Was leistet Additive Fertigung im Musikinstrumentenbau?
Wenn (Blas-)Musikinstrumente mittels Additiver Fertigung hergestellt werden, hat dies deutliche Vorteile hinsichtlich der Designfreiheit. Bis zur möglichen industriellen Implementierung ist es aber noch ein langer Weg – eine Studie zeigt Chancen und Probleme.
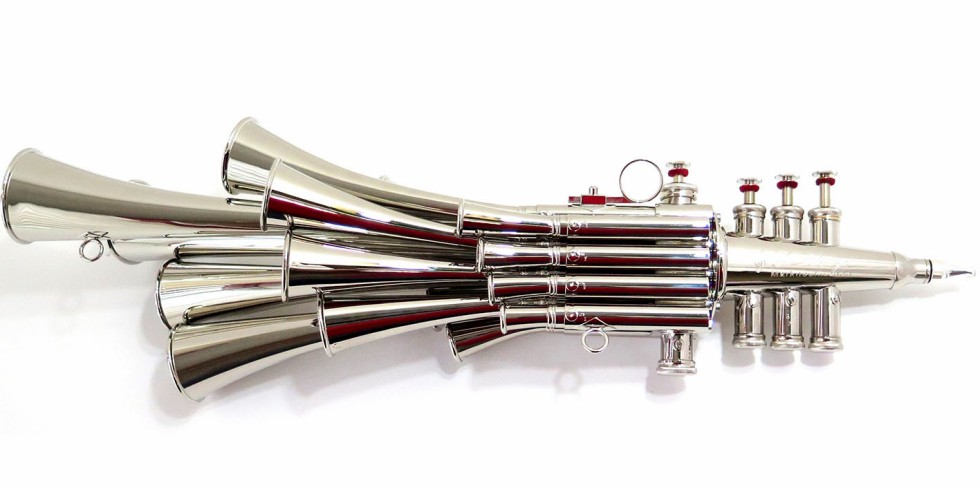
Additive Fertigungstechnologien in neuen Anwendungsfeldern: Im Musikinstrumentebau erlauben sie es zum Beispiel, die Fertigungszeit von Schalmeien zu verkürzen und Teile des Instruments kundenindividuell zu gestalten. Außerdem lassen sich Fachkraftprobleme entschärfen.
Foto: Voigt
Was ist nötig, um die fortschrittliche Technologie des Additive Manufacturing (AM) in diesem neuen Anwendungsfeld zu etablieren und integrieren? Die Gründe für die bisherige zögerliche Anwendung liegen vor allem in der Komplexität des Themas. Die Betrachtung der gesamten Prozesskette soll Abhilfe schaffen, um die Möglichkeiten der Additiven Fertigung im klassischen Musikinstrumentenbau zu beleuchten und die Hemmnisse bei den Anwendern zu überwinden.
Bedarfe offenlegen: Chancen dank Individualisierung und Automatisierung
Die Potentiale von AM eröffnen neue Wege, komplexe Teile zügig zu fertigen und durch Funktionsintegration die Prozessketten der Fertigung deutlich zu kürzen. Neben den bekannten industriellen Bereichen haben diese Technologien auch im Musikinstrumentenbau bereits Fuß gefasst [1]. Unterschiedlichen Studien befassen sich mit dem Bau von Musikinstrumenten-Prototypen,
Die jüngsten Ansätze, Musikinstrumente additiv zu fertigen, zeigen nicht nur die Möglichkeiten zur Fertigung der Einzelteile, sondern regen auch zum Überdenken der kompletten Musikinstrumente an. Besonders wegen des komplexen Fertigungsprozesses der Metallblasinstrumente verspricht die Einführung der AM-Technologie eine sinnvolle Ergänzung zur bisherigen Fertigung.
In diesem Beitrag werden die Ergebnisse des im Rahmen des BMBF-Programmes „WIR! – Wandel durch Innovation in der Region“ geförderten Forschungsprojektes zu Implementierung der AM-Technologien bei den Musikinstrumentenbauern in Vogtland dargestellt, die sich auf den in der Region stattfindenden Strukturwandel beziehen.
Die Prozesskette der konventionellen Fertigung
Musikinstrumente im Allgemeinen und Blasinstrumente im Speziellen bestehen aus mehreren wichtigen hochqualitativen Elementen, wie Luftstromverteiler, Mundstück, Ventilen und Klappen, die durch ihre komplexen Geometrien für die Tonerzeugung im Instrument verantwortlich sind. Die Qualität des Klangs eines Instruments hängt wesentlich von der Qualität der einzelnen Teile ab [2, 3].
