Die Automobilindustrie als Vorbild
Wie können Komponentenhersteller und Zulieferer für den Maschinen- und Automobilbau ihre innerbetrieblichen Logistikprozesse verbessern? Die moderne Automobilproduktion zeigt die Richtung - allerdings muss man deren Prinzipien an die spezifischen Bedingungen der Taktfertigung bei schwankenden Stückzahlen anpassen. Unternehmen, die diese Maßnahmen umsetzten, profitieren von geringeren Beständen, kürzeren Durchlaufzeiten und einem stabileren Materialfluss.
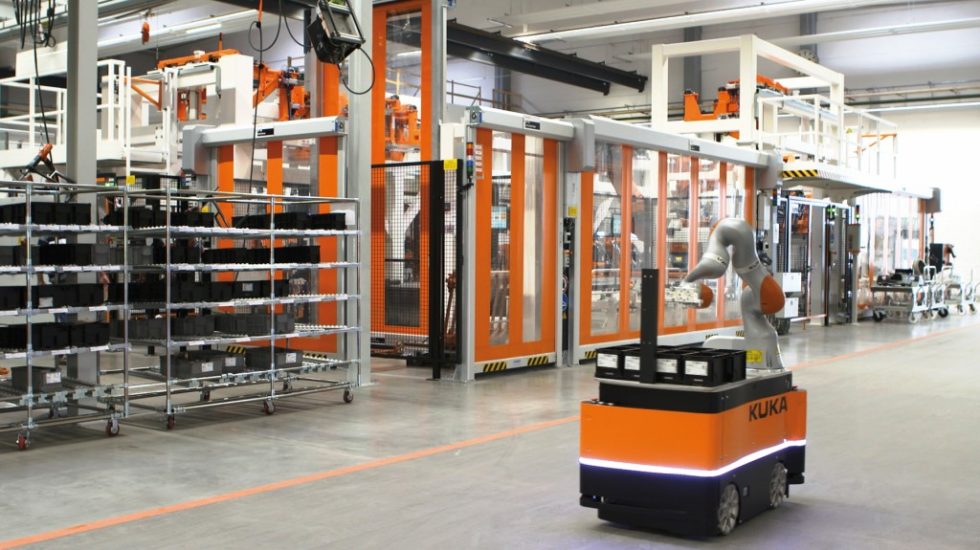
In Zukunft wird auch in der Komponentenfertigung vermehrt nach dem „Ware zum Mann“-Prinzip kommissioniert – zum Beispiel mit Kommissionier- und Transportrobotern. Bild: Kuka Roboter GmbH
Die Automobilindustrie ist nach wie vor Vorreiter bei der Implementierung schlanker und effizienter Prozesse in der Produktionslogistik. Bestandsreichweiten von weniger als einer Tagesproduktion sind gängiger Standard. Voraussetzung für derart geringe Bestände ist die Umsetzung der Maßnahmen, die in Bild 1 dargestellt sind.

Bild 1 Die Automobilproduktion nutzt einen „Werkzeugkasten“ von fünf Maßnahmen zur Optimierung der Intralogistik. Bild: Porsche Consulting
Herausforderungen für die Komponentenhersteller
Die Produzenten von Komponenten für den Automobilbau, aber auch für den Maschinen- und Anlagenbau stehen unter ebenso großem Wettbewerbsdruck wie die Automobilhersteller. Anbieter aus Niedriglohnländern wie China drängen in den hart umkämpften Markt. Zugleich befinden sie sich immer häufiger in einem Zielkonflikt, der sich aus einer steigenden Anzahl von Produktvarianten auf der einen und dem Wunsch der Kunden nach kürzeren Lieferzeiten auf der anderen Seite ergibt.
