3D-CAD-Modelle lenken die Fertigung
Bestandteil von „Industrie 4.0“ ist die Digitalisierung entlang des gesamten Produktlebenszyklus. Ein wesentlicher Baustein dafür ist eine durchgängige 3D-Modellkette, bei der das 3D-Mastermodell alle Schritte in der Fertigung und Qualitätssicherung mit den erforderlichen Informationen versorgt – wie die Arbeitsplanung, die CNC-Programmierung und die Messgeräteprogrammierung. Die 3D-Modellkette findet unter anderem bei neuen Produktreihen von Kraftwerkskomponenten Anwendung.
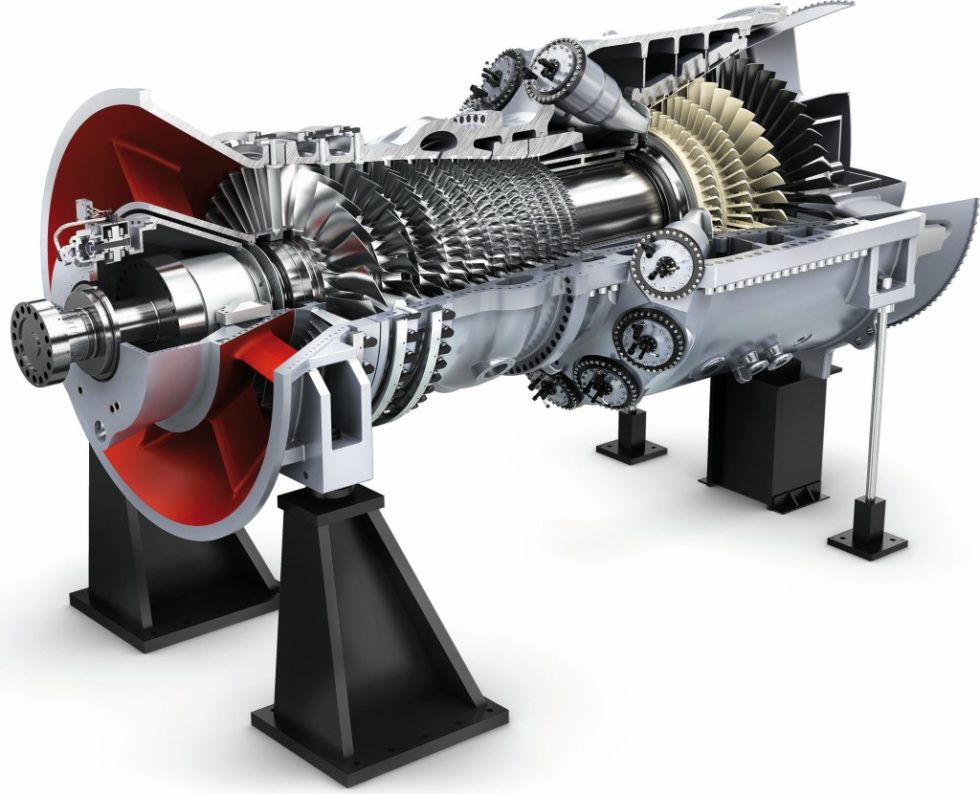
Schematische Darstellung einer Siemens-Gasturbine aus der neuen Baureihe der „HL“-Klasse. Bild: Siemens
Zu den neuen Produkten gehört die Gasturbinenbaureihe der „HL“-Klasse von Siemens und dazu die „SGT5-9000HL“, „SGT6-9000HL“ sowie die „SGT5-8000HL“. Durch Digitalisierung lässt sich eine signifikante Verkürzung der Lieferzeit kundenspezifischer Kraftwerkslösungen und eine Verkürzung des Time-to-Market bei Neuentwicklungen erzielen.
Ausgangssituation
Seit Mitte der 1990er Jahre läuft die Umstellung von 2D-Zeichnen auf 3D-Modellieren. In vielen Firmen wird gerade eine neue Generation 3D-fähiger CAD-Systeme eingeführt. Doch eine wirklich durchgängige Modellkette, basierend auf den 3D-CAD-Modellen und den darin dargestellten Konstruktionselementen (Features), ist in den wenigsten Firmen etabliert. Meistens findet auch heute die Produktdefinition von Bauteilen durch eine 2D-Zeichnung statt. Zwar wird diese von einem 3D-CAD-Modell abgeleitet, allerdings unterscheiden sich die Inhalte häufig. Zwar sind in modernen CAD-Systemen alle Funktionen vorhanden, um bidirektional und assoziativ zwischen 3D-CAD-Modell und 2D-Zeichnung arbeiten zu können. Jedoch mangelt es an standardisierten Methoden, um diese Funktionen anwenden zu können.
