Zukunftssicheres Maschinen-Upgrade mit KI und Edge Computing
Auch wenn das Ziel von Industrie 4.0 die Vernetzung des gesamten Maschinenparks ist: Für die Optimierung der Abläufe bleibt die einzelne Werkzeugmaschine ein entscheidender Ansatzpunkt. Was können Edge Apps im Betrieb von Bestandsmaschinen leisten?
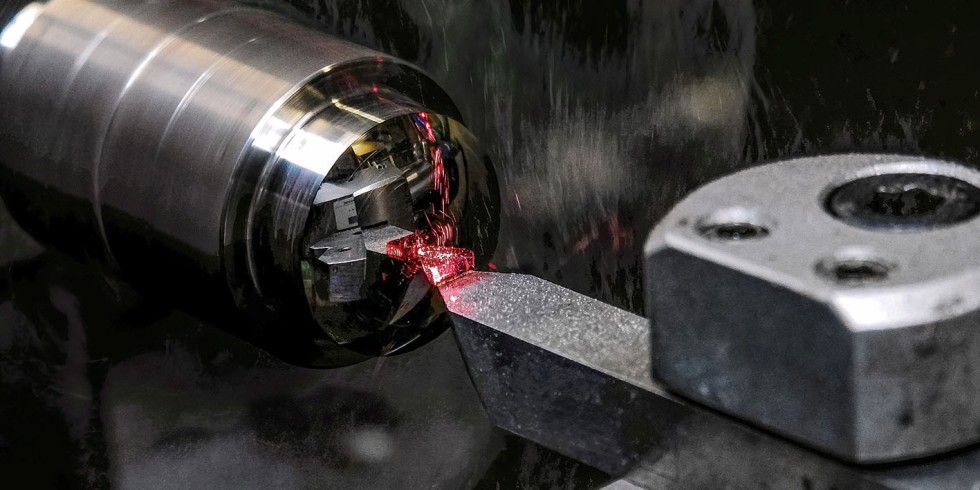
Überwachung des Zustands einer Wendeschneidplatte während der Ultrapräzisionsbearbeitung mittels eines Laservibrometers: Maßgeschneiderte Apps sollen künftig für spezifische Anwendungsfälle generiert werden. Zum Beispiel lassen sich dann Daten aus der Werkzeugeinsatz-Historie mit den Qualitätsdaten gefertigter Bauteile zusammenführen.
Foto: IWF TU Berlin / Michael Wendt
Voraussetzung für eine effiziente Vernetzung im Zuge der hochflexiblen Fertigung ist der reibungslose Informationsfluss über die gesamte Wertschöpfungskette. Aus Sicht der einzelnen Werkzeugmaschine spielt daher vor allem ihre Schnittstelle – quasi als Nadelöhr der Vernetzung – eine zentrale Rolle: Sie stellt sicher, dass die Maschine mit anderen Maschinen und Anlagen, IT-Systemen und Menschen große Mengen an Daten austauschen kann.
Big Data als Chance nutzen
Gleichzeitig stehen Unternehmen vor der schwierigen Aufgabe, die immer größeren digitalen Datenberge, die tagtäglich während der Produktion erzeugt werden, systematisch zu erfassen, zu speichern und auszuwerten. So generiert eine einzelne CNC-gesteuerte Werkzeugmaschine binnen einer Sekunde eine Vielzahl an Informationen – sei es zur Steigerung von Effizienz und Qualität der Fertigung, oder um den mechanischen Zustand der Maschine zu erfassen. Durch die intelligente Analyse dieser Daten lassen sich wertvolle Erkenntnisse gewinnen, die als Basis für Prozessoptimierungen und wichtige unternehmerische Entscheidungen dienen können. Doch bislang war das Heben dieses Datenschatzes für Unternehmen schwierig bis unmöglich.
