Zulieferteile: Präzision aus Aluminium oder Messing
Wer bei komplexen Zulieferteilen nur auf eine Umformtechnik setzt und lediglich eine Werkstoffklasse anbieten kann, wird selten die optimale Lösung im Angebot haben. Technologische Vielfalt „punktet“, wie Praxisbeispiele eines innovativen Herstellers aus diversen Anwenderbranchen zeigen.
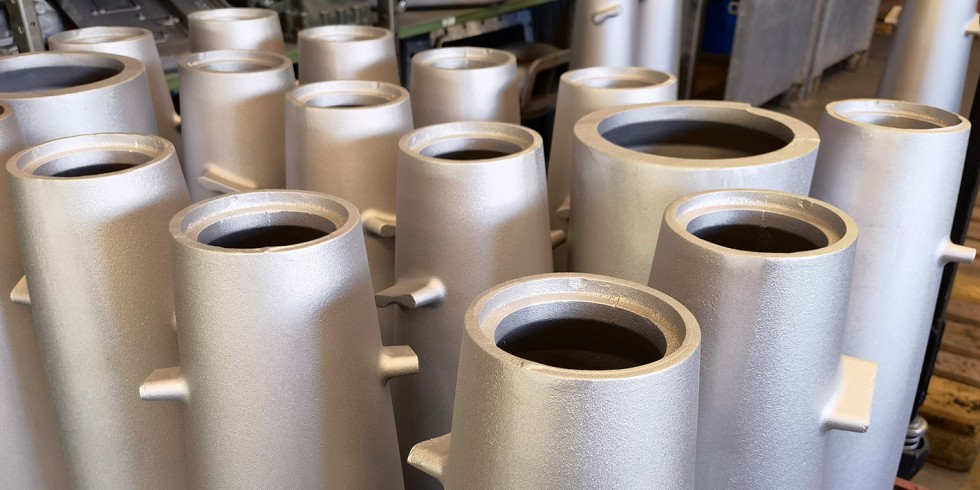
Im Sandgießverfahren hergestellte Aluminiumsäulen für moderne Diagnosesysteme für die Medizintechnik.
Foto: Klaus Vollrath
Häufig verfügen Lieferanten von hochwertigen Maschinenelementen über nur eine einzige Technologie – wie das Konstruieren mit Blech – oder nur eine Werkstoffklasse wie z.B. Stahl. In diesem Fall versucht der Betrieb bei Kundenanfragen natürlich, die Aufgabe damit zu lösen. Das kann im Vergleich zu anderen Technologien zu technisch oder finanziell „suboptimalen“ Ergebnissen führen.
Wer dagegen über eine breitere Palette an Verfahren und Werkstoffen im Portfolio hat, bietet mehr Freiheitsgrade bei der Wahl der geeigneten Lösung. Ein mittelständischer Schweizer Zulieferer setzt gleich drei Technologien ein und verarbeitet sowohl Aluminium- als auch Messing- und Kupferlegierungen. Ergänzt wird dies durch umfassende Zusatzleistungen – von der Entwicklungspartnerschaft über die hochpräzise Bearbeitung bis zur Lieferung komplett einbaufertig montierter Baugruppen.
Gießerei und Presswerk unter einem Dach
„Die meisten unserer Kunden suchen nach einer Lösung für eine bestimmte Aufgabenstellung. Bezüglich der Details wie Fertigungsverfahren oder Werkstoff lassen sie sich von uns beraten“, erläutert Fabrizio Passani, zuständig für den Verkauf bei der Firma Metalyss AG in Lyss (Schweiz). Daher sei es für sie vorteilhaft, dass im Hause eine außergewöhnlich breite Palette an Werkstoffen und Herstelltechnologien unter einem Dach vereint sei. 1899 gegründet, hat sich bis heute ein mittelgrosser, gut etablierter und unabhängiger Zulieferbetrieb etabliert, der rohe und einbaufertig bearbeitete Aluminiumguss- und Gesenkschmiedeteile in allen Seriengrößen herstellt. Mit rund 60 Mitarbeitern geschieht dies ausschließlich in der Schweiz.
