Best Fit in der Oberflächenmesstechnik
Die Methode des „Best Fit“ in der Oberflächenmesstechnik bietet zahlreiche Vorteile. Mit dem Einsatz automatischer Justage-Einrichtungen können Messprozesse optimiert werden. Das Dienstleistungsunternehmen für industrielle Messtechnik topometric mit Stammsitz in Göppingen wendet Best Fit-Verfahren in den eigenen Messlaboren an und hat damit durchweg positive Erfahrungen gemacht.
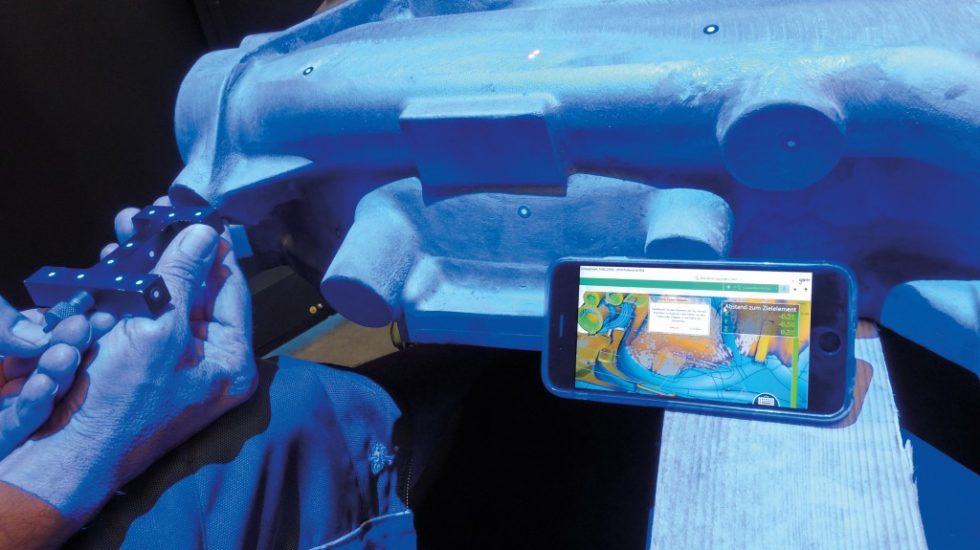
Bild 1. Markieren der Bohrungsmitte für eine Schraubbefestigung mithilfe der „Best Fit“-Methode: Das „iPhone“ dient als mobiler Bildschirm und zeigt die Positionskorrekturen an. Bild: topometric
Der Begriff Best Fit geht auf die statistische „Methode der kleinsten Quadrate“ zurück. Dabei wird die Soll-Oberfläche des CAD-Modells bestmöglich den gemessenen Ist-Daten angenähert, um in allen Messpunkten die kleinstmögliche Abweichung zu erreichen. Auf diese Weise ist das Bauteil theoretisch ideal ausgerichtet und der Restfehler geringer als bei klassischen Ausrichtungsverfahren.
Das mithilfe des Best Fit-Verfahrens ausgerichtete Bauteil liegt bis zu diesem Zeitpunkt allerdings lediglich als mathematisches CAD-Modell vor. An dieser Stelle wird die Rückführung häufig als Manko der Best Fit-Methode betrachtet, denn das frei im Raum liegende Bauteil muss ab diesem Zeitpunkt justiert werden.
Bauteile ausrichten: Klassische Verfahren versus Best Fit
Beim Ausrichten von Bauteilen wird grundsätzlich zwischen den klassischen und den stochastischen Verfahren unterschieden.
Klassische Verfahren
Klassische Verfahren ignorieren in aller Regel die tatsächliche Form des einzelnen Bauteils und setzen auf einfache Handhabung und Rückführbarkeit der nachfolgenden Arbeitsgänge. Diese Verfahren sind meist mathematisch eindeutig, wie das 3–2–1– beziehungsweise Ebene-Linie-Punkt-Verfahren. Da bei diesen Methoden die Ausrichtpunkte eindeutig sind, lassen sie sich auf weitere Bearbeitungsgänge vergleichsweise einfach übertragen. Ein gemessenes Teil kommt in nahezu gleicher Ausrichtung zum nächsten Bearbeitungsschritt, zum Beispiel auf die Fräsmaschine.
