Fertigungsstrategie als Gewinn für Mensch, Umwelt und Unternehmen
Bei der Metallbearbeitung kann eine schlechte Wahl des Werkzeugs oder der Bearbeitungsstrategie den Unterschied zwischen Erfolg und Misserfolg ausmachen – gezeigt wird, worauf es ankommt. Topaktuell ist ein Anwendungsbeispiel aus der Elektromobilität.
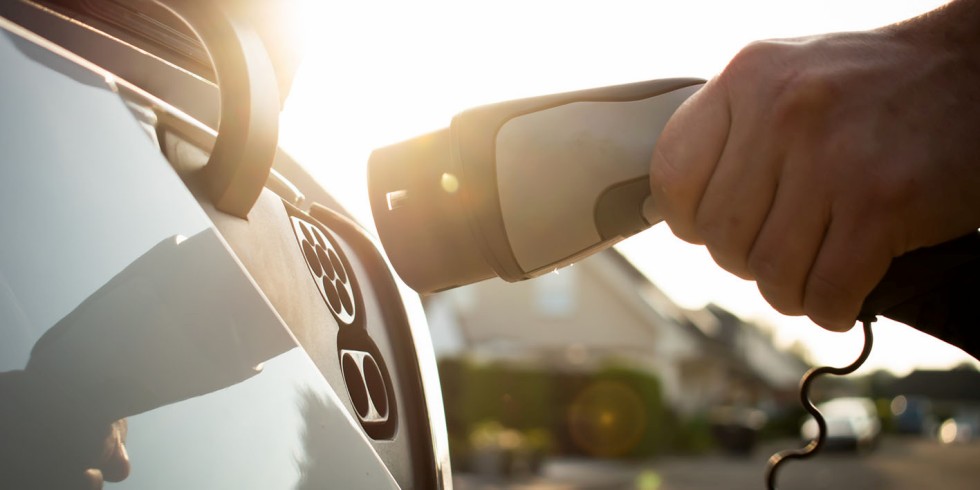
Laut McKinsey verursacht die Produktion von Elektrofahrzeugen fast 80 Prozent mehr CO2-Emissionen als die Herstellung von Fahrzeugen mit Verbrennungsmotor.
Foto: Shutterstock
Die Verschwendung von Material, eine hohe Ausschussquote sowie eine geringe Produktivität sind bei falsch gewählten Parametern die Anzeichen für einen nicht optimalen Bearbeitungsprozess. Doch auch wenn bekannt ist, dass sich mit den richtigen Tools und Verfahren bei Zerspanprozessen erhebliche Nachhaltigkeitsgewinne erzielen lassen, nutzen noch immer viele Fertigungsunternehmen diese Vorteile nicht.
Fortschritte bei der Reduzierung von Emissionen
Metalle sind das „Rückgrat“ der Industrie und ihre Einsatzmöglichkeiten reichen vom Stahl in Gebäuden, Aluminium in Autos, Titan in modernen Flugzeugen bis hin zu Kupfer in der Elektronik. Die Umsetzung von Plänen zur Dekarbonisierung wird die Nachfrage nach erneuerbaren Technologien und die Abhängigkeit von Metallen weiter ansteigen lassen. Der Stahl- und Eisentechnologie-Roadmap der Internationalen Energieagentur (IEA) zufolge wird die weltweite Nachfrage nach Stahl bis 2050 um mehr als ein Drittel zulegen. Damit steigen aber auch die Erwartungen an die Art und Weise, wie Metalle beschafft, hergestellt und in der Produktion verwendet werden.
Die Herstellung von Metallen gilt seit Langem als emissionsintensiver Prozess – doch es gibt Fortschritte. Beispielsweise wird bei „grünen Stählen“ Kokskohle, die traditionell für die erzbasierte Stahlerzeugung benötigt wird, durch erneuerbaren Strom und Wasserstoff ersetzt. Dadurch können die CO2-Emissionen bei der Metallherstellung drastisch reduziert werden. Doch auch Fertigungsunternehmen sollten sich mit ihren Prozessen beschäftigen, um ihre Nachhaltigkeitsziele umzusetzen.
Das „richtige“ Werkzeug wählen
Gerade für schwer zu bearbeitende Metalle, die mit engen Toleranzen und höchster Oberflächenqualität zu zerspanen sind, kommt es auf die richtigen Werkzeuge und das erforderliche Fachwissen an. Die Verschrottung von Bauteilen, die falsch bearbeitet wurden, ist unbedingt zu vermeiden. Häufige Gründe dafür sind die Verwendung falscher Tools, menschliche Fehler bei der Maschinenprogrammierung und unerkannte Schwankungen des Rohmaterials. Zudem haben Abfälle, wenn sie nicht recycelt werden, schwerwiegende Auswirkungen auf die Umwelt.

