Perfekte Zähne für hohe Drehmomente
Save costs – take the best: Dies gilt bei einem Handhabungstechnik-Spezialisten nicht nur für die eigenen Produkte, sondern auch für die dafür genutzte Zerspanungstechnik, wie das vorgestellte Erfolgsbeispiel anschaulich zeigt.
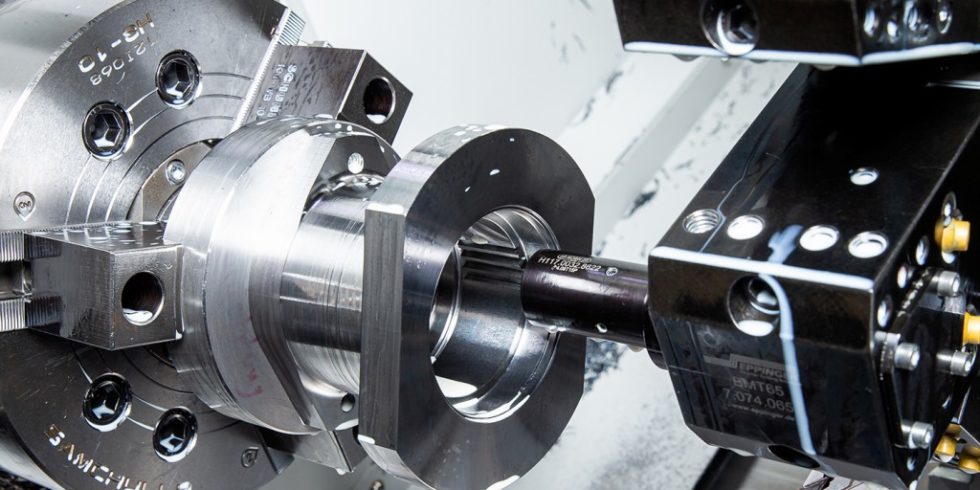
Spezialgebiet von Jäger Handling sind ergonomische, industrielle Schraubtechnikmontagesysteme für die Automobilindustrie. Dabei sind viele Verzahnungen herzustellen - im Bild ist das Stoßen der Innenverzahnung eines Planetenträgers zu sehen.
Foto: Horn/Sauermann
Nach dem bewährten Motto realisiert die Firma Jäger Handling unterschiedlichste Aufgabenstellungen für handgeführte und teilautomatisierte Handlingsysteme. Die Spezialität des Unternehmens aus dem schwäbischen Sulzbach-Laufen sind ergonomische Handhabungslösungen, die bei industriellen Schraubtechniksystemen in der Automobilindustrie zum Einsatz kommen. Dafür wird auch eine Vielzahl an Verzahnungen benötigt, die im eigenen Betrieb gefertigt werden. Für deren Herstellung an unterschiedlichen Bauteilen setzt der Leiter der spanenden Fertigung, Thomas Knöpfle, auf Werkzeugsysteme aus Tübingen: „Werkzeuge von Horn sind einwandfreie Problemlöser. Wir konnten schon viel Zeit einsparen und unsere Bearbeitungsprozesse optimieren.“
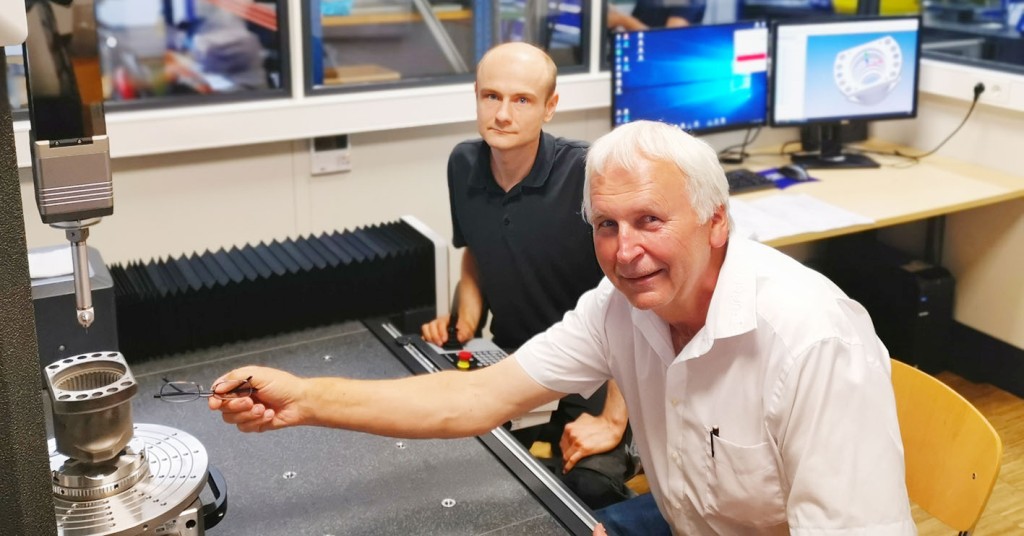
Rainer Jäger (Geschäftsfüher) zusammen mit Messtechniker Eugen Friesen im Messraum bei der Qualitätssicherung der Planetenträgergehäuse.