Stochastische Methoden
Bei stochastischen Verfahren – wie der Best Fit-Ausrichtung – wird die tatsächlich gemessene Oberfläche eines Bauteils per Gesamtanalyse ermittelt und das Bauteil zum Spannen virtuell derart verschoben, bis es in allen Flächen nur noch minimale Abweichungen zum CAD-Modell zeigt. Diese Vorgehensweise hat den Nachteil, dass der Vorgang lediglich am Computer existiert und eine Rückführung auf Spannvorrichtungen zum nächsten Arbeitsgang häufig mit erheblichem Aufwand verbunden ist.
Um die per Best Fit ermittelte Ausrichtposition auf den Bearbeitungs- und/oder Fräsmaschinen anwenden zu können, sind spezielle Justage-Vorrichtungen notwendig. Der Messtechnikspezialist topometric mit Sitz im baden-württembergischen Göppingen hat für dieses Umfeld eigene Justage-Vorrichtungen entwickelt und bereits mehrfach erfolgreich eingesetzt, Bild 1.
Selektive Anwendung
Da nicht jede Fläche eines Bauteils gleich wichtig ist, hat sich das „selektive Best Fit“ – auch als lokales oder diskretes Best Fit bezeichnet – etabliert. Hierbei werden in einem definierten Suchradius relevante Messpunkte ermittelt. Außerhalb liegende Punkte finden keine Berücksichtigung. Die Selektion wird damit nur auf die Bauteilflächen ausgerichtet, die für das Bauteil relevant sind.
Ein so ausgerichtetes Bauteil liegt in idealer Lage zu seinem Einsatzzweck. Häufig können Bauteile, die nach einer klassischen Methode Ausschuss wären, nach einer Best Fit-Ausrichtung noch Verwendung finden.
Best Fit-Verfahren kommen bereits seit einigen Jahrzehnten auch ohne optische Messmethoden zum Einsatz. Hilfsmittel sind Justage-Lehren, mit denen versucht wird, die ideale Lage des Bauteils innerhalb der Lehre herzustellen. Das Bauteil wird markiert oder gespannt und weiter bearbeitet. Da dieses Verfahren deutlich aufwendiger ist, als eine „normale“ Spannung auf dem Bearbeitungstisch, kommt es häufig nur bei kostenintensiven oder schwierig zu fertigenden Teilen zum Einsatz, um Restfehler und eine etwaige Verschrottung zu vermeiden.
Bei Massenfertigungen mit günstigen Rohstoffen hingegen – hier ist eine einfache und schnelle Handhabung entscheidend und eine bestimmte Ausschussquote kalkulierbar – kommen Best Fit-Verfahren meistens nicht zur Anwendung. Darüber hinaus wird Best Fit oft auch aufgrund seiner abstrakten, stochastischen Berechnungsmethode sowie mangels hinreichender praktischer Erfahrungen distanziert betrachtet.
Viele Anwendungsgebiete
Best Fit kann in nahezu allen Fertigungsbereichen der Industrie angewendet werden. Besondere Vorteile bietet die Methode bei der Rohteilfertigung oder bei Produktionsverfahren mit nicht eindeutig vorhersehbaren Herstellungsabweichungen. Angewendet wird Best Fit häufig in der Präzisionsfertigung, bei der Teile durch iterative Prozesse bis zum Idealmaß bearbeitet werden.
Aus der Praxis: Aluminiumrohteile für den Motorenbau
Bei einem besonders komplexen Aluminiumguss-Bauteil, das bisher mit erheblichen Restabweichungen produziert wurde, lag die Nacharbeitsquote bei 33 %. Um den Bauteilfehler entlang der X/Y/Z-Achsen zu vermitteln, musste das Bauteil vor dem Einsatz auf dem Bearbeitungszentrum als Ausrichthilfe manuell angerissen werden. Waren die Abweichungen so groß, dass sie sich nicht mehr ausgleichen ließen, mussten die Bauteile zum Hersteller zurückgeschickt werden.
Die Göppinger Messtechnikspezialisten stellten sich dieser Aufgabe, um eine bessere Lösung zu finden. Einige der aussortierten Teile wurden dafür in einer „ScanBox“ mithilfe eines „GOM-Atos-Triple-Scans“ komplett digitalisiert sowie auf Grundlage der Konstruktionszeichnungen maßgeschneiderte Ausrichtungen ermittelt, Bild 2.
