„Lean“ trifft auf „Industrie 4.0“
Viele Unternehmen beschäftigen sich seit Jahren mit dem Thema „Lean“. Dabei wurden bei konsequenter Umsetzung enorme Verbesserungen in Qualität, Durchlaufzeit, Mitarbeiter- und Flächenproduktivität erreicht. Nun prasselt auf die Unternehmen die Industrie 4.0 Botschaft ein: Eine vollständige informationstechnische Durchdringung der Produktion ist notwendig, um Transparenz in der Steuerung zu bekommen.
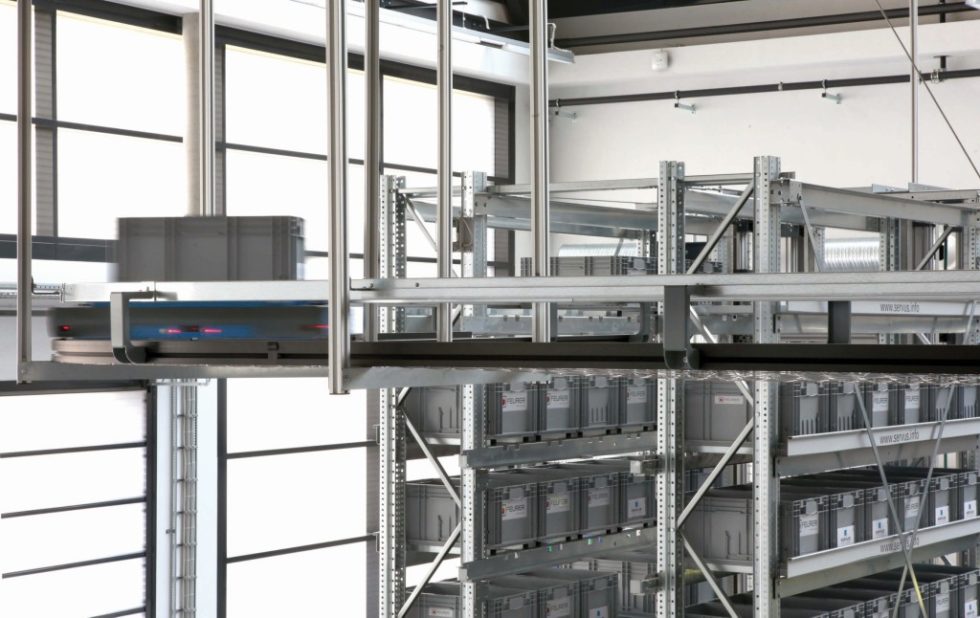
ntelligente Produktions‧logistik: Autonome Transportroboter mit kleinen Behältern und geringen Inhaltsmengen verwirklichen das Prinzip Fluss. Bild: Prof. Dr. Markus Schneider
Die Unternehmen befinden sich jetzt in einem Handlungsdilemma. Denn die Anforderungen der Lean Philosophie und von Industrie 4.0 erzeugen zunächst eine Reihe von Zielkonflikten. Es ist in der Praxis zu beobachten, dass viele Unternehmen, die bei der Lean Einführung bereits sehr weit waren, nun eine „Rolle rückwärts“ vollziehen. Komplett EDV-frei gesteuerte, minimale Shopfloorbestände, werden plötzlich wieder mit enormem Mehraufwand gescannt, nur damit die Daten in einem EDV-System vorhanden sind. Es wird wieder „auf-Teufel-komm-raus“ automatisiert. Dieser Fehler, den viele bereits aus Erfahrungen der Vergangenheit erkannt haben, wird nun unter dem Vorzeichen Industrie 4.0 wiederholt. Eine mögliche Lösung dieser Zielkonflikte könnte der Ansatz „Lean vor Industrie 4.0“ sein. Zunächst sollten alle Prozesse und Strukturen eines Unternehmens der Lean Philosophie entsprechend optimiert und erst im einem Folgeschritt ermittelt werden, welche Industrie 4.0-Technologien diesen Ansatz sinnvoll unterstützen können.
Acht systemische Grundprinzipien
Bei der Überprüfung kommen die acht systemischen Grundprinzipien von Lean – Fluss, Takt, Standard, Pull, Integration, Synchronisation, Perfektion und Robustheit – zur Anwendung. Um diese zu verdeutlichen, soll auf eine Analogie zurückgegriffen werden. Stellen wir uns die zu vergleichenden Produktionssysteme Lean Production und die klassische Massenproduktion als zwei Skigebiete vor.
