Systeme, Software und Modernisierung
Die Intralogistik hat auch in der Fertigung die wichtige Aufgabe, die richtigen Teile zur richtigen Zeit an den richtigen Ort zu bringen. Dafür braucht es moderne Systeme und Software-Lösungen – und vor allem den richtigen Partner, der Anwender technologieoffen berät, solche Systeme plant, entwickelt und umsetzt – nicht auf der grünen Wiese, sondern auch im Bestand. Das zeigen zwei aktuelle Beispiele.
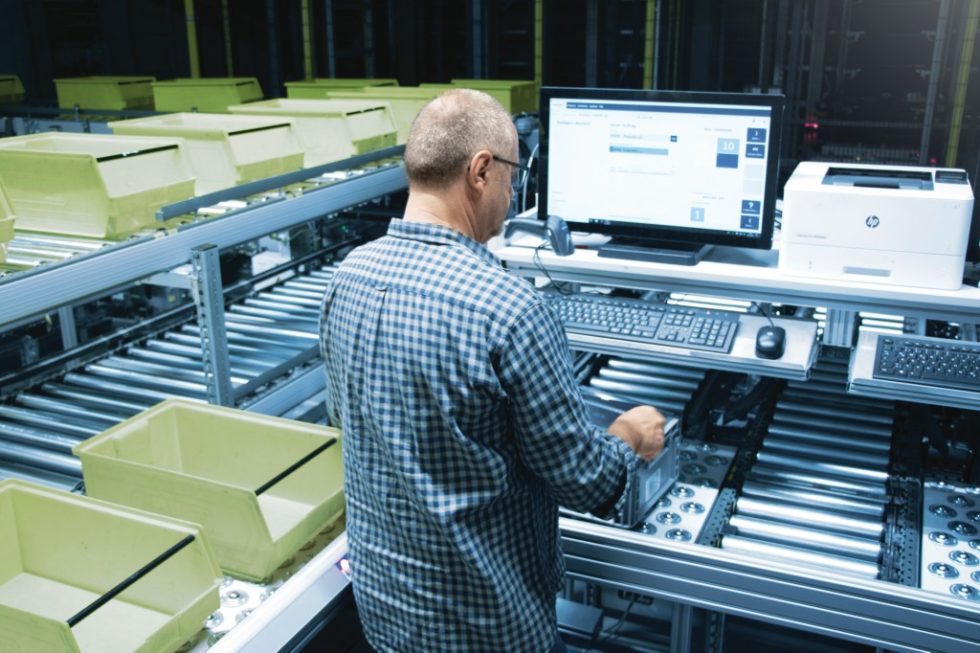
Das neue Lager ist nicht nur Dreh- und Angelpunkt des neuen Standorts von Eisele Pneumatics, sondern auch das Herzstück der Digitalisierung im Unternehmen. Bild: viastore
Unsere Kunden erwarten die schnelle und fehlerfreie Lieferung ihrer Waren“, sagt Artur Vogel, Teamleiter Optimierung/Kontinuierlicher Verbesserungsprozess bei Eisele Pneumatics. Denn ohne diese Anschlusskomponenten aus Ganzmetall – zum Beispiel Steckanschlüsse, Schnellschlusskupplungen oder Schlauchverschraubungen – steht die Produktion von Maschinen und Anlagen bei deren Kunden still. Durch die erfolgreiche internationale Expansion, insbesondere in den USA und Asien, hat das Familienunternehmen viele Automobilkunden hinzugewonnen, die es pünktlich und zuverlässig beliefern muss. Das alte Lager stieß hierbei an seine Grenzen.
