Intelligente Technologiekette optimiert das Nachbearbeiten additiv gefertigter Bauteile
Ein Alleinstellungsmerkmal der werkzeuglosen Additiven Fertigung ist die effiziente Herstellung von Bauteilen in Losgröße 1. Forschende am Fraunhofer-Institut für Produktionsanlagen und Konstruktionstechnik IPK entwickeln aktuell neue Technologien, um die Wirtschaftlichkeit der Endbearbeitung bei metallischen AM-Bauteilen zu steigern.
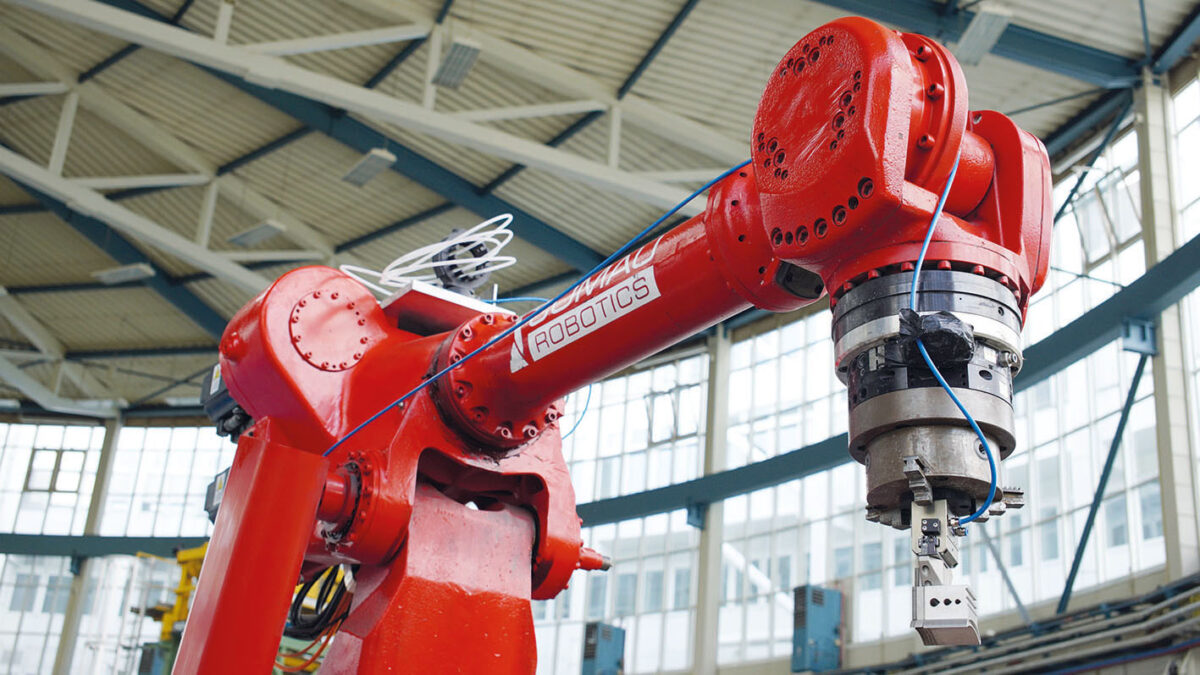
Durch die intelligente Technologiekette wird die optimale Abfolge der Endbearbeitungsschritte additiv gefertigter Bauteile ermittelt und von einem Industrieroboter automatisiert ausgeführt.
Foto: Gero Esser
Die Endbearbeitung von AM (Additive Manufacturing)-Metallbauteilen, welche auch als „Post-Processing“ bekannt ist, trägt mit einem Anteil von über 25 Prozent [1] maßgeblich zu den Kosten k bei. Die Ursachen hierfür sind eine unzureichende Wissensbasis über effiziente Abläufe sowie eine Vielzahl von manuell ausgeführten Tätigkeiten. Forschende am Fraunhofer IPK arbeiten an der Entwicklung einer intelligenten Technologiekette, welche die Effizienz und den Automatisierungsgrad des Post-Processing additiv gefertigter metallischer Komponenten von einer Losgröße 1 bis zur Serienfertigung adressiert.
