Wenn jedes Gramm zählt: Werkzeuge für schnelle Elektromobile
E-Rennwagen der Formula Student erzielen beeindruckende Leistungswerte. Für die erfolgreiche Entwicklung ist das Zusammenspiel ganz unterschiedlicher Disziplinen entscheidend. Das „Zünglein an der Waage“ sind die zur Bearbeitung der Komponenten eingesetzten Werkzeuge.
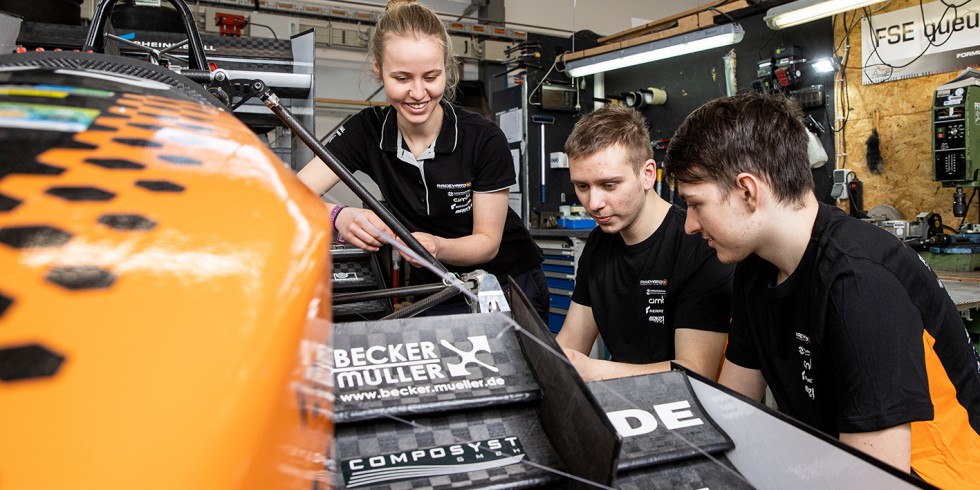
Die Entwicklung des Rennwagens ist Teamwork und erfordert Kenntnisse in zahlreichen Disziplinen: Julia Zindel mit Jonas Chlechowitz und Derik Brede (v.l.n.r.).
Foto: Horn/Sauermann
„Beim Beschleunigen drückt es einen ganz schön in den Sitz“, erzählt Julia Zindel. Sie ist Mitglied des Formula Student Teams Raceyard der Fachhochschule (FH) Kiel. Vergleichbar mit dem Drehmoment eines Bugatti Chirons, katapultieren die vier Elektromotoren des „T-Kiel A 22 E“-Rennwagens den Fahrer in unter drei Sekunden von Null auf Hundert. Mit ihrem eigenentwickelten und selbst gefertigten Elektrorennwagen treten sie in Kategorie „E“ der Rennserie „Formula Student“ an. Für die Fertigung von Bauteilen des Wagens berät die Firma Paul Horn aus Tübingen die Kieler Studenten mit Werkzeugen für Dreh- und Fräsbearbeitungen. „Wir schätzen das Know-how in der Zerspanung sehr. Von unserem Ansprechpartner bekommen wir immer einen guten Rat und schnelle Unterstützung“, erzählt Zindel. Für die zerspanende Bearbeitung der Motorwellen aus Titan setzt das Raceyard-Team auf einen Vollhartmetall-Schaftfräser und ein Stechsystem, jeweils mit spezieller Titangeometrie.
