Verzahnungsherstellung: Technologietrends und Digitalisierung
Neue Entwicklungen in der Werkzeugtechnologie und moderne 5-Achs-Maschinen mit interpolierenden Achsen machen es möglich, Verzahnungen auch ohne spezialisierte, nur für diesen einen Zweck nutzbare Maschinen herzustellen. Gezeigt wird, welche Verfahren aktuell im Trend liegen und welche Werkzeuge die Wirtschaftlichkeit optimieren.
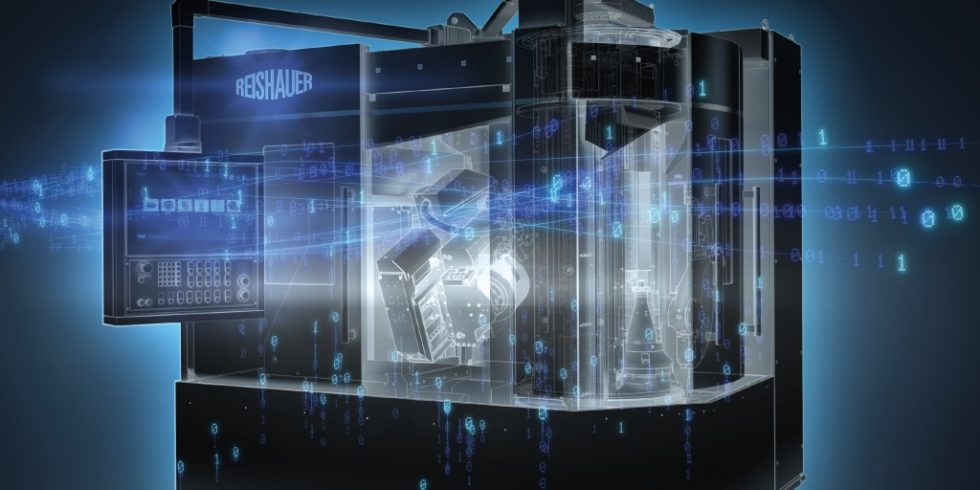
Mithilfe zahlreicher Daten, die aus der Prozess- und Komponentenüberwachung gewonnen werden, ist jedes gefertigte Zahnrad zu 100 % rückverfolgbar.
Foto: Reishauer
Viele Fertigungsverfahren führen in der Verzahnungsherstellung zum Ziel. Lange dominierende Techniken wie Stoßen oder Räumen werden durch Wälzschälen bzw. „Skiven“ abgelöst – dank intelligenter Softwareunterstützung und moderner NC-Steuerungen sowie NC-Maschinen wird dies möglich. Eine große Rolle spielen Entwicklungen im Werkzeugbereich. Auch auf die Wiederaufbereitung der meistens kostenintensiven Hochleistungstools wird eingegangen. Teil 2 des Artikels beschreibt das Verzahnen auf modernen 5-Achs-Maschinen, die Feinbearbeitung mittels Wälzschleifen und Verzahnungshonen sowie den Nutzen von Industrie 4.0 im Produktionsprozess.