Siemens Power and Gas nutzt bei der Digitalisierung ihrer Produktentstehungsprozesse die Umstellung der etablierten 2D-zeichnungsbasierten Prozessketten auf durchgängige 3D-Modellketten, um die Lieferzeit von kundenspezifischen Lösungen zu reduzieren und die Entwicklungszyklen für Kraftwerkskomponenten wie Gasturbinen, Dampfturbinen und Generatoren zu verkürzen. Für die Realisierung der durchgängigen 3D-Modellkette werden Siemens „NX“ als integrierte Software für die Bereiche CAE, CAD, CAM und Messgeräteprogrammierung (zum Beispiel für Koordinatenmessmaschinen – KMM) verwendet.
Zeichnungsbasierte Prozessketten
Bei etablierten 2D-zeichnungsbasierten Prozessketten, die heute im Maschinen- und Anlagenbau weit verbreitet sind, ist eine 2D-Zeichnung wichtige Grundlage für Arbeitsplanung, CNC- und Messgeräteprogrammierung, Bild 1.
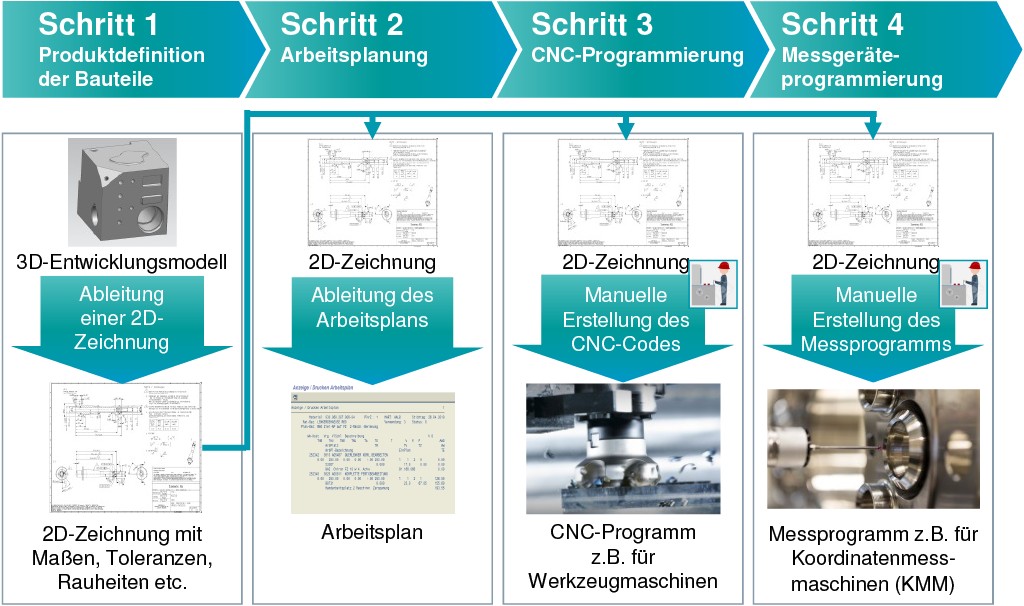
Bild 1. 2D-zeichnungsbasierte Prozesskette für die Produktdefinition der Bauteile, Arbeitsplanung, CNC- und Messgeräteprogrammierung (Darstellung am Beispiel eines Referenzbauteils). Bild: Siemens
In Schritt 1 wird ein 3D-Entwicklungsmodell in der Nennmaßgeometrie erstellt (Bild 1). Davon wird eine 2D-Zeichnung abgeleitet. Dort werden alle für die Fertigung und die Qualitätssicherung relevanten Informationen dokumentiert. Damit folgt die Überprüfung und Freigabe der Produktdefinition der Bauteile auf Grundlage der 2D-Zeichnung. In den Schritten 2 bis 4 werden auf Grundlage der 2D-Zeichnung die Fertigungs- und Prüfprozesse geplant, vorbereitet und durchgeführt. Die Erstellung der CNC-Programme folgt entkoppelt vom 3D-Entwicklungsmodell und Änderungsworkflow. Heute verfolgen CAM-Experten und Maschinenbediener dabei meist eine der folgenden Strategien:
- Das CNC-Programm wird auf Grundlage der 2D-Zeichnung erstellt – in Form einer Werkstatt- oder einer Büro-Programmierung („Off-line-Programmierung“).
- Ein prozessspezifisches „3D-Arbeitsvorgangsmodell“, das vom 3D-Entwicklungsmodell unabhängig ist, wird auf Grundlage der 2D-Zeichnung erstellt. Auf dessen Grundlage folgen beispielsweise für Werkzeugmaschinen die Definition der zu verwendenden Zerspanungswerkzeuge, die Bahnplanung und die Definition der Bearbeitungsparameter.
