Pilotlinie zur Herstellung maßgeschneiderter Freiform-Mikrooptiken
Freiform-Mikrooptiken erlauben es, gleichermaßen kompakte sowie leichte und energieeffiziente Beleuchtungssysteme zu entwickeln. Zusätzlich überzeugen sie durch reduzierte Fertigungskosten. Ein EU-Verbundprojekt soll nun die Ideen weiterentwickeln und mithilfe einer Pilotanlage zur Marktreife bringen.
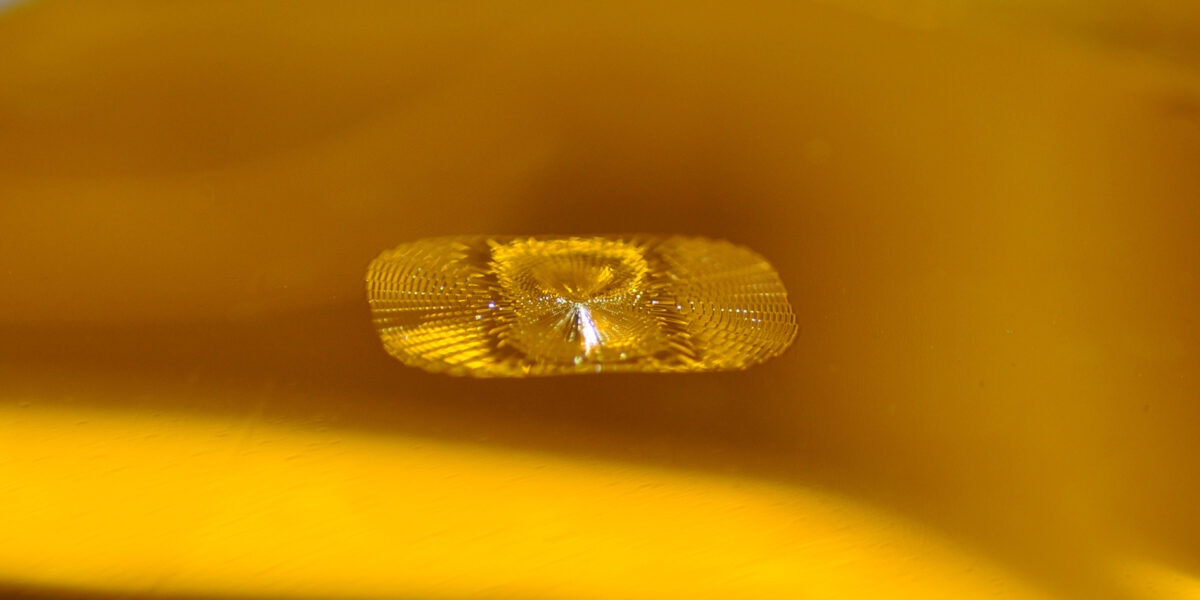
Ein noch nicht galvanisierter Master aus dem Upscaling-Prozess: Solchen komplexen Oberflächenformen von Optiken widmeten sich die Forschungspartner im PHABULOuS-Projekt.
Foto: Seisenbacher
Am Projekt „PHABULOuS“ beteiligen sich die drei branchenspezifischen Industrie-Experten Hella, Seisenbacher und Zumtobel, um neuartige Beleuchtungslösungen zu kreieren. Hella, mittlerweile ein Unternehmen der Forvia-Gruppe, entwickelt Beleuchtungen für Automobile, Seisenbacher ist im Bereich Schienenfahrzeuge aktiv und Zumtobel sucht repräsentative Beleuchtungslösungen für Museen, Büroräume und dergleichen. Allen gemein sind hohe Qualitäts- und Sicherheitsstandards. Der neuartige Lösungsansatz gestattet hier nicht nur ein modernes Lichtdesign, sondern liefert auch neue Ansätze in Sachen Lichtsteuerung, -verteilung und Ästethik.
Welche Vorteile bieten FFMOs?
LED (Light-Emitting Diode)-Technologie setzt sich in der Beleuchtung immer weiter durch. Die Verdrängung klassischer Lichtquellen bringt aber neue Herausforderungen mit sich: So steigen mit der zunehmenden Leistungsdichte die thermischen Anforderungen an optische Komponenten. Und effiziente Diffusoren werden benötigt, um das ausgestrahlte Licht möglichst homogen zu verteilen und die einzelnen LEDs als solche nicht sichtbar zu machen. Insbesondere aber steigen die kundenspezifischen Ansprüche hinsichtlich der Strahlformung stetig, um immer komplexere Beleuchtungsszenarien realisieren zu können.
