Experimentelle Modalanalyse an Industrierobotern
Industrieroboter lassen sich mit vielfältigen Werkzeugen ausstatten und somit für komplexe Bearbeitungsaufgaben an großvolumigen Bauteilen nutzen. Beim Einsatz in der spanenden Bearbeitung führt die Schwingungsneigung jedoch oft zu Problemen. Durch umfangreiche Messungen werden Grundlagen zum dynamischen Strukturverhalten erarbeitet.
![Bild 1. Industrieroboter übernehmen immer mehr Auf‧gaben bei der spanenden Bearbeitung von Bauteilen [1]. Bild: ISW, Universität Stuttgart](https://www.ingenieur.de/wp-content/uploads/2020/01/ZA-3024-Merovic-Bild-1-1-980x348.jpg)
Bild 1. Industrieroboter übernehmen immer mehr Auf‧gaben bei der spanenden Bearbeitung von Bauteilen [1]. Bild: ISW, Universität Stuttgart
Roboter finden zunehmend Einsatz bei der Bearbeitung von Oberflächen wie zum Beispiel beim Schleifen, Polieren, Bohren und Fräsen [1]. Bild 1 zeigt Industrieroboter im Einsatz bei der Bearbeitung von großvolumigen Bauteilen. Wenn die Roboter als serielle Kinematik aufgebaut sind, bedingt dies jedoch eine hohe Schwingungsanfälligkeit. Bei spanenden Prozessen führt die periodische Anregung aus dem Prozess zu einer schlechten Oberflächengüte oder einer Abweichung von der Soll-Geometrie des Werkstücks. Darüber hinaus ergibt sich ein erheblicher Verschleiß am Werkzeug und führt zu häufigen Wartungsarbeiten.
Eine Minimierung dieser Nachteile ist nur möglich, wenn das dynamische Strukturverhalten analysiert und somit bekannt wird. Hierfür wird häufig die Methode der experimentellen Modalanalyse (EMA) verwendet. Damit die Modalanalyse korrekt durchgeführt werden kann, müssen mehrere Fragen im Vorfeld beantwortet werden: Wo wird angeregt? Wie wird angeregt? Wo wird gemessen? Diese Fragen werden anhand zahlreicher Messungen am Roboter beantwortet, um den hohen Messaufwand einer EMA möglichst zu verringern.
Versuchsstand
