Größte berührungslose Robotermesszelle der Welt arbeitet in einer Gießerei
„Casting is our Passion“, so lautet das Unternehmensmotto in der Gießerei Siempelkamp in Krefeld. Für diese Leidenschaft ist der Mittelständler jetzt in einer Kooperation ungewöhnliche Wege gegangen und hat außerdem eine Großinvestition getätigt – das Ergebnis ist beeindruckend.
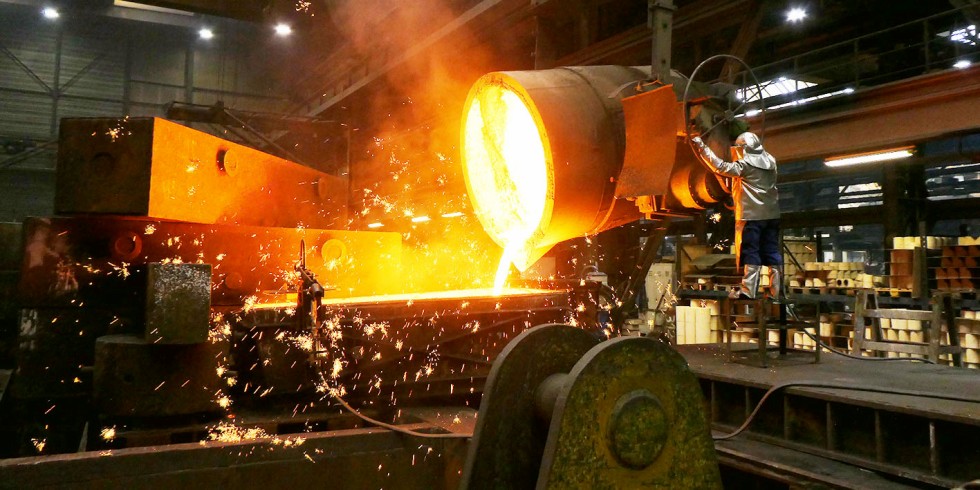
Abguss von über 1.300 Grad Celsius heißem Sphäroguss: Beim Blick auf einen Gießvorgang in der Siempelkamp Giesserei offenbart sich dem Betrachter noch nicht, wie hochgradig digitalisiert die Arbeitsgänge im Werk inzwischen ablaufen.
Foto: Etmanski
Mit ihren Gussteilen setzen die Krefelder bereits seit Langem Maßstäbe in Sachen Komplexität, Präzision, Qualität und Zuverlässigkeit. Dies äußert sich unter anderem darin, dass überall auf der Welt Großbauteile aus Krefeld in industriellen Anlagen zu finden sind. Nun ist ein weiterer Superlativ hinzugekommen: Ende 2022 wurde die nach eigenen Angaben „weltweit größte berührungslose Robotermesszelle der Welt“ der Öffentlichkeit vorgestellt. Obwohl diese mit ihren Dimensionen fast eine komplette Halle einnimmt und meterlange, tonnenschwere Bauteile vermessen kann, erinnern die erzielbaren Messwerte mit unter 0,6 Millimetern Genauigkeit fast an gängige Präzisionsbauteile.
Fruchtbare Kooperation
Für die Umsetzung des ambitionierten Vorhabens holten sich die Verantwortlichen zwei Projektpartner „mit ins Boot“: Zeiss Industrial Quality Solutions aus Aalen ist zuständig für die „Hardware“ und das Braunschweiger Start-up a3Ds feilte erfolgreich an der technischen Realisierung einer passenden Automatisierung. Neben der bestmöglichen Qualität für den Kunden werden mit der Investition noch weitere Ziele verfolgt: „Mit dieser hochinnovativen Technologie treiben wir unsere umfassende Digitalisierungsstrategie weiter voran. Wir sind nun in der Lage, die Bauteilgeometrie unserer Produkte vom Modell über die Gießform bis zum fertigen Gussteil durchgehend digitalisiert zu verfolgen“, erklärt Dr. Georg Geier, Geschäftsführer der Gießerei. Auch für den renommierten Messtechnikspezialisten aus Aalen bedeutet die erfolgreiche Umsetzung eine Premiere und ist zugleich ein Vorzeigeprojekt.