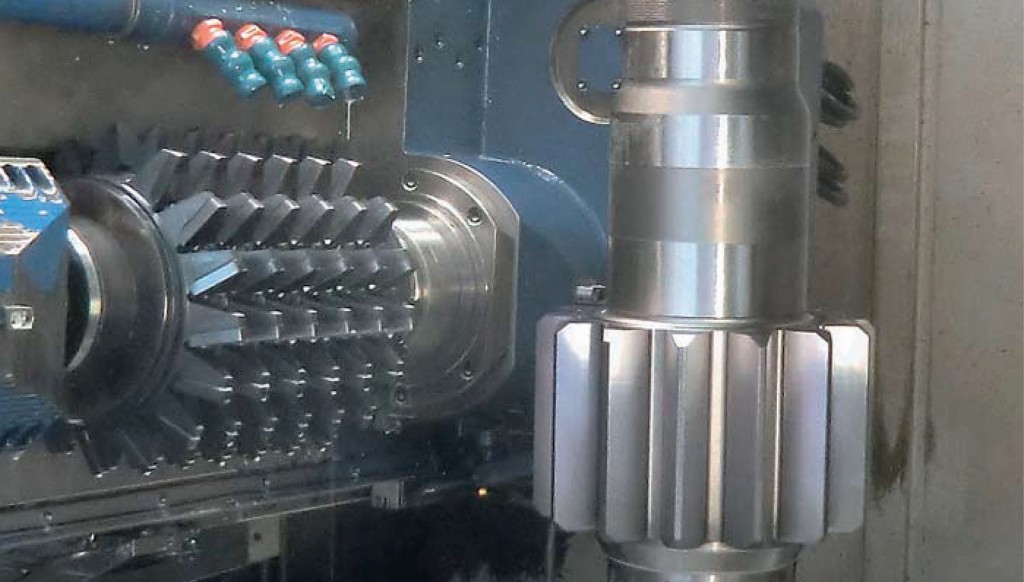
Schäl-Wälzfräser aus Hartmetall im Einsatz: Durch das Schälwälzfräsen wird der Härteverzug beseitigt und die Qualität der Verzahnung verbessert.
Foto: LMT Fette
Verzahnen auf Bearbeitungszentren
Der Werkzeugmaschinenhersteller Hermle aus Gosheim stellt hochflexible Bearbeitungszentren her, die viele komplexe Aufgaben erledigen, sich aber „ganz nebenbei“ auch zum Verzahnungsfräsen nutzen lassen. Die „C 52“ / „C52 U MT“ ist ein flexibles Multitalent mit großem Arbeitsraum auf minimaler Stellfläche. Bis zu 2000 kg schwere Werkstücke können damit in fünf Achsen simultan bearbeitet werden – bei besonderer Präzision. Die Maschinen werden in anspruchsvollen Branchen wie dem Maschinenbau, Automobilsektor oder in der Luft- und Raumfahrt geschätzt. Wie das Wälzschälen (Power Skiving) auf der C 52 funktioniert, zeigt anschaulich ein Video.
Auch die Grob-Werke, Mindelheim, zeigen in einem Firmenvideo die effiziente Herstellung von Außen- und Innenverzahnungen mithilfe von Wälzschälfräsern auf dem Universal-Bearbeitungszentrun „G550T“.
Der Werkzeugmaschinenbauer Index, Esslingen, bietet das Kegelradverzahnen auf seinen Fräs-/Drehzentren „R200/300“ an. Hierzu hat er ein Paket „Kegelradabwälzfräsen“ entwickelt, das aus einem speziellen Steuerungszyklus und vier Messerköpfen mit modulabhängigen Schneidplatten besteht.
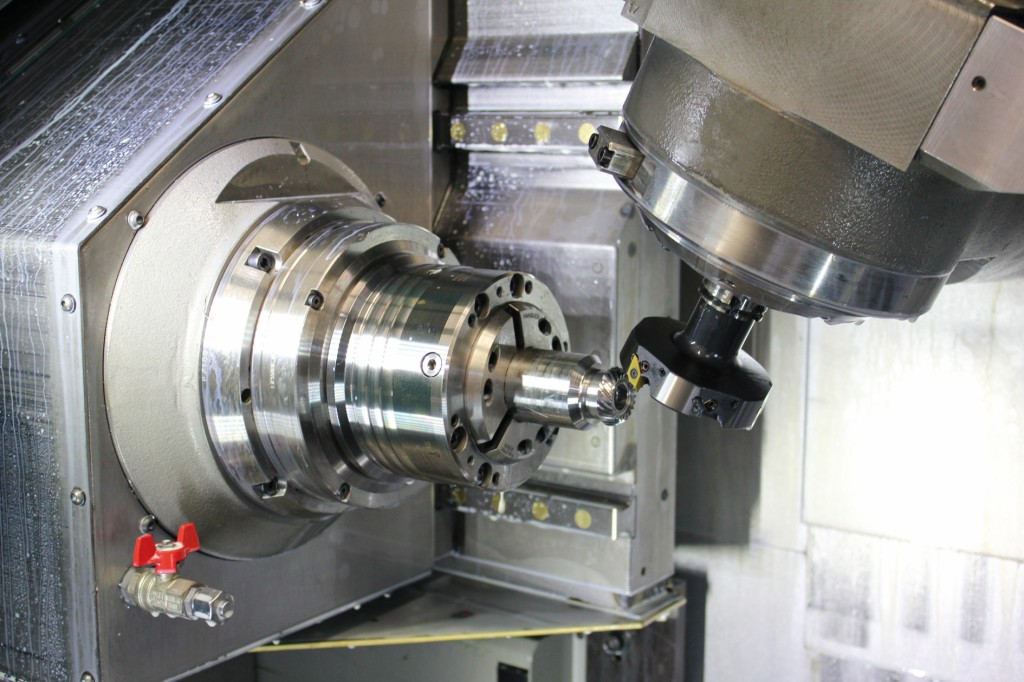
Mit einem Technologiepaket werden die Dreh-/Fräszentren zu Verzahnungsmaschinen: Ein speziellerr Steuerungszyklus sorgt dafür, dass spiralverzahnte Kegelräder durch Abwälzfräsen im kontinuierlichen Teilverfahren entstehen.
