Werkzeugmaschinen – unerlässliche Helfer beim Upgrade von Formel-1-Autos
Technik, Geschick und Geschwindigkeit – darauf basiert der Erfolg in der Welt der Formel 1. Doch nur wenige Fans dieser Rennserie wissen, welche Ingenieurleistungen und welche Maschinentechnik die F1-Boliden zu ihren Leistungen befähigen.
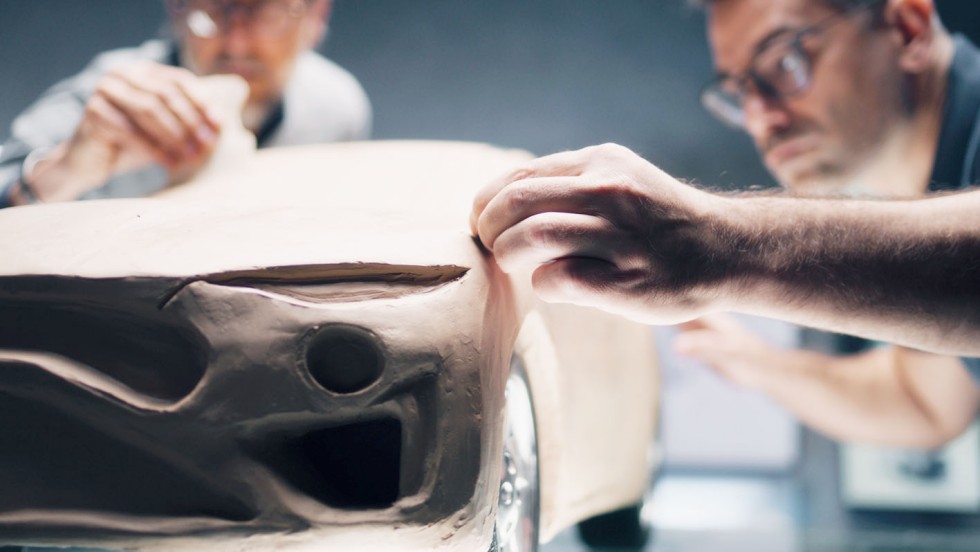
Ein handgefertigtes Tonmodell, das detailreich ausgearbeitet wurde, dient auch den Entwicklungsingenieuren in der Formel 1 in der Regel als erstes Anschauungsobjekt. Für größere Bauteile und Tests empfiehlt sich jedoch die effizientere, schnellere Erstellung von Prototypen auf hochgenauen Fräsmachinen.
Foto: Frame Stock Footage / Shutterstock.com
Wie wird ein Formel-1-Auto von der ersten Idee bis zur Rennstrecke entwickelt? Und welche Hightech-Maschinen machen diesen Prozess überhaupt erst möglich? Darauf gibt dieser Artikel einige spannende Antworten. Hintergrund: Vier dieser High-End-Bearbeitungszentren stehen zurzeit auf der Plattform Surplex.com zum Verkauf.
Die Maschinerie hinter dem Spektakel
Die Formel 1 zieht Millionen von Zuschauern weltweit in ihren Bann. Doch hinter diesem Spektakel aus Geschwindigkeit und Präzision verbirgt sich eine tiefgreifende Welt der Technik und der Strategie. Wussten Sie zum Beispiel, dass allein bei Red Bull Racing – dem amtierenden Weltmeister und aktuellen Führenden in der Konstrukteurs- und Fahrerwertung – fast 1.100 Mitarbeiter arbeiten, davon 350 in der Motorenabteilung? Jeder Millimeter, jede Schraube und jedes Bauteil sind das Ergebnis endloser Stunden von Planung, Tests und Weiterentwicklung.