Überdimensionale Eisengussteile „handgeformt“ erzeugen
1902 als Siempelkamp’sche Eisen- und Metallgießerei gegründet, stehe der traditionsreiche Name laut Geier auch für eine Verpflichtung: dem Kunden stets die „perfekte Antwort in Guss zu geben“. Allein die Größe der Teile bedeutet ein Alleinstellungsmerkmal: im Bereich ab 100 Tonnen Gussteilmasse gibt es kaum noch Wettbewerber. Möglich sind in Krefeld sogar Teile bis zu 320 Tonnen. Der Durchschnitt liegt bei etwa 20 Tonnen.
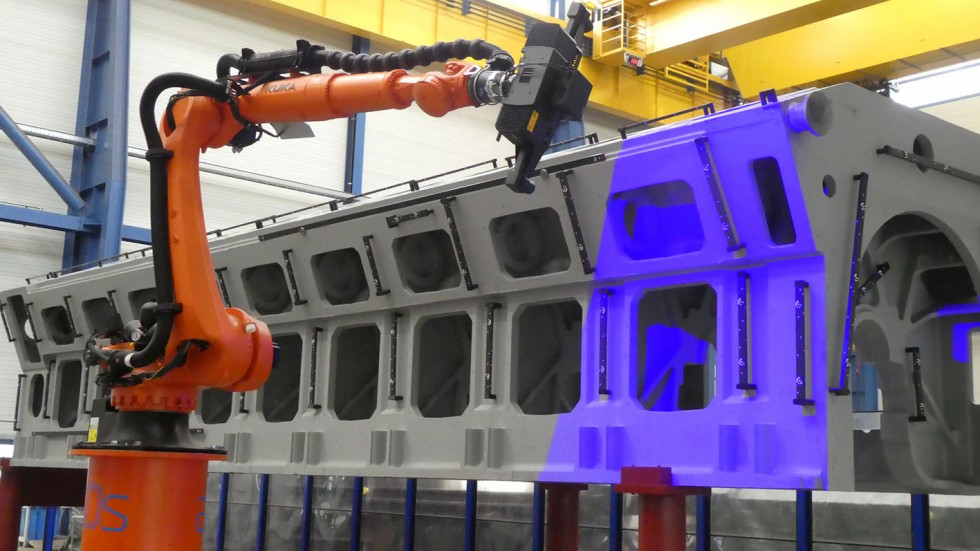
Als Demonstrationsobjekt für die Messzelle diente das Kubelgehäuse eines 18-zylindrigen Goßmotors in V-Bauweise. Jedes Jahr entstehen in Krefeld rund 100 Motorgehäuse, zum Teil mit bis zu 10 Metern Länge und 90 Tonnen an Gusseisen.
Foto: Etmanski
Dazu gehören Komponenten für Windkraftanlagen ebenso wie riesige Industriemotoren oder Gehäuse für die Zementindustrie. Im letzteren Fall ließen sich sogar bis zu 90 % Energie (und CO2) im Betrieb einsparen – durch effizientere Mahlwerke. Aktuell werden rund 2.000 Gussteile im Jahr produziert, und sowohl der Bedarf als auch die Anforderungen wachsen ständig. Investitionen sichern dabei die Leistungsfähigkeit des Standorts.
Vor allem gehöre zur Verpflichtung aber die Passion für das „Handwerk“ – nur so werde aus der Ursprungsidee das perfekte Gussteil, und aus der Vision Innovation. Als Grundlagen nennt Geier die lange Erfahrung, großes metallurgisches Know-how, ständige Forschung und Entwicklung sowie persönlicher Einsatz für jedes Projekt. Um den Kundenforderungen und auch den gesetzlichen Vorgaben gerecht zu werden, ist zudem eine ständige, zuverlässige Qualitätssicherung (QS) vonnöten. Dazu überwachen die Spezialisten alle Projektschritte und Materialien – vom eingesetzten Rohstoff bis zur Endkontrolle des fertigen Gussprodukts. Zahlreiche Zertifikate und branchenspezifische Zulassungen zeigen, dass die gesetzten Qualitätsziele bestens erreicht werden.
