Hochpräziser Bearbeitungsroboter profitiert von neuartigem Antriebsstrang
Eine Forschungskooperation hat eine Lösung für die ressourceneffiziente, flexible und automatisierte Produktion entwickelt. Die neue Fräskinematik auf Linearachse erlaubt eine vielseitige und effiziente Bearbeitung – von Leichtbauwerkstoffen über Metalle bis hin zu Stählen – mit einer guten Fertigungstoleranz.
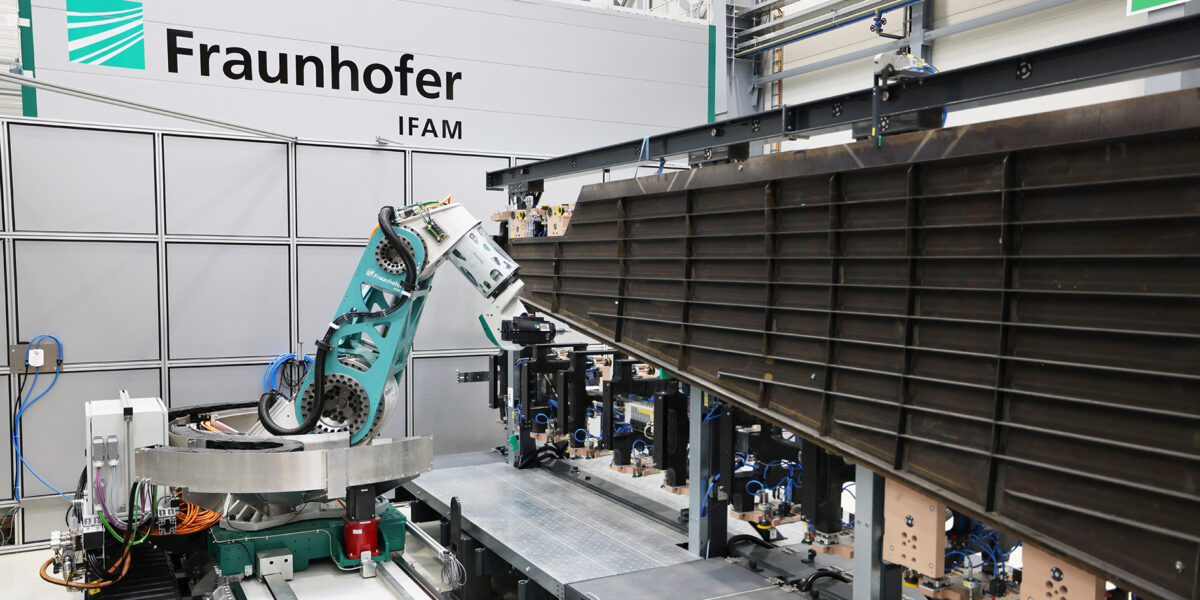
Die neu entwickelte flexible Fräskinematik mit Hybridantrieb auf einer Linearachse bearbeitet hochpräzise ein CFK-Flugzeugseitenleitwerk im 1:1-Maßstab.
Foto: Fraunhofer IFAM
Die Herausforderung des erfolgreich abgeschlossenen niedersächsischen LuFo-Projekts „Roboter Made in Niedersachsen 2“ (RoMaNi 2) bestand darin, die Lücke zwischen Industrierobotern und Werkzeugmaschinen zu schließen. Das vom Verbundführer Fraunhofer IFAM in Stade gemeinsam mit den Projektpartnern Broetje-Automation, Hexagon Aicon Etalon, Siemens sowie den assoziierten Partnern Airbus Operations und A&T Service erzielte Ergebnis der FuE-Arbeiten ist ein hochpräziser Bearbeitungsroboter mit besonderem Antriebsstrang, der nicht nur die Bearbeitung von Leichtbauwerkstoffen, sondern auch die von Metallen und sogar von Stählen in flexibler und effizienter Weise zulässt. Dabei wird eine Fertigungstoleranz bis zu 0,1 Millimetern erzielt.