Bei einer experimentellen Modalanalyse wird die Struktur des Systems mit einer Kraft angeregt und die daraus resultierenden Schwingungen gemessen. Dabei wird meist die Beschleunigung der Schwingungen von Sensoren erfasst. Die Kraftanregung kann zum einen mit einem „Shaker“ („Rüttler“) und zum anderen mit einem Impulshammer in alle drei Raumrichtungen geschehen [2]. Der verwendete Shaker ist in Bild 2 (links) dargestellt.
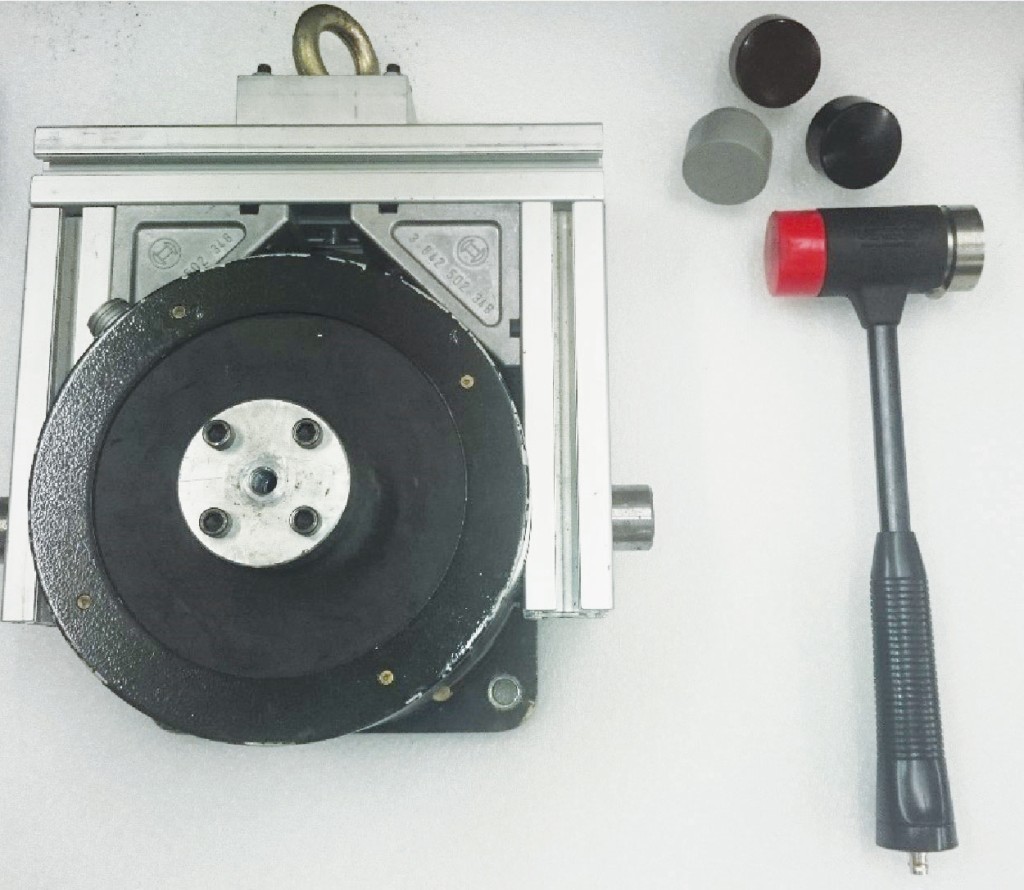
Bild 2. „Bruel&Kjaer Exciter Typ 4808“ (links) und „PCB Piezotronics Impact Hammer 086D20“ mit verschiedenen Spitzen (rechts). Bild: ISW, Universität Stuttgart
Durch die Verwendung können unterschiedliche Anregungen erzeugt und in das System eingeleitet werden. Die aufgebrachte Kraft wird von einem Kraftsensor zwischen Shaker und Roboter gemessen. Die Amplitude der Anregung ist ebenfalls einstellbar.
Diesem Test steht der „Impact“ (Stoß)-Test gegenüber. Dabei findet die Anregung über einen Impulshammer statt. Der Impuls wird mit dem Hammer manuell in das System eingeleitet. In Bild 2 (rechts) ist der verwendete Impulshammer mit mehreren aufschraubbaren Hammerspitzen zu sehen. Diese unterscheiden sich in ihrer Härte und somit darin, welchen Frequenzbereich sie anregen [3]. Mit der roten Hammerspitze wird der Frequenzbereich bis 100 Hz, in welchem die dominanten Eigenfrequenzen des Roboters auftreten, ausreichend angeregt.
Die aus der Anregung resultierenden Schwingungen der Struktur wurden mit uniaxialen Beschleunigungssensoren gemessen und ausgewertet. Dabei ist die Anregung und Erfassung der niedrigen Eigenfrequenzen eine Herausforderung. Das zu untersuchende System war ein Roboter des Augsburger Herstellers Kuka, Bild 3.
Niedrige Eigenfrequenzen sind für Stellungen zu erwarten, in denen die Roboterstruktur einen langen Hebel aufweist. Daher fiel die Auswahl auf eine Extremstellung, wie in Bild 4 dargestellt.
