Warmfeste Superlegierungen mit kurzer Bearbeitungszeit zerspanen
Die vollen Auftragsbücher in der Luftfahrtbranche sorgen für eine hohe Auslastung der Triebwerkshersteller und deren Zulieferer. Eine Verkürzung der Bearbeitungszeit von Bauteilen ist daher besonders wünschenswert. Bei warmfesten Superlegierungen beträgt die Schnittgeschwindigkeit von Hartmetallfräsern etwa 50 m/min. Keramikfräser bieten einen anderen Ansatz: mit Schnittgeschwindigkeiten bis zu 1000 m/min.
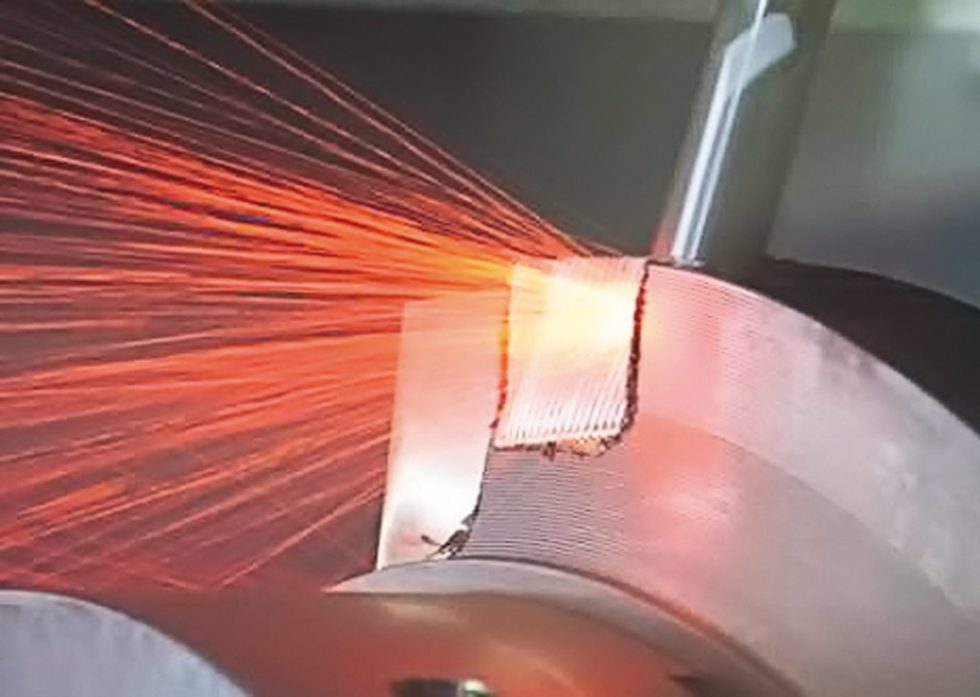
Keramikfräser MC275 beim Vollnutfräsen von Inconel 718 mit 670 m/min Schnittgeschwindigkeit. Produktivität und Gesamtspanvolumen sind deutlich höher als mit Hartmetallfräsern. Bild: Walter
Das Produktprogramm der Walter AG umfasst zwei Keramikfräser-Familien: Der „MC275“ mit Universalgeometrie passt für die meisten Anwendungsfälle; der „MC075“ ist als Hochvorschubfräser konzipiert. Beide Produktreihen, Bild 1, gibt es mit Schneidendurchmessern von 8 mm bis 25 mm Die Werkzeuge von 8 mm bis 12 mm sind als Integralfräser, die Werkzeuge von 12 mm bis 25 mm sind als „ConeFit“-Fräser verfügbar.

Bild 1. Übersicht der Keramikfräser „MC275“ mit Universalgeometrie sowie „MC075“ mit Hochvorschubgeometrie als Schaftfräser und „ConeFit“-Lösung aus dem Standardsortiment. Bild: Walter
In beiden Fällen besteht nur der Kopf des Werkzeugs aus Keramik. Dieser ist entweder auf einen Hartmetallschaft oder auf einen Hartmetall-ConeFit-Träger aufgelötet. Im Prinzip könnte zwar der gesamte Fräser aus Keramik bestehen, ein Hartmetallschaft erhöht jedoch die Biegefestigkeit und Dämpfung des Werkzeugs. Im Vergleich zu Vollkeramikwerkzeugen lassen sich dadurch größere Auskraglängen und höhere Zerspanvolumen realisieren.