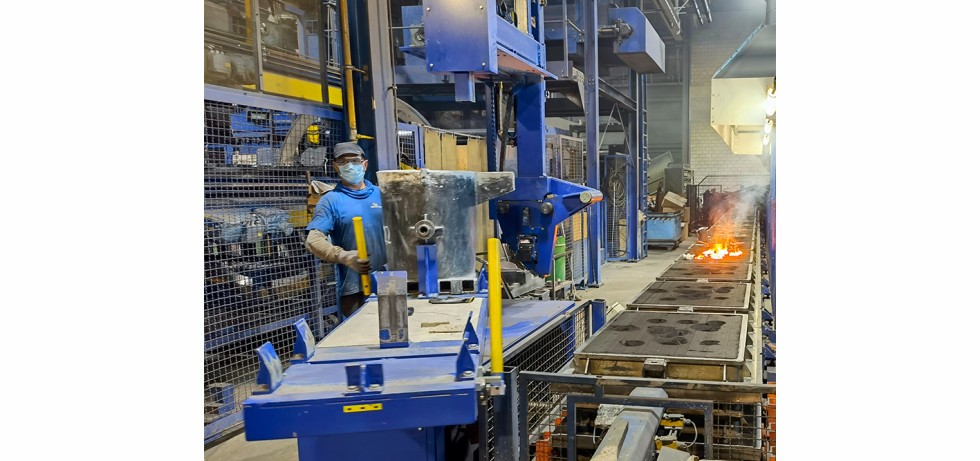
Die „Gießhexe“ entlastet die Mitarbeiter von schwerer körperlicher Arbeit. Die Steuerung erfolgt mittels Joystick, und ein Laserkreuz markiert die exakte Gießposition.
Foto: Klaus Vollrath
In der Gießerei werden zahlreiche Aluminiumlegierungen sowohl in Sand als auch in Kokille vergossen. Im Presswerk entstehen Warmpressteile aus Aluminium-, Messing- oder Kupferlegierungen. Diese Vielfalt der Verfahren und Werkstoffe ermögliche es ihm, seine Kunden werkstoff- und technologieneutral zu beraten – und ihnen somit eine möglichst gut auf ihren spezifischen Bedarf hin optimierte Lösung anzubieten. Zudem werden insbesondere beim Gießen zahlreiche „Sonderkniffe“ eingesetzt. Abgerundet wird das Leistungspaket durch präzise Bearbeitung auf automatisierten Werkzeugmaschinen sowie durch hochwertige Oberflächenveredlung.
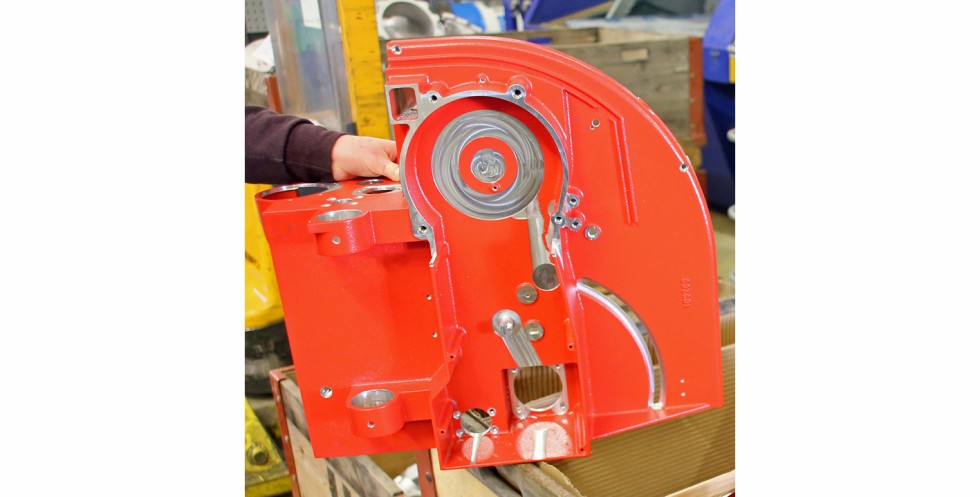
Präzision und Ästhetik: Die Fähigkeit zur Bearbeitung bereits lackierter Gussteile ermöglicht die Verwirklichung ausgefallener Designideen.