Foto: Index
Bei vielen Zulieferunternehmen rücken die Produktionsprozesse für steigende Stückzahlen in den Fokus. Mit der zweispindligen Pick-Up-Drehmaschine „VL 1 T“ von von Emag, Salach, werden zwei gleiche Kegelräder simultan in einem Arbeitsraum bearbeitet. Zudem ist es einfach möglich, diese Maschine per Roboterzelle und Schwenktisch zu beladen. So verkürzt sich die Taktzeit auf bis zu 4,5 Sekunden. Die Automatisierungslösung kann in einem Lehrfilm verfolgt werden.
Wälzschleifen transparent gemacht dank Prozessüberwachung
Das kontinuierliche Wälzschleifen hat sich auch nach Ansicht von Reishauer, Wallisellen/CH, als das produktivste Verfahren der Hartfeinbearbeitung von hochgenauen Zahnrädern durchgesetzt. Auf der Wälzschleifmaschine aus der Schweiz werden Abricht- und Schleifintensität mittels intelligenter Echtzeit-Datenverarbeitung und erprobten Algorithmen konstant überwacht. Die aufgezeichneten Prozessdaten jedes einzelnen Zahnrads werden dazu aufgezeichnet, in einer Datenbank abgelegt und bleiben 100%ig rückverfolgbar. Mithilfe der ebenfalls gespeicherten Toolingdaten sowie auch der Werkstückidentifikation (DMC) ergeben sich umfassende Analysemöglichkeiten. Grenzüber- oder unterschreitende Werkstücke werden automatisch ausgeschleust. Zyklische automatische Prüfabläufe kontrollieren zudem permanent alle im Prozess beteiligten Achsen der Schleifmaschine. Hieraus lassen sich frühzeitig elektromechanische Abweichungen diagnostizieren und Wartungen optimal planen.
Industrie 4.0 setzt sich auch beim Verzahnen durch
Die Verzahnungsindustrie befindet sich – wie die gesamte Produktionstechnik – in einem Wandel. Produktionssysteme werden zunehmend digitalisiert. Gefordert sind entsprechend „intelligente“ Systeme, die den Bediener unterstützen und Produktionssysteme aktiv steuern. Fertigungssysteme müssen sich selbst optimieren. Viele Bausteine für diesen Prozess hat die Firma Klingelnberg entwickelt. Für die Fertigbearbeitung von Zahnrädern bieten die Hückeswagener Wälzschleifmaschinen und -messzentren „aus einer Hand“. Das Know-how von Kegelrädern wurde mit der Maschinengeneration „Speed Viper“ auf Stirnräder übertragen. Entstanden ist ein komplettes System mit neuer Auslegungs- und Bediensoftware sowie innovativer Maschine. Die Stirnradmaschinen lassen sich zudem direkt mit den eigenen Präzisionsmesszentren wie dem „P 26“ vernetzen.
