Hohes Zeitspanvolumen für eine überzeugende Manövrierfähigkeit
Hohe Wellen, der Wind stürmt gegen Backbord und die Gischt peitscht über das Deck. Das Versorgungsschiff ist nur wenige Meter von den gewaltigen Stützfüßen der Offshore-Plattform entfernt. Jedoch weicht das Schiff nicht einen Meter von seiner Position. Wie ist das möglich? Die Crew steuert dieses mit Voith-Schneider-Propellern.
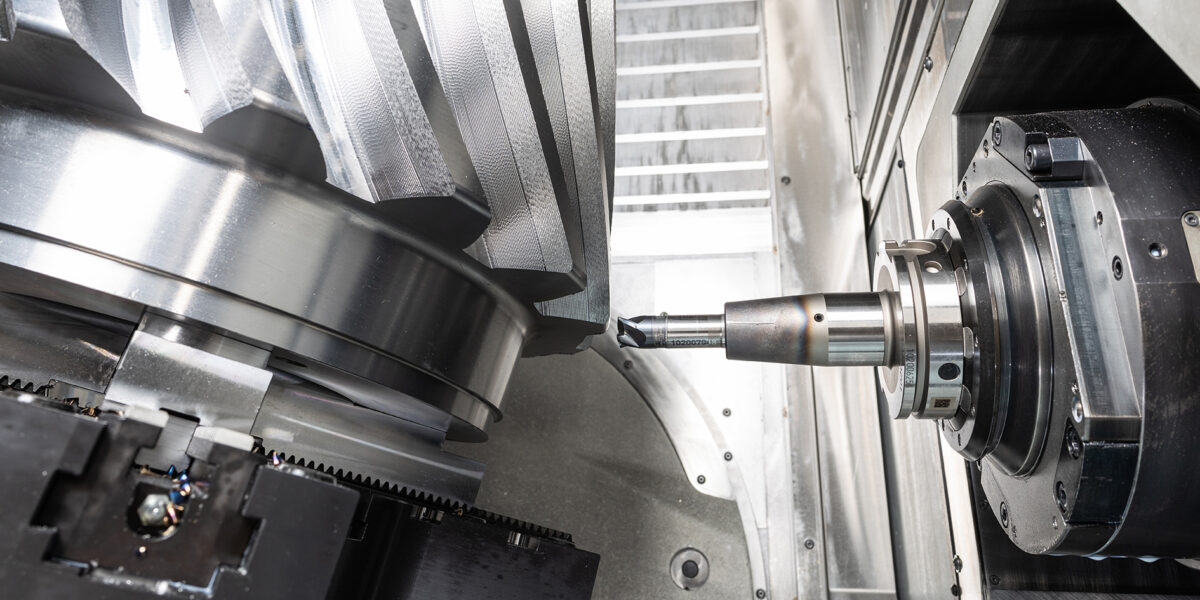
Verzahnungen für hocheffiziente Schiffsantriebe: Durch die Umstellung auf das Hochvorschubfräsen konnte Voith die Bearbeitungszeit bei der Herstellung um 55 Prozent senken.
Foto: Horn/Sauermann
Seit rund 100 Jahren produziert Voith diesen speziellen Antrieb im schwäbischen Heidenheim. Die Kraftübertragung geschieht bei der mechanischen Variante der Antriebstechnik über enorme Verzahnungsbauteile. Zum Schruppen der Verzahnungen setzt das Team rund um den Prozess-Ingenieur Dr. Thomas Glaser auf Hochvorschub-Frässysteme der Hartmetall-Werkzeugfabrik Paul Horn aus Tübingen, ergänzt durch ein System des Kooperationspartners Boehlerit aus Kapfenberg in Österreich.