Vom Handlager zum Automatik-Lager
„An unserem früheren Standort mitten in Waiblingen hatten wir ein Handlager“, erklärt Vogel. Es war in verschiedene Bereiche aufgeteilt, die mit zwei Meter hohen Fachbodenregalen ausgestattet und in drei Stockwerken untergebracht waren. „Es platzte aus allen Nähten“, erinnert er sich und ergänzt: „Es bot keinerlei Reserven für weiteres Wachstum oder für neue Produktgruppen.“ Das Unternehmen entschied sich daher für den Neubau eines modernen automatischen Kleinteilelagers. Es sollte die schnelle Verteilung der Waren auch in Zukunft sicherstellen und bildete zugleich den ersten Schritt des Firmenumzugs von Eisele – raus aus der beengten Lage, hinein in ein Gewerbegebiet am Stadtrand. Das schaffte die Möglichkeit, die bisher getrennten Bereiche in einem zusammenzuführen: „In das neue Lager werden die produzierten Einzelteile sowie die fertig montierten Baugruppen eingelagert. Es verbindet somit die Fertigung mit der Montage und dient gleichzeitig als Versandlager für unsere Fertigwaren“, erläutert Vogel. Nur das Ausgangsmaterial für die Ganzmetall-Anschlüsse – Stangenmaterial aus Messing, Edelstahl und Aluminium – puffert der Mittelständler, der eine Fertigungstiefe von nahezu 100 % hat, in einem der zerspanenden Fertigung vorgelagerten Bereich. Ansonsten werden alle für das fertige Produkt benötigten Teile über das Lager geführt.
Shuttle-Lager und Service für sichere Produktionsversorgung
Eisele entschied sich nach eingehender Beratung durch viastore für die Shuttle-Technik: „viastore war eine der wenigen Firmen, die ein solches System inklusive der passenden Softwarelösung im Angebot hatten“, sagt Vogel.
Das Shuttle-Lager dient Eisele als Halbfertigteillager mit Wareneingang, versorgt die Produktion und Montage mit Bauteilen und ist gleichzeitig Versandlager für die gefertigten Produkte. Bild: viastore
Für den Stuttgarter Anbieter sprachen aber noch weitere Gründe: „Als mittelständischer Betrieb ohne Erfahrung mit Automatiklagern haben wir weder das Know-how noch die Fachleute für die Auslegung, die Implementierung und die Wartung eines solchen Systems“, berichtet Vogel weiter. „Daher haben uns die Intralogistik-Experten vom ersten Schritt an eng an der Hand genommen und uns die für uns passenden Lösungen gezeigt.“ viastore-Projektmanager Peter Polywka ergänzt: „Wir können unsere Kunden technologieunabhängig beraten.“ Zudem bietet viastore auch die Warehouse-Management-Software (WMS) an – der Kunde bekommt das gesamte aufeinander abgestimmte System aus einer Hand. „Das ist vor allem im Betrieb der Anlage vorteilhaft, da unsere Kunden auf diese Weise auch für den Service und die Betreuung nur einen Ansprechpartner haben“, ergänzt er.
Flexibilität und Skalierbarkeit
viastore lieferte für das neue Eisele-Lager eine flexible Shuttle-Lösung, die Platz für 17 280 Behälter bietet. Als Shuttle dienen Fahrzeuge vom Typ viaflex³. Sie sind nicht nur über verschiedene Regalgänge in einer Ebene unterwegs, sondern können diese auch wechseln. „Dadurch stellen wir sicher, dass wir immer auf alle Produkte zugreifen können“, begründet Vogel die Systemwahl. Für ihn war die Skalierbarkeit ein weiteres wichtiges Argument für diese Technologie: „Wir sind mit fünf Fahrzeugen gestartet – das hat den Anfangs-Invest reduziert und reicht uns vollkommen für den aktuellen Bedarf. Wenn wir mehr Leistung benötigen, können wir sukzessive bis zu zwanzig Shuttles in der vorhandenen Regalkonstruktion fahren lassen“. Auch bei den Lagerplätzen sieht das Konzept Erweiterungen vor: Während im Erdgeschoss der Raum komplett mit Behälter-Stellplätzen gefüllt ist, kann die Regalkonstruktion im zweiten Stockwerk noch erweitert werden, sodass bis zu 26 780 Behälter Platz finden. Der Lift dafür ist schon eingebaut.
Dreh- und Angelpunkt des neuen Firmen-Standorts
Das neue Lager ist auch das Herzstück der Digitalisierung im Unternehmen. Denn das alte war listengeführt, ohne Handhelds oder ähnliche digitale Hilfsmittel – was bei der stetig wachsenden Zahl an Artikeln und dem zunehmenden Produktportfolio zu immer mehr Problemen führte, wie Vogel sich erinnert: „Ware war immer wieder nicht auffindbar, die Bestände stimmten nicht und die Such- und Zugriffszeiten wurden länger.“ Mit dem neuen automatischen Lager geht ein modernes Warehouse-Management-System einher. „Unser ERP-System kann die erforderlichen Logistikfunktionen nicht abdecken“, erklärt Artur Vogel. Eisele hat Sage b7 im Einsatz, ein speziell für mittelständische produzierende Unternehmen konzipiertes System. „viastore bietet mit viadat 9 ein zukunftsfähiges WMS, wir erhielten Lagertechnik und Software aus einer Hand. Ein Drittanbieter hätte unnötige Schnittstellen bedeutet.“ viadat 9 lässt sich über standardisierte Interfaces an die ERP-Systeme unterschiedlicher Hersteller anbinden, sodass die Kommunikation zwischen Sage b7 und dem WMS schnell und einfach war.