Beide Skigebiete haben die gleiche Kapazität. Es sollen 1 000 Personen pro Stunde nach oben transportiert werden können. Das eine Skigebiet verfügt über eine Seilbahn mit einer 100-Personen-Gondel, die alle 6 min fährt, das andere über einen 8er-Sessellift mit einer 30-Sekunden-Frequenz. Für welches Skigebiet entscheiden Sie sich? Vermutlich für jenes mit dem 8er-Sessellift, also für das Prinzip Fluss. Denn zum einen hat man dabei das Gefühl, dass es schneller vorangeht. Zum anderen kommen oben im Skigebiet kontinuierlich alle 30 s 8 Personen an, die sich recht schnell auf der Piste verteilen.
Material im Fluss halten
Bei der 100-Personen-Gondel kann es jedoch passieren, dass man 6 min in der Kabine warten muss, bis man losfährt, oder es geht gleich los, wenn man zufällig als einer der letzten einsteigt. Ein weiteres Problem ist, dass dann oben auf der Piste 100 Personen gleichzeitig aussteigen und es wesentlich länger dauert, bis sich alle auf die Piste verteilt haben. Auf die Gestaltung von Unternehmen übertragen bedeutet Fluss u. a. eine möglichst geringe Transportlosgröße und kleine Behälter mit geringen Inhaltsmengen, die häufig transportiert werden, um das Material im Fluss zu halten. Interessanterweise führt uns eine kostenorientierte Betrachtungsweise eher zur Entscheidung für die 100er-Gondel, also die seltenere Fahrt, die die Kosten auf mehr transportierte Objekte verteilt.
Kommen wir zur Abfahrt – auf Unternehmen übersetzt zur Produktion. Unser Skifahrer hätte am liebsten die gesamte Piste für sich allein, sodass er ohne Unterbrechung bis ins Tal hinabfahren könnte. Da es eher unwahrscheinlich ist, dass dieser Fall eintritt, wird ein weiteres Grundprinzip angewendet, nämlich der Takt. Wir lassen die Skifahrer mithilfe einer Ampel im Abstand von 50 m starten und hintereinander herfahren (Bild 2).
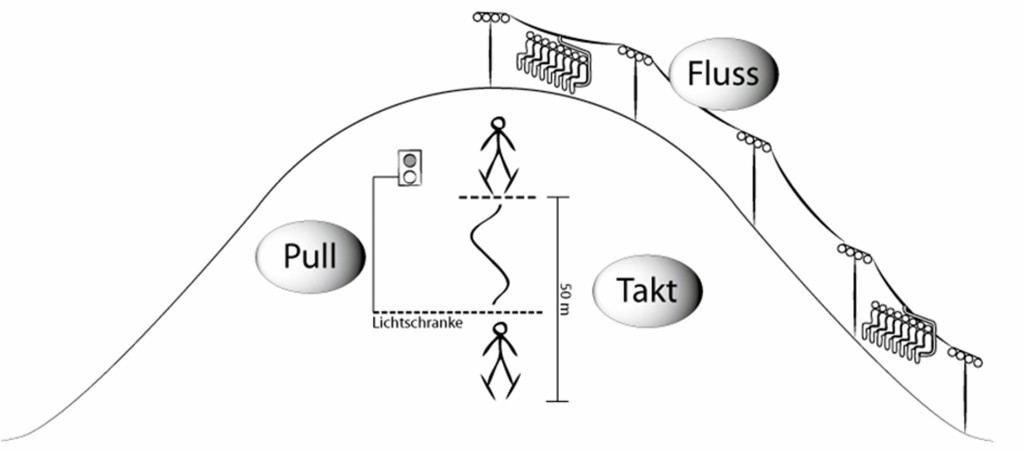
Bild 2 Grundprinzip Takt: Im Vergleichsmodell starten die Skifahrer mithilfe einer Ampel im Abstand von 50 m und fahren hintereinander her. Bild: Prof. Dr. Markus Schneider
So hat jeder von ihnen das Gefühl, die Piste komplett für sich allein zu haben. Gleiches gilt für die Produkte in einer getakteten Linie. Jedes Produkt wird ohne Unterbrechung fertig bearbeitet und hat für sich die kürzestmögliche Durchlaufzeit.