Jedes Jahr alles auf Anfang setzen
Für jede Saison der Formula Student kommt ein neuer Rennwagen zum Einsatz. So wie der Rennwagen stellt sich auch nahezu jedes Jahr das Team neu zusammen. Das bedeutet, dass jedes neue Team die Entwicklung, Fertigung, Montage sowie die Tests des Rennwagens in eigener Regie durchführt und an den Rennen teilnimmt. Dabei fließen die Erfahrungen der vergangenen Saisons in die Neuentwicklung mit ein. Das Team Raceyard 2021/2022 besteht aus 35 Mitgliedern, welche sich auf vier Hauptbereiche aufteilen: Sponsoring und Finanzen, Mechanik, Elektro und Marketing. Julia Zindel ist schon das dritte Mal dabei: „Ich freue mich darüber, wenn ich meine gesammelten Erfahrungen an unsere neuen Teammitglieder weitergeben kann.“
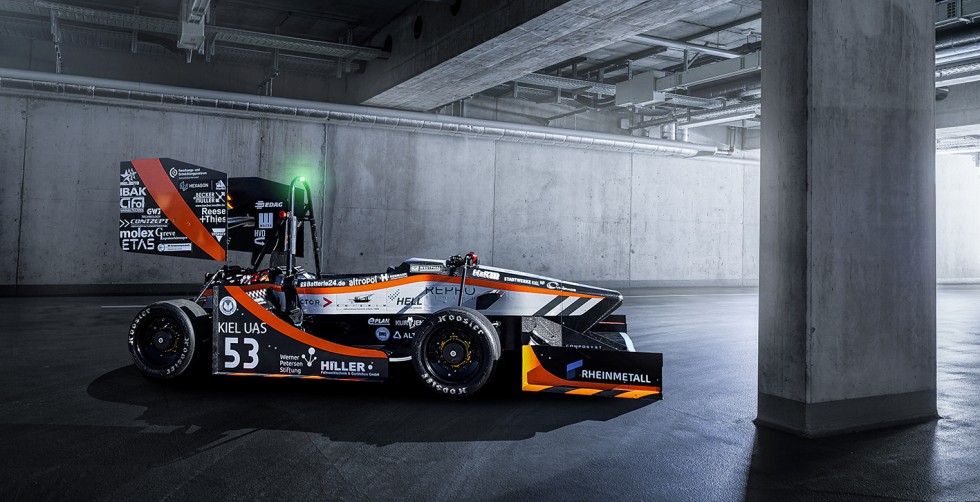
Den Rennwagen „T-Kiel A 22 E“ mit dem Spitznamen „Bendix“ präsentierte das Team im Mai 2022.
Foto: Raceyard/Horn/Sauermann
Den aktuellen Rennwagen T-Kiel A 22 E mit dem Spitznamen „Bendix“ präsentierte das Team im Mai 2022. Die Leistungsdaten lassen die Herzen der Sportwagenfans höherschlagen. Alle vier Räder sind mit je 30 Kilowatt direkt angetrieben. Im Verbund liefern die vier Elektromotoren eine Leistung von 120 Kilowatt (rund 163 PS). Bei einer Fahrzeugmasse von nur 164,5 Kilogramm sind dies rund ein Kilogramm pro PS Leistung. In Summe liefern die Nabenmotoren ein beeindruckendes Drehmoment von 1.480 Newtonmetern. Der Top-Speed liegt bei maximal 120 Kilometern in der Stunde.
Die Komponenten für den elektrischen Antrieb sind eigene Entwicklungen des Teams. Beim Akku sind nur die Einzelzellen Kaufteile. Das Zusammenschließen der 288 Lithium-Polymerzellen sowie die elektronische Auslegung und Fertigung der Sicherheits- und Ladeelektronik übernahmen die Studenten selbst. Der Akku hat eine Kapazität von 7,3 Kilowattstunden bei einer Bordspannung von 600 Volt.