Innovative Entwicklung vom Messtechnik-Marktführer
Mit der Robotermesszelle ist nun ein weiterer wichtiger QS-Baustein hinzugekommen. Sie macht eine vollautomatisierte, berührungslose und zuverlässige Inspektion fertiger Bauteile bis zu einem Gewicht bis 240 Tonnen möglich. Trotz der Dimensionen der Zelle liegt ihre Messgenauigkeit dank der bis zu zwölf Millionen 3D-Messpunkte bei unter 0,6 Millimetern.
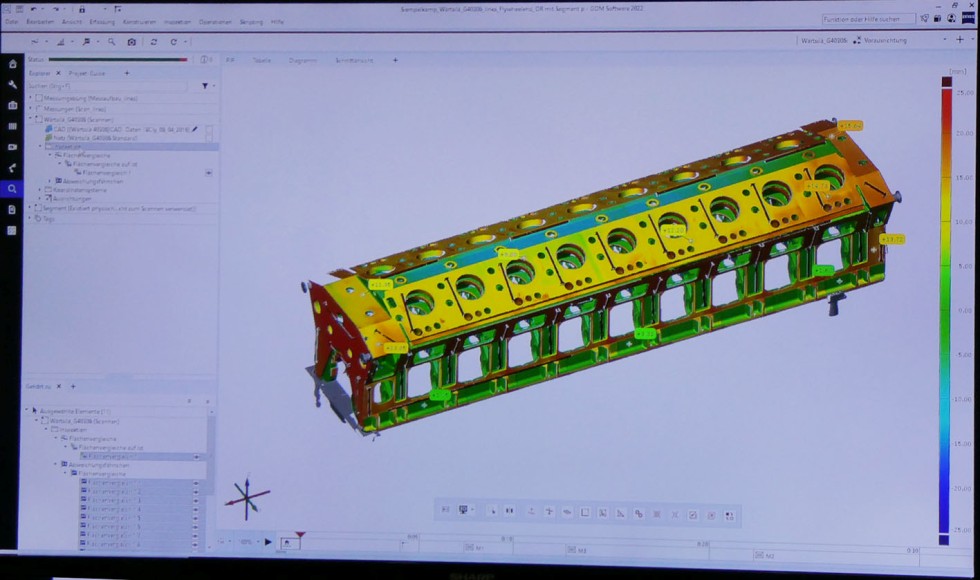
Die Grafik zeigt die Ergebnisse der Vermessung des Großmotors, die Abweichungen vom Sollmaß sind farblich gekennzeichnet.
Foto: Etmanski
„Dieses System ist das weltweit modernste und leistungsstärkste seiner Art und hilft uns dabei, unsere Gieß- und Fertigungsprozesse durch digitale Technik noch weiter zu optimieren“, ergänzt Geier. So werde die Abschätzung von Schwund oder Ausdehnung im 3D-Raum jetzt auf einem ganz neuen Präzisionsniveau möglich. Zugleich haben sich die Messzeiten durch das automatisierte Vorgehen ganz erheblich verkürzt.
Auch die Kunden der Gießerei profitieren: Dank der millimetergenauen Prüfung übergroßer Komponenten steige die Qualität der Bauteile zugunsten von Nachhaltigkeit und Effizienz, die sich in Bearbeitung und Betrieb äußert. So könne letztlich mit viel weniger Aufmaß kalkuliert werden, sodass später auch weniger Bearbeitungsaufwand anfalle, oder Bauteile lassen sich dünnwandiger konstruieren.
Hergestellt wurde die Robotermesszelle vom Spezialisten Zeiss Industrial Quality Solutions in Kooperation mit den Automatisierungsexperten des Start-ups a3Ds. Zeiss gilt als Innovationsführer im Bereich der optischen 3D-Messtechnik und entwickelte für die Zelle eigens einen hochmodernen Scanner. Dieser verfügt über ein Messfeld von 2.000 x 1.600 Millimetern und ist dank bahnbrechender Tiefenschärfe in der Lage, die hochkomplexen Bauteile wie Schiffsmotoren, Mahlschüsseln oder Pressen in kürzester Zeit aufzunehmen. Und mit insgesamt zwei Messräumen, die Parallelarbeiten zulassen, bietet das Automatisierungssystem besondere Flexibilität sowie größtmögliche Effizienz.