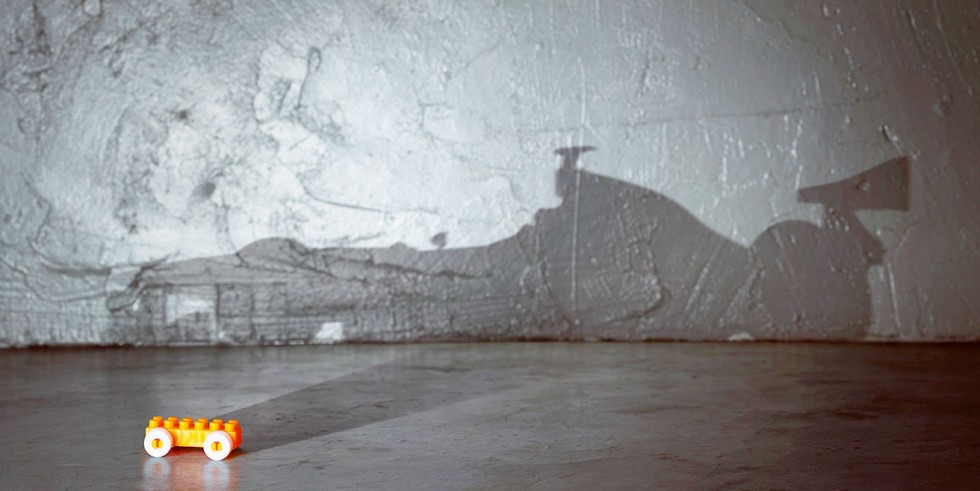
Von der ersten Idee bis zum fertigen Rennauto: In der Formel 1 werden Fahrzeuge immer wieder weiterentwickelt und optimiert. Grafik: jamesteohart / Shutterstock.com
So ist das Fahrzeug, das im letzten Rennen einer Saison an den Start geht, die x-te Version des Autos des ersten Rennens. Dank ständiger Innovationen und Upgrades wird es über die Saison hinweg permanent angepasst und optimiert.
Strategische Planung muss auf den Punkt genau passen
In der rasanten Welt der Formel 1 ist die Planung entscheidend. Auch bei umfangreichen Überarbeitungsprojekten ist die Zeit von der ersten Idee bis zur Implementierung bemerkenswert kurz – oft nur wenige Wochen oder Monate. Die Komplexität des Upgrades beeinflusst den Zeitplan. Schlüsselkomponenten wie der Frontflügel benötigen viel Entwicklungszeit und werden früh angegangen. Im Laufe der Saison fokussieren sich Teams auf Bauteile mit mittlerer Entwicklungsdauer – wie den Unterboden und den Diffusor. Bauteile wie Bremsschächte, die schnell Vorteile bringen, werden später hinzugefügt, um kurzfristige Optimierungen zu erzielen.
Auf der Rennstrecke sichtbare Bauteile sind nur die „Spitze des Eisbergs“. Von unzähligen Entwürfen schafft es nur ein Bruchteil aufs Auto, und nicht jedes Upgrade bringt den erhofften Erfolg. Dieser intensive Entwicklungsprozess bindet Hunderte von Experten und unzählige Arbeitsstunden in die Perfektionierung jedes Details.
Digitales Design und Simulationstest
Welche computer-unterstützten Methoden werden für die Optimierungen von Bauteilen genutzt? Die „Geburt“ eines F1-Updates beginnt immer mit einer innovativen und kreativen Idee und Skizze. Eine CAD (Computer Aided Design)-Software ist das erste Tool, mit dem Ingenieure arbeiten, um diese zu digitalisieren.
Fortgeschrittene Tools wie CFD (Computational Fluid Dynamics)-Software kommen zum Einsatz, um die Aerodynamik des Fahrzeugs zu simulieren. FEM (Finite Elemente Methode)-Software dient dazu, die mechanischen Eigenschaften und das Verhalten von Materialien unter verschiedenen Belastungen zu simulieren, um die Leistung und Sicherheit der daraus gefertigten Komponenten zu gewährleisten. Doch die Formel 1 ist nicht nur eine Welt der „digitalen Designkunst“, sondern auch der handwerklichen Präzision – wie bei der Herstellung von Modellen für den Windkanal und den tatsächlichen Prototypen bzw. dem endgültigen Bauteil.
Fahrzeugmodelle: Vom Computer in den Windkanal
In der Formel 1 regulieren die „Aerodynamic Testing Restrictions“ (ATR) die Ressourcen, die jedes Team für aerodynamische Tests verwenden darf. Das Ziel ist Chancengleichheit: Je besser ein Team in der vorherigen Saison abgeschnitten hat, desto weniger Testzeit steht ihm zu. So darf Red Bull Racing als amtierender Meister nur 1260 CFD-Simulationen und 202 Windkanal-Runs und 50 Stunden Zeit durchführen. Williams hingegen, das Team, dass 2022 auf dem letzten Platz landete, hat Anspruch auf fast doppelt so viele Testmöglichkeiten.
