Im Mannheimer John Deere-Werk prüft der „Sky Hawk“ die Traktoren
Selbständig fahrende Traktoren, aufeinander abgestimmte Erntemaschinen, KI-Unterstützung bei dynamischen Arbeitssituationen rund um den Acker – die Zukunft der Landwirtschaft ist schon auf vielen Betrieben zum Arbeitsalltag geworden. Doch die Digitalisierung findet nicht nur auf dem Feld statt.
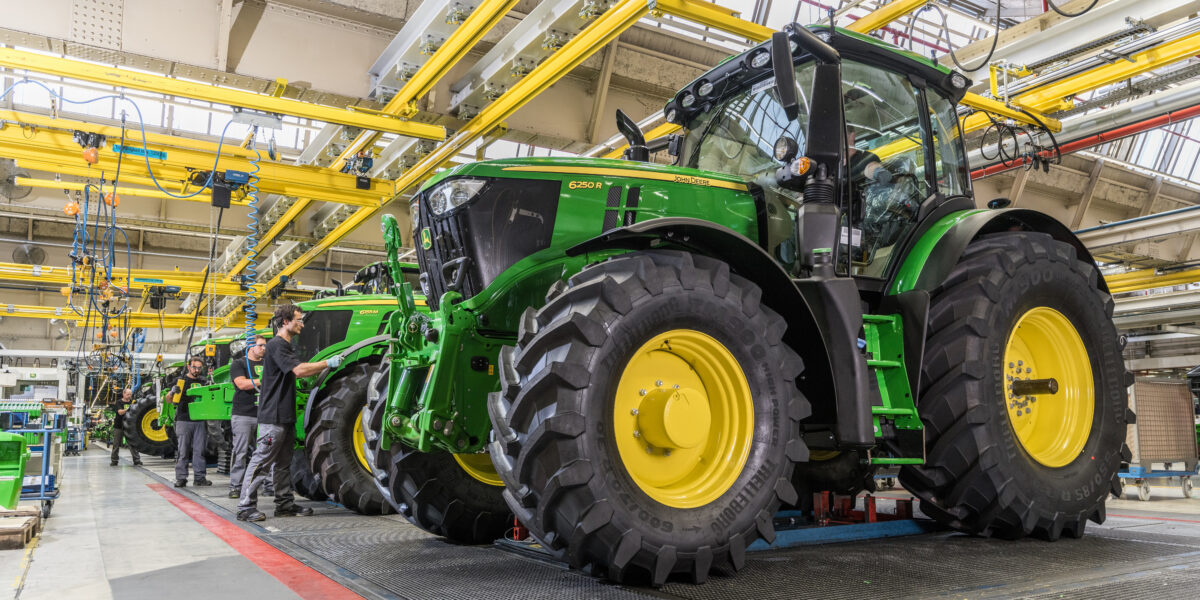
Mitarbeiter im John-Deere-Werk montieren im Bild Traktoren der Serie 6250R. Seit Kurzem werden sie von einer hochmodernen Lösung zur automatisierten Qualitätssicherung unterstützt.
Foto: John Deere
Im Werk von John Deere in Mannheim erkennt und behebt bereits heute ein Kameraroboter Fehler im Produktionsprozess. Denn: Die 140 Traktoren, die im Mannheimer Betrieb täglich vom Band rollen, müssen hohen Qualitätsansprüchen entsprechen. In verschiedenen Fertigungszuständen werden sie auf einem großen, über 80 Meter langen Montageband durch die Werkshalle befördert. Dabei entsteht dann aus einem nackten Chassis ein kompletter Traktor mit Kabine, Motorhaube, Reifen und Beleuchtung. Ihr Weg führt die Traktoren an Prüfungsstationen vorbei, an denen sichergestellt wird, dass jedes Teil richtig eingebaut wurde. Vor drei Jahren hat sich diesbezüglich das Team der Automatisierten Fertigung bei John Deere überlegt, den Produktionsschritt der Qualitätssicherung effizienter zu gestalten.