Einsatzmöglichkeiten von Keramik-Schneidstoffen
Der Anwendungsbereich von keramischen Schneidstoffen umfasst die warmfesten Legierungen der ISO S-Gruppe auf Nickel-, Kobalt- und Eisenbasis. Superlegierungen auf dieser Basis sind: Inconel 718, René 80, Nimonic 80A, Haynes 556, Mar-M-247 und Stellite 31. Warmfeste Superlegierungen werden auch als HRSA (Heat Resistant Super Alloys) bezeichnet. Diese werden bevorzugt in Baugruppen von Flugzeugtriebwerken eingesetzt, die hohen Temperaturen ausgesetzt sind.
Der Schneidwerkstoff Keramik ist angepasst an die Fräsbearbeitung. SiAlON-Keramiken sind unempfindlicher gegenüber Temperaturschwankungen als Whisker-verstärkte Keramiken. Für Fräsoperationen sind sie deshalb die erste Wahl. Durch den unterbrochenen Schnitt variiert die Temperatur an der Schneide und der Einsatz von Kühlmedien kann die Temperaturdifferenz weiter steigern. Ein Thermoschock-Effekt tritt ein. Beim Zerspanen von Superlegierungen mit Keramikfräsern empfiehlt Walter daher die Trockenbearbeitung. Hinzu kommt die ökologische und ökonomische Wirkung, die der Anwender beim Verzicht auf Kühlschmierstoffe erzielt.
Verschleißursachen
Hauptgründe für Verschleiß beim Fräsen von Nickelbasislegierungen mit Keramik sind zum einen der temperaturbedingte chemische Verschleiß, zum anderen die Aufbauschneidenbildung. Während der chemische Verschleiß beziehungsweise Diffusionsverschleiß kontinuierlich den Schneidstoff schwächt, ist der Verschleiß durch die Aufbauschneide nicht berechenbar und geschieht in Sprüngen. Aufgrund der hohen Bearbeitungstemperatur, Bild 2, und der hohen Zähigkeit von Superlegierungen selbst bei hohen Temperaturen (Beispiel Inconel 718; Rm = 880 N/mm² bei 750 °C) können große Spanablagerungen am Werkzeug entstehen.
Diese verschmelzen mit der Oberfläche des Schneidstoffs; beim Ablösen können Teile der Keramik abplatzen. Die aufgeschweißten Ablagerungen am Werkzeug sind in Bild 2 sehr gut zu erkennen.
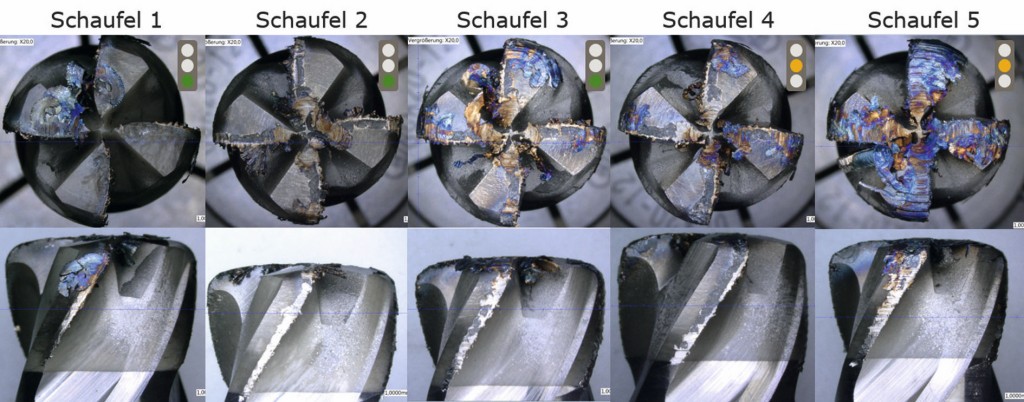
Bild 2. Trotz deutlicher Aufbauschneide und einer Abplatzung ist der Keramikfräser nach fünf Schaufeln noch voll einsatzfähig. Die Färbungen der Spanaufklebungen weisen auf eine hohe Bearbeitungstemperatur hin. Bild: Walter
Obwohl die hohen Temperaturen bei der Bearbeitung von HRSA einen negativen Einfluss auf die Standzeit haben, sind sie erforderlich. Erst durch sie reduziert sich die Materialhärte und der Werkstoff lässt sich effizient zerspanen.
