Wissensmanagement für Fräsprozesse
Aufgrund der Unsicherheit der Lieferketten liegt es im Trend, ausgelagerte Fertigungsprozesse wieder ins Haus zu holen. Dazu gehört auch die Bauteilefertigung mithilfe des Fräsens. Damit das erfolgreich gelingt, sind jedoch frische Kompetenzen und einiges an Know-how vonnöten.
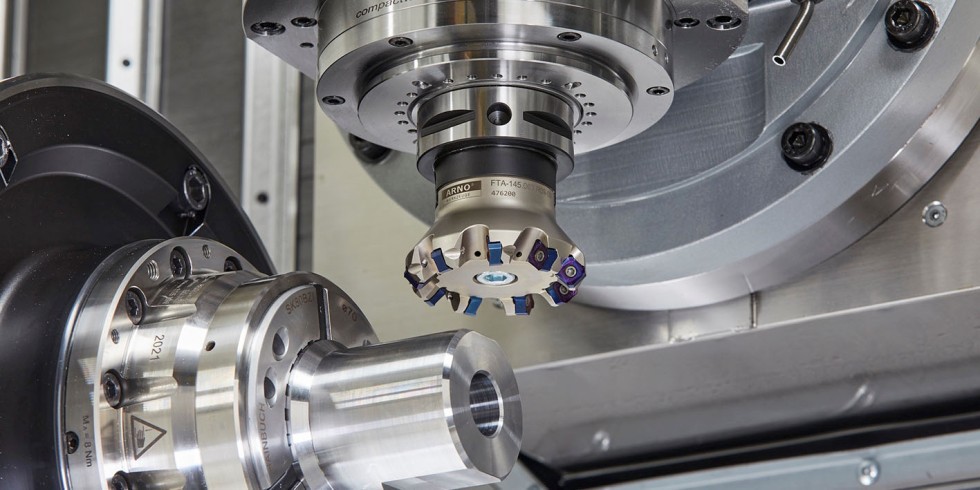
Neben den bewährten Dreh- und Abstechwerkzeugen liefert der Anbieter aus Ostfildern auch (weniger bekannte) Fräswerkzeuge. Diese werden in Deutschland entwickelt und hergestellt.
Foto: Arno
Zeitlos ist der allgemeine Trend, die Produktivität zu steigern und die Wirtschaftlichkeit zu verbessern. Bei aktuellen Vorhaben können die Verantwortlichen und Werkenden in Fertigungsbetrieben jedoch schnell den Überblick verlieren. In der Zerspanung sind die Auswahl und der Einsatz der richtigen Werkzeuge sowie Trägersysteme bedeutend – entscheiden sie doch maßgeblich über ein qualitatives und wirtschaftliches Ergebnis. Was liegt also näher, als einen Hersteller von Werkzeugen zu Rate zu ziehen?
Trend mit Tücken: Fertigungsprozesse zurückverlagern
Wenn die Krisen der letzten Jahre eines deutlich vor Augen geführt haben, denn dies, wie fragil unsere Lieferketten sind – und wie schnell diese auch gestört sein können. Daraus resultiert die Tatsache, dass derjenige „das Geschäft macht“, der überhaupt in vertretbarem Zeitrahmen liefern kann. Infolgedessen werden etliche Prozesse wieder ins Haus geholt, die Hersteller und Fertigungsunternehmen vor Jahren aus Kostengründen zum Beispiel ins Ausland ausgelagert haben. Auf Metallbearbeitungsmessen wie der „AMB“ im Herbst 2022 wurde dieser Trend offensichtlich – und war ein Grund für deren Erfolg. „Unglücklich“ ist aber, wenn mit den Prozessen auch das Know-how abgewandert ist.
Das erfolgreiche Zerspanen von Stahl im Allgemeinen und das kompetente und wirtschaftliche Fräsen im Besonderen ist von zahlreichen Stellgrößen beeinflusst, deren Komplexität einem Fertigungsbetrieb schnell „über den Kopf wachsen kann“. Willkommen sind daher Werkzeughersteller, die von der Anwendungsseite her denken – und die bei komplexen Fertigungsprozessen auch bereitwillig beraten können.
Der schwäbische Mittelständler Karl-Heinz Arnold ist unter der Marke „Arno Werkzeuge“ bekannt für seine bewährten Dreh- und Abstechwerkzeuge und seit vielen Jahren eine feste Größe bei diesen Prozessen. Weniger bekannt ist, dass das familiengeführte Unternehmen ebenso auch innovative Fräswerkzeuge im Programm führt – und auch in Deutschland herstellt. Dies geschieht mit großer Fertigungstiefe und eigener Entwicklungskompetenz, unterstützt durch globale Vertriebsstrukturen.