Der Spezialist bietet Lösungen für vielfältige Zahnradgeometrien. Mit der Multifunktionsmaschine „Viper 500 MFM“ ist 2019 der Einstieg in den Markt der Zykloidenverzahnungen gelungen; dies eröffnet zum Beispiel der Roboterindustrie neue Perspektiven. Um die hier geforderten engen Toleranzen einzuhalten, wurde das Prinzip „Done-in-One“ mit dem intern entwickelten System „Adaptive Grinding“ kombiniert. Was steckt genau dahinter? Die beiden genauigkeitsbestimmenden Arbeitszyklen Bohrungs- und Verzahnungsschleifen sind auf einer Maschine zusammengefasst. Beim Adaptive Grinding wird durch eine geschickte Abfolge von Schleif- und Messoperationen der Fußkreisdurchmesser der Zykloide relativ zu einem Referenzdurchmesser hergestellt. Dadurch lassen sich die kritischen Toleranzen für eine derartige Verzahnung prozesssicher einhalten.
Auch für die Fahrzeugindustrie gibt es maßgeschneiderte Lösungen – wie die Stirnrad-Wälzschleifmaschine „Speed Viper2“ mit Doppelspindelkonzept. Sie erfüllt die hohen Produktivitätsanforderungen der Branche und deren Zulieferer. Zwei Werkstückspindeln im Drehturm erlauben das zeitgleiche Be- und Entladen des Zahnrads während des Schleifprozesses. Spezielle Schleifschnecken sowie ein automatisches Werkzeug-Spannsystem mit integrierter Wuchteinheit verkürzen die Rüstzeiten. So gelang es, die aus dem Markt bekannten Nebenzeiten deutlich zu reduzieren und die Produktivität zu maximieren.
Software- und Technologie-Know-how sind entscheidend
Besonderer Wert wird bei Klingelnberg auf die Softwareunterstützung gelegt. „Gear Engineer“ ist ein System für das Wälzschleifen, das zu jedem Produktionsschritt einen „digitalen Zwilling“ der Stirnräder erschafft.
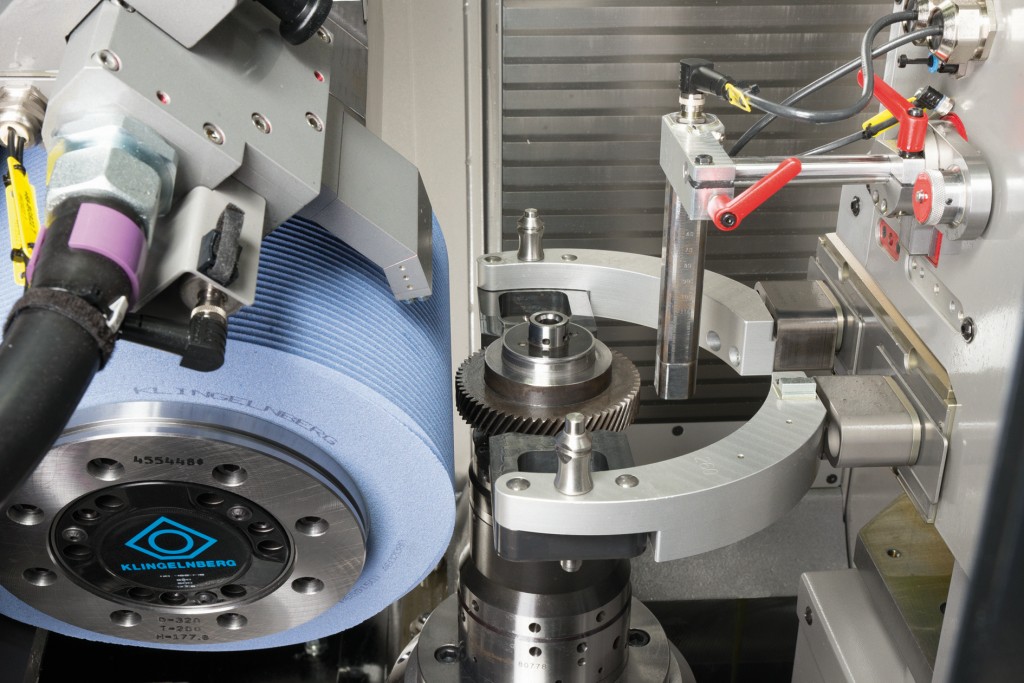
Die Spezialisten aus Hückeswagen bieten innovative Technologien und Maschinen unter anderem für das hochproduktive Wälzschleifen an.