Schnittdaten variieren
Die Schnittdaten ergeben sich aus dem Schneidstoff sowie dem zu bearbeitenden Werkstoff. Der spröde, aber warmfeste Schneidstoff kann zwar bei hohen Temperaturen verwendet werden, aber die geringe Kerbschlagfestigkeit bedingt geringe Zahnvorschübe von 0,02 mm bis 0,05 mm sowie kleine Eingriffsverhältnisse mit ap = 5 % vom Dc beim Vollnuten und ae = 5 % vom Dc beim Umrissfräsen mit maximaler Schneidenlänge. Die Ausnahme bildet der MC075 mit Hochvorschubgeometrie mit fz = 0,15 mm und einem ap 8 apf. Die Schnittgeschwindigkeit für beide Produktreihen liegt zwischen 400 m/min und 1000 m/min.
Der Vergleich von Fräsern mit Hartmetall- und Fräsern mit Keramikschneide könnte nicht gegensätzlicher ausfallen. Die Verschleißaufnahmen in Bild 2 zeigen, warum die Keramikfräser nur zum Schruppen eingesetzt werden: Wo ein Hartmetallfräser längst „am Ende wäre“, sind Verschleißerscheinungen wie Abplatzungen an der Schneide und Verschleißmarkenbreiten über 0,5 mm für den keramischen Schneidstoff kein Grund, „aufzugeben“.
Dies sind Gegensätze, die auch beim Vergleich der Schnittparameter deutlich werden. Schaftfräser mit 10 mm Durchmesser beim Vollnuten von Inconel 718 werden beispielhaft verglichen, siehe Tabelle: Die deutlich höhere Vorschubgeschwindigkeit der Keramik kann trotz größerer Schnitttiefe vom Hartmetall nicht eingeholt werden.
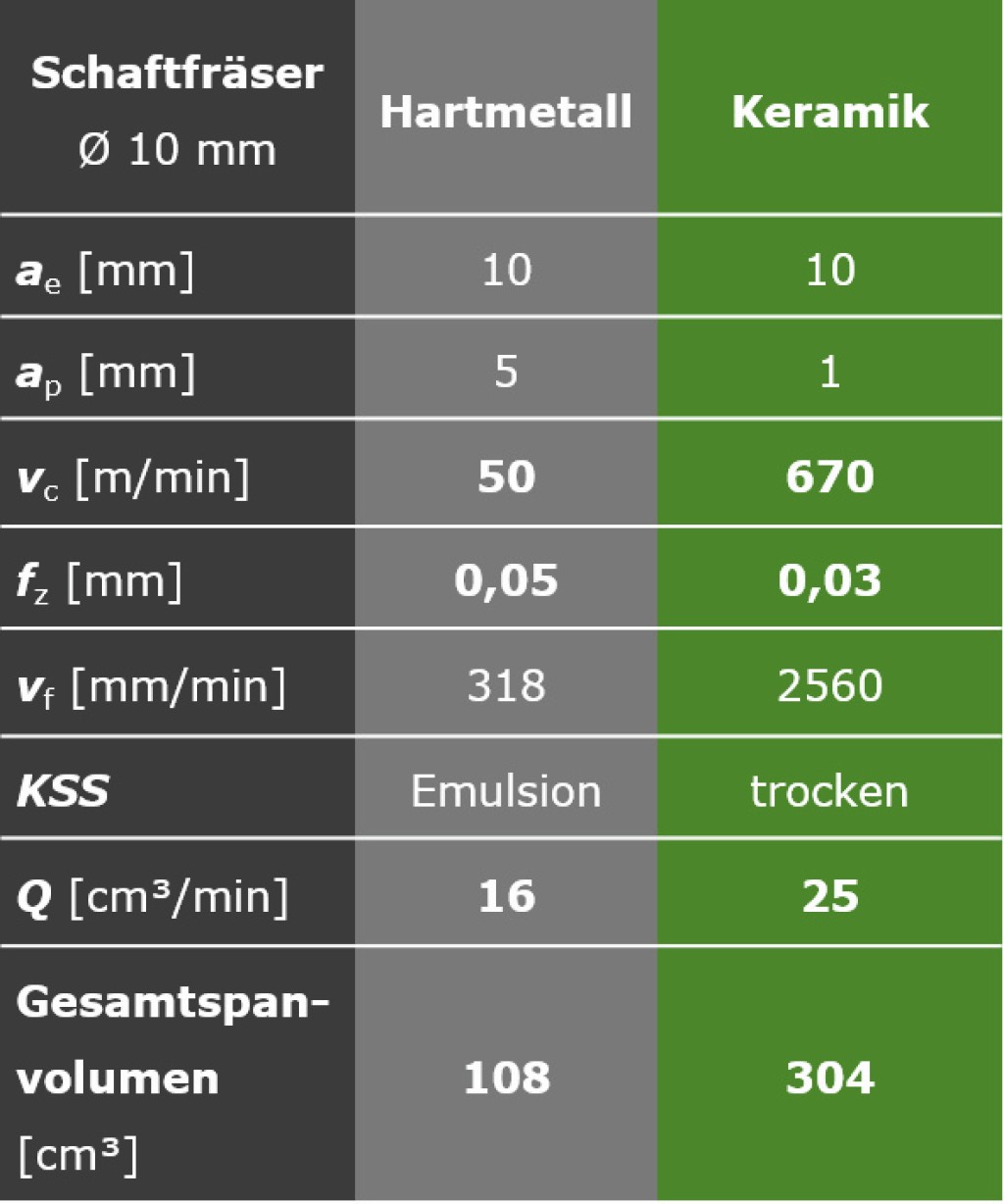
Tabelle. Inconel-Bearbeitung: Der Vergleich zeigt die viel höheren Werte für Schnittgeschwindigkeit, Zeitspanvolumen und Gesamtspanvolumen des Keramikfräsers. Bild: Walter
