Schneller „Gesundheitscheck“ für die Werkzeugmaschine
Wem die „Gesundheit“, also die Verfügbarkeit und Produktivität seiner Produktionsmaschinen am Herzen liegt, der sollte diese regelmäßig durchchecken lassen. Gezeigt wird, was der „Fingerprint“ dazu beitragen kann.
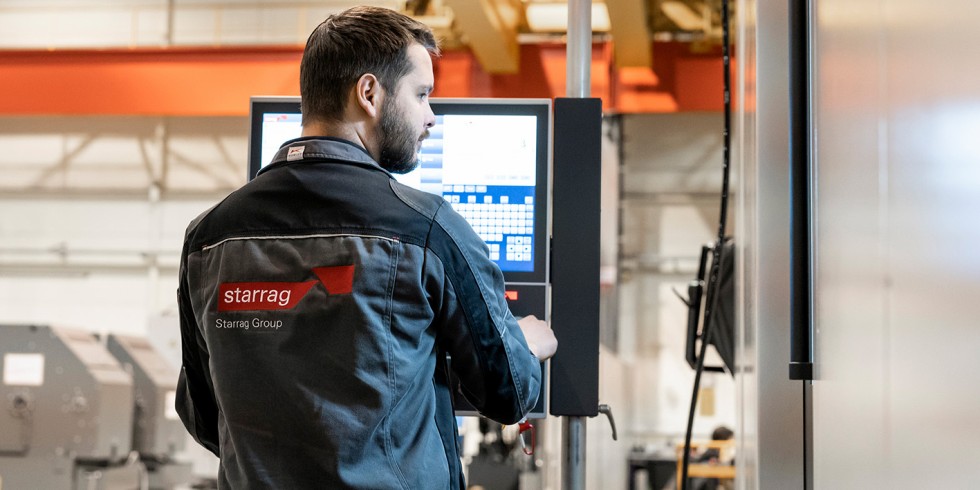
In nur einer Stunde erfassen Servicetechniker via Remotezugang wichtige Maschinenzustände, und spätestens am nächsten Werktag erhält der Kunde eine detaillierte Übersicht über den Verschleisszustand der mechanischen Baugruppen.
Foto: Starrag
Für die regelmäßig notwendige Kontrolle bietet ein Schweizer Werkzeugmaschinenbauer den sehr effizienten Fingerprint seit Mitte des Jahres 2021 auch in einer Online-Variante an. Das digitale Tool, das die Serviceangebote abrundet, ist kostengünstig, schnell und vor allem aufschlussreich. Der Kunde muss die Maschine lediglich für eine Stunde aus der Produktion nehmen.
Wie läuft der Online-Fingerprint ab?
Zum vereinbarten Termin meldet sich der Remoteservice von Starrag beim Kunden, der die Maschine für die Untersuchung bereits vorbereitet hat. Was ist zuvor zu tun? Auf der Maschine befindet sich eine Leerpalette, und es sind keine Werkzeuge eingewechselt, sodass bei den Testläufen jegliche Kollisionsgefahr ausgeschlossen ist.
Der Maschinenbediener gibt an der Maschine den Zugriff zum Fingerprint frei. Erst jetzt kann der Servicetechniker vom deutschen Standort des Werkzeugmaschinenbauers in Chemnitz aus darauf zugreifen. Er startet ein eigens dafür entwickeltes Programm, das verschiedene Aufgaben abarbeitet. Dazu zählen Frequenzgang- und Schwingungsanalysen sowie ein Kreisformtest. Außerdem werden die Stromaufnahme aller Bearbeitungsachsen, der Verschmutzungs- und Verschleißgrad der Linearmesssysteme sowie Zählerstände und Temperaturdaten erfasst.
Die festgestellten Daten werden mit den bereits früher erfassten Werten verglichen und analysiert. Spätestens am nächsten Werktag erhält der Kunde ein Ergebnisprotokoll, das alle Zustände aufschlüsselt – und darüber hinaus gegebenenfalls Vorschläge zur Beseitigung von Fehlern oder für Wartungsarbeiten enthält.

Mit dem „Online-Fingerprint“, hier am Beispiel einer „HEC_X40“, steht Anwendern eine schnelle, qualifizierte Maschinenanalyse bereit. Kosten für Instandhaltung und Ressourcen lassen sich verringern; ungeplanten verschleissbedingten Maschinenausfällen wird vorbeugt.
Foto: Starrag
Für welche Bearbeitungszentren gibt es den Check?
Im Bild ist als Anwendungsbeispiel die Konstruktion einer „HEC X40“ zu sehen. Sie gehört zu einer Serie von neu entwickelten horizontalen Bearbeitungszentren (BAZ), die vor etwa zwei Jahren vorgestellt wurden. Basierend auf einem vorteilhaften modularen Konzept, entstanden die „L40“ (Linienmodul für 400er-Palette) und „H50“ (vier-achsiges BAZ mit 500er-Palette) sowie die fünf-achsigen „X40/45“ und die multifunktionale „T45“. Bei der Entwicklung dieser Baureihe von Heckert stand eine hohe Flächenproduktivität mit bis zu 30 Prozent geringerem Platzbedarf im Fokus.
Die kompakten Bearbeitungszentren verfügen über eine hohe Steifigkeit: Vor allem in den Gestellbaugruppen – also im Maschinenbett, Ständer sowie im Tisch bzw. der Dreh-/Schwenkeinheit – gilt dies als ein entscheidendes Qualitätsmerkmal, das nicht nur für die Schwerzerspanung benötigt wird, sondern auch für die Bearbeitung anspruchsvoller Werkstoffe sowie zum hochperformanten Auskoffern von Leichtbaumaterialien, wie im Flugzeugbau üblich.
Welche Vorteile kann der Kunde verbuchen?
Die Vorzüge des neuartigen Vorgehens zur Maschinenkontrolle sind für den Anwender Gewinn bringend: Ohne aufwendige Demontage- und Montagearbeiten erhält der Kunde eine schnelle und aussagekräftige Analyse über den Verschleißzustand der Hauptbaugruppen seiner Maschine. Unterm Strich verbucht er dadurch eine gesteigerte Maschinenverfügbarkeit und Produktivität, eine längere Lebensdauer der Maschine sowie niedrigere Werkstückkosten. Das Angebot zum Online-Fingerprint besteht seit Mitte 2021. Es wird zunächst für alle Heckert-Maschinen ab dem Baujahr 2017 mit „Siemens-Operate“-Steuerung angeboten. Nach und nach wird es auf andere Produktbereiche des Anbieters mit Stammsitz in Rohrschacherberg/CH „ausgerollt“.
Die Starrag Group bietet Präzisions-Werkzeugmaschinen zum Fräsen, Drehen, Bohren und Schleifen von Werkstücken aus Metall, Verbundwerkstoffen und Keramik. Zu den Kunden zählen die führenden Unternehmen in den Abnehmer-Industrien Aerospace, Energy, Transportation und Industrial (Industrial Components, Luxury Goods, Med Tech). Die Dachmarke verbindet zahlreiche Produktbereiche, zu denen auch die Heckert-Maschinen aus Chemnitz gehören. Die Firmengruppe betreibt Produktionsstandorte in der Schweiz, Deutschland, Frankreich, Großbritannien und Indien sowie Vertriebs- und Servicegesellschaften in den wichtigsten Abnehmerländern.
Das könnte Sie auch interessieren:
Bei der Spindelanalyse ist Eigeninitiative gefragt
Werkzeugmaschinen werden intelligent
Aktive Schwingungsdämpfung als Retrofit-Lösung für Werkzeugmaschinen