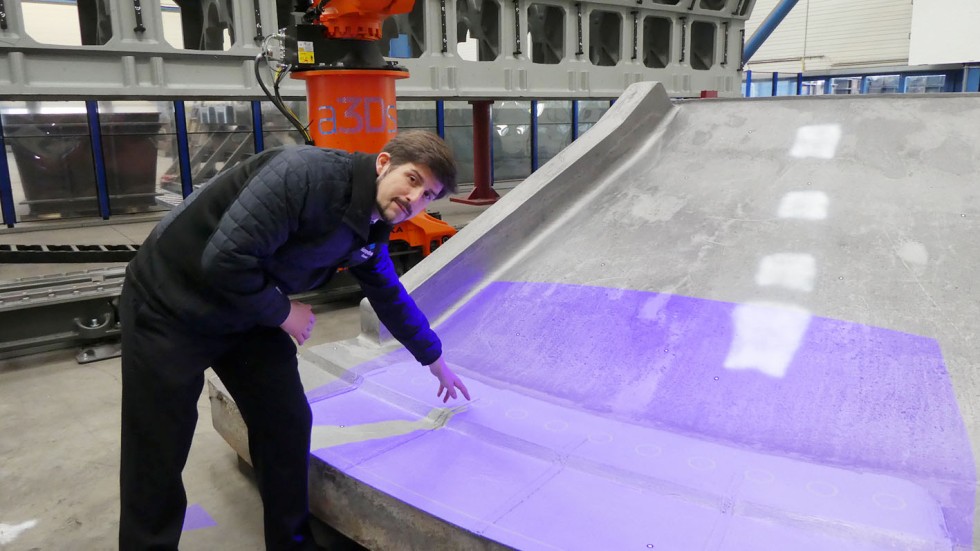
Dr. Georg Geier, Geschäftsführer der Siempelkamp Giesserei, erläutert die Funktionsweise des Sensors an einem Mühlensegment.
Foto: Etmanski
Beispiel für maßgeschneiderte Digitalisierung im industriellen Mittelstand
Beste Voraussetzungen bietet der Einsatz moderner Robotertechnologie, mit deren Hilfe sich schnell und bedienungsfreundlich ein kompletter „digitaler Zwilling“ des untersuchten Bauteils am Bildschirm erstellen und analysieren lässt. Dirk Behring, Geschäftsführer von Zeiss Industrial Quality Solutions Deutschland, fasst zusammen: „Für uns ist die hier realisierte automatisierte Messanlage ein Best-Practice-Beispiel für die Vermessung sehr großer Gussbauteile. Unsere Lösungen erfüllen die hohen Anforderungen an effektive Messverfahren in der Produktion und punkten durch Flexibilität. Insbesondere machen sie die vollständige Digitalisierung von Bauteilen möglich.“
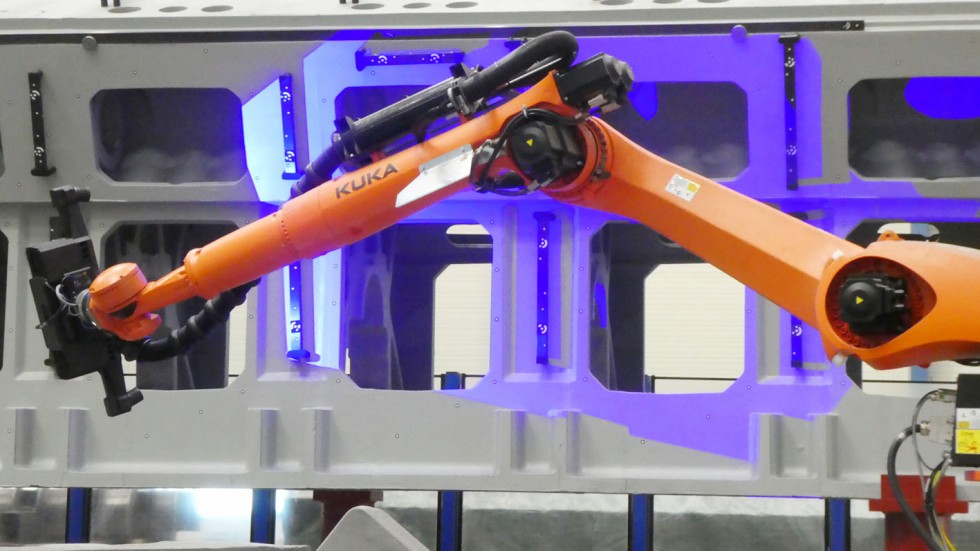
Der Messroboter vermisst den tonnenschweren Schiffsmotor und erstellt einen digitalen Zwilling des Objekts. Durch die Beweglichkeit des Roboterarms werden auch schwer zugängliche Bereiche erreicht.