Bearbeitungsverfahren sollen hohe Bauteilqualität und Wirtschaftlichkeit gewährleisten
Wie in Bild 1 am Beispiel einer Fahrradkurbel gezeigt, weisen Bauteile nach dem additiven Fertigungsprozess noch nicht den gewünschten Endzustand auf. Dazu sind im Anschluss an Verfahren wie der laserbasierten Pulverbettfusion (PBF-LB) weitere Bearbeitungsschritte erforderlich. Additiv gefertigte Komponenten verfügen vielfach über unterschiedliche Funktionsflächen und komplexe dreidimensionale Oberflächen, weshalb der Einsatz mehrerer Verfahren je Bauteil erforderlich ist. Einzelne Schritte umfassen zum Beispiel die Reduktion der Oberflächenrauheit, die Entfernung von Stützstrukturen oder die Endbearbeitung von Innenkonturen. Die Auswahl der einzusetzenden Verfahren muss je Bauteil und Anforderungen individuell ablaufen.
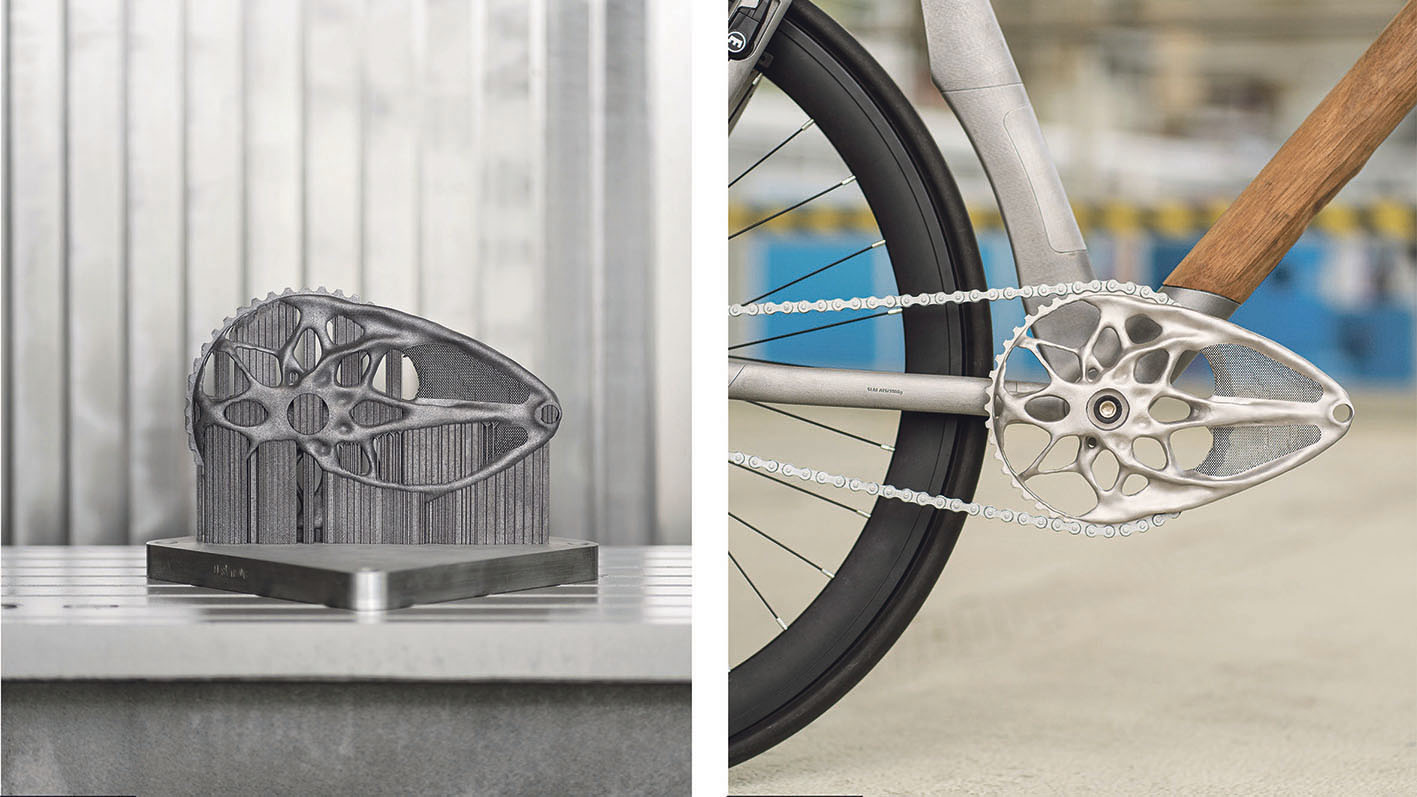
Bild 1. Erforderliches Post-Processing an einer additiv gefertigten Fahrradkurbel: Das Bauteil nach dem additiven Fertigungsprozess mit Stützstrukturen (links) und nach dem Post-Processing (rechts).
Foto: Larissa Klassen
Aktuell steht ein umfassendes Portfolio an Post-Processing-Verfahren bereit, welche jedoch durch signifikante Unterschiede hinsichtlich der Fähigkeiten und Restriktionen für verschiedene Bauteilgeometrien, der Kosten k und der erzielbaren Bauteilqualität gekennzeichnet sind. Die Diversität der Anforderungen an Oberflächen und Formgenauigkeiten sowie die Vielzahl an Verfahren erschwert es den Anwendern, eine optimale Prozesskette auszuwählen.