Werkzeugspezialisten bieten Anwendungs-Know-how „gratis“
So entstehen in Ostfildern moderne und leistungsfähige Fräswerkzeuge, die weltweit für produktives Zerspanen eingesetzt werden. Dazu gehören vor allem ein Trägerwerkzeug für Eckfräs- und HFC-Wendeschneidplatten, ein multifunktionales System zum HFC- und Eckfräsen sowie ein Planfrässystem und Vollhartmetallfräser. Mit Hochvorschubwerkzeugen (HFC steht für High-Feed-Cutting) lässt sich beispielsweise dank sehr hoher Vorschübe und Schnittgeschwindigkeiten auf modernen Fräsmaschinen eine hohe Zerspanleistung erzielen. Diese Hochleistungsfräser verfügen über eine spezielle Schneidengeometrie mit mehreren Schneidkanten.
Doch insbesondere ein neues System zum Planfräsen aus Ostfildern berücksichtigt eine aktuelle Entwicklung. „Ein Trend bei Anwendern geht zu kleineren Aufmaßen der zu bearbeitenden Werkstücke, die schneller – mit höheren Vorschubgeschwindigkeiten – gefahren werden“, berichtet Anwendungstechniker Marco Staiger. Das neue, stabile FT-Planfrässystem 09 belegt, dass bei den Schwaben „von der Anwendung her gedacht wird“. Es ist grundsätzlich sehr stabil ausgelegt und zeichnet sich durch einen weichen Schnitt sowie hohe Laufruhe aus. Das schont die Spindel maximal. Möglich wird das durch eine große Plananlage der Trägerwerkzeuge, einen positiven Spanwinkel (trotz negativer Einbaulage) sowie die Differenzialteilung – viel Know-how ist in einem Werkzeug vereint.
Mehr Zähne und kleinere doppelseitige Wendeschneidplatten
Das neue Frässystem besteht aus zwei Varianten an stabilen Trägerwerkzeugen, die einen Durchmesserbereich von 20 – 125 Millimetern abdecken. Sie sind mit acht Schneiden und dazu passenden kleineren Wendeschneidplatten bestückt. Die Differenzialteilung der Trägerwerkzeuge sorgt dabei für einen ruhigen und vibrationsarmen Fräsprozess. Speziell bei kleinen Aufmaßen verspricht der Hersteller ein höheres Zeitspanvolumen, weil höhere Vorschubgeschwindigkeiten gefahren werden können.
„Weil wir in dem Trägerwerkzeug trotz kleinem Durchmesser eine engere Teilung realisieren konnten, können wir nun im Werkzeug mehr Zähne platzieren“, erklärt Staiger. So lassen sich sogar bis zu neun Wendeschneidplatten montieren, wo seither nur sechs möglich waren. Trotz der engeren Baumaße müssen Anwender nicht auf Kühlung verzichten. Durch die inneren Kanäle für Kühlmedien, wird Kühlschmiermittel oder – bei Trockenbearbeitung – Luft direkt in die Schneidzone geführt und sorgt für wesentlich höhere Standzeiten der Werkzeuge und optimale Spanausbringung. Überzeugend ist vor allem die optimale Ausnutzung der Schneide bei kleineren Zustellungen bis maximal vier Millimetern. So müssen Anwender nicht mehr nur halb genutzte Wendeschneidplatten wegwerfen.
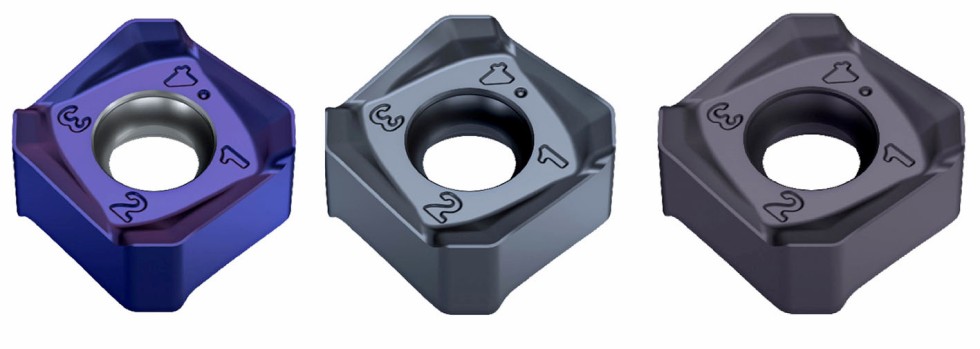
Passend zu den Trägerwerkzeugen gibt es drei Sorten kleiner doppelseitiger Wendeschneidplatten mit je acht Schneiden.