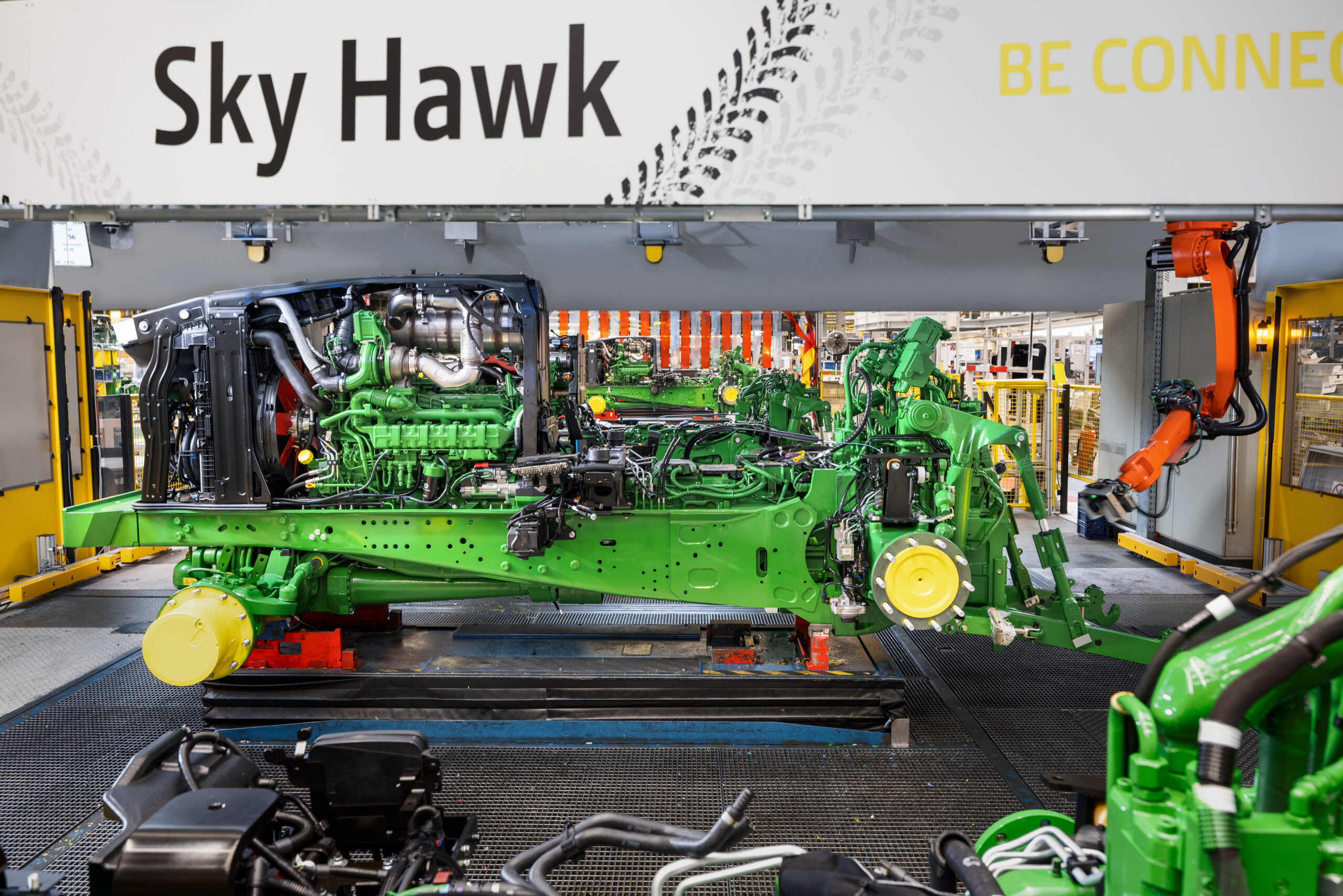
Der „Sky Hawk“ arbeitet mittlerweile ausgezeichnet mit den menschlichen Kollegen des John Deere-Werkes zusammen.
