Schwingungen revolutionieren Dreh- und Bohrprozesse
Viele Optimierungsmaßnahmen in der industriellen Serienfertigung scheinen weitgehend ausgeschöpft zu sein. Beispielsweise Zerspanprozesse noch weiter zu verbessern, ist schwierig. Einen Erfolg versprechenden Weg hat ein junges Chemnitzer Gründerteam entdeckt.
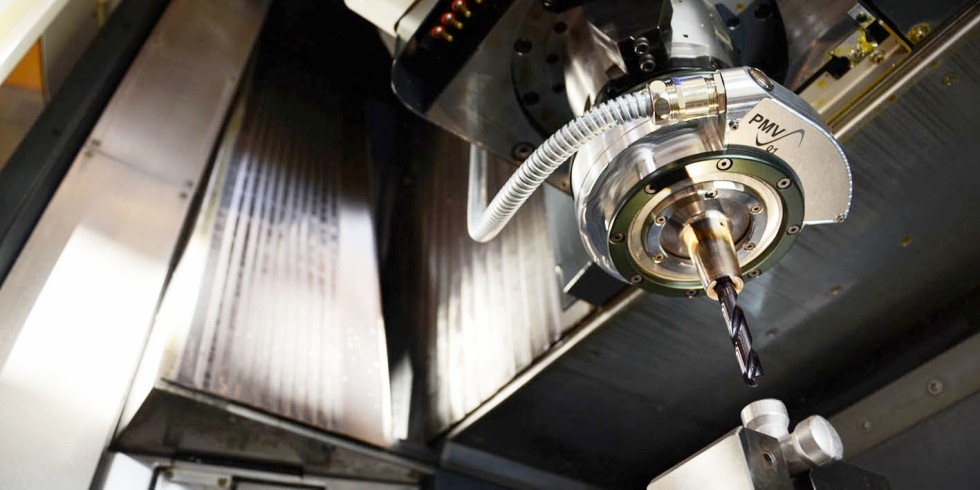
System für das ultraschallunterstützte Bohren und Tiefbohren: Die Produktivität steigt dank einer Erhöhung der Schnittwerte signifikant und zahlt sich für Fertigungsbetriebe in barer Münze aus.
Foto: Fraunhofer IWU
Wer sich im produzierenden Gewerbe erfolgreich behaupten möchte, muss seine Teilefertigung kontinuierlich optimieren. Oftmals stoßen Forschende und auch Industriebetriebe an ihre Grenzen und stellen fest, dass kaum noch spürbare Verbesserungen erzielbar sind. Dies gilt gerade auch für Zerspanungsprozesse, die oft einen erheblichen Teil der Wertschöpfung ausmachen.
Ein Weg zu weniger Verschleiß und kürzeren Bearbeitungszeiten
Das Gründerteam „VibroCut“ am Fraunhofer IWU (Institut für Werkzeugmaschinen und Umformtechnik) zeigt in einem aktuellen Projekt: durch innovative Schwingungsunterstützung lassen sich in Zerspanprozessen Bearbeitungskräfte, Werkzeugverschleiß, Gratbildung und Spanbruchprobleme reduzieren. Dank der Schwingungen ist eine deutliche Produktivitätssteigerung realisierbar, auch Stillstandszeiten von Maschinen und Anlagen werden erheblich verringert. Bei der Zerspanung schwer spanbarer Werkstoffe ist die Schwingungsunterstützung sogar Grundvoraussetzung für eine industrielle Machbarkeit.
Das Team am Fraunhofer IWU um Dipl.-Ing. Oliver Georgi nutzt gezielt erzeugte Schwingungen im Bereich bis 100 Hertz oder im Ultraschallbereich über 16 Kilohertz, um bei Zerspanungsprozessen bestehende Verfahrensgrenzen zu verschieben. In zahlreichen Industrieprojekten konnte es das technische Potential der schwingungsunterstützten Zerspanung nachweisen und signifikante Kostenvorteile beim Einsatz in der mechanischen Teilefertigung zeigen. Insbesondere in der Großserienfertigung sind die Skaleneffekte groß.