Die im Projekt entwickelten Freiform-Mikrooptiken (FFMOs) – im Englischen ist der Begriff „freeform microlens arrays“ (FMLA) üblich – ermöglichen zusätzliche Leistungen und Funktionalitäten, sind aber gleichzeitig extrem anspruchsvoll in der Fertigung. Deshalb wurde im Januar 2020 bei CSEM das europäische Projekt „PHABULOuS“ (Pilotlinie zur Bereitstellung einer hoch entwickelten & robusten Fertigungstechnologie für optische Freiform-µ-Strukturen) ins Leben gerufen. Das Projekt firmiert im Rahmen des Arbeitsprogramms „Horizont 2020“ mit Mitteln in der Größenordnung von 15 Millionen. Euro (https://phabulous.eu/). Das CSEM ist ein Schweizer Forschungs- und Entwicklungszentrum, das in den Bereichen Mikrofertigung, Digitalisierung und erneuerbare Energien tätig ist, und hat seinen Hauptsitz in Neuenburg/CH.
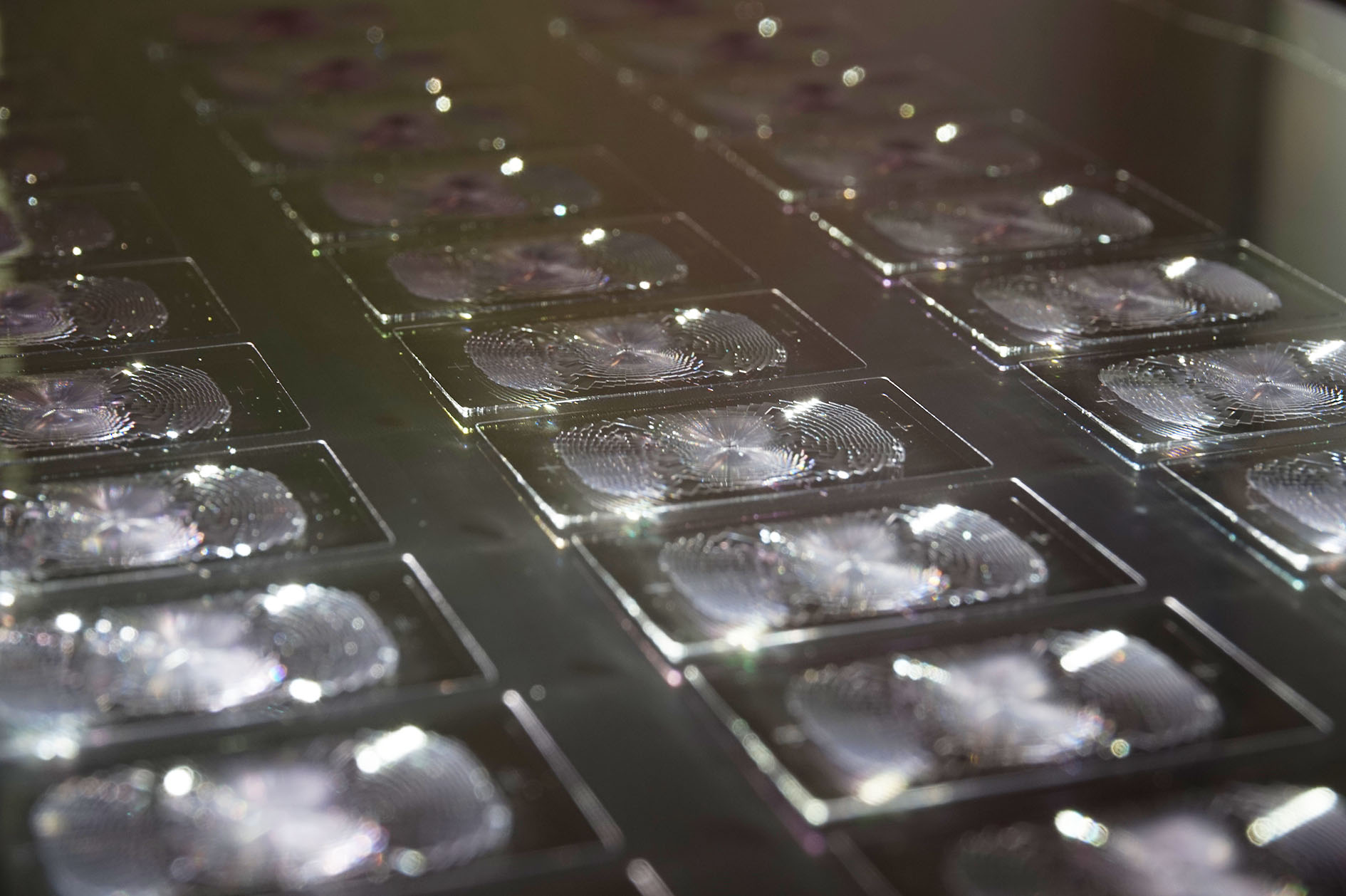
Das Bild zeigt einen Ausschnitt des kompletten, in der Pilotanlage erzeugten FMLA’s (sprich des Arrays).