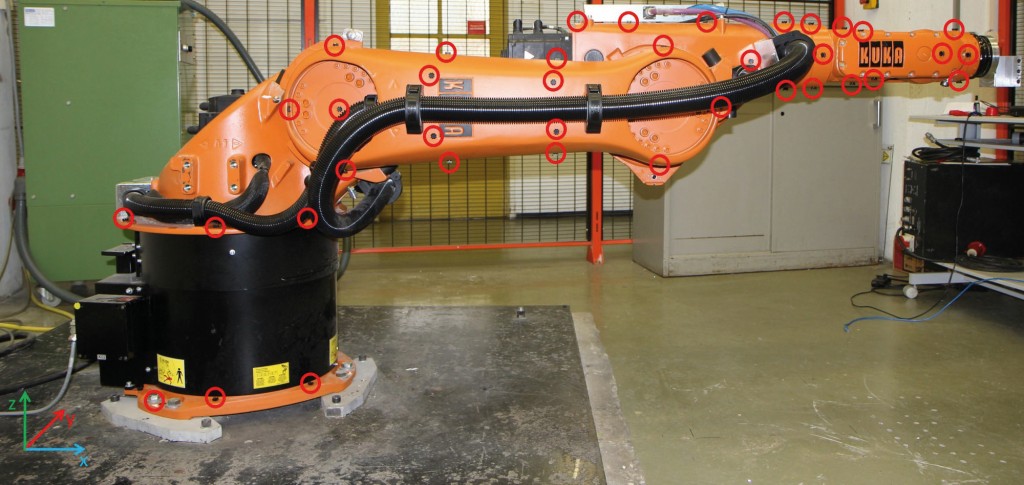
Bild 4. Der untersuchte Roboter in ausgestreckter Pose: Die Schwingungsanfälligkeit ist dann am größten. Bild: ISW, Universität Stuttgart
Diese Pose beschreibt den parallelen Verlauf von Schwinge, Arm und Hand.
Wo wird angeregt und wo wird gemessen?
Am Roboter wurden komponentenweise entsprechende Stellen für die Mess- und Anregungspunkte bestimmt. Dabei wurden glatte und ebene Flächen bevorzugt. Andernfalls weicht die tatsächlich gemessene Beschleunigung von der gewünschten Beschleunigung aufgrund der nicht übereinstimmenden Richtungen ab. An jedem Messpunkt wurde eine Halterung mit Sekundenkleber befestigt, wie in Bild 4 durch rote Kreise angedeutet. Die Halterungen sind speziell für die Beschleunigungssensoren hergestellt. So wurden die Sensoren an den Halterungen angebracht und erleichterten die Messung. Zusammenfassend wurden am Industrieroboter 86 Messpunkte definiert. Darunter befanden sich 19 Messstellen am Karussell, 30 an der Schwinge, 20 am Arm und 17 an der Hand.
Der Wahl der Messpunkte folgte die Wahl der Anregungspunkte für den Shaker-Test als auch den Impact-Test. Der Shaker wurde durch eine Vorrichtung frei schwingend aufgehängt, um eine Kraft auf die Struktur mithilfe seiner trägen Masse aufzubringen. Am Roboter werden für die mechanische Kopplung Bohrungen vorausgesetzt, welche am Karussell und an der Hand vorhanden sind. Die Masse des Shakers verändert die Steifigkeit des Roboters durch die Verschraubung. Die Anregung an der Hand entspricht jedoch der Anregung in der Realität und würde prinzipiell auch weniger Energie brauchen, um die Anregung der gesamten Struktur sicherzustellen.
Bei Anbringung des Shakers am Karussell hingegen ist der Einfluss aufgrund der Massenverhältnisse vernachlässigbar. Die Verschraubung des Karussells mit dem Fundament verringert den Einfluss zusätzlich. Untersuchungen haben keine Unterschiede bezüglich der Ergebnisse ergeben. Die Montage des Shakers am Karussell regt alle Eigenfrequenzen an und ist somit unbedenklich. Vor allem im Hinblick auf die Durchführung von experimentellen Modalanalysen in verschiedenen Roboterposen ruft die Kopplung des Shakers mit der Hand Schwierigkeiten hervor. Bei Montage des Shakers mit dem Karussell dagegen kann der Roboter in der x-z-Ebene frei positioniert werden. Aus diesen Gründen wurde der Shaker mit dem Karussell gekoppelt.
Die Aufhängung des Shakers machte nur die Anregung in x- und y-Richtung möglich, welche aber wie beschrieben zur Anregung aller Eigenmoden ausreichte [2]. Für den Impact-Test wurden komponentenweise mehrere Stellen am Roboter für die Anregung definiert. Da keine Einschränkung bezüglich der Richtung der Schlagausführung existierte, wurde in allen drei Raumrichtungen angeregt. Am Karussell und am Arm wurden drei, an der Schwinge vier und an der Hand fünf Stellen als mögliche Anregungspunkte identifiziert. Im Anschluss daran wurden die möglichen Anregungspunkte für den Impact-Test durch probeweises Anregen mit dem Hammer untersucht und miteinander verglichen. Basierend auf den Ergebnissen dieser Voruntersuchungen, wurde der Roboter beim Impact-Test in x-, y- und z-Richtung an der Hand angeregt.