Untergangsszenarien sind angesichts dieser Entwicklung sicherlich fehl am Platze, denn die Mehrheit der deutschen Zulieferer und Komponentenhersteller ist nach wie vor sehr gut aufgestellt. Insgesamt besitzt die Logistik bei vielen Komponentenherstellern noch nicht den Stellenwert, den sie aufgrund ihres Effizienzpotenzials verdient. Um in Deutschland weiterhin wettbewerbsfähig zu sein, ist es notwendig, dieses Potenzial auszuschöpfen. Hierzu gibt es diverse Möglichkeiten, und es ist sinnvoll, den „Werkzeugkasten“ zu verwenden, den die Automobilindustrie in solchen Fällen nutzt.
Von der Automobil-produktion lernen
Moderne Automobilwerke haben in den vergangenen Jahren Maßnahmen umgesetzt, die eine deutliche Effizienzsteigerung in der Logistik bewirkten:
klare Trennung der wertschöpfenden Tätigkeiten (Maschinen- und Anlagenbedienung) von den nicht wertschöpfenden (Mate– rialver- und -entsorgung)
Flexibilisierung der Fertigung mit dem Ziel, auch bei hoher Varianz der Produkte eine effiziente Materialbereitstellung mit minimalen logistischen Rüstverlusten zu erreichen
Erhöhte Produktivität der Logistiktätigkeiten durch Taktung
Kompensation von Verbrauchsschwankungen durch einen dynamischen Aufbau von „Supermärkten“. Das sind Pufferzonen zwischen einzelnen Fertigungsbereichen mit festgelegtem Minimal- und Maximalbestand der gelagerten Materialien. Sie werden in der Regel über Kanban gesteuert und eignen sich vor allem für Bauteile mit gleichmäßigem Verbrauch. In der dynamischen Variante müssen nicht alle Teile immer vorrätig sein.
Versorgung der Bestände in Supermarkt und Lager über eine Anlieferung in kurzer Taktung durch Gebietsspediteure ohne Erhöhung der Frachtkosten
exakte Definition und vertragliche Fixierung der Anforderungen an die Lieferanten (im Bauteil- und Logistikqualität, z.B. Liefertreue)
Spezifisch Anforderungen bei der Komponentenfertigung