Jedes Gramm zählt – Leichtbaukomponenten und -werkstoffe sind gefragt
„Das Team hat bei der Entwicklung und Konstruktion der einzelnen Komponenten immer den Fokus auf die Einsparung des Gewichts“, sagt Zindel. So kommen bei den vier Elektromotoren unterschiedliche Werkstoffe zum Einsatz. Alle Komponenten fertigen die Studenten in den mechanischen Werkstätten der FH Kiel selbst. So besteht das Motorgehäuse aus einer Aluminiumlegierung. Die Baugruppen des Planetengetriebes, welche zur Übertragung des Drehmoments dienen, sind hingegen auch aus Stahl gefertigt. Neben Dreh- und Fräsbearbeitungen setzt das Team auch auf die additive Fertigung. „Bei Komponenten wie beispielsweise den Bremssätteln setzten wir auf den 3D-Metalldruck. Dieses Verfahren gibt den Konstrukteuren die Möglichkeit, komplexe Bauteilgeometrien schnell und einfach in ein fertiges Teil in Einzelfertigung umzusetzen“, erzählt Zindel.

Die meisten Komponenten ihres E-Rennwagens fertigen die Studenten selber. Bei der Eigenentwicklung kommt es für eine bestmögliche Leistungsentfaltung auf jedes Gramm an.
Foto: Horn/Sauermann
Als es um die Fertigung der Motorwelle des Elektromotors ging, suchten die Studenten Unterstützung bei der Auswahl der Werkzeuge. Für die Bearbeitung der Titan-Welle empfahl der Horn-Techniker Thomas Wassersleben zum einen den Vollhartmetall-Schaftfräser des Werkzeugsystems „DS“ mit spezieller Titangeometrie, und zum anderen das Stechsystem „S224“. Dieses besitzt ebenfalls eine spezielle Geometrie und eine Werkzeugbeschichtung, welche für die produktive Zerspanung von Titanlegierungen ausgelegt ist.
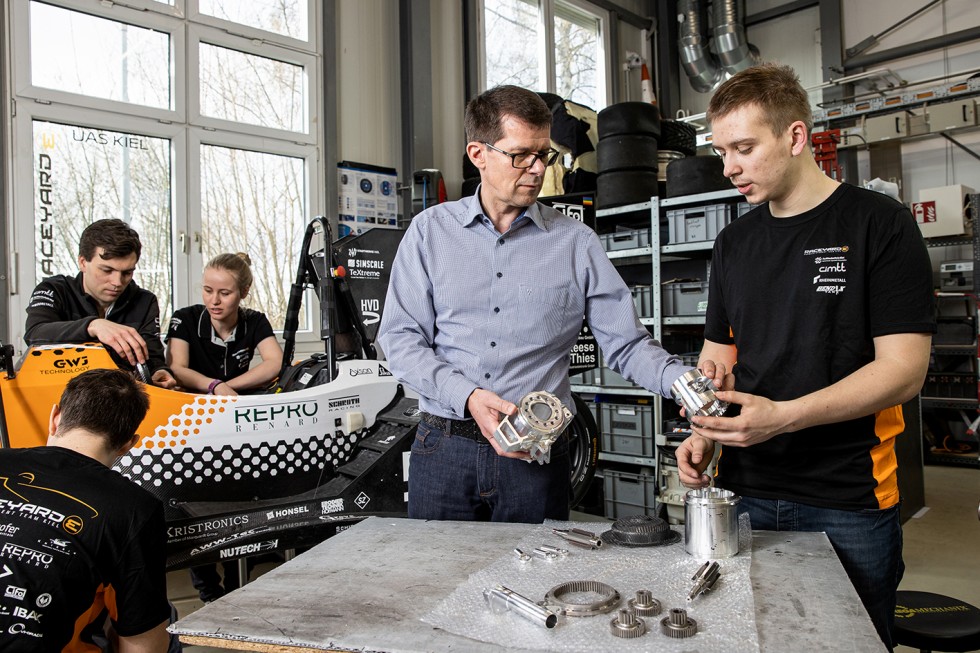
Immer eine passende Werkzeuglösung für jeden Bearbeitungsfall parat: Thomas Wassersleben (links) im Gespräch mit Jonas Chlechowitz.
