Fertigung von Hybridbauteilen – additiv und robotergestützt
3D-Druck bietet vielfältige Möglichkeiten – trotzdem ist er in der industriellen Anwendung in seiner bisherigen Form nur eingeschränkt anzutreffen. Multiaxiale Lösungen und insbesondere der Materialauftrag auf beliebige Freiformflächen versprechen neue Anwendungsgebiete.
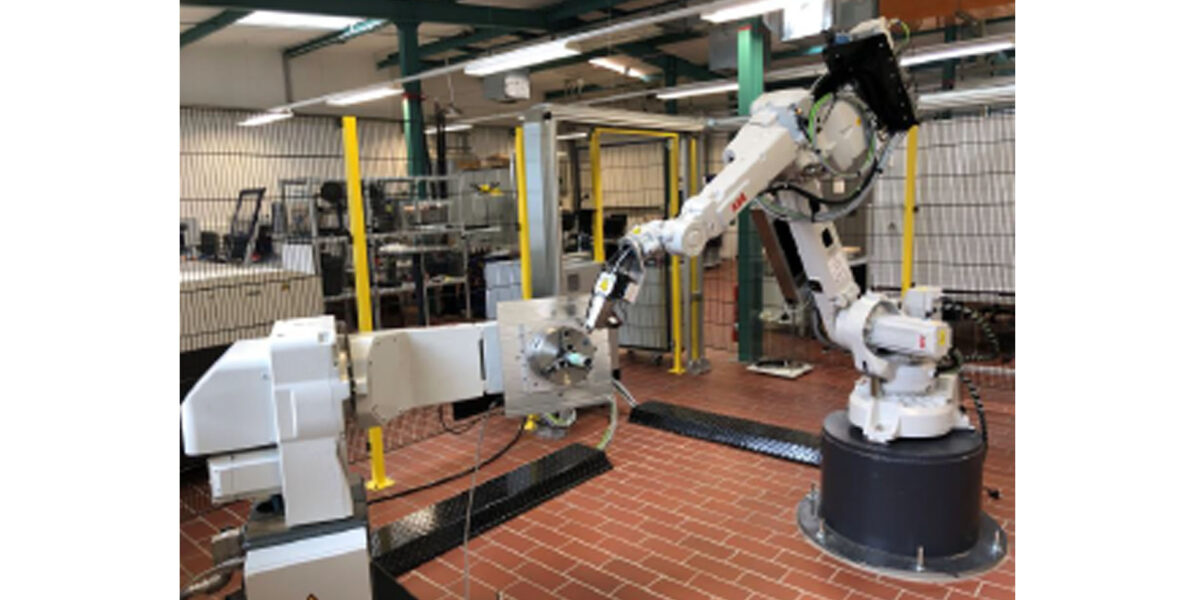
Versuchsanordnung mitsamt Industrieroboter zur Fertigung von Hybridbauteilen mit komplexer Geometrie im Prüflabor.
Foto: FH Südwestfalen
Um zusätzlich die Vorzüge verschiedener Fertigungsverfahren und Materialien sinnvoll zu kombinieren, wird an der Fachhochschule Südwestfalen (FH-SWF) ein Fertigungsprozess zur Herstellung individualisierter Hybridbauteile sowie eine zugehörige digitale Prozesskette entwickelt. Das Forschungsvorhaben wird vom Ministerium für Kultur und Wissenschaft des Landes Nordrhein-Westfalen gefördert.
Multiaxialer additiver Prozess ist besonders anspruchsvoll
Im Rahmen des Projekts wird ein polymerbasierter Materialextrusionsprozess (MEX) gezielt eingesetzt, um Verbindungsknoten additiv und robotergestützt auf vorgeformte Aluminiumprofile aufzubringen. Hierdurch kann ein großvolumiger und dabei individualisierter Gesamtverbund, wie beispielsweise ein auf spezifische Anforderungen optimierter Fahrradrahmen hergestellt werden. Besondere Herausforderungen liegen jedoch in der Bahnplanung und Simulation des multiaxialen additiven Fertigungsprozesses, welcher gegenüber klassischem 3D-Druck eine deutlich höhere Komplexität aufweist. Dem entgegen stehen eine gesteigerte Produktivität sowie besondere Möglichkeiten, wie dem flexiblen Auftrag auf Freiformflächen und um Störkonturen herum.