Foto: Seisenbacher
FFMOs – extrem kleine, komplexe optische Elemente – steuern präzise die Lichtverteilung und -intensität. Das steigert die Effizienz und senkt den Energieverbrauch. Sie eignen sich ideal zur Integration in kompakte Architekturen. Ziel von PHABULOuS ist der Aufbau einer europäischen Pilotlinie, die die Kompetenzen unterschiedlicher Partner zusammenbringt. Das Projekt bietet interessierten Unternehmen eine einzige Anlaufstelle für dieses Technologiefeld. Das beschleunigt Innovations- und Produktionszyklen, verkürzt und verbilligt den Weg vom Prototypen bis zur Serienproduktion. Das Einrichten der Pilotlinie soll dabei kosteneffizient mittels UV-Replikationstechnologien wie „Wafer-Scale“, „Rolle-zu-Platte“ (R2P) und „Rolle-zu-Rolle“ (R2R) geschehen.
Etablieren einer Pilotlinie
Im Projekt wollte das Unternehmen Seisenbacher ultradünne Leuchten mit weniger als 10 Millimetern Dicke, einer deutlich reduzierten Anzahl von LEDs und einem maßgeschneidertem Beleuchtungsmuster entwickeln. Die Vorgaben von Hella waren, Primär- und Sekundärlinsen sowie Shutter in ein einziges mikrooptisches Bauteil zu integrieren. Zumtobel hatte die Entwicklung eines neuartigen LED-Downlights ins Auge gefasst. Um dies zu erreichen, arbeiteten diese drei Unternehmen mit weiteren Spezialisten zusammen – wie Joanneum Research, CSEM, Morphotonics, Wielandts UPMT PowerPhotonic, SÜSS MicroOptics, Nanocomp und Lasea.
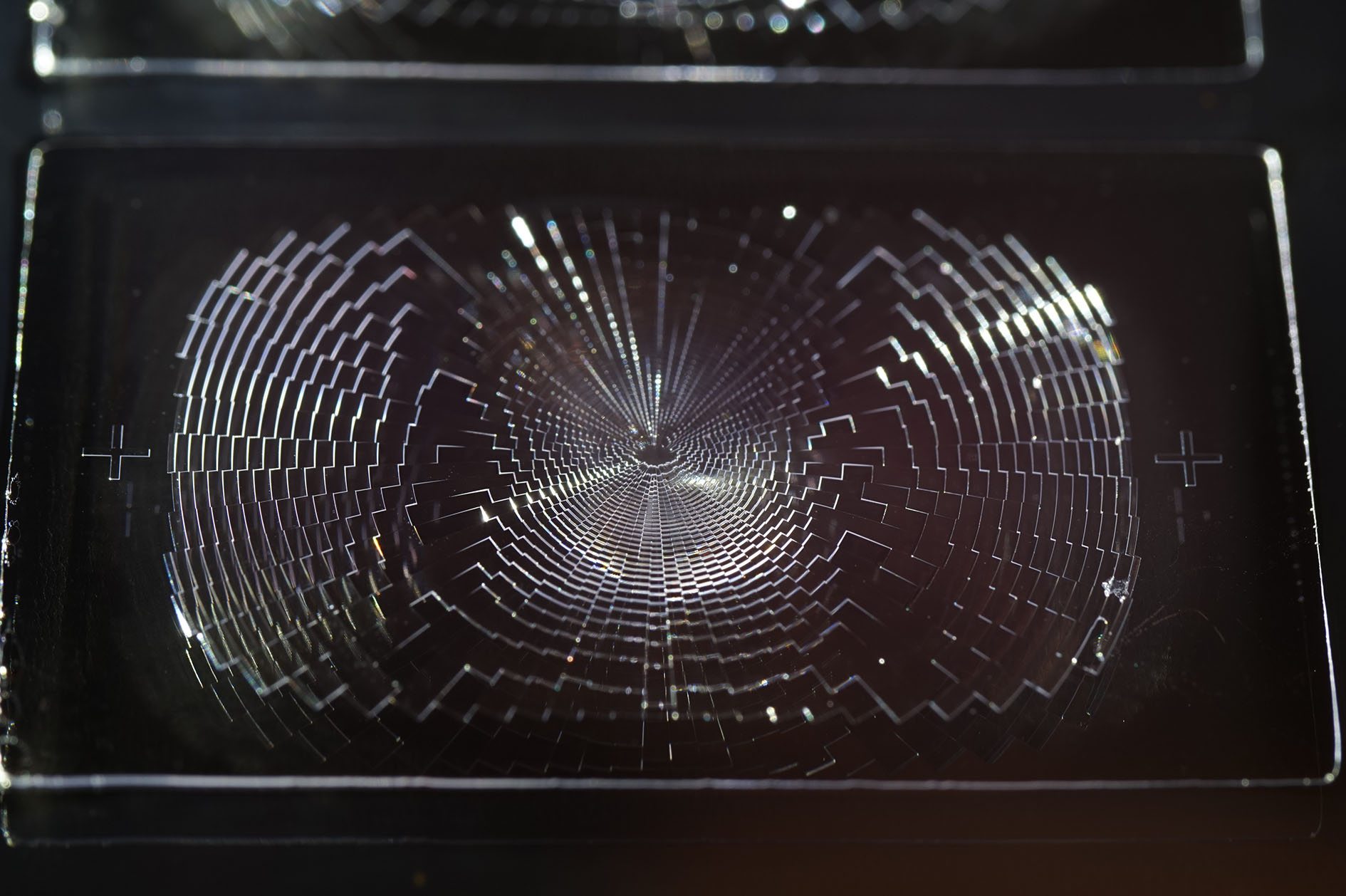
Einzelelement eines FMLAs (freeform microlens arrays) – ein einzelnes im R2P-Verfahren auf ein Substrat aufgedrucktes FMLA.