Messdurchführung und -ergebnisse
Beim Shaker-Test wurde die Methode des „Rowing Accelerometer“ verwendet. Dafür wurden die uniaxialen Beschleunigungssensoren von einer Messstelle zur nächsten umpositioniert. Die zuvor genannten Halterungen erleichtern dabei die Durchführung. Dieses Vorgehen wurde für die weiteren Anregungsrichtungen wiederholt. Um möglichst alle Eigenfrequenzen des Roboters anzuregen, wurde ein „Sinus-Sweep“ verwendet. Er beschreibt einen Sinusverlauf mit einer linear zunehmenden Frequenz [5].
Beim Impact-Test ist auf eine „saubere“ Ausführung des Schlags zu achten. Bevorzugt wird das Fassen mit einer Hand, möglichst am Ende des Hammerrumpfes. Unmittelbar nach dem Aufprall soll der Hammer vom Rückschlag geführt werden. Ein zu festes Halten des Hammers in diesem Augenblick erzeugt ein Prellen, was die Messungen verfälschen kann. Für eine zuverlässige Messung ist stets ein konstanter und reproduzierbarer Schlag auszuführen. Auch hierfür wurde die Methode des Rowing Accelerometer verwendet.
Nach der Durchführung des Shaker- und Impact-Tests wurden die Messdaten auf dem Arbeitslaptop mit Hilfe der Messsoftware „LMS Test.Lab“ bearbeitet und ausgewertet. Dies schloss die Veranschaulichung der Ergebnisse im Frequenzbereich und die Animation der Moden an einem geometrischen Simulationsmodell des Industrieroboters in der ausgewählten Pose ein. Bild 5 zeigt die Übertragungsfunktionen der jeweiligen Messungen.
Eigenfrequenzen sind in der Übertragungsfunktion als Peaks zu erkennen. Im Bereich bis 60 Hz liegen alle für das dynamische Verhalten relevante Eigenfrequenzen, deshalb ist die x-Achse der Darstellung dementsprechend begrenzt.
Die detektierten Eigenfrequenzen beim Shaker-Test unterscheiden sich von den Eigenfrequenzen beim Impact-Test nur geringfügig – wobei diese beim Impact-Test stets größer sind als beim Shaker-Test. Neben den Eigenfrequenzen sind auch ihre Amplituden beim Impact-Test größer, zum Teil bis zu zwölfmal.
Werden die animierten Moden der Tests miteinander verglichen, unterscheiden sie sich nur quantitativ. Das heißt, es besteht nur ein Unterschied in der Amplitude der Schwingung. Die Schwingformen dagegen sind ähnlich. Beim Shaker-Test sind im Bereich vor der ersten Eigenfrequenz Peaks zu sehen. Der Shaker erzeugt jedoch erst ab einer Frequenz von circa 9 Hz eine geeignete Anregungskraft, deshalb sind die Ergebnisse unterhalb dieser Frequenz nicht aussagekräftig und wurden vernachlässigt.
Folgerung
Die Auswertung der Moden hat gezeigt, dass die Anzahl von 86 Messstellen reduziert werden kann. Bild 6 zeigt die zweite Mode beim Shaker-Test bei 35,3 Hz.
Sie dient exemplarisch für die Modendarstellung in der Messsoftware LMS Test.Lab. Das Karussell bewegt sich nahe der Verschraubung mit dem Fundament kaum. Deshalb entfallen dort die Messpunkte. In den ersten drei Moden sind wenige Deformationen an den Antrieben zu erkennen. Darüber hinaus bewirken Messungen an den Antrieben eine schlechte Kohärenz aufgrund der dort verbauten nichtlinearen Getriebe. Somit fallen die Messpunkte an den Antrieben weg. Demnach reichen drei Messpunkte am Karussell.
