Laser – unersetzliche Helfer für die Elektromobilität
Laser sind entlang der gesamten Prozesskette der Batteriefertigung im Einsatz. Inzwischen wird mehr als jeder zweite Euro beim Marktführer aus Ditzingen im Bereich Elektromobilität verdient – was leistet die Technik im Einzelnen?
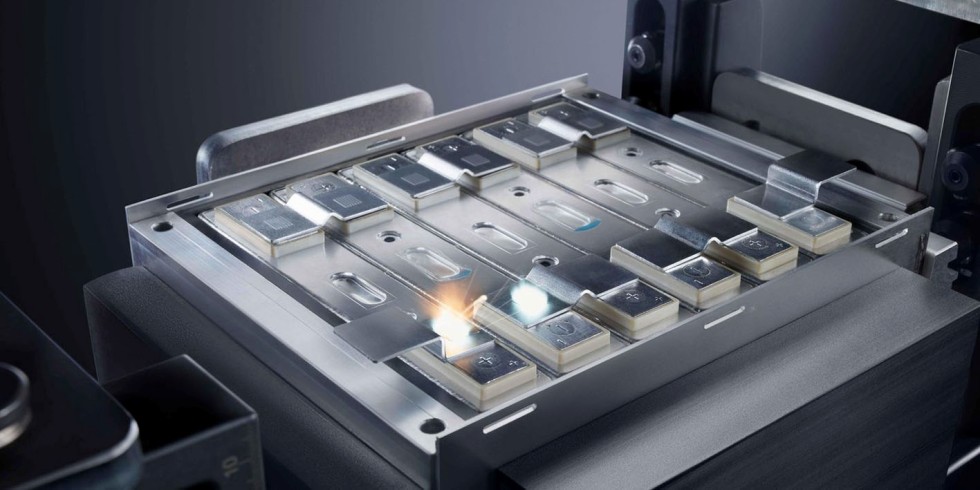
Durch das Laserschweißen wird eine elektrisch hoch leitfähige und mechanisch stark belastbare Busverbindung möglich.
Foto:Trumpf
Das Hochtechnologieunternehmen Trumpf bietet industrielle Lasertechnik und viele „smarte Technologien“ für die effiziente Fertigung von Batterien, ohne die in der Elektromobilität „nichts fährt“. Im Rahmen der Fachmesse „Battery Show“ in Stuttgart, die vom 30. November bis zum 2. Dezember 2021 ausgetragen wird, präsentiert das Unternehmen Lösungen, mit denen Hersteller die Komponenten entlang der gesamten Prozesskette der Batterieerzeugung effizient produzieren können.
Die Battery Show Europe bringt gemeinsam mit der „Electric & Hybrid Vehicle Technology Expo“ mehr als 10.500 Branchenexperten und mehr als 500 führende Zulieferer zusammen. Dies gibt den Unternehmen die Möglichkeit, sich mit wichtigen Akteuren der gesamten Lieferkette für Batterie-, Elektro- und Hybridtechnologie zu vernetzen und ihre Ideen zu diskutieren.
Passende Technologien für viele sensible Fertigungsschritte
Zur Prozesskette der Batteriefertigung gehören beispielsweise Verfahren zum Schneiden, Schweißen und Trocknen von Batteriefolien. Des Weiteren zählen das Verbinden von einzelnen Batteriezellen zu Batteriemodulen dazu, ebenso wie das Dichtschweißen von gesamten Batteriewannen. „Die Produktion von Lithium-Ionen-Batterien ist ein sehr aufwendiger und sensibler Prozess. Denn diese wichtigen Bauteile müssen den hohen Anforderungen der Automobilindustrie genügen – zum Beispiel hinsichtlich ihrer Sicherheit und Lebensdauer. Es gibt kein anderes Werkzeug als den Laser, um alle die hochkomplexen Anforderungen mit Blick auf Effizienz und Wirtschaftlichkeit zu erfüllen“, erläutert Johannes Bührle, Leiter Automotive Industry bei Trumpf.
Boomende Elektromobilität sorgt für volle Auftragsbücher
Das Geschäft mit der Elektromobilität läuft auf Hochtouren – mittlerweile beliefert das Unternehmen alle großen Batteriehersteller mit Lasertechnik. Im Vergleich zum Stand vor drei Jahren haben sich die Produktionskapazitäten ebenso wie die Nachfrage mehr als verdreifacht. „Wir werden allein im ersten Halbjahr 2022 mehr als 500 Laser an Batteriehersteller ausliefern. Bereits mehr als jeder zweite Euro, den wir mit der Automobilindustrie umsetzen, kam im vergangenen Geschäftsjahr aus der ,elektrifizierten Welt‘. Das entspricht einem dreistelligen Millionenbetrag“, so Bührle weiter.