Foto: Seisenbacher
Bei den drei Aufgaben wurde zuerst jeweilig ein Master erstellt, der dann hochskaliert wurde. Zu diesem Mastern wurde eine Art serientauglicher Prägestempel erzeugt. Diese Replikate wurden mittels UV-Rolle-zu-Platte R2P- oder Rolle-zu-Rolle R2R-Technologie erzeugt. Das Replikat, ein auf ein Substrat aufgedrucktes FFMO, wurde anschließend weiterverarbeitet und für die Integration in das Endprodukt vorbereitet.
Effiziente Fertigung von FFMOs: der Herstellungsprozess
In der anfänglichen Designphase werden mit Simulationen und Modellierung die optimale Form, Abmessungen und Oberflächeneigenschaften ermittelt. Mithilfe von Softwaretools simulieren Ingenieure das Verhalten von Licht innerhalb der Optik und analysieren so deren Form, Oberflächen und optischen Eigenschaften. Eine Anforderung, die die Aufgabenstellung komplex macht: FFMOs benötigen komplizierte Designs, die präzise Fertigungsvorgaben erfordern, was ihre Integration in bestehende Technik komplex macht. Auch das Hochskalieren der Fertigung in die Massenproduktion mit gleichbleibender Qualität ist aufgrund der komplexen Fertigungstechniken eine Herausforderung.
Auch wenn die Partner aktuell noch kein vermarktbares Produkt haben, ist man sich bei Seisenbacher des Potentials der FMLAs sicher. Fortschritte in der FFMO werden zukünftig zu größerer Designflexibilität führen und Beleuchtungslösungen ermöglichen, die nicht nur funktional, sondern auch ästhetisch ansprechen und das Innendesign von Räumen verbessern.
