So werden Kennzahlensysteme für Produktionslogistikbereiche stimmig
Ein am Technologiezentrum PULS der Hochschule Landshut erstelltes Modell beschreibt neue Ansätze, mit denen sich Zielsysteme in Bereichen der Produktionslogistik generieren und anwenden lassen.
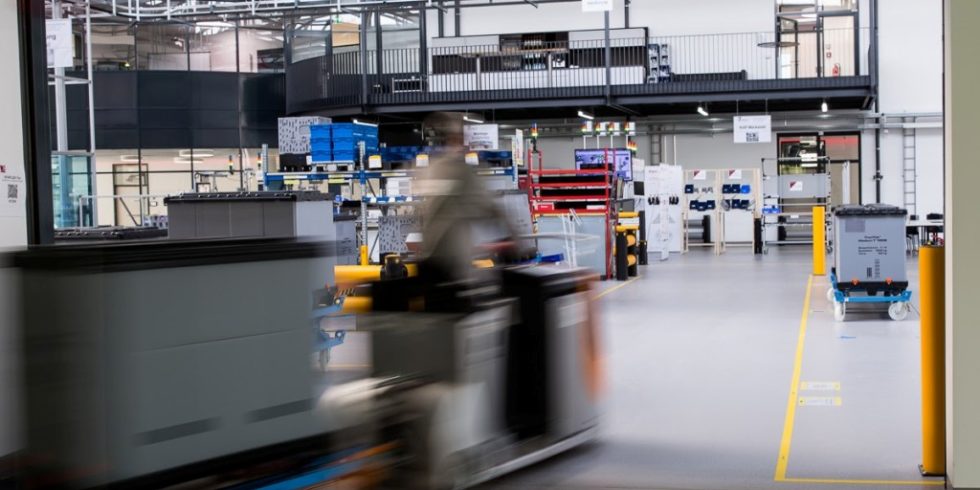
Musterfabrik zum Validieren von Logistik-Kennzahlensystemen am Technologiezentrum PULS der Hochschule Landshut in Dingolfing.
Foto: Verfasser
Die Optimierung von Produktionsbereichen auf der Basis der Leistungsmessung von Mensch und Maschine ist in den vergangenen Jahrzehnten immer stärker etabliert worden. Es finden sich in vielen Unternehmen in sich schlüssige so genannte Produktionssysteme. Diese beinhalten festgelegte Zielekaskaden und klare Verantwortungen im Hinblick auf Produktivitätsverbesserungen. So weiß etwa ein Vorarbeiter in einer industriellen Produktion genau, welche Zielsetzungen im Hinblick auf die Stückzahl in einer Schicht in unterschiedlichen Segmenten seiner Produktion erwartet werden und im Nachgang auch gemessen werden können.
Auf der Basis von Kennzahlen werden Ziele definiert und die ausführenden Bereiche können über eine entsprechende Rückmeldung kommunizieren, indem ein bestimmter Grad der Zielstellung erreicht wird. Kennzahlen im Umfeld der Produktion können somit als Kommunikationsmittel in beide Richtungen verstanden werden.
Für die Produktion an sich sowie für die Logistik im Sinne der so genannten „Straßenlogistik“, also im Umfeld der Planung und Ausführung von Transporten zwischen Werken, wurden in den vergangenen Jahrzehnten viele Systeme entwickelt, die es unterstützen, auf einfache Weise Transparenz zwischen Zielen und erreichten Leistungen darzustellen.
Kennzahlensystem fehlt
Allerdings ist im Bereich der „Produktionslogistik“, eine Bezeichnung, die im Verlauf des vorliegenden Beitrags eingeordnet wird, bisher kein in sich stimmiges und verbreitet industriell eingesetztes Kennzahlensystem etabliert.
Eine wesentliche Motivation für die Beschäftigung mit diesem teilweise im Bereich des operativen und strategischen Managements noch unterrepräsentierten Umfeld der Produktionslogistik ist dessen stetig steigende Bedeutung – gespeist aus einer seit Jahrzehnten zunehmenden Produktindividualisierung in Verbindung mit einer weiter zunehmenden Arbeitsteilung sowohl innerhalb eines Werkes, aber auch in Werksverbund-Systemen sowie über Unternehmensgrenzen hinaus.