Foto: Klaus Vollrath
Niedrige Preise mit hoher Flexibilität kontern
„Als Mittelständler in Europa können wir gegen asiatische Mikropreise vor allem durch Schnelligkeit, Flexibilität und die kurzen Wege zu unseren Kunden punkten“, betont Passani. Während es bei anspruchslosen Großserienteilen vor allem auf den niedrigsten Preis ankomme, zähle bei europäischen Kunden oft der Mehrwert, der sich aus der Kombination aus Beratung, Schnelligkeit, Liefertreue und Qualität ergebe.
Ein Beispiel sind Aluminium-Kupplungsstücke für Hydranten, die aus einer hochfesten Aluminium-Knetlegierung hergestellt werden. Im Vordergrund steht „zero waterloss“. Das Aluminium-Kupplungsstück bildet das Gehäuse eines Rückschlagventils, welches verhindern soll, dass kontaminiertes Wasser zurück ins Trinkwassernetz gelangt. Diese Bauteile werden inzwischen in so großen Stückzahlen nachgefragt, dass sie vollautomatisch rund um die Uhr auf einem Dreh-Fräs-Bearbeitungszentrum hergestellt werden. Die Be- und Entladung erfolgt hierbei mittels Roboter.
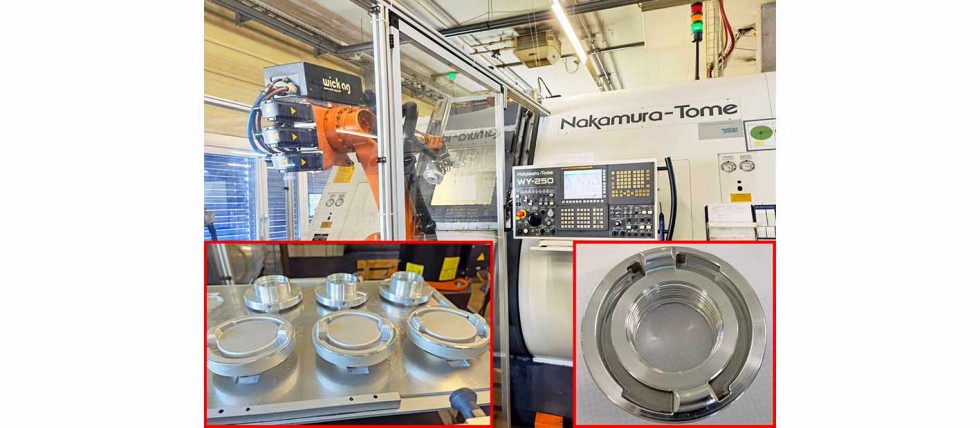
Die wassersparende Schlauchkupplung für Feuerwehr-Hydranten (unten rechts) wird auf einem Dreh-/Fräszentrum hochpräzise bearbeitet. Dank einer Roboterbeschickung läuft die Fertigung rund um die Uhr.
Foto: Klaus Vollrath
Hightech-Komponenten und Entwicklungspartnerschaft überzeugen
„Unsere wichtigste Zusatzleistung ist die Unterstützung unserer Kunden bei der Entwicklung neuer Produkte“, ergänzt Passani. Jeder Herstellprozess habe seine spezifischen Besonderheiten und Rahmenbedingungen, die zu berücksichtigen sind. Ansonsten entstehen unzureichende Ergebnisse mit Nachteilen sowohl technischer als auch wirtschaftlicher Natur. Jedes Herstellverfahren birgt spezielle Kniffe. So lassen sich beispielsweise in die Bauteile ohne nennenswerten Zusatzaufwand zusätzliche Funktionen integrieren. Deshalb sei es sehr wichtig, dass die Entwicklungsabteilungen von Kunde und Lieferant so frühzeitig wie möglich in der Entwurfsphase zusammen kommen. Dank langjähriger Tradition und geringer Fluktuationsquote punktet der Betrieb zudem mit erfahrenen Mitarbeitern, denen zudem neueste computergestützte Programme für die Produkt- und Prozessentwicklung zur Verfügung stehen.