Einfaches Prinzip – perfekt umgesetzt
Durch seine Bauweise erzeugt ein Voith-Schneider-Propeller (VSP) Schub in jede beliebige Richtung. Er ist daher Antrieb und Steuerung in einem. Dank kurzer Reaktionszeiten auf Steuerbefehle ermöglicht der VSP zudem auch unter widrigen Bedingungen ein schnelles, sicheres und präzises Manövrieren. Sogar eine seitliche Bewegung (Traversieren) erlaubt das System. Zum Einsatz kommt dieses Antriebskonzept bei Schiffen, die eine hohe Manövrierfähigkeit benötigen. Dazu zählen beispielsweise Hafenschlepper, Doppelendfähren, Schwimmkräne sowie Bohrinselversorgungsschiffe.
In einem Radkörper sind senkrecht bewegliche und steuerbare Flügelblätter montiert. Je nach Typ variiert die Anzahl zwischen vier und acht Flügeln. Rotiert der Radkörper und die Flügel führen währenddessen eine Schwingbewegung aus, dann wird Schub erzeugt. Die Drehzahl des Radkörpers und die Schwingungsamplitude bestimmen dessen Kraft. Die Phasenlage der Flügel bestimmen die Richtung. Der VSP arbeitet im Betrieb mit geringen Drehzahlen. Diese betragen nur rund 25 Prozent von herkömmlichen Schiffspropellern. Die dadurch entstehenden hohen Drehmomente verlangen nach einer robusten Konstruktion des Systems. Der Antrieb der VSP erfolgt über Diesel- oder Elektromotoren.
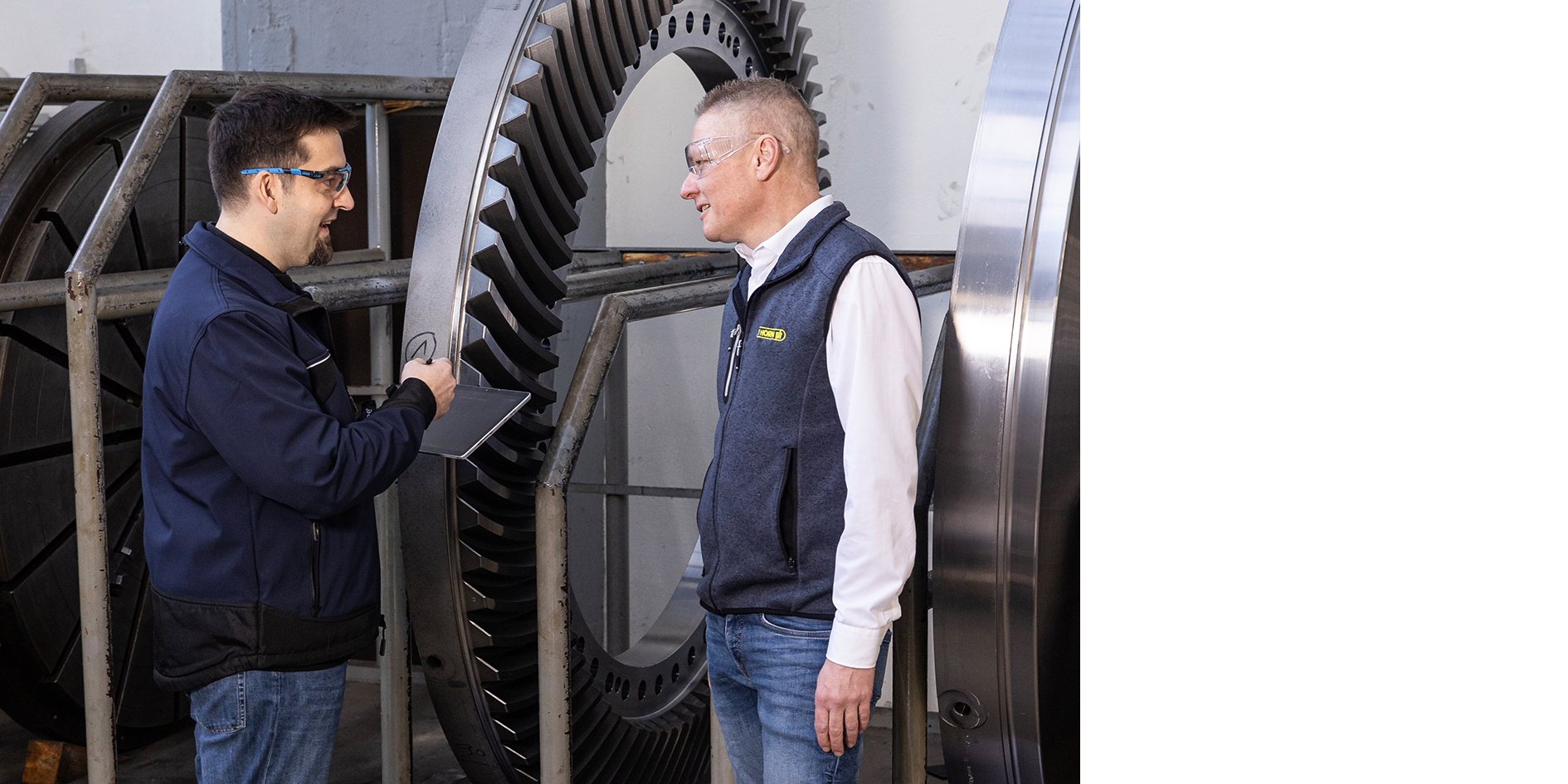