Die effiziente Herstellung von Bauteilen mit einer Losgröße 1 ist von der Industrie gewünscht, sie muss jedoch ebenfalls durch geeignete Endbearbeitungstechnologien ergänzt werden. Klassische weggesteuerte Verfahren wie zum Beispiel das Fräsen sind aufgrund des erheblichen Zeit- und Kostenfaktors für die Programmierung der Bahnplanung nicht geeignet. Demnach bieten kraftgeregelte Verfahren wie zum Beispiel das Gleitspanen, welche keine komplexe, geometrieabhängige Programmierung benötigen, einen großen Vorteil für additiv gefertigte Bauteile.
Effizienzsteigerung durch eine optimale Technologiekette
Im Rahmen des von der Investitionsbank Berlin IBB geförderten und durch die Europäische Union mit Mitteln des Europäischen Fonds für Regionale Entwicklung kofinanzierten Projekts „Pro Fit HTA Phase II“ entwickelt das Fraunhofer IPK eine intelligente Technologiekette und innovative kraftgeregelte Verfahren für das Post-Processing additiv gefertigter Bauteile. Ein Kernaspekt ist die Integration der Endbearbeitung in die digitale Wertschöpfungskette. Die Technologiekette stellt ein Werkzeug zur automatisierten Ableitung bauteilspezifischer, effizienter Prozessketten zur Endbearbeitung dar. Eine Prozessoptimierung zur gezielten Reduktion der Anzahl erforderlicher Bearbeitungsverfahren je Bauteil führt zu einer gesteigerten Produktivität und einer Senkung des ökologischen Fußabdruckes. Es wird erforscht, wie durch den Einsatz von Künstlicher Intelligenz (KI) zur Vorhersage von Bearbeitungsparametern die Effizienz gesteigert und Durchlaufzeiten verkürzt werden können. Die Entwicklung automatisierter kraftgeregelter Bearbeitungsverfahren trägt zur Verringerung von Ausschuss und zur verbesserten Wirtschaftlichkeit bei.