Forschende am Produktionstechnischen Zentrum (PTZ) Berlin haben sich dieser Herausforderung angenommen und untersucht, wie sich Steuerungsdaten von Werkzeugmaschinen ohne großen Aufwand erfassen, auswerten und nutzbar machen lassen. Konkret geht es darum, bereits vorhandene, hochproduktive Maschinen mittels neuer Schnittstellen zu optimieren und dadurch ihre Fähigkeiten gezielt zu erweitern.
KI und Edge: ein „starkes Duo“ für die Prozessoptimierung
Das „digitale Retrofit“ – das Nachrüsten von Maschinen mit modernster Sensorik und Kommunikationstechnik – haben die Datenspezialisten des PTZ über eine Edge-Computing-Lösung mithilfe von Künstlicher Intelligenz (KI) realisiert. Beim Edge Computing werden die Daten direkt am Ort des Entstehens, der Edge, erfasst und gespeichert. So müssen sie keine weiten Strecken zu zentralen Rechenzentren zurücklegen, sondern können ohne große Verzögerung weiterverarbeitet werden. Das ist wichtig, da es in der automatisierten Produktion auf kurze Reaktionszeiten ankommt und die Verzögerungszeit des Cloudzugriffs auf lokale KI-Anwendungen oft zu hoch ist.
Da die KI-Modelle beim Edge Computing nicht in der Cloud, sondern auf dem Endgerät ausgeführt werden, ist zudem eine rechenstarke Hardware einer der Grundpfeiler. Für das Projekt wurde ein Industrie-PC mit zwei Ethernet-Anschlüssen verwendet, der über eine interne Hochfrequenzschnittstelle direkt an die Maschinensteuerung angeschlossen wird.
Mithilfe des Edge-Geräts und in Verbindung mit einer neuartigen Edge-Plattform gelang es dem Team am PTZ, rund einhundert verschiedene Systemvariablen einer Werkzeugmaschine zu erfassen. Dies beinhaltet etwa Daten in Bezug auf die Spindeldrehzahl, den Zahnvorschub, die Schnitttiefe, die Vorschubgeschwindigkeit, Konturabweichungen sowie indirekte Informationen zur Bauteilqualität. Zeitsynchron zu diesen Parametern und bis zu 30.000 mal pro Sekunde können zudem Daten aus externer Sensorik wie Kameras oder Kraftsensoren ausgelesen sowie Informationen über Standzeiten und Fehlermeldungen abgerufen werden.
Von der Datenerfassung zur nutzenbringenden Auswertung
Die derart erfasste, unstrukturierte Rohdatenflut wird durch den Einsatz der KI auf der Edge-Plattform systematisch analysiert und in aussagekräftige Erkenntnisse – das heißt in wirtschaftlichen Mehrwert – umgeformt: Durch die kluge Datenanalyse lassen sich versteckte Optimierungspotenziale aufspüren, es werden Fehlerquellen identifiziert sowie Maschinenverschleiß und -defekte rechtzeitig offengelegt.