Schwingungen im Ultraschallbereich helfen beim Bohren und Tiefbohren
Hochfrequente Schwingungen im Ultraschallbereich (ab 16 Kilohertz) erhöhen beim Bohren und Tiefbohren die Produktivität und Prozesssicherheit. Die Ultraschallschwingungen führen in bestimmten Materialien, wie Kupfer- oder Aluminiumlegierungen, zu werkstofftechnischen Effekten. Dadurch konnte erreicht werden, dass die Zerspanungskräfte deutlich sinken. In der Folge ließ sich die Produktivität dank einer dadurch möglichem Erhöhung der Schnittwerte steigern. Ein Beispiel: Bei einem Maschinenstundensatz von 130 Euro, einer jährlichen Planbelegungszeit von 6000 Stunden sowie einem Hauptzeitanteil des Bohrens von 35 Prozent führt eine 40-prozentige Erhöhung von Drehzahl oder Vorschub zu einer Produktivitätssteigerung von 10 Prozent. Dies entspricht Einsparungen in Höhe von 78.000 Euro. Werden diese Schnittparameter um 100 Prozent erhöht, können sogar 136.000 Euro an Betriebskosten eingespart werden.
In anderen Anwendungsfällen steht die positive Auswirkung in Bezug auf die Gratbildung im Vordergrund. Durch die Reduzierung der Vorschubkraft wird diese so weit vermindert, dass Bearbeitungsaufwände, die für das nachträgliche Entgraten notwendig wären, sich reduzieren lassen. In manchen Fällen können sie sogar vollständig entfallen.
Beim Tiefbohren sorgt die Ultraschallunterstützung für einen verbesserten Spanabtransport und mehr Prozesssicherheit. Durch die genannten werkstofftechnischen Effekte wird Mittenverlauf verringert, der für die Qualität ausschlaggebend ist. Die Ultraschallschwingung modifiziert zusätzlich Reibungskontakte in der Zerspanungszone und damit den Werkzeugverschleiß. Die Werkzeugstandzeit verbessert sich dadurch deutlich. In bestimmten Anwendungen, etwa bei der Zerspanung von schwer spanbaren Materialien wie Nickelbasislegierungen, macht die Ultraschallunterstützung eine ausreichende Prozessfähigkeit, akzeptable Werkzeugstandzeiten und damit eine wirtschaftliche Fertigung überhaupt erst möglich.
Schwingungen im niederfrequenten Bereich unterstützen beim Drehen
Bei Zerspanungsprozessen mit kontinuierlichem Schneideneingriff, wie dem Drehen, ist der Spanbruch eine große Herausforderung. In der Serienfertigung führen Störgrößen wie Werkzeugverschleiß oder Chargenschwankungen dazu, dass oft kein prozesssicherer Spanbruch eingestellt werden kann. Lange Späne und Wirrspäne können die Werkstücke beschädigen. Außerdem führen sie zur Bildung von Spänenestern, welche den Spänefluss stören. Solche Spänenester müssen manuell beseitigt werden, was nur bei Maschinenstillstand möglich ist. Wird der Spanbruch nicht beherrscht, ist in einigen Fällen sogar der Fertigungsprozess nicht automatisierbar.

Mit Schwingungsunterstützung erzeugte kurze Späne (im Vordergrund des Bildes) im Vergleich zu langen Spänen. Diese wurden in einem konventionellen Drehprozess mit identischen Parametern erzeugt. Sie können zu Bauteilschädigungen sowie höherem Zeitaufwand in der Zerspanung führen.
Foto: Fraunhofer IWU
Durch die Schwingungsunterstützung mit bis zu 100 Hertz und 0,6 Millimetern Schwingweite entstehen prozesssicher kurze und definiert gebrochene Späne. In vielen Fällen mussten Drehmaschinen bisher – sogar in der Serienfertigung – mehrere Minuten pro Stunde gestoppt werden. Dank der Nutzung der neuartigen Technologie verursacht der Spanbruch nun keine Produktionsunterbrechungen mehr.
Wie funktioniert das Verfahren?
Die Schwingungsunterstützung bei der Zerspanung wird mit innovativen und flexiblen Systemen realisiert, welche als Werkzeughalter am Revolver der Drehmaschinen oder in Bearbeitungszentren eingewechselt werden können. Folgendes Beispiel beim Innendrehen unterstreicht das Einsparpotential durch die verbesserte Maschinenverfügbarkeit: Bei einem Maschinenstundensatz von 85 Euro und einer jährlichen Planbelegungszeit von 6000 Stunden führt ein spanbruchbedingter Nutzungsausfall von durchschnittlich sechs Minuten pro Stunde zu einem jährlichen Nutzungsverlust von 10 Prozent und Stillstandskosten in Höhe von 51.000 Euro. Diese Kosten sind durch den Einsatz der neuartigen Technologie vermeidbar.