Die Verschwendung von Material, eine hohe Ausschussquote sowie eine geringe Produktivität sind Anzeichen für einen nicht optimalen Bearbeitungsprozess – und für eine nicht nachhaltige Bearbeitung.
Foto: Sandvik Coromant
Was zeichnet zuverlässige Werkzeuge für Drehprozesse aus?
Um den Ausschuss zu reduzieren, müssen Fertigungsunternehmen mit den richtigen Werkzeugeinstellungen und Schnittdaten arbeiten. Ansonsten sind hoher Werkzeugverschleiß und unkalkulierbare Standzeiten die Folge. Effizientes Drehen von Stahl führt beispielsweise zur Verringerung des Ausschusses und ist Teil einer effektiven Strategie zur Senkung der Produktionskosten in einem bestehenden Bearbeitungs-Setup.
Für eine sichere und produktive Bearbeitung sollten Drehsorten in Betracht gezogen werden, die eine lange und vorhersehbare Standzeit sowie eine gute Spankontrolle bieten. Die Wahl eines Werkzeugs mit längerer Standzeit in Kombination mit höherer Verschleiß- und Hitzebeständigkeit bringt greifbare Vorteile. Ungeplante Stopps oder Schäden am Werkstückmaterial oder der Hartmetall-Wendeschneidplatte lassen sich minimieren – notwendige Voraussetzungen für eine nachhaltige Bearbeitung. Das Engagement von Sandvik Coromant, recycelte Materialien für die eigenen Drehsorten zu nutzen, ist ebenfalls ein wichtiger Faktor, der die Fertigung der Kunden nachhaltiger macht.

Die „richtigen“ Werkzeuge und Technologien können die Produktivität steigern, Abfälle reduzieren und die Nachhaltigkeit der Metallzerspanung verbessern.
Foto: Sandvik Coromant
Wie Industrie 4.0 die Nachhaltigkeit unterstützt
Ebenso wie das Bewusstsein für Nachhaltigkeit nimmt auch die digitale Transformation in fast allen Branchen an Fahrt. In einer Umfrage unter mehr als 400 globalen Fertigungsunternehmen gaben 94 Prozent der Befragten an, dass Industrie 4.0 dazu beigetragen hat, ihren Betrieb während der Pandemie am Laufen zu halten. Die Herausforderungen von Covid-19 waren wie ein „Weckruf“ für viele Hersteller. Die Digitalisierung hilft Managern und Mitarbeitenden, fundiertere Entscheidungen zu treffen, führt zu einer höheren Produktivität, verringert Produktionsfehler und ermöglicht höhere Gewinne.
Weniger bekannt ist jedoch die entscheidende Rolle, die Industrie 4.0 für die Nachhaltigkeit spielt. Maschinen, die über das Internet der Dinge (IoT) vernetzt sind, können die unschätzbaren Erfahrungen menschlicher Mitarbeiter erweitern und bieten zusätzlich neue Möglichkeiten für Transparenz, optimierte Planung und rationalisierte Produktion. Ein guter Ausgangspunkt für jede Nachhaltigkeitsstrategie ist die Durchführung eines Audits, das den aktuellen Status eines Werks erfasst und datengestützte Erkenntnisse liefert. Mit diesem Ansatz lassen sich ineffiziente Bereiche identifizieren. Wenn beispielsweise vor Ort vorzeitiger Werkzeugverschleiß, minderwertige Oberflächen oder hohe Maschinenstillstandszeiten auftreten, können die mithilfe von Sensoren gesammelten Daten den Maschinenbedienern helfen, ihre Bearbeitungsprozesse derart zu verbessern, dass weniger Abfall anfällt und die Energieeffizienz erhöht wird.

Ein Kriterium im Entwicklungsprojekt des schwedischen Unternehmens liegt darin, den Einsatz von recyceltem Material in Werkzeugen zu erhöhen und den Abfall zu reduzieren.
Foto: Sandvik Coromant
Welche Lösungen sind sinnvoll und verfügbar?
Das „CoroPlus-Productivity Improvement Programme“ (PIP) ist eine der Lösungen, um Nachhaltigkeit und Effizienz zu verbessern. Der bewährte, strukturierte Prozess kann an einer einzelnen Maschine, einer Prozesskette oder im gesamten Werk durchgeführt werden. Zu Beginn identifizieren die Experten Ineffizienzen und installieren Lösungen zur Maschinenüberwachung, die Dateneinblicke in Echtzeit bieten. Dies bildet die Grundlage für eine eingehende Analyse der kompletten Produktionszelle bis hin zum Schneidwerkzeug. So wird sichergestellt, dass Maschinen so effizient wie möglich „laufen“. Neben der Eliminierung möglicher Verschwendung reduziert sich auch der Energieverbrauch. Nicht zuletzt werden auch die Arbeitsbedingungen für die Mitarbeitenden vor Ort verbessert, da sie sich auf reibungslose, stabile und vorhersehbare Prozesse verlassen können.
