Neuartige Sensortechnologien überwachen Fertigungsprozesse
Automatisierungslösungen für Fertigungsprozesse werden in der Industrie immer wichtiger. Die zuverlässige Erfassung des aktuellen Prozesszustands spielt dabei eine zentrale Rolle. Sie setzt zugleich sensitive wie auch robuste Sensortechnologien voraus.
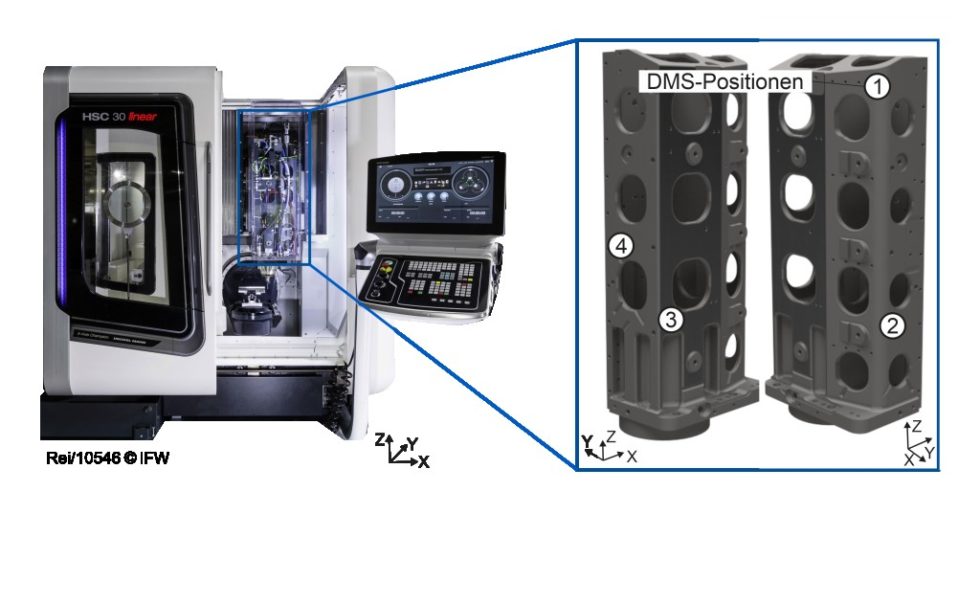
Prozessüberwachung an Werkzeugmaschinen: Umgesetzte Sensorpositionen am Spindelschlitten des 5-Achs-Bearbeitungszentrum DMG Mori „HSC 30“.
Foto: IFW
Halbleiter-Dehnungsmessstreifen (DMS), die in der Maschinenstruktur von Werkzeugmaschinen integriert sind, stellen eine kostengünstige Alternative zu bisherigen Lösungen dar: Ohne Steifigkeits- und Leistungsverluste erlauben sie eine präzisere Erfassung der Zustandsgrößen als herkömmliche Sensortechnologien.
Industrie 4.0 erfordert umfangreichere Datenerfassung
Im Zuge der Industrie 4.0 wird perspektivisch die vollautonome Produktion angestrebt [1]. Die Überwachung von Prozesszuständen ist dabei ein zentraler Bestandteil. Nur mithilfe einer robusten und sensitiven Prozessüberwachung können intelligente Systeme autonom auf Prozessveränderungen reagieren, um gleichzeitig eine hohe Produktivität und Bauteilqualität zu gewährleisten.
Die Prozesskraft eignet sich aufgrund ihrer Sensitivität gegenüber Prozessveränderungen besonders gut zur Überwachung des Prozesszustands. Konventionelle Kraftmessplattformen zur Erfassung der Prozesskraft sind kostenintensiv und beeinflussen den Prozess, bedingt durch die Reduzierung der Steifigkeit und Einschränkung des Arbeitsraums. Durch die Integration von Sensorik direkt in die Maschinenkomponenten wird diese Prozessbeeinflussung vermieden.
Strukturintegrierte Kraftmessung
Die im Prozess wirkende Kraft führt zu einer Strukturdehnung, die mithilfe von Dehnungsmessstreifen (DMS) an den Maschinenkomponenten erfasst werden kann. Mit zunehmender Steifigkeit der Komponente sinkt die Strukturdehnung, sodass die mögliche Auflösung der Prozesskraft verringert wird. Dennoch ist es dem Institut für Fertigungstechnik und Werkzeugmaschinen (IFW) gelungen, eine strukturintegrierte Kraftmessung an dem Spindelschlitten eines 5-Achs-Bearbeitungszentrums DMG Mori „HSC 30“ umzusetzen. Hierbei konnte eine Messgenauigkeit der Prozesskraft zwischen 40 N und 100 N in die einzelnen Richtungen erzielt werden.