Spätestens an diesem Punkt werden bei Spezialisten aus der Komponentenfertigung Zweifel aufkommen, ob sich diese Maßnahmen in ihrem Verantwortungsbereich tatsächlich umsetzen lassen. Denn die Rahmenbedingungen der Komponentenproduktion sind – aus der Sicht der Logistik – deutlich ungünstiger (Bild 2).
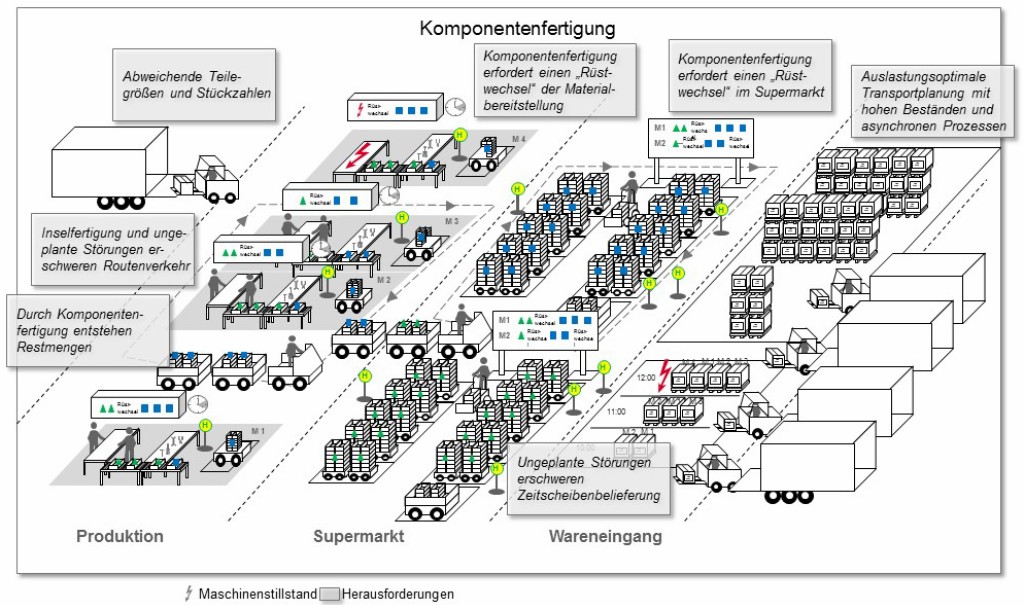
Bild 2 In der Komponentenfertigung sind die Rahmenbedingungen deutlich ungünstiger als in der Automobilproduktion. Bild: Porsche Consulting
Auf einer Maschine werden häufig Produkte mit abweichenden Teilegrößen und Stückzahlen gefertigt. Zudem ist die Produktion oftmals als „Inselfertigung“ organisiert, in der es unterschiedliche Taktraten sowie ungeplante Störungen gibt. Zumeist wird in Losen gefertigt, bei denen Restmengen in den bereitgestellten Gebinden entstehen. Aufgrund der Losfertigung ist jeweils ein „Rüstwechsel“ der Materialbereitstellung sowie ein „Rüstwechsel“ im Supermarkt erforderlich. Ungeplante Störungen erschweren eine kurz getaktete und gleichmäßige Belieferung durch die Lieferanten. Die Bestände sind auch deshalb häufig hoch, weil die Produktion nicht über Direktanlieferungen von Gebietsspediteuren versorgt wird. Nicht zuletzt sind die Anforderungen an die Lieferanten meist nicht definiert, kaum vertraglich fixiert, und sie werden noch seltener konsequent eingefordert und regressiert.
Welche branchenspezifischen Lösungen sind zielführend?
Trotz dieser Unterschiede können die in der Automobilproduktion bereits bekannten Prinzipien zur Implementierung einer „schlanken“, flexiblen und effizienten Logistik auch in der Komponentenfertigung greifen – sofern man die Prinzipien bzw. ihre Umsetzung entsprechend adaptiert (Bild 3).
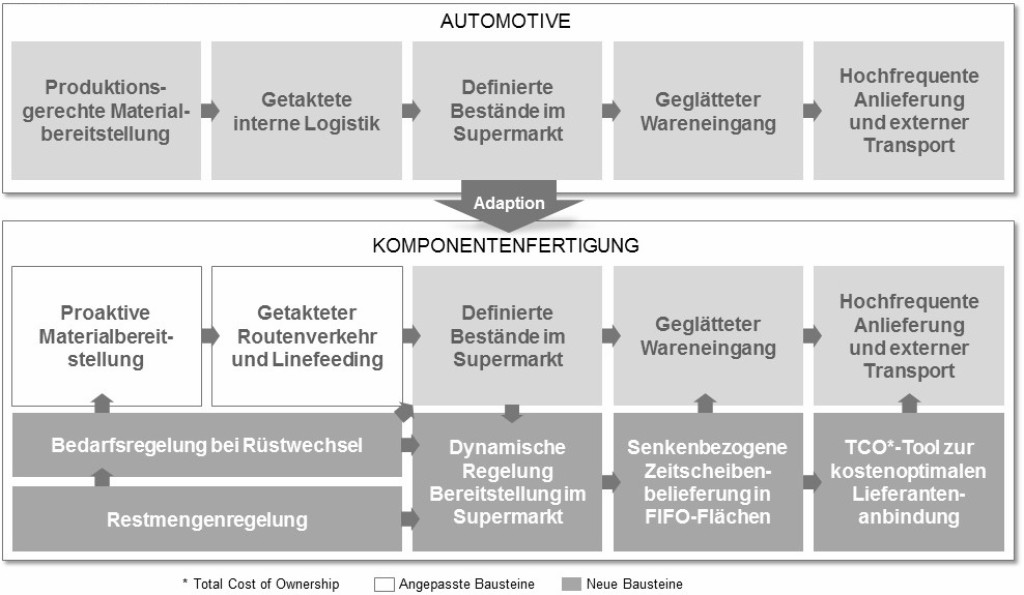
Bild 3 Für die Umsetzung einer „schlanken“ Logistik nach den Prinzipien der Automobilindustrie sind in der Komponentenfertigung zusätzliche Maßnahmen nötig. Bild: Porsche Consulting
So sollte zum Beispiel die Materialbereitstellung an die Anforderungen der Branche angepasst werden, ebenso die Taktung des Routenverkehrs und der Versorgung der einzelnen Linien.
