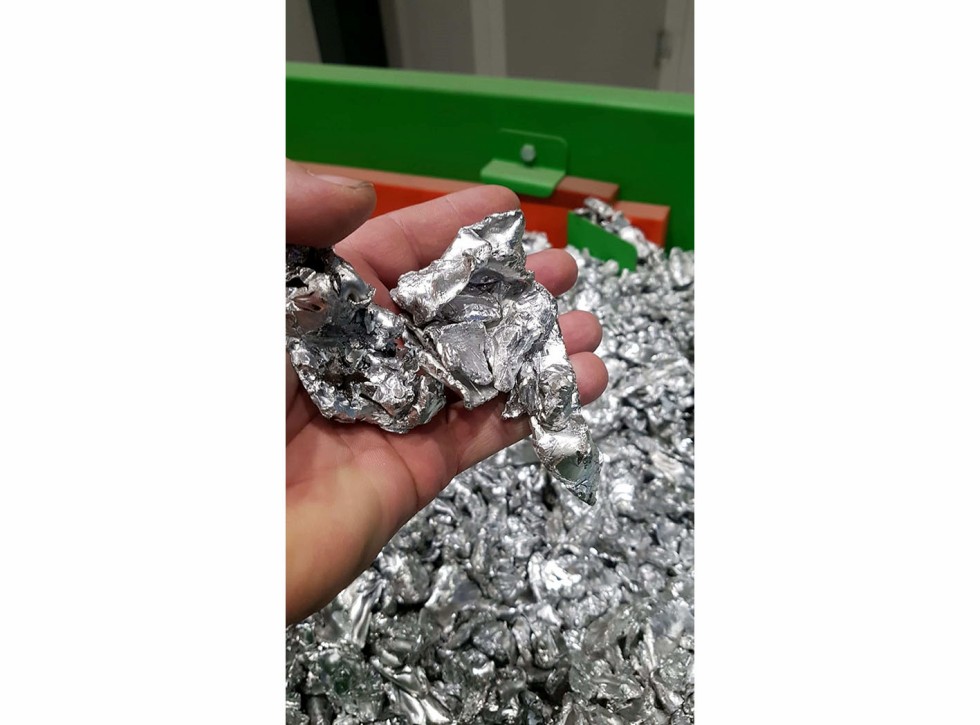
Output-Material: Die effiziente Zerkleinerung von immer größer werdenden Aluminiumstrukturbauteilen gilt als neue Herausforderung in der Automobilbranche.
Foto: Erdwich
„Fehlangüsse von Getriebegehäusen oder ganzen Motorblöcken, aber auch von kompletten Heckdeckeln in Form von sogenannten Angussspinnen – sowie von Batteriegehäusen für Elektroautos – lassen sich selbst in den produktionsoptimiertesten Betrieben nicht vermeiden“, weiß Maximilian Gutmayr, Vertriebsleiter beim Anbieter Erdwich. „Hinzu kommen auch kleinere Gussreste oder Stanzabfälle, in denen vor allem bei Aluminiumgießereien wertvolle Rohstoffe stecken.“
Integration in den laufenden Prozess
Ressourcenknappheit, teure Einkaufspreise und der steigende Bedarf an Aluminium im Bereich der Elektrifizierung von Fahrzeugen sorgen dafür, dass Recycling einen immer höheren Stellenwert einnimmt. Die Menge an Ausschussprodukten, die zur Wiederverwertung aufbereitet werden soll, wächst permanent, ebenso die Teilegröße. Dies wirft aber auch logistische Probleme auf. Die effiziente Zerkleinerung gilt – aufgrund sich ändernder Karosseriekonzepte und Antriebsstränge – als neue Herausforderung in der Automobilbranche.
Bisher wurden die Fehlangüsse und Restmaterialien, darunter Motorblöcke, Getriebe- und Kupplungsgehäuse, Federbeinaufnahmen sowie Bauteile von Schwellern, gesammelt und wieder eingeschmolzen. Diese Vorgehensweise ist zeitaufwendig und die Zwischenlagerung der oftmals großen und sperrigen Teile nimmt viel Platz in Anspruch. Mit dem Grobzerkleinerer RM1350/2, der sich auch nachträglich in bestehende Druckgießzellen einbinden lässt, gibt es nun eine effektive Lösung. Neben der Integration der Reißermaschine in den laufenden Prozess kann der Zerkleinerer auch als Stand-Alone-Variante im Innen- wie Außenbereich der Gießerei platziert werden.