Autoleuchten – ein „Sonderkapitel“
Von schmalen Lichtbändern bis zu homogenen, leuchtenden Flächen stehen viele Stylings für Automobile zur Verfügung – und Freiform-Optik bietet hier großes Potential. Klassische Freiform-Makro-Optiken lassen sich effizient mit Spritzguss herstellen, leider sind sie aus größerer Entfernung sichtbar. Die aktuellen Trends verlangen aber die Integration in die Karosserie oder deren „Unsichtbarkeit“.
Bei seinen FlatLight-Produktfamilien „FlatlLight|µDO“ und „FlatLight|µMX“ verwendet Hella schon länger FFMOs. Ein Hinderungsgrunde für den Einsatz in Automobilen liegt an der benötigten hohen optischen Oberflächenqualität. Die Anwender wünschen sich hier eine kostengünstige Mastering- und Serienproduktion, vergleichbar mit Spritzguss, bei denen sich weiterhin die für die Automobilindustrie zertifizierten Materialien verwenden lassen.
Hella plante, Primär- und Sekundärlinsen sowie Shutter in ein einziges mikrooptisches Bauteil zu integrieren. Die Gestaltung einer Fläche als Primäroptik und der zweiten als Sekundäroptik sollte eine präzise Kontrolle über die Lichtverteilung zulassen. Das Ergebnis ist eine doppelseitige Mikrooptik – so klein wie eine Ein-Cent-Münze und zwischen 0,3 und 2,5 Millimetern dick.
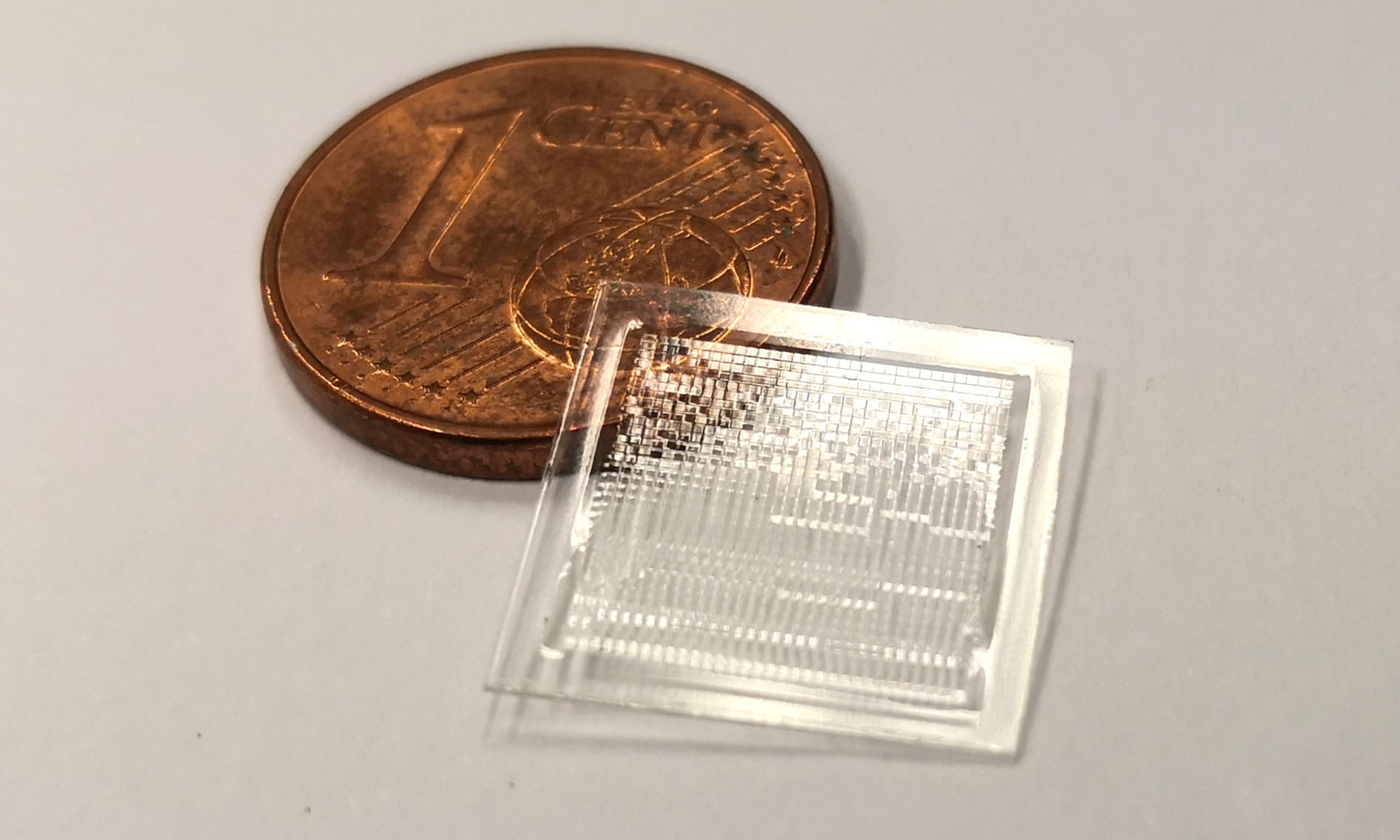
Eine im Projekt PHABULOuS hergestellte Freiformmikooptik, die sich in der Automobilindustie für Fern- und Abblendlicht nutzen lässt.