Foto: Etmanski
Auch David Skuratowicz, Mitgründer und Geschäftsführer von a3Ds, ist stolz, bei der Entstehung der Anlage einen entscheidenden Anteil geleistet und diese große automatisierte Messanlage erfolgreich realisiert zu haben. In diesem Geschäftsfeld sieht er generell Wachstumspotenzial für das Start-up: „Der Bedarf an solchen oder ähnlichen Anlagen wird in vielen Industriebereichen sicherlich steigen. Industrielle, optische und automatisierte 3D-Messtechnik wird immer wichtiger. Hier sehen wir den Trend in Richtung Digitalisierung, Effizienzsteigerung sowie der Optimierung und Absicherung von Prozessen im Qualitätsmanagement.“
Digitale Messtechnik kommt auch am Beginn der Prozesskette zum Einsatz
Doch nicht nur die fertig gegossenen Bauteile werden zukünftig mithilfe digitaler Technologie millimetergenau auf die Einhaltung höchster Qualitätsstandards untersucht. Bereits am Anfang der Prozesskette kommt die 3D-Messtechnik von Zeiss zum Einsatz: Mit dem „T-Scan hawk“ hat die Gießerei ihre Möglichkeiten bei der optischen Lasermesstechnik in der Modellbauschreinerei nochmals deutlich erweitert.
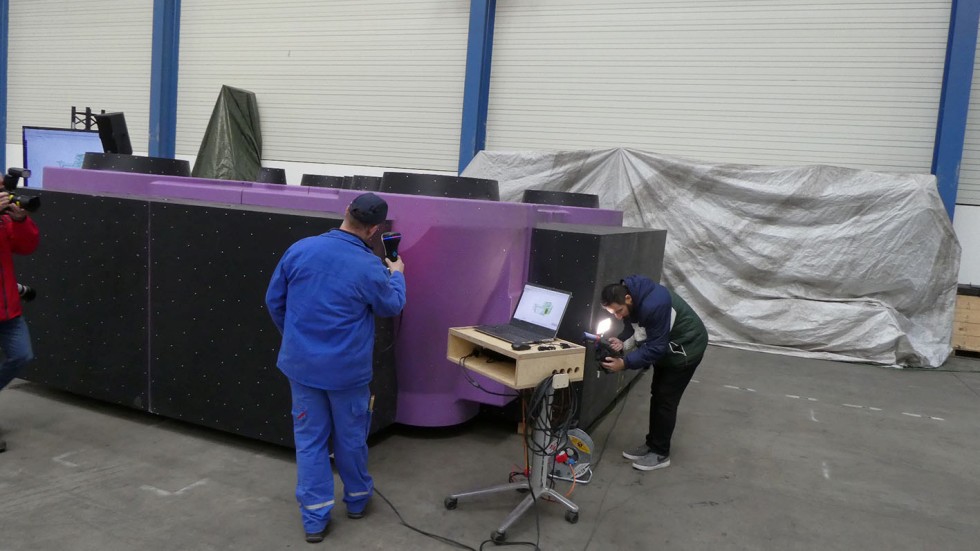
Auch die Vermessung eines großen Holzmodells mithilfe des „T-Scan hawk“ von Zeiss wurde live präsentiert.