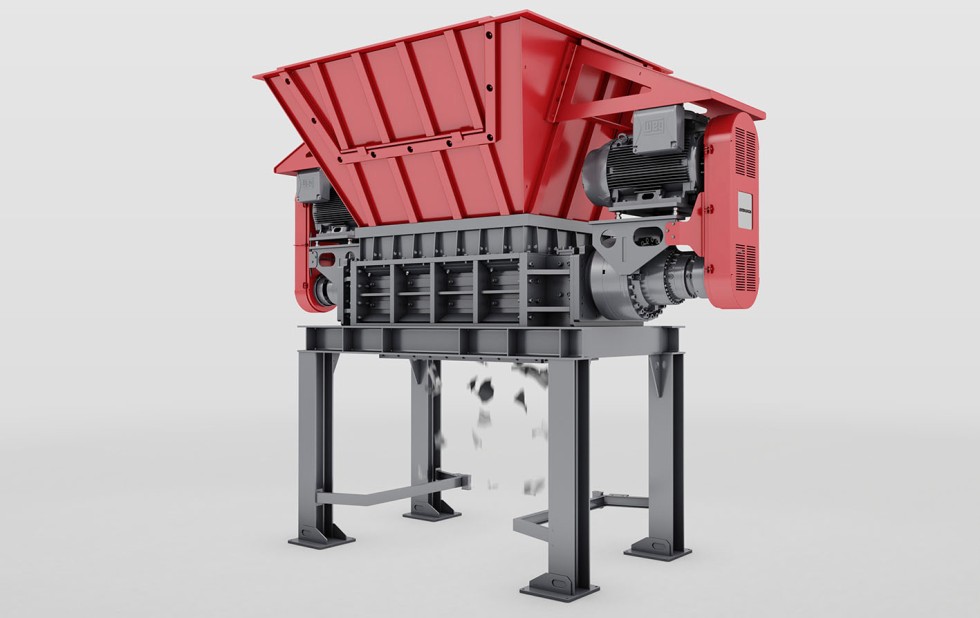
Der Zweiwellen-Reißer ist eine Lösung, um die wertvollen Reststoffe unmittelbar vor Ort zu zerkleinern, platzsparend zu lagern und schnellstmöglich zurück in den Produktionsprozess zu führen.
Foto: Erdwich
Energie- und kosteneffizienter Recyclingkreislauf
Das Schneidwerk des Zweiwellen-Reißers kann in seiner Länge zwischen 1.500, 2.000 und 2.500 Millimetern ebenso passgenau auf die Input-Materialien ausgelegt werden, wie die elektromechanische Antriebsleistung von 45 bis 132 Kilowatt (inklusive Frequenzumrichter zur individuellen Festlegung der Wellendrehzahlen). Je nach zugeführtem Stoffstrom und geforderter Endgröße ist dabei ein Durchsatz von 1,5 bis 5 t/h, möglich. Mithilfe der einzeln gesteckten Messer aus robustem Spezialstahl lassen sich individuelle enge wie auch weite Steckfolgen umsetzen, sodass ein optimales Zerkleinerungsergebnis für den nachfolgenden Prozess erreicht wird. Damit es auch bei Gussmaterialien mit besonderer Geometrie und spezieller Materialmix-Zusammensetzung nicht zu Stillstandzeiten an der Gesamtanlage kommt, ist der vollautomatische Zweiwellen-Reißer mit einer eigens entwickelten SPS inklusive Reversier- und Abschaltautomatik ausgestattet. Zusätzlich lassen sich die beiden Wellen mittels mehrerer hinterlegter Programme in der Steuerung des Zerkleinerers unabhängig voneinander vor- und rückwärts fahren, um den Durchsatz und das Handling auch bei unhandlichen Gussteilen nochmals zu erhöhen.