Ausgehend von einem regelbasierten Konstruktions- und Optimierungsprozess, an dessen Ende eine individualisierte Multi-Material-Geometrie ausgegeben wird, ist der additive Fügeprozess zu planen (Slicing) und ein maschinenspezifischer Programmcode zu generieren. Hierbei ist die Kinematik einer Roboterzelle – bestehend aus einem 6-Achs-Knickarmroboter und einem 2-Achs-Positionierer – zu berücksichtigen, die zur Evaluierung zur Verfügung steht. Zur Bereitstellung der benötigten CAM-Funktionen wurden verschiedene Softwarelösungen auf ihre Grenzen hin untersucht, um eine vollständige CAD/CAM-Kette, wie in Abbildung 1 gezeigt, zusammenstellen zu können. In diesem Beitrag werden die Möglichkeiten und Grenzen aktueller Softwaretools zur Planung dieses multiaxialen additiven Fertigungsschrittes betrachtet.
Stand der Technik zur multiaxialen Materialextrusion
Um die im Projekt beabsichtigen Verbindungsknoten additiv fertigen zu können, sind diese in einer geeigneten Art und Weise in Schichten zu unterteilen, deren sukzessiver Aufbau nach und nach die Zielgeometrie erzeugt. Dieses Aufteilen wird im Allgemeinen als „Slicing“ bezeichnet und erfolgt heutzutage hauptsächlich in 2½ Dimensionen. Zwar werden 3D-Objekte aufgebaut, jedoch werden lediglich zwei Achsen simultan und eine dritte zur Zustellung verwendet. Dieses Vorgehen ist beispielsweise auch beim Fräsen als sogenannte 2½D-Strategie bekannt. Ausgehend von einer planaren Ausgangsfläche wird dazu entlang einer fixen Baurichtung planar geslict und anschließend Material aufgetragen.
Aufgrund des Umstands, dass im Forschungsvorhaben auf Freiformflächen Material appliziert werden soll, ist eine 2½D-Strategie jedoch nicht zielführend. Daher sind komplexere Strategien erforderlich, die heutzutage Gegenstand der Forschung sind. Neben der Einschränkung, nur auf planare Flächen Material auftragen zu können, hat die klassische additive Fertigung in 2½D-Strategie weitere Nachteile. Hierzu zählen die Entstehung des Treppenstufen-Effekts, Eigenschafts-Anisotropien sowie die Notwendigkeit aufzutragender und zu entfernenden Stützstrukturen. Dabei kann die durch einen multiaxialen Materialauftrag eingesparte Fertigungsdauer 75% und mehr betragen [1; 2).
Bisherige Ansätze aus der Literatur und ihre Defizite
Um die Vorteile des multiaxialen Materialauftrags zu untersuchen, greift daher eine Vielzahl an Forscherteams auf anwendungsspezifische Programmierung zurück [3–5]. Entweder entstammen die Daten zur Maschinensteuerung eigens entwickelten Skripten oder die Maschinenbewegungen werden händisch geteacht. Jedoch befassen sich auch einige Projekte mit der Entwicklung von Algorithmen zur Fertigung beliebiger Geometrien. Unter diesen stellt die einfachste Version eines multiaxialen Materialauftrags die Unterteilung der Ausgangsgeometrie in Teilbereiche dar, sodass diese jeweils ohne Stützstrukturen gefertigt werden können. Entwickelte Strategien, wie die von Wu et al. [6] oder von Wulle et al. [2] basieren jedoch nur auf einem 2½D-Materialauftrag. Ansätze mit 3D-Materialauftrag, wie sie beispielsweise von Coupek et al. [1], Li et al. [7] oder auch Etienne et al. [8] verfolgt werden, lassen sich jedoch auch nicht problemlos auf die Fertigung komplexer belastungsoptimierter Verbindungsknoten übertragen. Die entwickelten Algorithmen führen zu einer erhöhten Kollisionsgefahr. Sie verwenden teilweise nur eine geringe Anzahl an Achsen und sind darüber hinaus (noch) nicht für den industriellen Einsatz geeignet. Jedoch erscheint insbesondere der von Etienne gewählte Ansatz, die Depositionshöhe lokal zu variieren, um geschwungene Layer und somit einen stetigen Übergang zwischen äußeren Oberflächen zu erhalten als sehr interessant. Ein solches Verfahren – wenn es um zusätzliche Freiheiten, wie beliebige Düsenausrichtungen ergänzt und aktuell vorhandene Schwachstellen behoben werden – kann sicherlich dazu genutzt werden, die Eigenschaften additiv gefertigter Bauteile deutlich zu verbessern.