Foto: John Deere
Das Konzept drehte sich von Anfang an um High-Tech-Kameras und Künstliche Intelligenz. Ein ähnliches System von John Deere, genannt „See & Spray“, unterscheidet bereits auf dem Acker Nutzpflanzen von Unkräutern – selbständig und in Sekundenbruchteilen. Bei „See & Spray“ erfassen satellitengestützte Hochgeschwindigkeitskameras zentimetergenau, welche Ackerpflanzen mit ihrer individuellen Dosis Pflanzenschutzmittel versorgt werden und welche nicht. Eine solche selbständige Erkennung käme auch der Fertigung zugute, um Abweichungen in der Produktion frühestmöglich zu erkennen. Damit war die Idee um ein vollautomatisches Inspektionssystem mit einem KI-gesteuerten Kameraarm, welches Montageergebnisse mit industrieller Bildverarbeitung interpretiert, geboren.
Aus dem Digitalen in Werkstruktur
Die erste Herausforderung war es, ein solches System nahtlos in die über Jahre gewachsene Fabrikstruktur in Mannheim zu integrieren. Schwierig war es vor allem, die Größe des Systems mit einem unterbrechungsfreien Fertigungsalltag in Einklang zu bringen. Um mehr über die Funktionalität der Anlage herauszufinden, baute das Team der Automatisierten Fertigung erstmals einen komplett digitalen Prototypen des Systems und taufte diesen ganz heroisch „Sky Hawk“.
Der gesamte analoge Prüfungsablauf eines Traktors – von vorne bis hinten und von unten bis oben – wurde zunächst in ein digitales Modell übertragen, bevor die Anlage schließlich ins reale Werk implementiert wurde. Üblicherweise werden Kamera-Prüfsysteme parallel zu der Montagelinie aufgebaut. Durch das parallele Fahren ist dann eine Synchronisation an die Montagegeschwindigkeit möglich. Das