Eine Erfolgreiche Zusammenarbeit: Dr. Thomas Glaser im Gespräch mit dem Horn-Außendienstmitarbeiter Stephan Weiß (rechts). Im Hintergrund ist das passende Tellerrad zu dem gefrästen Ritzel zu sehen.
Foto: Horn/Sauermann
Die Kraftübertragung von Motor zum Propeller geschieht in der mechanischen Variante über ein Kegelradgetriebe. Je nach Größe des VSP, gestalten sich auch die Ausmaße der Verzahnungsbauteile. Aufgrund der teils langen Bearbeitungszeiten sucht Glaser stets nach Punkten, wie er die Bearbeitungsprozesse optimieren kann: „Die Fertigung eines Kegelritzel mit dem Modul 21,4 erforderte eine Anpassung. Für die Vorbearbeitung des Ritzels benötigten wir auf einer speziellen Schälmaschine eine sehr lange Bearbeitungszeit“. Das Ziel war die Umstellung vom Schälen zum 5-Achs-Simultan-Schrupp-Fräsen, um die Bearbeitungszeit nahezu zu halbieren. „Ein weiterer wichtiger Punkt war die Standzeit der Werkzeuge. Hier legten wir fest, dass der Standweg eines Werkzeugs mindestens ein Bauteil betragen muss“, so Glaser.
Hochvorschubfräser zweier Kooperationspartner bringen den Durchbruch
Aufgrund der guten Erfahrungen mit Horn-Vollhartmetall (VHM)-Fräsern beim Hart- und Fertigfräsen war der Tübinger Werkzeughersteller der erste Ansprechpartner für den Fräsprozess der Modul 21,4-Verzahnung. Wegen des hohen Zerspanvolumens – und der geforderten Reduktion der Bearbeitungszeit um 40 Prozent – kommen zum Schruppen Hochvorschubfrässysteme zum Einsatz.