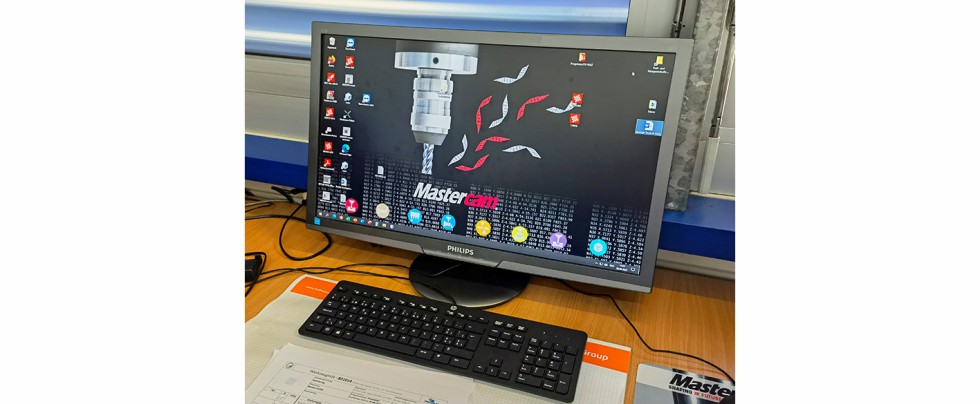
Den Entwicklern stehen moderne CAD/CAM-Programme für Konstruktion und Bearbeitungsplanung zur Verfügung. Software von Magma unterstützt die Simulation des Gießprozesses.
Foto: Klaus Vollrath
Im Gießereibereich kommt das Programm „Magma“ zur Simulation von Gießvorgängen zum Einsatz. Mithilfe der so ermittelten Ergebnisse werden fallweise auch Prototypen als Anschauungs- und Funktionsmodelle im 3D-Druck aus Kunststoff hergestellt. Geht es bei Gussteilen lediglich um Einzelstücke oder Kleinserien, so können entsprechende Formen als 3D-Sandgussteile günstiger extern bezogen werden. Die Vorteile überwiegen gegenüber der „klassischen“ Herstellung aufwendiger Modelle für die Herstellung der Gießformen. Die so erzeugten Prototypgussteile entstehen somit sowohl im Serienverfahren als auch aus dem Serienwerkstoff und sind voll funktionsfähig. In derartigen gemeinsamen Projektarbeiten entstehen Produkte, die sowohl von der Leistungsfähigkeit als auch von den Kosten her deutlich vorteilhafter sind als die ursprünglichen Entwürfe.
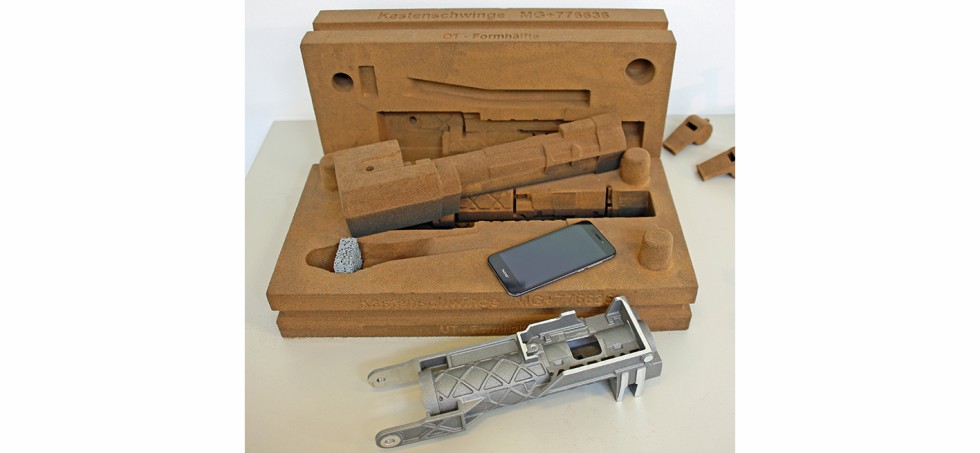
Im 3D-Druckverfahren hergestellte Sandform einschließlich des Kerns. Im Vordergrund ist das damit im Serienverfahren und aus dem Serienwerkstoff hergestellte Prototypen-Gussteil zu sehen.
Foto: Klaus Vollrath
Geschickte Maßnahmen für Kosteneffizienz in der Gießerei
„In der Gießerei investieren wir kontinuierlich in moderne, rationelle Technologie“, sagt Passani. Vergossen werden Aluminium – sowohl im Sand- als auch im Kokillengießverfahren – geschmiedet werden nebst Aluminiumlegierungen auch Messing- und weitere Kupferlegierungen. Hervorzuheben sei die neue „Gießhexe“ in der Sandgießerei. Dabei handelt es sich um eine automatisierte Gießstation, die den Gießer von schwerer körperlicher Arbeit entlastet und es ihm gestattet, den Gießvorgang einfach durch Joystick zu steuern. Zusätzlich hilft ein Laser-Fadenkreuz dabei, Fehler beim Anvisieren der Gießöffnung zu vermeiden.