Foto: Jäger Handling
In Industrieunternehmen in der ganzen Welt im Einsatz
Mit einer Erfahrung von mehr als 25 Jahren stellt sich der Geschäftsführer Rainer Jäger mit seinem Team den unterschiedlichsten Aufgabenstellungen für die Handhabungstechnik. Beispiele sind die Lösungen zur Schraubtechnikmontage: Diese entwickelt und produziert das Unternehmen unter anderem für die Automobil-, Nutzfahrzeug-, Bau- und Landmaschinenbranche. So sind die Handlingsysteme an einer Vielzahl von Fließbändern in den genannten Industrien weltweit zu finden. Der Kernpunkt des Handelns sind die „Keep it simple“-Lösungen. Diese entstehen unter den Gesichtspunkten Ergonomie, neuester Stand der Technik sowie hoher Nutzen für den Anwender. Mit dem technischen Know-how und der Erfahrung der vielen umgesetzten Projekte entwickelte Jäger Handling ein eigenes Baukastensystem. Dieses ist flexibel für die unterschiedlichsten Anforderungen einsetzbar.
Eine Vielzahl von Verzahnungen sind zur Funktionserfüllung nötig
„Achsmontage, Getriebemontage, Motormontage und die Endmontage: Überall dort, wo an den Fließbändern geschraubt wird, sind unsere Systeme im Einsatz“, erzählt Knöpfle. Die elektrischen Schraubspindeln kauft das Unternehmen zu. Die Schnittstellen zwischen der Schraube und der Spindel fertigen die Mitarbeitenden bei Jäger selbst. „Hier geschieht alles auf Kundenwunsch und je nach den zu verschraubenden Teilen“, so Knöpfle. Zu den Schnittstellen gehören beispielsweise Winkelköpfe, Planetengetriebe, Offset-Getriebe oder mehrspindlige Schraubsysteme zum gleichzeitigen Verschrauben von Radmuttern. Für diese Schnittstellen müssen von der Fertigungsabteilung eine Vielzahl von Verzahnungen hergestellt werden, wofür unterschiedliche Verfahren zum Einsatz kommen.
Bei einem Teil davon bestand Bedarf zur Optimierung der Fertigung. „Einige Verzahnungen haben wir bisher erodiert, was für jede einzelne Verzahnung einen hohen Zeitaufwand bedeutete. Andere Verzahnungen mussten wir extern fertigen lassen“, erklärt Knöpfle. Das Ziel der Optimierungen war, die Bauteile inklusive der fertigen Verzahnung in einer Aufspannung zu fertigen. Mit dieser Aufgabenstellung wandte sich Knöpfle mit seinem Team an den Horn-Außendienstmitarbeiter Stephan Weiß. „Wir haben uns über die Zeit ein hohes Know-how in der Bearbeitung von Verzahnungen erarbeitet und beherrschen mit unseren Werkzeuglösungen einige Prozesse in der Herstellung von präzisen Verzahnungen“, sagt Weiß.