Die intelligente Technologiekette bildet – wie in Bild 2 dargestellt – den zentralen Baustein des Projekts, und führt die Orchestrierung des Post-Processing-Ablaufes durch. Das Ziel ist die Zuweisung einer effizienten Abfolge an Endbearbeitungsschritten durch die intelligente Technologiekette, basierend auf der individuellen Geometrie.
Analyse und Segmentierung der Bauteilmodelle
Zunächst erfolgt dazu eine Analyse der Werkstücke auf Basis von Messdaten, Informationen aus dem Fertigungsprozess und der Bauteilgeometrie, beispielsweise anhand der CAD-Daten. Das Bauteil und alle verfügbaren Daten werden in einen digitalen Zwilling überführt, welcher die Eigenschaften und Anforderungen der intelligenten Technologiekette zugänglich macht.
Eine Herausforderung in der Entwicklung eines bauteilspezifischen Post-Processing liegt in der hohen Variantenvielfalt und Komplexität additiv gefertigter Bauteile. Dies wird durch eine Segmentierung der digitalen Bauteilmodelle in allgemeine Features adressiert. Dabei wird die Erstellung der Prozessketten zunächst in komplexitätsreduzierte Einzelaufgaben zerlegt. In einem ersten Schritt wurden durch Forschende generalisierte Features der Bauteilgeometrie, wie Kanten, Nuten oder ebene, konkave und konvexe Flächen identifiziert. Im zweiten Schritt übernimmt ein digitales Werkzeug die automatisierte Erkennung der Bauteilfeatures. Dazu wurde ein Neuronales Netzwerk trainiert, sodass der Algorithmus die Features direkt aus den digitalen Bauteildaten ableiten kann.
In Bild 3 ist ein verwendetes Demonstrator-Bauteil mit mehreren Features abgebildet. Durch den direkten Zugriff auf Messdaten wird die Ist-Geometrie den Soll-Daten gegenübergestellt. Die intelligente Technologiekette erstellt daraus Bearbeitungsaufgaben für die einzelnen Features, zu welchen im nächsten Schritt effiziente Lösungen ermittelt werden.
Prozessoptimierung unter Einsatz von Künstlicher Intelligenz
Für die Prozessoptimierung müssen der intelligenten Technologiekette die Fähigkeiten und Restriktionen der Bearbeitungsverfahren vorliegen. Die intelligente Technologiekette greift auf einen digitalen Verfahrens-Steckbrief zurück, in welchem weiterhin Informationen zu den verfügbaren Werkzeugmaschinen und verfügbaren Bereichen der Prozessparameter hinterlegt sind. Basierend auf diesen Informationen erfolgt eine Analyse von Bearbeitungsverfahren als Lösungsmöglichkeiten der zuvor erstellten Bearbeitungsaufgaben für die Features. Die Besonderheit: Ein auf Künstlicher Intelligenz (KI) basierendes System gibt Prognosen zu den Bearbeitungsparametern, den Kosten kB und der Bearbeitungsdauer tB der möglichen Bearbeitungsverfahren.
Zu jedem Feature des Bauteils liegen nun ein oder mehrere Post-Processing-Verfahren vor, welche zum gewünschten Endzustand führen können. Aus der Menge der Endbearbeitungsschritte je Feature muss die Prozesskette für das gesamte Bauteil abgeleitet werden. Ein essenzieller Schritt ist die Prüfung möglicher Inkompatibilitäten der Bearbeitungsverfahren mit einzelnen Features der Bauteile. In Bild 3 sind dünne Stege als Beispiel aufgeführt, welche durch hohe Bearbeitungskräfte FB beschädigt werden. Weist ein Bauteil schmale Stege auf, ist die Bearbeitung auch anderer Features dieses Bauteils mit Verfahren wie dem Gleitschleifen nicht kompatibel. Innerhalb der intelligenten Technologiekette erfolgt eine regelbasierte Prüfung der Kompatibilität der Post-Processing-Schritte mit den vorhandenen Bauteilfeatures. Die dazu erforderliche Wissensbasis zur Kompatibilität von Features und Bearbeitungsverfahren wird derzeit in Bearbeitungsversuchen an Demonstrator-Bauteilen erforscht.