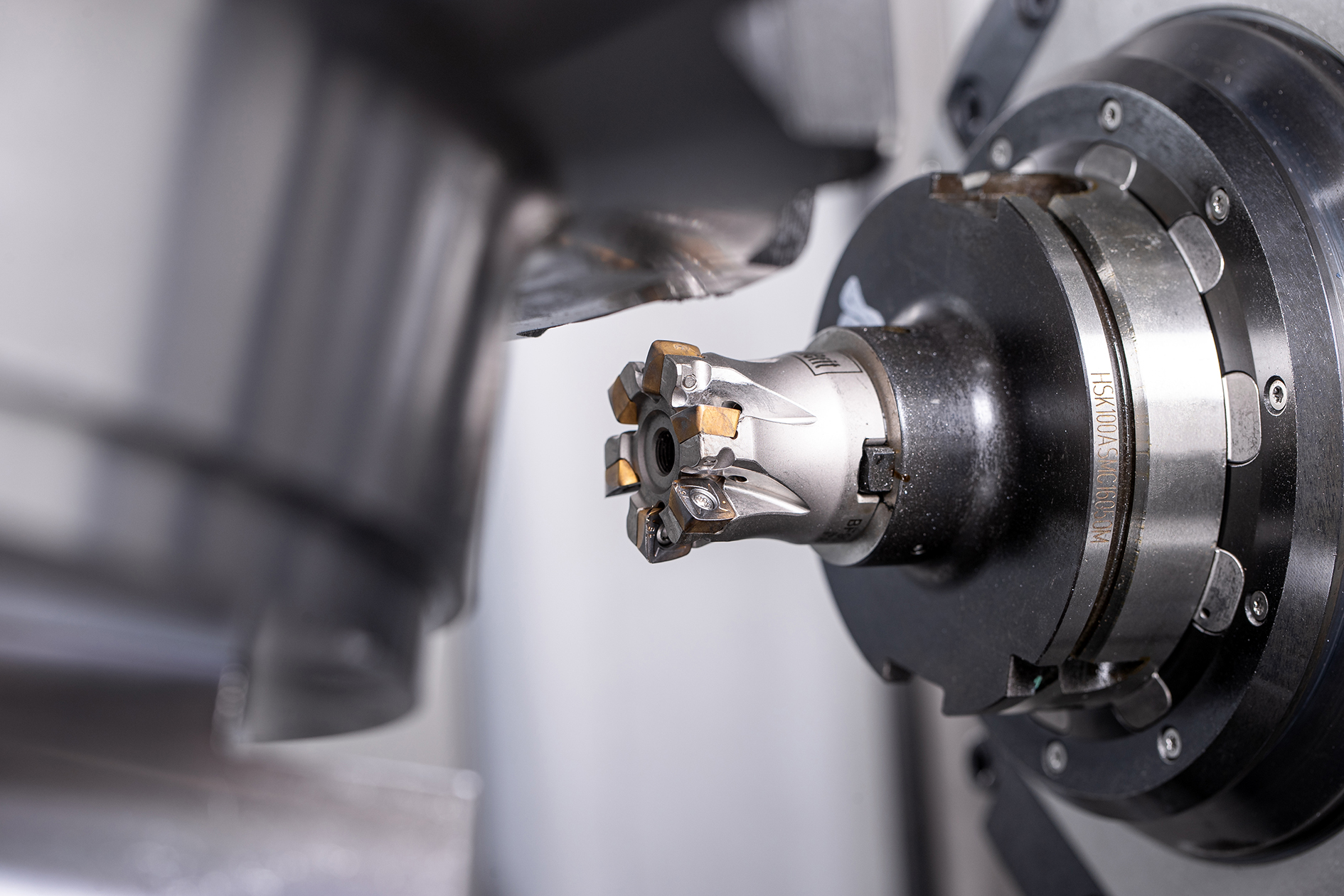
Für den ersten Schnitt kommt ein Hochvorschub-Wendeschneidplattenfräser des Kooperationspartners aus Kapfenberg/A zum Einsatz.
Foto: Horn/Sauermann
Die Wahl fiel, aufgrund der Verzahnungsgeometrie, auf drei unterschiedliche Durchmesser sowie unterschiedliche Fräsertypen. Den ersten Schnitt übernimmt ein Wendeschneidplattenfräser mit einem Durchmesser von 40 mm und sechs Zähnen von Boehlerit. Die zweite Zustellung übernimmt Horn-Wechselkopffräser des Typs „DGH“ mit vier Schneiden und einem Schneidendurchmesser von 20 mm.
Zum Schruppen des Zahngrunds des Ritzel kommt ein VHM-Schaftfräser der Baureihe „DSH“ mit dem Durchmesser 12 mm und ebenfalls vier Zähnen zum Einsatz.
