Wie entstehen hochfeste Schrauben für die Endoprothetik?
Bei der Bearbeitung von Kobalt-Chrom-Legierungen stellt ein Fertigungsbetrieb, der sich auf hochwertige Produkte für die Medizintechnik spezialisiert hat, aufgrund der immensen Werkstoffkosten besonders hohe Ansprüche an die zum Einsatz kommenden Werkzeuge. Der Erfolg gibt ihm recht.
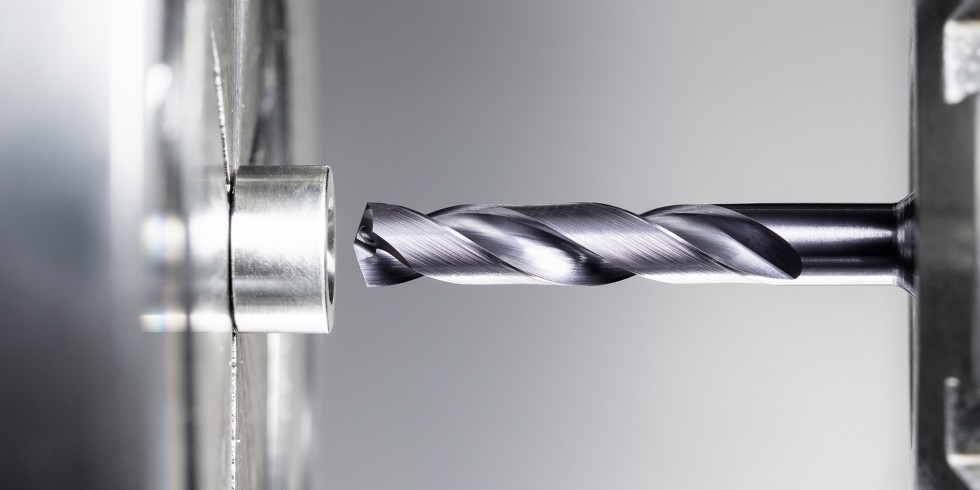
Der erste Schritt: Bohren des Schraubenkopfes mit dem System DD. Der Bohrer mit innerer Kühlmittelzufuhr hat eine Geometrie, die für rostfreie Stähle bestens geeignet ist.
Foto: Horn/Sauermann
Tibor Veres, Geschäftsführer der Hymec Fertigungstechnik aus Norderstedt bei Hamburg, setzt beim Zerspanen von Superlegierungen auf Tools eines Hartmetall-Werkzeugspezialisten aus Tübingen. Die Präzisionswerkzeuge kommen auch beim Stoßen eines Innensechskants einer Implantat-Schraube aus Cobalt-Chrom zum Einsatz. Zusammen mit dem technischen Berater von Horn, Thomas Wassersleben, machten sie die anspruchsvolle Bearbeitung prozesssicher.
Wie lässt sich die geforderte Feinstpräzision erzielen?
„Wir sehen uns als Manufaktur für die Feinstpräzision in höchster Qualität“, sagt Veres. Das Unternehmen hat sich auf medizintechnische Produkte, Einzelanfertigungen und anspruchsvolle Kleinserien spezialisiert. Das Bearbeiten von Hightech-Werkstoffen wie hochfesten Aluminium- und Titanlegierungen, Implantatstählen und Superlegierungen wie Kobalt-Chrom (CoCr) gehören bei Hymec zum Tagesgeschäft. Das Tätigkeitsspektrum umfasst sowohl die Herstellung von feinmechanischen Elementen und kompletten Baugruppen als auch die umfassende Unterstützung bis hin zum Qualitätsaudit.
