Ultraschallschweißen unterstützt Innovationen in der Automobilindustrie
Gewichts- und Energieeinsparung bei gleichzeitig immer mehr Funktionen, die es in die Fahrzeuge zu integrieren gilt, werden den Leichtbau im Automobilbau weiter vorantreiben. Dabei kommt der Fügetechnik eine große Bedeutung zu.
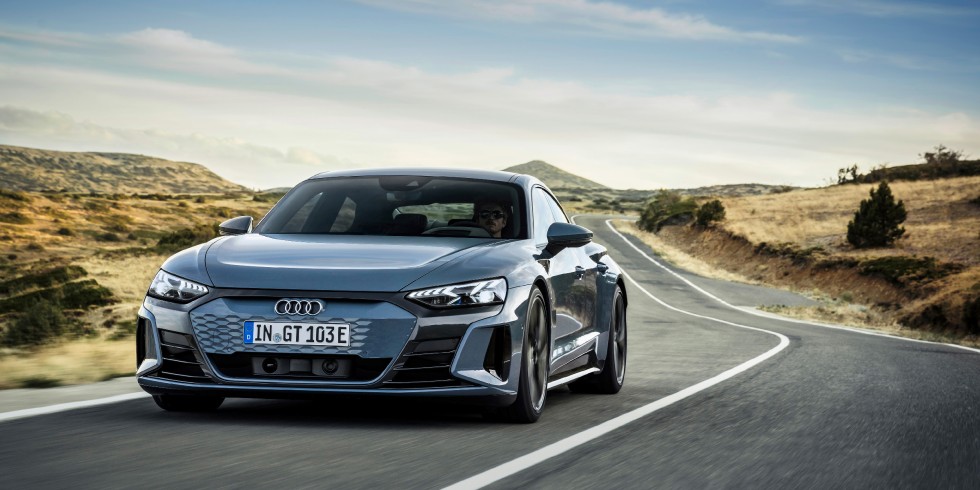
Leichtbau gewinnt im Automobilbau weiter an Bedeutung. Neben Gewichts- und Energieeinsparungen sind auch ästhetische Merkmale für das Gesamtfahrzeug von zentraler Bedeutung. Grafik: Audi AG
Bei den Neuentwicklungen spielen Themen wie autonomes Fahren und alternative Antriebskonzepte eine wichtige Rolle. Neben Gewichts- und Energieeinsparung sind aber auch ästhetische Merkmale für das Gesamtfahrzeug von zentraler Bedeutung und ein möglichst einfaches Recycling der verbauten Komponenten steht heute ebenfalls im Fokus. Traditionelle Schweiß- und Klebeverfahren stoßen dann oft an ihre Grenzen, sowohl im Hinblick auf die Nachhaltigkeit als auch in puncto Ästhetik.
Wie funktioniert das Fügen mit Ultraschall?
Als technisch und wirtschaftlich überzeugendes Fügeverfahren setzt sich wegen der genannten Defizite – gerade bei der Forderung nach hochwertigen Oberflächen – immer mehr die Ultraschalltechnologie durch. In Zukunft wird sich dieser Trend sicher noch verstärken.
Als Ultraschall werden Schallfrequenzen oberhalb der menschlichen Hörgrenze bezeichnet, also ab etwa 20 Kilohertz. Zum Schneiden und Schweißen kommen Frequenzen im Bereich von 20, 30 oder 35 Kilohertz zum Einsatz. Erzeugt werden sie durch einen Piezo-Konverter, der eine Sonotrode in eine hochfrequente resonante Schwingung versetzt, die besonders wirkungsvoll ist und dabei gleichzeitig wenig Leistung benötigt. So entstehen bei geringer thermischer Belastung von Produkt und Umgebung hochfeste Fügeverbindungen. Bei besonders empfindlichen Oberflächen ist die konventionelle lineare Ultraschall-Fügetechnik allerdings nicht immer die beste Wahl, vor allem wegen der doch immer vorhandenen thermischen Materialbelastung.
Schonendes Dünnwandschweißen ohne Abzeichnungen
Der Ultraschallspezialist Telsonic hat deshalb mit dem torsionalen „Soniqtwist“ ein Ultraschallschweißverfahren entwickelt, das gerade im Hinblick auf den Leichtbau das Anwendungsspektrum der effizienten Fügetechnik deutlich erweitert.