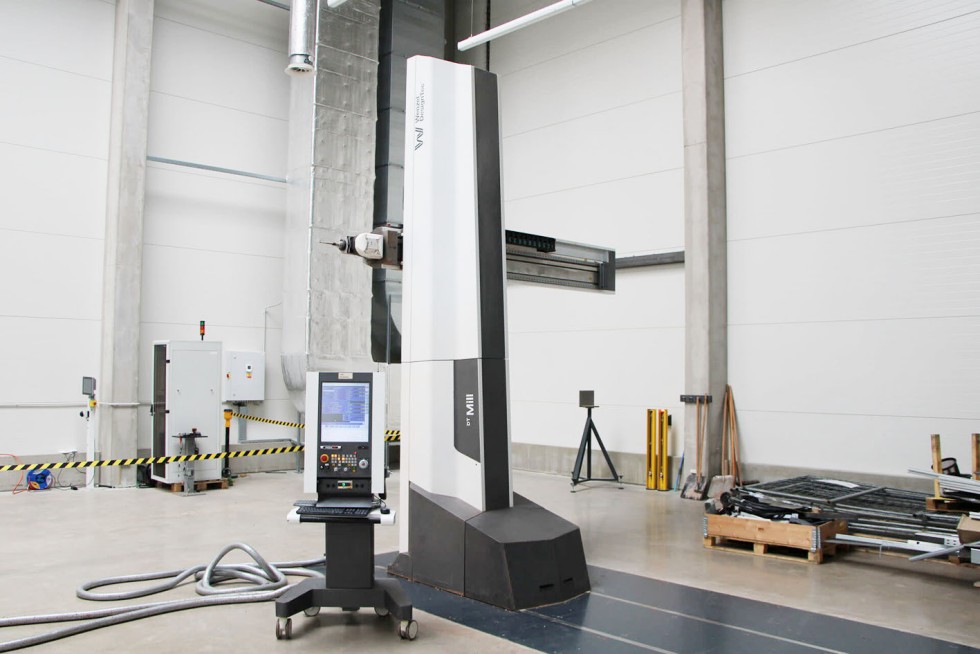
Mit der High-Performance Fräsmaschine „DT-Mill“ von Wenzel DesignTec lassen sich Automodelle im Maßstab 1:1 aus Hartschaum, Ton oder Ureol fertigen.
Foto: Surplex
Für die Windkanaltests werden oft Modelle aus „Ureol“, Hartschaum oder einem Art-Ton hergestellt, weil diese Materialien leicht zu formen und zu bearbeiten sind. Das Erstellen solcher Modelle, ob vom gesamten Auto oder nur von einzelnen Bauteilen, läuft entweder händisch ab, oder es werden spezielle Fräsmaschinen genutzt. Dies sind Portalfräsmaschinen oder es kommt sogar „mobiles Fräsen“ zum Einsatz. Diese Methoden wurden speziell für den Modellbau im Automotive-Bereich entwickelt.
Ein Beispiel aus diesem Segment ist die Fräsmaschine „DT-Mill“ des Anbieters Wenzel DesignTec aus Hengersberg. Damit können Automobil-Modelle im Maßstab 1:1 aus Hartschaum, Ton oder Ureol gefertigt werden. Eine derartige Maschine steht beim Düsseldorfer Gebrauchtmaschinenspezialisten Surplex aktuell zum Direktkauf. Sie stammt aus dem Werk eines tschechischen Automobil-Prototypenbauers.