Gerade die Materialbereitstellung bietet bei der Komponentenfertigung hohes Potenzial für Verbesserungen. Denn die steigende Variantenvielfalt führt dazu, dass eine immer größere Anzahl von Varianten bereitgestellt werden muss. Daraus resultiert, dass die klassische Art der Montagelinien- oder Maschinenversorgung über Stapler und Großbehälter nicht mehr funktioniert bzw. sehr fehleranfällig und ineffektiv wird. Besser ist eine dynamische Materialbestellung, die bei einem Rüstwechsel auch die bereitgestellten Teile austauscht. Dafür ist – analog zur Automobilindustrie – zu definieren, welches Teil wie zugeführt wird. Neben einer statischen oder dynamischen Bereitstellung sind für alle Umfänge auch die jeweiligen Ladungsträger festzulegen (Groß- oder Kleinladungsträger, Kommissionier- oder Sequenzbehälter). Die Steuerung erfolgt jeweils auftrags- oder verbrauchsgesteuert.
Als zusätzliche Maßnahmen sind eine Bedarfsregelung bei Rüstwechseln sowie eine dynamische Steuerung der Bereitstellung im Supermarkt zu berücksichtigen. Außerdem muss eine Regelung für den Umgang mit Restmengen getroffen werden: Werden die Teile bei auftragsgesteuerten Umfängen abgezählt oder werden komplette Behälter bereitgestellt? Dabei ist der Aufwand zwischen dem Restmengenprozess und dem Abzählen abzuwägen.
Wichtig ist in der Komponentenfertigung auch eine senkenbezogene Zeitscheibenbelieferung in FiFo-Flächen (Bild 4).
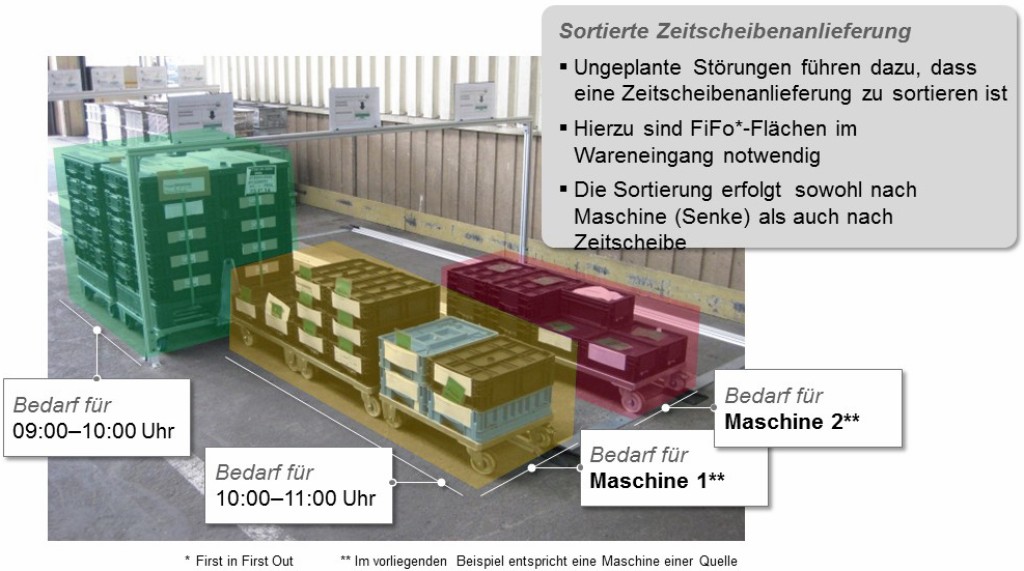
Bild 4 Praktisches Beispiel: Die Bereitstellung einer definierten Menge von Vorprodukten an der Maschine verhindert eine Unterbrechung des Materialflusses, wenn es in vorgelagerten Bereichen zum Maschinenstillstand kommt. Bild: Porsche Consulting
Das bedeutet, dass an den einzelnen Maschinen bzw. in einzelnen Produktionsbereichen definierte Mengen an Vorprodukten bereitgestellt werden. So wird vermieden, dass der Materialfluss ins Stocken gerät, sobald eine Maschine (geplant oder ungeplant) stillsteht.