An allen Messstellen der Schwinge sind Bewegungen zu erkennen. Die Messpunkte an den Gelenken können entfernt werden, weil die dortigen Bewegungen mit denen der nächstliegenden Messstellen an der Schwinge zwischen den Gelenken übereinstimmen. Daher bleiben insgesamt 20 Messpunkte an der Schwinge. Am Arm sind keine komplexen Schwingungen zu erkennen, deshalb genügen rings um den Arm herum vier Messpunkte für die Erfassung der Eigenmoden. An der Hand werden zwölf Messpunkte benötigt. Sie sind ebenfalls alle rings um die Hand definiert. Die restlichen Messstellen an der Hand sind nicht notwendig, da ihre Bewegungen mit den zwölf Messpunkten zuvor identisch sind.
Zusammengefasst konnte die Anzahl von 86 Messpunkten auf 39 reduziert werden. Sofern sich keine Platzprobleme für den Shaker aufgrund der Aufhängung ergeben, genügt beim Shaker-Test die Anregung in x-Richtung. Wird nicht genügend Platz gewährleistet, besteht die Möglichkeit, auf den Impact-Test zurückzugreifen. Dabei reicht die Anregung in z-Richtung.
Bei beiden Tests wird an allen 39 Messstellen in drei Raumrichtungen gemessen. Der Impact-Test nimmt allerdings mehr Zeit in Anspruch als der Shaker-Test. Letzteres ist für den Nutzer angenehmer, da die Messdurchführung per Mausklick am Laptop gestartet wird – wohingegen beim Impact-Test stets ein manueller und reproduzierbarer Hammerschlag auszuführen ist. Es ist aber sicherzustellen, dass der verwendete Shaker den relevanten Frequenzbereich abdeckt und innerhalb dessen auch genügend Kraft für die Anregung der Struktur am Karussell erzeugen kann. Auf Basis dieser grundlegenden Erkenntnisse, können experimentelle Modalanalysen an weiteren Posen des KR 60 HA und auch an anderen Robotern mit weniger Aufwand durchgeführt werden.
Literatur:
BosS – Energieeffizienter Bearbeitungsroboter mit selbstadaptierendem Systemverhalten für spanende Arbeitsvorgänge an inhomogenen Werkstoffverbunden. Gemeinsamer Ergebnisbericht des BMBF-geförderten Verbundprojekts BosS, 2015.Allemang, R.; Avitabile, P.: Handbook of Structural Dynamics. New York: Springer-Verlag, 2007. Kohrmann, M.; Völtl, R.; Müller, G.; Schanda, U.; Buchschmid, M.: Planungshilfen zur schall- und schwingungstechnischen Beschreibung von Holzdecken und zur Bewertung und Dimensionierung von angepassten Schwingungsschutzsystemen. Technische Universität München, Lehrstuhl für Baumechanik, Abschlussbericht zum AiF-Forschungsvorhaben „VibWoodd“, 2014.Kuka-Roboter GmbH: http://www.kuka-robotics.com/germany/de/products/industrial_robots/special/high_accuracy_robots/kr60_ha/start.htm (09.09.2015). Schlauch, T.: Aufbau und Optimierung eines kompakten und leistungsfähigen fs-Diodenlasersystems. Dissertation, Ruhr-Universität Bochum, Fakultät für Elektro- und Informationstechnik, 2011 .
Petrit Merovci, B.Sc., Jahrgang 1992, studierte Mechatronik an der Universität Stuttgart. Seit 2015 ist er zusätzlich als Hilfswissenschaftler am Institut für Steuerungstechnik der Werkzeugmaschinen und Fertigungseinrichtungen (ISW) der Universität Stuttgart tätig. // Ali Karim, M.Sc., Jahrgang 1975, studierte Antriebssysteme und Mechatronik an der FH Heilbronn. Seit 2011 ist er wissenschaftlicher Mitarbeiter im Bereich „Zerspanen mit Industrieroboter“ am ISW. // Dr.-Ing. Armin Lechler, Jahrgang 1979, studierte Technische Kybernetik an der Universität Stuttgart. Seit 2009 leitet er am ISW die Abteilung Steuerungstechnik. Seit 2011 ist er am ISW zudem geschäftsführender Oberingenieur.