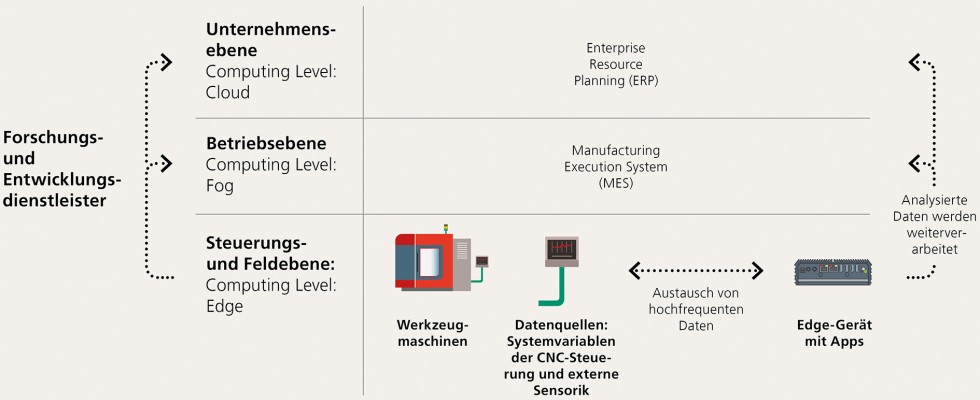
Systemarchitektur der Edge-Computing-Plattform: Damit gelang es dem Team am PTZ, rund einhundert verschiedene Systemvariablen einer Werkzeugmaschine zu erfassen. Grafik: IWF TU Berlin
Weitere Schnittstellen des Edge-Geräts, unter anderem „Open Platform Communications Unified Architecture“ (OPC UA), dienen zur Weiterleitung der Daten an übergeordnete Systeme wie MES (Manufacturing Execution System) oder ERP (Enterprise Resource Planning), an „Data Lakes“ zur Speicherung großer strukturierter Datenmengen sowie an unternehmenseigene Server oder Cloud-Plattformen. Die Auswirkungen des Datenverkehrs auf die CPU der Werkzeugmaschine sind hingegen minimal, da die eigentliche Verarbeitung auf dem Edge-Gerät erfolgt. Das bedeutet, dass das Edge-Gerät in bestehende Werkzeugmaschinen eingebaut werden kann, ohne diese in ihrer eigentlichen Steuerungsaufgabe zu beeinträchtigen.
Darüber hinaus ist es möglich, über eine Feedback-Schleife die Bearbeitungsparameter der Werkzeugmaschine zu beeinflussen, also Befehle an die Maschinensteuerung zurückzumelden. Die Forschenden arbeiten bereits daran, erste Teile dieses Prozesses an eine entwickelte KI auszulagern.
Beispiel: Mit KI Werkzeugverschleiß erkennen
Nachdem das Edge-Gerät erfolgreich an der Werkzeugmaschine installiert ist, können Apps dabei helfen, die Maschinendaten einfach und übersichtlich anzuzeigen. Neue Applikationen oder Sicherheitspatches lassen sich hierbei unkompliziert implementieren. In App Stores werden bereits Anwendungen zum Download bereitgestellt, die sich auf die Überwachung des Werkzeugzustands und die Vorhersage des Werkzeugverschleißes fokussieren. Hiermit können Anwender passgenaue Entscheidungen, basierend auf einem KI-Modell, treffen.
Edge Apps im Einsatz: Chancen für die Produktion
Als Dienstleister entwickeln die Datenexperten des PTZ auch maßgeschneiderte Apps für spezifische Anwendungsfälle von kleinen und mittelständischen Unternehmen (KMU). Denkbar ist beispielsweise, Informationen aus datenintensiven Experimenten in Form einer App zu extrahieren, die dann an einer Werkzeugmaschine mit speziell angepasstem Edge-Gerät eingesetzt wird. Ebenso können Daten aus der Werkzeugeinsatz-Historie mit den Qualitätsdaten gefertigter Bauteile zusammengeführt werden. Sie lassen sich dann für eine Optimierung von Werkzeuggeometrien und -werkstoffen nutzbar machen. Möglich ist auch die intelligente Online-Überwachung der Werkzeugmaschine: Fertigungsfehler, beispielsweise aus vorangegangenen Prozessen, werden so unmittelbar erkannt und lassen sich unmittelbar beheben.
Das könnte Sie auch interessieren:
Onlinefähiges Ratter-Frühwarnsystem erkennt Prozessinstabilitäten

Martin Heper ist wissenschaftlicher Mitarbeiter und Data Scientist in der Gruppe Zerspanung im Fachgebiet Werkzeugmaschinen und Fertigungstechnik am Institut für Werkzeugmaschinen und Fabrikbetrieb IWF der Technischen Universität Berlin. Foto: IWF
Martina Rennschmid arbeitet als freie Redakteurin und schreibt vorzugsweise über Wissenschafts- und Forschungsthemen.