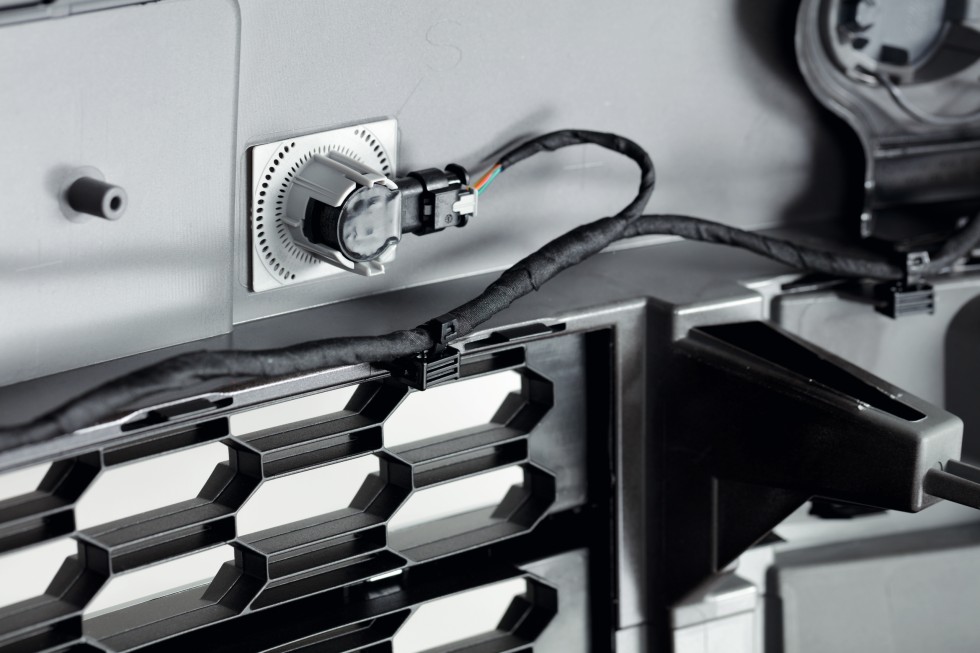
Halterungen an Dünnwandstoßfängern lassen sich mit „Soniqtwist“ besonders schonend, aber dennoch mit hoher Festigkeit anbringen. Zudem ist die Schweißzeit ausgesprochen kurz.
Foto: Telsonic
So ist das Verfahren bestens geeignet zum Beispiel für Fahrzeugstoßfänger aus Polypropylen (PP). Das patentierte und äußerst schonende Schweißverfahren ermöglicht es, die Wanddicke signifikant zu reduzieren (unter 2,5 Millimeter), ohne dass sichtbare Abzeichnungen auf Class-A-Oberflächen von bereits lackierten Fahrzeugteilen entstehen.
Das torsionale Verfahren bietet den Vorteil, dass die Schwingungen nur wenig in den Bereich um die Schweißnaht herum eingeleitet werden. Dadurch werden einerseits empfindliche Bauteile sowie Oberflächen geschont und anderseits im Schweißbereich höhere Energiedichten erzielt. So entsteht eine feste, mechanisch stabile Verbindung, die auch starken Vibrationen standhält.