Passend zu einer Darstellung von Lödding [1] scheitert die optimale Anwendung von Logistikprozessen zu einem wesentlichen Anteil an einem mangelnden Verständnis des Gesamtsystems. Die Bildung und Nutzung schlüssiger Kennzahlen zur Beschreibung von Zielzuständen kann helfen, systematisches Verständnis zu gewinnen.
Im Folgenden sollen daher Ansatzpunkte hergeleitet werden, mit Hilfe welcher eine Basis für die Etablierung für Kennzahlensysteme in der Produktionslogistik geschaffen werden soll.
Relevante Charakteristika der Produktionslogistik
Der Begriff „Produktionslogistik“ wird in vielfacher Weise verwendet, daher ist es unerlässlich, den Betrachtungsgegenstand zu erläutern. Passend für den vorliegenden Zusammenhang erscheint die Definition nach Augustin, der Produktionslogistik als Sammelbegriff für die Gestaltung, Planung und Steuerung aller Teilprozesse von Produktions-, Material- und Informationsprozessen ansieht [2].
Versucht man eine Einordnung von Geschehnissen der Produktionslogistik in einem Produktionsbereich vorzunehmen, wird deutlich, dass sowohl an den Systemgrenzen einer Produktion aber auch innerhalb des Systems produktionslogistische Aktivitäten verortet werden können. An den Systemgrenzen lassen sich einerseits die vereinnahmenden Prozesse oder die Vorbereitung der Zustellung in die Produktion beschreiben; andererseits werden naturgemäß produktionslogistische Aufgaben vor dem Verlassen der Produktion etwa in Form von Zuordnen, Verpacken oder Kennzeichnung umgesetzt.
Aber auch innerhalb des Systems „Produktionsbereich“ entstehen logistische Anforderungen zur Unterstützung der einzelnen Fertigungsprozesse, etwa Zustellungs-, Positionierungs- oder Warteprozesse. Prozessbegleitende Puffer können überdies eine Entzerrung und damit eine Optimierung der Produktivität der einzelnen Fertigungsverfahren bewirken (s. Bild 1).
Die Notwendigkeit, Ziele und Zielsysteme für produktionslogistische Umfänge spezifisch zu betrachten und diese praxisorientiert umzusetzen, wird im folgenden Abschnitt beleuchtet.
Aufbauanleitung für Kennzahlensysteme in der Produktionslogistik
Eine anschauliche Beschreibung der Komplexität zur Abbildung von Zielen in der Produktionslogistik zeigt die so genannte „Logistik-Schizophrenie“, geprägt durch Seeck [3]. Es wird darin dargestellt, dass Verzögerungen oder Qualitätseinbußen von einzelnen Teilprozessen eine Multiplikation des Gesamtverlustes beinhalten. Daher ist eine separierte Betrachtung der jeweiligen Bedeutung einzelner durch Planungen provozierter Verluste vorzunehmen. Ja nach Kontext kann in einem produktionslogistischen Gefüge etwa Ausschuss zum Ende einer Prozesskette durch ein vorhergehendes „Blockieren“ der bisher durchlaufenen Prozesse deutlich gravierendere Auswirkungen auf die Gesamtleistung des Produktionsbereiches haben als ein Ausschuss in selben prozentualem Maß eines Prozessschrittes zu Beginn der Kette.
Dies zeigt, dass standardisierte, eventuell technologiebezogene Herangehensweisen für Zielsystembetrachtungen in Produktionsbereichen nicht ohne Weiteres auf Produktionslogistik-Umfänge zu übertragen sind [4].
Fokus der Betrachtung ist die Erzielung eines übergreifenden Optimums, weshalb auch im ersten Schritt das Gesamtsystem, wie etwa in Bild 1 gezeigt, zu definieren ist.
Im Zentrum der im Rahmen dieses Beitrags gezeigten Vorgehensweise steht der Konflikt zwischen den drei Fundamentalzielen der Produktionslogistik:
- Bestandsoptimierung im Verantwortungsbereich der Logistik zur Minimierung der Kapitalbindung und Fokussierung auf Wertschöpfungssupport.