Nach Abschluss der regelbasierten Kompatibilitätsprüfung steht eine Auswahl verschiedener Prozessketten für die Endbearbeitung der Bauteile bereit. Doch welche dieser Prozessketten bietet die höchste Effizienz und Wirtschaftlichkeit? Im Rahmen einer Prozesskettenoptimierung werden zusätzliche Daten wie die Energiekosten kE, Materialkosten kM, Bearbeitungsdauer tB und Rüstdauer tR ausgewertet. Die gewünschten Kriterien zur Bestimmung der optimalen Prozesskette, beispielsweise Gesamtkosten kGes oder die Gesamtbearbeitungsdauer tGes können je nach Bedarf angepasst werden und ermöglichen somit einen flexiblen Einsatz der intelligenten Technologiekette.
Implementierung der intelligenten Technologiekette in die Fertigungsumgebung
Die Erprobung der intelligenten Technologiekette erfolgt anhand von Bearbeitungsversuchen additiv gefertigter Bauteile. Am Produktionstechnischen Zentrum (PTZ) Berlin erfolgt derzeit der Aufbau von Versuchsständen durch das Fraunhofer-Institut für Produktionsanlagen und Konstruktionstechnik IPK und das Institut für Werkzeugmaschinen und Fabrikbetrieb IWF der TU Berlin. Zum Post-Processing stehen vollintegrierte, automatisierte Verfahren sowie teilintegrierte Verfahren zur Verfügung.