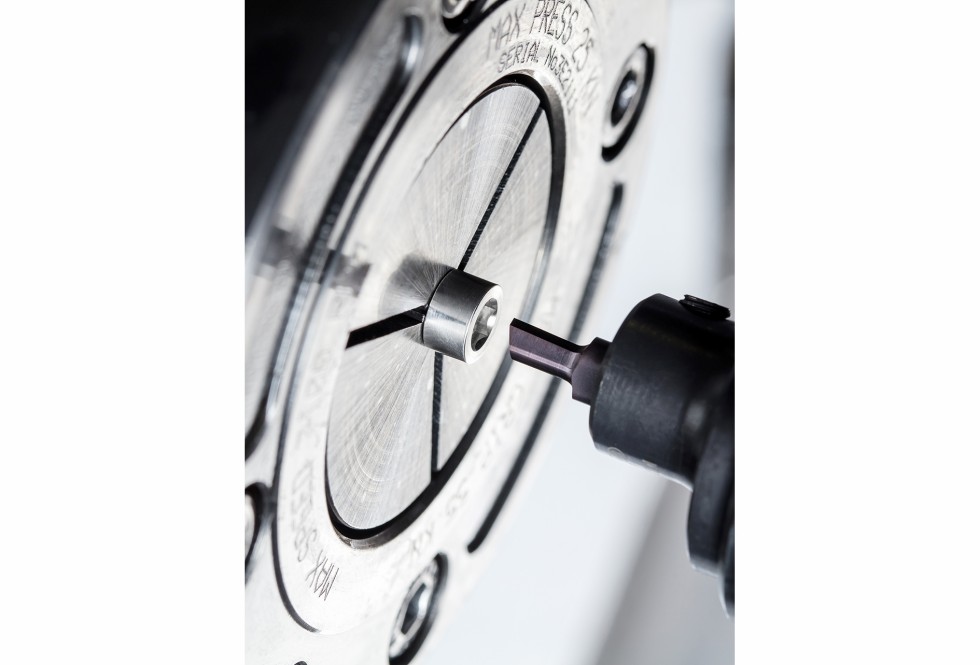
Mit der Umsetzung des Stoßprozesses in Kobalt-Chrom stellt der Werkzeughersteller sein Know-how in der Präzisionsbearbeitung von Superlegierungen unter Beweis. Der harte und zähe Werkstoff erforderte zahlreiche Anpassungen des Schneidstoffs und der Strategie.
Foto: Horn/Sauermann
Veres führt Hymec in der zweiten Generation. Der von seinem Vater im Jahr 1972 gegründete Betrieb erwarb sich recht schnell einen guten Ruf als „Manufaktur für Feinstpräzision“. Heute gilt er als Top-Lieferant für Orthopädie-Implantate mitsamt den dazugehörigen Instrumenten. Der Kundenkreis aus aller Welt profitiert aber nicht nur von den hochwertigen Dreh-, Fräs- und Erodierarbeiten, sondern auch von zahlreichen Dienstleistungen, die den Produktentstehungsprozess von der technischen Beratung über die Konstruktion bis hin zur zertifizierten Qualität begleiten.
Enge Zusammenarbeit ist der Erfolgsgarant
Seit 30 Jahren arbeitet Hymec eng mit Horn zusammen. „Die Zusammenarbeit ist ausgezeichnet, weil wir bis jetzt immer eine wirtschaftliche Lösung für unsere Aufgaben bekommen haben.“ Der Geschäftsführer legt ein hohes Augenmerk auf die Auswahl der Werkzeuge und sucht immer die beste Werkzeuglösung seiner Zerspanaufgaben. Für die Herstellung eines Innensechskants in eine Schraube aus CoCr bat er Wassersleben um die technische Unterstützung.
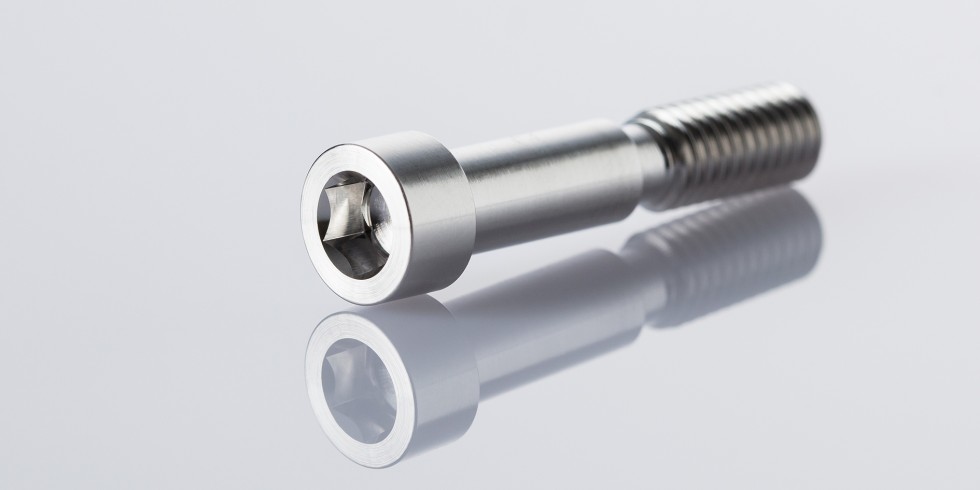
Die Schraube aus Kobalt-Chrom findet den Einsatz in einem künstlichen Kniegelenk.