Vom Mikro-Design bis zur Makro-Fertigung
Aber die Formel 1 ist nicht nur ein Schauplatz für aerodynamische Feinheiten, sondern auch für Präzisionsmechanik auf höchstem Niveau. Jede Komponente eines F1-Wagens, egal wie klein, spielt eine entscheidende Rolle im Gesamtpaket. Um diese Perfektion zu erreichen, wird auf eine Reihe von fortschrittlichen Fertigungstechniken zurückgegriffen. Mithilfe von CNC-Fräsmaschinen und -Drehmaschinen können komplexe und hochpräzise Teile aus Metallblöcken gefertigt werden. Diese Maschinen ermöglichen es den Ingenieuren, mit großer Genauigkeit und Wiederholbarkeit zu arbeiten. Dadurch sind sie ideale Werkzeuge für die Produktion von kritischen Komponenten eines F1-Autos. Auch 3D-Drucker werden genutzt. Der additive Fertigungsprozess ermöglicht die schnelle Prototypenherstellung und die Fertigung von komplexen Teilen, die mit herkömmlichen Methoden schwer herzustellen wären.
Vom Formel-1-Rennstall in die Auktion
Die stetige Evolution und Entwicklung in der Formel 1 bedingt, dass Rennställe kontinuierlich ihre Ausstattung erneuern und modernisieren. Diese hochwertigen, teils nur wenig gebrauchten Maschinen finden dann ihren Weg auf den Markt für Gebrauchtmaschinen – ein Glücksfall für Fachbetriebe, die nach Premium-Anlagen suchen.
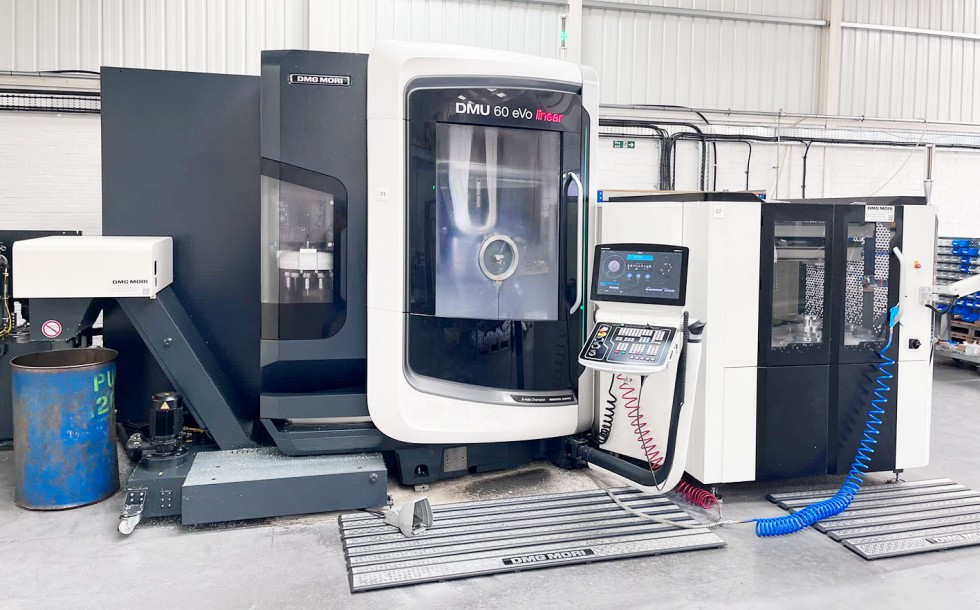
Das 5-Achs-Bearbeitungszentrum DMU 60 eVo Linear lässt sich, wie im Bild gezeigt, mit einem Palettenladesystem für maximale Effizienz bei der Bauteilfertigung optimieren.
Foto: Surplex
Während einige Teams ihre Ausrüstung intern weiterverwenden oder sie an Partner weitergeben, gibt es immer wieder die Möglichkeit, solche außergewöhnlichen Maschinen auch gebraucht zu erwerben. Ein aktuelles Beispiel: Ein britischer Formel-1-Rennstall bietet nun vier seiner High-End-5-Achs-Bearbeitungszentren (BAZ) vom renommierten Hersteller DMG Mori über das Industrieauktionshaus Surplex.com zum Direktkauf an. Dabei handelt es sich um:
- zwei DMU 60 eVo Linear mit Palettenladesystem (Baujahr 2018 und 2017);
- eine DMU 65 monoBlock (Baujahr 2016),
- eine DMU 50 der dritten Generation mit Palettenladesystem (Baujahr 2017).