war platzbedingt in der Mannheimer Produktion nicht realisierbar, deshalb ist der Sky Hawk so einzigartig, denn nur eine Portalanlage, die quer zur Fertigungslinie über den Traktoren arbeitet, war umsetzbar. Nur eine maßgeschneiderte Lösung war eine Option.
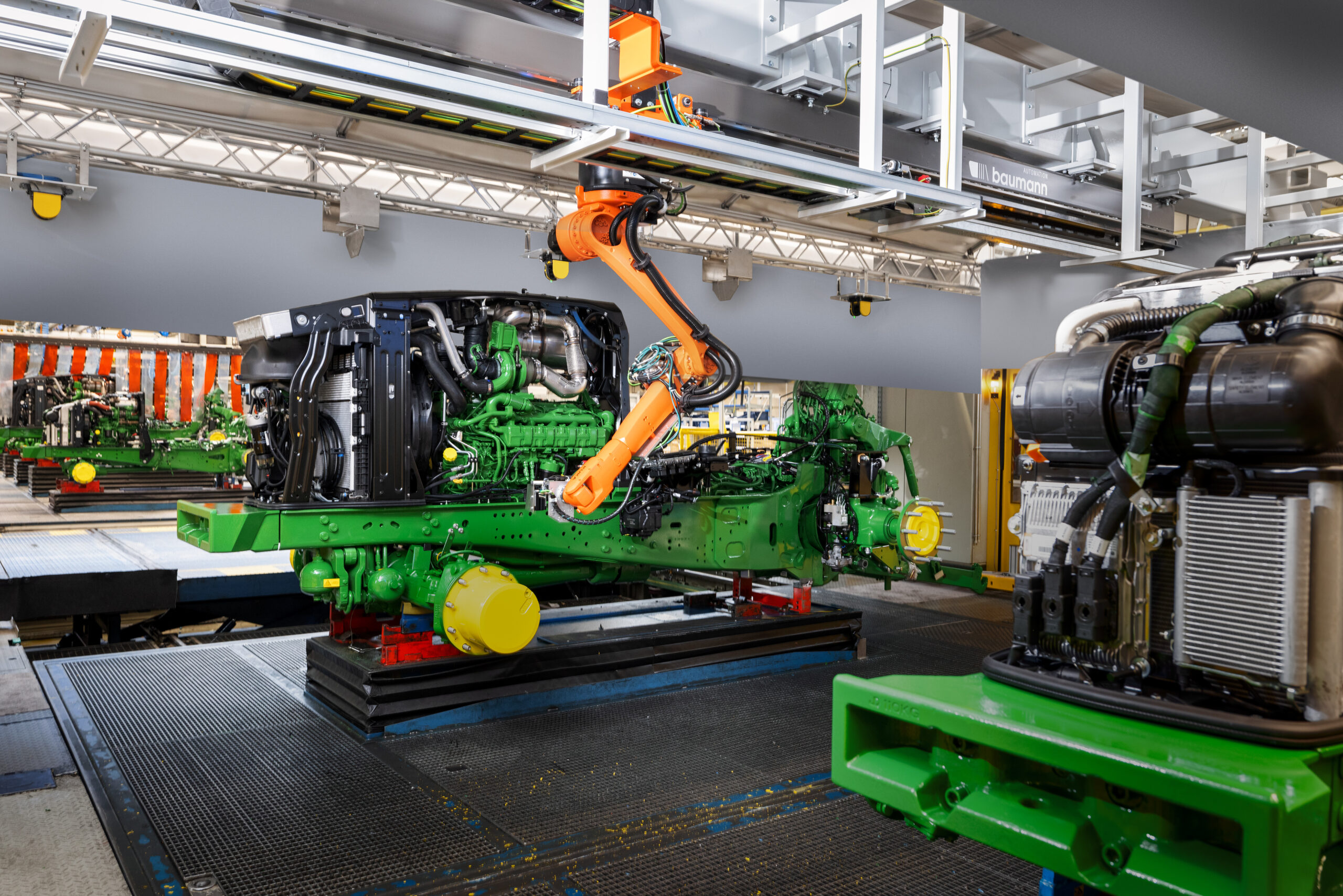
Je nach Modell werden vom Sky Hawk bis zu 600 Prüfpunkte angefahren. Alle gefundenen Fehler werden behoben und im System archiviert.
Foto: John Deere
Neben der räumlichen Herausforderung galt es nun, Hard- und Software miteinander zu verknüpfen. Insbesondere musste die quer stehende Portalanlage gewährleisten, dass eine große Variantenvielfalt an Prüfpunkten erfasst, bewertet und in der maximalen Taktgeschwindigkeit von 3 Metern pro Minute abgearbeitet werden konnte. Um dies zu erreichen, arbeiteten die unterschiedlichen Prüfstellen der Traktormontage zusammen und übertrugen nach und nach Prüfpunkte für z. B. Motor, Kühler oder Achse ins System. Nach vielen Teststunden und programmierten Codezeilen funktionierte der „digitale Sky Hawk“ und das Team baute das System in einer leeren Halle auf dem Mannheimer Werksgelände für erste Testläufe auf.
Nachdem diesem Testlauf in der „echten Welt“ wurde die Portalanlage endlich in den Produktionsalltag integriert. Die Betriebsferien des Mannheimer John Deere-Werks waren der ideale Zeitpunkt. 14 Tage hatte das Team Zeit, das Sky Hawk-System in der Testhalle ab und in der Traktorenproduktion an den Hauptbändern wiederaufzubauen – inklusive aller Anpassungen der Werkselektronik und aufwendigen Montagearbeiten. Pünktlich zum Ende der Betriebsruhe kam die topmoderne Lösung im August 2023 zum Einsatz.