Kinematik bewährt sich bereits in der Anwendung
Im Projekt wurden zwei für die Bearbeitung ausgelegte Roboterkinematiken eingehend untersucht, durch steuerseitige Einstellungen und messtechnische Unterstützung für bahngenaue Prozesse optimiert und anhand realer Anwendungsfälle aus der Luftfahrt im 1:1-Maßstab erprobt. Die Forschenden des Fraunhofer IFAM konnten im Projekt RoMaNi 2 die bereits im Vorläuferprojekt „Flexible Kinematik 4.1“ (Flexmatik 4.1) entwickelte Prototyp-Kinematik mit neuartigem Hybridantrieb komplett montieren, in Betrieb nehmen und in Bearbeitungsprozessen erproben.
Im Fraunhofer-Verbundprojekt Flexmatik 4.1 hatte das Fraunhofer IFAM gemeinsam mit dem Fraunhofer IPK und dem Fraunhofer LBF einen Roboter mit wesentlich verbesserten dynamischen Eigenschaften entwickelt. Er eignet sich für herausfordernde Aufgaben, zum Beispiel die Bearbeitung anspruchsvoller Materialien. Zum Projektabschluss von RoMaNi 2 gelang es nun, nicht nur ein Seitenleitwerk aus CFK (kohlenstofffaserverstärkter Kunststoff) des assoziierten Partners Airbus, sondern auch einen Prüfkörper aus Stahl hochpräzise zu bearbeiten.
Serielle flexible Industrieroboter oder stationäre hochpräzise Werkzeugmaschinen?
Serielle Industrieroboter zeichnen sich durch ihre Bauweise aus, die ein flexibles Maschinendesign möglich macht und ein vorteilhaftes Verhältnis zwischen der benötigten Aufstellfläche und dem verfügbaren Arbeitsraum bietet. Ihr Einsatz in verschiedenen Fertigungs- und Produktionsprozessen erweist sich als effizient und vielseitig. In Anwendungsfeldern der Handhabungs- und Montagetechnik sind sie etablierte Industrielösungen zur Automatisierung von Prozessschritten. Weitere Anwendungsgebiete – beispielsweise die spanende Bearbeitung von Leichtbauwerkstoffen – verzeichnen ebenfalls einen zunehmenden Einsatz von Industrierobotern.
Jedoch stoßen die Konzepte bisher bei steigenden Anforderungen, bedingt durch härtere Materialien oder anspruchsvollere Toleranzen, im Vergleich zu Werkzeugmaschinen an ihre Grenzen. Dies ist auf die begrenzten dynamischen Eigenschaften und die höhere Nachgiebigkeit zurückzuführen. Werkzeugmaschinen haben, bedingt durch ihre kinematische Bauweise, eine geringe Nachgiebigkeit und hohe Präzision. Bei der Skalierung auf größere Bauteile im Meterbereich führt dieses Maschinendesign jedoch zu einem erheblichen Material- und Investitionseinsatz.
Beispiel: spanende Bearbeitung von CFK-Großbauteilen im 1:1-Maßstab
Mit dem Einsatz neuer Herstellungsverfahren konnten in den vergangenen Jahren weitere Entwicklungen in der Designfreiheit und strukturellen Integrität von endkonturnahen Bauteilen aus carbonfaserverstärkten Kunststoffen (CFK) im Flugzeugbau erzielt werden. Aufgrund der wirtschaftlichen und technischen Anforderungen werden hochpräzise mechanische Nachbearbeitungen von Großbauteilen im Meterbereich mit Toleranzangaben im Submillimeterbereich heute üblicherweise mit großen Werkzeugmaschinen in Portalbauweise durchgeführt. Bedingt durch ihre kinematische Struktur, sind Portalmaschinen aber sehr groß. Dies diktiert oftmals den Aufbau der Produktionsstätten und es kann nur wenig flexibel auf Änderungen im Produktionsablauf reagiert werden.