Da auch kommerzielle CAM-Anbieter schon ihre eigenen Ansätze multiaxialer Strategien und Strategien zum Materialauftrag auf Freiformflächen in ihre Softwarelösungen implementiert haben, wurden diese im Forschungsprojekt anhand mehrerer Beispielgeometrien detailliert auf ihre Möglichkeiten hin untersucht. Aus der Vielzahl der Anbieter wurden vier vielversprechende Lösungen (SprutCAM, Siemens NX, ExaptSolid und AdaOne) identifiziert und ausgiebig getestet.
Vorgehen und Ergebnisse der Softwareauswahl
Zur Evaluierung grundlegender Funktionen wurden zunächst zwei allgemeine Geometrien untersucht. Eine Platte mit geschwungener Oberfläche, wie sie in Abbildung 2 dargestellt ist, dient der Überprüfung hinsichtlich eines lokal variablen Materialauftrags, sodass ein fließender Übergang zwischen Ausgangs- und Deckfläche (sogenanntes Morphing) erfolgen kann. Hierdurch wird mithilfe eines stetigen Übergangs des Layeraufbaus versucht, die Anisotropie der Eigenschaften zu verringern.
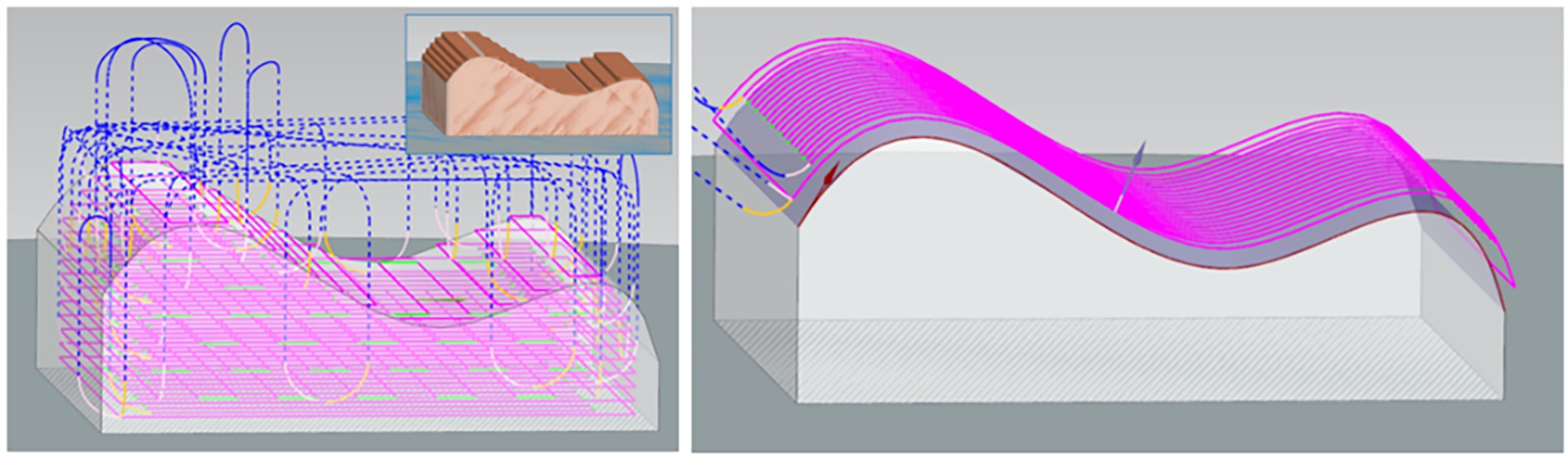
Bild 2. Als Beispielgeometrie dient im Bild eine Platte mit geschwungener Oberfläche. Grafik: FH Südwestfalen
Als zweite allgemeine Geometrie wurde der Bogen aus Abbildung 3 untersucht, welcher der Überprüfung multiaxialer Bahnplanung dient. Mithilfe des Bogens wurde getestet, ob Slicing-Algorithmen zur Herstellung einer Struktur entlang einer Basiskurve zur Verfügung stehen. Durch den Einsatz eines mehrachsigen Vorgehens wird beabsichtigt, den Treppenstufen-Effekt zu eliminieren und die Anisotropie zu verringern. Außerdem wird die Fertigbarkeit von ausgeprägten Überhängen möglich.