Qualitätssicherung gelingt in nur drei Minuten
Durch einen großen Torbogen führt das Montageband seitdem die Traktoren. Der Arbeitsbereich des Sky Hawk wird durch blaue Lichter auf dem Boden markiert. Die Kamera fährt innerhalb von drei Minuten pro Station bis zu 50 Prüfpunkte an und vergleicht den Zustand des Traktors mit Bildern des Sollzustands, welche zuvor von Prüfern des Teams der Automatisierten Fertigung im System abgespeichert wurden. Die Kamera kann jeden Winkel des Traktors inspizieren, sie ist an einem Sechs-Achs-Roboterarm montiert, der sich auf einer Linearachse über dem Traktor bewegt. Auf diese Art wird der menschliche Bewegungsablauf einer Prüfung durch eine Werkerin oder einen Werker imitiert – präzise, schnell und zuverlässig.
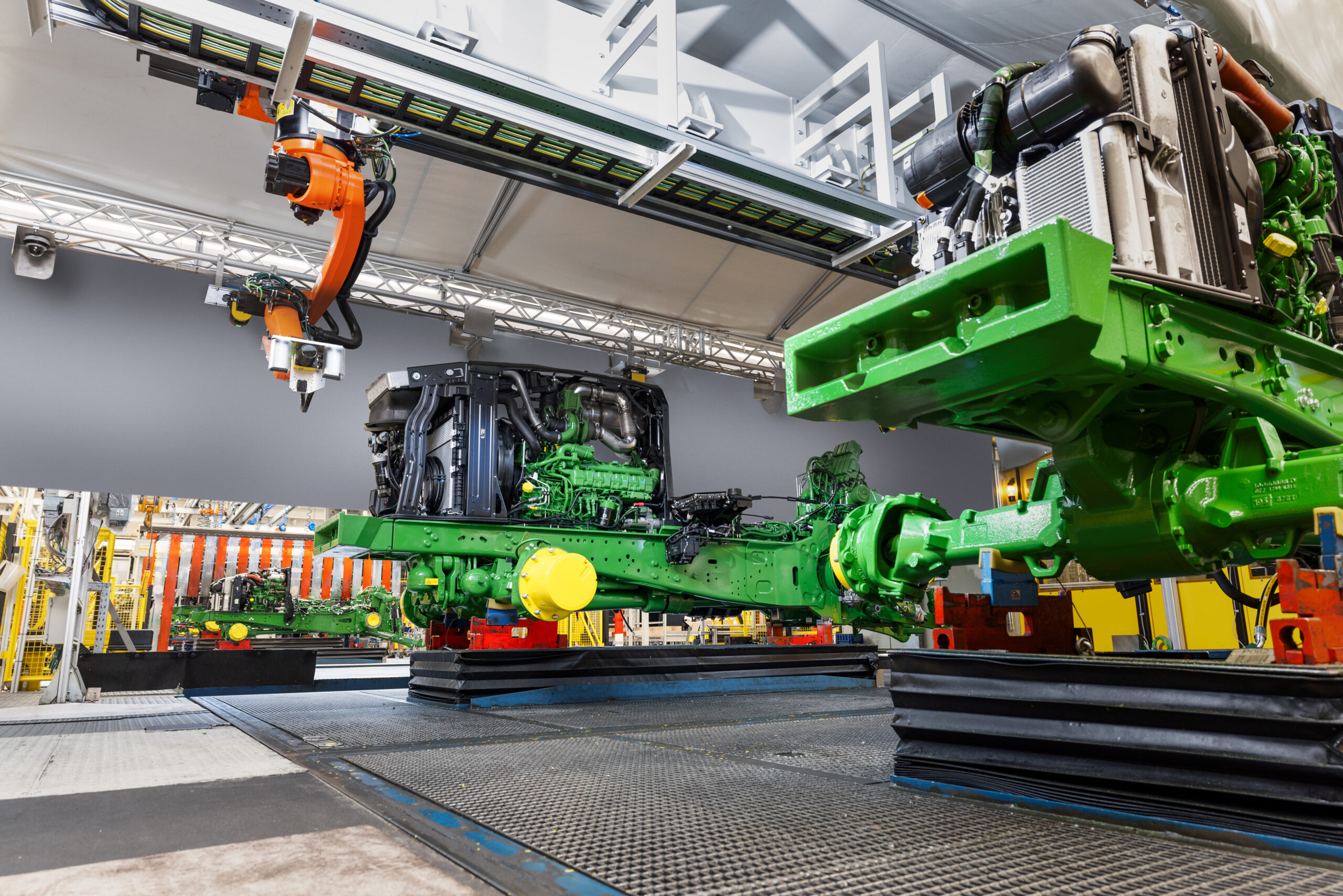
Die an einem Sechs-Achs-Roboterarm montierte Kamera kann jeden Winkel des Traktors inspizieren. Der orangefarbene Arm bewegt sich auf einer Linearachse über dem Traktor.