Bei der 2D-zeichnungsbasierten Prozesskette besteht in allen beschriebenen Strategien jedoch keine Assoziativität zwischen Geometrie- und Fertigungsinformationen (wie Toleranz- und Oberflächeninformationen auf der 2D-Zeichnung) und der CNC- und KMM-Programmierung. Deswegen haben Änderungen in der Produktdefinition in Form der 2D-Zeichnung händische – und damit arbeitsintensive sowie fehleranfällige Arbeitsvorgänge – bei der CNC- und Messgeräteprogrammierung zur Folge (Bild 1). Die fehlende Assoziativität zwischen Produktdefinition und Fertigungsvorbereitung sowie Vorbereitung der Qualitätssicherung behindert Simultaneous Engineering (die Parallelisierung der Prozessschritte bei der Produktentstehung).
Eine durchgängige 3D-Modellkette stellt die Assoziativität zwischen der Produktdefinition der Bauteile in Form eines 3D-Mastermodells und der CNC- sowie Messmittelprogrammierung her.
Durchgängige 3D-Modellkette
Kennzeichen einer durchgängigen 3D-Modellkette sind die Assoziativität zwischen dem 3D-Mastermodell, das ebenfalls die Produktdefinition der Bauteile darstellt, und dem Arbeitsplan sowie der CNC- und Messmittelprogrammierung. Damit führen Änderungen in der Produktdefinition direkt zu Anpassungen im Arbeitsplan, in der CNC-Programmierung und in der Messgeräteprogrammierung, Bild 2.
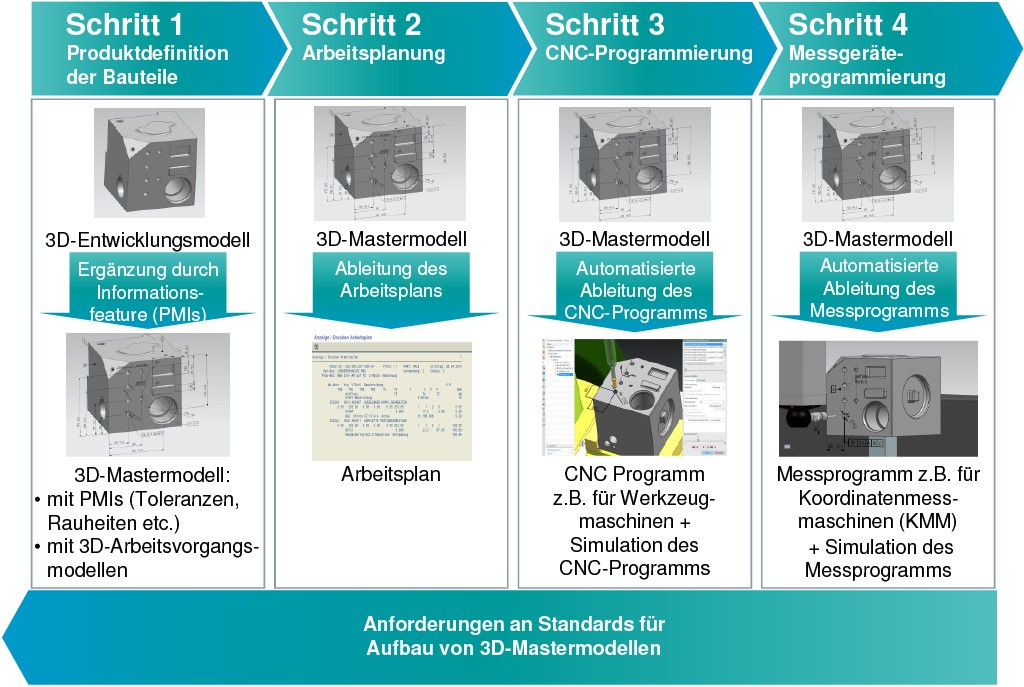
Bild 2. Bausteine der bei Siemens Power and Gas umgesetzten durchgängigen 3D-Modellkette (Darstellung am Beispiel eines Referenzbauteils). Bild: Siemens
Um die Assoziativität automatisiert gewährleisten zu können, sind Standards beim Aufbau des 3D-Mastermodells unerlässlich. Diese werden von den Anforderungen aus den Schritten Arbeitsplanung, CNC- und KMM-Programmierung abgeleitet, sodass das 3D-Mastermodell idealerweise mit vorhandenen oder zumindest standardisierten Werkzeugen hergestellt und das Bauteil anschließend geprüft werden kann. Um die Standards im Konstruktionsprozess für 3D-Mastermodelle zu verankern, werden diese so weit wie möglich aus wiederkehrenden Geometrie- und Informationselementen aufgebaut – den „Features“ [1].