Vollintegrierte Verfahren ermöglichen eine automatisierte Bearbeitung der AM-Werkstücke. Das Werkstückhandling durch einen Industrieroboter bietet die flexible Handhabung der Bauteile in den einzelnen Arbeitsschritten. Vollintegriert bedeutet, dass die Bahnplanung des Roboters sowie die Parameter der Bearbeitungsanlagen direkt über die intelligente Technologiekette gesteuert werden. Die Geräte sind dazu über Schnittstellen vernetzt und zentral ansteuerbar. Bild 4 zeigt die roboterbasierte Bearbeitung eines Demonstrator-Bauteils, welches über einen Greifer automatisiert aufgenommen und in die Bearbeitungszelle geführt wird.
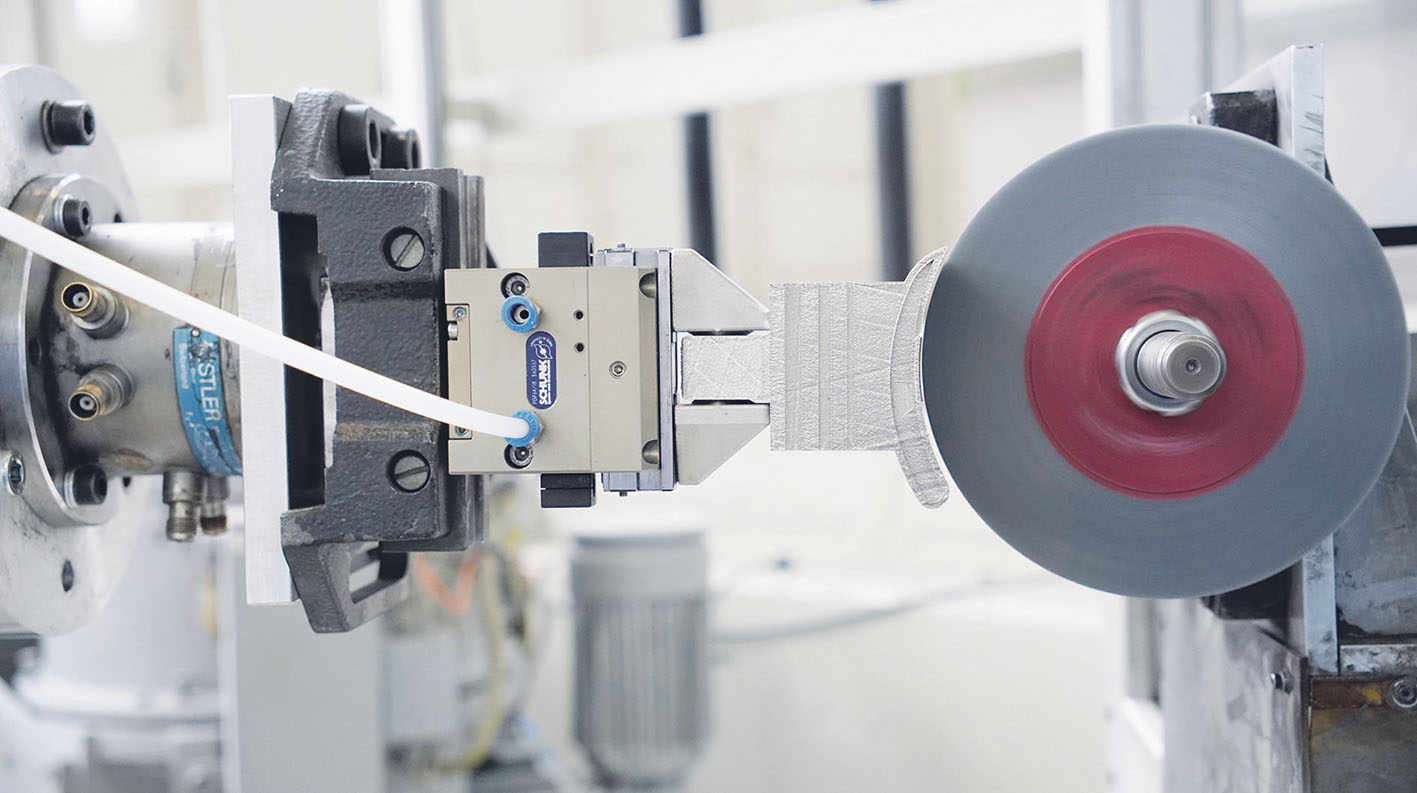
Bild 4. Ein Industrieroboter übernimmt das Bauteilhandling. Die Bauteile werden an verschiedenen Versuchsständen bearbeitet, im Bild gezeigt ist das Bürstspanen.
Foto: Gero Esser
Manche Bearbeitungsverfahren sind jedoch nicht vollständig automatisierbar oder räumlich getrennt, beispielsweise aufgrund besonderer Anforderungen an die Umgebung oder einer komplexen Handhabung. Für diese Bearbeitungsverfahren bietet die intelligente Technologiekette einen teilintegrierten Ansatz. Anhand der Prozesskette werden zu den einzelnen Arbeitsschritten detaillierte Arbeitsanweisungen erstellt. Über eine intuitive Benutzeroberfläche werden diese Arbeitsanweisungen den Mitarbeitenden bereitgestellt, sodass eine fehlerfreie und präzise Umsetzung sichergestellt ist.
Am PTZ werden die Bearbeitungsverfahren Gleitschleifen, Bürsten, Bandschleifen und Meißeln als vollintegrierte Versuchsstände aufgebaut. Die Verfahren Strömungsschleifen und Strahlspanen werden teilintegriert ausgeführt.