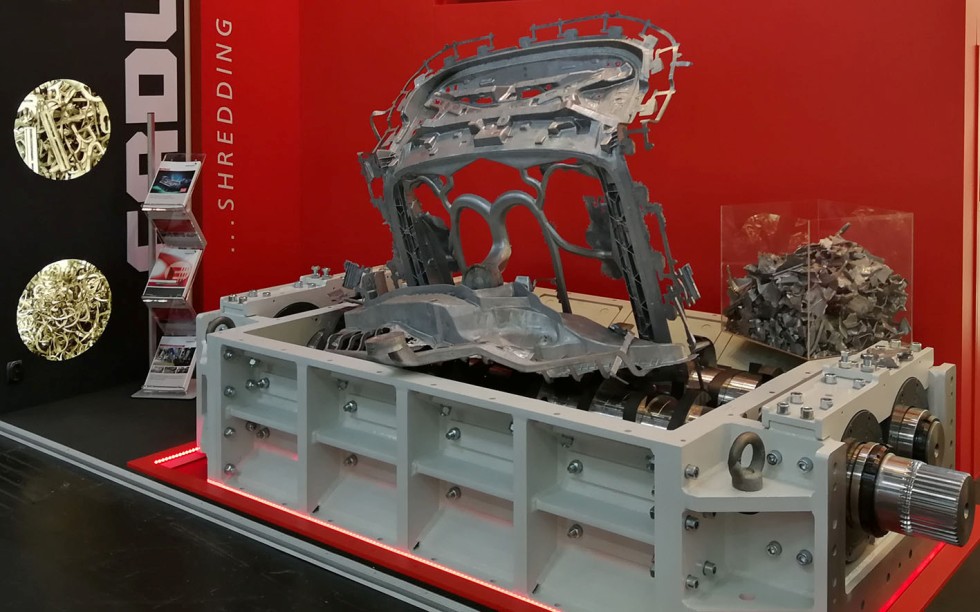
Die Menge an Ausschussprodukten, die wiederaufbereitet werden sollen, wächst permanent. Außerdem werden die Komponenten immer größer und bestehen aus teilweise zusammenhängenden Strukturbauteilen.
Foto: Erdwich
„Der RM1350/2 wird unmittelbar in die Produktionslinie integriert und zerkleinert alle Ausschussmaterialien direkt dort, wo sie anfallen“, erklärt Gutmayr. „Anschließend können die nun handlichen Aluminiumteile entweder über Förderbänder ohne Umwege zurück zu den Ofenanlagen transportiert oder platzsparend gesammelt werden.“ Letzteres ist möglich, da der Grobzerkleinerer das Volumen der Reststoffe um 50 bis 60 Prozent verringert. Zudem reduziert dieser Zerkleinerungsschritt den Energieaufwand beim Wiedereinschmelzen, da die Öfen optimal auf die Materialmasse eingestellt werden können. Dadurch verbessert sich das Abbrandverhalten, was zu weniger Materialverlusten im Ofen führt. Die Wiederaufbereitung der Schrottteile wird so zum ersten Recyclingschritt in einem energie- und kostensparenden Fertigungskreislauf. Auf der GIFA ist die Technologie des Zweiwellen-Reißers RM1350/2 in Form eines Modells gemeinsam mit weiteren Zerkleinerern für das Gussteile-Handling und die Späne-Zerkleinerung zu sehen(Halle 16 / Stand E25).
Überzeugende Fertigungstiefe
Die inhabergeführte Erdwich Zerkleinerungs-Systeme GmbH wurde 1972 als Maschinen- und Metallbaubetrieb von Johann Erdwich senior gegründet und hat ihren Sitz im bayerischen Igling. Der Schwerpunkt des hochspezialisierten Engineering- und Produktionsunternehmens liegt auf der Entwicklung und Herstellung von Anlagen im Bereich Recycling- und Schreddertechnologie. Die Zerkleinerer, Ripper, Hammermühlen und schlüsselfertigen Anlagen lassen sich entweder als eigenständige Maschinen installieren oder in bestehende Zerkleinerungs- und Recyclinganlagen integrieren und sorgen für den effizienten Materialaufschluss. Durch die hohe Fertigungstiefe sowie das hauseigene Technikum ist der Betrieb außerdem in der Lage, alle wesentlichen Fertigungsprozesse – von der Zerspanung über den Maschinenbau bis hin zu anlagenspezifischen Maschinenkomponenten – betriebsintern durchzuführen. Das Unternehmen ist nach ISO 9001 und 14001 zertifiziert.
Das könnte Sie auch interessieren:
Technologien der Batteriefertigung gemeinsam optimieren
Zulieferteile: Präzision aus Aluminium oder Messing
Schnell und einfach: Produktionsprozesse mit Industrierobotern
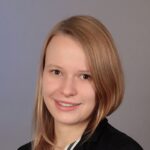
Sandra Walz ist freie Redakteurin aus München. Foto: Autorin