Foto: Klingelnberg
Der Ingenieur hat ein Werkzeug zur Hand, um die Zahnradgeometrie zu simulieren. Bereits bei der Verzahnungsauslegung lässt sich so feststellen, welche fertigungsbedingten Abweichungen auftreten und ob sich diese negativ auf das Geräuschverhalten auswirken werden. Das IT-System führt Auslegungs- und Produktionsdaten zusammen – damit können spannende Fragestellungen rund um Werkzeugstandzeit, Maschinenstatus, Bauteilverfolgung und Dokumentation beantwortet werden. Anwendungen wie „SmartTooling“ für die Kegelradproduktion und das Closed-Loop-Production-System für das Stirnrad-Wälzschleifen sind ebenfalls auf dieses IT-System gehoben worden. Der vollautomatisierte Qualitätsregelkreis legt in der Stirnradproduktion eine wichtige Grundlage für einen Produktionsprozess im Sinne von Industrie 4.0.
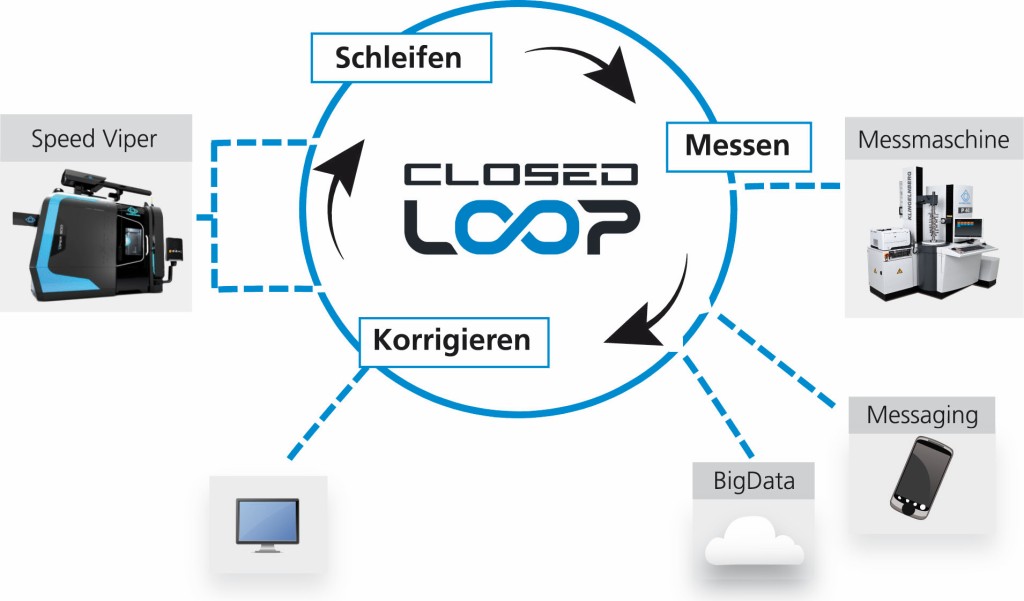
Industrie 4.0 „inklusive“: Das Produktionssystem einschließlich des Qualitätsregelkreis „Closed Loop“, der Verzahnungsschleifen und Messtechnik verbindet, sorgt für eine effektive und hochgenaue Fertigung von Zahnrädern.