Im traditionellen Musikinstrumentenbau sind die Fertigung und die Montage der Teile stark von manueller, handwerklicher Arbeit geprägt, wie in Bild gezeigt. Der Automatisierungsgrad ist somit sehr niedrig. Maschinelle Fertigung kommt überwiegend bei den Mundstücken und Ventilelementen zum Einsatz. Die z.B. von der Stange abgeschnittenen Rohteile erhalten durch Bearbeitung auf Dreh-, Fräs- und Bohrmaschinen oder durch Umformen ihre endgültige Gestalt und werden oft mittels Fügetechniken (z.B. Hartlöten) aus verschiedenen einfacheren Einzelbauteilen zu einem komplexen Bauteil zusammengesetzt. Die anschließende Nachbearbeitung gibt den Oberflächen den erforderlichen Glanz. Dieser mehrschrittige Fertigungsprozess führt nicht nur bei der Fertigung selbst, sondern auch bei der Planung und Organisation des gesamten Herstellungsprozesses zu einem hohen Aufwand.
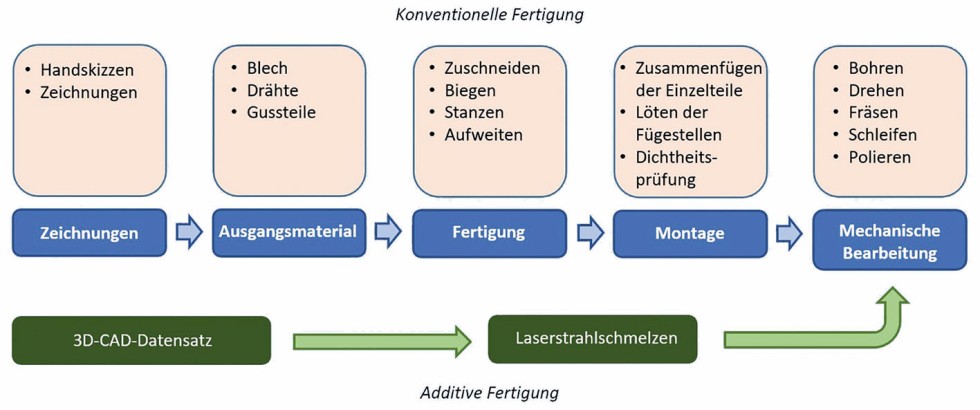
Gegenüberstellung der konventionellen und der Additive-Manufacturing-Prozesskette im Musikinstrumentenbau. Grafik: IMKF
Welche Verbesserungen sind zu erwarten?
Die Einführung der Additiven Fertigung als Prozessinnovation soll die Musikinstrumentenbauer dabei unterstützen,
- sich unabhängig von Zulieferern zu machen,
- die eigene Fertigungstiefe zu erhöhen,
- Bauteile zu individualisieren (z.B. Kinnhalter an Kinnform des Kunden anpassen, Mundstücke individuell gestalten),
- die eigene Innovationsfähigkeit zu stärken, da neue Produktideen schnell und kostengünstig als Prototypen selbst angefertigt und erprobt werden können,
- grundsätzlich die hauseigene Produktion effizienter und schneller zu gestalten.
Hinzu kommt noch die Möglichkeit, dem zunehmenden Fachkraftmangel in der Region Vogtland durch die Verkürzung der Prozesskette und der Steigerung der Automatisierung des Prozesses besser entgegenzusteuern. Durch die Anwendung der Additiven Fertigung können viele konventionelle Fertigungsschritte entfallen. Damit können die Arbeitsabläufe im Unternehmen effizienter und flexibler gestaltet werden.
Geeignetes Additives Fertigungsverfahren identifizieren
Die Auswahl eines geeigneten Fertigungsverfahrens resultiert vor allem aus den Anforderungen an die mechanischen Eigenschaften des Bauteils und Werkstoffs, wie Härte und Steifigkeit, die auf die Klangeigenschaften einen wichtigen Einfluss haben. Dazu sollen die Teile der Blasinstrumente formstabil sein und möglichen äußeren Belastungen standhalten (z.B. Stoßbelastungen während des Transports). Weitere Kriterien zur Verfahrensauswahl bilden die Anforderungen an die Oberflächenqualität einzelner Bauteile. Die additiv gefertigten Teile sollen zu bisherigen Bauteilen vergleichbare Rauheitswerte besitzen, um die Kundenanforderungen zu erfüllen. Diese Teile verfügen bereits ohne Nachbearbeitung über eine Rauheit Ra von nur 0,5 Mikrometern.