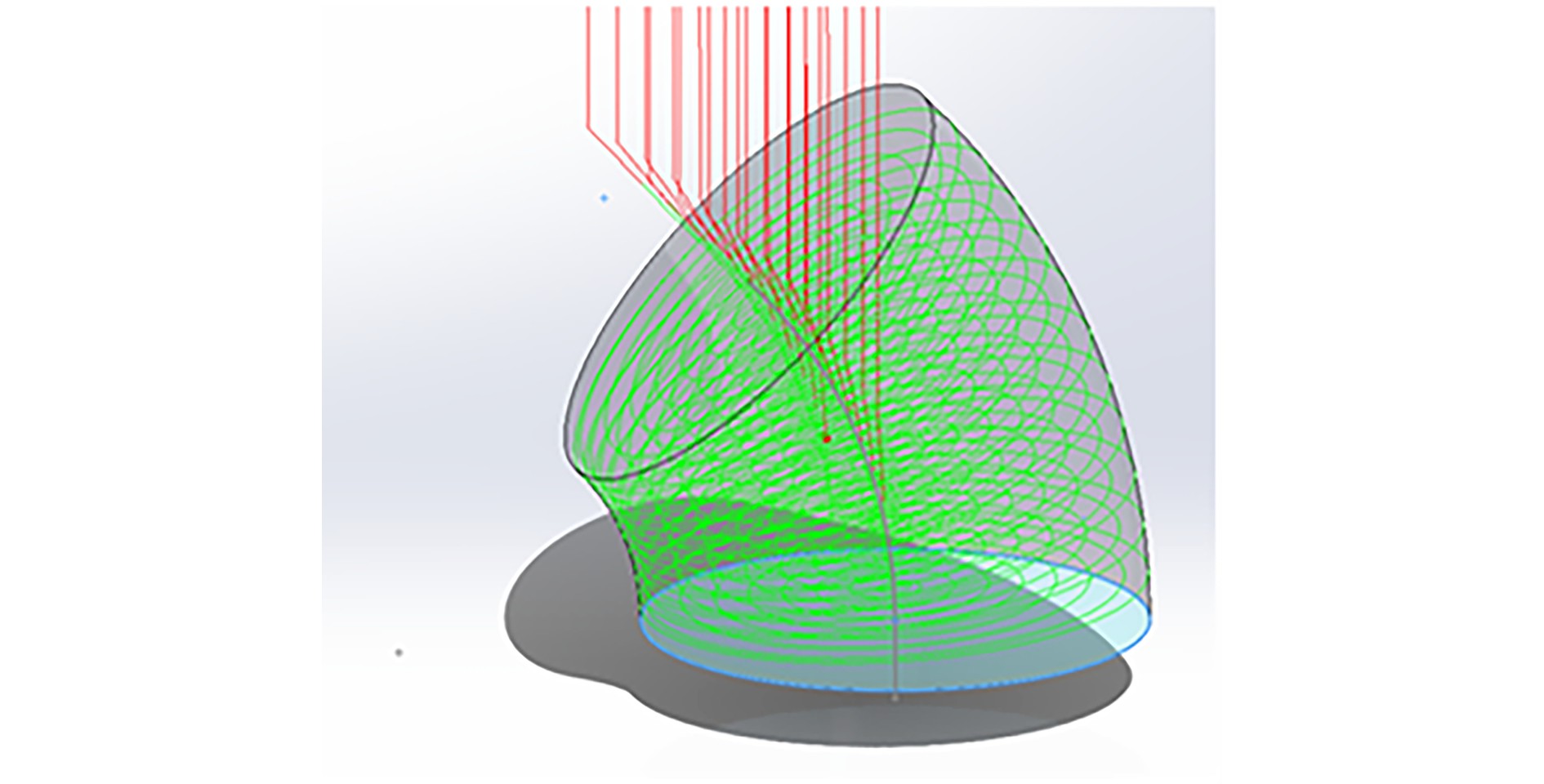
Bild 3. Die Mustergeometrie „Bogen“ ist mit den zur Verfügung stehenden Algorithmen planbar. Grafik: FH Südwestfalen
Um anschließend die Einsatzfähigkeit für das Forschungsvorhaben evaluieren zu können, wurden zwei Ausführungen eines T-Stoßes untersucht, welche in Abbildung 4 und Abbildung 5 dargestellt sind. Diese stellen einen vereinfachten Sattelknoten ohne Anbindung eines Hinterbaus dar, wobei einer davon aus einfachen Grundkörpern zusammengesetzt und ein zweiter bereits Topologie-optimiert ausgeführt ist.
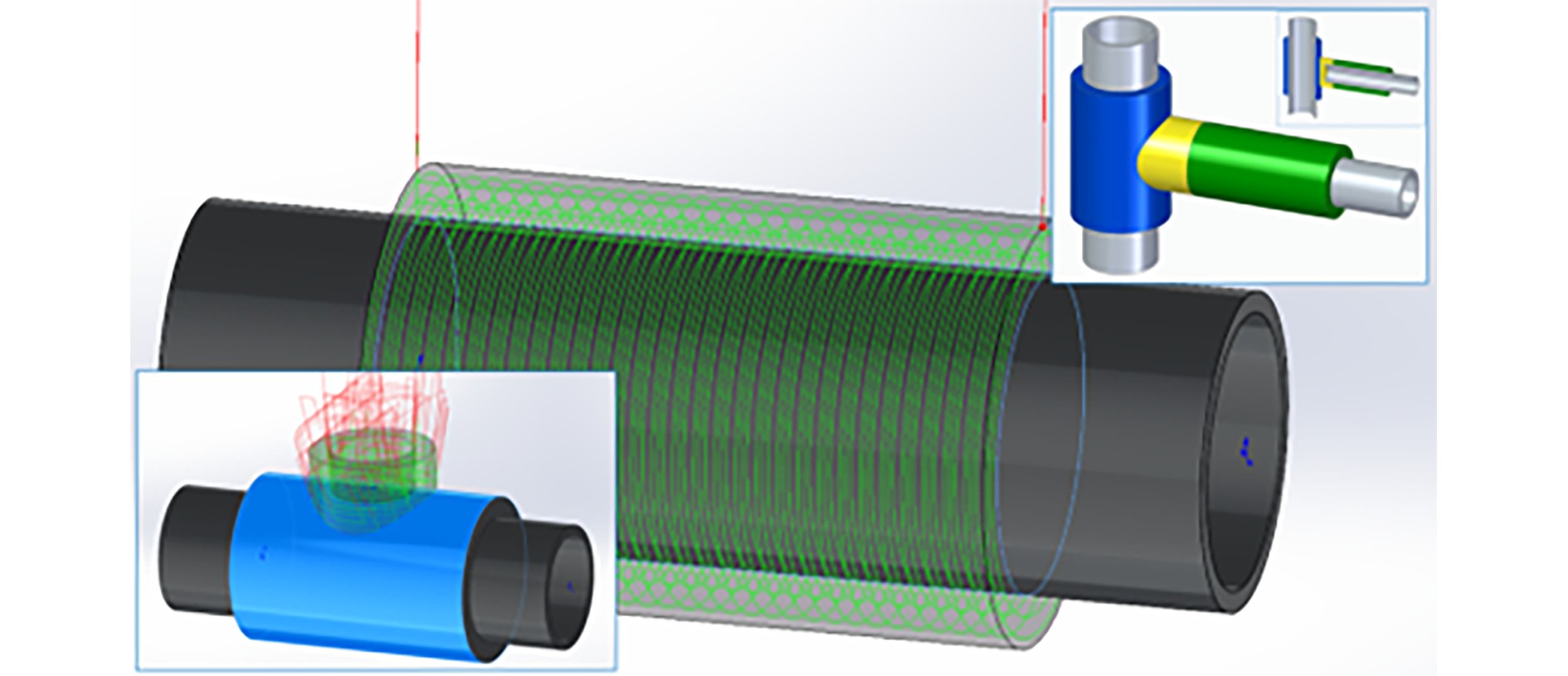
Bild 4. Der Verbindungsknoten (ohne Topologie-Optimierung) ist zum Teil bereits planbar. Grafik: FH Südwestfalen
Mit der Planung dieser Verbindungen wurde überprüft, ob die benötigten Slicing-Algorithmen und eine Simulation einschließlich