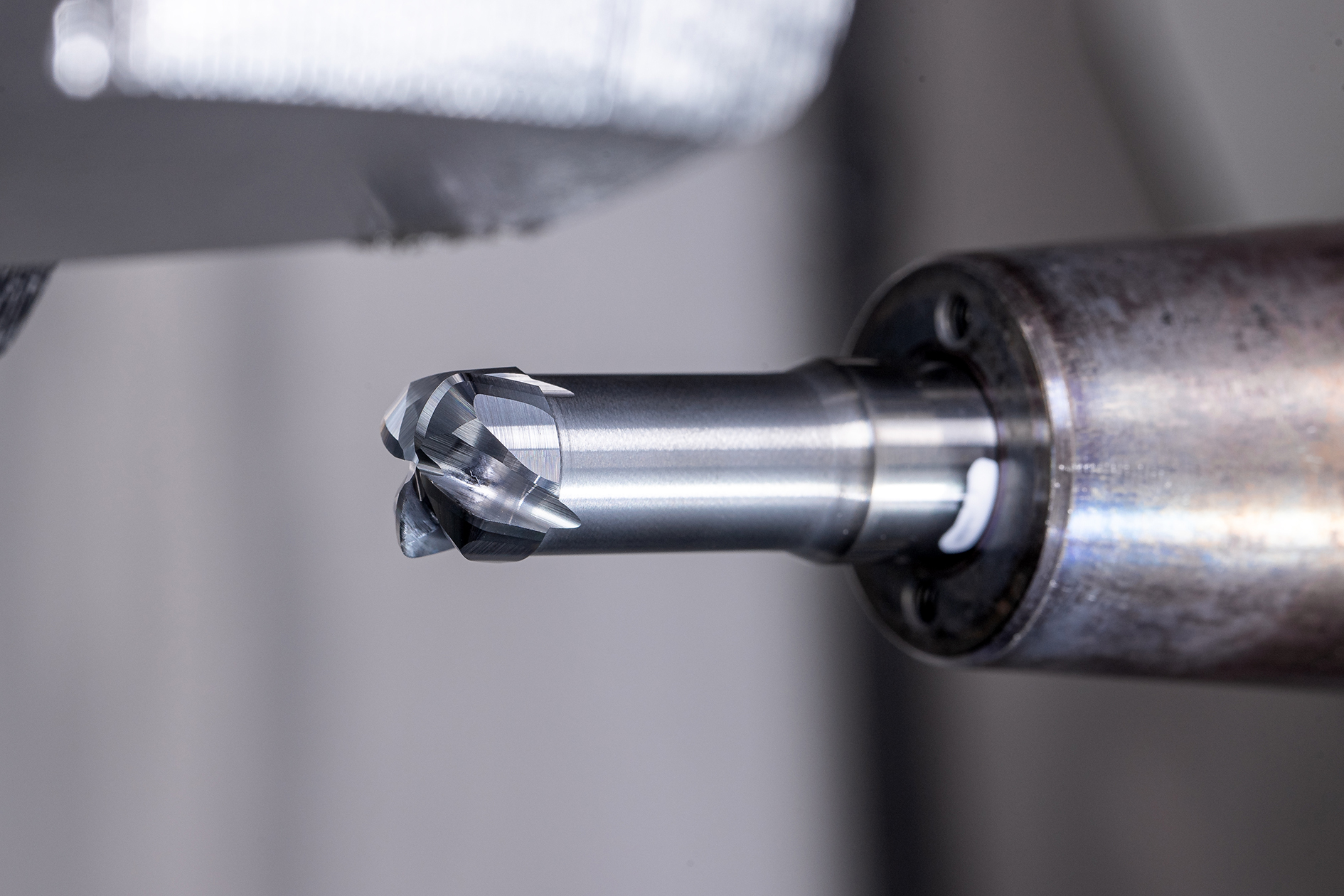
Den finalen Schruppschnitt übernimmt ein Vollhartmetall-Schaftfräser des Typs „DSH“.
Foto: Horn/Sauermann
Hochvorschubfräser schneiden stirnseitig. Durch die Belastung in Achsrichtung ist die Werkzeugspindel vorwiegend auf Druck belastet und die Querkräfte sind verhältnismäßig niedrig. Wegen der geringen Vibrationsneigung können die Werkzeuge die hohen Belastungen bei den üblichen Zahnvorschüben von fz = 1 mm bei Schnitttiefen ap bis 1,5 mm sicher aufnehmen. Der große Radius an der Hauptschneide der Wendeschneidplatten erzeugt einen weichen Schnitt, sichert eine gleichmäßige Aufteilung der Schnittkräfte und damit lange Standzeiten.