In diesem Fall ist das Zeitspanvolumen mit keramischer Schneide um 56 % höher. Zudem fällt das Gesamtspanvolumen um 180 % höher aus als beim Hartmetallfräser. Zeitspanvolumen und Gesamtspanvolumen sind die Kenngrößen, bei denen die Keramik gegenüber dem Hartmetall eindeutige Vorteile zeigt. Die kürzere Bearbeitungszeit gestattet bei einem identischen Maschinenpark höhere Stückzahlen; bei einer Neuauslegung des Maschinenparks kommt der Anwender mit weniger Bearbeitungszentren aus. Aufgrund des höheren Gesamtspanvolumens reduzieren sich die Werkzeugkosten.
Anwendungsbeispiel
Ein klassisches Bauteil aus einer Nickelbasislegierung ist ein Blisk (Flugzeugtriebwerk). Dieses rotierende Integralbauteil besteht aus einer Scheibe und vielen Schaufeln. Die Zwischenräume zwischen den Schaufeln können mit Hartmetallfräsern im Schruppprozess zerspant werden. Die Bearbeitungszeit dafür beträgt etwa 30 min. Der Keramikfräser MC075 mit der Hochvorschubgeometrie arbeitet dieselben Zwischenräume in 10 min heraus. Dabei werden in einer warmfesten Nickelbasislegierung mit einer Härte von 44 HRC beziehungsweise einer Zugfestigkeit von 1400 N/mm² Vorschubgeschwindigkeiten von 9500 mm/min erreicht – Werte, die eher in der Aluminiumzerspanung zu vermuten wären.
Trotz der herausragenden Bearbeitungsmöglichkeiten stellt sich die Frage, ob es bei den hohen Zerspantemperaturen, die Keramikfräser erreichen, nicht zu Beschädigungen im Werkstoff kommt? Da die Werkzeuge aber nur zum Schruppen verwendet werden, muss lediglich sichergestellt sein, dass die Tiefe der Schädigung im Werkstoff geringer ist als das Schlichtaufmaß.