Beispiel: Präzise Bohrungen für die E-Mobilität
Ein Anwendungsbeispiel eines optimierten Zerspanprozesses aus der Automobilindustrie soll zum Abschluss zeigen, was „machbar“ ist. Häufig wird über die geringere Umweltbelastung von Elektrofahrzeugen im Vergleich zu Fahrzeugen mit Verbrennungsmotor gesprochen. Doch wie sieht es mit der Reduzierung von CO2-Emissionen bei der Fertigung von Elektrofahrzeugen eigentlich aus? Hier liegt noch einiges „im Argen“: Laut einer McKinsey-Studie entstehen bei der Produktion eines Elektroautos fast 80 Prozent mehr Emissionen als bei der Herstellung eines Fahrzeugs mit Verbrennungsmotor, vor allem aufgrund der Batterie und des höheren Anteils an Aluminiumkomponenten.
Robert Smith, Offer Manager für Bohrungen und Verbundwerkstoffe im Geschäftsbereich Vollhartmetallwerkzeuge bei Sandvik Coromant, erläutert, wie der Einsatz von wiederaufbereiteten Vollhartmetallbohrern einen Beitrag zu einer nachhaltigen Fertigung leisten kann. Dem Werkstoff Aluminium kommt eine Schlüsselrolle zu, da die leichten Bauteile zur Reduzierung des Fahrzeuggewichts und damit zu mehr Energieeffizienz beitragen. Aluminium-Motorblöcke für Elektrofahrzeuge enthalten jedoch viele Löcher, entsprechend leistungsfähig und langlebig sollten die genutzten Werkzeuge für die Bohrungen sein.
Ein brasilianisches Unternehmen, das Lösungen zur Gewichtsreduzierung für die weltweite Automobilindustrie entwickelt und herstellt, benötigte Unterstützung beim Tieflochbohren von Zylinderblöcken aus mittelfestem Aluminium 6082 (AISI CMC 30.21). Dabei traten Probleme mit dem Vollhartmetallbohrer auf, insbesondere hinsichtlich der Bohrungsausrichtung auf beiden Seiten des Zylinderblocks. Als Lösung empfahl Sandvik Coromant den „CoroDrill 865“: Der für Gusseisen, Stahl und Aluminium optimierte Vollhartmetallbohrer verfügt über eine innovative Geometrie, die eine höhere Produktivität und eine stabile Herstellung von tiefen Bohrungen bis zum 30-fachen des Bohrerdurchmessers ermöglicht. Zudem sorgen die Geometrie und das Nutenprofil des Bohrers für eine verbesserte Spanbildung und -abfuhr – beides sind eine wichtige Voraussetzungen für eine stabile, dauerhafte, gleichmäßige und produktive Bohrbearbeitung.

Der Vollhartmetallbohrer „CoroDrill 865“ kann zu einer nachhaltigeren Herstellung von Elektrofahrzeugen beitragen – dies belegen Testreihen.
Foto: Sandvik Coromant
Der Leistungstest: Der CoroDrill und ein Vergleichsbohrer wurden auf einer Heller-Drehmaschine „HMC 2000“ mit identischen Schnittparametern betrieben. Während das Werkzeug des Wettbewerbers nur maximal 1.200 Bauteile pro Schneide und somit 2.400 Bohrungen schaffte, produzierte der Vollhartmetallbohrer des schwedischen Herstellers 1.500 Bauteile pro Schneide bzw. 3.000 Bohrungen. Dabei hatte er nicht nur eine um 25 Prozent höhere Standzeit, sondern zeigte auch keinerlei Bohrabweichungen und löste dadurch das Hauptproblem des Kunden.
Nicht nur die Werkzeugleistung, auch das Werkzeug selbst kann zu einer nachhaltigeren Fertigung beitragen. Inzwischen arbeiten einige der größten Automobilhersteller nur dann mit Zulieferern zusammen, wenn diese wiederaufbereitete Werkzeuge einsetzen. Aber wie schneiden diese im Vergleich zu neuen Werkzeugen ab? Auch das wurde bei dem brasilianischen Unternehmen getestet. Nach dem ersten Einsatz wurden die CoroDrill 865-Bohrer in einem der elf weltweiten Wiederaufbereitungszentren wieder „auf Vordermann gebracht“. Dabei werden verschlissene Vollhartmetallbohrer und -fräser wieder in ihre ursprüngliche Qualität zurückversetzt. In weiteren Test zeigten diese Bohrer die gleiche Leistung wie neue Werkzeuge. Sie tragen somit entscheidend dazu bei, auch bei der Fertigung von Elektrofahrzeugen Nachhaltigkeit und Produktivität maßgeblich zu steigern.
Das könnte Sie auch interessieren:
Wenn jedes Gramm zählt: Werkzeuge für schnelle Elektromobile
Werkzeuge werden produktiver und nachhaltiger
Planfräser erzielen Leistungssprung für die Drucklufterzeugung