Foto: Horn/Sauermann
Die Werkzeuge bewähren sich im Einsatz
Der erste Bearbeitungsschritt ist das Stechdrehen der Außenkontur. Die Schneidplatte des Typs S224 fertigt die einzelnen Durchmesser der Welle. Auch das Schlichten der eng tolerierten Lagersitze übernimmt das Stechsystem mit spezieller Titangeometrie. Die Entwicklung dieser „WT“ genannten Geometrie – eigens für Titan – erfolgte mittels umfangreicher Simulationen. Sie hat sich auf Anhieb in der Praxis bei der Bearbeitung von anspruchsvollen Werkstoffen bewährt. Neben einem sicheren Spanbruch sorgt die angepasste Geometrie für einen weichen Schnitt. So sind höhere Vorschübe möglich, was einer schnelleren Bearbeitungszeit entspricht.
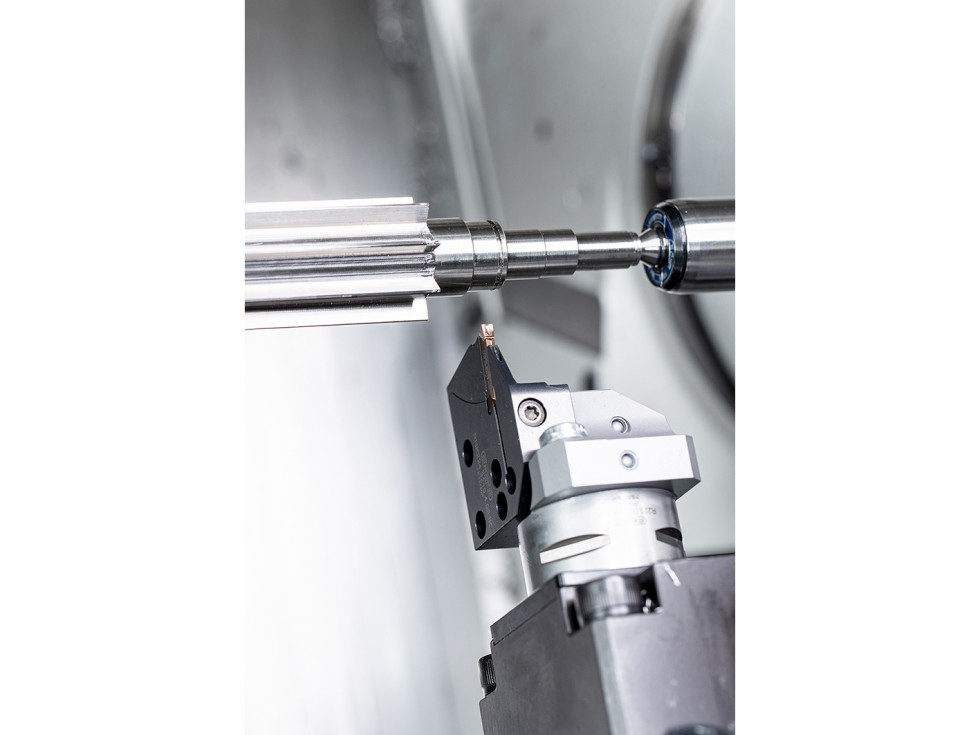
Für die Stechdrehoperation setzte der Techniker des Werkzeugspezialisten auf das System S224 mit der Titangeometrie WT.
Foto: Horn/Sauermann
Zum Fräsen der Nuten setzt Wassersleben auf die VHM-Schaftfräser des Typs DS. Die Werkzeuge sind speziell auf das Fräsen von Titanlegierungen abgestimmt. Horn setzt dabei auf das neu entwickelte Substrat IG3I. Durch die Kombination der Hartmetallsorte und der Werkzeugbeschichtung lassen sich bedeutende Standzeiterhöhungen erreichen. Darüber hinaus weist das Substrat ein homogenes Verschleißverhalten auf. Eine scharfe Mikrogeometrie an den Schneidkanten, positive Spanwinkel, große Freiwinkel und polierte Spanräume beugen beim Zerspanen von Titan einer Kaltverfestigung der Werkstückrandzone sowie Aufbauschneidenbildung auf den Spanflächen vor.