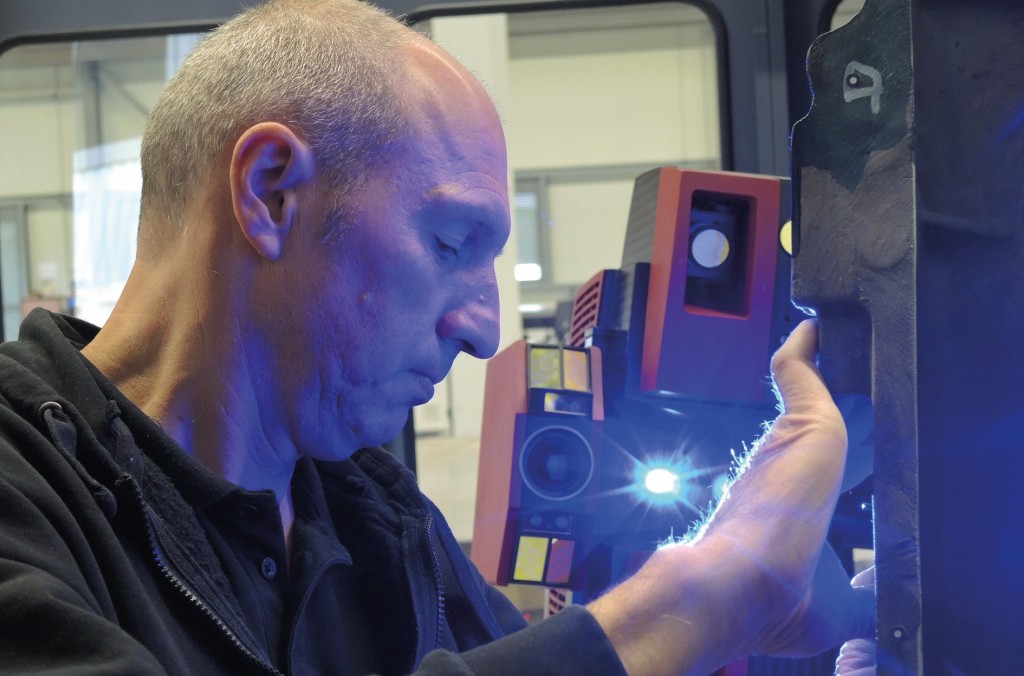
Bild 2. Zur kompletten Digitalisierung werden die Teile gescannt und mithilfe der Konstruktionszeichnungen maßgeschneiderte Ausrichtungen bestimmt. Bild: topometric
Anhand dieser Ausrichtungen wurde die Bauteillage bestimmt, in der alle entscheidenden Flächen innerhalb der Toleranz lagen und das Bauteil somit ohne Nacharbeit verwendet werden konnte. Die farbig ausgegebenen Messberichte helfen dem Hersteller, die Nacharbeitsbereiche auf einen Blick zu erfassen und gezielte Korrekturmaßnahmen einzuleiten.
Um das Bauteil auf dem Bearbeitungszentrum korrekt ausrichten zu können, wurde es unter Anwendung eines von topometric entwickelten Justage-Werkzeugs markiert. Diese Vorgehensweise lässt sich künftig noch weiter vereinfachen. Durch eine Teilautomatisierung kann das Verfahren zu einem Prozessschritt entwickelt werden, der an die Stelle des „Anreißens“ tritt. Damit lassen sich bei ähnlicher oder sogar geringerer Gesamtprozesszeit die Nacharbeitskosten erheblich senken.
Verfahren künftig deutlich einfacher umsetzbar
Bei höheren Stückzahlen sind auch vollautomatisierte Justage-Anlagen möglich. Pascal Kohl, Projektmanager Automation bei topometric, hat bereits umfangreiche Erfahrungen mit vollautomatischen Justage-Systemen gemacht und wird die Entwicklung weiterer Justage-Werkzeuge künftig vorantreiben. „Wir haben ausgezeichnete Ergebnisse mit den ersten selbst entwickelten Justage-Werkzeugen erzielt“, berichtet Kohl.
Bisher sprach lediglich die reale Umsetzung der virtuell ermittelten Ausrichtung gegen die Best Fit-Strategie. Mit der Entwicklung spezieller Justage-Vorrichtungen, die den Best Fit-Positionen entsprechen können, sind diese Nachteile weitestgehend ausgeräumt, Bild 3.