Kollisionserkennung verfügbar sind. Darüber hinaus konnte ermittelt werden, ob und wie eine Geometrie, die aus mehreren Elementen besteht, mit der jeweiligen Software verarbeitet werden kann.
Resultate sind noch nicht zufriedenstellend
Die Untersuchung ergab, dass keines der getesteten Programme für die zuvor beschriebene Fertigungsweise der Platte mit geschwungener Oberfläche geeignet ist (siehe Abbildung 2). Keines der Tools konnte beim Slicing einen variablen Materialfluss berücksichtigen, sodass Morphing nutzbar wird. Es ist zwar durchaus möglich, eine 2½D-Basis zu planen und diese mit einer geschwungenen 3D-Oberfläche zu versehen, jedoch ist hierdurch kein stetiger Verlauf gegeben. Außerdem wird davon ausgegangen, dass ein 3D-Materialauftrag auf der gestuften Basis ein unsauberes Druckergebnis mit Fehlstellen und hoher Kollisionsgefahr hervorrufen wird. Somit herrscht in diesem Bereich großes Optimierungspotenzial, um die Fertigbarkeit von komplexen Bauteilen mit optimalen Eigenschaften sicherzustellen.
Die Evaluierung anhand des Bogens (Abbildung 3) ergab jedoch, dass die Idee eines lokal variablen Materialauftrags teilweise bereits implementiert ist. Körper, deren Querschnitt entlang einer Kurve verlaufen, sind mit den zur Verfügung stehenden Algorithmen aktuell schon planbar.
Ebenfalls konnte der Sattelknoten ohne Topologie-Optimierung (Abbildung 4) von mehreren Programmen erfolgreich geplant werden. Schwierigkeiten traten lediglich bei der Planung des Ansatzes zur Anbindung des zweiten Rohres auf. Lediglich bei einem der getesteten Tools war die Planung nicht erfolgreich, da Begrenzungsgeometrien nicht hinreichend berücksichtigt wurden.