Damit dies funktioniert, müssen die Skifahrer allerdings ungefähr gleich schnell fahren. Dieses Prinzip wird als Standard bezeichnet. Ihrem Können entsprechend werden den Skifahrern unterschiedliche Pisten des Skigebietes zugewiesen, jeweils für Anfänger, Fortgeschrittene und eventuell für Snowboarder. Im Unternehmen bedeutet dies, eine Produkt- und Produktionssegmentierung und darauf basierend eine Ressourcentrennung durchzuführen. Jede Produktgruppe sollte eigene Ressourcen nutzen, um ein einfach zu steuerndes System mit kurzen Durchlaufzeiten zu bekommen.
Pull-Prinzip bei Störungen
Was passiert bei Störungen im System? Hierfür wird das Prinzip Pull genutzt. In der Skigebiet-Analogie kann man sich den Pull-Mechanismus wie eine Lichtschranke vorstellen, die mit der Ampel zur Taktung verbunden wird. Der nächste Takt kann nur ausgelöst werden, wenn die Lichtschranke meldet, dass der vorherige Fahrer die Piste passiert hat und diese frei ist. Im Unternehmen wird dies als Jidoka, die „Kultur des Anhaltens“ bezeichnet. Treten Störungen auf, muss das System so lange angehalten werden, bis die Fehlerursache behoben ist. Damit wird zum einen die Produktion von Ausschuss und zum anderen der Aufbau von Bestand verhindert. Bestand verlängert die Durchlaufzeit und macht Systeme unsteuerbar.
Lean Prinzip Integration
In einem gut integrierten Skigebiet liegen die Einstiege für die weiteren Lifte immer unterhalb des Ausstiegs des unteren Liftes, damit die Skifahrer ohne Kraftanstrengung und schnell zum nächsten Lift gelangen können. Im Unternehmen bedeutet dieses Lean Grundprinzip Integration u. a. kurze Wege, materialflussorientierte Strukturen und eine weitgehende Vermeidung bzw. gute Gestaltung von Schnittstellen.
Zurück zur Piste: Wenn von unten ein moderner 8er-Skilift viele Skifahrer nach oben bringen kann, wird es zu Stauungen kommen, wenn oben nur eine langsame 2er-Sesselbahn den Weitertransport übernimmt. Hier sollte ein weiteres Prinzip, die Synchronisation, angewendet werden. Umgemünzt auf Unternehmen heißt es v. a. aufeinander abgestimmte Ressourcen, Kapazitäten und Schichtmodelle (z. B. ähnliche Geschwindigkeiten aufeinanderfolgender Maschinen, gleiche Schichtmodelle über aufeinanderfolgende Produktionsbereiche usw.) Nicht synchronisierte Abläufe führen immer zu Stauungen und Beständen.
Achtes Grundprinzip Robustheit
Das siebte Systemische Grundprinzip ist die Perfektion, die im Kern die „sofortige Fehlerbehebung am Ort der Entstehung“ bedeutet. Es darf kein fehlerbehaftetes (Teil-)Produkt an den nächsten Schritt weitergegeben werden. Nur so wird ein Feedback und ein Lernen innerhalb der Organisation erreicht. Sind alle diese Prinzipien erfüllt, erreicht man das achte Grundprinzip Robustheit. In einer Welt, die immer schwieriger vorhersagbar wird, ist die Gestaltung weniger anfälliger Systeme, die nicht auf Volatilität reagieren, besonders wichtig. Für ein robustes System spielen Unordnung und Schwankungen keine Rolle. Dies gilt sowohl für das Skigebiet als auch für Unternehmen.
Erweiterung um Industrie 4.0 Technologien
Beginnen wir mit der flächendeckenden Ausstattung unserer Produktion mit Sensorik. In der Skigebiet-Analogie bedeutet dies beispielsweise, alle Pisten und auch angrenzende Hänge mit Sensoren zu versehen, die die Schneehöhe und -beschaffenheit, Temperatur etc. überwachen (Bild 3).