Neues Planungsinstrument: Das „Line Back-Verfahren“
Als Planungs- bzw. Optimierungsinstrument bei der Umsetzung des hier vorgestellten Konzeptes ist eine Line-Back-Planung empfehlenswert. Darunter versteht man die Analyse der gesamten logistischen Wertschöpfungskette in umgekehrter Richtung: Sie beginnt bei der Maschine oder beim Mitarbeiter an der Maschine bzw. in der Montage und endet beim Lieferanten.
Es gibt mittlerweile viele Beispiele für den Nutzen einer Line-Back-Planung bei der Konzeption und Umsetzung einer „schlanken“ und flexiblen Logistik. Zu den wesentlichen Vorteilen gehören geringere Bestände bei verkürzten Durchlaufzeiten. Die erhöhte Logistikeffizienz mündet aber auch in eine deutlich höhere Prozessqualität, d.h. in weniger Fehlteile.
Auch hier geht es nicht darum, die in der Automobilproduktion bewährten Konzepte 1:1 zu übernehmen. Sie müssen vielmehr an die Anforderungen der Komponentenfertigung adaptiert werden. Zum Beispiel ist beim Routenverkehr in einer Losgrößenfertigung mit unterschiedlichen Bauteilabmessungen der Takt zwischen den Maschinen nicht konstant. Vielmehr schwankt der Bedarf. Die Routenverkehre sollten deshalb über so genannte Taktanzeiger gesteuert werden. Dabei wird der Takt über die geringsten Reichweiten der Produktion ermittelt und elektronisch erfasst.
Praxisbeispiel zur Umsetzung der Maßnahmen in der Fertigung
In Bild 5 sind die Lösungswege für die Umsetzung einer schlanken Logistik unter den spezifischen Bedingungen der Komponentenfertigung dargestellt.
Dieses Konzept wurde – unterstützt durch Porsche Consulting – bei dem Automobilzulieferer Schaeffler im Werk Hirschaid bei Bamberg umgesetzt.
Als Ausgangssituation fanden die Berater hier U-förmige Montagelinien vor, die von Staplern mit Teilen auf Großladungsträgern oder in Kartonlagen beliefert wurden. Die Aufgabestationen wurden auf Zuruf bestückt, und die Bestände am Band waren hoch.
Innerhalb eines Jahres wurde im Werk eine schlanke Logistik nach dem beschriebenen Prinzip eingeführt. Standard sind heute Bestände am Verbauort von wenigen Stunden, ein sich selbst steuernder Restmengenprozess, eine Anlieferung in Fünf-Stunden-Scheiben, eine staplerlose Belieferung der Produktion mit Routenzügen sowie ein durchgängiger Abruf über E-Kanban. Herr Reges, Leiter Logistik im Werk Hirschaid, beschreibt die Bedeutung dieses Konzeptes für die gesamte Produktion wie folgt: „Die Logistik ist der Stoffwechsel der Fertigung. Um schlank und gesund zu bleiben, ist ein gesunder Stoffwechsel notwendig. Wenn das nicht funktioniert, sind negative Folgen vorprogrammiert.“
Die Umsetzung des beschriebenen Konzeptes erzeugte messbare Resultate. Die Ausbringungsmenge in der Produktion stieg an, die Bestände in der Materialbereitstellung sanken auf weniger als die Hälfte, und die Fehlteilmengen gingen nach der Einführung einer proaktiven Materialbereitstellung deutlich zurück. Die einzelnen Linien werden nun in zyklischen Routen versorgt. Eine dynamische Regelung der Bereitstellung im Supermarkt vereinfacht das Handling und macht auch einen Lagerschritt überflüssig. Im Rahmen der Realisierung dieses Konzeptes wurden auch die Planungs- und Steuerungsprozesse entsprechend angepasst.