Die Gießerei ist zudem besonders flexibel, weil sie zum einen mit zwei verschiedenen Gießkastenformaten arbeitet und dadurch eine große Bandbreite an Abmessungen darstellen kann. Zweiter Pluspunkt ist darüber hinaus, dass neben dem Sandgießen auch das wesentlich formgenauere Kokillengießen angeboten wird. In diesem Bereich kommen metallische Dauerformen zum Einsatz, in denen das Metall sehr schnell erstarrt. Das Gefüge ist deshalb feiner und dichter und daher auch fester und belastbarer als bei Sandgussteilen. Zudem haben Kokillengussteile eine deutlich glattere Oberfläche, so dass weniger Bearbeitungsaufwand entsteht. Derartige Teile aus Aluminium kommen beispielsweise bei Komponenten für Beatmungsgeräte in der Medizintechnik zum Einsatz.
Eine Spezialität sind Verbundgussteile – beispielsweise aus Aluminium mit eingegossenen Metallrohren, die zur Durchleitung von Wasser oder anderen Temperiermedien dienen. Weiteres Spezialgebiet ist der Einsatz von Formen, die mit Hilfe des 3D-Druckverfahrens aus speziell beschichteten Formstoffen erzeugt werden. Das 3D-Drucken ist in solchen Fällen sehr kostengünstig, wenn es sich um Einzelstücke oder Kleinstserien handeln, weil keine aufwendigen Modelle für die Formen erzeugt werden müssen.
Schmiedeteile: hochfest und druckdicht
Schmiedelegierungen erreichen hohe Festigkeiten und halten zudem Druck besonders gut stand. Verarbeitet werden alle drei Werkstoffe: Aluminium, Kupfer bzw. Messing. Zu den Aluminium-Schmiedeteilen gehören beispielsweise Fahrradnaben mit sehr anspruchsvoller Geometrie, die im fertig bearbeiteten Zustand sehr filigran und daher leicht sind. Die Legierung muss zur Gewährleistung der vom Kunden geforderten Festigkeitswerte in einem sehr engen Temperintervall geschmiedet und wärmebehandelt werden. Auch bezüglich ihrer Zusammensetzung sind so enge Toleranzen vorgegeben, dass das Material ungeachtet höherer Kosten ausschließlich von einem Schweizer Zulieferer bezogen wird. In ihrem Inneren beherbergen die Fahrradnaben zudem die anspruchsvolle Mechanik, u.a. für den Freilauf.
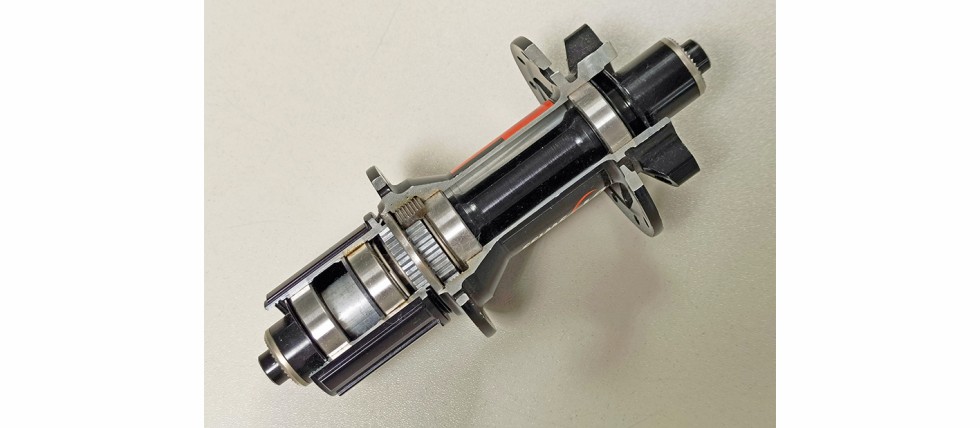
Diese sehr anspruchsvolle Fahrradnabe wird aus einem Schmiedeteil in einem 12-Achs-Bearbeitungszentrum in einer Aufspannung gefertigt. Damit lassen sich sogar die Löcher für die Speichen von innen ansenken.