Auf der Innenseite sorgt ein kleiner Schneidenradius für ein problemloses und schnelles Eintauchen. Ein Primär- und Sekundärfreiwinkel führt zu einem stabilen Keilwinkel und guter Schneidenstabilität. Durch bedeutend höhere Vorschübe als beim konventionellen Fräsen ist das Zerspanvolumen beim Hochvorschubfräsen wesentlich höher – trotz der geringeren Zustelltiefen.
Werkzeugspektren ergänzen sich ideal
Die Vertriebskooperation zwischen Horn und Boehlerit besteht seit dem September 2016. Ziel dieser Zusammenarbeit ist es, sowohl die Produkt- als auch die Vertriebssynergien von zwei mittelständischen Unternehmen zu bündeln und als familiengeführte Betriebe gemeinsam in gezielten Märkten zu wachsen. Für Horn ist das Boehlerit-Fräsprogramm eine passende Produktergänzung zum eigenen Fräsprogramm. Die Tübinger erweitern somit ihre führende Werkzeugposition bei technisch anspruchsvollen Anwendungen, auch im Hinblick auf die allgemeine Zerspanung.
Das erfreuliche Fazit: Ziel erreicht
Für das Schruppen der Verzahnung setzt man bei Voith auf ein neues, vollautomatisiertes Fertigungssystem von Grob. Die Anlage besteht aus drei 5-Achs-Bearbeitungszentren mit automatischen Linearspeichern sowie diversen Rüststationen.
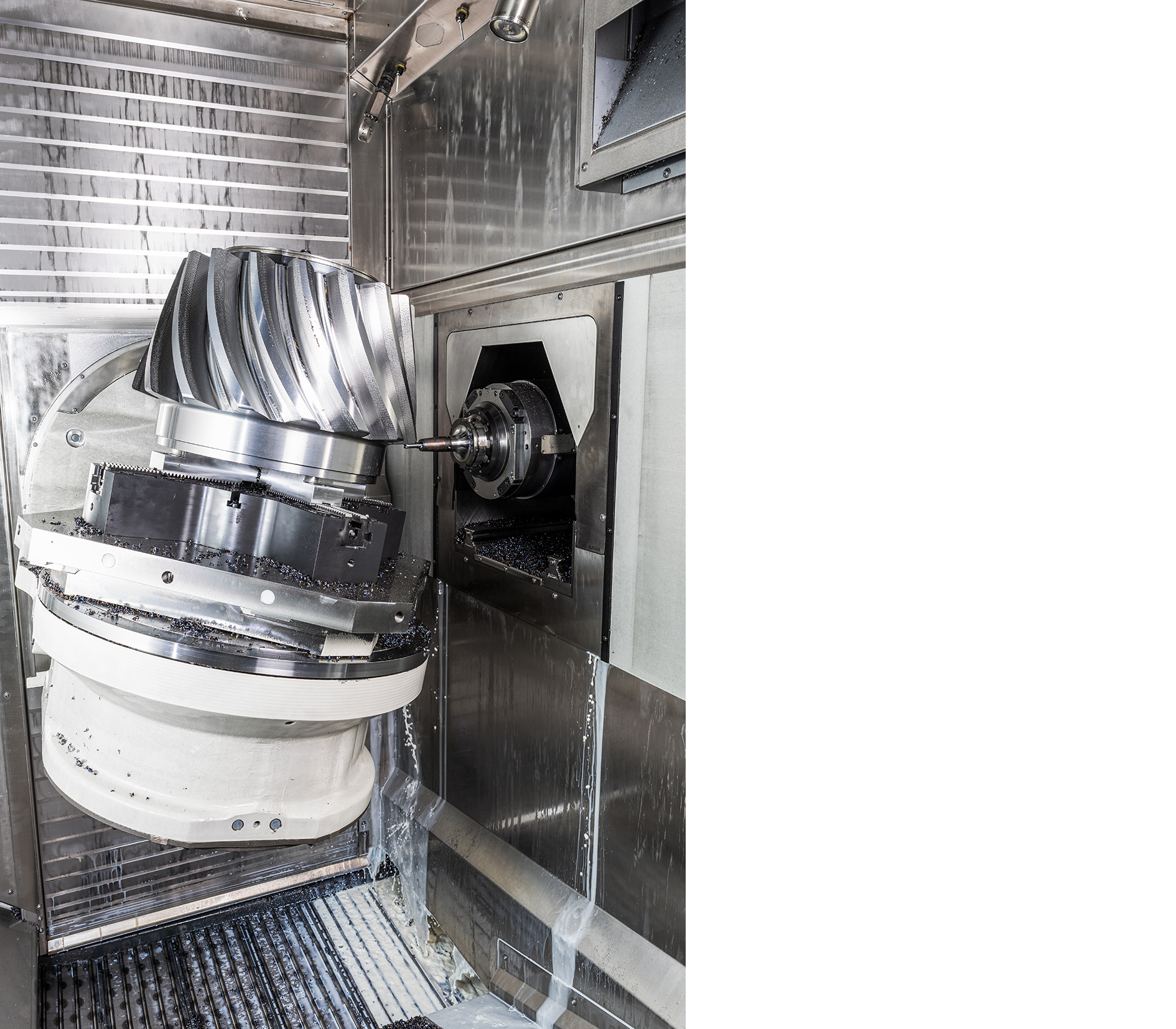
Beim Heidenheimer Antriebstechnik-Spezialisten setzt man auf Bearbeitungszentren der Mindelheimer Grob Group.
Foto: Horn/Sauermann