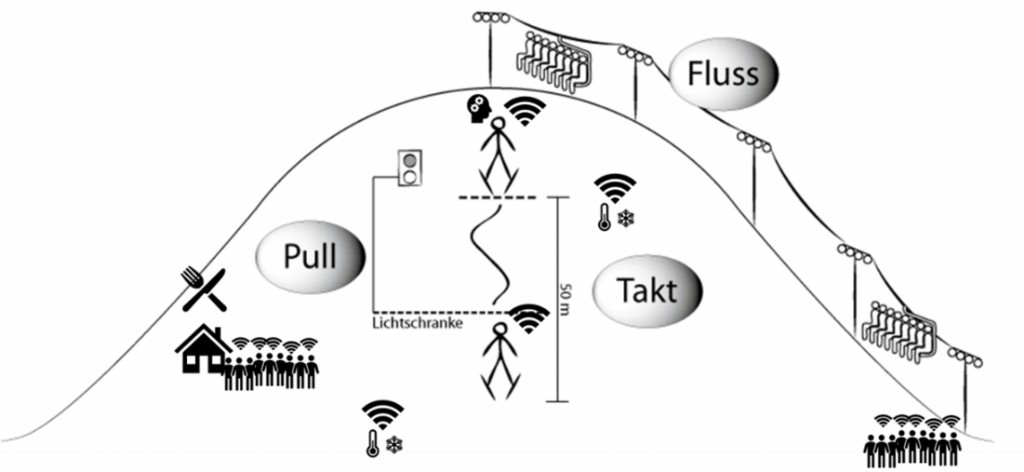
Bild 3 Ausstattung der Produktion mit Sensorik: In der Skigebiet-Analogie bedeutet dies beispielsweise, alle Pisten und auch angrenzende Hänge mit Sensoren zu versehen, die die Schneehöhe und -beschaffenheit, Temperatur etc. überwachen. Damit könnten einerseits den Skifahrern Informationen über den Zustand der Pisten übermittelt werden, aber auch Pistenraupen und Beschneiungsanlagen könnte man vorausschauender und gezielt steuern. Bild: Prof. Dr. Markus Schneider
Damit könnten einerseits den Skifahrern Informationen über den Zustand der Pisten übermittelt werden, aber auch Pistenraupen und Beschneiungsanlagen könnte man vorausschauender und gezielt steuern. Diese Informationen würden hauptsächlich helfen, Verschwendung zu vermeiden – beispielsweise durch schlechte Pisten verursachte Wartezeit oder Überproduktion von künstlichem Schnee am falschen Ort. Zudem könnten die erhobenen Daten für die Bewertung der Lawinengefahr oder für die Notwendigkeit für Pistensperrungen nützlich sein.
Kundenauftrag erhält Optimierungsspielraum
In Bezug auf den Produktionsprozess bedeutet dies, dass Bestände besser überwacht und gezielt hochgefahren sowie Personal- und Maschinenkapazitäten früher und genauer geplant werden könnten. Auch die Skifahrer, also die Kundenaufträge, könnten in einem weiteren Schritt mit Sensoren ausgestattet werden. So wäre jederzeit bekannt, wo sich die Skifahrer befinden und wie schnell sie sich gerade bewegen. Hieraus ließen sich interessante Schlüsse aufgrund von Bewegungsmustern ziehen und für die kurzfristige Steuerung nutzen. Bekäme der Skifahrer beispielsweise aktuelle Infos über Stauungen bei bestimmten Liften oder auf den Hütten in seine Skibrille eingeblendet, so könnte er seine Route entsprechend anpassen, um Wartezeiten zu vermeiden. Auf eine reale Produktion übertragen wird häufig davon gesprochen, dass „sich das Produkt selbst den Weg durch die Produktion sucht“. Dieses Bild führt vielleicht etwas zu weit. Vielmehr geht es darum, dem Kundenauftrag auf dem Weg durch die Produktion dezentral auf Basis von vorgegebenen Randbedingungen einen gewissen Optimierungsspielraum zu geben. Sollten mehrere Ressourcen, z. B. Maschinen, zur Verfügung stehen, die nicht in einen Fluss integrierbar sind, dann könnte sich der Kundenauftrag an der Ressource mit der geringsten Wartezeit einreihen. Zu begrüßen und richtig ist aus Lean-Sicht jedenfalls die Tendenz, den Kundenauftrag als wichtigstes Optimierungskriterium für den Produktionsdurchlauf zu sehen und nicht mehr die Auslastung einzelner Ressourcen. Diese sind nur noch das Resultat und werden (außer am Engpass) nicht mehr aktiv geplant. Dies entspricht absolut der Lean Philosophie.
Prof. Dr. Markus Schneider - Professor für Logistik, Material- und Fertigungswirtschaft an der Hochschule Landshut sowie Gründer und Geschäftsführer der PuLL Beratung GmbH