Hohe Zeiteinsparung dank präzisionsgefertigter Tools
Die Innenverzahnung mit dem Modul 1,5 eines Planetenträgers fertigte Knöpfle in der Vergangenheit über das Senkerodieren. Dies ist ein Verfahren, bei dem die gewünschte Form durch eine Elektrode hergestellt wird. Diese stellt das Gegenstück zur geplanten Werkstückform dar. Das Werkstück befindet sich in einem Bad aus Dielektrikum, sodass das Überspringen des Funkens auch ohne Berührung gewährleistet ist. Das Verfahren nimmt viel Zeit in Anspruch.
Das zu fertigende mehrstufige Planetengetriebe sitzt im späteren Einsatz in einem Winkelkopf und erhöht das Drehmoment von 500 auf 1.500 Newtonmeter. Es kommt bei der Montage von Achsen und Querlenkern zum Einsatz. „Die Erodierzeit war bei den steigenden Stückzahlen nicht produktiv“, so Knöpfle. Stephan Weiß schlug hierzu das Verfahren des Verzahnungsstoßens vor. Zum Einsatz kommt das Horn-Werkzeugsystem „117“ mit einer präzisionsgeschliffenen Schneidplatte. Das Profil der Schneidplatte gleicht dem Profil der Verzahnung.
Im Einsatz stellt die Maschine das Werkzeug vor dem Bauteil an und stellt die programmierte Zustellung zu. Dann folgt der Hub in das Werkstück. Am Ende der Verzahnung befindet sich ein Einstich, welcher als Freilauf für das Stoßwerkzeug dient. Dort hebt das Werkzeug wieder ab und fährt zur Ausgangsstellung zurück. Dieser Vorgang wiederholt sich so oft, bis die erforderliche Tiefe erreicht ist. Die Zustellung pro Hub beträgt für dieses Bauteil 0,1 Millimeter. Danach taktet die Spindel einen Zahn weiter und beginnt von vorn, bis alle Zähne des Planetenträgers gefertigt sind. „Durch die Umstellung können wir das Bauteil fertig fallend produzieren. Gegenüber dem Erodieren haben wir eine enorme Zeiteinsparung erreicht. Darüber hinaus konnten wir gleichzeitig die Qualität der Verzahnung steigern“, erklärt Knöpfle.
Das Verfahren des Stoßens auf der Maschine bringt dem Anwender diverse Vorteile. Es können unterschiedliche Nuten, Profile, Verzahnungen oder auch Führungsnuten gefertigt werden. Zum Fertigen des Werkstücks reicht eine Aufspannung. Somit lassen sich weitere Bearbeitungsschritte oder sogar Investitionen wie Räummaschinen oder Erodieranlagen einsparen. Des Weiteren trägt die Komplettbearbeitung zur Steigerung der Präzision bei und erhöht die Produktivität der Bearbeitungsprozesse.
Problemlöser: Die Zirkularfräser mit Verzahnungsprofil
Ein weiteres Bauteil ist eine Antriebswelle, die ebenfalls in einem Winkelkopf zur Übertragung des Kraftflusses dient. Die Fertigung der Außen-Steckverzahnung gab Knöpfle bisher extern in Auftrag. Diese Aufgabe wollte er nun wieder in den eigenen Betrieb zurückholen. Die Güte der Oberfläche sowie die Genauigkeit der Zahnprofile verlangten auch hier eine Optimierung. Weiß setzte zur Fertigung auf das sechsschneidige Zirkularfrässystem „613“.
Das Werkzeug fräst jeden der 25 Zähne der Verzahnung auf die volle Tiefe von 1,5 Millimetern in einem Zug. Die Fräsrichtung erfolgt im Gegenlauf. Die Werkzeuge bieten, trotz des hohen Schnittdrucks durch die sechs Zähne, eine hohe Stabilität. „Die sechs Zähne sorgen für eine höhere Fräsleistung und die Möglichkeit, höhere Schnittgeschwindigkeiten zu fahren“, sagt Weiß. Das Optimierungsziel lautet: Zeiteinsparung bei gleichzeitiger Erhöhung der Qualität. Dies konnte der Tübinger Werkzeugspezialist auch bei diesem Bauteil erfüllen.