Foto: Hella
Auch wenn die optische Qualität der Bauteile überzeugte, erreichten die Lichtverteilungen noch nicht den Standard von Automobilprodukten. Ein Grund ist die Verwendung von LEDs als Lichtquellen. Die Algorithmen zur Berechnung von Mikrooptiken sind meist auf ideale Lichtquellen wie Punktlichtquellen beschränkt, was für LEDs nicht gilt.
„Für Hella ist diese aktuelle Herausforderung jedoch kein Grund, die Forschungs- und Entwicklungsaktivitäten an diesem Thema zu beenden. Die Ergebnisse aus dem PHABULOuS Projekt belegen das Potential für die Verwendung von Mikrooptiken mit LEDs und es gibt noch einige vielversprechende Ansätze, die es in Zukunft zu untersuchen gilt“, berichtet Dr. Daniela Karthaus, Optik-Ingenieurin bei Hella.
Inhomogene Leuchtdichte beherrschen
Das Problem bei Zumtobel bestand darin, die inhomogene Leuchtdichte einer Lichtquelle aus kalt- und warmweißen LEDs in den Griff zu bekommen. Um den spektralen Inhalt der Beleuchtung zu ändern müssen die Lichtquellen abstimmbar sein.
Das neue System besteht aus einer Lichtquelle aus kaltweißen und warmweißen LEDs und einem Diffusor. Für den Diffusor wurde ein Master mittels Laserablation hergestellt. Und für eine glatte Oberfläche wurde mit einer zweiten Glättungsstufe das Obermaterial aufgeschmolzen.
Resümee der Projektpartner
Die komplexen und segmentierten Oberflächenformen bringen viele Herausforderungen an Design, Herstellung und Qualitätskontrolle mit sich. Eine deutliche Hilfestellung zur Lösung der Aufgabenstellung trägt das EU-Forschungsprojekt bei: Hierin wurden beispielsweise CAD-basierte Algorithmen entwickelt, um die Auswahl der richtigen Herstellungs-/Entstehungsmethode zu erleichtern und den Bewertungsprozess zu beschleunigen. Das reduziert die Rückkopplungsschleifen zwischen Optikdesignern und -herstellern drastisch, was erheblich Zeit und Kosten spart.
„Die Zusammenarbeit mit PHABULOuS hat uns viel Know-how gebracht, um mit diesen Technologien Optiken für die Allgemeinbeleuchtung zu entwickeln. Die Steigerung der Leistungsfähigkeit der Pilotlinie ist beeindruckend“, so die Aussage von Katharina Keller, Leiterin Optik bei Zumtobel.
„Die optischen Ergebnisse entsprechen noch nicht zu 100 Prozent den Vorgaben, aber im Projekt wird weiter an der Umsetzung der Technologie geforscht werden“, so das optimistische Resümee von Christian Stacher, Konstruktion & Entwicklung bei Seisenbacher.
Das könnte Sie auch interessieren:
Revolution im laserbasierten Schweißen für den Leichtbau
Lasertechnik als Enabler für die Zukunft der europäischen Raumfahrt
Forschung und Industrie fokussieren gemeinsam die nachhaltige Produktion
Barbara Stumpp ist freie Fachjournalistin in Freiburg.