Effiziente Helium-Dichtheitsprüfung von großen Automobil-Bauteilen
Beim Verbrennungsmotor waren Dichtheitsprüfungen in der Linienfertigung üblich. Aber auch nachhaltigere alternative Antriebe stellen ihre ganz eigenen Anforderungen an die Dichtheit der Antriebskomponenten. Eine optimale Prüfung gewährleistet Funktion und Sicherheit.
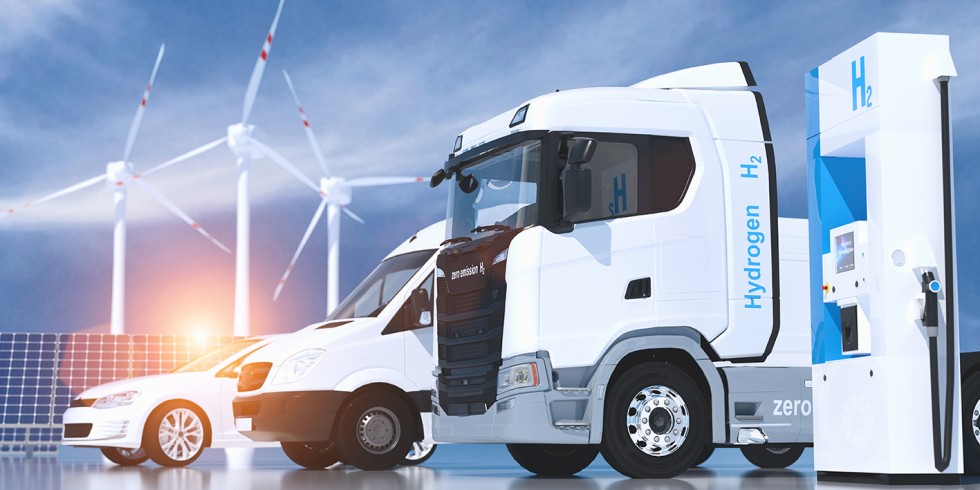
Ein Wasserstoff-Truck für emissionsfreie, umweltfreundliche Transporte: Neuartige Antriebskonzepte erfordern zuverlässige Dichtheits-Prüfverfahren, um Lecks ausschließen zu können. Grafik: shutterstock
Egal, ob es um die Gasdichtheit der einzelnen Lithium-Ionen-Zellen, die Wasserdichtheit der Batteriegehäuse oder um die Dichtheit der zahlreichen Komponenten eines Brennstoffzellenantriebs geht – den Wasserstofftank eingeschlossen – die Dichtheitspüfung ist bei Komponenten für alternative Antriebe unerlässlich.
Heliumprüfung hat sich als Methode etabliert
Eine besonders schnelle, empfindliche und zuverlässige Dichtheitsprüfmethode in der Linie ist die Heliumprüfung in einer Vakuumkammer. Gerade bei größeren Bauteilen steigen allerdings der Zeitbedarf und der Heliumverbrauch bei der Vakuumprüfung. Dank einer innovativen Softwarefunktion hat Inficon, Dichtheitsprüfspezialist aus Köln, die Effizienz der Prüfung auch bei großen Bauteilen jetzt deutlich erhöht. Denn „I·Zero“ berechnet den Helium-Untergrund, der die Messung beeinträchtigt, jetzt nicht mehr statisch, sondern erstmals dynamisch.
Die Prüfung in einer Vakuumkammer mit Helium als Prüfgas war immer schon das schnellste Dichtheitsprüfverfahren, mit deutlich kürzeren Taktzeiten als beispielsweise bei der Akkumulationsprüfung. Denn bei dieser Methode wird die Prüfkammer nicht evakuiert (weswegen der Prüfer warten muss, bis sich genügend Prüfgas in der Luft der Kammer angesammelt hat, um detektierbar zu sein). Der zeitliche Aufwand kann aber auch bei der Vakuummethode steigen – wenn die zu prüfenden Bauteile größer werden. Denn mit dem Bauteil wächst in der Regel auch das Totvolumen in der Prüfkammer, also der verbleibende Raum, der zunächst zu evakuieren ist. Denn erst dann kann ein Massenspektrometer ermitteln, ob und wie viel Helium-Prüfgas in das Vakuum austritt. Daraus ergibt sich erst, wie groß die Lecks im Prüfteil genau sind.