Erfolgreiche Anwendung in der industriellen Radlagerfertigung
Insbesondere in der Automobilindustrie kann die schwingungsunterstützte Zerspanung einen Beitrag leisten, die Effizienz bei der Fertigung zahlreicher Teilefamilien zu verbessern. Der Automobil- und Industriezulieferer Schaeffler setzt das schwingungsunterstützte Drehen inzwischen erfolgreich beim Innendrehen in der Radlagerfertigung ein, um die Produktivität weiter zu steigern. Auch die Ultraschallunterstützung realisierte das Unternehmen gemeinsam mit dem Fraunhofer IWU für die Kernbohrungen der Gewinde in den Radlagern.
Das Gründungsvorhaben VibroCut ist quasi die „Antwort“ des Forscherteams um Oliver Georgi auf das große Interesse vieler Industriepartner. Die Nachfrage an innovativen Lösungen für mehr Effizienz in der Zerspanung ist groß. Die Gründer planen, zukünftig Schwingsysteme zu vertreiben, die als Funktionserweiterung für bestehende Werkzeugmaschinen nachgerüstet werden können. Darüber hinaus wird das Unternehmen Dienstleistungen wie die kundenspezifische Technologieentwicklung, Maschinenintegration sowie Schulungen anbieten – seine Kunden also mit Komplettlösungen für die schwingungsunterstützte Zerspanung begleiten.

Das künftige VibroCut-Team (v.l.n.r.): Dipl.-Ing. Carlo Rüger (Applikationsingenieur für zerspanungstechnische Prozesse), Dipl.-Ing. Oliver Georgi (Geschäftsführung, Technischer Vertrieb), M.A. Viola Lehmann (Kaufmännische Leitung, Finanzen, Verwaltung, Marketing), M.Sc. Martin Schwarze (Entwicklung).
Foto: Fraunhofer IWU
Für den Markteinstieg konzentriert sich das Team auf die Verfahren Bohren und Drehen. Das Unternehmen wird sich jedoch nicht auf einzelne Marktnischen beschränkten, sondern künftig weitere Anwendungen in unterschiedlichen Zerspanungsprozessen abdecken. Großes Marktpotential sieht VibroCut in der Automobil- und deren Zuliefererindustrie, im Maschinenbau oder in der Luft- und Raumfahrtechnik. Das Bundesministerium für Wirtschaft und Klimaschutz fördert VibroCut im Rahmen von „EXIST“, einem Programm zur Unterstützung herausragender forschungsbasierter Gründungsvorhaben. Die Unternehmensgründung ist für Mitte 2023 vorgesehen.
Über das Gründerteam und das Fraunhofer IWU
Das VibroCut-Gründerteam besteht aus drei Wissenschaftlern und einer Betriebswirtin des Fraunhofer IWU. Die Wissenschaftler haben das Forschungsfeld der schwingungsunterstützten Zerspanung am Institut seit 2015 maßgeblich vorangetrieben. Entstanden sind dabei patentierte, nachrüstbare und hochflexible Schwingsysteme, die ihre einzigartige Leistungsfähigkeit und Robustheit auch bei Hochleistungszerspanungsprozessen unter Beweis gestellt haben: beste Voraussetzungen für einen nachhaltigen Markterfolg.
Das Fraunhofer-Institut für Werkzeugmaschinen und Umformtechnik IWU ist eine treibende Kraft für Forschung und Entwicklung in der Produktionstechnik. Rund 670 Mitarbeitende sind an den Standorten Chemnitz, Dresden, Leipzig, Wolfsburg und Zittau tätig. Der Schwerpunkt liegt auf Technologien und Produktionsanlagen für umformende, spanende und fügende Fertigungsschritte. Im Fokus von Wissenschaft und Auftragsforschung stehen Bauteile, Verfahren und Prozesse sowie die zugehörigen komplexen Maschinensysteme und das Zusammenspiel mit dem Menschen – somit die ganze Fabrik.
Das könnte Sie auch interessieren:
Herausforderungen beim Wälzstoßen von Pfeilverzahnungen