Ein alternatives Maschinenkonzept bietet hier der Industrieroboter inklusive Arbeitsraumerweiterung durch eine flächenbewegliche Plattform, dem Aufbau mehrerer Roboter oder unter Einsatz von translatorischen Zusatzachsen (wie Linearachsen). Im Vergleich zu Portalanlagen ist dieses Maschinenkonzept wesentlich platzsparender und nicht ökonomisch an einzelne Großbauteile gebunden. Zusätzlich entfällt der Einsatz von Sonderfundamenten, was eine zukünftige Anpassung von Fertigungsstraßen erleichtert. Im Projekt RoMaNi 2 wurde der Prototyp-Roboter mit einer Linearachse für bahngenaue Roboter kombiniert.
Obwohl Industrieroboter schon erfolgreich in der Bearbeitung von dünnen Schalenbauteilen aus der Luftfahrt eingesetzt wurden, ist eine Erhöhung der Robustheit gegenüber auftretenden Prozesskräften sowie die Erschließung anspruchsvollerer Bearbeitungsaufgaben der nächste Schritt, um den wachsenden Einsatz in der Produktion großer Bauteile im Luftfahrtbereich zu erschließen.
Hybridantrieb verbessert dynamisches Verhalten von seriellen Industrierobotern deutlich
Die selbst entwickelte Kinematik des seriellen Prototyp-Roboters ist grundsätzlich auf die Bedürfnisse von Bahnprozessen ausgelegt. Ziel war das Einhalten der Fertigungstoleranz von mindestens ± 0,1 Millimetern bei der Bearbeitung von Großbauteilen bereits ab Bauteil 1. Die Montage der gesamten Kinematik, die Inbetriebnahme, steuerseitige Optimierung und Weiterentwicklung sowie die intensive Untersuchung der Roboterkinematik konnte nun im Projekt RoMaNi 2 erfolgreich abgeschlossen werden. Dabei bestätigten Genauigkeitsuntersuchungen, dass das angestrebte Ziel erreicht wurde.

Anhand der hochpräzisen Bearbeitung eines Prüfkörpers aus Stahl zeigt sich, dass der eigenentwickelte Roboter mit Hybridantrieb geeignet ist, die Lücke zwischen Industrierobotern und Werkzeugmaschinen zu schließen.
Foto: Fraunhofer IFAM
Ein zentrales Element zur Verbesserung des dynamischen Verhaltens des Prototyp-Roboters ist neben der Strukturoptimierung der Einsatz eines innovativen Antriebskonzepts in den Grundachsen. Durch den Einsatz eines zusätzlichen Direktantriebs, parallel zum herkömmlichen Getriebeantrieb, kann direkt auf der Lastseite ein Moment aufgeschaltet werden. Dieses Hybrid-Antriebskonzept verbindet die Möglichkeit, unerwünschte Effekte des Getriebes zu kompensieren und Anregungen hoher Frequenzen zu dämpfen, bei gleichzeitig hoher Energieeffizienz im statischen und quasistatischen Lastfall. Angesteuert wird die Kinematik mit der „Sinumerik One“ von Siemens. Die weit verbreitete Expertise der Bedienung von CNC-Maschinen ist somit – ohne Umschulung auf neuartige Steuerungstypen – nutzbar. Im Projekt konnten Steuerungskomponenten für den Hybridantrieb so weiterentwickelt werden, dass nun das volle Potenzial des Antriebs in der erprobten Industriesteuerung abrufbar ist.