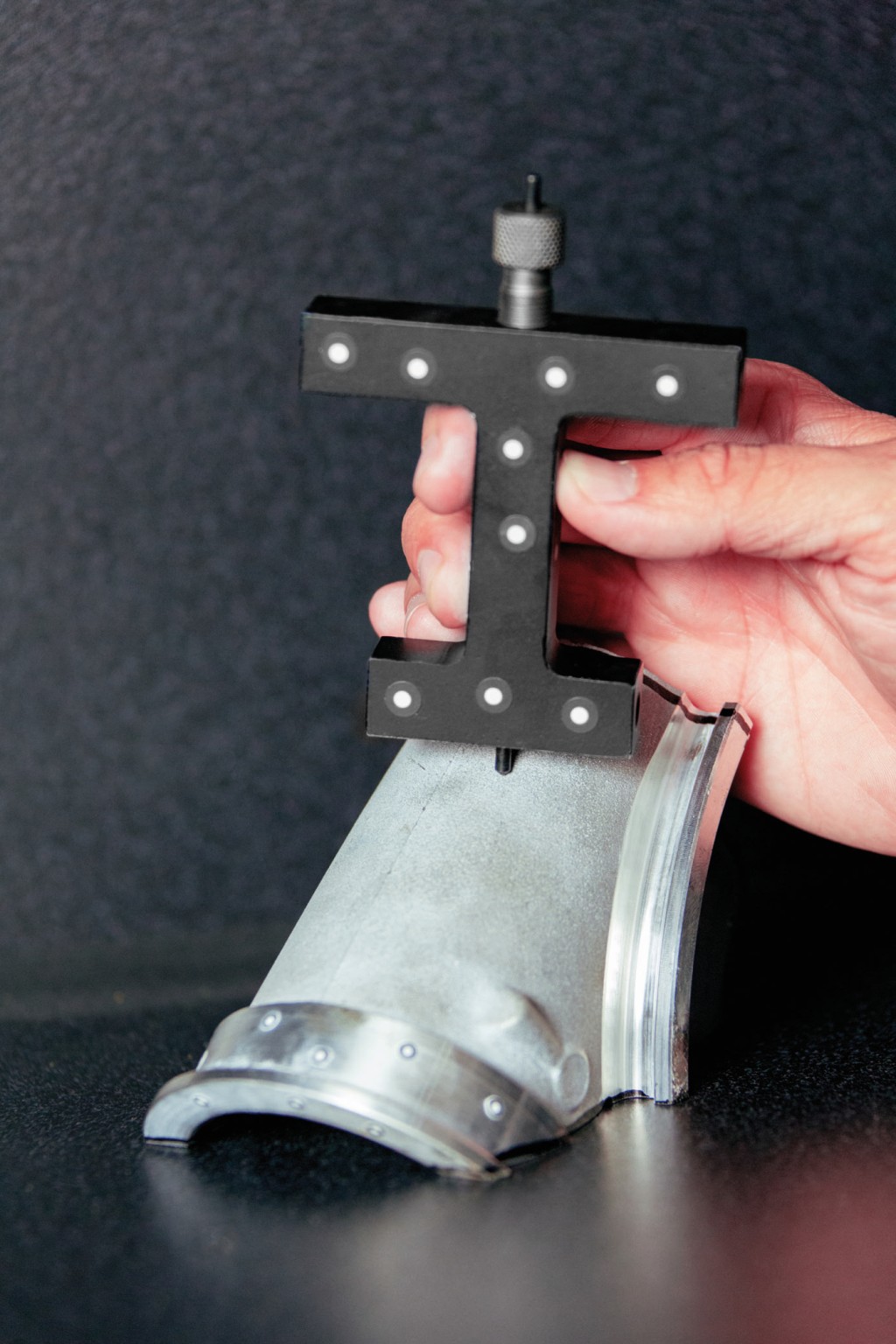
Bild 3. Die Göppinger Messtechnikspezialisten haben eigene Justage-Werkzeuge entwickelt, um das Verfahren noch einfacher umsetzen zu können. Bild: topometric
Das Verfahren ist somit entscheidend einfacher umsetzbar und hilft, gleichermaßen Zeit und Kosten zu sparen als auch Ressourcen zu schonen.
Dienstleister für industrielle Messtechnik
Das 2001 in Göppingen gegründete Unternehmen gilt als führender Dienstleister im Bereich der industriellen Messtechnik. Darüber hinaus entwickeln die baden-württembergischen Spezialisten Automationstechniken für die Messindustrie. Auf einer Gesamtnutzungsfläche von 6000 m2 werden nahezu alle Bereiche der optischen und taktilen Messtechnik abgedeckt. Der Betrieb ist nach DIN EN ISO/IEC 17025 akkreditiert. Das Unternehmen beschäftigt 80 Techniker und Ingenieure, davon zwölf am 2012 gegründeten Standort Unterschleißheim sowie fünf Mitarbeiter am 2016 gegründeten Standort Eching bei Landshut.
www.topometric.de
Maren Röding ist Presseverantwortliche für topometric in Göppingen.