Schnellere Produktion gelingt mit weniger Energie
Eine Batterie ist komplex und mehrstufig aufgebaut. Sie besteht aus drei wesentlichen Komponenten: der Batteriezelle, dem Batteriemodul und dem Batteriepack. Die Batteriezellen setzen sich aus mehreren hauchdünnen, beschichteten Trägerfolien zusammen. Diese bestehen aus Kupfer (Anode) und Aluminium (Kathode) – den sogenannten Elektrodenfolien.
Bevor die beschichteten Folien zu einer Zelle verbunden werden, müssen sie trocknen. Konventionelle Verfahren wie etwa Trocknungsöfen nehmen bisher in den Fabriken viel Platz ein. Der Ditzinger Technologieführer hat deshalb die spezielle „VCSEL“-Technik entwickelt. Bei der VCSEL (vertical-cavity surface-emitting laser)-Laserdiode wird das Licht senkrecht zur Ebene des Halbleiterchips abgestrahlt, im Gegensatz zur kantenemittierenden Laserdiode, bei der das Licht an einer oder zwei Flanken des Chips austritt. Mit diesem innovativen Verfahren ist der Anwender in der Lage, große Flächen sehr schnell zu bestrahlen (respektive zu erwärmen) und somit zu trocknen – und das mit wesentlich weniger Energie, als wenn konventionellen Trocknungsöfen zum Einsatz kämen.
Effizient Kupfer schweißen mit grünem Laser
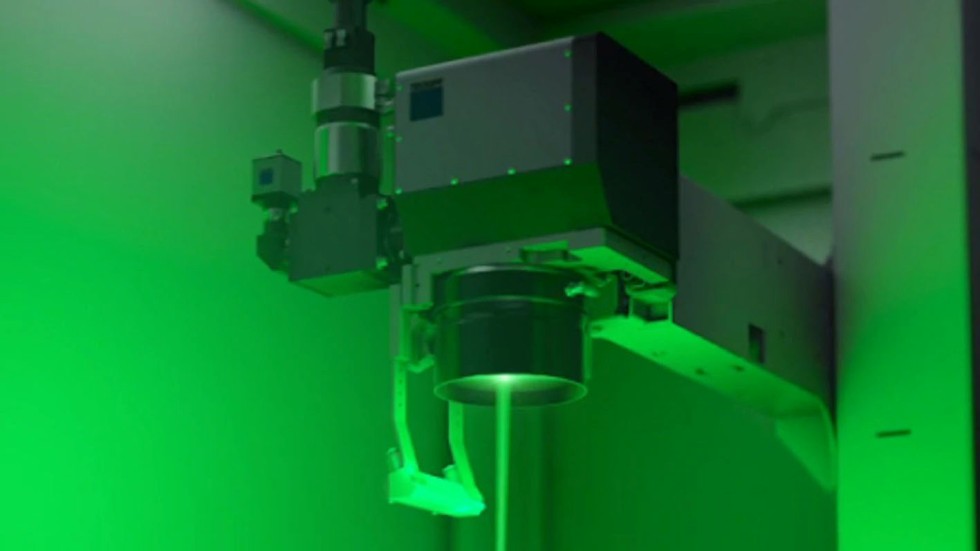
Erst die Nutzung des „grünen“ Laserlichts machte es rmöglich, Kupferfolien für Batteriezellen effizient und prozesssicher zu schweißen.
Foto:Trumpf
Im nächsten Schritt gilt es, die Elektrodenfolien zuzuschneiden, die zwischen 6 Mikrometer und 14 Mikrometer dünn sind. Hierfür eignen sich Kurzpulslaser am besten – zum Beispiel jene aus der Produktreihe „TruPulse nano“. In Kombination mit einer Scanneroptik bewegen sich diese Laser schnell über die Folien und bringen sie effizient in die benötigte Form.