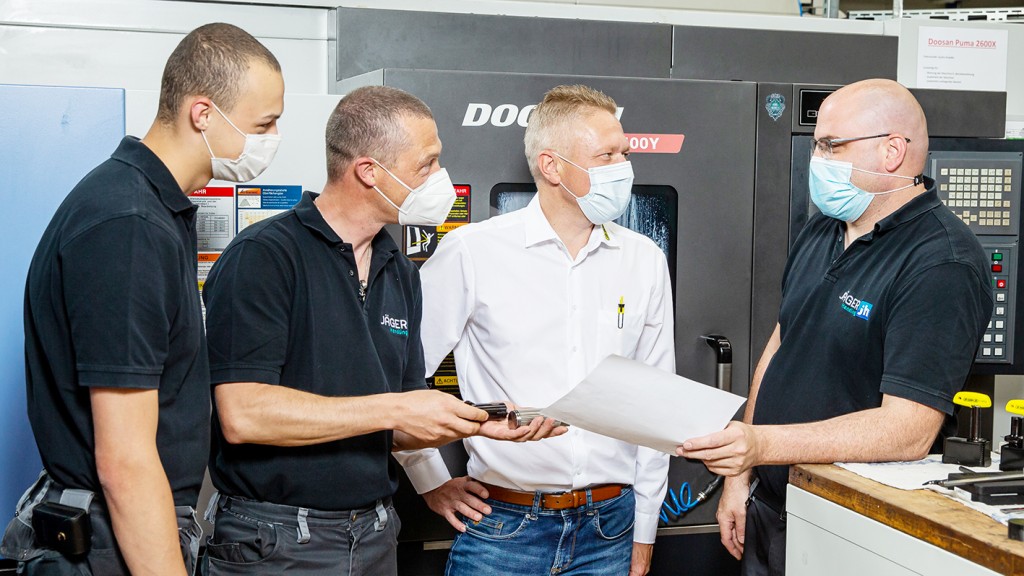
Eine erfolgreiche Zusammenarbeit: Dustin Knöpfle im Gespräch mit Thomas Knöpfle (beide Firma Jäger), Stephan Weiß (Firma Horn) und dem Leiter der Arbeitsvorbereitung bei Jäger, Michael Meier.
Foto: Jäger Handling
Thomas Knöpfle zeigt sich mit den Optimierungen zufrieden: „Horn ist für uns der ,Supersportwagen‘ unter den Werkzeugherstellern und spielt bei uns eine große Rolle als Problemlöser. Auch bei der jüngsten Aufgabe wurden wir mit der technischen Beratung durch den Außendienst wieder vollständig zufriedengestellt.“
Verzahnungswerkzeuge vom Spezialisten
Das Produktportfolio der Tübinger (www.phorn.de) umfasst ein breites Werkzeugprogramm zur Herstellung von unterschiedlichen Verzahnungsgeometrien mit Modul 0,5 bis Modul 30. Unabhängig davon, ob es sich um Verzahnungen an Stirnrädern, Welle-Nabe-Verbindungen, Schneckenwellen, Kegelrädern, Ritzeln oder an kundenspezifischen Profilen handelt – alle erdenklichen Zahnprofile lassen sich mit den Werkzeugen zum Fräsen, Nutstoßen und anderen Prozessen äußerst wirtschaftlich herstellen.
Einen weiteren Beweis der Kompetenz beim Verzahnen bietet das Produktprogramm Wälzschälen. Das Verfahren ist zwar bereits seit über 100 Jahren bekannt. Eine breitere Anwendung findet es aber erst, seit Bearbeitungszentren und Universalmaschinen mit voll synchronisierten Spindeln und verfahrensoptimierter Software die Anwendung dieser hochkomplexen Technologie zulassen.
Das könnte Sie auch interessieren:
Elektromobilität: Nichts geht ohne Verzahnungen
Auf dem Weg vom Wunsch-Zahnrad zum perfekten Werkzeug
Nico Sauermann arbeitet als Redakteur & Fotograf bei der Paul Horn GmbH in Tübingen.