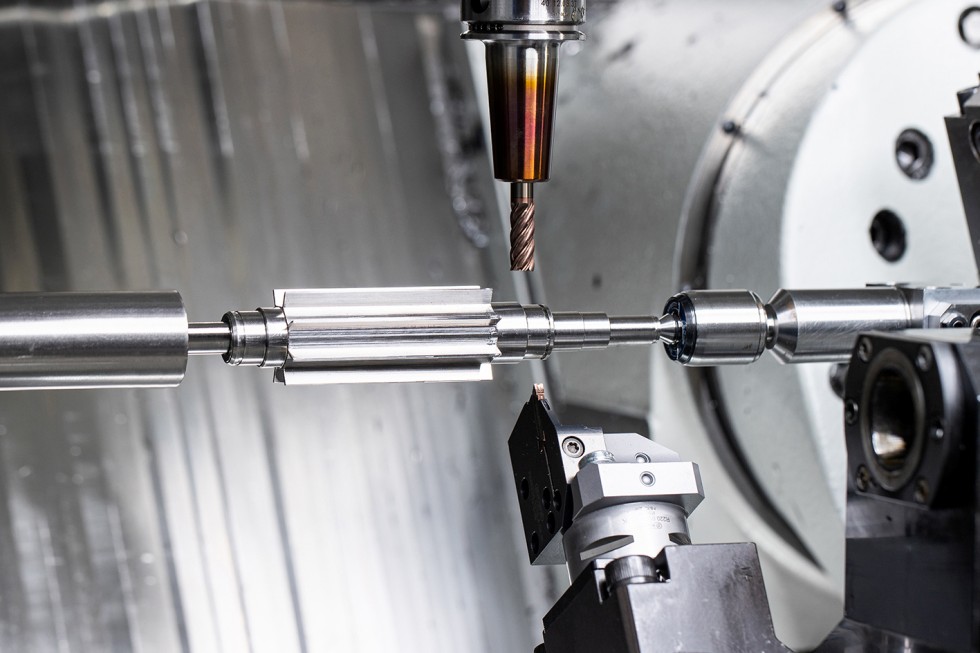
Für die Bearbeitung der Titan-Legierung kamen Werkzeuge zum Einsatz, die speziell auf die hochfesten Legierungen ausgelegt sind.
Foto: Horn/Sauermann
Für einen ruhigen und vibrationsarmen Fräsprozess sorgen variable Drallwinkel und unterschiedliche Zahnteilungen. Die Beschichtung bietet trotz scharfer Schneidkanten eine sehr hohe Schichthaftung und sorgt daher für eine hohe Schneidkantenstabilität. Aufgrund der hohen Temperaturbeständigkeit dient die Schicht als Hitzeschild, um die Wärmeeinleitung in das Hartmetall zu verringern.
Carbon-Monocoque: Leichtbau par excellence
Das Chassis des Rennwagens besteht aus einem Monocoque aus CFK (kohlenstofffaserverstärkter Kunststoff). Für die aerodynamischen Komponenten und die anderen Bauteile wie das Lenkgestänge wählten die Studenten ebenfalls den Werkstoff aus Kohlefasern. „Das Laminieren der einzelnen Kohlefaserschichten ist immer eine Herausforderung, da die Faserrichtungen der einzelnen CFK-Lagen für die spätere Steifigkeit des Chassis und der anderen Baugruppen Sorge tragen“, so Zindel. Für die Berechnungen der Aerodynamik sowie der Steifigkeit des Chassis und den weiteren Komponenten setzten die Studenten leistungsstarke Computer und fortschrittliche Simulationsprogramme ein, welche im Kieler CIMTT zur Verfügung stehen.