Damit aus den beschichteten Kupfer- und Aluminiumfolien Zellen werden, müssen sie – beispielsweise ebenfalls per Laser – kontaktiert werden. Weil Kupfer aber hochreflektierend ist, lässt es sich mit gängigen Industrielasern nur sehr eingeschränkt bearbeiten. Deshalb wurde ein spezieller „TruDisk“-Scheibenlaser mit kürzerer Wellenlänge im sichtbaren grünen Lichtspektrum entwickelt. Das „grüne“ Laserlicht macht es möglich, Kupferfolien für Batteriezellen effizient und prozesssicher zu schweißen. Ein Scheibenlaser ist ein Festkörperlaser, bei dem das aktive Medium in Scheibenform vorliegt. Die für das Entstehen der Laserstrahlung notwendige Energie wird durch den mehrfachen Durchgang einer Pumpstrahlung durch die Laserscheibe erzeugt. Der speziell für die Aufgabe des Kontaktierens ausgelegte Laser gewährleistet dank grüner Wellenlänge Spritzerfreiheit beim Kupferschweißen.
Ein Batteriemodul besteht üblicherweise aus vielen Einzelzellen. Diese Zellen werden mit sogenannten „Busbars“ aus Kupfer oder Aluminium miteinander kontaktiert. Die Materialkombinationen und Blechdicken variieren je nach Zell- und Anwendungstyp. Somit kommen hierfür die unterschiedlichsten Lasertypen (hinsichtlich der Wellenlänge, Strahlqualität und Leistung) zum Einsatz – immer in Verbindung mit Scanneroptiken. Letztere positionieren den Laser automatisch an der korrekten Stelle und fahren dann die gewünschte Schweißgeometrie ab.
Dichte Schweißnähte – sichere Batteriepacks
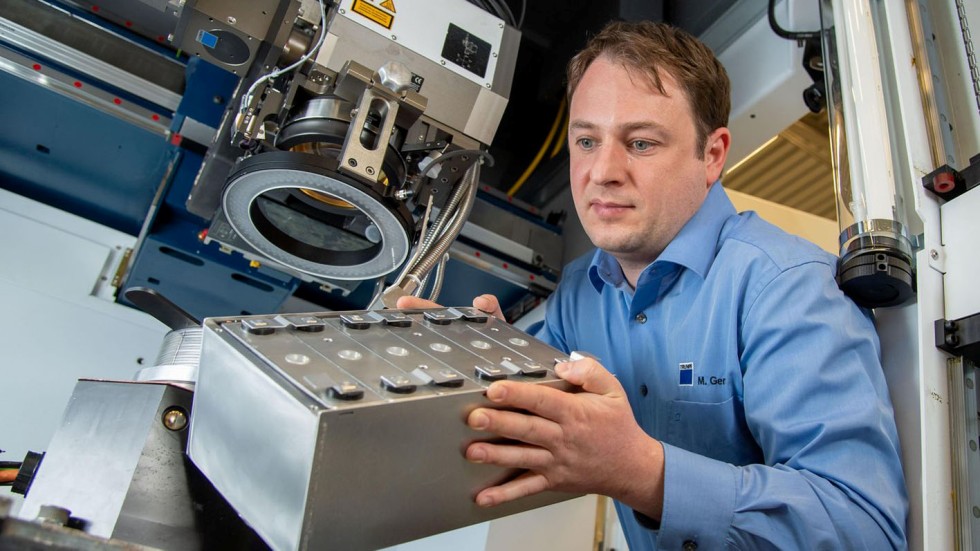
Mitarbeiter mit einem kompletten Batteriemodul: Dieses besteht üblicherweise aus vielen Einzelzellen. Diese werden mit „Busbars“ aus Kupfer oder Aluminum miteinander kontaktiert.
Foto:Trumpf
Als „Batteriepack“ wird schließlich das komplette Batteriesystem inklusive Leistungselektronik und Kühlmanagement bezeichnet, welches letztendlich in die Elektrofahrzeuge eingebaut wird und diesen zu ihrer Leistung verhilft. Der Pack muss absolut dicht sein: Denn es dürfen keinesfalls Chemikalien austreten, weder im Normalbetrieb noch bei einem Crash des Fahrzeugs. Um den Sicherheitsanforderungen gerecht zu werden, schweißen Hersteller die Wannen, die aus Stahl- oder Aluminiumblechen bestehen, luftdicht zusammen. Mit Hilfe des Scheibenlasers gelingt es, diesen besonders hohen Anforderungen hochproduktiv gerecht zu werden. Somit ist die Prozesskette der Batteriefertigung geschlossen – und für jeden einzelnen Schritt steht die passende Technologie zur Verfügung.
Das könnte Sie auch interessieren:
Hochpräzisions-Bearbeitung mit „kaltem“ Wasser-Laser
Innovative Lasermikrobearbeitung bewährt sich in der Sensor-Fertigung
Schwarmautomatisierung sorgt für flexible Produktion