Intuitive Bedienung
viadat verfügt in seiner aktuellen Version über eine selbsterklärende Bedienoberfläche, über die Kommissionierer intuitiv über Touchscreen und ohne große Einarbeitungszeit in unterschiedlichen Zonen im Distributionszentrum arbeiten können. Für Artur Vogel ein wichtiges Feature, denn die Lager-Mitarbeiter waren den Umgang mit Software nicht gewohnt. „Uns hat viadat mit seinem Bedienkonzept und seinen Tools überzeugt. Wer ein Smartphone bedienen kann, kann auch viadat bedienen. Das hat uns den Umstieg enorm erleichtert.“ Beispielsweise sind die Dialoge immer gleich aufgebaut – egal, ob es ein Arbeitsplatz am Wareneingang, in der Kommissionierung oder im Versand ist. Die Mitarbeiter können dadurch flexibel zwischen den verschiedenen Stationen wechseln.
Fit für den digitalen Wandel
„Vor allem aber machen wir mit viadat 9 das Unternehmen fit für den digitalen Wandel“, ist Vogel überzeugt. „Wir können jetzt jederzeit exakte Bestände abrufen und schnell und einfach Auswertungen fahren.“ Dadurch lassen sich Schnellläufer und Ladenhüter identifizieren und aktuelle Verbräuche abfragen. „Auch die jetzt mögliche permanente Inventur ist ein großer Vorteil für uns“, ergänzt Vogel. „Das alte Lager mussten wir zwischen Weihnachten und Neujahr schließen, um die eingelagerten Artikel zu zählen. Heute ist der Aufwand minimal und ich kann die Inventur im laufenden Betrieb machen.“ Ziel von Eisele ist, die Geschäftsprozesse vom Auftragseingang und der Produktionsplanung über die Fertigung und Qualitätskontrolle bis zum Versand weiter zu optimieren. „Wir wollen im gesamten Unternehmen papierlose Prozesse etablieren“, erklärt Vogel. „Im Lager haben wir das mit viadat 9 bereits geschafft.“ In zukünftigen Projekten sollen Fertigung und Montage folgen. Vielleicht profitiert Eisele dann noch einmal von viadat – denn viastore kooperiert mit MPDV, Hersteller des Manufacturing Execution System (MES) Hydra. Damit können Logistik und Fertigung eng verzahnt werden, was für eine hohe Transparenz in den Prozessen und mehr Effizienz sorgt.
Mit guter Vorplanung und Team- arbeit zum erfolgreichen Retrofit
Ein anderes Beispiel, um die intralogistische Versorgung der Fertigung sicherzustellen: Die Modernisierung des 24 Jahre alten Produktionslagers von Metabo in Nürtingen. 1995 lässt der traditionsreiche Hersteller von Elektrowerkzeugen für professionelle Anwender von viastore ein automatisches Lager zur Versorgung der Produktion bauen, um Kapazitäten für weiteres Wachstum zu schaffen. Mit Erfolg: Heute erwirtschaftet Metabo knapp 500 Mio. € Umsatz – und das Lager versorgt die Montage immer noch sicher mit Bauteilen und Rohwaren. Dennoch war die Zuverlässigkeit nicht mehr ganz gegeben, wie Dennis Bosch, Leiter Logistik im Hauptwerk, erklärt: „Wir hatten zwar schon 2005 den Materialflussrechner modernisiert, doch nahm die Anzahl der Störungen mit den Jahren zu, auch wenn sie noch nicht ausuferte.“ Das Risiko eines Stillstands wollte Metabo vermeiden, denn das Lager muss immer verfügbar sein – die Produktion beim Werkzeughersteller ist so strukturiert, dass nach maximal vier Stunden Nachschub am Verbauort liegen muss. „viastore hat uns regelmäßig daran erinnert, dass in unserer Anlage veraltete Komponenten ein Risiko für die Verfügbarkeit darstellen“, schildert Bosch.