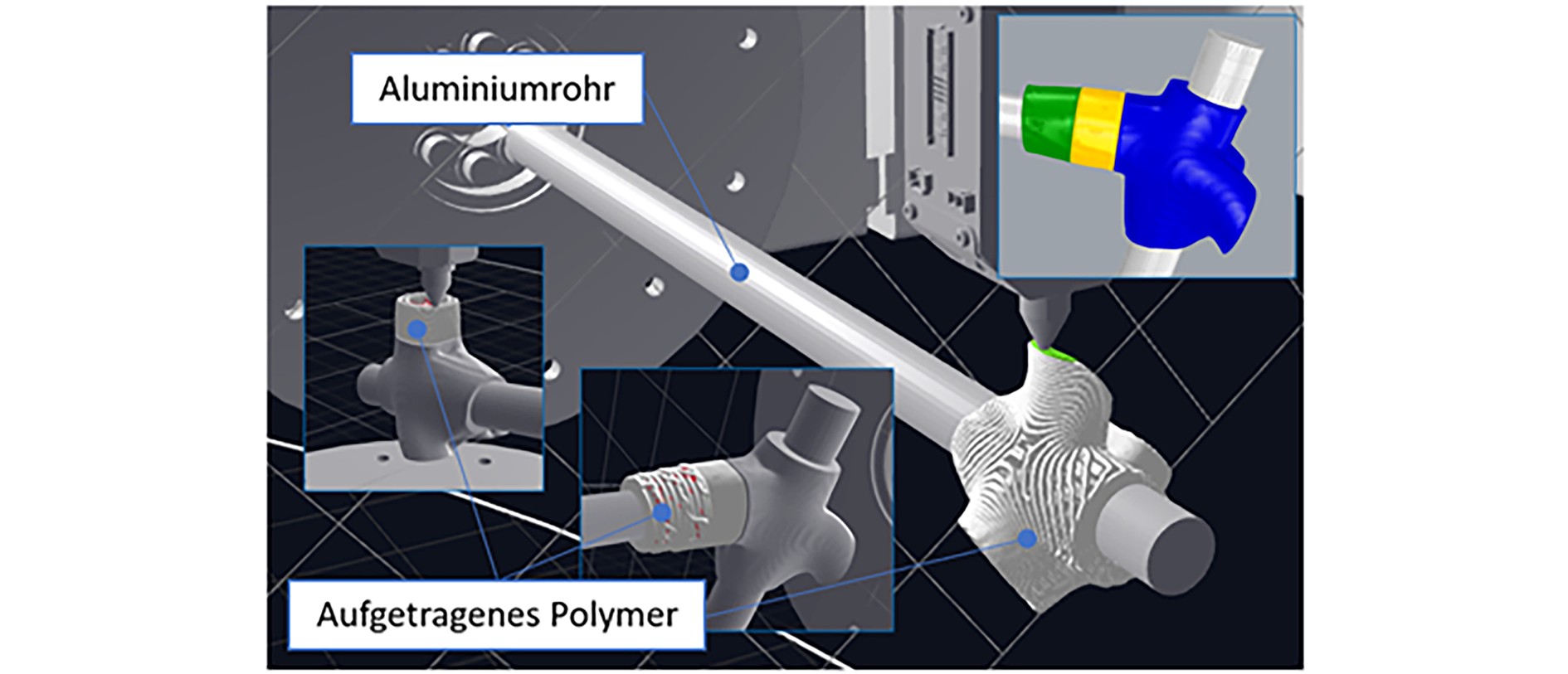
Bild 5. Der Verbindungsknoten mit Topologie-Optimierung ist für die getesteten Programme eine Herausforderung. Grafik: FH Südwestfalen
Jedoch führte die Planung des Topologie-optimierten Sattelknotens (Abbildung 5) nur mit einer Software zu einem zufriedenstellenden Ergebnis. Zwei der drei verbleibenden Tools konnten diesen nicht oder nur stark eingeschränkt für den Materialauftrag aufbereiten. Lediglich mit AdaOne ist es gelungen, den Sattelknoten mit optimierter Topologie-zu planen, wobei jedoch auch bei dieser Software noch Verbesserungspotenzial besteht. Insbesondere die Berücksichtigung von Störkonturen und die Verwendung der Positioniererachsen, die für die integrierte Fertigung von Verbundknoten im Rahmen des Forschungsvorhabens benötigt werden, stellen aktuell Herausforderungen dar. Die zur Verfügung stehenden Algorithmen und Einstellmöglichkeiten sind zwar vielfältig, jedoch nicht optimal auf den Materialaufbau auf bestehende Geometrien und die damit beabsichtigte Fertigung von Multi-Material-Strukturen zugeschnitten. Außerdem stellt die Bahnplanung aktueller Lösungen lediglich eine Idealplanung dar. Verfahrensspezifische Besonderheiten fließen nicht in die Berechnung ein.