Auch dank der dynamischen „I∙Zero“-Funktion bekam der Anwender Maceas den Helium-Untergrund in der Prüfanlage in den Griff.
Foto: Maceas
Die Grenzen der statischen Untergrundbestimmung
Um den Prüfprozess bei der Vakuummethode zu beschleunigen, kamen bisher vor der eigentlichen Messung bereits sogenannte „Zero-Funktionen“ zum Einsatz. Eine Zero-Softwarefunktion hat den Sinn, den Helium-Untergrund auszublenden und nur das Helium aus dem Leck anzuzeigen – vergleichbar mit der Tara-Taste an einer Waage. Alle herkömmlichen Lösungen wählen auf der fallenden Kurve, den die Heliumkonzentration durch die Evakuierung beschreibt, bestenfalls den insgesamt niedrigsten Punkt aus, der als Nullpunkt der Messung dient. Bislang hat dieser statische Ansatz den Einsatz der Zero-Funktionen aber stark limitiert. Denn gerade, wenn Dichtheitsprüfungen gegen kleine Grenzleckraten nötig sind oder wenn in Vakuumkammern mit großem Volumen geprüft werden muss, lässt sich wegen der statischen Nullpunktbestimmung erst nach einer vergleichsweise langen Evakuierungsphase sinnvoll messen. Anderenfalls bliebe jede Leckrate unterhalb des definierten Nullpunkts schlicht unerkannt.
Neue Zero-Funktion beschleunigt den Prüfzyklus
Der große Unterschied der neuen Funktion zur Untergrundbestimmung ist, dass sie keinen festen Heliumwert als Nullpunkt definiert, sondern dynamisch vorgeht. Der Vorteil: Mithilfe eines dynamischen Nullpunkts lässt sich die Messung bereits viel früher beginnen. Die Software analysiert dazu kontinuierlich die Kurve, mit der der Helium-Untergrund während der Evakuierung und Prüfung fällt. Die jeweils vergangenen zwei Sekunden dienen dem Algorithmus dazu, das weitere Verhalten des Helium-Untergrunds zu extrapolieren. Das macht Leckraten, die ansonsten im Untergrund einfach verschwinden würden, bereits viel früher messbar.

Eine kleine Leckrate erweist sich als unmessbar bei Verwendung der herkömmlichen Zero-Funktion. Grafik: Inficon
Prozesssichere Dichtheitsprüfungen sind also schon nach einer deutlich kürzeren Evakuierungsphase möglich, sodass sich Durchsatz und Geschwindigkeit spürbar erhöhen. Abhängig vom Prüfteil und der Grenzleckrate, gegen die es getestet werden muss, ermöglicht es I·Zero zudem, die Anlage für die Vakuumprüfung weniger aufwendig auszulegen. Denn bei einer dynamischen Untergrundermittlung lässt sich auch mit kleineren, weniger stromhungrigen Vakuumpumpen bereits ausreichend evakuieren.
Zuverlässige Prüfung auch bei verringerter Heliumkonzentration
Eine deutlich schnellere Vakuumprüfung mit geringerem Evakuierungsaufwand ist der eine mögliche Vorteil, den eine dynamische Untergrundbestimmung eröffnet. Ein anderer ist die Option, den Heliumverbrauch zu reduzieren: Entweder man entscheidet sich dafür, mithilfe von I·Zero vor allem schneller zu messen, oder man verwendet für seine Prüfungen weniger Helium. Denn statt das manchmal kostspielige und mitunter aufwendig zu beschaffende Helium in unverdünnter Form zu verwenden, lässt sich nun auch die Konzentration des Prüfgases auf beispielsweise zehn Prozent reduzieren. Für das Dichtheitsprüfgerät ist das so, als würde gegen eine zehnfach kleinere Leckrate geprüft.
Werden bestehende Dichtheitsprüfanlagen mit einer Software zur dynamischen Untergrundbestimmung ausgerüstet, lässt sich der Prüfgasbedarf also auf einen Bruchteil reduzieren – ohne Abstriche bei der Empfindlichkeit und Geschwindigkeit. Angesichts der momentan angespannten Versorgungslage nicht nur bei Erdgas, sondern auch bei Helium, ist diese Möglichkeit hoch interessant. Dies gilt ebenso aus der Perspektive größerer Nachhaltigkeit. Einen dritter potenzieller Vorteil: Prüfanlagen werden flexibler. Früher mussten Prüfkammer und Prüfling in ihrer Größe gut aufeinander abgestimmt sein. Jetzt ist es möglich, große Vakuumkammern auch mit kleineren Prüflingen sinnvoll zu nutzen, trotz des damit einhergehenden größeren Totvolumens.