- Aufwandsoptimierung in Bezug auf Wege, Personal, Ladungsträger, Flächen, Handling und Nutzung passender Verpackungen.
- Ausfallminimierung in Bezug auf die passgenaue Zustellung für alle weiteren Abnehmer, etwa LKW-Beladung oder Anlagenbestückung.
Konfliktlösung
Diese Fundamentalziele bezeichnen ein Ergebnis des Arbeitskreises „Komplexitätsreduzierung in der Produktionslogistik“ am Institut der Autoren, welche im Rahmen des EFRE-geförderten Projekts „Intelligente Produktionslogistik“ in den Jahren 2017 bis 2020 gemeinsam mit Vertretern und Verantwortungsträgern in der Logistik von 13 produzierenden Unternehmen umgesetzt wurde.
Die Auflösung dieses Konflikts bedingt in erster Linie ein situationsspezifisches Verständnis aller Wirkzusammenhänge dieser Fundamentalziele (sowohl untereinander als auch in Bezug auf deren Instrumentalziele). Erst dadurch ist es überhaupt möglich, Zielvorgaben mit bestimmten Intentionen und dem klaren Wissen um Stoßrichtungen und „Nebenwirkungen“ zu implementieren.
Eine stimmige Auflösung des Konfliktes der beschriebenen Fundamentalziele ist dadurch beschrieben, dass jede relevante Entscheidung eines Verantwortlichen in der Produktionslogistik bewusst mit der Kenntnis der jeweiligen Beeinflussung der einzelnen Fundamentalziele getroffen wird und passend kommuniziert sowie visualisiert wird. Im Sinne einer „balanced scorecard“, also einer ausbalancierten Zielelandkarte können so die strategischen Vorgaben des Unternehmens bestmöglich durch die jeweilige Zielerreichung aufgelöst werden.
Kriterien für die Umsetzung des Modells
Drei grundsätzliche Restriktionen sind zu berücksichtigen, um das beschriebene Modell umsetzen zu können.
Erstens ist sicherzustellen, dass Prozesse und Ressourcen in ausreichendem Maß vorhanden sind, um überhaupt gestalterisch wirken zu können und Alternativen bei Entscheidungen gezielt auswählen zu können. In Abgrenzung zum Fundamentalziel „Aufwandsoptimierung“ beschreibt die Sicherstellung der Ressourcen hier das minimale Maß, welches zum Betrieb notwendig ist.
Zweitens ist darauf zu achten, dass die zum Betrieb notwendigen Informationen eindeutig und rechtzeitig vorhanden sind. Etwa Transparenz oder eindeutige Regeln zu Auftragsreihenfolge, Transportzielen, Verpackungsmedien sind hier zu nennen.
Drittens muss Fehlerfreiheit in der Systemauslegung gegeben sein. Hier können Poka-yoke-Anwendungen helfen, um durch Scanprozesse und Zuordnungsrestriktionen das System bereits so zu gestalten, dass nicht Ziele dadurch verfehlt werden, indem durch systemseitige Fehler Mehraufwand entsteht.
Werden die drei Fundamentalziele mit diesem Verständnis und im Rahmen dieser Vorgehensweise kontinuierlich gemessen, kann ein entsprechendes Verbesserungsmanagement etabliert und Mehrwert generiert werden. Die zugrunde liegenden Zusammenhänge sind in Bild 2 zusammengefasst.
Fazit und Ausblick
Das auf den Managementphilosophen Peter Drucker zurückzuführende Zitat, dass nur verbessert werden kann, was auch gemessen werden kann, findet im Rahmen dieses Beitrags Anwendung für die Produktionslogistik. Hierbei ist festzustellen, dass viele Zielsysteme, die heute in produzierenden Unternehmen etabliert sind, aufgrund der spezifischen Anforderungen der Produktionslogistik an ihre Grenzen geraten. In einem Arbeitskreis am Institut der Autoren wurde ein Referenzzielsystem für Produktionslogistik erarbeitet, welches erlaubt, individuell Zielsysteme für die Produktionslogistik auszuarbeiten.