Foto: Arno
Großer Pool von betrachteten Anwendungsfällen sorgt für Kompetenz
Wer sich bei der Bearbeitung nicht zwischen „schnell“ oder „fein“ entscheiden will, greift am besten zum „FD“-Frässystem. Die vernickelten und somit langlebigen Grundhalter für Eckfräs– und HFC–Wendeschneidplatten mit vier effektiven Schneidkanten pro Platte erlauben einen hohen Vorschub. Auch diese Trägerwerkzeuge verfügen über eine Differenzialteilung. Das reduziert Vibrationen und bringt im Ergebnis glatte Oberflächen. Das System sorgt für lange Standzeiten und lässt sich komfortabel handhaben.
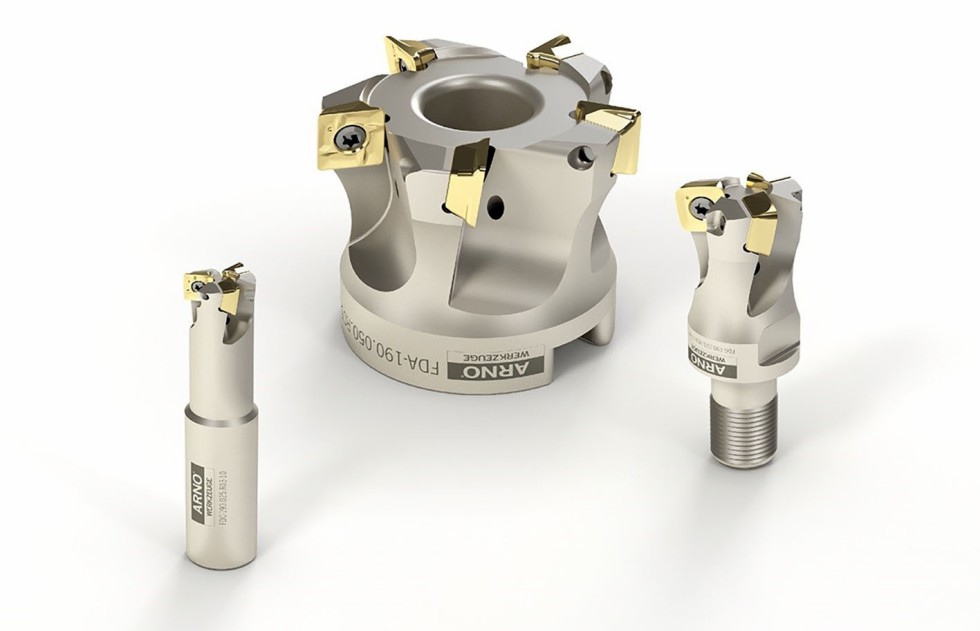
Wer sich bei der Bearbeitung nicht zwischen „schnell“ oder „fein“ entscheiden will, greift am besten zum „FD“–Frässystem.
Foto: Arno
Mit Wendeschneidplatten in 10er und 15er Größen setzen Anwender die Prioritäten bei der Bearbeitung. Mit der kleineren Platte lassen sich aufgrund einer großen Planfase hohe Oberflächengüten erreichen. Dagegen eignen sich die 15er-Platten ideal zum Schruppen, weil sie besonders stabil sind. Mit verschiedenen Geometrien und Sorten kann die Bearbeitung an den jeweiligen Anwendungsfall flexibel angepasst werden. Genau hierbei zeichnet sich der Hersteller aus, weil er aus einem riesigen Pool von Anwendungsfällen Erfahrungen schöpft und zum jeweils passenden Werkzeugsystem beraten kann.
Einen weichen Schnitt versprechen die präzisionsgefertigten, positiven Spanleitstufen der Wendeschneidplatten. Und weil sie auch umfanggeschliffen und poliert sind, kann die „PMA“-Geometrie ebenso gut Aluminium und Nichteisen-Metalle zerspanen.