Einfachere Prüfung von Wasserstofftanks
Von der Beschleunigung des Prüfprozesses über mehr Flexibilität der Prüfanlage bis hin zur drastischen Reduzierung des Heliumbedarfs – die dynamische Untergrundbestimmung eröffnet vielfältige Möglichkeiten. Besonders positive Effekte kommen dadurch zustande, dass ein großes Totvolumen den Prüfablauf und die Taktzeiten weit weniger negativ beeinflusst als bisher. Gerade bei großen Bauteilen, die große Vakuumkammern erfordern, wird die Prüfung beschleunigt. Dies können beispielsweise Batteriewannen für Elektrofahrzeuge sein, Wasserstofftanks von Fuel Cell Vehicles oder Treibstofftanks für herkömmliche Verbrennungsmotoren.
Wasserstofftanks für Brennstoffzellenfahrzeuge sind meist sogenannte Typ-IV-Tanks, die aus Verbundwerkstoffen hergestellt werden. Solche Drucktanks für Pkws sind üblicherweise konstruiert, um Betriebsdrücken von bis zu 700 bar (oder 10.153 psi) zu widerstehen. Die Dichtheits- bzw. Leckratenanforderungen dafür ergeben sich aus einer Reihe von internationalen Normen, die maximal zulässige Permeationsraten für diese Tanks definieren. Dies sind Normen wie ISO15869 B.16, EU 406–2010 4.2.12.3. und ECE R134 5.3.3. Die materialbedingte Permeationsrate eines Wasserstofftanks ist bei seiner Dichtheitsprüfung mit einer Leckrate gleichzusetzen.
Bei einem Pkw-Wasserstofftank mit 30 l Kapazität und 700 bar Druck ergibt sich nach den Permeationsgrenzwerten umgerechnet eine Helium-Grenzleckrate im Bereich von 10–3 mbar∙·l/s. In der Realität werden Wasserstofftanks aber oft nicht bloß den Permeationsnormen entsprechend geprüft, sondern gegen Helium-Leckraten, die noch eine Dekade kleiner sind: im Bereich von 10–4 mbar∙l/s. Denn letztlich ist jede ermittelte Helium-Leckrate, die unterhalb der Permeationsrate des Materials selbst liegt, ein Beleg dafür, dass ein Leck existiert. Und Wasserstoffdichtheit ist eine unverzichtbare Anforderung an die Betriebssicherheit eines Brennstoffzellenfahrzeugs.

Fehlerhaftes Messergebnis: Eine große Leckrate scheint kleiner zu sein, mit herkömmlicher Zero-Funktion. Grafik: Inficon
Wasserdichte Batteriewannen für Elektrofahrzeuge
Zu den größten Bauteilen von Elektrofahrzeugen gehören die Gehäuse der Traktionsbatterien, genauer gesagt: die Batteriewannen. Ihre Aufgabe ist es, die Batterie vor einem Wassereintritt von außen zu schützen. Gegossene Batteriewannen weisen meist große Dichtflächen auf. Es ist darum sinnvoll, sie bereits vor dem Zusammenbau der Traktionsbatterie einer Dichtheitsvorprüfung zu unterziehen. Würden etwaige Lecks in der Batteriewanne erst nach dem Zusammenbau bei End-of-line-Prüfungen ermittelt, wäre der bisherige Fertigungsaufwand für die Traktionsbatterie verloren.
Viele Hersteller vermeiden dies durch entsprechende Vorprüfungen. Oft ziehen sie für die Dichtheitsprüfung gegenüber einem Wassereintritt in das Batteriegehäuse die Schutzklasse IP67 heran. Allerdings spricht die IP67 nur davon, dass ein Bauteil nach einem 30-minütigen Wasserbad in einem Meter Tiefe nach wie vor funktionstüchtig zu sein hat – konkrete Leckraten spezifiziert die IP67 nicht. Welche Grenzleckrate sinnvoll ist, hängt stark vom Gehäusematerial ab. Kunststoffe sind etwas weniger kritisch, aber Gehäuse aus Aluminium beispielsweise verlangen für die Prüfung ihrer Wasserdichtheit recht kleine Leckraten von 10–5 mbar∙l/s. Der Grund: Wassertropfen lösen sich von Aluminium sehr viel leichter ab als etwa von ABS oder Stahl. Darum dringt Wasser durch ein Aluminiumleck viel leichter in ein Batteriegehäuse ein. Ob bei der Dichtheitsprüfung von Batteriegehäusen oder von Wasserstofftanks: In all diesen Fällen steigert eine dynamische Helium-Untergrundbestimmung die Effizienz der Vakuummethode.