Die Maschinen im Detail
Das Universal-Bearbeitungszentrum „DMU 60 eVo“ eignet sich für die 5-Achs-Simultanbearbeitung und ist dazu mit dem bewährtem Schwenkrundtisch ausgestattet (Schwenkbereich der B-Achse –5° / +110°). Das BAZ hat maximale Verfahrwege von 600 / 500 / 500 Millimeter (X-/X-/Z-Achse). Das maximale Werkstückgewicht beträgt 400 Kilogramm. Als Steuerungs- & Softwarealternativen stehen bei diesem BAZ herstellerseitig Modelle der Anbieter Siemens oder Heidenhain zur Verfügung.
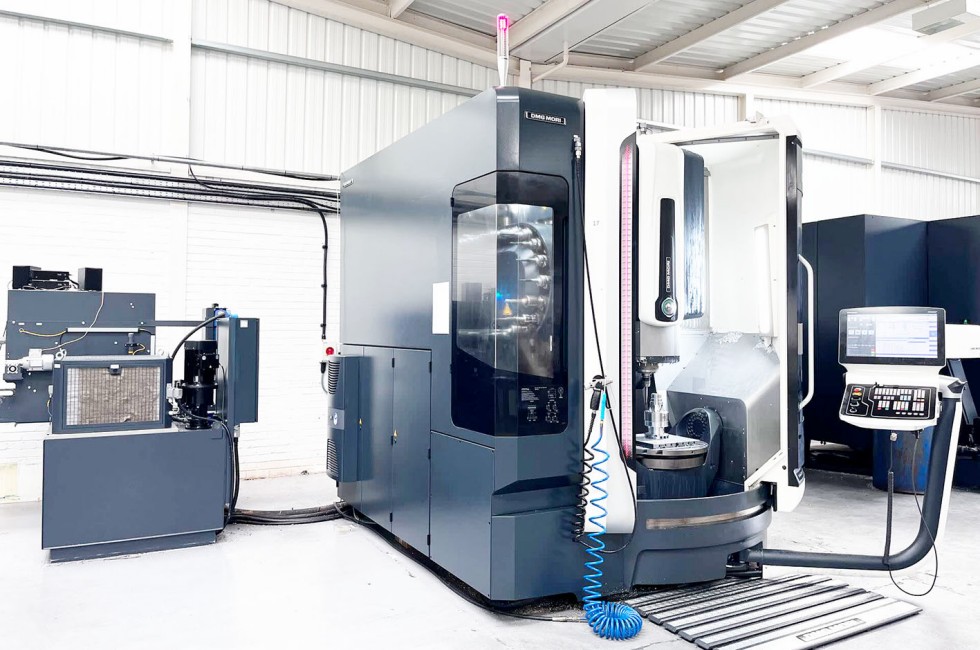
Garant für Präzisionsarbeit: Das steife 5-Achs-Bearbeitungszentrum DMU 65 monoBlock stellt hochkomplexe Bauteile mit überzeugender Genauigkeit her.
Foto: Surplex
Das 5-Achs-Bearbeitungszentrum „DMU 65 monoBlock“ überzeugt mit dem eigensteifen, verrippten und FEM-berechneten Maschinengestell. Weitere Vorteile sind die gute Zugänglichkeit bei Beladung und Bedienung und das bedienungsfreundliche Achskonzept. Außerdem hat die Baureihe Vorzüge, was die Thermostabilität aller genauigkeitskritischen Baugruppen angeht. Der Arbeitsraum beträgt 735 / 650 / 560 Millimeter (X-/Y-/Z-Achse).
Die CNC-Universal-Fräsmaschine „DMU 50“ mit Schwenkrundtisch bietet maximale Verfahrweg von 650 / 520 / 475 Millimetern (X-/Y-/Z-Achse). Der große Schwenkbereich der B-Achse (–35° / +110°) erlaubt hohe Flexibilität. Die größtmögliche Werkstückhöhe ist 600 Millimeter, das maximale Werkstückgewicht beträgt 300 Kilogramm. Die „speedMaster“-Technologie erlaubt die 5-Achs Bearbeitung mit bis zu 20.000 Umdrehungen in der Minute.
Diese verkäuflichen Anlagen befinden sich in Newcastle upon Tyne im Nordosten von England.
Das könnte Sie auch interessieren:
Zerspanungsprozesse beherrschen: Erfolgskonzepte live auf der EMO
Sensorische Schwenkspannelemente: Garant für sicheres Spannen