Foto: Horn/Sauermann
Die Schraube ist ein Implantat und gehört zur Baugruppe eines künstlichen Kniegelenks. Hymec fertigt die Schrauben in verschiedenen Schlüsselweiten von 2,5, 3,5 und 5 Millimetern. Der Innensechskant ist als Passung mit einer geringen Toleranz gefertigt, damit die Schraube beim Einsetzen fest auf dem Sechskantschlüssel sitzt. Des Weiteren muss die Oberflächengüte qualitativ besonders hochwertig sein, da schon geringe Riefen und Grataufwürfe Keimherde darstellen können. Rund 5000 Schrauben dieses Typs fertigt das Unternehmen im Jahr.
Der Fertigungsprozess „Räumen“ ist in Serie kaum möglich
„Die Herstellung von einem Sechskant in Titan ist relativ einfach durch das Profilräumen herstellbar. In Kobalt-Chrom ist das Räumen in Serie wegen der hohen Festigkeit jedoch kaum möglich und der Werkzeugverschleiß ist erheblich“, so Veres. Aufgrund dieser Problematik kam der Vorschlag, den Innensechskant über das Stoßverfahren herzustellen. Das Verfahren bietet hohe Präzision und hohe Prozesssicherheit, da sich die Schneidengeometrie und das Hartmetallsubstrat leicht an den zu bearbeitenden Werkstoff anpassen lässt. Die ersten Versuche brachten schnell die erhoffte Lösung. „Durch das Stoßwerkzeug ist die Herstellung von genauen Passungen möglich und die Oberflächen sind sehr gut“, sagt Veres.
Der Stoßprozess gestaltet sich wie folgt: Ein Vollhartmetallbohrer des Horn-Systems „DD“ bohrt eine Bohrung mit dem Durchmesser 4,9 Millimeter in den Schraubenkopf. Der Bohrer mit innerer Kühlmittelzufuhr stammt aus dem Standard-Sortiment – mit einer Geometrie für rostfreie Stähle. Der Anschnittkegel der Sacklochbohrung dient beim Stoßen als Auslauf- beziehungsweise Freilaufzone des Stoßwerkzeuges.
Aufgrund der geringen Höhe des Schraubenkopfes war ein Freistich als Auslauf nicht möglich. Das Werkzeug fährt zum Brechen der Späne am Ende der Schlüsselfläche auf einer programmierten Bahn in die Freilaufzone. Das Stoßen des Innensechskants mit der Schlüsselweite von 5 Millimetern übernimmt ein Supermini des Typs „N105“. Die Zustellung der Einzelhübe liegt bei 0,02 Millimetern. Nach der Fertigstellung einer Fläche dreht das Futter weiter, um mit der nächsten Fläche fortzufahren.
Die Prozesszeit der Stoßoperation liegt bei rund zwei Minuten. Zum Einsatz kommt eine CNC-Drehmaschine von Mori Seiki. Der Stoßprozess läuft über die Bewegung des Werkzeugrevolvers ab.
Pro Schneide sind 100 Schrauben möglich
Veres ist mit der Leistung sehr zufrieden: „Die Werkzeuge sind sehr präzise, nach einem Wechsel ist eine Korrektur kaum nötig. Des Weiteren stimmt uns die erreichte Standzeit von 100 Schrauben pro Schneide sehr zufrieden.“ Die erreichte Oberflächengüte des Innensechskants ist so hoch, damit keine weitere Nachbehandlung der Oberfläche nötig ist. Der harte und zähe Werkstoff Kobalt-Chrom erforderte eine Anpassung der Schneidengeometrie, des Hartmetallsubstrates, der Beschichtung, den Bearbeitungsbedingungen und der Kühlschmierung. Die Hartpartikel in der Legierung neigen zur Bildung von Abrasiv- und Kolkverschleiß. Darüber hinaus stellt die Kaltferfestigung der Oberfläche ein Problem bei der Zerspanung dar.
Die Werkzeugschneide ist wie bei der Zerspanung von Titan schleifscharf und nicht verrundet, aber im Gegensatz zur Titanbearbeitung ist der Schneidkeil stabiler ausgeführt. Als Hartmetallsubstrat dient eine zähe Feinstkornsorte. Die Beschichtung der Werkzeuge muss hart und hitzebeständig sein. Darüber hinaus ist die effiziente Kühlschmierung der Kontaktzone zwischen Werkzeug und Werkstück eine weitere Voraussetzung für die erfolgreiche Zerspanung der Superlegierung. Zudem stellt der hohe Materialpreis große Ansprüche an die Prozesssicherheit der eingesetzten Werkzeuge.