In Zusammenarbeit mit dem Fraunhofer IPT in Aachen wurden die Tiefe und der Grad der Aufhärtung gemessen – von verschieden intensiv verschlissenen Keramikfräsern, beim Vollnuten in Inconel 718. Die Härtemessung geschah, nachdem die Werkzeuge jeweils 13 beziehungsweise 14 Nuten mit mittlerem Verschleiß sowie 23 Nuten mit sehr starkem Verschleiß gefräst hatten. Um die maximale thermische Belastung zu erfassen und auszuwerten, wurden die unteren Messpunkte der Nut gewählt, Bild 3.
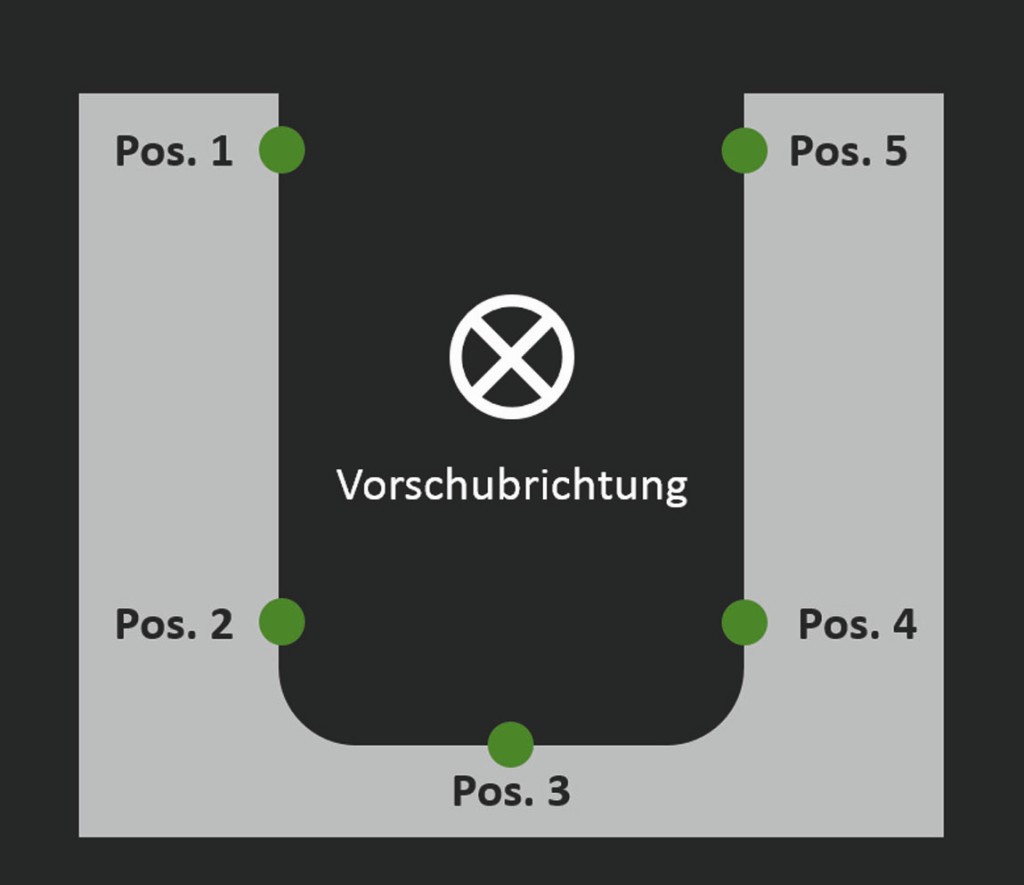
Bild 3. Die kritischsten Messpunkte sind Position 2 bis 4 aufgrund der erhöhten Temperatur am Boden der Nut. Bild: Walter
Für eine korrekte Erfassung der Härte fanden die Messungen wie in Bild 4 gezeigt statt.