Nicht nur Vollgas: Auf viele Disziplinen kommt es an
Bei den einzelnen Disziplinen der Formula Student kommt es nicht nur auf die Performance des Autos an. Sie gliedern sich in statische und dynamische Disziplinen. Bei den statischen Disziplinen spielt die betriebswirtschaftliche Seite und die konstruktiven Ansätze des Teams eine große Rolle. So müssen die Studenten in zwei Präsentationen den Business Plan und den Kostenreport darstellen und begründen. Eine weitere statische Disziplin ist das Engineering und Design Event. Dort muss das Team die Jury von ihrem Design und Konstruktion überzeugen. Hierbei geht es vor allem um die Diskussion, bei der mit guten Argumenten und Rechtfertigungen auf die Anmerkungen der Jury eingegangen werden muss.
Zu den dynamischen Events gehören Acceleration, Skid Pad, Autocross und Endurance. Die Disziplin Acceleration ist ein Beschleunigungstest auf einer geraden Strecke von 75 Metern. Die Rennwagen beschleunigen hierbei in unter drei Sekunden von 0 auf 100 Kilometern in der Stunde. Beim Skid Pad fahren die Autos eine Strecke in Form einer liegenden Acht. Hohe Fliehkräfte beziehungsweise Querbeschleunigungen können bei dieser Disziplin zum Ausbrechen des Fahrzeugs führen.
Beim Autocross steuern die Fahrer ihre Rennwagen einzeln in einem eng abgesteckten Kurs auf Zeit. Dabei sind der Rennfahrer und die Fahrdynamik des Fahrzeugs auf einer Strecke von einem Kilometer Länge sehr gefordert. Die Endurance ist die größte und letzte Disziplin bei jedem Formula Student Event. Hier muss der Rennwagen seine Zuverlässigkeit auf einem Rundkurs von 22 Kilometern Länge beweisen. Diese Disziplin zählt zu einem Drittel der erreichbaren Gesamtpunktzahl.

Studieren, wo andere Urlaub machen: Das CIMTT der Fachhochschule Kiel liegt direkt an der Kieler Förde.
Foto: Horn/Sauermann
Die Zusammenarbeit mit dem Institut für CIM-Technologietransfer (Computer integrated manufacturing – CIMTT) besteht schon mehrere Jahre. Thomas Wassersleben berät die mechanischen Werkstätten des Instituts mit Zerspanungslösungen und Werkzeugen. Zahlreiche Aufgaben konnte der Horn-Außendienstmitarbeiter in dieser Zeit schon lösen. Auch Julia Zindel bewertet die Zusammenarbeit äußerst positiv: „Wir sind froh, dass wir für unsere Zerspanaufgaben einen Werkzeugpartner an unserer Seite zu haben, mit dem wir gemeinsam an den Bearbeitungslösungen unserer Bauteile arbeiten können.“
Wissenswertes über die Formula Student
Die Formula SAE wurde 1981 in den USA gegründet und später als Formula Student nach Europa ausgeweitet. Seit 1999 gibt es jährliche Events im englischen Silverstone und seit 2006 auch in Deutschland, und zwar auf dem Hockenheimring. Mittlerweile macht die Formula Student auch in Italien, Spanien, Brasilien oder in Japan halt und trägt dort Wettbewerbe aus. Die Rennserie ermöglicht es ambitionierten Studierenden, sich intensive praktische Erfahrungen in Konstruktion, Fertigung und wirtschaftlichen Aspekten rund um den Automobilbau anzueignen – und das Ganze außerhalb eines Hörsaals. Jedes Team entwickelt dazu einen einsitzigen Rennwagen auf Grundlage eines umfangreichen Regelwerks.
Das könnte Sie auch interessieren:
Eignung von Verfahren zur Ermittlung der Zerspankraft
Planfräser erzielen Leistungssprung für die Drucklufterzeugung
Kantenverrundung optimiert Leistung von Präzisionswerkzeugen
Nico Sauermann ist in der Pressearbeit bei der Paul Horn GmbH in Tübingen tätig.