Halbleiter-DMS bieten im Gegensatz zu herkömmlichen Metall-DMS eine deutlich bessere Sensitivität, wodurch sich ein hohes Potential für die strukturintegrierte Kraftmessung in Maschinenkomponenten ergibt. Der k-Faktor ist ein Maß für die Sensitivität der DMS. Bei Metall-DMS ist ein k-Faktor von 2 üblich, Halbleiter-DMS dagegen sind mit einem bis zu 100-fache höheren k-Faktor entsprechend 100-fach sensitiver [2].
Halbleiter-DMS für sensorischen Spindelschlitten
Als nicht-rotierende Komponente und durch die Prozessnähe zeichnet sich der Spindelschlitten bei Fräsmaschinen für eine Sensorintegration besonders aus. Am IFW wurden die Metall-DMS am Spindelschlitten der HSC 30 daher durch Halbleiter-DMS ergänzt. Aufgrund der kompakten Bauweise verfügt der Spindelschlitten der HSC 30 über eine statische Steifigkeit von 200 – 3000 N/m in Abhängigkeit von der Messrichtung [3].
Am Spindelschlitten wurden insgesamt vier Halbleiter-DMS-Vollbrücken an passenden Positionen appliziert. Diese wurden durch statische und dynamische Simulationen so ausgewählt, dass sie eine hohe Nachgiebigkeit haben und nicht auf Schwingungsknoten liegen. Die Anordnung als Vollbrücke reduziert thermische Einflüsse.
Die Signale der Halbleiter-DMS werden mit einer Abtastrate von fAbt. = 20 kHz aufgezeichnet und mit einem analogen Tiefpassfilter mit einer Grenzfrequenz von fGrenz = 5 kHz gefiltert. Durch die vergleichsweise hohe Abtastrate können sowohl das statische als auch des dynamische Prozessverhalten erfasst werden.
In Bild 1 ist das Signal des Halbleiter-DMS an Position 2 für die Fräsbearbeitung von C45 zu sehen. Die Darstellung des Signals im Polar-Koordinatensystem des Werkzeugs erlaubt eine optische Differenzierung der einzelnen Werkzeugschneiden. Schäden am Werkzeug, beispielsweise der Ausbruch einzelner Schneiden, werden in dieser Darstellung sichtbar.
Bild 2 zeigt den Signalverlauf des DMS an Position 4 bei einem Rampenfräsprozess. Oberhalb des Signalverlaufs im Zeitbereich sind die markierten Signalabschnitte im Frequenzbereich dargestellt. Durch die zunehmende Schnitttiefe verändert sich auch die Prozessstabilität.
Ratterdetektion mit dem Spindelschlitten
Zu Beginn des Prozesses im Bereich a) ist der Prozess noch stabil. In Bereich b) geht der stabile Prozess in einen instabilen Prozess über. Während in der Signalamplitude im Zeitbereich noch keine sichtbaren Veränderungen auftreten, zeichnet sich im Frequenzbereich bereits die Ratterfrequenz bei 2 kHz als dominante Frequenz ab. In Bereich c) sind die Ratterschwingungen durch die hohe Signalamplitude auch im Zeitbereich ersichtlich und auf der Werkstückoberfläche durch deutliche Rattermarken zu erkennen.
Die Integration von Dehnungsmessstreifen in den Spindelschlitten einer Werkzeugmaschine setzt eine individuelle Auslegung der Sensorpositionen voraus. Dagegen ist die Übertragung der strukturintegrierten Kraftmessung auf standardisierte Führungswagen der Profilschienenführung einer universellen Umsetzung gleichzusetzen. Nach einer einmaligen Auslegung sind die Führungswagen unabhängig von der Baugröße oder der Werkzeugmaschine einsetzbar.
Erfolgreiche Rekonstruktion der Prozesskraft
In Bild 3 ist die Kraftmessung der strukturintegrierten Sensorik der Führungswagen im Vergleich zu einer Referenzkraftmessung mittels Kraftmessplattform dargestellt. Für die Kraftberechnung werden die Sensorsignale der vier Führungswagen nach einer Tiefpassfilterung mit einer Kalibriermatrix fusioniert.