Bipolarplatten von Brennstoffzellen
Die dynamische Untergrundbestimmung findet ihre praktische Anwendung auch schon in Einsatzszenarien, bei denen eine Verseuchung des Untergrunds mit Helium nahezu unvermeidbar ist. Bipolarplatten beispielsweise, das Herzstück von Wasserstoff-Brennstoffzellen, verfügen über drei Kanäle, die alle untereinander und nach außen dicht sein müssen. Eine Bipolarplatte enthält jeweils einen Kanal für die beiden Prozessgase Wasserstoff und Sauerstoff sowie einen dritten Kanal für das Kühlmittel. All die erforderlichen Dichtheitsprüfungen recht schnell und unmittelbar nacheinander durchzuführen – in derselben Vakuumkammer –, wird nur deswegen möglich, weil die dynamische Nullpunktbestimmung in der Lage ist, die jeweils nächste Evakuierung zu verkürzen. Denn sie rechnet den sich nach jeder einzelnen Prüfung ergebenden restlichen Helium-Untergrund einfach aus der nächsten Messung heraus. Die kleinste Grenzleckrate, gegen die neue, innovative Anlagen die Dichtheit von Bipolarplatten heute prüfen können, liegt bei einem Helium-Volumenstrom von 10–5 mbar∙l/s – bei 10 Prozent Heliumanteil.
Die effizientere Helium-Prüfung
Als Faustregel darf gelten: Je größer das Bauteil und je größer die Vakuumkammer, desto größer die Vorteile, die sich durch eine dynamische Bestimmung des Prüfgas-Untergrunds während der Evakuierung ergeben. Bei etlichen Einsatzszenarien ist die Vakuummethode in der Fertigungslinie wegen ihrer grundsätzlich hohen Geschwindigkeit und Empfindlichkeit bereits die Methode der Wahl. Die dynamische Bestimmung des Helium-Untergrunds macht die Vakuumprüfung noch attraktiver. Wichtige Vorteile des innovativen Softwarealgorithmus reichen von einer nochmals gesteigerten Geschwindigkeit bei großen Prüfteilen bis zur Minimierung des Heliumverbrauchs.
In der Praxis um ein Drittel schneller
Der Entwickler Inficon hat seine neue Funktion zur dynamischen Bestimmung des Helium-Untergrunds bei der Dichtheitsprüfung in der Vakuumkammer „I·Zero“ genannt. Die innovative Softwarefunktion ist allerdings nur in Verbindung mit den Helium-Prüfgeräten des Herstellers erhältlich, denn der Algorithmus muss exakt an die Eigenschaften des jeweiligen Vakuumdichtheitsprüfgeräts angepasst sein. Zudem wurde die neuentwickelte Funktion zum Patent angemeldet.
Zahlen aus einer realen Anwendung belegen den Geschwindigkeitsvorteil des I·Zero-Algorithmus: Der Zweck des Testsystems war es dabei, ein großes Bauteil in einer 450 Liter messenden Vakuumkammer gegen eine Helium-Grenzleckrate von 10–5 mbar∙l/s zu prüfen. Mit der neuen dynamischen Untergrundbestimmung war das Testsystem in der Lage, die Zykluszeit vom Beginn des Abpumpens bis zum Vorliegen des Messergebnisses von 31 auf 20 Sekunden zu verkürzen – eine Beschleunigung um 35 Prozent.
Das könnte Sie auch interessieren:
Batterie-Recycling: Vom Problemfall zum erfolgreichen Geschäftsmodell
Die Automobilindustrie vor der Euro-7-Herausforderung
Eine „runde Sache“ – Assistenz für fehlerfreie Fertigungsprozesse

Dr. Jochen Puchalla arbeitet im Application Development bei der Inficon GmbH in Köln. Foto: Inficon