Getriebe für den Luftverkehr werden leichter und langlebiger
Energieeffiziente und leisere Flugzeuge sind ein hochaktuelles Thema. Auch kleine Bauteile wie Zahnräder können dazu einen Beitrag leisten. Gezeigt wird, was eine neuartige Fertigungs-Prozesskette bewirken kann.
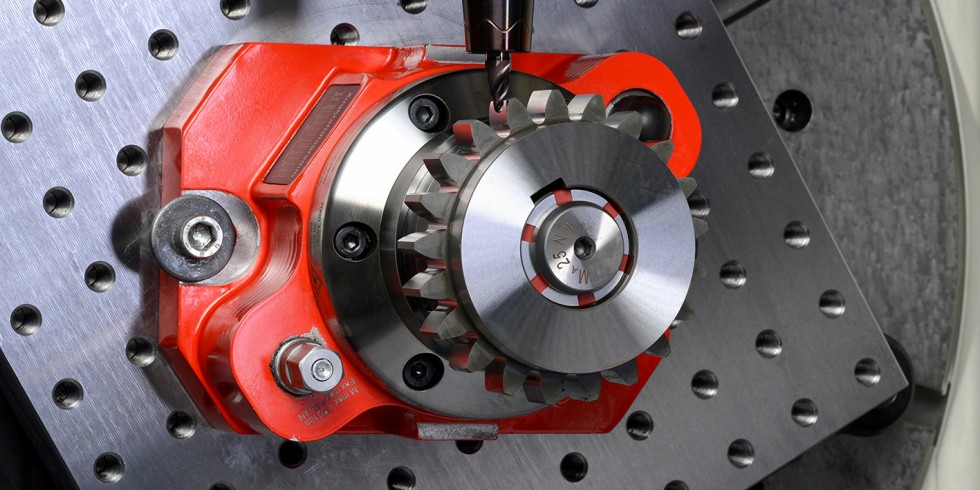
Zahnräder für Flugzeugtriebwerke: Erstmalig realisierten die Projektpartner eine Prozesskette mittels 5-Achs-Fräsen und anschließendem 5-Achs-Schleifen. Das Forschungsteam kam zu dem Ergebnis, dass die Fräsbearbeitung die maximal erreichbare Formgenauigkeit der Zahnräder vorgibt.
Foto: Fraunhofer IPT
Der Einsatz doppelschrägverzahnter Planetenradgetriebe macht Flugzeugtriebwerke effizienter: Diese Art der Verzahnung gewährleistet eine hohe Lastaufnahme und gleichzeitig eine beständige Laufruhe. Restriktionen kommen jedoch aus dem Bereich der Fertigungstechnik. Denn konventionelle Herstellungsverfahren für Verzahnungen können bei diesen Zahnradgeometrien nur mit großen Abstrichen beim Bauteilgewicht eingesetzt werden. Ein Forschungsteam des Fraunhofer-Instituts für Produktionstechnologie IPT in Aachen hat deshalb kürzlich in einem Konsortialprojekt eine neue Prozesskette entwickelt. Diese soll es erlauben, doppelschrägverzahnte Zahnräder mittels 5-Achs-Fräsen mit anschließendem 5-Achs-Schleifen zu fertigen. Die Zahnräder sind leichter und langlebiger als die bisherigen. Damit sind sie besser geeignet für den Einsatz in modernen Flugzeugtriebwerken.
Auswirkungen des Luftverkehrs auf Klima und Gesundheit verringern
Das zugrunde liegende Forschungsprojekt „CompactGears4Turbo“ wurde mit Mitteln des Bundesministeriums für Wirtschaft und Energie (BMWi) gefördert, denn effizientere Flugzeuge sind für das BMWi ein wichtiges Ziel: „Die Bundesregierung unterstützt auf nationaler, europäischer und internationaler Ebene Maßnahmen, um die Auswirkungen des Luftverkehrs auf Klima und Gesundheit zu verringern, die Emissionen des Luftverkehrs zu senken und auch im Bereich Luftverkehr zu den internationalen Klimazielen beizutragen“, so die Antwort auf eine Parlamentarische Anfrage hinsichtlich der Forschungs- und Entwicklungsausgaben des Bundes für die Luftfahrt aus dem Jahr 2019. Im geförderten Projekt, das zu diesen Maßnahmen gehört, hat das Fraunhofer IPT gemeinsam mit fünf Industriepartnern neue Prozessketten zur Herstellung kompakter und leichter Zahnräder erforscht (Förderkennzeichen: 20Q1705E). Beteiligt waren die Firmen ModuleWorks aus Aachen (Koordination), Aixpath aus Aachen, Rolls-Royce Deutschland aus Oberursel (assoziierter Partner), Aerospace Transmission Technologies aus Friedrichshafen (assoziierter Partner) sowie das Werkzeugmaschinenlabor WZL der RWTH-Aachen.