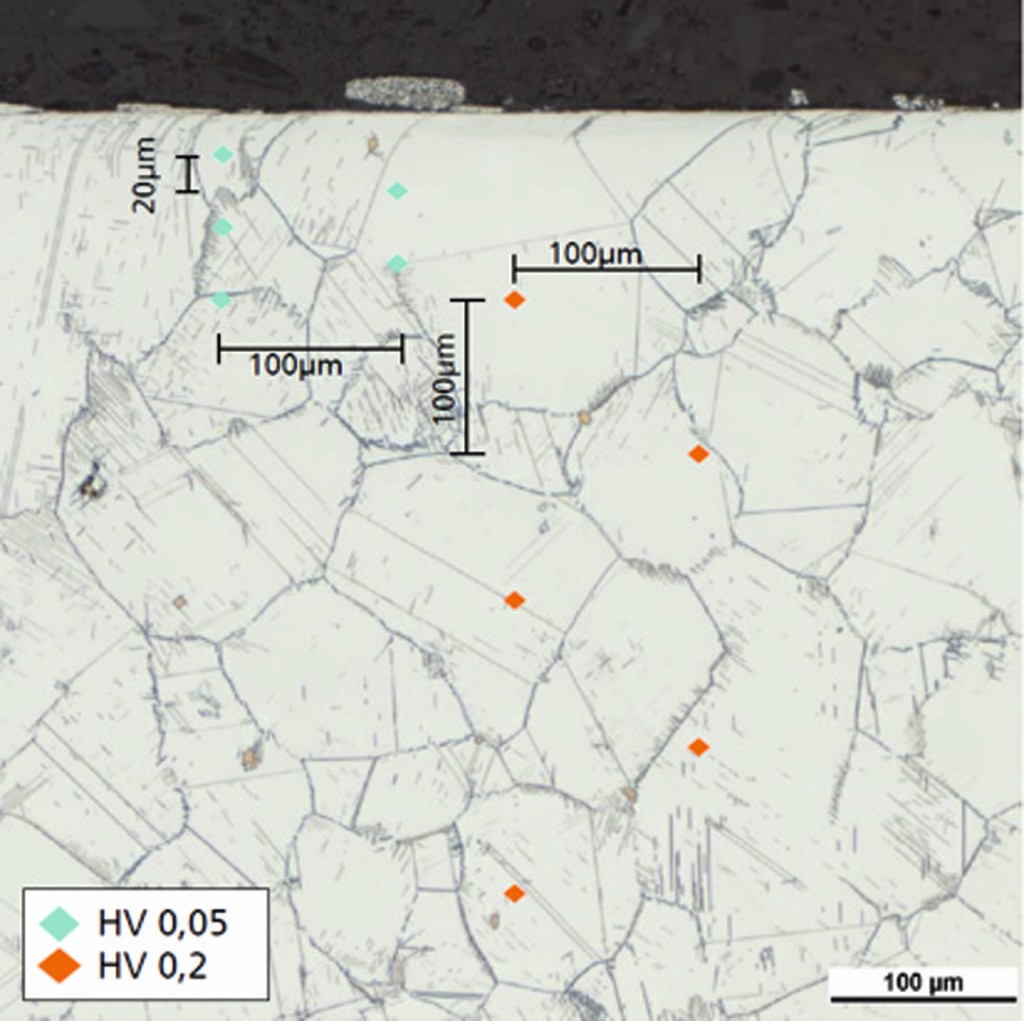
Bild 4. Das Gefügebild zeigt die Anordnung der Messpunkte für die Härtemessung. Eine Aufhärtung über das Schlichtaufmaß hinaus ist unzulässig. Bild: Fraunhofer IPT
Die Grundhärte des Werkstoffs beträgt 446 HV. Ergebnis: Innerhalb einer Tiefe von 100 mm wurde eine Aufhärtung auf bis zu 640 HV festgestellt. Eine Aufhärtung ab 200 mm Tiefe konnte – unabhängig vom Verschleiß der Werkzeuge oder der Messrichtung – nicht nachgewiesen werden, Bild 5.

Bild 5. Die Diagramme zeigen eine Aufhärtung des Werkstoffs bis zu einer Tiefe von 100 mm. Ab einer Tiefe von 200 mm wurde keine Aufhärtung gemessen, unabhängig vom Werkzeugverschleiß und der Messposition. Bild: Fraunhofer IPT
Da das allgemeine Schrupp-Aufmaß drei bis fünf Zehntelmillimeter beträgt, ist eine Schädigung nach dem Schlichtprozess durch das Vorschruppen mit Keramik demnach nicht zu erwarten.
www.walter-tools.com
Stefan Benkóczy ist Component Manager Aerospace bei der Walter AG in Tübingen.