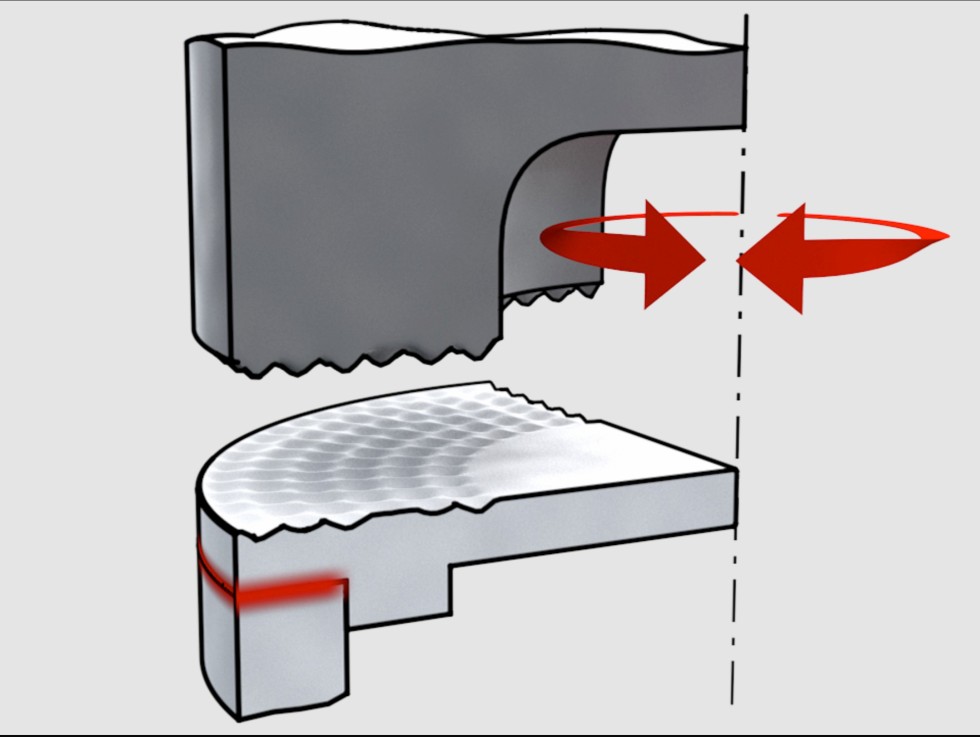
Das torsionale Ultraschallschweißen ist besonders materialschonend. Wärmeenergie wird durch die Grenzflächenreibung erzeugt. Grafik: Telsonic
So funktioniert das Verfahren: Das Schweißsystem ist in der Regel vertikal aufgebaut. Die Schwingungen werden jedoch tangential in das Bauteil eingeleitet; die Sonotrode nimmt den oberen Fügepartner mit und bewegt ihn horizontal zum unteren Teil. Durch die hohe Schwingfrequenz von 30 Kilohertz bei angepasster Amplitude und Schweißdruck entsteht eine Schmelze zwischen den Fügepartnern. Gleichzeitig sorgt die torsionale Bewegung der Sonotrode dafür, dass die Umgebung der Schweißzone durch den Ultraschall praktisch nicht belastet wird. Deshalb eignet sich das Verfahren besonders für empfindliche Anwendungen wie bei bereits lackierten Dünnwandstoßfängern, wo Schwingungen und Temperatureintrag außerhalb der Schweißzone eine Schädigung hervorrufen könnten.
Stoßfänger sind mehr als eine Verkleidung
Stoßfänger sind heute weit mehr als eine Verkleidung. Es wird z.B. immer mehr Sensorik integriert; gleichzeitig steigen die Anforderungen an das Design, wobei heutige und zukünftige Leichtbaumaterialien viel gestalterische Freiheit bieten. Dies wird vom torsionalen Ultraschallweißen wirkungsvoll unterstützt. Halterungen an Dünnwandstoßfängern lassen sich damit besonders schonend anbringen. Gegenüber einer konventionellen Ultraschallschweißung benötigt Soniqtwist dafür lediglich ein fünftel der Schweißzeit und erzielt höhere Festigkeiten.
Magna Exterios beispielsweise, ein global agierender Tier 1 Zulieferer von Verkleidungskomponenten und -systemen, setzt das Verfahren bereits seit 2017 im Produktionsprozess ein.Genutzt wird es beispielsweise für die Stoßfänger aktueller Skoda-Fahrzeuge der Serien „Fabia“, „Oktavia“ und „Kamiq“. 2018 wurde Magna dafür mit dem Automobil SPE und ACE Innovation Award ausgezeichnet (Platz 1 in der Kategorie „Enabler Technology“). Mit dem Preis werden Produkt- und Prozessleistungen gewürdigt, die für die Branche eine Vorreiterrolle spielen. Durch die minimalistische Ausführung der Sensorhalter sind zum Beispiel die Materialeinsparungen enorm. Aber auch in anderer Hinsicht kann die Ultraschalltechnik durch Nachhaltigkeit punkten: So sind keine Zusatzstoffe wie beim Kleben notwendig, was das spätere Recycling der Komponenten erleichtert. Außerdem muss nichts aushärten. Die mit Ultraschall gefügten Teile können sofort weiterverarbeitet werden.