Die Bearbeitungszeit beim Vorverzahnen konnte durch die Umstellung auf das neue Werkzeugkonzept im Vergleich zum Schälen um 55 Prozent reduziert werden. Das Ziel von 40 Prozent wurde somit übertroffen. Die Standzeit der Werkzeuge beläuft sich wie gefordert auf ein Bauteil pro Werkzeug, beziehungsweise eine Schneide beim Wendeschneidplattenfräser. „Die Leistungen der Fräser haben uns vollständig überzeugt. Es sind jedoch nicht nur die Werkzeuglösungen: Zur Umsetzung von solchen Projekten gehört auch die kompetente technische Beratung sowie eine schnelle Reaktions- und Lieferzeit. Diese Merkmale erfüllt Horn für uns als Werkzeugpartner bestens“, erzählt Glaser.
Über den Antriebstechnik-Spezialisten
Die Voith Group ist ein weltweit agierender Technologiekonzern. Mit einem breiten Portfolio aus Anlagen, Produkten, Serviceleistungen und digitalen Anwendungen werden Maßstäbe in den Märkten Energie, Papier, Rohstoffe und Transport gesetzt. Gegründet 1867, ist Voith heute mit rund 22.000 Mitarbeiterinnen und Mitarbeitern, 5,2 Milliarden Euro Umsatz und Standorten in über 60 Ländern der Welt eines der großen Familienunternehmen Europas. Der Konzernbereich Voith Turbo ist Teil der Voith Group und ein Spezialist für intelligente Antriebstechnik, -Systeme sowie maßgeschneiderte Serviceleistungen. Durch innovative und smarte Produkte werden hohe Effizienz und Zuverlässigkeit geboten. Kunden aus zahlreichen Branchen wie Öl/Gas, Energie, Bergbau, Maschinenbau, Schiffstechnik, Schienen- und Nutzfahrzeuge setzen auf diese Spitzentechnologien und die digitalen Lösungen.
Das könnte Sie auch interessieren:
TechDays 2025 – Einladung an alle Akteure der Zerspanungsindustrie
Nico Sauermann arbeitet als Fotograf und Redakteur bei der Hartmetall-Werkzeugfabrik Paul Horn GmbH in Tübingen.