Die bei Siemens Power and Gas umgesetzte durchgängige 3D-Modellkette basiert auf dem 3D-Mastermodell, das vom 3D-Entwicklungsmodell abgeleitet wird. Das 3D-Mastermodell dient als Produktdefinition der Bauteile der Kraftwerkskomponenten und speist darauffolgende Schritte wie die Arbeitsplanung, die CNC-Programmierung und die Messgeräteprogrammierung mit Daten. Fertigungsrelevante Informationen wie Toleranzangaben und Oberflächenrauheiten sind in Form von PMIs (Informationsfeatures [2]) hinterlegt, Bild 3.
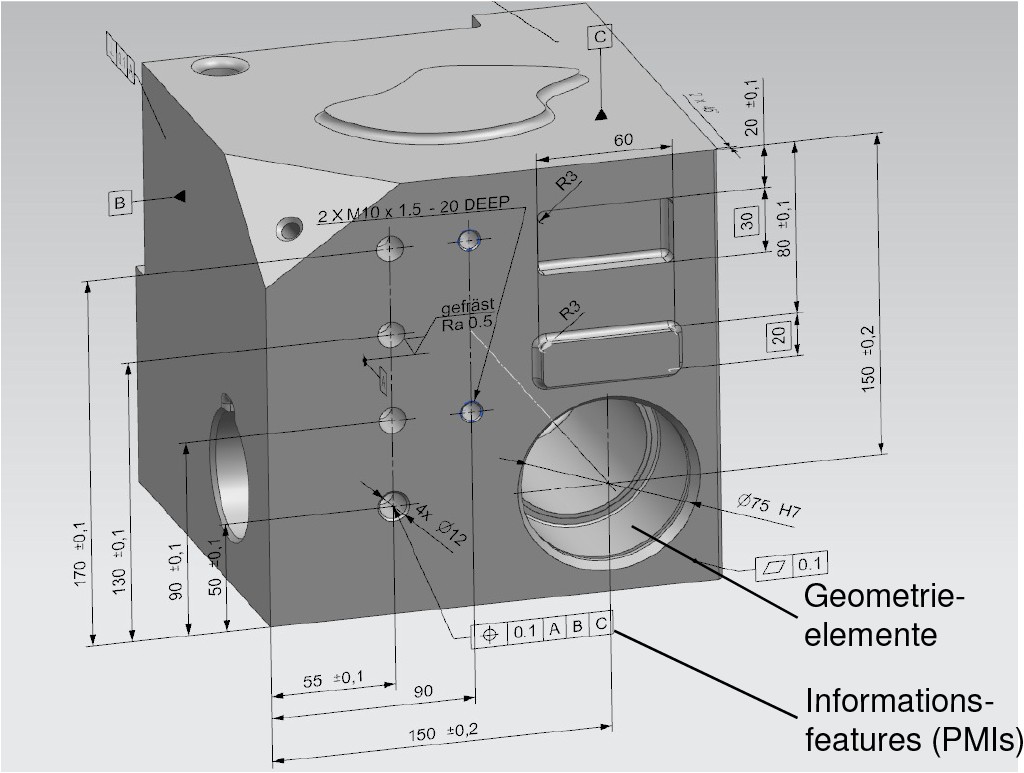
Bild 3. 3D-Mastermodell eines Testbauteils mit fertigungsrelevanten Informationen wie Toleranzangaben und Oberflächenrauheiten in Form von Informationsfeatures (PMIs). Bild: Siemens
Bei Bauteilen, zu deren Fertigstellung verschiedene Bearbeitungsschritte erforderlich sind, wird für jeden Bearbeitungsschritt ein „3D-Arbeitsvorgangsmodell“ als Bestandteil des 3D-Mastermodells aufgebaut. Bei rotationssymmetrischen Stahlbauteilen, die mit Drehprozessen hergestellt werden, findet beispielsweise im ersten Bearbeitungsschritt mit der Weichbearbeitung die Festlegung der Geometrie statt. Im zweiten Bearbeitungsschritt werden mit der Wärmebehandlung die Werkstoffeigenschaften (wie Festigkeit) festgelegt. Im abschließenden Bearbeitungsschritt, der Hartbearbeitung, wird die Bauteilgeometrie in die gewünschten Toleranzbänder überführt.
Für jeden der drei Bearbeitungsschritte wird im 3D-Mastermodell ein eigenes 3D-Arbeitsvorgangsmodell angelegt. Damit setzt die Erstellung des 3D-Mastermodells voraus, dass der Bauteilentwickler – neben den funktionalen Anforderungen – den Herstellungsprozess kennt und danach seine Modellierungsstrategie aufbaut.