Mit Vollhartmetallfräsern haben die Schwaben darüber hinaus Werkzeuge im Sortiment, mit denen durch weniger Werkzeugwechsel optimale Produktionsprozesse bei geringen Stillstandszeiten gelingen. Die Vollhartmetallfräser sind aus „Ultra-Micro-Grain“ – Feinstkorn-Hartmetall zwischen 0,1 und 0,5 µm – gefertigt und überzeugen durch eine konstante Materialbeschaffenheit. Je nach Ausführung sind sie mit TiAIN, TiCN oder AlCrN beschichtet.
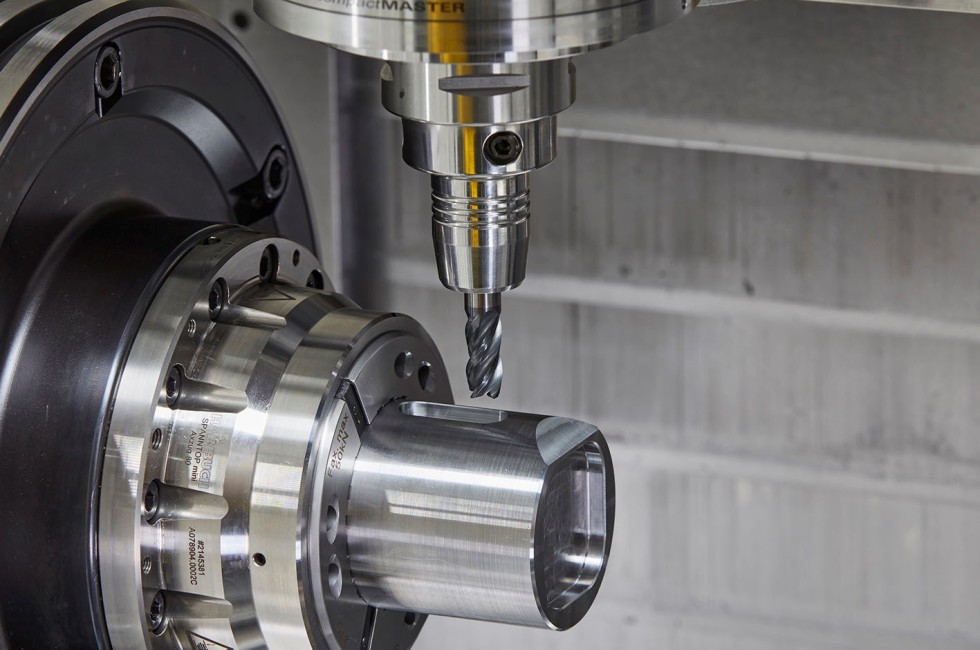
Mit den Vollhartmetallfräsern lassen sich dank einer geringeren Zahl an Werkzeugwechseln optimale Produktionsprozesse bei niedrigen Stillstandszeiten erzielen.
Foto: Arno
Individuelle Lösungen „punkten“
Ideal ist es aus Anwendersicht, wenn sich der Werkzeuganbieter mit speziellen Produktlinien auf die Bedürfnisse seiner Kunden einstellen kann. So gibt es mit der „Basic-Series“ wirtschaftliche, grundsolide Werkzeuge mit vielen Sorten und Geometrien, die sich für ein breites Spektrum an Zerspanungsaufgaben eignen. Wenn hingegen Oberflächen überragend sein müssen, bei Standzeiten jede Minute zählt, schwer zerspanbare Werkstoffe bearbeitet werden oder große Serien laufen, gibt es die Werkzeuge der „Major-Series“. Die können, zum Beispiel bei Beschichtungen oder Trägerwerkzeugen, individuell angepasst werden. Mit seinen durchdachten und ausgereiften Fräswerkzeugen braucht sich der Werkzeuge-Anbieter also „nicht zu verstecken“.
Das 1941 von Emil Arnold gegründete Unternehmen wird in dritter Generation von den Eigentümern geführt. Die leistungsfähigen Werkzeuge werden weltweit für die produktive Zerspanung beim Kurz- oder Langdrehen, Stechen, Drehen, Bohren oder Fräsen eingesetzt. Mit über 200 Mitarbeitern am Stammsitz in Ostfildern und in den sechs Niederlassungen sowie zahlreichen Vertriebsstandorten weltweit setzt das Traditionsunternehmen auf Kundennähe. 2023 werden voraussichtlich 54 Millionen Euro Umsatz erzielt – und damit fast wieder das Vorkrisenniveau erreicht.
Das könnte Sie auch interessieren:
Wenn jedes Gramm zählt: Werkzeuge für schnelle Elektromobile
Werkzeuge werden produktiver und nachhaltiger
Planfräser erzielen Leistungssprung für die Drucklufterzeugung