Innerhalb von drei Wochen wurde das Produktionslager von Metabo grundlegend modernisiert. Bild: viastore
Anlagenanalyse als Basis
Schließlich fiel die Entscheidung, die Verfügbarkeit des Lagers und eine zuverlässige Funktion zu erhöhen und für die nächsten Jahre zu sichern. „Hierfür hat viastore den Zustand der gesamten Anlage umfangreich analysiert“, sagt Dennis Bosch. Die Retrofit-Experten untersuchen den Zustand jeder Komponente und jedes Bauteils des Lagersystems. Bis zu drei Wochen kann solch eine Anlagenanalyse dauern – aber der Aufwand lohnt sich. Denn als Ergebnis erhält der Betreiber eine grafische Übersicht, die jedes Bauteil hinsichtlich seines Modernisierungsbedarfs bewertet und in Form einer Ampel darstellt: Zeigt die Ampel „grün“, besteht kein Handlungsbedarf, „gelb“ sollte im Auge behalten werden und „rot“ erfordert schnellstmögliche Maßnahmen. „Mit dieser Analyse arbeiten wir die Risiken sehr klar heraus und können entsprechende Handlungen ableiten. Zudem erarbeiten wir Vorschläge zur Reorganisation, da sich die Prozesse unserer Kunden im Laufe der Jahre oft ändern“, veranschaulicht Lars Breuer, stellvertretender Leiter Retrofit bei viastore.
Alles auf Rot
„Bei uns stand kaum eine Ampel auf Grün“, erinnert sich Dennis Bosch. Lars Breuer geht ins Detail: „Sehr viele Komponenten waren abgekündigt. Gerade für die alten S5-Steuerungen in der Fördertechnik und in den Regalbediengeräten waren keine Ersatzteile mehr verfügbar.“ Vor allem aber war die Hardware der IT veraltet. Sie setzte unter anderem noch für die Kommunikation mit der Fördertechnik auf das alte Bussystem Sinec L2 FMS, für das es inzwischen keine Schnittstellenkarte mehr gab. „Dabei hat uns die Cyberattacke 2017 nachhaltig die Augen geöffnet“, erinnert sich Dennis Bosch. Damals infizierte der Virus Petya mehr als 1 000 Arbeitsplatzrechner sowie 350 Server bei Metabo und verursachte eine tagelange Produktions- und Lieferunterbrechung. Alle betroffenen Systeme waren komplett neu aufzusetzen – die bereits abgekündigten Schnittstellenkarten konnten nur mit Mühe noch irgendwo organisiert werden. „Das hat uns noch einmal klar gemacht, was Verfügbarkeit bedeutet“, betont Bosch.
Exakte Vorplanung anhand detaillierter Roadmap
Auf Basis der Anlagenanalyse entschied das Unternehmen, nicht nur einzelne Komponenten zu modernisieren, sondern ein gesamtheitliches Retrofit durchzuführen. „Die dafür nötigen Vorarbeiten waren nicht ohne“, erinnert sich Dennis Bosch. „Denn wir mussten die Artikel, die wir im Zeitraum der Modernisierung in der Produktion benötigten, aus dem Lager holen und an anderen Orten im Werk unterbringen – in einem extra errichteten Zelt, aber auch direkt in den verschiedenen Abteilungen.“ Damit Metabo das planen konnte, hat viastore mit der Anlagenanalyse zugleich einen zeitlichen Rahmen definiert, den das Unternehmen für das Retrofit benötigt. In einer Roadmap wurde detailliert festgehalten, welche Arbeiten wann auszuführen sind. „So wussten wir genau, wann und wie lange die Anlage stehen würde“, erläutert Bosch. „Zudem konnten wir sagen, welche und wie viele Artikel aus dem Lager wir extern unterbringen mussten und was wir zu welchem Zeitpunkt zu tun hatten.“ Das half auch bei der Abstimmung mit allen anderen Beteiligten im Unternehmen, zum Beispiel mit den Abteilungen, in denen wir Platz für die zwischenzeitliche Lagerung der benötigten Artikel schaffen mussten.