Die konventionellen Teile werden in der Regel aus dem etablierten Werkstoff Messing gefertigt. Da dieser Werkstoff für die additiven Verfahren im Pulverbett noch nicht ausreichend untersucht ist, wurden die ersten Prototypen aus reinem Kupfer gefertigt.
Basierend auf den Kenntnissen der technologischen Potentiale einzelner AM-Verfahren, wird für die Umsetzung die LBM (Laser Beam Melting)-Methode ausgewählt, da mit diesem Verfahren eine effiziente Fertigung von komplexen Teilen mit filigranen inneren und äußeren Geometrien möglich ist. Außerdem ist LBM in der Lage, luftdichte Komponenten für die Blasinstrumente zu liefern. Das Bild zeigt die Vorgehensweise.
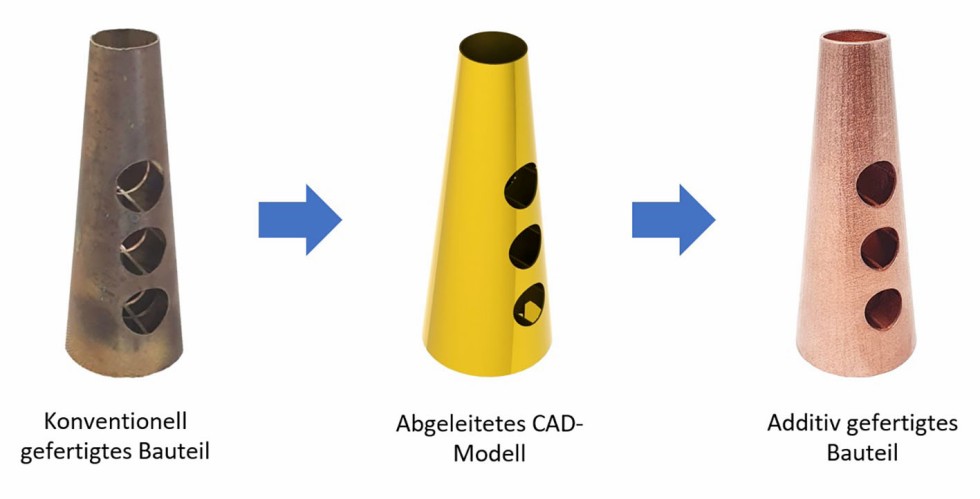
Vorgehensweise zur Additiven Fertigung eines Musikinstrumententeiles aus einer Vorlage. Grafik: IMKF
Wie die Studie der Situation in diesem Bereich zeigt, erfolgt die klassische Fertigung von Musikinstrumenten immer noch auf der Grundlage von 2D-Zeichnungen. Um eine erfolgreiche Einführung der AM-Technologie in das Fertigungsumfeld des Musikinstrumentenbaus zu realisieren, soll diese Hürde in der Datengenerierung und -aufbereitung für AM überwunden werden. Diese ist mit zusätzlichen Investitionen verbunden, die nicht nur die Beschaffung der CAx- und AM-Anlagentechnik, sondern auch die Digitalisierung der etablierten und immer noch aktuellen Bauteilgeometrien umfassen.
Nachbearbeitung von Musikinstrumenten: Nutzen und mögliche Verfahren
Musikinstrumententeile besitzen aus optischen und haptischen Gründen eine glatte Oberfläche, deren Umsetzung bei AM-Bauteilen eine gewisse Herausforderung ist. Aufgrund des schichtweisen Aufbauprozesses hat die Oberfläche der gefertigten Bauteile immer eine bestimmte Abweichung von der Idealform. Dazu kommen noch die spannungsbedingten Gestaltabweichungen, Rückstände der Stützstruktur und nicht fertigbare Geometrieelemente, wie präzise Bohrungen oder/und Gewinde. Dies alles erfordert die Nachbearbeitung von Bauteiloberflächen, was zur Erweiterung der AM-Prozesskette führt [4]. Die Nachbearbeitungsverfahren wie Partikelstrahlen oder Plasma-elektrolytisches Polieren (PeP) ergänzen sie.