Der erste Prototyp (links) wurde mit herkömmlichen metallischen DMS umgesetzt. Zu erkennen ist das unzureichende Folgeverhalten der beiden Kraftrichtungen (Fx, Fy) mit dem Referenzsignal FRef eines kommerziellen Kraftsensors. Die Kraftauflösung ist durch die unzureichende Sensitivität der metallischen DMS auf ± 75 N begrenzt. Aus diesem Grund wurde ein zweiter Prototyp (rechts) mit Halbleiter-DMS umgesetzt. Deutlich zu erkennen ist die damit erzielte hochgenaue Abbildung von FRef. Dies gestattet erstmals eine Prozessüberwachung der Prozesskraft mit einer standardisierten und zudem hochsteifen Maschinenkomponente.
In Bild 4 sind vier DMS-Signale eines Führungswagens währen einer Verfahrbewegung mit einer Vorschubgeschwindigkeit vf = 1200 mm/min dargestellt. Das Signal wurde aus dem Zeitsignal in den räumlichen Frequenzbereich transferiert. Somit ist eine Zuordnung der einzelnen Frequenzamplituden mit geometrischen Randbedingungen möglich. In dem Signal sind die Anregung der Wälzkörper (Wellenlänge λ = 10 mm) sowie Bohrungen in den Profilschienenführungen (Wellenlänge λ = 52,5 mm) erkennbar. Dies kann genutzt werden, um den Zustand des Führungswagens zu überwachen. So ist beispielsweise ein verklemmter Span im Wälzkontakt durch eine Signalüberhöhung direkt ersichtlich. Weitere Untersuchungen ergaben, dass sich auch eine Fehlausrichtung der Linearschiene eindeutig im Messsignal widerspiegelt [4].
Prozessverhalten mit hoher Signalgüte erfassbar
Sensorische Maschinenkomponenten bieten ein hohes Potential zur Prozess- und Zustandsüberwachung. Durch den Einsatz von Halbleiter-DMS können selbst hochsteife Maschinenkomponenten wie Spindelschlitten und Führungswagen zur prozesssicheren Bestimmung der Prozesskräfte herangezogen werden. Gezeigt wurde, dass durch die strukturintegrierten Halbleiter-DMS das statische und das dynamische Prozessverhalten mit einer hohen Signalgüte gemessen werden können. Dies erlaubt die präzise Erfassung von Prozessinformationen, ohne in den Prozess einzugreifen, die Struktur zu schwächen oder den Arbeitsraum einzugrenzen. Somit bildet dies die Grundlage für eine Vollautomatisierung der Produktion im Rahmen der „Industrie 4.0“.
Die Autoren danken der Deutschen Forschungsgemeinschaft (DFG) für die Unterstützung des Projekts Intelligente Werkzeugmaschine (Projektnummer: 385522239).
Literatur
- Behrens B-A; Groche, P; Krüger, J; Wulfsberg, JP: WGP-Standpunkt Industriearbeitsplatz 2025. WGP Wissenschaftliche Gesellschaft für Produktionstechnik e.V., Frankfurt/Main, 2018.
- Keil, S: Dehnungsmessstreifen. Berlin: Springer-Verlag, 2. Auf., 2017.
- Boujnah, H: Kraftsensitiver Spindelschlitten zur online Detektion und Kompensation der Werkzeugabdrängung in der Fräsbearbeitung. Dissertation, Universität Hannover. Band 2019, 6: Berichte aus dem IFW. PZH Produktionstechn. Zentrum, Garbsen, 2019.
- Denkena, B; Park, J-K; Bergmann, B; Schreiber, P.: Force sensing linear rolling guides. Euspen‘s 18th International Conference & Exhibition, Venice/I, 2018, S. 4–5.
Das könnte Sie auch interessieren:
Intelligente Fertigungszelle erfüllt strenge Medizintechnik-Richtlinien
Präzision durch adaptive Produktion
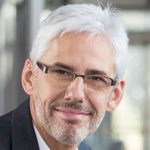
Prof. Dr.-Ing. Berend Denkena, Jahrgang 1959, leitet seit 2001 das Institut für Fertigungstechnik und Werkzeugmaschinen (IFW) am Produktionstechnischen Zentrum der Leibniz Universität Hannover.
Dr.-Ing. Benjamin Bergmann, Jahrgang 1985, studierte Maschinenbau an der Leibniz Universität Hannover und ist seit 2017 Leiter des Bereichs Maschinen und Steuerungen am IFW.
Svenja Reimer, M. Sc., Jahrgang 1993, studierte Mathematik an der Universität Stuttgart und ist seit 2020 Leiterin der Abteilung Prozessüberwachung und -regelung am IFW.
Alexander Schmidt, M. Sc., Jahrgang 1990, studierte Maschinenbau an der Leibniz Universität Hannover und ist seit 2015 wissenschaftlicher Mitarbeiter am IFW.