Bestens geeigneter Werkstoff für die Medizintechnik
Je nach Hersteller besteht Kobalt-Chrom in der Regel aus 50–90 Prozent Kobalt, 10–30 Prozent Chrom und aus den zusätzlichen Legierungsbestandteilen Molybdän, Wolfram, Niob, Mangan oder Silizium. CoCr gehört zu den leistungsfähigsten Werkstoffen für die Endoprothetik. Der Werkstoff eignet sich besonders für künstliche Kniegelenke und Hüftprothesen. Darüber hinaus ist CoCr auch weit der Zahnprothetik verbreitet. Wegen der hohen Biokompatibilität mit dem menschlichen Gewebe und seiner absoluten Korrosionsfreiheit kommen CoCr-Legierungen aufgrund des hohen Werkstoffpreises vorwiegend in der Medizintechnik vor, der Spezialität es Anbieters aus Norderstedt.
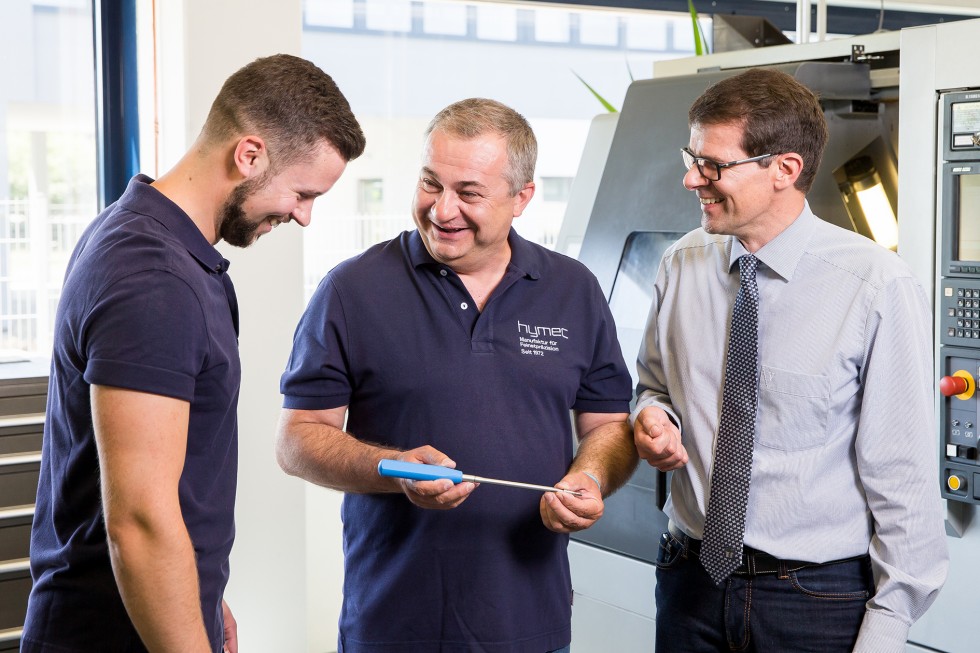
Eine erfolgreiche Partnerschaft, die seit 30 Jahren besteht: Der Geschäftsführer von Hymec, Tibor Veres (Mitte) im Gespräch mit einem Mitarbeiter und dem technischen Berater von Horn, Thomas Wassersleben (rechts).
Foto: Horn/Sauermann
Horn stellt mit der Umsetzung des Stoßprozesses erneut sein Know-how in der Präzisionsbearbeitung von Superlegierungen unter Beweis. Durch die eigene Forschung und Entwicklung entwirft der Werkzeughersteller stetig neue Substrate, Geometrien und Beschichtungen für die wirtschaftliche Bearbeitung von schwer zerspanbaren Werkstoffen. Die hohe Fertigungstiefe bietet den Vorteil, dass Horn auf alle Prozessschritte der Werkzeugherstellung, vom Pulver bis zur Beschichtung, den vollen Einfluss hat.
Das könnte Sie auch interessieren:
Wendelschaftfräser erklimmt „Champions League“ in der Schrupp-Bearbeitung
Chancen für Zerspaner und Werkzeughersteller erschließen
Testzentrum bringt Werkzeuge zur Perfektion
Diamantschichten nach Maß für hochleistungsfähige Zerspanwerkzeuge
Nico Sauermann arbeitet als Fotograf und Redakteur bei der Hartmetallfabrik Paul Horn GmbH in Tübingen.