Prognose und Parametrisierung der Verfahren
Teil der intelligenten Technologiekette ist eine Prognose geeigneter Prozessparameter für die Bearbeitungsverfahren, sowie eine kraftgeregelte Prozessführung. Allerdings fehlen derzeit allgemeingültige Modelle zur Vorhersage und Parametrisierung der Post-Processing-Verfahren. Die zur Entwicklung erforderliche einheitliche Prozessdatenbasis wird derzeit durch umfassende Untersuchungen der Bearbeitungsverfahren an Demonstratorbauteilen erarbeitet. Diese weisen eine Vielzahl von Bauteilmerkmalen auf, welche für AM-Bauteile typisch sind. Die sequenzielle Anwendung verschiedener Verfahren wird dabei im Besonderen betrachtet. Beispielsweise wird analysiert, ob die Kombination von Strahlspanen, Bürsten und Gleitschleifen im Vergleich zur alleinigen Anwendung von Gleitschleifen zur Erzielung der gewünschten Rauheit in Bezug auf Prozessdauer tP und Kosten kP Vorteile bietet. Für die kraftgeregelte Bearbeitung wird ein Industrieroboter eingesetzt, welcher mit einer Werkstückspannvorrichtung mit integrierter Kraftmessplattform ausgerüstet ist. Neben der Entwicklung von Algorithmen zur automatisierten Bahnplanung der kraftgeregelten Bearbeitung wird der Einfluss der Bearbeitungskraft FB in Versuchsreihen analysiert. Die Daten und Algorithmen fließen in die intelligente Technologiekette ein, und ermöglichen die automatisierte Durchführung der vollintegrierten Bearbeitungsverfahren.
Fazit und Weiterentwicklung der intelligenten Technologiekette
Mit der intelligenten Technologiekette wird eine in den digitalen Produktionsprozess integrierbare Lösung zur Effizienzsteigerung und Automatisierung des Post-Processing additiv gefertigter Metallbauteile adressiert. Die Grundlagenuntersuchungen zur Bearbeitung geometrisch komplexer Werkstücke tragen zur Entwicklung einer Wissensbasis bei, die einen effizienten Einsatz der Endbearbeitungsverfahren ermöglicht. Für die nahe Zukunft ist eine Erprobung der intelligenten Technologiekette anhand der Bearbeitung von Demonstrator-Bauteilen geplant. Anhand verschiedener Bauteilgeometrien wird die intelligente Technologiekette in einem realitätsgetreuen Anwendungsszenario erprobt und für den Einsatz in der industriellen Serienfertigung weiterentwickelt.
Das Projekt „Pro FIT HTA Phase II“ wird kofinanziert von der Europäischen Union durch den Europäischen Fonds für regionale Entwicklung (EFRE).
Literatur
- Baumers, M.; Beltrametti, L.; Gasparre, A.; Hague, R.: Informing additive manufacturing technology adoption: total cost and the impact of capacity utilisation. International Journal of Production Research 55 (2017), 23, 6957–6970. DOI: https://doi.org/10.1080/00207543.2017.1334978.
Das könnte Sie auch interessieren:
Metallischer 3D-Druck von und für die Stahlindustrie
Fertigung von Hybridbauteilen – additiv und robotergestützt
Die gesamte Prozesskette des Additive Manufacturing im Blick
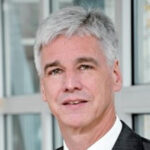
Prof. Dr. h. c. Dr.-Ing. Eckart Uhlmann, Jahrgang 1958, ist Leiter des Fraunhofer-Instituts für Produktionsanlagen und Konstruktionstechnik IPK sowie Leiter des Fachgebiets Werkzeugmaschinen und Fertigungstechnik am Institut für Werkzeugmaschinen und Fabrikbetrieb (IWF) der TU Berlin im Produktionstechnischen Zentrum Berlin. Foto: IPK
Prof. Dr.-Ing. Julian Polte, Jahrgang 1985, ist Leiter des Bereichs Produktionssysteme des Fraunhofer IPK sowie Leiter des Fachgebiets Maschinen und Technologien für die Additive Präzisionsfertigung metallischer Bauteile am IWF der TU Berlin.
Tobias Neuwald, M.Sc., Jahrgang 1993, ist Leiter der Abteilung Fertigungstechnologien des Fraunhofer IPK.
Gero Esser, M. Sc., Jahrgang 1997, ist wissenschaftlicher Mitarbeiter am Fraunhofer IPK. Sein Schwerpunktthema ist die Additive Fertigung metallischer Bauteile.