Durch zusätzliche Maßnahmen, die sich zurzeit in der Vorbereitung befinden, lässt sich die Logistik weiter optimieren. Dazu gehören die Vereinheitlichung der eingesetzten Behälter und die stärkere Integration der Lieferanten.
Praktische Umsetzung in fünf Schritten
Bei der Realisierung dieser Maßnahmen empfiehlt sich ein fünfstufiger Prozess. Zunächst sind die richtigen Voraussetzungen für das Projekt zu schaffen: Das Projektteam sollte nicht nur aus Logistikern bestehen, sondern interdisziplinär mit Mitarbeitern aus Beschaffung und Produktion sowie Planung/ Steuerung besetzt sein. Auch über die Systemgrenzen sollte Klarheit herrschen: Wird nur die Intralogistik untersucht oder auch die In- und Outbound-Logistik? Empfehlenswert ist als „Minimum“ die Betrachtung aller Prozesse vom Lieferanten bis zum eigenen Warenausgang. Das Projekt sollte zunächst in einem Pilotbereich umgesetzt werden, um erste Kennzahlen zu ermitteln und das Gesamtpotenzial errechnen zu können.
In Schritt zwei wird ein Projektmanagement implementiert und das Konzept in unterschiedlichen Arbeitspaketen erstellt. Im Anschluss daran erfolgt die Planung einer proaktiven Materialbereitstellung bis zur Supermarktausplanung sowie die Pilotierung in einem Produktionsbereich. Im vierten Schritt wird die Belieferung des Supermarkts bis hin zur Anbindung des Lieferanten geplant und in einem Bereich pilotiert. Abschließend ist der Roll-Out zu planen, den die Verantwortlichen im Werk eigenständig umsetzen können. Zudem sollten alle Hauptlieferanten integriert werden.
Erst wenn diese neuen Prozesse stabil laufen, sollte der Anwender weitere Schritte zur Optimierung bzw. zur Reduzierung von Verschwendungen initiieren. Dazu zählen etwa – wie im zuvor genannten Beispiel – die Auswahl und Vereinheitlichung der eingesetzten Behälter und Ladungsträger, eine Verbesserung und Stabilisierung des Planungsprozesses und eine stabile Einhaltung des Taktes.
Im Trend: Kommissionierung im „Ware zum Mann“-Prinzip“
Darauf aufbauend empfiehlt sich eine weitere Reduktion der Verschwendung im Logistikprozess durch eine Forcierung von Automatisierung und IT. Ein Beispiel ist die (teil-)automatisierte Kommissionierung nach dem Ware-zum-Mann-Prinzip, die Laufwege reduziert, die Prozesse verstetigt und den Aufwand für den Restmengenprozess verringert.
Diese Automatisierung wird unter anderem von Amazon genutzt. Das Unternehmen erreicht durch den Einsatz von Fahrerlosen Transportsystemen (FTS) eine deutliche Effizienzsteigerung im Kommissionierprozess. Inzwischen hat Amazon einen US-amerikanischen FTS-Hersteller aufgekauft und als Ausblick das Ziel genannt, diese Fahrzeuge verstärkt in der produzierenden Industrie einzusetzen. Die Vorteile liegen auf der Hand. Auch andere Unternehmen nutzen bereits diese neue Art der Kommissionierung und der Teileversorgung von Produktionslinien und Montage-Arbeitsplätzen (Bild 6).
Ferdinand Graf, Senior Projektmanager
Reinhard Baller, Projektmanager, beide Porsche Consulting GmbH, Bietigheim-Bissingen.