Fazit und Ausblick
Zusammenfassend kann festgehalten werden, dass für einzelne Bereiche der multiaxialen Bahnplanung schon heute funktionierende Softwaretools zur Verfügung stehen. Beschichtungen oder auch aus einfachen Grundprimitiva zusammengesetzte Körper sind durchaus planbar. Wenn es jedoch um die einfache und flexible Planung beliebiger Geometrien unter der Zuhilfenahme aller kinematischer Freiheiten oder die Fertigung von Multi-Material-Strukturen geht, besteht noch Forschungsbedarf. Darüber hinaus könnte die Berücksichtigung verfahrensspezifischer Besonderheiten und die Integration eines lokal variablen Materialauftrags die Einsatzmöglichkeiten der industriellen Materialextrusion deutlich erweitern. Diese Themen sind aktuell Gegenstand weiterer Forschungsaktivitäten an der FH-SWF.
Literatur
- Coupek, D., J. Friedrich, D. Battran und O. Riedel. Reduction of Support Structures and Building Time by Optimized Path Planning Algorithms in Multi-axis Additive Manufacturing [online]. Procedia CIRP, 2018, 67, 221–226. ISSN 22128271. Verfügbar unter: doi:10.1016/j.procir.2017.12.203
- Wulle, F., D. Coupek, F. Schäffner, A. Verl, F. Oberhofer und T. Maier. Workpiece and Machine Design in Additive Manufacturing for Multi-Axis Fused Deposition Modeling [online]. Procedia CIRP, 2017, 60, 229–234. ISSN 22128271. Verfügbar unter: doi:10.1016/j.procir.2017.01.046
- Gardner, J., T. Nethercott-Garabet, N. Kaill, I. Campbell, G.A. Bingham, D. Engstrom und N.O. Balc. Aligning Material Extrusion Direction with Mechanical Stress via 5-axis Tool Paths. In: D. Bourell, Hg. Proceedings of the 29th Annual International Solid Freeform Fabrication (SFF) Symposium – An Additive Manufacturing Conference, 2018, S. 2005–2019.
- Keating, S. und N. Oxman. Compound fabrication: A multi-functional robotic platform for digital design and fabrication [online]. Robotics and Computer-Integrated Manufacturing, 2013, 29(6), 439–448. ISSN 07365845. Verfügbar unter: doi:10.1016/j.rcim.2013.05.001
- Kaill, N., R.I. Campbell, P. Pradel und G.A. Bingham. A Comparative Study Between 3-Axis and 5-Axis Additively Manufactured Samples and their Ability to Resist Compressive Loading: University of Texas at Austin, 2019.
- Wu, C., C. Dai, G. Fang, Y.-J. Liu und C.C. Wang. RoboFDM: A robotic system for support-free fabrication using FDM. In: 2017 IEEE International Conference on Robotics and Automation (ICRA): IEEE, 2017, S. 1175–1180. ISBN 978–1–5090–4633–1.
- Li, Y., K. Tang, D. He und X. Wang. Multi-Axis Support-Free Printing of Freeform Parts with Lattice Infill Structures [online]. Computer-Aided Design, 2021, 133, 102986. ISSN 00104485. Verfügbar unter: doi:10.1016/j.cad.2020.102986
- Etienne, J., N. Ray, D. Panozzo, S. Hornus, C.C.L. Wang, J. Martínez, S. McMains, M. Alexa, B. Wyvill und S. Lefebvre. CurviSlicer [online]. ACM Transactions on Graphics, 2019, 38(4), 1–11. ISSN 0730-1.
Das könnte Sie auch interessieren:
Trends in der Additiven Fertigung: ein Blick in die Zukunft
Die gesamte Prozesskette des Additive Manufacturing im Blick
Sascha Eckardt, M. Eng., Prof. Dr.-Ing. Gerrit Pohlmann, Prof. Dr.-Ing. Jörg Kolbe und Hendrik Holz, B. Eng., sind beziehungsweise waren im Rahmen des Forschungsprojekts zur Herstellung individualisierter Hybridbauteile an der FH Südwestfalen tätig.