Gemäß ISO 16792 [3] besteht die Produktdefinition eines Bauteils aus einem 3D-Mastermodell sowohl in nativem Datenformat als auch in einem Datenaustauschformat, dem in ISO 14306 [4] definierten „Jupiter Tesselation“ (JT)-Format. Während das 3D-Mastermodell in JT-Format der Kommunikation mit externen Partnern und der Archivierung dient, wird für alle betriebsinternen Schritte in der durchgängigen 3D-Modellkette das 3D-Mastermodell in nativer Form herangezogen.
Auf Grundlage des 3D-Mastermodells folgen in den Schritten 2 bis 4 die Arbeitsplanung, die CNC-Programmierung und die Messgeräteprogrammierung. Diese Schritte werden mithilfe der Feature-Erkennung teilautomatisiert durchgeführt, die im Folgenden am Beispiel der CNC-Programmerstellung erläutert wird.
Um ein CNC-Programm auf Grundlage eines 3D-Mastermodells teilautomatisiert zu erstellen, wird folgende Infrastruktur aufgebaut:
- CAM-Feature-Bibliothek: Für definierte Geometrie- und Informationselemente werden im CAM-System Bearbeitungsstrategien wie Bahnplanung, Bearbeitungsparameter und Werkzeugauswahl hinterlegt.
- 3D-Modelle der Fertigungshilfsmittel: Alle für den Fertigungsprozess benötigten Systeme und Hilfsmittel wie die Werkzeugmaschine, Spannvorrichtungen und Werkzeuge werden als 3D-Modell gegebenenfalls mit Kinematik abgebildet.
- Postprozessoren: Ein Postprozessor übersetzt das Ergebnis der CAM-Programmierung maschinentypspezifisch und steuerungsspezifisch in einen maschinenlesbaren CNC-Code.
Zunächst werden die Arbeitsvorgangsmodelle des 3D-Mastermodells, die die Arbeitsschritte der CNC-Bearbeitung abbilden, in die CAM-Umgebung überführt. An den Arbeitsvorgangsmodellen, auf deren Grundlage die CAM-Modelle aufgebaut werden, folgt die Feature-Erkennung. Dabei werden die in der CAM-Feature-Bibliothek definierten geometrischen Strukturen im CAM-Modell identifiziert. Dadurch greift das CAM-System auf das in der Feature-Bibliothek hinterlegte Fertigungswissen zurück und plant Bearbeitungsverfahren, Maschinentyp, Werkzeuge, Bearbeitungswege und -parameter automatisch [5;6], Bild 4.
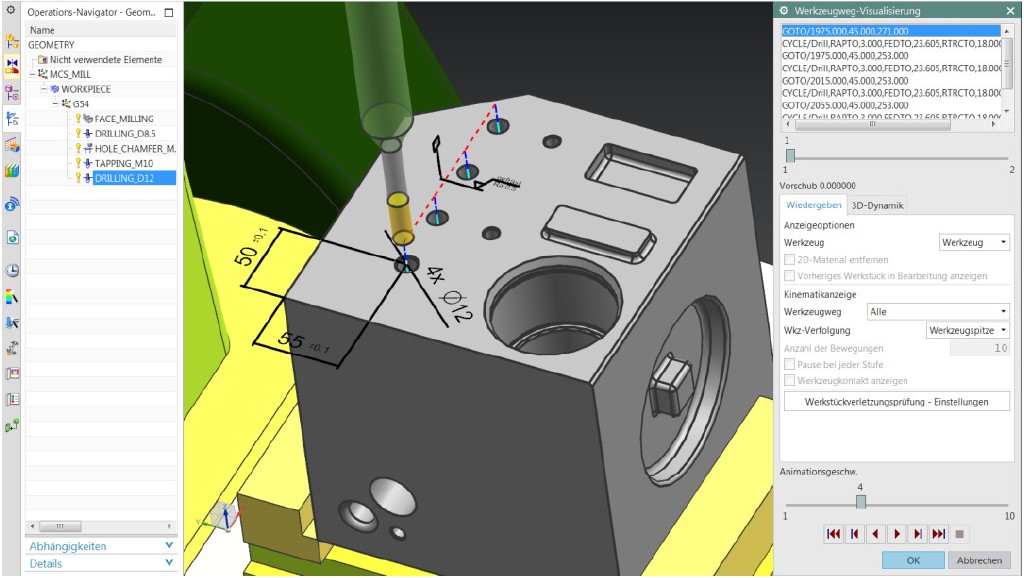
Bild 4. Beispiel für die Planung eines Bearbeitungsvorgangs für ein Feature in der Software „NX CAM“, wobei die im CAM-Modell hinterlegten Geometrie- und Informationselemente wie Informationsfeatures verwendet werden. Bild: Siemens
Nur für die Teile des CAM-Modells, die nicht in der Feature-Bibliothek hinterlegt sind, muss diese Planung manuell geschehen.
Zur Qualitätssicherung des CAM-Modells wird der Prozess der CNC-Bearbeitung simuliert, Bild 5.
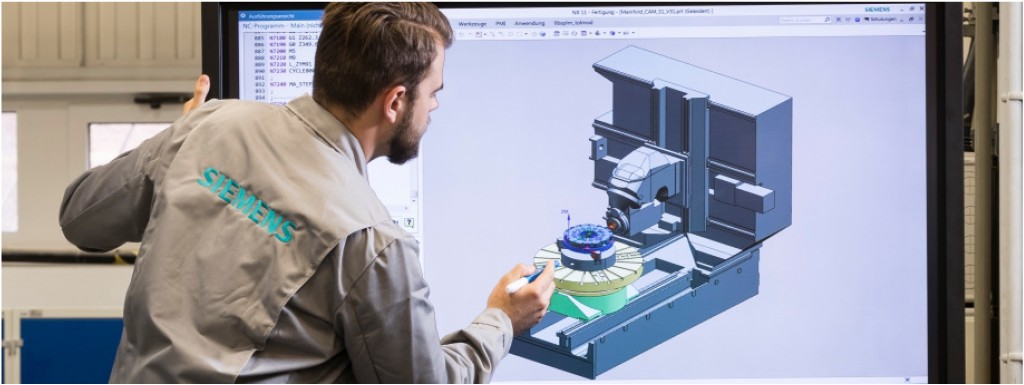
Bild 5. Simulation des CNC-Bearbeitungsprozesses unter Verwendung der virtuellen Abbildung der Fertigungshilfsmittel wie Werkzeugmaschine, Spannmittel und Werkzeuge. Bild: Siemens
Dazu werden die 3D-Modelle um Fertigungshilfsmittel wie Werkzeugmaschine, Spannmittel und Werkzeuge ergänzt. Durch die Simulation des Bearbeitungsprozesses werden bereits Kollisionen bei der Bearbeitung erkannt und können damit vor dem Transfer des Programms auf die Werkzeugmaschine behoben werden.
Abschließend wird das Ergebnis der CAM-Programmierung mithilfe eines Postprozessors in einen durch die Werkzeugmaschine lesbaren CNC-Code übersetzt.
Die Messgeräteprogrammierung entspricht in großen Teilen der CNC-Programmierung. Für Koordinatenmessmaschinen findet sie in einer eigenen Umgebung für Messgeräteprogrammierung in „NX CMM“ statt, Bild 6.
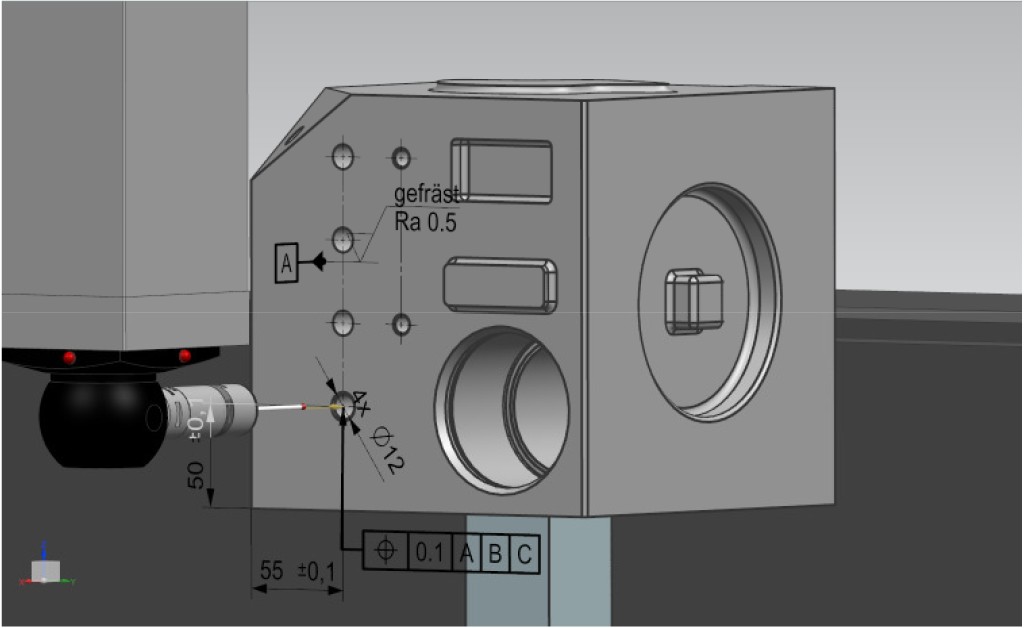
Bild 6. Messgeräteprogrammierung für das Testbauteil mit Verwendung der im 3D-Mastermodell hinterlegten Geometrie- und Informationselemente wie Informationsfeatures (PMIs). Bild: Siemens
Damit stellt bei einer durchgängigen 3D-Modellkette das 3D-Mastermodell alle zur Herstellung und Prüfung eines Bauteils erforderlichen Informationen bereit. Die Methodik zur Entwicklung dieser modellzentrierten Arbeitsweise und die dadurch erzielten Vorteile werden im Folgenden erläutert.
Methodik zur Entwicklung einer durchgängigen 3D-Modellkette
Die Schritte einer durchgängigen 3D-Modellkette (Bild 2) werden im Regelfall nicht durch ein Qualifikationsprofil und eine Organisationseinheit abgedeckt. So findet die Produktdefinition und damit der Aufbau des 3D-Mastermodells in der Entwicklung statt, während die Arbeitsplanung sowie die CNC-Programmierung in der Arbeitsvorbereitung und die Messmittelprogrammierung meist in der Qualitätssicherung erstellt werden.
Um alle Vorteile einer durchgängigen 3D-Modellkette vollständig zu realisieren, ist eine Verknüpfung aller Schritte der 3D-Modellkette erforderlich. Beispielsweise ist für die Entwicklung der Standards für den Aufbau von 3D-Mastermodellen bei der Produktdefinition der Bauteile eine profunde Kenntnis der darauffolgenden Arbeitsschritte erforderlich. Deshalb wurde bei Siemens Power and Gas ein übergeordnetes Projekt zu deren Erarbeitung aufgesetzt. Dem Projekt ist ein iteratives Vorgehen zugrunde gelegt (Bild 2).
Durch jede Iteration werden die Standards für den Aufbau der 3D-Mastermodelle weiterentwickelt – indem Produkt- und Bauteilspektrum erweitert werden, auf die die Standards angewendet werden und dann die Arbeitsplanung, die CNC-Programmierung und die Messgeräteprogrammierung von den 3D-Mastermodelle abgeleitet werden. Dadurch wird die Anwendbarkeit der Standards zum Aufbau der 3D-Mastermodelle für ein wachsendes Teilespektrum validiert und weiterentwickelt.
Außerdem wird mit jeder Iteration die digitale Infrastruktur in der Fertigung – beispielsweise die CAM-Feature-Bibliothek, die 3D-Modelle-Bibliothek der Fertigungshilfsmittel und die Postprozessoren für Werkzeugmaschinen – ausgebaut.
Die erste Iteration geschieht auf Grundlage des eigens für die Entwicklung von Standards konstruierten Testbauteils (Bild 3), eines kubischen Bauteils mit diversen bei Kraftwerkskomponenten häufig verwendeten Features. Dadurch wird die durchgängige 3D-Modellkette für bei Kraftwerkskomponenten häufig verwendeten Features an einem Testbauteil in einem produktiven Umfeld aufgesetzt, ohne den produktiven Betrieb in der Entwicklung, der Arbeitsvorbereitung und der Qualitätssicherung zu beeinträchtigen. In der zweiten Iteration wird die durchgängige 3D-Modellkette für ausgewählte Bauteile von Serienprodukten sowie im Prototypenbau eingesetzt. In der aktuell durchgeführten Iteration setzt Siemens Power and Gas die durchgängige 3D-Modellkette für Bauteile der neuen Gasturbinenbaureihe der HL-Klasse ein.
Vorteile einer 3D-Modellkette und begleitende Schritte
Hauptziel der Nutzung der durchgängigen 3D-Modellkette ist eine Verbesserung des Angebots für die Kunden der Siemens Power and Gas auf dem Energiemarkt. Dabei soll die durchgängige 3D-Modellkette insbesondere zu einer Verkürzung der Lieferzeit bei kundenspezifischen Kraftwerkslösungen und zu einer Produktpalette mit aktuellen technischen Entwicklungen beitragen. Dies soll durch folgende Effekte sowohl in der Serienproduktion als auch im Prototypenbau von Kraftwerkskomponenten erzielt werden:
- Die Assoziativität zwischen der Produktdefinition der Bauteile, dem 3D-Mastermodell sowie der Arbeitsplanung, der CNC- und der Messgeräteprogrammierung erlaubt eine schnelle fehlerarme Umsetzung von Änderungen in der Produktdefinition eines Bauteils (in allen dazugehörigen Arbeitsplänen, Modellen und Programmen). Dies sorgt für die verstärkte Parallelisierung von Prozessen in der Entwicklung und der Arbeitsvorbereitung. Dadurch kann eine Verkürzung des Time-to-Market erzielt werden.
- Die für die durchgängige 3D-Modellkette erforderlichen Standards für das 3D-Mastermodell führen zu einer höheren Standardisierung der Designlösungen.
- Der Anteil der Werkstattprogrammierung wird zugunsten der „Off-line-Programmierung“ reduziert. Dies führt zu einer Zeitoptimierung bei der Arbeitsvorbereitung und einer Steigerung des Nutzungsgrads der Maschinen und Anlagen.
- Durch die Teilautomatisierung der Arbeitsplanung, der CNC-Programmierung und der Messgeräteprogrammierung mithilfe der Feature-Erkennung kann eine Verkürzung des Time-to-Market erzielt werden.
- Die beschriebene Umstellung, bei der alle Informationen für die Produktentstehung durch das 3D-Mastermodell organisiert und bereit gestellt werden, stellt einen Paradigmenwechsel in der Arbeitsweise dar. Damit dies erfolgreich ist, sind zusätzlich zur Einführung einer durchgängigen 3D-Modellkette unter anderem folgende begleitende Maßnahmen erforderlich:
- Das Berufsbild des „Bauteilentwicklers“, des „Arbeitsplaners“, des „CAM-Experten“ und des „Maschinenbedieners“ werden dadurch erheblich weiterentwickelt. Alle diese Arbeitsschritte verlagern sich weg von der textuellen Arbeitsweise hinein in die 3D-modellbasierte Arbeitsweise und damit in den „virtuellen Raum“ (Bild 5).
- Neue Formen der organisationsübergreifenden Zusammenarbeit werden etabliert, um ein vorausschauendes und prozessorientiertes Denken bereits während des Schritts der Produktdefinition der Bauteile weiterzuentwickeln und um die Anforderungen aller Schritte der durchgängigen 3D-Modellkette bei der Erstellung des 3D-Mastermodells zu berücksichtigen.
- Das PLM-System – „Teamcenter“ bei Siemens Power and Gas – wird zu einer integrierten Datenverwaltung für alle im Laufe eines Produktlebenszyklus benötigten und generierten Daten – beispielsweise für Arbeitspläne, Fertigungshilfsmittel und Werkzeuge – weiterentwickelt.
Neben unternehmensinternen Maßnahmen zur Transformation von einer 2D-zeichnungsbasierten Arbeitsweise zu einer 3D-modellbasierten Arbeitsweise sind für Siemens Power and Gas die Entwicklung und Definition der Schnittstellen zu externen Partnern und Zulieferern entscheidend dafür, die Potentiale der digitalen Revolution mithilfe einer durchgängigen 3D-Modellkette nutzen zu können.
www.siemens.com/ingenuityforlife
Literatur:
[1] Richtlinie VDI 2218: Informationsverarbeitung in der Produktentwicklung – Feature-Technologie. Düsseldorf: VDI-Gesellschaft Entwicklung Konstruktion Vertrieb (VDI-EKV), März 2013.[2] Robl, P.: Integratives NC-Modell für die Vereinfachung der werksübergreifenden Produktion auf der Basis einer Feature-Skelett-Methode. Grafenau: Morsak-Verlag, 2013. [3] International Organization for Standardization (ISO): Technical Product documentation – Digital product definition data practices. ISO 16792; ISO-Norm, 2015. [4] International Organization for Standardization (ISO): Industrial automation systems and integration – JT file format specification for 3D-visualization. ISO 14306; ISO-Norm, 2012.[5] Humpa, M.; Köhler, P.; Hrsg.: Brökel, K. Feldhusen, J.; Grote K.-H.; Rieg, F.; Stelzer R.: Effizienzsteigerung des Produktentwicklungsprozesses durch fertigungsgerechte CAD-Methoden. In: 12. Gemeinsames Kolloquium Konstruktionstechnik 2014 – Methoden in der Produktentwicklung: Kopplung von Strategien und Werkzeugen im Produktentwicklungsprozess. 12. Gemeinsames Kolloquium Konstruktionstechnik, Bayreuth, 16./17. Oktober 2014, Tagungsband, S. 263–273.[6] Feldhusen, J.; Grote, K.-H. (Hrsg.: Pahl/Beitz): Konstruktionslehre – Methoden und Anwendung erfolgreicher Produktentwicklung. Berlin: Springer-Vieweg-Verlag, 2013.
Dr.-Ing. Sebastian Neubert ist Abteilungsleiter Engineering Standards bei der Siemens AG Division Power and Gas. // Dr.-Ing. Peter Robl ist Abteilungsleiter Digital Manufacturing Technologies bei der Siemens AG Corporate Technologies.