Die ersten pilothaften Anwendungen bei produzierenden Unternehmen zeigen den Erfolg der beschriebenen systematischen Vorgehensweise. Eine stringente digitale Unterstützung der Vorgehensweise beschreibt den Fokus der kommenden Forschungsaktivitäten am Technologiezentrum PULS der Hochschule Landshut in Dingolfing.
Literaturverzeichnis
[1] Lödding, H.: Produktionslogistik, in: Furmans, K.; Kilger, C. (Hrsg.): Betrieb von Logistiksystemen, Fachwissen Logistik. Berlin: Springer-Verlag GmbH Deutschland, ein Teil von Springer Nature, 2019.
[2] Augustin, S.: Produktionslogistik, in: Koether, R. (Hrsg.): Taschenbuch der Logistik, 5. Aufl., München: Hanser-Verlag, 2018.
[3] Seeck, S.: Erfolgsfaktor Logistik – Klassische Fehler erkennen und vermeiden. Wiesbaden: Gabler-Verlag, 2010.
[4] Roeren, S.; Mannke, C.: Ansatz zur systematischen Zieleableitung für Produktionsbereiche Unternehmensstrategie und Produktionsmerkmale als Ausganspunkt für Zielfokussierungen in der Produktionsplanung. In ZWF – Zeitschrift für wirtschaftliche Fabrikplanung: 10/2012, S. 712–716.
Förderhinweis:
Das Technologietransferprojekt „Kompetenznetzwerk Intelligente Produktionslogistik“ (KIP) wird aus Mitteln des Europäischen Fonds für regionale Entwicklung (EFRE) – Operationelles Programm mit Ziel „Investition in Wachstum und Beschäftigung“ Bayern 2014 – 2020 gefördert.
Folgende Beiträge könnten Sie auch interessieren:
Hohes Potenzial für lernende Systeme in logistischen Entscheidungsprozessen
Systeme, Software und Modernisierung
3D-Druck verändert auch die Produktionslogistik
Digitalisierung als Chance für die Produktionslogistik
Autoren: Prof. Dr.-Ing. Sven Roeren, geboren 1978, ist promovierter Maschinenbau-Ingenieur und beschäftigt sich etwa seit der Jahrtausendwende mit herausfordernden Aufgaben an der Schnittstelle zwischen Automobil-OEM und Zulieferern. Er hat mehrere Jahre die Produktion am Stammwerk eines Zulieferers geleitet und etwa 200 Forschungs- und Beratungsprojekte zur Reduzierung von stellenweise unnötiger Komplexität in der Produktion verantwortet. 2011 wurde er zum Professor für Produktionssystematik an der Hochschule in Landshut ernannt. Er war neben seiner Lehr- und Forschungstätigkeit mehrere Jahre Dekan der Fakultät Maschinenbau ebenda und leitet ein Beratungsunternehmen sowie ein An-Institut der Hochschule Landshut (Technologiezentrum Dingolfing). B. Eng. Sandra Meier, geboren 1987, sammelte erste Berufserfahrung in der Konstruktionsabteilung eines Interieur-Zulieferers der Automobilbrache. Danach studierte sie Maschinenbau an der Hochschule in Landshut mit dem Schwerpunkt Leichtbau. Seit 2015 ist sie in der roeren GmbH, einem mittelständischen Beratungsunternehmen für Produktion und Management, in München tätig. Als wissenschaftliche Mitarbeiterin am Technologiezentrum Produktions- und Logistiksysteme (TZ PULS) der Hochschule Landshut beschäftigt sich Frau Meier seit 2017 vor allem mit der Thematik von Kennzahlensystemen in der Produktionslogistik. B. Eng. Denis Alt, geboren 1989, studierte Maschinenbau an der Hochschule in Landshut mit dem Schwerpunkt konstruktiver Leichtbau. Seit 2017 ist er in der roeren GmbH, einem mittelständischen Beratungsunternehmen für Produktion und Management, in München tätig. Als wissenschaftlicher Mitarbeiter am Technologiezentrum Produktions- und Logistiksysteme (TZ PULS) der Hochschule Landshut beschäftigt sich Herr Alt seit 2017 mit der flexiblen Puffersteuerung bei asynchronen Prozessketten speziell für kleine und mittelständische Unternehmen.