Foto: John Deere
Experten haben die Prüfpunkte, an denen die Kamera halten muss, genau programmiert und vorgegeben. Digitale Modelle bilden die Grundlage für die Prüfung: Die Kamera fährt im Live-Betrieb tatsächlich nicht den physischen Traktor vor sich ab, sondern einen digitalen „Mantel“, der über der jeweiligen Maschine liegt. Welches Modell in welcher Konfiguration geprüft werden soll, erfährt der Sky Hawk über einen RFID-Chip im Tankdeckel jedes Traktors.
Das beste beider Welten
Der Sky Hawk arbeitet mittlerweile ausgezeichnet mit den menschlichen Kollegen des John Deere-Werkes zusammen. Ein fester „Springer“ eines jeden Produktionsbereiches trägt eine Smartwatch am Handgelenk. Stellt Sky Hawk eine Unregelmäßigkeit fest, analysiert das System in Echtzeit, welcher Produktionsbereich dieses Problem beheben kann. Über seine Smartwatch erhält der Springer aus dieser Prüfstelle dann einen Alarm, welcher anzeigt, wo der Unterschied zwischen dem digitalen Mantel und dem echten Traktor sitzt. An der Sky Hawk-Station kann der Springer das Problem dann beheben.
Danach drückt der Springer auf einen Knopf seiner Prüfstation und schickt den Traktor über das Laufband weiter zur nächsten Prüfung. Abhängig vom Traktorenmodell werden vom Sky Hawk bis zu 600 Prüfpunkte angefahren und jeder gefundene Fehler wird behoben und im System von Sky Hawk archiviert. Auf diese Weise entsteht ein individuelles Produktionsprofil für jedes Traktorenmodell bei John Deere. Der nächste Schritt der Qualitätssicherung wäre dann, dass der entstehende Traktor auf dem Montageband seine eigene Wartung selbständig durchführt und Fehler bei „seiner“ Fertigung meldet.
Fazit
Das Sky Hawk-Projekt ist ein Sinnbild für die Integration moderner technischer Systeme in bestehende Produktionsstrukturen. Aktuell wird bereits ein zweites System in der Mannheimer John Deere-Getriebefabrik aufgebaut – wie sein Vorgänger ist es maßgeschneidert auf die Räumlichkeiten und di Anforderungen.
Das könnte Sie auch interessieren:
Kaltumgeformte Präzisionsteile direkt im Fertigungsprozess prüfen
Qualität in der Industrie sichern mittels Terahertz-Spektroskopie
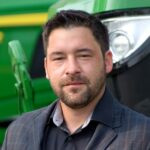
Tobias Trunk ist Factory Automation Engineering Lead bei der John Deere Group im Stammwerk Mannheim und zuständig für die europäischen Produktionswerke. Er ist Experte für Fertigungs- und Montageautomation. Seine Hauptbeschäftigung ist aktuell die Integration von „Pick and place“ Lösungen in bestehende Montagelinien – mit den Schwerpunkten Geometrie, Gewicht und Variantenvielfalt. Foto: Autor