Zulieferer sind bestens gerüstet für die Zukunft
Für die Zukunft ist die torsionale Ultraschallschweißtechnik gut aufgestellt. Schon heute können die unterschiedlichsten Kunststoffmaterialien bearbeitet werden, zum Beispiel auch Materialien mit einem hohen Naturfaseranteil oder Recycling-Kunststoffe. Telsonic arbeitet hier eng mit Anwendern aus dem Bereich Automotive und Consumer zusammen und gilt als verlässlicher Entwicklungspartner für komplexe Applikationslösungen und deren Industrialisierung. Das gilt für OEM- und Tier 1-Zulieferer ebenso wie für Maschinenbauer.
Die Anwenderwünsche der letzten Jahre wurden zudem in einem Upgrade umgesetzt. Dazu gehört beispielsweise eine platzsparende, verschlankte Bauweise, sodass sich die Soniqtwist-Sonotroden sehr gut in Robotiklösungen oder auch vorhandene Maschinen integrieren lassen.
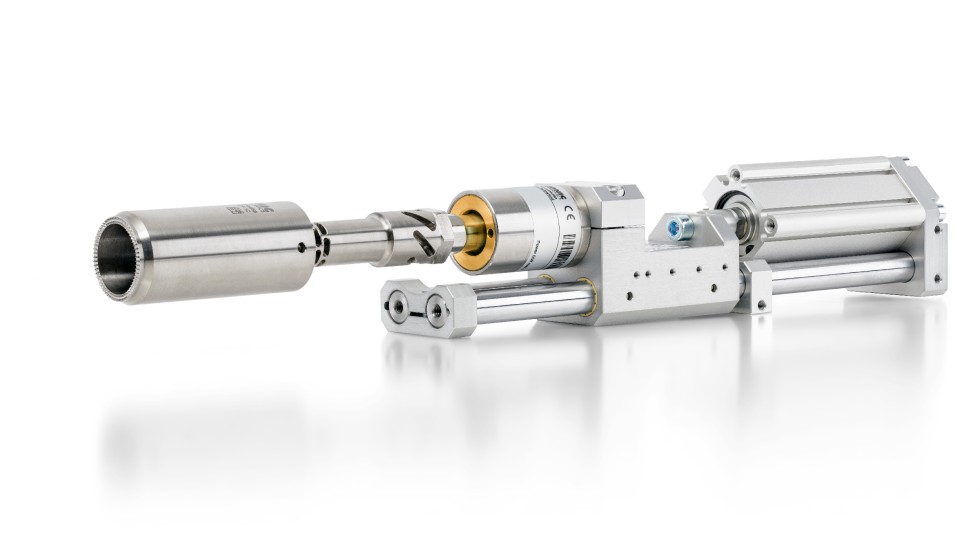
Die besonders schlanken Einbaumodule eignen sich auch für bestehende Maschinenkonzepte.
Foto: Telsonic
Das Anwendungsspektrum der patentierten torsionalen Ultraschalltechnik ist deshalb breit gefächert. Typische Einsatzbereiche in der Automobiltechnik sind beispielsweise auch Innenverkleidungen, Türschweller, Belüftungsmodule, Spoiler, Armaturenbretter und vieles mehr (wobei sich für einige dieser Applikationen auch das lineare Ultraschallschweißen eignet).
Große Expertise in der Ultraschalltechnik
Die Telsonic-Gruppe mit Hauptsitz in Bronschhofen (Schweiz) ist seit 1966 mit technologischen Ultraschall-Lösungen in Europa, Amerika und Asien vertreten. Ständige Innovationen tragen dazu bei, dass sich das Unternehmen in vielen Anwendungen einen Vorsprung erarbeitet hat, der den Anwendern einen Mehrwert bietet. Das inhabergeführte Familienunternehmen mit über 250 hoch qualifizierten Mitarbeitern hat sich auf das Kunststoff- und Metallschweißen sowie das Reinigen, Sieben und Schneiden mit Ultraschall spezialisiert (www.telsonic.com/de). Diese Kompetenzen sind bei aktuellen Trendthemen stark gefragt – dazu gehören Leichtbau, Elektromobilität, Batterieherstellung, Verpackungsindustrie, Medizintechnik und 3D-Druck.
Das könnte Sie auch interessieren:
Wie funktioniert „Sandstrahlen“ mit Licht?
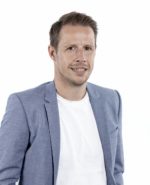
Andreas Helfenberger ist Teamleader Sales & Project Management Plastics in der Business Unit Automotive bei Telsonic in Bronschhofen/CH. Foto: Telsonic
Ellen-Christine Reiff arbeitet für das Redaktionsbüro Stutensee.