Foto: Klingelnberg
Auch Werkzeuge werden „raffinierter“
Ein Technologieführer beim Wälzfräsen mit besonders breitem Werkzeugprogramm ist LMT Fette, Schwarzenbek. Firmenvideos zeigen die Schwerpunkte des Portfolios von kleinmoduligen Automotive-Fräsern bis hin zu großmoduligen Verzahnungswerkzeugen. Mit neuen Schneidstoffen – vom PM-HSS (Pulvermetallurgie-High Speed Steel) über „SpeedCore“ bis zum Hartmetall – und neuartigen nanostrukturierten Beschichtungen wird die Werkstoffpalette stetig erweitert. Speedcore ist ein Schneidstoff mit einer deutlich höheren Warmhärte, der auf intermetallischen Phasen aus aus Kobalt, Molybdän und Eisen sowie der nanostrukturierten Beschichtung „Nanosphere 2.0“ beruht. Systeme, die mehrere Aufgaben wie Verzahnen und Anfasen ohne Werkzeugwechsel erledigen, steigern zusätzlich die Effizienz.
Verschiedene Verzahnungstechnologien lassen sich auch mit den Werkzeugen von Horn, Tübingen, realisieren – von der Bearbeitung einer Zyklo-Palloid-Verzahnung bis hin zur Herstellung der Außen- und Innenverzahnungen durch Stoßen und Wälzschälen, zu sehen hier.
Ein weiterer Hersteller, der spezialisierte Werkzeuge für das Verfahren Skiven entwickelt hat, ist Sandvik Coromant, Düsseldorf. Mit den vielseitigen Tools des schwedischen Anbieters lassen sich komplette Bauteile mit Verzahnungen und Steckverzahnungen auf Multitask-Maschinen oder Bearbeitungszentren in nur einer Aufspannung fertigen; außerdem sind sie ebenso auf speziellen Wälzschälmaschinen nutzbar. Das Power Skiving (mit Bohrungs- und Schaftwerkzeugen sowie Wendeschneidplattenfräsern) sei um ein Vielfaches schneller als das Wälzstoßen und flexibler als das Räumen – so die Ansicht des Werkzeugherstellers.
Verzahnungshonen statt Wälzschleifen für die Endbearbeitung?
Die Endbearbeitung von Zahnrädern für Automobilgetriebe findet vorrangig durch Wälzschleifen oder Verzahnungshonen statt. Das Wälzschleifen mit keramisch gebundenen Korund- beziehungsweise Sinterkorund-Tools ist nach Ansicht des Werkzeugherstellers Hermes Schleifmittel gut geeignet, Aufmaße nach dem Härten abzutragen, jedoch ist die Oberflächenqualität oft nicht ausreichend. Das Verzahnungshonen erzeugt hingegen die geforderten Oberflächenqualitäten und -strukturen auf den Zahnradflanken: geringe Rauheiten im Bereich Rz < 1 µm bei gleichzeitig hohen Traganteilen. Aufgrund der erzeugten Topografie wird die häufig gewünschte Reduzierung der Geräuschemissionen erzielt.

Das Schleifen und Polieren von Zahnrädern in einer Aufspannung mit modernen Kombinationswerkzeugen sorgt für geringere Geräuschemissionen bei deren Einsatz.
Foto: Hermes Schleifmittel / Fraunhofer IWU
Das „Power-Honen“ mit keramisch gebundenen Sinterkorund-Honringen ist aktuell das effizienteste Verfahren, Zahnräder hochproduktiv bei gleichzeitiger hoher Qualität zu bearbeiten. Nicht ganz so leistungsfähig wie keramisch gebundene Werkzeuge sind Honringe mit Kunstharzbindung. Aufgrund der leicht elastischen Bindung ergeben sich höhere Oberflächenqualitäten der Verzahnungen, die die Anforderungen von Getrieben für E-Fahrzeuge bestens erfüllen. Für dieses „Fein-Honen“ bieten die Hamburger die passenden Werkzeuge unter der Produktreihe „Profine GH“ an.
Die aktuellsten Generationen an Elektromotoren haben noch höhere Anforderungen an Geräuschemissionen, was zur Folge hat, dass auch die Hohlräder in Planetengetrieben bearbeitet werden müssen. Dafür wurde das Portfolio über die Honringe hinaus um Honräder mit keramischer und elastischer Bindung erweitert. In Kooperationen mit Premium-Automobilherstellern entstanden die Qualitäten, die künftig die Getriebeindustrie fordert. Kombinationswerkzeuge, die aus der aufwendigen Verbindung von zwei gänzlich unterschiedlichen Schleifwerkzeugen bestehen, erlauben zudem eine hochproduktive Schruppbearbeitung sowie eine hochpräzise Schlichtbearbeitung von Zahnrädern in einer Aufspannung.