Foto: Klaus Vollrath
Eigener Maschinenpark für die hochpräzise Fertigbearbeitung
„Mit Rohteilen können unsere Kunden in der Regel wenig anfangen. Sie wollen eher präzise, bei der Lieferung bereits einsatzfertige Komponenten, die ihnen direkt in die Fertigung zugeliefert werden“, verrät F. Passani. Diese Wünsche könne man dank eines Maschinenparks von insgesamt zwölf Werkzeugmaschinen, zumeist Drehfräszentren oder reine Fräszentren mit fünf oder mehr Achsen, erfüllen.
Ein Beispiel für solche Lösungen sind unter anderem zwei Komponenten für einen Teilapparat für Senkerodiermaschinen, bei denen es auf äußerste Rechtwinkligkeit sowie Koaxialität ankommt. Die geforderte Bearbeitungsgenauigkeit liegt bei ± 4 Mikrometern, bezüglich der Oberflächenqualität wird M5 erreicht. Das Bauteil wird auf einem Dreh-Fräszentrum mit zwölf Achsen und automatischer Zuführung einbaufertig bearbeitet. Abnehmer sind vor allem bekannte Schweizer Markenhersteller.
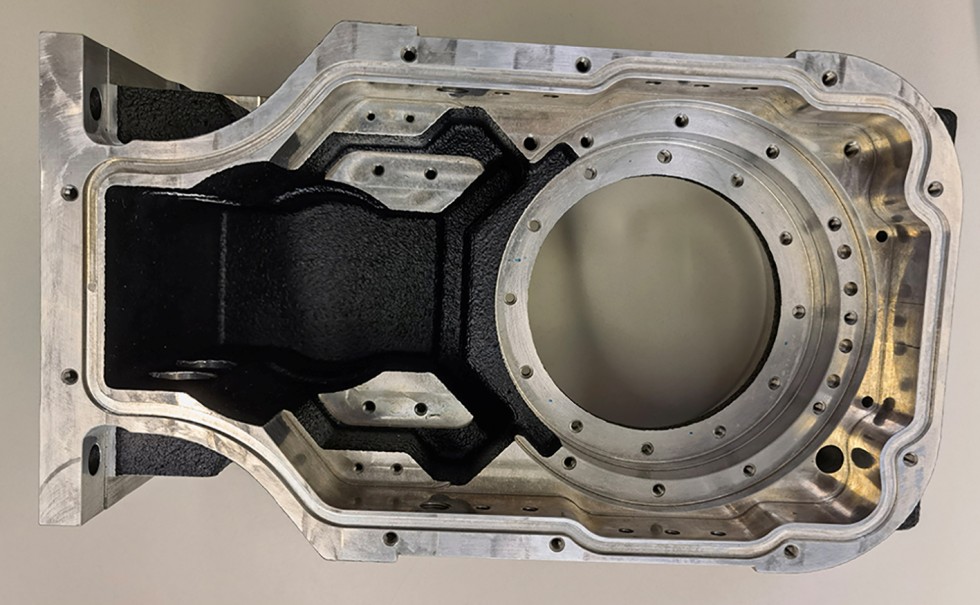
Komponente für einen Teilapparat für Senkerodiermaschinen mit hohen Ansprüchen an Rechtwinkligkeit sowie Koaxialität. Die geforderte Bearbeitungsgenauigkeit liegt bei ± 4 µm.
Foto: Klaus Vollrath
Für besonders diffizile Bearbeitungsaufgaben stehen zwei Anlagen mit zwölf beziehungsweise neun Achsen zur Verfügung. Viele dieser Bearbeitungszentren sind zudem mit Zuführsystemen oder Robotern automatisiert. Auch die Qualitätssicherung überzeugt: Sie läuft mit modernen Messsystemen in einem temperaturstabilisiertem Messraum ab.
Das könnte Sie auch interessieren:
Effiziente Helium-Dichtheitsprüfung von großen Automobil-Bauteilen
Hartwalzen optimiert Festigkeit wälzbelasteter Funktionsflächen
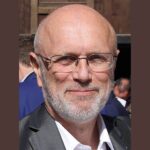
Klaus Vollrath ist freier Fachjournalist in Aarwangen. Foto: Autor