In drei Wochen umfassend modernisiert
In drei Wochen ist die Logistikanlage von Grund auf modernisiert worden: Moderne S7-Steuerungen ersetzten die alten S5, der Verschiebewagen – er verbindet die Auslagergassen der Regalbediengeräte (RBG) mit den Kommissionierstationen – erhielt einen neuen Antrieb. Auch die Steuerungen und Antriebe der drei Brandschutztore, die den Regalbereich im Brandfall von der Vorzone und der restlichen Halle abtrennen, wurden modernisiert. „Hier war eine eigene Steuerung des Herstellers installiert, die ebenfalls inzwischen abgekündigt war“, erklärt Gregor Rentschler, Projektmanager bei viastore. „Mit den neuen Steuerungen haben wir eine Freifahrtsteuerung inklusive Notstromversorgung realisiert – damit ist sichergestellt, dass im Brandfall die Förderstrecke an den Brandtoren freifährt und die Tore sicher schließen können.“ Ein Aspekt, den die Brandschutzversicherungen heute fordern.
Auch der Materialflussrechner wurde überarbeitet: Er ist nicht mehr als Hardware ausgeführt, sondern läuft auf einem virtuellen Server, der sich auf einem Großrechner befindet und entsprechend gesichert ist. Die Visualisierung erhielt ebenfalls ein Update. Die Regalbediengeräte und die Fördertechnik wurden auf ein aktuelles Bussystem modernisiert. Die S7-Steuerung der Fördertechnik ist schließlich über Ethernet an übergeordnete Systeme angebunden, sodass fortan eine Fernwartung der Anlage bis in jede einzelne Komponente möglich ist.
Austausch der RBG brachte 30 % mehr Leistung
Die spektakulärste Maßnahme war der Austausch der alten Regalbediengeräte. „Wir wussten, dass unser Verschiebewagen noch Leistungsreserven hatte“, erläutert Dennis Bosch. „Daher wollten wir mit dem Retrofit auch gleich die Leistung der RBG steigern.“ viastore hat durchgerechnet, was das Ersetzen der RBG durch aktuelle Modelle im Vergleich zu einer reinen Modernisierung der alten Geräte an Leistungsgewinn bringen würde – und wie hoch dabei die Mehrkosten wären. „Mit komplett neuen, dynamischeren RBG steigern wir die Leistung um 30 %“, schildert Lars Breuer. Da fiel die Entscheidung leicht. Die beiden alten Geräte sowie die Fahrschienen wurden durch zwei Dachluken aus-, die neuen RBG auf gleichem Weg eingebracht. Die Betriebsfeuerwehr hat für die Sicherung auf dem Dach gesorgt und darüber hinaus beim Ein- und Ausbringen der Masten geholfen. „Dieses gemeinsame Stemmen des Projekts hat die Arbeit besonders gemacht“, betont Gregor Rentschler. Dennis Bosch bestätigt, „dass das Team ein Schlüssel war, um das Gesamtprojekt so erfolgreich umzusetzen.“
Leistungsschub für das Lager
Obwohl die modernisierte Anlage erst seit wenigen Monaten in Betrieb ist, zeigen sich schon Erfolge: „Noch ist es zu früh, konkrete Zahlen zu nennen“, berichtet Dennis Bosch. „Aber ich gehe davon aus, dass sich die Leistungssteigerung im zugesagten zweistelligen Bereich einpendeln wird. Die Kollegen im Lager haben bereits festgestellt, dass die Anlage schneller läuft. Nicht nur die Ware ist zügiger draußen, auch die Datensätze stehen jetzt blitzschnell bereit.“
Bereits kurz nach Inbetriebnahme der modernisierten Anlage verzeichneten die Metabo-Verantwortlichen eine deutliche Leistungssteigerung.
Bild: viastore
Über die Fernwartung lassen sich Ereignisse rasch online beheben. Zudem wird der Energieverbrauch sinken, da in den neuen RBG eine Zwischenkreiskopplung für einen internen Energieausgleich von motorischen und generatorischen Lasten sorgt. „Das gesamte Projekt verlief sehr gut“, resümiert Dennis Bosch zufrieden. Unternehmen, die eine Modernisierung ihrer Anlage beabsichtigen, empfiehlt er, „sich ausreichend Zeit für die Vorplanung zu nehmen – das sollte man nicht unterschätzen. Die Anlagenanalyse und die detaillierte Roadmap von viastore sind dafür eine verlässliche Basis.“
viastore SYSTEMS GmbHMagirusstr. 13D-70469 StuttgartTel.: +49 711 9818–0info.de@viastore.com