Im Trend: Nachschliff von gebrauchten Werkzeugen
Weil die Herstellung von neuen Werkzeugen für das Wälzschälen oftmals mit hohen Werkzeugkosten verbunden ist, gewinnt das Thema Nachschleifen an Bedeutung. Dies wird nicht nur von den Originalherstellern, sondern auch von Dienstleistern angeboten, beispielsweise von der Hommel Schleifmanufaktur in Bochum. Der Werkzeug-Aufbereitungsbetrieb sorgt für den Nachschliff sowie das Beschichten von Wälzschälrädern.
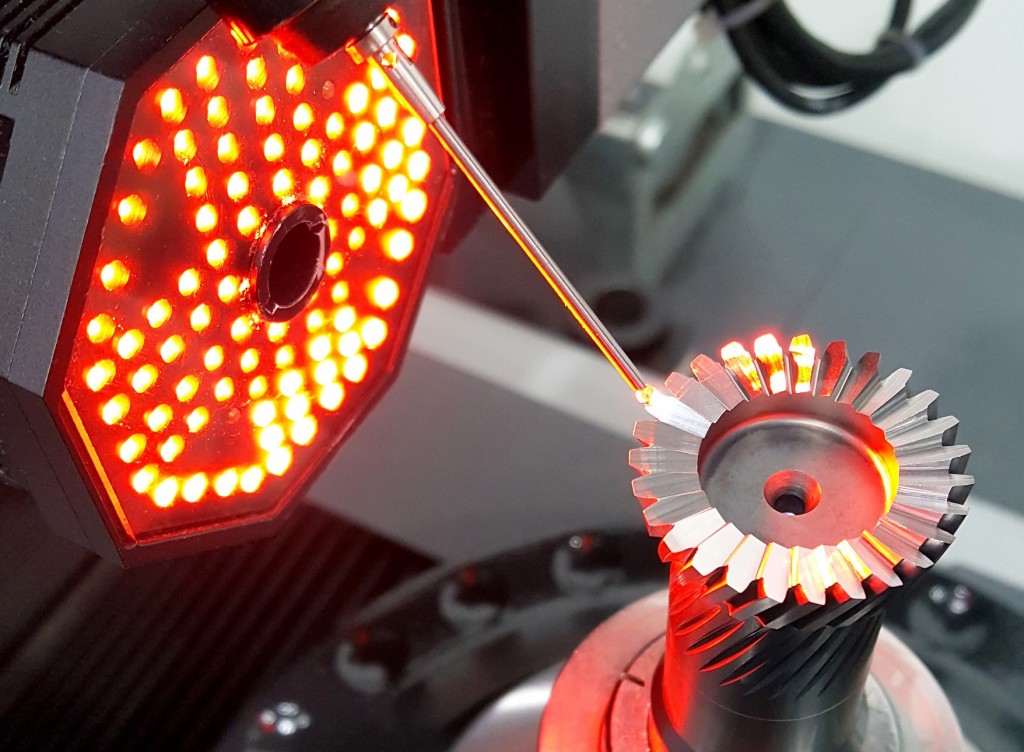
Die Wiederaufbereitung teurer Hochleistungswerkzeuge wie Wälzfräser wird inzwischen auch von Dienstleistern angeboten.
Foto: Hommel
Von moderner Software unterstützt, schleifen erfahrene Techniker die Tools an CNC-Werkzeugschleifmaschinen nach. Es folgt eine Beschichtung, um die Standzeit zu optimieren – in Bochum wird dazu auf „Balinit Alcrona-Pro“ von Oerlikon Balzers zurückgegriffen. Nach Angaben des Aufbereiters arbeiten die Werkzeuge anschließend auch bei hoher Belastung im Zerspanungsprozess wieder zuverlässig.
Das könnte Sie auch interessieren:
Birgit Etmanski, promovierte Maschinenbauingenieurin, ist Chefredakteurin der Zeitschrift VDI-Z