Hintergrund: Um Triebwerke effizienter zu gestalten, werden in der neuesten Triebwerksgeneration doppeltschrägverzahnte Planetenradgetriebe eingesetzt. Die Doppelschrägverzahnung gewährleistet eine hohe Lastaufnahme bei gleichzeitig beständiger Laufruhe. Allerdings ist ihre Fertigung sehr anspruchsvoll. Gängige Fertigungsverfahren, zum Beispiel das Wälzfräsen, benötigen große Ein- und Auslaufzonen, die ihrerseits breite Nuten zwischen den Radteilen erfordern. Das hat zur Folge, dass konventionell gefertigte Zahnräder dieser Art vergleichsweise schwer sind und hohe Verzahnungsbreiten aufweisen – beides ist nachteilig für die Verwendung in Flugzeugtriebwerken.
Im Fokus: Prozesskette zur Fertigung von kompakten, leichten Zahnrädern
Die Prozesskette zur Herstellung von Zahnrädern mit schmalen Nuten für Luftfahrtgetriebe umfasst fünf Schritte:
- die digitale Modellierung der Zahnräder (CAD),
- die computerbasierte Prozessauslegung (CAM),
- die Herstellung der Zahnrad-Makrogeometrie (5-Achs-Hartfräsen),
- die Herstellung der Zahnrad-Mikrogeometrie (5-Achs-Schleifen),
- die Prüfung der Zahnräder offline (Vermessung und Lebensdauertests) sowie durch neue Online-Ansätze (Industrie 4.0: Digital Twin).
Aufgabe des Fraunhofer IPT war es, geeignete Prozessstrategien für die 5-Achs-Fräs- sowie 5-Achs-Schleifbearbeitung der Zahnräder zu entwickeln. Konkret erarbeitete das Team des Fraunhofer IPT eine Prozesskette für das 5-Achs-Fräsen sowie eine Prozesskette für das 5-Achs-Fräsen mit anschließendem 5-Achs-Schleifen. Bei den Untersuchungen stellte sich heraus, dass die Fräsbearbeitung die maximal erreichbare Qualität der Zahnräder vorgibt. Das anschließende 5-achsige Schleifen hat zwar keine bedeutsamen Auswirkungen auf die Geometrie der Zahnräder. Die Schleifbearbeitung der Oberfläche hat jedoch für den Betrieb des Bauteils große Auswirkungen, da eine geringere Oberflächenrauheit die Reibung zwischen den Zahnflanken im Getriebe vermindert.

Das 5-Achs-Schleifen von Verzahnungen war bislang wenig erforscht. Tests im Rahmen des Projekts „CompactGears4Turbo“ zeigen, dass das Schleifen sich zwar eher nachteilig auf die Makrogeometrie der Zahnräder auswirkt, ihre Lebensdauer jedoch deutlich verbessert.
Foto: Fraunhofer IPT
Eine besondere Herausforderung war die Integration des Schleifens in die Prozesskette, denn das 5-Achs-Schleifen von Verzahnungen war bis dahin so gut wie unerforscht. Die beiden Verfahren – Fräsen und Schleifen – in einer solchen Prozesskette zu kombinieren, war also Pionierarbeit. Zunächst waren deshalb umfangreiche grundlegende Untersuchungen erforderlich, um geeignete Prozessstrategien zu erarbeiten. Insbesondere die Identifikation der passenden Werkzeuge für die 5-Achs-Schleifbearbeitung der Zahnräder war eine Aufgabe, die einiges an Aufwand beanspruchte.
CAM-Planungssoftware erleichtert die 5-Achs-Bearbeitung
Die im Projekt gewonnenen Erkenntnisse für die Auslegung der neuen Prozesskette flossen in die Entwicklung eines CAM-Planungssoftwarepakets für „Siemens NX“ ein. Diese Software dient zur Prozessplanung und umfasst auch die Bahnplanung für das Fräsen und Schleifen der komplexen Doppelschrägverzahnungen.
Testreihen mit mehreren gefertigten Zahnrädern ergaben, dass das zusätzliche 5-Achs-Schleifen die Lebensdauer der Zahnräder deutlich verbessert. Dies ist auf die verringerte Oberflächenrauheit zurückzuführen. Dank der neuen Prozesskette mitsamt der entwickelten CAM-Planungssoftware wird es nun möglich, optimierte Zahnräder für Planetengetriebe in Luftfahrtanwendungen herzustellen: Die Zahnräder fallen leichter sowie kompakter aus und haben eine längere Lebensdauer. Das Fraunhofer IPT plant, in Folgeprojekten seine Kompetenzen in diesem Bereich weiter zu vertiefen.
Das könnte Sie auch interessieren: