Produktion und Logistik perfekt synchronisiert
In die Erweiterung ihres Waldkraiburger Werks investiert die Süddeutsche Gelenkscheibenfabrik insgesamt rund 30 Mio Euro. Im Bereich der Intralogistik standen u.a. ein vollautomatisches Hochregallager sowie ein innovatives Routenzugsystem mit automatischer Be- und Entladung auf der Agenda. Als Generalunternehmer verantwortet der SAP EWM Generalunternehmer IGZ aus Falkenberg die Umsetzung dieser durchgängig in SAP EWM integrierten Gesamtsystemlösung.
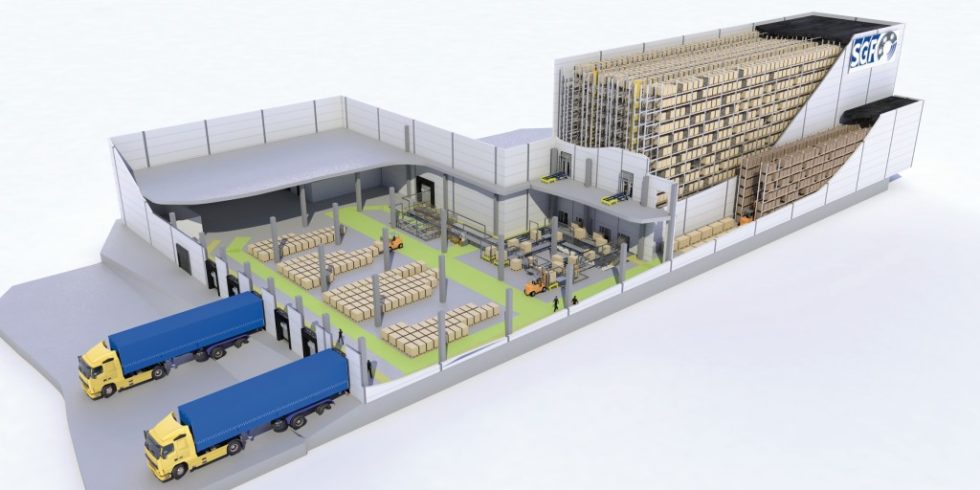
Die Süddeutsche Gelenkscheibenfabrik (SGF) wird die bestehenden Werke in Kraiburg und Waldkraiburg zusammenführen und Produktion und Logistik noch enger verzahnen. In Waldkraiburg entsteht im Rahmen der Umstrukturierungen ein neues Logistikzentrum. Bild: IGZ
Im Verlauf ihres bald 70-jährigen Bestehens hat sich die heutige Süddeutsche Gelenkscheibenfabrik GmbH & Co. KG (SGF) zum Marktführer im Bereich der Drehmomentübertragung entwickelt. Das Portfolio des mit Hauptsitz im oberbayerischen Waldkraiburg ansässigen Familienunternehmens umfasst Gelenkscheiben in Kardanwellen und Lenksäulen, Schwingungsdämpfer in Antriebssträngen, Auspuffaufhängungen und -tilger sowie diverse Gummi-Metallteile für die Lagerung unterschiedlicher Aggregate. Abnehmer der konsequent unter dem Gütesiegel „Made in Germany“ angefertigten Produkte sind in erster Linie die Automobilindustrie sowie Maschinen- und Anlagenbauer.
Neustrukturierung als zukunftssichere Lösung
Mit dem symbolischen ersten Spatenstich fiel im März 2015 der Startschuss für die Umsetzung des intralogistischen „Neubauprojekts SGF 2020“. Der bislang größten Investition in der Firmengeschichte war die strategische Entscheidung vorausgegangen, die bestehenden Werke in Kraiburg und Waldkraiburg zusammenzuführen, die Produktionskapazitäten massiv auszubauen und diese mit der Logistik noch enger zu verzahnen. Darüber hinaus sollten Arbeitsbedingungen geschaffen werden, die die Altersstruktur der Mitarbeiter angemessen berücksichtigen.
Auf dem weitläufigen Werksgelände in Waldkraiburg waren der Gestaltung nahezu keine Grenzen gesetzt. In einem ersten Schritt sind nun in direkter Anbindung an den vorhandenen Hallenkomplex neue Produktionsflächen auf rund 8 300 m² geschaffen und daran unmittelbar angrenzend ein 24 m hohes vollautomatisches Hochregallager errichtet worden. „Die Entscheidung für ein vollautomatisch betriebenes Hochregallager wurde durch eine Wirtschaftlichkeitsbetrachtung unterschiedlicher Lagersysteme herbeigeführt“, erklärt Gerald Seidinger, Leiter Logistik und stellvertretender Werksleiter der SGF . „Das bisher eingesetzte 7,5 m hohe und konventionell per Stapler bediente Lager war einer 2-gassigen automatischen Systemlösung mit rund 5 800 Palettenstellplätzen bei doppelttiefer Lagerung weit unterlegen.“ Ergänzt werden sollte die neue Automatikanlage durch eine angegliederte Gasse mit ca. 600 Stellplätzen für nicht genormte Gebinde unterschiedlicher Größen, die dort mit Staplerunterstützung ein- und ausgelagert werden. Zu errichten war ferner ein separates Gefahrstofflager.
Gerald Seidinger und sein Team waren zudem aufgefordert, die aus dem Prinzip der Werkstattfertigung resultierenden hohen Umlaufbestände zu eliminieren. Um den „Teiletourismus“ und die Belegung teurer Produktionsfläche mit nicht unmittelbar benötigtem Material zu unterbinden, sollte eine ebenfalls SAP EWM-gestützte Routenplanung mit automatischer Routenzugbe- und -entladung implementiert werden, die Stapler im direkten Produktionsumfeld letztlich gänzlich überflüssig macht.
Ganzheitliche Kompetenz gefordert
Die Suche nach einem Generalunternehmer für die Umsetzung der in SAP zu integrierenden Gesamtsystemlösung gestaltete sich zunächst aufwendiger als gedacht. „Wir mussten bald feststellen, dass nicht jeder Generalunternehmer für die Lagerlogistik auch SAP EWM kann. Und nicht alle, die SAP können, haben eigenes Know-how, sondern kaufen dieses von Drittanbietern zu. Das wollten wir nicht, es musste ein Ansprechpartner für alles sein“, betont der SGF-Logistikleiter. Darüber hinaus war das Konzept einer automatischen Routenzugbeladung mit einer Zykluszeit von weniger als drei Minuten zu realisieren. Fehlendes bzw. nicht hinreichendes Know-how diese Idee umzusetzen, sei ein weiteres Ausschlusskriterium gewesen.
In diesem Kontext überzeugte das Preis-/Leistungsverhältnis des SAP EWM Generalunternehmers IGZ. Die „SAP-Ingenieure“ aus dem oberpfälzischen Falkenberg bieten über die SAP-Beratung und -Implementierung hinaus auch Generalunternehmer-Leistungen im Bereich der Anlagen- und Steuerungstechnik für Neubauläger, Erweiterungen und Retrofits an. Diese ganzheitlichen Lösungen basieren ausschließlich auf SAP EWM (Extended Warehouse Management) mit direkter SPS-Anbindung mittels SAP EWM/MFS (Material Flow System). „Als Generalunternehmer bieten wir unseren Kunden von der Software bis zur Mechanik alles aus einer Hand und sorgen dafür, dass die mit einer höheren SAP-Integration verbunden Ziele hinsichtlich Effizienz, Stabilität, Transparenz und Qualität auch tatsächlich erreicht werden“, sagt Johann Zrenner, neben Wolfgang Gropengießer Geschäftsführer von IGZ.
Hochregallager mit Energiesparfaktor
Gesagt, getan. Entstanden ist ein 2-gassiges, vollautomatisch betriebenes Hochregallager (HRL) mit rund 5 800 Palettenstellplätzen bei doppelttiefer Lagerung. Diese werden von zwei Regalbediengeräten ver- und entsorgt, die je mit zwei Lastaufnahmemitteln bestückt sind und den definierten Anforderungen nach maximal möglicher Energieeffizienz gerecht werden. Von der 24 m hohen Anlage verbleiben sichtbare 21,5 m. Grund ist, dass das HRL rund 2,8 m tief in das Erdreich abgesenkt wurde, um eine natürliche Kühlung für temperaturempfindliche Rohstoffe und Produkte herbeizuführen. Auch diese Lösung spart Energie, senkt Betriebskosten und ist nicht zuletzt unter Umweltschutzaspekten sinnvoll.
Die neue Intralogistik bei SGF in Waldkraiburg ist so ausgelegt, dass zukünftig über sieben Ladebrücken täglich bis zu 100 Lkw abgefertigt werden können. Auf Paletten angelieferte Waren werden per Gabelstapler entladen und auf die Fördertechnik in der Vorzone des HRL aufgegeben, wo sie die automatische Gewichts- und Konturenkontrolle durchlaufen. Durch die Gewichtsermittlung und die in SAP hinterlegten Stückgewichte ist sichergestellt, dass auch die Menge korrekt erfasst wird. Die Einlagerung der Paletten folgt definierten SAP EWM-Lagerstrategien, so dass für jeden Ladungsträger – in Abhängigkeit von den enthaltenen Artikeln – der jeweils optimale Lagerplatz ausgewählt wird. Die Auslagerung von Fertigwaren erfolgt nach FIFO (first in – first out).
Vollautomatische Routenzugbe- und -entladung
„Clou der durchgängig aus SAP heraus gesteuerten Gesamtsystemlösung ist die in EWM integrierte Routenzuglösung, über die eine getaktete, fertigungssynchrone Materialver- und -entsorgung sichergestellt ist “, sagt IGZ-GU-Projektleiter Georg Witt. Das sieht auch Gerald Seidinger so: „IGZ ist es gelungen, die Idee unserer Mitarbeiter von einer Routenzugplanung mit vollautomatischen Be- und Entladung in die Realität zu überführen. Damit hat das Unternehmen auch unsere Forderung nach einer Zykluszeit der Be- und Entladung von unter drei Minuten bedient. Diese fußt auf der Überzeugung, dass ein Routenzug erst bei Einhaltung eines solch minimalen Zeitfensters wirtschaftlich betrieben werden kann.“ Benötigte Waren und Behälter fordern die Mitarbeiter in der Produktion nun über bereits vorhandenen BDE-Terminals an. Parallel wird der Rücktransport von Fertigprodukten sowie nicht mehr benötigte Roh- und Halbfertigwaren angemeldet. Diese Meldungen werden im SAP EWM-Dialog verarbeitet, so dass in Folge ein entsprechender Auslagerauftrag aus dem HRL generiert wird. Die Materialien durchlaufen die verbindende Fördertechnik und werden über Eckumsetzer an den Übergabestationen des Routenzug-Bahnhofs bereitgestellt. Dort nehmen vier im Boden abgesenkte Teleskopgabeln die aus der Produktion zurückgeführte Ware vom Routenzug und legen diese auf der Förderstrecke ab. Direkt im Anschluss können dann die für die Produktion benötigten Teile ebenfalls automatisch abgenommen und auf den Routenzug geladen werden.
„Somit werden Umlaufbestände auf ein Minimum bzw. auf das reduziert, was tatsächlich für die unmittelbare Bearbeitung erforderlich ist“, unterstreicht Gerald Seidinger. Zudem werde die Produktion staplerfrei betrieben. „Es kreisen nur noch Routenzüge und Arbeitsmittel der Instandhaltung für Rüst- und Reparaturzwecke.“ Eine hohe Spurtreue ist über einen mittig am Zugfahrzeug der Gespanne angebrachten Laserpointer sichergestellt. Pro Schicht sind zwei Routenzüge mit jeweils vier Wagen im Einsatz, die in Summe täglich etwa 56 km zurücklegen. Hochgerechnet auf ein Jahr entspricht dies einer Wegstrecke von rund 14 100 km.
Anlagenvisualisierung auch über mobile Endgeräte
Um die geforderte Verfügbarkeit und einen sicheren Betrieb des bei der SGF installierten Gesamtsystems kontinuierlich aufrecht zu erhalten, setzt der Mittelständler auch auf WinCC. Hierbei handelt es sich um eine von der IGZ weiterentwickelte portable Variante der Anlagenvisualisierung für Tablets & Co. Der Detaillierungsgrad reicht bis auf Sensor- und Aktorebene und ermöglicht somit eine frühzeitige Problemerkennung und -behebung. Auch SAP-Informationen, wie z.B. Paletten- oder Auftragsdaten, können online zu transportierten Ladeeinheiten eingeblendet werden. Über eine touchscreenfähige Menüführung lassen sich die Tablets ganz einfach und nahezu intuitiv bedienen. Das kommt auch älteren Mitarbeitern entgegen, also einer Generation, die nicht wie selbstverständlich mit Computern, Internet, Smartphones und Social Media aufgewachsen ist.
SAP EWM-unterstützt zur schlanken Produktion
In die Entwicklung der umgesetzten Automatisierungslösung auf Basis von SAP EWM / MFS haben die Projektverantwortlichen der SGF die eigenen Mitarbeiter früh einbezogen. Erstes Ergebnis des konstruktiven Miteinanders waren konkrete Handlungsempfehlungen auf Basis einer detaillierten Analyse der Produktions- und Logistikprozesse, die auf baulicher sowie auf Ebene der Mechanik nun sichtbar Gestalt angenommen haben. Darüber hinaus sollten sämtliche Funktionen in SAP integriert und vernetzt werden.
„Auch hier hat sich der Kooperationsgedanke bewährt“, sagt Logistik-Chef Gerald Seidinger. Neben den Experten von IGZ sind auch die Spezialisten von SGF zu erwähnen, die die SAP-Datenfunkoberfläche mit designed haben. Zufrieden zeigt er sich auch mit dem Engagement des IGZ-Teams unter der Leitung von GU-Projektleiter Georg Witt und betont die stets offene und faire Kommunikation durch das „tolle Team“. Natürlich sei die Umsetzung derart anspruchsvoller Projekte niemals diskussionsbefreit. Aber man habe stets schnellstmöglich Lösungen gefunden, die den Projektzielen von SGF entsprachen.
Auf das gemeinsam mit der IGZ als verantwortlichem Generalunternehmer Erreichte ist Gerald Seidinger stolz. Zugleich verweist er auf den Stellenwert der implementierten Lösung für die weiteren Geschicke der Süddeutschen Gelenkscheibenfabrik. „Das neue Hochregallager ist zusammen mit den Fördertechniken und SAP EWM Herz und Motor unseres neuen Werkes. Die zum Einsatz kommenden Routenzüge hingegen sind die Adern – durch ein innovatives und neuartiges automatische Beladesystem wesentlich unterstützt und in ihrer Wirtschaftlichkeit gesteigert.“ Mit dem Erweiterungsbau habe man nun die Voraussetzungen geschaffen, auch zukünftig überzeugende Produkte entwickeln und neue Märkte erschließen zu können. Die optional noch zur Verfügung stehende Fläche am Standort Waldkraiburg lässt zukünftig erforderliche Weiterentwicklungen jederzeit zu. Fix vereinbart ist schon jetzt die Errichtung eines automatischen Langgutlagers für die Lagerung von über sechs Meter langen Rohrbündeln. Auch hier liefert IGZ als Generalunternehmer die komplette Anlagentechnik inkl. Steuerungstechnik und verantwortet deren Integration in die bestehende SAP EWM/MFS-Landschaft der SGF. Der Go-Live ist für Januar 2016 geplant.