Foto: Etmanski
Der handliche Scanner kann die Abmessungen und Geometrien von Holzmodellen, die ein Positiv des fertigen Gussbauteils sind, genauestens prüfen und Fehler bereits zu Beginn der Bauteilproduktion vermeiden. „Auf diese Weise lassen sich Soll und Ist im Frühstadium unserer Herstellungsprozesse transparent für unsere Kunden abbilden. Außerdem werden bisher ungeahnte Potenziale bei der Konstruktionsgenauigkeit gehoben“, verdeutlicht Dirk Howe, ebenfalls Geschäftsführer der Siempelkamp Giesserei. Dank der Softwareplattform „Quality Suite“ lässt sich die Bauteilentstehung über den gesamten Prozess in der Gießerei lückenlos verfolgen. Die Kunden profitieren von einer Vielzahl an Informationen rund um die gefertigten Bauteile, die durch die digitalen Prozesse ermittelt wurden und die sie für deren weiteren Einsatz nutzen können.
Digitalisierungsoffensive dank starker technologischer Partnerschaften
Dirk Howe ist stolz auf die jüngsten Erfolge der Digitalisierungsstrategie: Die Inbetriebnahme der technologisch bahnbrechenden Robotermesszelle sei nur der jüngste Meilenstein im Komplettkonzept der Siempelkamp Giesserei, welche das Ziel hat, die gesamte Prozesskette automatisierter und digitaler zu machen. Bereits im Jahr 2021 wurden mit der Digitalisierung der Induktions-Tiegelöfen Maßstäbe gesetzt. Dank der Optimierung der Messtechnik in der Gießerei ist nun eine weitere Pionierleistung gelungen.
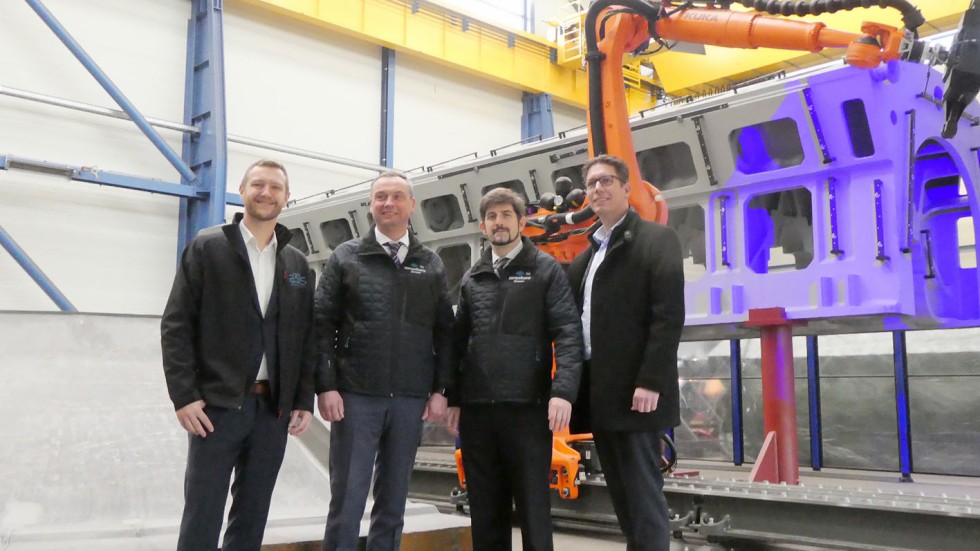
Gruppenbild der Projektverantwortlichen (v.l.n.r.): David Skuratowicz (a3Ds), Dirk Howe, Dr. Georg Geier (beide Siempelkamp Giesserei) sowie Dirk Behring (Zeiss).
Foto: Etmanski
„Mit unseren Kooperationspartnern haben wir aus eigenem Antrieb die weltweit erste High-Tech-Robotermesszelle für so große und komplexe Bauteile entwickelt. Damit stärken wir den Wirtschaftsstandort Deutschland nachhaltig und leisten gleichzeitig einen spürbaren Beitrag für mehr Digitalisierung und Automatisierung im deutschen Mittelstand. Wir freuen uns, Kunden in aller Welt jetzt qualitativ noch hochwertigere Lösungen für ihren Wettbewerbsvorteil zu bieten“, so Howe.
Das könnte Sie auch interessieren:
Wie Messroboter die Qualitätssicherung autonom bewältigen
Spektakuläre Großteile fertigen: 60 Tonnen und 14 Meter „auf einen Streich“
Herausforderungen beim Wälzstoßen von Pfeilverzahnungen
Birgit Etmanski, promovierte Maschinenbauingenieurin, ist Chefredakteurin der Zeitschrift VDI-Z in Düsseldorf.