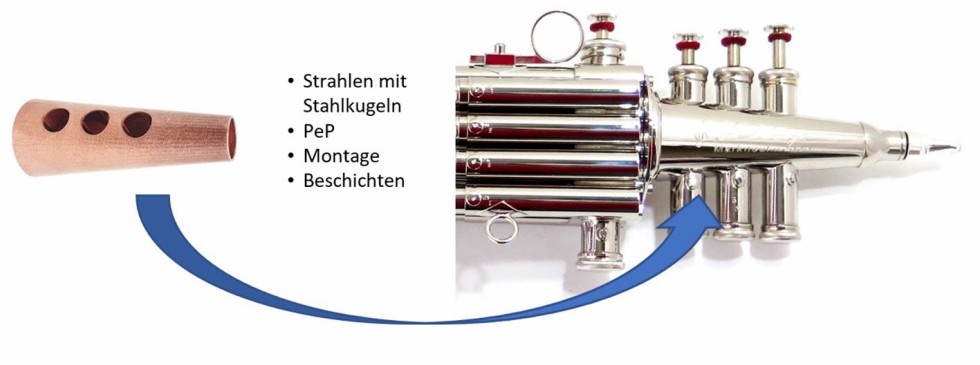
Nachbearbeitung der additiv gefertigten Probenteile, um die Oberflächenrauheit zu verbessern. Grafik: IMKF
Die Ergebnisse der Oberflächencharakterisierung der AM-Probekörper mittels des 3D-Konfokalmikroskops „MarSurf CM“ zeigen, dass diese trotz der gewünschten Funktionserfüllung eine relativ grobe Oberfläche besitzen (Rz = 80 µm). Das eingesetzte Partikelstrahlen auf einer automatisierten Strahlanlage der Fa. BMF (Modell Twister) ermöglicht die Verbesserung der Rauheit von 80 auf 20 Mikrometer. Die nachfolgende Bearbeitung mittels PeP-Verfahren sorgt für eine Reduzierung der Rauheit auf 5 Mikrometer. Dieser Aspekt wird weiter untersucht, da die Oberflächen traditionell gefertigter Blasinstrumententeile Rauheitswerte von nur 0,1 Mikrometern aufweisen.
Der Einsatz mehrerer Zwischenschritte zur Nachbearbeitung von additiv gefertigten Oberflächen soll das Potential der Verbesserung der Oberflächenrauheit zeigen. Dieser Aspekt ist Gegenstand aktueller und zukünftiger Forschungsarbeiten der im Rahmen der genannten Kooperation agierenden Partner. Nur mit geeigneten Oberflächen kann das Erreichen der Klangqualität von traditionellen Bauteilen an Musikinstrumenten gewährleistet werden.
Fazit und Ausblick
Im Beitrag wurden erste Ergebnisse zur industriellen Anwendung der Additiven Fertigung im Musikinstrumentenbau vorgestellt. In den Untersuchungen hat sich ergeben, dass für die Fertigung der Blasinstrumentenkomponente das LBM-Verfahren gut geeignet ist. Die Oberflächen der gefertigten Probekörper weisen eine für das Verfahren typische hohe Rauheit auf, welche mittels der konventionellen Fertigungsverfahren reduziert werden sollte. Um die optimale Qualität der Musikinstrumente zu erreichen, muss die Nachbearbeitungskette noch weiter optimiert werden.
Literatur
- Damodaran, A., Sugavaneswaran, M. & Lessard, L.: An overview of additive manufacturing technologies for musical wind instruments. SN Appl. Sci. (2021), Nr. 3 (162).
- Bucur, B.: Handbook of Materials for Wind Musical Instruments. Springer-Verlag Cham, 2019, 840 S.
- Fletcher N. H., Rossing T. D.: The physics of musical instruments. 2nd edn. Berlin: Springer-Verlag, 1998, p. 756.
- Zeidler, H.; Aliyev, R.; Gindorf, F.: Efficient Finishing of Laser Beam Melting Additive Manufactured Parts. J. Manuf. Mater. Process. (2021), Nr. 5 (106).
Das könnte Sie auch interessieren:
Ultraschall für langlebige Bauteile aus dem 3D-Drucker
Durchbruch: Roboter druckt funktionale Strukturen auf Bauteile
Wie die EMS-Branche von der additiven Fertigung profitiert
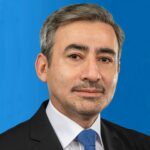
Rezo Aliyev, Dr.-Ing., ist wissenschaftlicher Mitarbeiter am Institut für Maschinenelemente, Konstruktion und Fertigung (IMKF) der TU Bergakademie Freiberg. Foto: Autor
Henning Zeidler, Prof. Dr.-Ing., leitet seit 2017 die Professur „Additive Fertigung“ am IMKF der TU Bergakademie Freiberg.
Stefan Krinke, M.Sc., ist wissenschaftlicher Mitarbeiter am IMKF der TU Bergakademie Freiberg.
Kerstin Voigt ist Inhaberin und Geschäftsleiterin der Firma JÜRGEN VOIGT Meisterwerkstatt für Metallblasinstrumente in Markneukirchen.