Breites Anwendungsfeld durch Kombination Linearachse / Roboter mit Hybridantrieb
Die Kombination einer seriellen Knickarm-Kinematik mit einer Linearachse bietet gegenüber großen Portalanlagen und Sondermaschinen vielfältige Vorteile. Die geringere Standfläche sowie die modular gestaltete Linearachse sorgen für eine hohe Flexibilität. Durch den Einsatz zweier verspannter Ritzel-Zahnstangen-Antriebe werden Umkehreffekte kompensiert und eine ausreichend hohe Antriebssteifigkeit des Linearachsschlittens für bahngenaue Roboterprozesse erreicht. Aufgrund der hohen Struktursteifigkeit der Linearachse sind die Einflüsse auf die Robotergenauigkeit – trotz großer Hebelarme zum Lastangriffspunkt – gering. Im Projekt ließen sich so Bahngenauigkeiten von 0,15 Millimetern sogar für Großbauteile bis zu 7 Metern erzielen. Die Forschenden des Fraunhofer IFAM sind überzeugt, dass höhere Genauigkeiten durch die Kompensation weiterer statischer Einflussfaktoren wie der Temperatur erreichbar sind.
Eine deutliche Verbesserung des Führungsverhaltens und der Störunterdrückung der Roboterkinematik auf Achsebene wird durch den Einsatz von Direktantrieben erreicht. Die direkte mechanische Übertragung der Motormomente auf die Kinematik erlaubt zudem eine erhöhte Ruck-Einstellung aller Grundachsen. Diese liegt um den Faktor 10–100 höher gegenüber konventionellen Robotern mit Servoantrieben. Dies bietet ein erhebliches Potenzial zur Steigerung der Produktivität. Darüber hinaus lässt sich eine wesentliche Erhöhung der Bahngenauigkeit auch bei hohen Bahngeschwindigkeiten nachweisen. Bei hoher Vorschubgeschwindigkeit von 10 Meter/Minute ist eine Bahngenauigkeit im Bereich der vorab erfassten statischen Genauigkeit nachweisbar. Eine Dämpfung der ersten Eigenmoden, verursacht durch die Getriebeantriebe, bietet zudem Chancen zu einer verbesserten Störunterdrückung.
Mit der Bearbeitung eines Stahlprüfkörpers konnte das Projekt erfolgreich den nächsten Schritt – Erschließung neuer Anwendungsgebiete für Industrieroboter – gehen. Der Prüfkörper umfasste dabei verschiedene Geometrien wie Ecken, Flächen und Kreise. Die Bearbeitung erfolgte mit den gegebenen Bearbeitungsparametern des Werkzeugherstellers.
Weiterentwicklung bis zur Serienreife
Im nächsten Schritt wollen die Forschenden des Fraunhofer IFAM die neue Technik zusammen mit Partnern aus der Industrie bis zur Serienreife weiterentwickeln. Für Industrieroboter mit Hybridantrieb gibt es eine Vielzahl von Anwendungen: Das Spektrum reicht in Kombination mit einer Linearachse von Bearbeitungsaufgaben aus der Luftfahrt – wie leichteren Faserverbundstrukturen und Aluminiumlegierungen – bis zur Bearbeitung härterer Materialien, wie Stahl oder Titan. Diese Werkstoffe kommen beispielsweise im Schienen-, Nutzfahrzeug- und Schiffbau sowie in der Energiebranche zum Einsatz. Eine Bearbeitung solcher Bauteile und Materialien war bisher mittels Industrieroboter nicht industriell robust realisierbar. Insbesondere die Bearbeitung schwer zerspanbarer Materialien durch die neue Lösung erscheint somit zukunftsträchtig.
Das Niedersächsische Ministerium für Wirtschaft, Verkehr, Bauen und Digitalisierung und die NBank förderten das LuFo-Forschungsprojekt „Roboter Made in Niedersachsen 2“ (Förderkennzeichen: ZW1–80155399). Im Namen aller Projektpartner bedankt sich das Fraunhofer IFAM bei diesen Förderern sowie beim Deutschen Zentrum für Luft- und Raumfahrt (DLR) als Projektträger für deren Unterstützung.
Das könnte Sie auch interessieren:
Hochleistungs-Mikrofräsen hochharter Stähle am Beispiel Bipolarplatten
Schneestrahltechnologie – eine Alternative für schwer bearbeitbare Werkstoffe
Spröd-harte Werkstoffe – eine Herausforderung für die Zerspanung